Inventory Management Chapter 12 PDF
Document Details
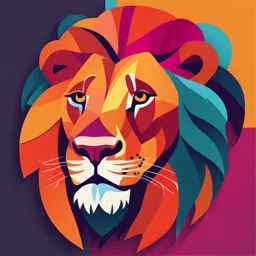
Uploaded by ConstructiveYeti
Tags
Related
Summary
This document is a chapter on inventory management. It details planning and controlling operations within an organization. It covers topics such as inventory planning and control, and reasons to support inventory.
Full Transcript
Part Three Deliver – Planning and controlling operations Chapter 12 Inventory Management Inventory management Operations Topic covered...
Part Three Deliver – Planning and controlling operations Chapter 12 Inventory Management Inventory management Operations Topic covered strategy in this chapter Operations Inventory planning Design management Improvement and control The market requires … Planning the availability of products and and control services at a particular time The operation supplies... the delivery of a quantity products and services when required Figure 12.1 This chapter covers inventory management Key questions What is project management? How are projects managed and controlled? What is network planning? All processes, operations and supply networks have inventories Table 12.1 Examples of inventory held in processes, operations or supply networks ‘Inventories’ Process, operation or supply network Physical inventories Queues of customers Information in databases Hotel Food items, drinks, toilet items At check in and check out Customer details, loyalty card holders, catering suppliers Hospital Dressings, disposable Patients on a waiting list, Patient medical records instruments, blood patients in bed waiting for surgery, patients in recovery wards Credit card Blank cards, form letters Customers waiting on the Customer’s credit and application process phone personal information Computer Components for assembly, Customers waiting for delivery Customers’ details, supplier manufacturer packaging materials, finished of their computer information computers ready for sale All processes, operations and supply networks have inventories (continued) Input Inventory Output process process Rate of supply from input process Inventory Rate of demand from output process Figure 12.2 Inventory is created to compensate for the differences in timing between supply and demand. Why should there be any inventory? Table 12.2 Some reasons to avoid inventories Inventories Reason to avoid Physical inventories Queues of customers Digital information in databases Cost Ties up working capital and Primarily time-cost to the Cost of set-up, access, update there could be high customer, i.e. wastes customers’ and maintenance administrative and insurance time. costs. Space Requires storage space. Requires areas for waiting or Requires memory capacity. May phone lines for held calls. require secure and/or special environment. Quality May deteriorate over time, May upset customers if they Data may be corrupted or lost or become damaged or obsolete. have to wait too long. May lose become obsolete. customers. Operational/ May hide problems (see lean May put undue pressure on the Databases need constant organisational synchronisation – Chapter 15). staff and so quality is management; access control, compromised for throughput. updating and security. So, why have inventory? Produce A Produce B Produce C Produce A Produce B Produce C Inventory level Deliver A Deliver B Deliver C Deliver A Deliver B Deliver C Time Figure 12.3 Cycle inventory in a bakery Reducing physical inventory Table 12.3 Some ways in which physical inventory may be reduced Reason for holding Example How inventory could be inventory reduced As an insurance Safety stocks for when demand or Improve demand forecasting against uncertainty supply is not perfectly predictable Tighten supply, e.g. through service level penalties To counteract a lack Cycle stock to maintain supply Increase flexibility of of flexibility when other products are being processes, e.g. by reducing made changeover times (see Chapter 11) Using parallel processes producing output simultaneously (see Chapter 7) To take advantage of Suppliers offer ‘time limited’ Persuade suppliers to adopt relatively short-term special low cost offers ‘everyday low prices’ (see opportunities Chapter 13) To anticipate future Build up stocks in low demand Increase volume flexibility by demands periods for use in high demand moving towards a ‘chase periods demand’ plan (see Chapter 11) Reducing physical inventory (continued) Table 12.3 Some ways in which physical inventory may be reduced (continued) Reason for holding Example How inventory could be inventory reduced To reduce overall Purchasing a batch of products in Reduce administration costs costs order to save delivery and through purchasing process administration costs efficiency gains Investigate alternative delivery channel that reduce transport costs. To fill the processing Items being delivered to customer Reduce process time between ‘pipeline’ customer request and dispatch of items Reduce throughput time in the downstream supply chain (see Chapter 13) The effect of inventory on return on assets Ability to supply Obsolescence, Storage from stock damage, loss costs Ordering costs Profit Revenues Costs Return on Assets = = Total assets Working capital + Fixed assets Amount you owe Amount customers Cost of funding suppliers owe you inventory Figure 12.4 Inventory management has a significant effect on return on assets. Inventory profiles Steady and Order predictable quantity = Q demand (D) Slope = demand rate Inventory level Average Q inventory = 2 Q Time D D Instantaneous deliveries at a rate of Q per period Figure 12.5 Inventory profiles chart the variation in inventory level. The economic order quantity (EOQ) formula Demand (D) = 1,000 items per year 400 Plan A Inventory level Q = 400 Average inventory for plan A = 200 Plan B Q = 100 Average inventory 100 for plan B = 50 Time 0.1 yr 0.4 yr Figure 12.6 Two alternative inventory plans with different order quantities (Q) The economic order quantity (EOQ) formula (continued) Table 2.4 Cost of adoption of plans with different order quantities Demand (D) = 1 000 units per year Holding costs (Ch) = R1 per item per year Order cost (Co) = R20 per order Order quantity Holding costs + D costs Order = Q Total costs (Q) (0.5 Ch) Co 50 25 20 20 = 400 425 100 50 10 20 = 200 250 150 75 6.7 20 = 134 209 200 100 5 20 = 100 200* 250 125 4 20 = 80 205 300 150 3.3 20 = 66 216 350 175 2.9 20 = 58 233 400 200 2.5 20 = 50 250 * Minimum total cost The economic order quantity (EOQ) formula (continued) 400 350 300 Total costs 250 Costs 200 150 Holding costs 100 Order costs 50 Economic order quantity (EOQ) 50 100 150 200 250 300 350 400 Order quantity Figure 12.7 Graphic representation of the economic order quantity Gradual replacement – the economic batch quantity (EBQ) model Order quantity Q Inventory level Slope = P D Slope = D M Time Q P Figure 12.8 Inventory profile for gradual replacement of inventory Using EOQ models as prescriptions Revised total costs Revised holding costs Original total Costs costs Original holding costs Original order costs Revised order costs 50 100 150 200 250 300 350 400 Revised EOQ Original EOQ Order quantity Figure 12.9 If the true costs of stock holding are taken into account, and if the cost of ordering (or changeover) is reduced, the economic order quantity (EOQ) is much smaller. Sappi – perfect paper supply for every need Figure 12.10 The role of the paper merchant When to place an order – the timing decision Demand (D) = 100 items per week 400 Order quantity (Q) = 400 Inventory level Re-order level 300 Re-order point 200 100 0 0 1 2 3 4 5 6 7 8 Time Order lead time Figure 12.11 Re-order level (ROL) and re-order point (ROP) are derived from the order lead time and demand rate. When to place an order – the timing decision (continued) Re-order level (ROL) Distribution of Inventory level lead-time Q usage d1 d2 s t1 t2 Time Figure 12.12 Safety stock(s) helps to avoid stock-outs when demand and/or order lead time are uncertain. Lead-time usage distribution 0.4 0.4 Probability Probability 0.3 0.3 0.2 0.2 0.1 0.1 0 0 1 2 3 4 5 110 120 130 140 Order lead time Demand rate 0.4 Probability 0.3 0.2 0.1 0 100–199 120–299 300–399 400–499 500–599 600–699 700–799 Lead-time usage Figure 12.13 The probability distributions for order lead time and demand rate combine to give the lead-time usage distribution. Continuous and periodic review Qm Q1 Q2 Q3 Inventory level T0 T1 T2 T3 Time t1 t2 t3 tf tf tf Figure 12.14 A periodic review approach to order timing with probabilistic demand and lead time Two-bin and three-bin systems Two-bin system Three-bin system Bin 1 Bin 2 Bin 1 Bin 2 Bin 3 Items being Reorder level + Items being Reorder level Safety used safety used inventory inventory inventory Figure 12.15 The two-bin and three-bin systems of re-ordering Case study: supplies4medics.com Chapter 12 ‘end-of-chapter’ case Questions 1. Prepare a spreadsheet-based ABC analysis of usage value. Classify as follows: a) A-Items: top 20% of usage value b) B-Items: next 30% of usage value c) C-Items: remaining 50% of usage value. 2. Calculate the inventory weeks for each item, for each classification, and for all the items in total. Does this suggest that the Pierre Laroche’s estimate of inventory weeks is correct? 3. If so, what is your estimate of the overall inventory at the end of the base year, and how much might that have increased during the year? Case study: supplies4medics.com (continued) Chapter 12 ‘end-of-chapter’ case Questions 1. Based on the sample, analyse the underlying causes of the availability problem described in the text. 2. Calculate the EOQs for the A-items. 3. What recommendations would you give to the company? Case study: supplies4medics.com (continued) Last 12 Inventory Catalogue Sales unit Re-order Sample months’ as at last reference Sales unit description ** cost quantity number Sales year end number* (Euro) (units) (units) (units) 1 11036 Disposable aprons (10 pk) 2.40 100 0 10 2 11456 Ear-loop masks (box) 3.60 6 000 120 1 000 3 11563 Drill type 164 1.10 220 420 250 4 12054 Incontinence pads large 3.50 35 400 8 500 10 000 5 12372 150 ml syringe 11.30 430 120 100 6 12774 Rectal speculum 3-prong 17.40 65 20 20 7 12979 Pocket organiser blue 7.00 120 160 500 8 13063 Oxygen trauma kit 187.00 40 2 10 9 13236 Zinc oxide tape 1.50 1 260 0 50 10 13454 Dual head stethoscope 6.25 10 16 25 11 13597 Disp. latex catheter 0.60 3 560 12 20 12 13999 Roll-up wheelchair ramp 152.50 12 44 50 13 14068 Lavage tube 1.40 22 500 10 500 8 000 14 14242 Cervical collar 12.00 140 24 20 15 14310 Head wedge 89.00 44 2 10 Table 12.10 16 14405 Three-wheel scooter 755.00 14 5 5 Representative 17 14456 Neonatal trach. tube 80.40 268 6 100 18 14675 Mouldable strip paste 10.20 1 250 172 100 sample of 20 19 14854 Sequential comp. pump 430.00 430 40 50 catalogue 20 24943 Toilet safety frame 25.60 560 18 20 Items * Reference numbers are allocated sequentially as new items are added to catalogue. ** All quantities are in sales units (e.g. item, box, case, pack).