Coke Ovens And Coal Chemicals PDF
Document Details
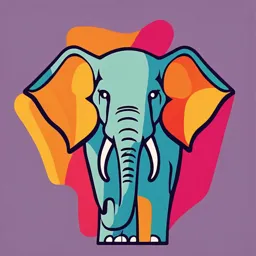
Uploaded by PraisingCerium
Tags
Summary
This document discusses coke ovens and coal chemicals, covering topics like coke making, coal formation, and classification of coking coals. It also details the properties of coking coal, including ash content, volatile matter, swelling index, fluidity, and inherent moisture. The document also touches upon coal handling plants and the importance of crushing and blending in the context of coal processing. It further elaborates on the carbonization process and its relation to coke production, and the significance of coke size in the blast furnace. Finally, the document briefly describes coal chemicals, pollution control norms, equipment, and safety measures.
Full Transcript
Chapter – 2 COKE OVENS AND COAL CHEMICALS 2.1 Introduction Coke making is the process to convert coking coal, through a series of operations, into metallurgical coke. The process starts from unloading of the coal at the wagon tipplers & ends at sizing & transportation of coke to Blast furnace. Forma...
Chapter – 2 COKE OVENS AND COAL CHEMICALS 2.1 Introduction Coke making is the process to convert coking coal, through a series of operations, into metallurgical coke. The process starts from unloading of the coal at the wagon tipplers & ends at sizing & transportation of coke to Blast furnace. Formation of Coal: The plant & vegetations buried under swamp bottom during earthquakes or due to other environmental changes were subjected to heat & pressure. During the initial period plant & vegetations decay to form PEAT. Over a long period of time water is forced out due to tremendous pressure of the overburden & due to heat generation, converting the mass to LIGNITE. Continuous compaction & ageing converts the Lignite to Bituminous coal. This process takes million of years. Types & Sources of Coking Coal: Coals are primarily divided into two categories i.e. coking coals and non coking coals. Coking coals are mainly used in steel industries for coke making. Indigenous coking coals are classified as: Prime Coking Coal (PCC) Medium Coking Coal (MCC) While imported coking coals are classified as. Hard coking coals (HCC) Soft Coking Coal (SCC) Coal is extracted from coal mines & processed in the coal washeries to lower down the ash content to make it fit for coke making. The different sources of Indigenous coking coal are named after the respective washeries while imported coking coals are named after the name of countries and are as follows in next page: PCC - Bhojudih - Sudamdih - Munidih - Patherdih - Dugda - Mahuda -Chasnala - Jamadoba - Bhelatand MCC - Kathara - Swang - Rajrappa - Kedla - Nandan - Dahibari 18 ICC (Hard) – Australia - USA -Mozambique Benga) - Indonesia - Canada 2.2 SCC -Australia -USA Properties of Coking Coal Percentage of Ash: Lower the ash percentage better is the coal. Indian coal normally contains a high percentage of ash. This is reduced to some extent by suitable beneficiation process at the washeries. Volatile Matter (VM): This is the volatile matters present in the coal which goes out as gas during carbonization. Free Swelling Index (FSI): The free- swelling index is measure of the increase in volume of coal when heated under specific conditions. It is also known as Crucible swelling number (CSN) Low Temperature Gray King coke Type (LTGK): The purpose of the test is to assess the caking properties of coal or coal blend and the yield of the various byproducts during carbonization. Gieseler Fluidity: This test measures the rheological properties of coal. This test tells about the initial softening temperature, temperature at which maximum fluidity occurs, Plastic range, maximum fluidity and re-solidification temperature. This is expressed in dial division per minute (DDPM). This test tells about the compatibility of different coals in coal blend. Inherent Moisture: This gives a very good idea about the maturity of the coal with advancement of rank the inherent moisture generally comes down. Mean Max Reflectance (MMR): Rank of coal is determined by measuring the reflectance of coal, which is determined by MMR value. MMR is directly proportional to the strength of COKE. Table -1: Properties of incoming Indigenous and Imported coking coals Coal Ash VM FSI LTGK MMR >E >E >G4 Inherent moisture < 1.5 < 1.5 < 1.5 PCC MCC Imported Soft Aust Hard USA Hard Mozambique (Benga) Indonesia Hard 19 - 23 20 – 25 8-10 21-23 23-25 25-30 >2.0 >1.0 >5.0 8-10 8-10 12 - 14 18-20 24-26 24-26 >5.0 >5.0 >5.0 >G4 >G4 >G4 < 1.5 < 1.5 < 1.5 1.25 1.10 1.15 10-12 24-26 >5.0 >G4 < 1.5 1.10 19 1.10 0.85 0.9 2.3 Coal Handling Plant Coke is one of the most important raw materials used to extract iron from the iron ore. The success of Blast Furnace operation depends upon the consistent quality of coke, which is used in Blast Furnace. The quality of coke depends upon the pre-carbonisation technique, carbonization & post-carbonization techniques used in Coke ovens. Pre-carbonization technique is controlled by Coal handling Plant. Unloading & lifting of coal: Washed coals from washeries are received at the Coal Handling Plant by Railways wagons. Generally 59 wagons, called a rake, are brought to the plant at a time. These wagons get unloaded in wagon tipplers. Here the wagons are mechanically clamped & turned up to 172° to discharge the coal onto down below conveyors. Then through a series of conveyors the coal is stacked in coal yard through a Stacker or directly to the silos by tripper car. The coal yard is divided into separate segments where different types of coal can be stacked in respective earmarked areas. It is very important to stack different types of coal separately so as to avoid mix up of two types of coal. Mix up of coal is highly detrimental for coke making. From the coal yard, coal is reclaimed through Reclaimer & by a series of conveyors gets transported to either crushers or silos as per prevailing system in different SAIL plants. In some plants, coal from different sources are tippled and carried by conveyors directly to the silos. Care is taken to load same grade of coal in the same silos, from where it is taken through weigh feeders to the hammer crushers and then the entire blended coal is transported to different coal towers by conveyors. Crushing & Blending: The sequence of crushing & blending is different in different SAIL plants. The system of crushing the coal & then blending is followed in RSP, whereas blending is done before crushing in other SAIL Plants. Importance of Crushing: Coal is a heterogeneous mixture of organic and inorganic materials. Finer crushing of good coal leads to increase in specific surface area of coal grains which will increase the quantity of plastic material required for wetting and enveloping the inert material. Courser crushing of inferior coals leads to generation of courser particles which are centers of weakness in coke matrix. Due to difference in the plastic and shrinkage behavior of these inert rich particles and rest of the charge, local stresses are developed and cracks appear adversely affecting coke quality. Crushing should ensure minimum differences between different size fractions. Organic materials-rich particles are softer than those of inorganic-rich or ash-rich particles. Ash or inerts content is higher in larger size particles (>5 mm size) and such particles needs finer crushing The mineral matter/inert reach component should be crushed to finer sizes compared to the reactive component for even dispersion of inert particles in the coal charge. Fine crushing of coal is essential to homogenize the different inherent constituents of coal blend. Crushing of coal is done by hammer crusher. Crushing also influence the bulk density of coal charge in 20 the ovens. Bulk density is the compactness or close packing of the coal charge in the oven. Higher the bulk density better is the coke strength. It is desirable to have 80% to 82% of -3.2mm size coal after crushing. This is known as crushing Index. However over crushing is not desirable as this reduces the bulk density & increases micro fines which cause jamming in gas off-take system. Fig : Bulk density variation with Crushing Index and +6.3 mm content in coal charge Importance of Blending: Different coal has different properties. Some coals may be good in coking properties but high ash and poor rank while others may have low ash and desired rank but poor coking properties. These properties are additive in nature except Fluidity. As evidenced from the table under properties of coal the Indigenous coals contain a relatively higher percentage of ash and poor coking properties & Imported coals contain a relatively lower percentage of ash and better coking properties. Hence blending of both types of coal is necessary for obtaining the desired quality of coal blend. Blending plays a vital role in producing good metallurgical coke. Blending is a process of mixing the different types of coal, i.e. PCC, MCC, Imported Soft & Hard, in different percentage to obtain the desired quality of the blend coal. However blending is to be done in a very accurate manner so that required coke property does not get adversely affected. Blending is generally done by adjusting the discharge of different types of coal from bunkers or silos to a common belt. The different type of coals gets thoroughly mixed during crushing where blending is done before crushing. In case where blending is done after crushing proper mixing takes place at several transfer points, i.e. during discharge from one conveyor to another conveyor through a chute, during transportation to coal towers or service bunkers. 21 COAL BLEND QUALITY: ASH VM MMR SULPHUR FSI MAXIMUM FLUIDITY MOISTURE 2.4 12% max 23 - 25% 1.15 to 1.20 < 0.7 % 5 to 6 300 to 600 7 to 9 % Carbonization Process The process of converting blend coal to metallurgical coke is known as carbonization. It is defined as heating the coal in absence of air. It is also the destructive distillation of coal. The carbonization process takes place in a series of tall, narrow, roofed chambers made of refractory bricks called ovens. A specific number of ovens constitute a Battery. The ovens are mechanically supported by Structural & Anchorage. A battery can be classified as per size & design. The most common classifications are: a. Tall Battery Small Battery – 7.0 m height. – 4.5/5.0 m height. b. Recovery type battery – Gas evolved during carbonization is collected and cleaned at byproduct plant. This clean gas is then used as a fuel gas throughout the Plant. Different chemicals are extracted as by-products during cleaning of gas. Non-Recovery type battery – No by products are formed as the generated gas acts as the fuel. c. Top charge battery – Conventional battery with charging from the top. The charging cars (machine that takes coal from coal tower to charge the ovens) run over the oven top and discharge the coal into the ovens through charging holes on the oven top. Stamp charged battery – A cake like mass is formed by ramming the coal and is charged by pushing the cake into the oven from Pusher/Ram side. Blend coal from coal tower is charged from top to the ovens. Each oven is sandwiched between two heating walls from which heat is transmitted to the coal charge inside the oven. When coal is charged inside an oven, it gets heated up to form a plastic mass which re-solidifies to form coke near the heating walls. The heat passes to the next layer of coal and so on till they meet at the center. During the process of carbonization the coal charge first undergo de-moisturisation (drying) upto a temperature of 250°C. Then it starts to soften at around 300°C. It then reaches a plastic or swelling state during 350°C to 550°C. The entrapped gasses are then driven out at 400°C to 700°C. The calorific value (CV) of Coke ovens gas is around 4300 kcal/m3.The gas is cooled to 800C by ammonia liquor/ flushing liquor. The mass inside the oven then re-solidifies (shrinkage) beyond 700°C. Finally coke is produced as a hard & 22 porous mass at around 1000°C.The total time taken for full carbonization is called coking time or coking period. The hot coke is then pushed out from the ovens. The hot coke is then cooled by water spray or dry nitrogen purging. This process is called quenching of coke. Generally coke is cooled by water spray for a period of 90 seconds and termed as quenching time. The cooled coke is then sent to Coke Sorting Plant for proper sizing & then to Blast Furnace. Major Equipments: Major equipment’s/machines used in the process of coke making are: Charging car: It collects the blended coal from coal tower & charges to empty ovens. Pusher Car or Ram Car: Its functions are to level the charged coal inside the oven during charging & to push out the coke mass from inside the oven after carbonization. Coke Guide Car: It guides the coke mass during pushing to the Quenching car. Quenching Car: It carries the hot coke to quenching tower & dumps the coke in the wharf after cooling. These machines have a lot of mechanical and electrical engineering devices in them. They have hydraulic operating systems run by VVFD (Variable voltage and variable frequency drive) drives controlled by PLC (Programmable Logical Controller) system. They are connected by radar based communication system which involves state of art technology. Quenching of Coke: There are two method of quenching the hot coke: 1. Wet Quenching: This is the conventional quenching system, where the red hot coke is cooled by spraying it with water (phenolic water / BOD water). The coke thus produced contains around 5% of moisture. 2. Dry Quenching: In this system, the red-hot coke is discharged into a closed chamber, where it is cooled by purging nitrogen into it. The sensible heat of the hot coke is recovered to produce steam. The coke thus produced contains around 0.2% of moisture and is of good quality. COKE SORTING PLANT: The coke, after wet quenching is dumped from the quenching car to a long inclined bed called wharf. The Quenching car operator should dump the quenched coke uniformly on the wharf from one end to the other. Quenched coke should be allowed to remain in the wharf for about 20 minutes (retention time) so that the heat remained inside the coke comes out & evaporates the surface moisture. To maintain this retention time, wharf is to be emptied out from one side & gradually progressing to the other side. If any hot coke remains after quenching, then they are cooled by manual water spray and is known as spot quenching. However this spot quenching is undesirable as it increases the moisture content in coke. The cooled coke is then taken to an 80 mm screen. The +80mm coke fractions are sent to coke cutter / crusher to bring down the size. The hard coke of size +25mm to -80mm size are then segregated to send to Blast Furnace. Coke fraction of +15mm to -25mm, which is called Nut coke, is also segregated & sent to Sintering Plants. The -15mm fractions, called fine breeze or breeze coke, are also sent to Sintering Plants. 23 In case of dry quenching, the coke is discharged from the chamber and passes through the same process of sizing and screening. 2.5 PROPERTIES OF COKE ASH: Ash in coke is inert & becomes part of the slag produced in the Blast Furnace. Hence, ash in coke not only takes away heat but also reduces the useful volume of the furnace. Hence it is desirable to have lower ash content in the coke. The desired ash content is less than 15%. VOLATILE MATTER (VM): The VM in coke is an indicator of completion of carbonization & hence the quality of coke produced. It should be as low as possible, i.e. < 1% GROSS MOISTURE (GM): It has got no role to play in the furnace. It only takes away heat for evaporation. Hence least moisture content is desirable. However during water quenching certain amount of moisture is inevitable. A level around 4.5% is desirable. MICUM INDEX: Micum index indicates the cold strength of coke. M10 value indicates the strength of coke against abrasion. Lower the M10 value better is the abrasion strength. A M10 value of around 8.0 indicates good coke strength. M40 value indicates the load bearing strength or strength against impact load. Coke having lower M40 value will crumble inside the furnace which will reduce the permeability of the burden and cause resistance to the gasses formed in the furnace to move upwards. A good coke should have a M40 value more than 80. COKE REACTIVITY INDEX(CRI): Coke reactivity determines percent weight loss of coke, as a result of carbon dioxide action on the coke at temperature 1100℃. It is the capacity of the coke to remain intact by withstanding the reactive atmosphere inside the furnace. Hence less the CRI value, better is the coke. Desirable value should be in the range of 21 - 24. COKE STRENGTH AFTER REACTION (CSR): It denotes the strength of the coke after passing through the reactive environment inside the furnace. CSR for a good coke should be in range of 64-66. It is also known as hot strength of coke. CRI &CSR are also known as hot strength of coke. 24 COKE SIZE: The size of coke is most important to maintain permeability of the burden in the furnace. The required size for Blast Furnace is more than 25mm size & less than 80mm size. If the undersize is more the permeability decreases as smaller coke pieces fill up the voids & increase the resistance to the flow of outgoing gasses. If the oversize is more the surface area of coke for the reactions reduces. Hence the size of the coke is to be maintained between +25mm & -80mm ROLE OF COKE IN THE BLAST FURNACE: Coke plays a vital role in Blast Furnace operation. For stable operation of the furnace, consistent quality of coke is most important. Variation in coke quality adversely affects the Blast Furnace chemistry. The roles of coke in Blast Furnace are: It acts as a fuel. It acts as a reducing agent. It supports the burden inside the furnace. It provides permeability in the furnace. 2.6 Coal Chemicals Process of heating coal in absence of air to produce coke is called coal carbonization or destructive distillation. Purpose of coal carbonization is to produce coke whereas co-product is coke oven gas. From coke oven gas, various by products like tar, benzol, naphthalene, ammonia, phenol, anthracene etc. are produced. Generally high temperature coal carbonization is carried out in coke oven battery of integrated steel plants at temp of 1000-1200 deg. Centigrade. In the by-product plant major byproducts like tar, ammonia and crude benzol are recovered from the coke oven gas evolved during coal carbonization. The output of the gaseous products, their composition and properties depend on the coal blend used for coking, the heating regime & the operating condition of the battery. Tar separated out of coke oven gas as a mixture of large quantities of various chemical compounds. From tar, a number of products are separated in the tar distillation plant which have market demand. Among the tar products, naphthalene is the costliest item & its yield is 50-55 % of the tar distilled. Other tar products are road tar, Anthracene, pitch creosote mixture, medium hard pitch & extra hard pitch etc. Ammonia in the coke oven gas is recovered as Ammonium sulphate, which is used as a fertilizer in agriculture sector. Output of crude benzol depends on the V.M content in the coal blend and temperature of coking. Light crude benzol is rectified in benzol rectification plant and the benzol products obtained are benzene, toluene, xylene, solvent oil etc. Yield of benzol products varies from 86-88% of the crude benzol processed. The by products recovered in the process are very important and useful.Tar is used for road making and as fuel in furnaces. Pitch is used for road making. The benzol products like benzene, toluene, phenol, naphthalene and xylene etc. are important inputs for chemical industries producing dyes, paint, pharmaceutical, insecticide, detergent, plasticiser and leather products. 25 The coke oven gas from Coke ovens contain lot of impurities, which needs to be properly cleaned before being used as a fuel gas for Coke Oven heating as well as elsewhere in Steel Plant. The impurities in coke oven gas are mainly tar fog, ammonia, naphthalene, hydrogen sulphide, benzol, residual hydrocarbon and traces of HCN. Cleaning of coke oven gas is done by passing it through a series of coolers & condensers and then treating the gas in ammonia columns, saturators, washers, tar precipitators, naphthalene washers, benzol scrubbers etc. for removal of these impurities. After the cleaning operation, the final coke oven gas still contains traces of impurities. Quality of coke oven gas depends on the contents of various impurities and its heat value. Typical analysis of impurities in good quality coke oven gas is as follows:-Tar fog: 30 mg/Nm³ ± 10mg, Ammonia- 30 mg/Nm³ ± 10mg, Napthalene- 250mg/Nm³ ± 50mg, Hydrogen Sulphide- 200 mg/Nm³ ± 50mg, HCN- Traces, CnHm- 1.5 to 2.5%. 2.7 By Products Plants of Coke Ovens The Gas generated in the Coke oven batteries during carbonization process is handled and cleaned in the By Product Plant. During the process of cleaning the gas some By Products are separated out and clean Gas is used as fuel in the plant. Following process are involved in cleaning the gas. TAR AND LIQUOR PROCESSING PLANT The tar and liquor processing plant process the flushing liquor that circulates between the by product plant and the coke oven battery. It also processes the waste water that is generated by the coke making process and which results from coal moisture and chemically bound water in the coal. The main functions of these plants are as follows: Continuous rapid separation of a suitable flushing liquor streams. This is the very important function since flow is needed to cool the hot oven exit gases down to a temperature which can be handled in the gas collecting system. Separation of a clean and tar free excess ammonia liquor for further processing. Separation of clean tar essentially free from water and solids. Since the flushing liquor supply is very important, stand by equipment are normally provided for flushing liquor decanting and recirculation. The flushing liquor flows into tar decanters where the tar separates out from the water and is pumped to tar storage for processing in tar distillation plant. Heavier solid particles separate out from the tar layer and these are removed as tar decanter sludge. The aqueous liquor is then pumped back to the battery, with a portion bled off from the circuit which is the coke plant excess liquor or waste water. This contains ammonia and after the further removal of tar particles, it is steam stripped in a still. PRIMARY GAS COOLER After separation of tar and ammonia liquor from gas, gas is fed into gas cooler where temperature of gas is lowered down by means water sprinkling. Primary gas cooler are two basic types, the spray type cooler and the horizontal tube type. In spray type cooler the coke oven gas is cooled by direct contact with recirculated water spray. As the coke oven gas is cooled, water, naphthalene and tar condensed 26 out. The condensate collects in the primary cooler system and is discharged to the tar and liquor processing plant. ELECTROSTATIC TAR PRECIPITATOR As the raw coke oven gas is cooled, tar vapour condenses and forms aerosols which are carried along with the gas flow. These tar particles contaminate and foul downstream processes and foul gas lines and burner nozzles if allowed to continue in downstream. The tar precipitator typically uses high voltage electrodes to charge the tar particles and then collect them from the gas by means of electrostatic attraction. The Tar precipitator can be installed before or after the exhauster. EXHAUSTER Exhausters are installed which sucks the gas generated in the batteries and sends to the desired destination for further processing. Another function of the exhauster is to maintain steady suction as per requirement so as to maintain the hydraulic main or gas collecting main (GCM) pressure. The exhauster is of prime importance to the operation of the coke oven battery. It allows the close control of the gas pressure in the collecting main, which in turn affects the degree of emission in the battery like door emission. A failure of the exhauster will immediately result in venting to atmosphere all the generated the raw coke oven gas through the battery flares / bleeder. AMMONIUM SULPHATE PLANT (ASP) Due to the corrosive nature of ammonia, its removal is very much necessary in by-products plants. The removal of ammonia from coke oven gas results into yield of ammonium sulphate. The ammonium sulphate processes are basically involves contacting the coke oven gas with solution of sulphuric acid. Raw coke oven gas from Exhauster outlet is passed through the saturators filled with Sulphuric Acid (H2SO4), where ammonia present in the gas is precipitated in the form of ammonium sulphate. Acidity of the saturator liquor is maintained at 3 % to 5 %. This ammonium sulphate is sold as Fertilizer. FINAL GAS COOLER (FGC) Final gas cooler removes the heat of compression from the coke oven gas which it gains while flowing through the exhauster. This is necessary since the efficiency of many of the by-product plant processes greatly improved at lower temperature. Gas coolers typically cool the coke oven gas by direct contact with a cooling medium. BENZOL RECOVERY PLANT (BRP) Benzol present in the raw coke oven gas is removed in this unit. The gas is passed through solar oil / Wash oil in the scrubbers. The benzol gets absorbed in the oil. Benzol rich oil is fed to distillation unit where oil and crude benzol are separated. The oil is reused in the scrubbers. The clean coke oven gas is used by the consumers through gas net work maintained by Energy Management Department. NAPTHALENE REMOVAL Naphthalene is removed from coke oven gas in a gas scrubbing vessel using wash oil. The vessel can be of packed type and it can be of the void type in which the wash oil is sprayed into the gas in several stages. 27 BENZOL RECTIFICATION PLANT Light crude benzol from benzol recovery plant is further processed in this unit and following by products are recovered: a. b. c. d. Benzene Toluene Xylene Carbon di-Sulphide (CS2) TAR DISTILLATION PLANT (TDP) Tar recovered from GCPH is further processed in TDP. The main products of TDP are: (a) Tar (b) Pitch (c) Pitch Creosote Mixture ( PCM ) (d) Naphthalene (e) Anthracene oil ACID PLANT Sulphuric acid is produced in acid plant by DCDA (Double Conversion Double Absorption) process. In this process sulphur is converted to Sulphur tri oxide (SO3) in presence of catalyst Vanadium pentoxide (V2O5) and then to Sulphuric acid. This acid is used in Ammonium Sulphate plant for removal of ammonia from raw coke oven gas. PETP / BOD PLANT In Phenolic Effluent Treatment Plant (PETP) or Biological Oxygen Demand (BOD) Plant, the contaminated water generated from whole of coke oven is treated to make it clean from the effluents with the help of Bacteria. The treated water is then used for quenching hot coke in the quenching towers. The norms for different effluent after treatment at BOD plant are: Ammonia Phenol Cyanide Tar & Oil : : : : 50 ppm 1 ppm 0.2 ppm 10 ppm Coke Oven Gas (CO Gas): The most important byproduct of Coke oven is the raw Coke oven gas. The basic constituents of clean coke oven gas are: Hydrogen 50 to 60% Methane 25 to 28% Carbon Monoxide 6 to 8% Carbon Dioxide 3 to 4% Other Hydrocarbons 2 to 2.5% Nitrogen 2 to 7% Oxygen 0.2 to 0.4% Calorific value 4300 kcal / m3 28 PROCESS FLOW DIAGRAM OF COKE OVEN & CCD Washed Coal from Washeries Wagons Wagon Tippler Unloading of coal Coal Yard / Silos Reclaiming Crusher Crushing & Blending Coal Tower +25 to -80 Hard Coke Batteries (Carbonization) Coke Sorting Plant B.F. +15 to -25 Nut Coke S.P. -15 Raw CO Gas Coke Breeze By Product Plant S.P. Tar Clean CO Gas Benzol (BTX) Ammonium Sulphate Naphthalene 29 Extra hard pitch Wash oil Anthracene oil Carbolic oil Light oil 2.8 Pollution Control Norms To protect the environment, Central Pollution Control Board (CPCB) has laid down strict pollution control norms. The different norms for coke ovens with respect to PLD (Percentage Leaking Doors), PLO (Percentage Leaking Off take), PLL (Percentage Leaking Lids) and Stack Emission are as follows: FACTORS PLD PLL PLO SO2 Stack Emission Charging Emission NEW BATTERY 5 1 4 800 mg/Nm3 50 mg/Nm3 16 sec/charge EXISTING BATTERY 10 1 4 800 mg/Nm3 50 mg/Nm3 50 sec/charge ISO 14001: 2004 is an environment management system which deals with the ways and means to make the environment pollution free. Its main thrust is to make Land, Air & Water free of pollutants. 2.9 Safety Safety is the single most important aspect in the steel industry. This aspect covers both personal as well as equipment safety. The use of PPE s (Personal Protective Equipment) is a must for the employees in the shop floor. The use of PPEs like safety helmet, safety shoes, hand gloves, gas masks, heat resistant jackets, goggles and dust masks are to be used religiously while working in different areas of coke ovens. Different laid down procedures like EL 20 / permit to work, as followed in different steel plants, are to be strictly followed before taking any shut-down of equipment for maintenance. The stipulated SOPs (Standard Operating Procedure) and SMPs (Standard Maintenance Procedure) should be adhered to strictly. Persons should be cautious about the gas prone areas and should know about the gas hazards. EMD clearance is a must before taking up any job in gas lines or gas prone areas. A life lost due to any unsafe act is an irreparable loss to the company as well as to the family which can not be compensated. 5-S SYSTEM (WORK PLACE MANAGEMENT): 5 S system is an integrated concept originated by the Japanese for proper work place management. Takasi Osada, the author of this concept says 5 s activities are an important aspect of team work applicable to all places. 30 1 S : s e i r i – It is the process of distinguishing, sorting & segregation between wanted & unwanted items in a work place & removal of the unwanted. 2 S : s e i t o n – It is the process of systematic arrangement of all items in a suitable place. 3 S : s e i s o – It is the process of proper house keeping of the work place including equipments. 4S:seikestu– cleaning of all It is the process of standardization 5 S : s h i t s u k e – Literal meaning of shitsuke is discipline. It is the process of following the system meticulously. 2.10 ISO45001:2018 (Occupational Health and Safety Management System: OH&SMS provides a formalized structure for ensuring that hazards are identified, their impact on staff assessed and appropriate controls put in place to minimize the effect. It further assists a company in being legally compliant, ensuring appropriate communication and consultation with staff, ensuring staff competency and having arrangements in place to deal with foreseeable emergencies. It is not concerned with the safety of the product or its end user. It is compatible with the established ISO 9001(Quality) and ISO 14001 (Environmental) management system standards. This helps to facilitate the integration of the quality, environmental and occupational health and safety management systems within the organization. Impacts of fully implemented OH&SMS are: (a) (b) (c) (d) (e) (f) Risks and losses will be reduced and/or eliminated Reduced accidents, incidents and costs Reliable operations Compliance to rules, legislation, company standards and practices A systematic and efficient approach to health and safety at work Positive company image and reputation --- 31