Building Materials & Testing Past Exam Paper PDF 2019-2020
Document Details
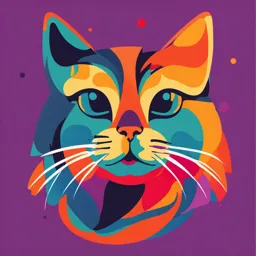
Uploaded by ArtisticMolybdenum
University of Halabja
Rabar H.A Faraj
Tags
Related
- Tema 6 Materiales PDF
- Building Technology 4 - Estimates Part 1: Concrete and Masonry PDF
- Module III Concrete Hollow Blocks PDF
- Construction Materials and Equipment Ch-1 part 2&3 PDF
- Construction Materials and Equipment Ch-1 part 1 PDF
- Coconut Husk Ash for Improved Thermal Insulation in CHB Wall Plaster - 2024
Summary
This document is a chapter from a book or lecture notes about building materials and testing, focusing on concrete blocks. It details the background, raw materials, manufacturing process, curing, form and size, different types of concrete blocks, and their properties. The text is part of a course at the University of Halabja, for first-year civil engineering students, and was delivered in 2019-2020.
Full Transcript
University of Halabja Course Name: Building Materials & Testing Civil Engineering Department Course Code: 1st Year Students Date / 2021...
University of Halabja Course Name: Building Materials & Testing Civil Engineering Department Course Code: 1st Year Students Date / 2021 : Lecturer: Rabar H.A Faraj 2019-2020 CHAPTER FOUR Blocks BACKGROUND: A concrete block is primarily used as a building material in the construction of walls. It is sometimes called a concrete masonry unit. A concrete block is one of several precast concrete products used in construction. The term precast refers to the fact that the blocks are formed and hardened before they are brought to the job site. Most concrete blocks have one or more hollow cavities, and their sides may be cast smooth or with a design. In use, concrete blocks are stacked one at a time and held together with fresh concrete mortar to form the desired length and height of the wall. The first hollow concrete block was designed in 1890 by Harmon S. Palmer in the United States. After 10 years of experimenting, Palmer patented the design in 1900. Palmer's blocks were 8 in (20.3 cm) by 10 in (25.4 cm) by 30 in (76.2 cm), and they were so heavy they had to be lifted into place with a small crane. By 1905, an estimated 1,500 companies were manufacturing concrete blocks in the United States. 1 RAW MATERIALS: The concrete commonly used to make concrete blocks is a mixture of powdered portland cement, water, sand, and gravel. This produces a light gray block with a fine surface texture and a high compressive strength. Concrete masonry units are manufactured in three classes, based on their density: lightweight units, medium-weight units, and normal-weight units, with dry unit weights as shown in Table. Well-graded sand, gravel, and crushed stone are used to manufacture normal-weight units. Lightweight aggregates such as pumice, scoria, cinders, expanded clay, and expanded shale are used to manufacture lightweight units. Lightweight units have higher thermal and fire resistance properties and lower sound resistance than normal weight units. 2 THE MANUFACTURING PROCESS: Mixing 1- The sand and gravel are stored outside in piles and are transferred into storage bins in the plant by a conveyor belt as they are needed. The portland cement is stored outside in large vertical silos to protect it from moisture. 2- As a production run starts, the required amounts of sand, gravel, and cement are transferred by gravity or by mechanical means to a weigh batcher which measures the proper amounts of each material. 3- The dry materials then flow into a stationary mixer where they are blended together for several minutes. 4-After the dry materials are blended, a small amount of water is added to the mixer. Admixture chemicals and coloring pigments may also be added at this time. The concrete is then mixed for six to eight minutes. Molding 8-The compacted blocks are pushed down and out of the molds onto a flat steel pallet. In some operations the blocks then pass under a rotating brush which removes loose material from the top of the blocks. 3 Curing 9-The pallets of blocks are conveyed to an automated stacker or loader which places them in a curing rack. Each rack holds several hundred blocks. When a rack is full, it is rolled onto a set of rails and moved into a curing kiln. 10-The kiln is an enclosed room with the capacity to hold several racks of blocks at a time. There are two basic types of curing kilns. The most common type is a low-pressure steam kiln. In this type, the blocks are held in the kiln for one to three hours at room temperature to allow them to harden slightly. Steam is then gradually introduced to raise the temperature at a controlled rate of not more than 60°F per hour (16°C per hour). 4 FORM AND SIZE There are three basic forms of concrete block, solid, cellular and hollow, and within each type a variety of products are available, thus providing versatility to block work construction both in style and function. Concrete masonry units are specified by their nominal dimensions. The nominal dimension is greater than its specified (or modular) dimension by the thickness of the mortar joint, usually 10 mm. For example, a (200*200*400 mm) block has an actual width of 190 mm height of 190 mm and length of 390 mm. Different types of concrete block: (a) solid, cellular and hollow blocks; (b) common and facing blocks; (c) normal and insulating blocks; (d) lintel, quoin, cavity closure and multipurpose. PROPERTIES The properties of concrete blocks depend to a varying degree on the type and proportions of the constituent materials, the manufacturing process, and the mode and duration of curing employed, as well as on the form and size of the block itself. 5 Density The density of concrete blocks is largely a function of the aggregate density, size and grading, degree of compaction or aeration and the block form. The typical range for dry density is 500- 2100 kg/m3 Strength In addition to size, compressive strength is the basic requirement of concrete blocks, Concrete masonry units can be classified as load bearing (ASTM C90) and non–load bearing (ASTM C129). Load-bearing units must satisfy a higher minimum compressive strength requirement than non–load-bearing units. The compressive strength of concrete blocks is dependent mainly on their mix composition , degree of compaction and to a lesser extent on the aggregate type and curing normally used. In general, for a given set of materials the strength of a concrete block will increase with its density. The compressive strength of individual concrete masonry units is determined by capping the unit and applying load in the direction of the height of the unit until failure (ASTM C140). Strength Requirements of Load Bearing and Non–Load-Bearing (ASTM C90) Water absorption The amount of water absorption of concrete masonry units is controlled by ASTM standards to reduce the effect of weathering and to limit the amount of shrinkage due to moisture loss after construction (ASTM C90). The absorption of concrete masonry units is determined by immersing the unit in water for 24 hours (ASTM C140). The absorption and moisture content are calculated as follows. 6 Weight Classifications and Allowable Maximum Water Absorption of Concrete Masonry Units ASTM C90, Dimensional changes Concrete blocks will undergo some dimensional changes owing to variations in the ambient moisture and temperature conditions. The magnitude of such movements, to a varying degree, is largely influenced by the constituent materials (mainly the aggregate), mix proportions and the process of block-manufacturing adopted. Drying shrinkage is considered to be the most important in normal applications. drying shrinkage of concrete blocks can be reduced significantly by ensuring that the units are properly matured and by preventing them from becoming excessively wet on site prior to their use. 7 Durability In general, concrete blocks are adequately durable for most normal applications. As a general rule, in extreme conditions of pollution (chemical attack) and weather (frost attack), fair faced blocks with strength in excess of 7 Mpa should be used. It should be noted that open-texture blocks are more susceptible to frost attack than other blocks owing to the freedom with which water can move within the block on freezing. Efflorescence Efflorescence of the type found in clay bricks is rarely a problem with concrete blocks. Such efflorescence as occurs in concrete blocks normally consists of sodium, potassium and calcium carbonates formed as a result of a reaction between the corresponding free hydroxides brought to the surface and atmospheric carbon dioxide. Fire resistance In general, concrete blocks have good fire-resistance properties. However, their actual fire- endurance is controlled by numerous factors. As a general rule, most concrete blocks of 100 mm thickness can provide an adequate resistance to fire for up to 2 hours if load-bearing or up to 4 hours if non-load-bearing but specific information should be obtained from the manufacturer. Thermal conductivity The thermal conductivity of a concrete block is largely dependent on its block density as can be seen from the relationship. Thus, in general, autoclaved aerated concrete and lightweight concrete blocks have relatively low thermal conductivities. Similarly cellular and hollow blocks, because of their lower net density, have lower thermal conductivities than their solid counterparts. The thermal conductivity of a concrete block is further affected by its moisture content, increasing as the moisture content increases. 8