Chapter 21: Relay & Electronic Interlocking Design Criteria PDF
Document Details
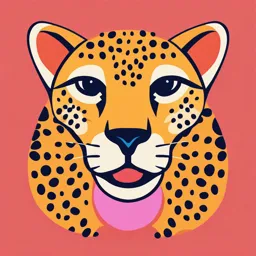
Uploaded by SolicitousOklahomaCity
null
Tags
Summary
This document details the design criteria for relay and electronic interlocking systems, focusing on signalling circuit design, control panel layout, and various indications. It covers route setting, control panel features, point operation, route indications, signal indications, and track circuit indications.
Full Transcript
Chapter 21: Relay & Electronic Interlocking Section 1: Design Criteria of Signalling Circuits 21.1.1 Circuits - General (a) The Detailed designs for circuits of interlocking may be required for; (i) Route Setting Type i.e. on the basis of En...
Chapter 21: Relay & Electronic Interlocking Section 1: Design Criteria of Signalling Circuits 21.1.1 Circuits - General (a) The Detailed designs for circuits of interlocking may be required for; (i) Route Setting Type i.e. on the basis of Entry/Exit principle. (ii) Non-route Setting Type i.e. Route is set with individual operation of points for existing installations or alterations. (b) The designs shall be suitable for RE as per stipulations in Chapter 22 of SEM on "Requirements of signalling in 25 KV AC electrified areas". (c) The designs shall be in accordance with the approved signalling plans, Control Table, Control Panel diagram, Relay contact analysis and relay rack arrangements. (d) The designs shall be suitable for the specific type equipment to be installed such as Make of Electronic Interlocking (Distributed or Central), MSDAC, SSDAC, UFSBI, Block Working built into Electronic Interlocking etc and the type of Interfacing & features, they provide. Use of dual OFC in Distributed type of Electronic Interlocking, are desirable as they reduce extent of copper cables & provide an alternate path in case of Failures. (e) The drawings & designs shall be made in accordance with Typical templates, RDSO`s Standard circuits/templates, guidelines, Board guidelines, Industry`s best practices & principles of Reliability, Availability, Maintenance & Safety in mind. 21.1.2 Control Panels-General (a) The display of the layout on the front of the Control Panel referred to as the illuminated diagram shall be well proportioned. Where additional facilities are likely to be provided, domino type panel shall, preferably, be used. The areas covered by each track circuit shall be clearly distinguished by use of different colours. (b) The operating members, namely route switches/buttons, point switches etc., referred to in the following clauses shall normally be provided on the illuminated diagram itself in Geographical order. A separate illuminated diagram for indication and a separate 'console' containing all the operating members may also be provided. (c) At Non-route setting type installations, the route may be set with individual operation of points. (d) The Route setting shall be on "Entry/Exit" principle for installations of Route Setting type. Each route shall be controlled by means of two push buttons-one at the entrance and the other at the exit of the route. Chapter 21: Relay & Electronic Interlocking Page 433 of 530 (e) In Non-route setting type installations, after setting of the route by individual operation of points is completed, signal can be cleared by an individual push button in conjunction with a group button or by an individual switch controlling each signal or a common switch for conflicting signals which are not required at the same time, or one push button at the entrance and other at the exit end. (f) Individual push button in conjunction with a common push button or two/three position switches shall be provided for individual operation of points. (g) Where a route has more than one overlap, it shall be possible to select and set the desired overlap beyond the exit signal of the route. (h) Where the route has alternate approach routes, it shall be possible to select and set the desired route with desired overlap. (i) The switches/buttons shall have distinctive colours so that they can be readily distinguished, such as running signal red, shunt signal yellow, calling on signal red with white dot & exit button white. The alternate overlap white with black dot, alternate route Grey, point black, slot green, crank handle blue and point group button black with red dot etc. 21.1.3 The control panel shall be provided with: (a) Arrangement for individual operation of points. (b) For emergency operation of points (where provided, during point zone track circuit failures), each individual operation shall be recorded on a counter. (c) Necessary slotting facilities for adjoining cabins, ground-frames, level crossings and crank handles etc. (d) Arrangement so that slot shall be controlled by operation of two buttons or a switch similar to route setting principle for individual line. For cancellation of slot, a group slot cancellation button to be operated along with entrance/exit button shall be provided. Each such cancellation shall withdraw the slot but the route controlled by the slot shall be kept held for a predetermined time delay or till route locking if any, is effective. Each slot cancellation shall be recorded in a counter. (e) When SM's key is taken out, it shall not be possible to change the last operated position of any signalling gear from control panel. However, facility shall be provided to put back the signal to 'ON' position without altering the route. It shall be ensured that no command gets executed automatically on reinsertion of SM's key. (f) An indication panel shall be provided in major yards, giving position of the yard and important indications for maintenance staff. 21.1.4 Indications on Control Panel The control panel shall be provided with the following indications. Chapter 21: Relay & Electronic Interlocking Page 434 of 530 (a) Point Indications (i) The position of points shall be indicated either by white/yellow or green lights near each individual point switch and by white strip light on the point zone and by white strip light on the point zone in case of push button. During operation of the points, light/strip light for the intended position shall flash till points are correctly set and locked. (ii) The point locked indication in route shall be given by illumination of a small white light near the point or points switch/button which shall be extinguished when point is free. (b) Route Indications (i) Route indication lamps shall be provided to indicate setting and locking of the route. Indication that route is set and locked shall be given by a set of white lights (not less than two) on each track section. When any route is not set, route indicator lamps shall be extinguished. (ii) The complete route over which the movement is to take place shall be lit with a row of white lights when the route is correctly set and locked. (iii) As the train moves over the route, the portion of the route occupied shall change to red and after the train has cleared the particular track, it should change back to white lights until the sectional route/entire route is released, when the white light is extinguished. (c) Signal Indications (i) Indication that a stop signal is at 'ON' shall be given by a red light and a permissive signal is at 'ON' shall be given by a yellow light on the corresponding signal symbols on the control panel. (ii) Indication that stop/permissive signal is 'OFF' shall be given normally by a green, yellow or double yellow light as signal is seen in the field, on the corresponding signal symbol on the control panel. In case of signal „OFF‟ aspect failed to lit at site, the corresponding signal aspect indication on the control panel shall be indicated with flashing. However, in case of a domino panel where indication of all aspects is not provided, any 'OFF' aspect can be shown by green along with the following flashing indications for conditions as enumerated below: Failure of green; green flashes red* blank; Failure of yellow; green flashes, red lit; Failure of double yellow, both green and red* flash; & Failure of red*, green not lit (blank), red* flashing. *To be read as yellow for a permissive signal. (iii) Signal indication for the 'ON' aspect of a shunt signal on the same post as the running signal, is not required. In the case of shunt signal on independent post, the 'ON' indication shall be given by a white light strip or two miniature white lights in a horizontal position on the corresponding shunt signal symbol on the control panel. Chapter 21: Relay & Electronic Interlocking Page 435 of 530 (iv) Signal indication for 'OFF' aspect of a shunt signal shall be given by a slanting white light strip or two miniature slanting white lights. Such indication of a shunt signal located on the same post as a running signal, shall be given below the running signal indication. (v) A white light for 'A'/'AG' marker indication should be lit up on the control panel below the symbol of the signal when set for automatic working. (vi) Indication that "Calling on" signal is 'OFF' shall be given by a white light below the running signal indication of corresponding signal symbol. (vii) Starter Indicator`s indication shall be provided by a white strip light which should be lit when repeater of the signal has displayed 'OFF' aspect. This indication should be provided by a white strip over the running signal symbol on the control panel. (d) Track Circuit Indications (i) Indication that the track circuit is occupied shall be given by a row of red lights (not less than two) on the each track circuit portion. (ii) When the track is not occupied, the red lights shall be extinguished. (e) Power Supply Indications (i) An indication to indicate the availability of the supply from the Mains/Diesel Generator/Catenary 1 or 2 should be suitably indicated, if such indications are not provided in Change over Panel in SM room. (f) Other Indications (i) Approach track circuits shall be indicated on illuminated diagram. In continuous track circuit territory, the approach track circuits will cover all the track circuits in rear of the first stop signal up to the next signal in rear or up to the track circuit specified in the Control Table for approach locking. An approach track circuit controlling calling on signal shall be indicated separately with a distinct mark. (ii) Advance approach warning of trains if required shall be indicated on the control panel in the form of flashing lights or other type of indication and audible bell warning to attract attention of Station Master. These visual and audible warnings shall stop as soon as the approach track circuits are occupied or signals are taken 'OFF' for the train. It shall be possible to silence the audible warning by pressing a push button. This cancellation shall not apply to train approaching subsequently for which the push button must be pressed again. (iii) Signal Lamp Failure alarm: Failure of lighting of a signal aspect/route aspect at site shall light a red indication on the control panel and give an audible warning for the same. Such indication may cover a group of signals. A common audible warning can also be provided for a group of signals. It shall be possible to silence the audible warning by pressing a push button. Such cancellation of audible warning shall not apply to subsequent failures for which the push button must be pressed again. Chapter 21: Relay & Electronic Interlocking Page 436 of 530 (iv) Indication shall be provided on the control panel distinguishing between locked and free condition of crank handle as below - When CH key is in & locked - Yellow Steady When CH key released from control panel but CH key is not extracted/When CH key is inserted back but CH control is not taken back from control panel - Red Flashing. When CH key released and CH key extracted - Red Steady When Emergency CH key release control given from control panel with 120 Seconds timer in progress - Yellow Flashing (v) The respective signal lock indication (white light) shall start flashing when an emergency route cancellation is initiated, in an approach locked condition of the route. This indication will extinguish after a lapse of two minutes and cancellation of the route. (vi) If push buttons are used on control panel, a buzzer to indicate that push button/push buttons has/have been left pressed may be provided. (vii) Suitable indications for slots shall be provided (viii) Gate control shall be provided on the control panel as below- When gate is closed & locked - Yellow Steady When gate slot released from control panel to open but gate is not open/When gate is closed but gate slot is not taken back from control panel - Yellow Flashing When gate is open - Red Steady (ix) The control panel indication lamps shall be operated by not more than 24V miniature type bulbs or light emitting diodes. (x) Return wires from indication lamps and relays shall be suitably bifurcated so that excessive current does not damage them. Any break in return wire shall not fail the indication/relay or give a wrong indication or pick-up a wrong relay. (xi) When an approved electronic flasher relay other than Mercury type is provided, a flashing white indication shall be provided at appropriate corner of the control panel to indicate to the operator the satisfactory working of electronic flasher relay. 21.1.5 Interlocking and Circuit Requirements: General (a) Before designing the detailed circuits, Control Table showing approach locking, back locking, overlap release, isolation, interlocking, dependence of signal aspect, grouping of crank handles and the condition for release of crank handles, route release, gate release etc. shall be drawn up and approved by the competent authority. Provisions of GR & SR shall be observed. (b) Signal circuits shall be so designed that the signal shall not change to a lesser restrictive aspect than intended one and route shall not be released because of fluctuations in power supply voltage or when the supply resume following its failure. Chapter 21: Relay & Electronic Interlocking Page 437 of 530 (c) Design of signal circuits and equipment shall be suitable for 25 KV AC electrified areas as per provisions of Chapter 22 of SEM on "Requirements of signalling in 25 KV AC electrified areas". (d) Common return shall not be provided in vital circuits. (e) Where relays other than 24 V, 1000 ohm relay with metal to carbon contacts are used, the circuits shall be so designed that not more than 45 such contacts are used in series in a circuit. (f) The proving of back contacts of metal to metal relays should be done in the circuitry. (g) All new installations shall be of route setting type interlocking. 21.1.6 Route Setting Type (a) The route setting and clearance of signal shall be with the following conditions: (i) SM's key is In (ii) The interlocking is free (b) The points are correctly set and locked in the route including overlap and isolation (if any) to desired position. (c) The crank handle keys for all the motor operated points in the route, overlap and isolation are locked and their control is not released, shall be proved in Signal Clearance only. The keys for all the key-locked points in the route, overlap and isolation are locked and their control is not released. (d) All interlocked level crossing gates are closed and locked against the road traffic in the route and overlap, if any, shall be proved in Signal Clearance only to allow gate closing in the last. (e) Slot if any, from other agency has been received. (f) The track circuits in the route up to the next signal/dead end, overlap and isolation and Fouling, if any, are clear. (g) Stop signal ahead is not blank (h) The interlocking between conflicting routes shall be achieved through route interlocking electric circuits at route initiation stage. (i) Approach locking or dead approach locking shall be provided for all manual stop signals. Approach locking shall be continuously effective from the predetermined point on approach of the signal. (j) Controls on level crossings, ground frames, cabins, sidings etc., shall be suitably interlocked. Chapter 21: Relay & Electronic Interlocking Page 438 of 530 (k) For clearing Calling On signals, proving of track circuits in the route and overlap are not required. Calling On signal shall detect all the points including interlocked level crossings in the route, which the main signal above it detects, except points in the overlap. Stop signal ahead is not blank is not needed. (l) For clearing of shunt signals, proving of berthing track circuits, points & LC gates in overlap, stop signal ahead is not blank is not needed. (m) A white indication for block control on the last stop signal should be provided on control panel, where- (i) Section ahead is worked on Absolute Block System and control panel and block instrument are placed at different locations. (ii) Block working is by means of axle counter or track circuit. 21.1.7 Non Route setting Type: (For existing installations & Alterations only. No new Installations of Non-Route setting type to be provided). The route setting and clearance of signal shall be with the following conditions: (a) The points in the selected route and if required in overlap and isolation are operated to required position by individual operation of switches or push buttons in conjunction with group push button. (b) Operation of entrance exit buttons/switches or one control switch clears the signal if; (i) SM's key is In (ii) The interlocking is free (c) The points including hand operated points in the route including overlap and isolation if any, are set, locked and detected. (d) Other conditions are same as para 21.1.6 (d) to 21.1.6 (m) above 21.1.8 Route Release Circuits (a) Complete route release including overlap shall be effective only after the signal governing the route is put back to 'ON' and corresponding route switch/button has been operated to normalize the route. Automatic route release by the passage of train and complete release of route through sequential route release shall be provided. (b) Where a route has got number of route sections, the circuit shall be so designed that the route section does not release only by picking up of the concerned track relay. Same is released only after the next track circuit is also dropped and picked up, except in case when the last track is a berthing track. In cases where the route is controlled by single track circuit, the route release shall be controlled after predetermined time delay. Chapter 21: Relay & Electronic Interlocking Page 439 of 530 (c) The route release circuit shall be so designed that it will release only when at least two track circuits drop and pick-up in sequence. (d) In installations provided with route setting system, sectional route release shall be provided if nos. of routes are more than 100. In such cases sub- route section already released shall permit setting up of other routes, if interlocking otherwise permits. (e) In case of installations provided with non-route setting system, sectional route release shall be provided if nos. of routes are more than 100. The complete route release shall be effective only after the signal governing the route is put back to 'ON' and corresponding route switch/push button has been operated to normalize the route. However, where sequence proving relays are provided to prove the authorized passage of a train, automatic route release shall be provided. (f) It shall be possible to release a route in emergency after suitable time delay as per Table-1, with the approach track occupied, provided the train has not passed the signal during the time interval. (g) It shall be possible to release a route in emergency after a suitable time delay as per Table-1, where approach track circuits have not been provided and after the signal has been put back to danger provided the train has not passed the signal during this time interval. (h) When the route is released by the passage of train, the overlap points shall be released only after the lapse of suitable time delay as per Table-1 after clearance of last point track circuit of the route i.e. the train is on berthing track. (However, in major yard this timing of route release can be reduced as per Table-1 with the approval of PCSTE). On cancellation, the overlap points shall be released simultaneously along with the main route. (i) Facility of emergency route/sub-route cancellation shall be provided and it shall be possible to release the route/sub-route with suitable time delay as per Table-1. Cancellation shall be operated after physical verification of the line by traffic representative. Every such cancellation shall be recorded on a non-resettable counter and in a register to be maintained by traffic representative. 21.1.9 Signal Control Circuits (a) It shall not be possible for a signal to assume 'OFF' aspect in installations provided with route setting facility unless the route switches/buttons have been operated and relevant route has been correctly set and locked and relevant track circuits are clear. In installation provided with non-route setting facility, the signal shall not assume 'OFF' aspect unless the route is set and locked, relevant track circuits are clear and signal switch/button has been operated. In case self-restoring type of push buttons are used, signal shall not assume 'OFF' aspect unless concerned push buttons are pressed simultaneously for 3 seconds and released. (b) Circuits shall be so designed that the failure of any part of a circuit affecting the control of the signal shall cause the signal to display a most restrictive aspect. Chapter 21: Relay & Electronic Interlocking Page 440 of 530 (c) The circuit shall be so designed that in case of failure of lighting of a Main signal aspect at site, the more restrictive aspect is lit automatically and in case of failure of lighting of ON aspect, it shall not be possible to clear the signal in rear. (d) Fouling protection, approach locking, indication locking, route locking, siding control key locking, crank handle locking and track locking shall be incorporated in the relevant control circuits. (e) Each aspect light of a signal may be proved where necessary and the aspect indication shall be provided. (f) Wherever required, necessary control on the level crossing, ground frames, cabins, siding control key, crank handles etc. shall be provided. (g) The correspondence of the point control relays and point indication relays may be proved in signal circuits before the signal displays an 'OFF' aspect. 21.1.10 Locking of Advanced Starter and Starter Signal at Junction Stations (a) Starter released by Advance starter is not required at way side stations having single & double line block working, where track circuiting have been completed. (b) Starter released by Advance starter is required at all diverging ends of junction stations, stations having twin single line block working and also at stations where track circuiting has not been provided between starter and Advance Starter. (c) All signals shall be automatically replaced to 'ON' by the passage of a train past the signal. However, starter signals shall be automatically replaced to 'ON' by the passage of a train (after a specified time delay, where required as per Table-1). 21.1.11 Level Crossing Gates circuits (a) It shall not be possible for a main signal to assume 'OFF' position unless all interlocked level crossing gates in its route and overlap are closed and locked against the road traffic. (b) It shall not be possible to open any such interlocked gate at a station until the concerned signal is replaced to 'ON' position and the route up to the gate is released or it is proved by suitable circuit arrangement that train has cleared the gate. (c) Mid section Gate signals shall be provided with Dead approach locking with Time delay as per Table-1. (i) Back locking for Gate signals in automatic signalling territory shall be provided. (ii) Back Locking may also be provided, if the distance of gate of a signal to LC gate is more than 180 meters, by two track circuits (where required) based on risk assessment. Chapter 21: Relay & Electronic Interlocking Page 441 of 530 21.1.12 Point Control Circuits (a) The points once set shall remain in the last operated position until these are operated by different route setting or by individual operation of points, except when stipulated otherwise. However, isolation points of catch siding, slip siding may operate automatically after the passage of train to their isolation position where sectional route release is provided. (b) Moreover, soon after CH/NX control is released, points shall not be operated by route setting operation. However, the points can be operated individually from the control panel/Control Terminal till such time the CH/NX key is not inserted in point machine. (c) Operation of points shall be possible only when the interlocking is free and relevant point track circuit is clear. Emergency operations, where provided when point zone track circuit fails, it shall be possible to operate the concerned point provided interlocking is free by releasing an emergency control. Each such operation shall be recorded on a counter. (d) Interlocking between points shall be provided only to the minimum extent necessary. (e) Point control circuits shall be so designed that a cross connection or a short circuit cannot operate a point or give a false indication of the same. (f) Hand operated points shall be equipped with circuit controllers that are operated by the switches when closed. Keys controlling such switches shall be electrically locked by the approach track back locking track circuit so that it's not possible to work them in the face of an approaching train. (g) Means shall be provided to cut off the motor feed in case of obstruction to the point movement after a predetermined time lag, based on the type of point machine used. (h) The point operating control circuits shall have track circuit control, overload protection and cross protection. 21.1.13 Crank Handle & Siding Control Keys (a) Crank handle/point NX key provided for manual operation of the points worked by electric point machine must be interlocked with signals. (b) The crank handles shall be provided to facilitate operation of points in case of failure of point machines. For this purpose, if necessary, the points in the yard may be divided into convenient groups and to distinguish particular groups, crank handles with different wards shall be used. The crank handles shall, however, normally be locked. It shall be possible to release them for use in point machine by releasing a control from the control panel. With the crank handle released, it shall not be possible to clear the signal for the concerned routes. The interlocking of crank handle can also be achieved by using NX key of different wards. Chapter 21: Relay & Electronic Interlocking Page 442 of 530 (c) It must not be possible to release the crank handle/point NX key unless the signals have been put back to 'ON' position and concerned route is released. However, if the route remains locked due to what so ever reason, it shall be possible to release the crank handle/point NX key after a time delay of 120 seconds from the time the signals have been put back to 'ON' position. Each such CH/NX keys release operation shall be recorded on non-resettable counter. (d) In major yard where number of points are more, these points should be grouped in different zones maintaining the yard flexibility. The crank handle/point NX key for each group of point machines should be so arranged that they cannot be interchanged. (e) Siding control key for manual operation of siding points, taking off from running lines, shall be so interlocked that it may not be possible to clear the signal leading over to that line when the key is released for operating siding points for shunting purposes. (f) It must not be possible to release the crank handle/point NX key unless the signals have been put back to 'ON' position and concerned route is released. However, in case of failure of Interlocking or for any other emergency case (E.I/both Control Terminal& Control Panel/both Control Terminals fails) an „Extreme Emergency Key‟ and self restoring „Extreme Emergency Button‟ shall be provided. Turning of key along with pressing of „Extreme Emergency Button‟, shall restore all signals to „ON‟ aspect and after a time delay as per Table-1, all CH/NX Keys shall be free and it shall be possible to release the CH/NX key. To normalize this emergency operation, ASM shall restore back the „Extreme Emergency Key‟. Each such „Extreme Emergency key‟ release operation shall be recorded on a non-resettable counter. 21.1.14 Cross Protection features (a) For purely internal circuits including vital circuits, double cutting or cross protection may not be provided, unless specifically required. (b) All external circuits shall be suitably protected from cross connections and rendered immune to false operation by induced voltages in RE areas. 21.1.15 Control Panel/Control Terminal [Video Display Unit (VDU)] (a) Stipulations given in above paras shall apply also apply to Control Panel for Electronic Interlocking Installations. These Control Panels shall not be used in future E.I installations. (b) Control Terminal/multiple Control Terminals shall be of appropriate size to display layout of the Yard in well-proportioned dimensions and shall display all functions clearly distinguishable. Normally Control Terminal/multiple Control Terminals shall be provided in redundant mode. (c) Video Display indications on Control Terminal shall conform to Control Panel indications and UFSBI Block panel as Block working built into Electronic Interlocking (EI) as covered in Section above or other approved type. Chapter 21: Relay & Electronic Interlocking Page 443 of 530 (d) Operation of Signals, Points and other Controls such as Gate, Crank handle, Siding, Slot, Block Working etc. shall be carried out through appropriate dropdown menus or other approved means. (e) Control Terminal shall have suitable protection facility against unauthorized operation which may be provided by physical „SM Key‟ in a separate box and key contacts are taken to pick up two separate „SM Key‟ relays in relay room for redundancy purpose. These relay contacts are taken as input through two different input cards preferable in different OC‟s and „SM Key IN‟ bit shall be made by their parallel proving inside E.I. (f) All Emergency operations shall be two-step process protected against unintended operations. (g) Control Terminal shall have provision for Signal, Point and Line Block Collars equivalent of Control Panel in the form of individual „Block‟ & „Un- Block‟ feature which shall remain effective even during changeover from one Control Terminal to other Control Terminal. „All Un Block‟ option shall be provided while E.I starts up to un-block all signals, points & lines after a time delay of at least 120 seconds. SM‟s key shall be required for unblocking of a function whereas no SM‟s key required for blocking. There should not be any automatic unblocking of functions. Blocking of a function shall be indicated on Control Terminal by different mark or colour over the concerned function. (h) Where Control Panel and Control Terminal are provided, it shall be possible to switchover the controls from Control Panel to Control Terminal and vice-versa, and where two Control Terminals are provided, it shall be possible to switch the controls from one Control Terminal to other Control Terminal through suitable means by either manual switch or password. (i) Indication that E.I system is healthy shall be displayed on the Control Panel using a blinking green LED or blinking green indicator on Control Terminal. (j) Operation of points shall be possible only, when the interlocking is free and relevant point track circuit is clear. Emergency operations provided when point zone track circuit fails and after line verification from site by traffic personnel, it shall be possible to operate the concerned point by inserting an emergency key in a separate box provided interlocking is free. Each such operation shall be recorded on a non-resettable counter. (k) Each „Normal‟ or „Reverse‟ operation of point shall be controlled through two output relays derived from two output bits should be from different output cards of E.I. (l) Last controlled position of points shall be available by using latch relay in point control circuits. (m) Mid stroke point reversal preventing feature shall be provided to prevent starting of operation when the point is under operation or tried for other position during mid stroke. Chapter 21: Relay & Electronic Interlocking Page 444 of 530 (n) Maintenance Terminal of Electronic Interlocking system shall be provided for the Signal Technician. (o) Block Working built into EI shall be provided for line clear purpose. It shall be possible to take a line clear when block section is clear upto first stop signal including Block overlap. Indication of Block built into VDU and indication of TCF, TGT, TOL, Bell, Block clear, SNK, SNOEK shall be as per drawing no. RDSO/S/32019. 21.1.16 Precautions for design of circuits using Electronic devices The following fail-safe principles shall be incorporated in the design of the equipment. (a) Component failure shall be self-detecting by way of causing a signal to display a most restrictive aspect as far as practicable. (b) All fail-safe circuits shall work on continuous energisation principle such that open circuits in wiring, relay contacts, etc., or loss of power supplies shall not cause unsafe conditions. (c) Due consideration shall be given to the effects of faults in fail-safe electronic equipment to allow open or short circuit or earthling conditions and variation in component values due to ageing, replacement of faulty component with new components of specified tolerance, etc. Safety shall not be impaired as a result of multi-terminal devices failing-either open circuit, short circuit or with partial short circuit between any pair of terminals or earthing. (d) The physical construction of fail-safe equipment shall be designed to eliminate the possibility of external objects causing short circuits between combinations of terminals in vital circuits. This may be achieved for example, by adequate separation of terminals, and by the fitting of protective shrouds where necessary. (e) Stipulated guidelines shall be followed in the design, Installation, Testing, Commissioning & Maintenance of Electronic Equipments/Systems. 21.1.17 Train Detection (Track Circuits & Axle Counters) (a) Provisions of SEM Chapter 17 on Train Detection (Track Circuits & Axle Counters) shall be followed. (b) DC track relays shall be centralized in location/relay room only by using separate cables of adequate cross section. (c) Track circuiting of the entire station section including all lines where direct reception is provided shall be done. (d) Type of Axle Counter – SSDAC, HA-SSDAC, MSDAC and Location of Track section Proving Relays and Type of Interface - whether Signal Cable or Quad cable or OFC shall be considered. Chapter 21: Relay & Electronic Interlocking Page 445 of 530 21.1.18 Signalling Cables. (a) Provisions of Chapter 15 of SEM on Cables shall be followed. (b) At least two cores of cable shall be provided between two ends of the yard to cater for telephone communication for maintenance purposes in non RE areas. Where the yard is extending over a large area, the location boxes may be grouped and one socket may be provided in one of the location boxes in the group so that telephone communication is conveniently available for co-ordination with the cabin during maintenance or rectification of failures of various ground equipments. Where such groups are situated in different directions from the cabin, a separate pair of conductors shall be used for each direction connected to the cabin. In RE area, provision shall be made for telephone communication through a telecommunication cable if already available or a separate telecom cable shall be laid for the purpose. (c) Earth leakage detectors of approved type may be provided to detect any leakage to earth in cable conductors. 21.1.19 Signals in Outdoor (a) The main signals shall be of multi unit colour light type. Shunt signals shall be of position light type. LED signals of approved type shall be used. (b) Route indicators shall be either of the direction type or multi lamp unit type or of Stencil type conforming to approved design. (c) 'A' & „AG‟ marker lights for semi-automatic signals shall be of approved type. 21.1.20 Point Machines - Operation a) The point operating control circuits shall have track circuit control, overload protection and cross protection. b) Crank handles with different wards shall be used. The slots in the point machines provided to take the crank handles would also be suitably made to take only the crank handle applicable to the group. The crank handles shall, however, normally be locked. It shall be possible to release them for use in point machine by releasing a control from the control panel. With the crank handle released, it shall not be possible to clear the signal for the concerned routes. The interlocking of crank handle can also be achieved by using NX key of different wards. Notes:- (i) For more details of Installation of Outdoor signalling Equipment, Refer to Chapter 19. (ii) In case of alterations to existing installations, Detailed documentation for alterations, duration of Non-Interlocking/Disconnection & sequence of working shall be made carefully and concerned staff to be briefed. 21.1.21 Various Timers in Signalling circuits shall be as given below in Table-1. Chapter 21: Relay & Electronic Interlocking Page 446 of 530 Para no:21.1.21 Timers in Various circuits – Table-1 S.No Description Delay in Conditions/Remarks seconds 1 Main Stop Signal (Route 120 1) Before movement, if back lock track circuits are clear. Sub routes (if any) should also get released cancellation)-Home, Starter etc with main route. 2) After movement, either back lock track circuits are clear or after physical verification by SM, if any back lock track circuit has failed. 2 Sub Route (Emergency 120 1) Where a route is divided into sub routes and such facility is operationally required. Cancellation) 2) On physical verification of the route by SM if any back Lock track circuits is showing occupation. 3 Crank handle (CH) emergency 120 Points are locked due to failure in any route/sub route. Cancellation timer to start after cancellation key release time buttons are operated duly putting back to ON position those signals which were taken OFF. 4 Shunt Signal (Route 120 1) Before movement, if back lock track circuits clear. Sub routes (if any) should also get released cancellation) with main route. 2) After movement, either back lock track circuits are clear or after physical verification by SM, if any back lock circuit has failed. 5 Calling On Signal (Route 120 1) Proving all back lock track circuits are clear (if they are functional). cancellation/Release) 2) Emergency cancellation of calling route (without proving any back lock track) can be provided, on physical verification of the full route by SM. 6 Signal Overlap (release) 120 Timer to start automatically , on clearance of last back track circuit of Home Signal route and on occupation of berthing track circuit (or as soon as Train has passed beyond signal overlap track circuits in which case timer gets bypassed). 7 -do- 60 For big yards with the approval of PCSTE. On clearance of last back track circuit of Home Signal route and on occupation of berthing track circuit. 8 Calling On Signal below Home 60 Calling on track circuit is occupied. (Initiation) 9 Calling On Signal below the 0 SM to ensure that train has come to a stop, before taking Off Calling-on. starter (Initiation) Chapter 21: Relay & Electronic Interlocking Page 447 of 530 Para no:21.1.21 Timers in Various circuits – Table-1 S.No Description Delay in Conditions/Remarks seconds 10 Opening of LC gate (Gate 60 1) Timer shall start on putting back the Gate signal. signal at 180 m from LC) 2) If two track circuits are provided to prove that train has passed beyond LC gate, such sequential proving is adequate to open LC gate immediately with out waiting for completion of 60 seconds. 11 Opening of LC gate (Gate 120 1) Timer shall start on putting back the Gate signal. signal at more than 180 m 2) If two track circuits are provided to prove that train has passed beyond, LC gate, such sequential from LC) proving is adequate to open LC gate without waiting for completion of 120 seconds. 12 Opening LC Gate (Traffic 120 When route/sub route is locked, LC gate opening control can be given after 120 sec time delay by Gate) applying cancellation, duly putting back the signals taken OFF. 13 Opening of LC gate in 120 When approach track circuits of an automatic signal protecting LC gate have failed. automatic section 14 Crank handle/LC gate key 120 To extract keys when Electronic Interlocking/VDU has failed. Extraction 15 Point failure alarm 15 Alarm to SM that point has failed to operate. 16 Point Operation timer 10 Point contactor relay to de-energise and cut off power to Point Machine to protect it. 17 Signal blank buzzer 10 Alarm to SM if any signal goes blank by proving that all ECRs are de-energised 18 Panel Button struck up alarm 10 Alarm to SM, whenever any button is struck up in button type panels (Button type panels) 19 HR Relay de-energisation 5 Slow to drop for HR relay of starter where starter is placed at 3 meters from controlling Track Circuit glued joint/Detection Point, to avoid confusion to Loco pilot 20 Holding HR relay energised 3 To prevent signal bobbing, in case of intermittent failures of Track circuit`s/Point detection due to loose packing. 21 HR control timer de- 5 For HR control timer de-energisation, if read back is not received from Concerned signal as per energisation command given by Electronic Interlocking 22 Power failure Alarm 5 Alarm to SM, if all power supplies fail Note: Above timers where not yet existing, may be provided for new works and major alterations. Chapter 21: Relay & Electronic Interlocking Page 448 of 530 Section 2: Installation & Testing of Relays 21.2.1 Relays – General Requirements: (a) Approved type of Plug-in Line relays of Neutral/Polar Biased/Magnetic latch/Interlocked type rated at 24/48/60 V DC shall normally be used. Approved type of LED Lamp proving relays shall be used for LED signal lamps. (b) Approved type of Relays shall be used in RE & Non-RE areas. Various types of relays used in signaling are given in Annexure: 21-A1. (c) Time element relays of approved type shall be used. Where approved electronic time element relays are used, these shall be two in number and their contacts shall be in series in the concerned time release circuits. (d) The relays, including track relays, located in the track side location boxes, shall be plug-in type. (e) All plug-in relays and relay groups shall be provided with coding pin arrangement to prevent the wrong relays/relay group being accidentally plugged-in during replacement. All relays, relay groups shall be sealed. (f) As far as possible, all relays shall be housed in the relay room of the controlling cabin to achieve maximum centralization. (g) Sequential proving of front and back contact shall be ensured where metal to metal contact relays are provided. (h) Removal or replacement of plug-in relays/relay groups from the relay racks during operation shall not cause any unsafe conditions in the circuits. (i) Where feasible all relays except track relays, shall have 10% of working contacts as spare subject to a minimum of one front and one back to facilitate addition and alteration to the circuits at a later date. Extra space (minimum 10%) to accommodate repeater relays shall be provided in the relay rack to cater for future expansion. (j) Where magnetic latch relays are used, the circuit shall be so designed so as to prevent undue dropping of the relay due to back EMF generated by other relays. (k) Wiring of 'Q' type relays shall be done through flexible multi strand wire preferably and contacts to be paralleled as feasible. (l) Mercury wet contact type relay shall be used for flasher circuits, alternatively, a solid state flasher may be used. If solid state flasher is used, flashing indication on operating panel should be provided for indicating healthy condition of flasher. (m) Relays shall not be stored in the vicinity of damp or chemically polluted environment. (n) Sealing screws of the relays shall be intact. (o) Care shall be exercised in transporting the relays from the place of storage to the work site so that the relays do not get damaged. Chapter 21: Relay & Electronic Interlocking Page 449 of 530 21.2.2 Fixing in Relay Room As far as practicable, the relay room is not located in the vicinity of chemical factory, loco shed or engine ash pits etc. In case it becomes unavoidable, necessary precautions shall be taken so that relays are least affected by the chemical fumes, dust etc. and are provided with dust free environment. Relay room shall be provided with double locks and door opening shall be monitored through Datalogger. (a) Where Relays cannot be located in the Cabin, they shall be housed in location box of approved type which are properly secured. (b) In 'Q' style relay the code pins configurations for plug in relay shall not be changed by drilling additional holes on plug board to avoid fixing of a wrong relay which may lead to unsafe condition. In Siemen's K-50 relays, the Code pins position on base plate should not be changed and to be retained as fixed by the manufacturer. (c) All relay clips shall be checked for proper locking in the base when plugged in. Extreme care shall be exercised while removing the clips from the jacks of the plug-in type relay. (d) In all installations, a relay index board shall be provided for locating relays easily. (e) Relays involving external circuits shall have cross protection and double cutting. Signal control relays shall preferably be provided with double cutting. (f) A contact analysis chart shall be prepared duly showing the contacts used circuit-wise with reference and spare contacts available, wire count for each contact and relay position in the rack. (g) Number of contacts in a circuit shall not exceed 45 Nos. due to voltage drop consideration. The voltage across R1& R2 of a relay shall not be less than 22 V. (h) Where available, spare contacts shall be paralled with working contacts. 21.2.3 Sealing of Plug-in Relays (a) In case of metal to carbon contact type relays, sealing shall be done at Manufacturer's premises before dispatch and if the seals have to be broken due to any defect noticed, resealing must be done at the workshops. (b) In case of metal to metal contact type relays, sealing of the cover shall be done by not below the rank of JE (Signal) at site. Whenever seals have to be broken at site for maintenance purposes, the same shall be done by an official not below the rank of JE(Signal). (c) Line Relays shall be energized at the rated voltage specified in the specification. Chapter 21: Relay & Electronic Interlocking Page 450 of 530 21.2.4 Maintenance of Relays (a) Cleaning shall be done regularly so that dust is not deposited on the relay. There is no loose connection on the terminals, plug in relays is fitted tightly & the sealing is intact. Metal contacts are not blackened due to arcing. There is no pitting of carbon contacts. No foreign materials or water vapor which can cause fungus formation, are inside the relay. There is no rusting or sulphation on the parts. Relays are not due for P.O.H., wherever applicable. (b) During routine inspection and maintenance, if high contact resistance is observed on any contact of a relay, spare contact to be used or the relay should be replaced. 21.2.5 Periodical Inspection of Relays Sectional SSE/JE (signal) shall visually inspect the relays, with particular attention to those used in vital circuits. During visual inspection, relay shall be taken out of service if any of the defects are noticed in respect of; (a) Movement of armature and contact carriage (b) Wiping of contacts (c) Arcing of contacts (d) Pitting or charring of contacts (e) Dust accumulation on contacts (f) Electro-plating (g) Corrosion, rusting of components (h) Crack or breakage in components (i) Presence of fungus and ants inside the relay casing (j) Charring of cover near contacts in the case of plug-in-type relays (k) Corrosion of Label (l) Absence or tampering of seal (m) Effectiveness of relay retaining clip to be checked in case of Q style Plug-in type relays (n) Any other abnormal condition 21.2.6 Replacement of Relays: Metal to carbon contact miniature plug-in type relays should not be overhauled. These relays except track relays should not be used after completion of the codal life of 25 to 30 years or after their failure. Plug in type track relays have to be replaced on completion of 12 years or earlier if warranted by the actual condition of the relay and/or its usage. Chapter 21: Relay & Electronic Interlocking Page 451 of 530 Section 3: Installation of Relay Interlocking 21.3.1 Wiring and Relay Racks (a) The wiring used in various equipment shall comply with the requirements laid down in IRS specification No. S 23. (b) All wiring in the cabin and locations shall be done in a neat manner so that the wiring does not in any way prevent the proper functioning over working parts and is easily accessible for maintenance. (c) All wiring in the cabin and location shall be terminated on approved type terminal blocks/tag blocks unless otherwise specially permitted. (d) At all locations and cabins, cable/entry arrangements of adequate size, conveniently located for ease of approach to terminals and other equipment so arranged as to protect the wires from damage, shall be provided. Such cable/entry arrangements shall be plugged and sealed with suitable compound after the wiring is completed. (e) The internal wiring of relay rack in locations and cabin shall be generally carried out with plain annealed copper conductors; PVC insulated unarmoured flame retarding type of 1100 V grade unless otherwise specially permitted. The size of the conductors may be as follows: Type Size (a) Single Core size 1 mm (b) Multi core each core of size 1 mm (c) Multi core each core of size 0.6 mm (d) Flexible insulated wire size 16/0.20 mm (e) Flexible multi strand wire size 3/0.75 mm (f) Rack to rack wiring shall be generally carried out with multi core cable having plain annealed copper single core conductor of size 1/0.6 mm or multi-strand 16/0.2 mm as per approved specification for indoor cables. (g) Following practice shall be adopted for internal wiring. The connecting wires shall be terminated on eyelets/lugs/receptacles unless otherwise specially permitted. (i) All connections to plug-in non-proved type relays flexible wire of 16/0.20 mm shall be used. (ii) All connections to proved typed relays shall be done with 0.6/1 mm single strand multi core cable. (iii) For all connections from cable terminations to tag blocks and indicators etc. shall be done with the help of 1 mm single strand wires. (iv) For all connections to circuit breakers, lever locks etc. single strand wire of 1.5/1.6 sq. mm size shall be used. Chapter 21: Relay & Electronic Interlocking Page 452 of 530 (h) Relay to Relay wiring on the same rack should be as far as possible direct without intermediaries like tag block/terminals. (i) Identification Marker for identifying the terminals and tags shall be provided to each terminal to identify the circuits for which it is used. (j) Relay racks shall have sufficient capacity to take additional equipment to the extent of 15% of equipment provided to permit additions and alterations. (k) Charts showing the position of relays on relay racks and contact analysis of relays indicating the spare and used contacts shall be prepared and kept in the relay room. (l) For future expansion, provision shall be made to accommodate additional relays, relay groups & racks in the relay room. 21.3.2 Fuses, Terminals and Terminal Links (a) Cartridge type fuses shall preferably be of Non deteriorating type. Where screw cap cartridge type fuses are used, these shall be of different colour codes for different current rating and these shall be non - interchangeable. (b) Fuses shall be so grouped that blowing of a fuse has minimum repercussion on train operation. (c) The fuses when blown off, shall preferably give a visual indication. (d) Each group of circuits shall be carefully protected by fuses in the cabins and in location to facilitate easy fault localization. (e) Fuses shall be so arranged that they can be easily replaced without causing interference or unsafe conditions to other circuits. (f) Cartridge fuse links shall be approved type. (g) The terminal block and tag blocks shall be of approved type unless otherwise specially permitted. (h) The terminal boards provided at the locations and other places shall be provided with suitable links to facilitate isolation of the two sides of the circuits which are connected through the terminal links. (i) For vital circuit fuse auto change over system of approved type to be provided. 21.3.3 Power Supply Arrangements The power supply systems for Signalling Installations shall be as per details given in Chapter 16 on "Power Supply Arrangement systems for Signalling Installations". 21.3.4 General Arrangements (a) Air conditioning may be provided for every signalling interlocking (PI/RRI) installation with more than 100 routes. For E.I installations air conditioning may be provided irrespective of number of routes to improve reliability. Chapter 21: Relay & Electronic Interlocking Page 453 of 530 (b) For other signalling installations, with less than 100 routes, air-conditioning may be provided for those installations which are (i) prone to dust (coal dust, stone dust, iron ore etc.) or (ii) in the vicinity of chemical/fertilizer/other industrial factories releasing harmful fumes or (iii) in areas with extreme temperature with the agreement of PCSTE and PCEE. (c) AC equipments shall be provided and maintained by Electrical department. Such ACs shall be connected with the local power supply. The switch to operate AC shall be outside the relay room. (d) 'Automatic Fire Detection and Alarm System' may be provided at all stations irrespective of number of routes. (e) Automatic Fire Suppression System' along with “Automatic Fire Detection And Alarm System“ may be provided at stations with more than 400 routes. Note: In case provision of “Automatic fire suppression system” along with “Automatic Fire Detection And Alarm System” is considered desirable by Zonal Railways at critical stations and important junction stations even below 400 routes, same may be provided with the approval of competent authority (i.e. PCSTE). (f) Firefighting equipment shall also be kept in the power supply equipment room. (g) Suitable standard earthing shall be provided for all control panel, power supply, switch board, transformers, inverters etc. (h) At all Relay Interlocking Installations, Data Logger shall be provided. (i) Communication between the SM's panel room, relay room, equipment room and locations shall be provided. 21.3.5 Lightning & surge protection, Earthing: Shall be done as per Section 5 of this chapter. 21.3.6 Testing & Commissioning of Relay Interlocking: (a) Once the indoor wiring works are completed before conducting the system Integrity testing, simulation test shall be conducted by simulating field gears such as Track circuits, Signals & Points on a simulation panel and errors removed. This will ensure the correctness of indoor wiring before connecting to outdoor gears. (b) Testing of wiring & Commissioning shall be done as per Para 19.8.5 to 19.8.12. (c) Recommended check list of items for commissioning is given at Annexure: 21-A2. This list may be suitably modified as needed. Chapter 21: Relay & Electronic Interlocking Page 454 of 530 Section 4: Electronic Interlocking (EI) 21.4.1 Essential Requirements of Electronic Interlocking (a) Electronic Interlocking System shall be approved type and shall conform to latest approved specification. (b) Electronic Interlocking System shall have the highest level of safety integrity as stipulated. (c) Electronic Interlocking System shall be suitable for working on Electrified and Non-Electrified sections. (d) Electronic Interlocking System Installation shall be of Route setting type using Dropdown menu Or Entry/Exit control with a facility for individual operation of points. (e) Signalling and interlocking arrangements for the Yard shall be in accordance with the approved Signal Interlocking plan (SIP) and Control Table. (f) Electronic interlocking system shall be capable of working with Control Panel or/and Control Terminal. (g) Electronic Interlocking system shall have adequate built-in redundancy as per approved specification. (h) Provisions given in Sections 1, 2 given above are generally applicable for Electronic Interlocking also. 21.4.2 Control Terminal (Video Display Unit (VDU)) (a) Same requirements given in Para 21.1.1, 21.1.2 shall apply for existing Control Panels (where provided) for Electronic Interlocking (E.I) installations. Control Panels shall not be used in future Electronic Interlocking installations. (b) Control Terminal/multiple Control Terminals shall be of appropriate size to display layout of the Yard in well-proportioned dimensions and shall display all functions clearly distinguishable. Normally Control Terminal/multiple Control Terminals shall be provided in redundant mode. (c) Video Display indications on Control Terminal shall conform to Control Panel indications as covered in Para 21.1.4 or other approved type. (d) Operation of Signals, Points and other Controls such as Gate, Crank handle, Siding, Slot etc., shall be carried out through appropriate dropdown menus or other approved means. (e) Control Terminal shall have suitable protection facility against unauthorized operation which may be provided by physical „SM Key‟ in a separate box and key contacts are taken to pick up two separate „SM Key‟ relays in relay room for redundancy purpose. These relay contacts are taken as input through two different input cards preferable in different OC‟s and „SM Key IN‟ bit shall be made by their parallel proving inside E.I. Chapter 21: Relay & Electronic Interlocking Page 455 of 530 (f) All Emergency operations shall be two-step process protected against unintended operations. (g) Only non-resettable counters shall be provided while working with Control Panel or Control Terminal. (h) Control Terminal shall have provision for Signal, Point and Line Block Collars equivalent of Control Panel in the form of individual „Block‟ & „Un- Block‟ feature which shall remain effective even during changeover from one Control Terminal to other Control Terminal. „All Un Block‟ option shall be provided while E.I starts up to un-block all signals, points & lines after a time delay of at least 120 seconds. SM‟s key shall be required for unblocking of a function whereas no SM‟s key required for blocking. There should not be any automatic unblocking of functions. Blocking of a function shall be indicated on Control Terminal by different mark or colour over the concerned function. (i) Where Control Panel and Control Terminal are provided, it shall be possible to switchover the controls from Control Panel to Control Terminal and vice-versa, and where two Control Terminals are provided, it shall be possible to switch the controls from one Control Terminal to other Control Terminal through suitable means by either manual switch or password. (j) Indication that E.I system is healthy shall be displayed on the Control Panel using a blinking green LED or blinking green indicator on Control Terminal. (k) Operation of points shall be possible only, when the interlocking is free and relevant point track circuit is clear. Emergency operations provided when point zone track circuit fails and after line verification from site by traffic personnel, it shall be possible to operate the concerned point by inserting an emergency key in a separate box provided interlocking is free. Each such operation shall be recorded on a non-resettable counter. (l) Each „Normal‟ or „Reverse‟ operation of point shall be controlled through two output relays derived from two output bits should be from different output cards of E.I. (m) Last controlled position of points shall be available by using latch relay in point control circuits. (n) Mid stroke point reversal preventing feature shall be provided to prevent starting of operation when the point is under operation or tried for other position during mid stroke. (o) When embedded block working in Electronic Interlocking is used, all indications like TGT, TCF, LC etc required for block working shall also be displayed 21.4.3 Interface with Electronic Interlocking (a) Interface between Control Panel, Video Display Unit and Electronic Interlocking system shall be of approved type. (b) Interface of Points, Signals, Track Circuits and Controls such as Crank Handle, LC Gate, Siding, Slot etc., with Electronic Interlocking System shall be through Relays of approved type or through any Electronic Modules of approved type conforming to approved specification. Interface with E.I of adjacent station, Digital axle counter shall be of approved type. Chapter 21: Relay & Electronic Interlocking Page 456 of 530 (c) Interface between external data logging equipment and Electronic Interlocking system shall conform to approved specification. (d) Electronic Interlocking System shall be capable of being controlled and monitored from a either centralized location or distributed locations as per requirement at site. (e) It shall be possible to network the Electronic Interlocking Systems for diagnostic function to a centralized location. (f) Electronic Interlocking system may be capable of being networked with other systems for the purpose of centralized control and monitoring. 21.4.4 Interlocking & Circuit Requirements (a) Interlocking application logic (site specific data) requirements for the E.I system shall be as per interlocking principles stipulated for Relay Interlocking and Standard Circuits for Electronic Interlocking. (b) It shall be possible to modify application logic for yard remodeling or change in interlocking using approved type of user interface. (Note: For Standardised Typical Circuits of Electronic Interlocking, may refer to http://10.100.2.19/signal/policy/uniform_circuit_diagram/Report%20SS%20155 %202019%20(std%20ckts%20of%20EI)%20Booklet%20print.pdf) 21.4.5 Powering up of Electronic Interlocking (a) Electronic Interlocking system shall drive all the relevant signals to the most restrictive aspects whenever internal failure of any nature arises or when Electronic Interlocking system is powered up or during shutdown. (b) After powering up of Electronic Interlocking the system shall block all signals and other operations. After verification of safety functions by Electronic Interlocking system, this blocking shall be released after a delay of at least 120 seconds. 21.4.6 Configuration of Electronic Interlocking a) Electronic Interlocking system shall have hot-standby arrangement and changeover from one system to other systems shall not interrupt status of signalling. b) Electronic Interlocking system shall be of either Centralised or Distributed type as per approved specification and as per policy directives. c) In case of Distributed configurations, redundancy with route diversity in OFC communication media and power supply system shall be provided for linking the subsystems. d) Electronic Interlocking system in any configuration shall have time synchronisation. Chapter 21: Relay & Electronic Interlocking Page 457 of 530 21.4.7 Version Control of Softwares of Electronic Interlocking (a) Version of the Generic System software and hardware shall be approved and controlled by authority competent to approve the Electronic Interlocking system and its specifications. (b) Version and checksum of the Application logic (station specific logic) shall be unique for the installation and shall be approved by the authority competent to approve the circuit diagrams. Corresponding Checksum shall be recorded and controlled by the same authority. (c) Version number and Checksum shall change whenever any modifications are carried out to the Application logic (site specific logic). (d) A proper record of Checksums shall be maintained at Station, Divisional Headquarters and Zonal Headquarters as a part of completion circuit diagrams. Section 5: Installation & Testing of Electronic Interlocking 21.5.1 Installation of Electronic Interlocking (a) Installation of Electronic Interlocking system shall be done as per approved guidelines and technical advisory notes issued from time to time. (b) Application logic (site specific logic) shall be verified for safety and functionality by carrying out exhaustive safety and functionality tests by officers authorized by PCSTE. (c) Only approved application logic with specified checksum shall be used in the E.I system and this data and checksum shall be version controlled and preserved by the Railways. (d) Electronic Interlocking is required to be provided in dust proof cabinets of approved type having transparent front door. (e) Interface Relays, where provided, shall be of approved type and contacts should be paralleled as far as possible for better reliability. (f) Wherever possible, the spare input/outputs shall also be wired from E.I cards up to Wago terminals for ease of carrying out future alterations. (g) The input and output cables of E.I shall be twisted to minimize EMI & EMC effect. (h) Electronic Interlocking system shall be installed closer to Operator Room, preferably adjacent room. Track crossing should be avoided between main E.I system and operator room. (i) The Electronic Interlocking room shall be provided with tiles or similar arrangements on floor and walls to avoid periodic painting of walls and resultant dust. Chapter 21: Relay & Electronic Interlocking Page 458 of 530 (j) FRP or insulated ladders arrangement shall be used to carry wires from rack to rack or from other equipment. (k) All entries to Electronic Interlocking room shall be suitably sealed to prevent entry of rodents, lizards, insects etc. (l) Electrostatic Floor Pads and Hand bands shall be provided near electronic equipment to prevent damages to electronic equipment due to electrostatic discharges. (m) The room where Electronic Interlocking is installed shall be provided with Air-conditioning. (n) The building/room where E.I is installed shall be protected by External Lightning protection arrangement at the top of building. In case there is any other metallic earthed structure is available nearby which protects the E.I building, then separate Class A at top of E.I room is not required. The guidelines in National Building Code of India (2016 or latest) shall be followed for calculations. (o) Surge and lightning protection devices of appropriate class and rating shall be provided for the regulated power lines before extending them to Electronic Equipment Room. All equipment in Electronic Equipment Room shall derive power from these regulated and protected power lines (clean), but not from electrical service lines (dirty) used for room lighting air- conditioning or fans. (p) Clean and dirty wiring shall be clearly segregated and routed in different enclosures/ladders, and where this is not feasible, a minimum distance of 150 mm between clean and dirty wiring shall be maintained. (q) If clean and dirty wiring need to cross at any place, then wiring should be arranged at perpendicular to each other. (r) Indicative type surge protection devices of appropriate class and rating shall be installed for all copper based external interface ports (power, communication, maintenance terminal, control panel interface etc). (s) The connectivity between E.I and sub-systems like Control Terminal, Control Panel, and Object Controller shall be planned with OFC cable to avoid damage due to surge and lightning. The OFC shall be provided in redundant manner to avoid failure due to cut/damage in one location/path. 21.5.2 Testing Of Electronic Interlocking (a) For Electronic Interlocking, the integrity of interlocking inside E.I designed for a specific station can be tested at factory which is termed as Factory Acceptance Test (FAT). This interlocking when installed at site and interface wiring is connected then the test carried out as laid down for relay interlocking, it is termed as Site Acceptance Test (SAT). Chapter 21: Relay & Electronic Interlocking Page 459 of 530 (b) Tests to be performed during FAT: FAT testing is performed with the computer simulation. Only the testing of interlocking on Application Software with reduced time as per SIP and RCC is performed during this stage. Interface with I/O card, intercommunication is not checked as E.I hardware is not used in FAT. Hence, the following test are to be usually done during FAT (Computer Simulation), besides any other tests as required- (i) Control Table (including Negative Testing). (ii) Cross Table (Also known as Square sheet testing). (c) Tests to be performed in SAT (for new installations): In SAT, similar testing is being performed at site with E.I hardware and simulation panel in first stage. The correspondence & Interface testing are also performed after interface with field gears. Any other test may also be conducted as required. (i) Logic and interlocking testing: Control Table (including Negative Testing). Cross Table (Square sheet). (ii) Interface and Equipment functional Test: Intercommunication test between sub-racks, Correspondence test (d) Tests to be performed in SAT (for alteration works):- (a) When the existing ports (I/O and communication) are not disturbed, the following tests, besides FAT, and any other tests as required, are to be done; (i) Logic and interlocking testing Control Table to the extent as decided by the Zonal Railway. (ii) Interface and Equipment functional Test: Correspondence test (new additions) Intercommunication test between sub-racks (if any new addition) (b) When the existing ports (I/O and communication) are disturbed, the following tests, besides FAT, and any other tests as required, are to be done; (i) I/O port correspondence check between Application logic and Interface circuits. (ii) Logic and interlocking testing Control Table to the extent as decided by the Zonal Railway. (iii) Interface and Equipment functional Test: Correspondence test (new additions) Intercommunication test between sub-racks (if any new addition) Chapter 21: Relay & Electronic Interlocking Page 460 of 530 Note: (i) FAT should preferably be conducted at factory premises. However, FAT can also be done at railway premises at central location but not at the site. For this, the setup should be made by all the Zonal Railways. (ii) FAT & SAT should be done by separate officials where ever feasible. 21.5.3 Power Supply for Electronic Interlocking (a) Adequate redundancy in power supply arrangements for E.I systems including Control Terminals shall be provided as per approved specifications and guidelines. (b) Wires connecting equipment shall be of adequate size so that there is not more than 0.5% loss in voltage. (c) The power supply for fan shall be fed with separate external supply, which should be completely isolated from Electronic interlocking supply and same shall be provided with fuse. 21.5.4 Lightning & surge protection, Earthing: Shall be done as per Section 7 of this chapter 21.5.5 Testing & Commissioning of Electronic Interlocking: Wiring, Testing & Commissioning shall be done as per Para 19.8.5 to 19.8.12. Recommended check list of items for commissioning is given at Annexure: 21- A2. This list may be suitably modified as needed. Section 6: Maintenance of Interlocking 21.6.1 Periodicity of Tests (for existing installations-Relay interlocking/Electronic Interlocking) All the tests indicated in this chapter shall be conducted at the time of new installation or making any alteration to the existing installations. (a) In a working installation, the following periodical tests shall be done: (i) Physical inspection once in a year or earlier as feasible. (ii) System integrity test as per para 19.8.8 once in five year or earlier if interlocking is altered. (iii) Insulation tests on Cables as per Chapter 15 of SEM. (iv) Test of individual equipment in accordance with specifications and instructions applicable for each apparatus as stipulated in current Chapter. (b) It will be personal responsibility of SSE/JE (Signal) to test all Electrical signalling circuits of relay interlocking up to 20 routes. (c) It will be personal responsibility of ASTE/DSTE concerned to test all electrical signalling circuits of relay interlocking with more than 20 routes. Chapter 21: Relay & Electronic Interlocking Page 461 of 530 21.6.2 Specific tests for Electronic interlocking (a) Maintenance of Electronic Interlocking system shall be done as per approved system maintenance manuals. A general maintenance schedule for Electronic interlocking is provided for guidance at Annexure: 21-MS3 in Appendix I. Note: At stations having dense traffic and high speed, the Railways may prescribe more frequent inspections, if considered necessary. (b) Maintenance Terminal of Electronic Interlocking system shall be provided in the Signal Technician Duty room. (c) Latest E.I station database files (application logic, Control Terminal database, etc.) shall be kept updated in centralized server as specified. (d) Periodic testing of redundant systems shall be carried out. Checksums shall be verified during periodic inspections. (e) Additional References for Electronic Interlocking. (i) Relevant International Standards (or equivalent standards) with latest revisions are also applicable to development and implementation of safety related railway signalling systems and projects including Electronic Interlocking. IEC stands for “International Electro technical Commission” and CENELEC stands for “European Committee for Electro technical Standardization”. (ii) RDSO Specifications and Technical Advisory Notes (TAN) with latest amendments are applicable for design, installation, testing and maintenance of Electronic System. Section 7: Lightning & Surge Protection for Signalling Equipments 21.7.1 Lightning-General: Lightning and surge protection shall be provided to protect Electrical & electronic signalling equipments from lightning & surges. (a) S&T equipment shall be protected as per National Building Code 2016 (NBC 2016) and IEC 62305. S&T equipment, including those given below, are to be grounded and protected from lightning surges. Code of Practices, Technical Advisory Notes, Guidelines issued by RDSO on the subject shall be taken into consideration. (i) Electronic Interlocking Installations including Object Controllers. (ii) BPAC Systems, Axle Counter Systems, Integrated Power Supply Systems. (b) Equi-potential bonding to be provided for all the equipment for effective lightning and surge protection in Signal Equipment Rooms. (c) External Lightning Protection and Class/Type I, II & III devices are to be provided at Chapter 21: Relay & Electronic Interlocking Page 462 of 530 (i) External Lightning Protection on Top of Buildings housing S&T equipment. (ii) Class B/Type-I devices at the Input of Power Supply Equipment. (iii) Class C/Type-II devices at Output of Power Supply Equipment. (iv) Class D/Type-III devices at Indoor and Field Equipment. 21.7.2 Earthing for Electronic Interlocking (a) Earthing shall be provided as per approved specifications, drawings and code of practice. (b) To the extent possible, perimeter earth shall be provided around the Electronic Interlocking room. (c) Earth value shall be less than one ohm and shall be measured annually during dry season. (d) Copper tape (Bonding ring conductor) as per drawing mounted on insulated stand-off is provided to cover the maximum area in the Relay room and the connection to equipment shall be made at the nearest point. (e) Earth wire from Surge protection device to main earth terminal inside the room should be as straight and short as possible to provide a low impedance path for discharge of surge energies. (f) Earthing wires from electronic interlocking subsystems to main earth terminal shall be of distinctive color. Green or Green Yellow (GNYE) color is recommended for quick identification of a loose or disconnected earth wire. (g) All earth wires shall be as straight as possible and shall never be coiled. All Earth wires should be made of copper of adequate current carrying capacity and should never be less than 4 Sq.mm cross section. Chapter 21: Relay & Electronic Interlocking Page 463 of 530 Note: This Chapter has under mentioned Annexures S.No AnnexureNo. Description 1 21-A1 Relays for Railway Signalling 2 21-A2 Pre Commissioning Check List Note: This Chapter has under mentioned Maintenance Schedules in Appendix I 1 21-MS1 Maintenance Schedule of Control Panel 2 21-MS2 Maintenance Schedule of Relays & Relay Room 3 21-MS3 Maintenance Schedule of Electronic Interlocking Note: This chapter has under mentioned Drawings in Appendix II S. No Drawing No Description 1 21-D1 S&T Building Plan up to 4 Road Stations 2 21-D2 S&T Building Plan for 5 to 8 Road Station 3 21-D3 S&T building plan for End Goomties (EI) 4 21-D4 ASM Room Layout Plan 5 21-D5 SM Table with Dual VDUs 6 21-D6 Contact Configuration (8F/8B) & (12F/4B) Contact Analysis Format (8F/8B), Contact Analysis with Posting 7 21-D7 of Contacts (12F/4B) (2 Sheets) 21-D8 Bonding & Earthing Connections for Signalling Equipments 8 (RDSO Drg) Chapter 21: Relay & Electronic Interlocking Page 464 of 530 Para No. 19.6.1, 21.2.1(b) Annexure: 21-A1 Relays for Railway Signalling 1.0 Relays in General (a) Relay Working Principle: A relay is an electromagnetic device, which is used for closing or opening of an electrical circuit. The relay may be classified as Shelf type and Plug-In Type. Plug-in-type relays which are plugged in to prewired terminal boards. It works on electromagnetic principle. Each relay has a base electromagnet, armature, contact spring, contacts, transparent cover, and handle. It works on a low current. A non-magnetic residual pin is fixed on the inner face of armature, in all relay except magnetic latch relays. When current is applied through the coil, it sets up a magnetic flux through the bar magnet, core, L shape heelpiece and armature. 2.0 Metal to Carbon Line Relay - Non- AC Immunized Relays (a) QN1 Style Relay: This is used as internal relay for all control and detection circuit except in external circuits of AC RE area. It`s specification No-B.R.S. No: 930A.Though it is immune to 300 Volt AC 50Hz but only in emergencies can be used in RE area with protection against AC Interface (b) QS3 Style Relay: It is sensitive line relay. It works on a low current. It works on 12 V DC. It`s Specification is B.R.S. 930A. (c) QB3 relay is biased neutral line Relay: It works on 12 V DC and has a contact configuration of 4F/2B.it is a biased relay. Its Biasing stands good up to 240 Volt DC. This is confirming to BRS Specification No.930A. (d) QNN1 Style Relay: This comprises two neutral line relays whose contacts and magnets are mounted side by side with a common heel piece on a base. These two relays operate independently to each other and also have equal number of front and back contacts. It is based on BR specification 960. 3.0 Metal- Carbon - AC Immunised Q- style line relays (a) AC Immunised DC neutral line Relay: The relay design shall be inherently such that the immunisation is achieved intrinsically without use of any external means. The relay shall not make any of its front contacts when 1000 V (r. m. s) of 50 Hz AC is applied at any instant to the terminals of relay coils. The relay shall not break any of its back contacts when 300 V (r. m. s) of 50 Hz AC is applied at any instant to the terminals of relay coils. This is confirming to IRS Specification No. S60 –78. Usage: these relays are used as interface relays in Electronic Interlocking systems. (b) QNA1 Relay: The immunisation is achieved by provision of a copper slug on the core at its armature end. In all other respects, it is similar to QN1.Its Specification is BR specification no. 931A. Usage: These relays are used as external relays. (c) QBA1 Relay: This is a DC biased AC immune neutral line relay. A copper slug is provided on the core for immunisation and a permanent magnet is provided on the core for Biasing. It does not operate if 20 times of the rated voltage is applied in reverse direction. It’s specification is BR Specification No. 932 A. Chapter 21: Relay & Electronic Interlocking Page 465 of 530 (d) QBCA1 Relay: This is similar to QBA1 relay but having two heavy-duty front contacts. It can carry 30A inductive current at 110 V through its front contact. The back contact can carry 3A continuous and 2A switching current like any other relay. Its Specification is BR specification no. 943.Usage: These relays are used as Point contactor relays. (e) QSPA1 relay: Only this relay is permitted to be used as the repeater for immunised ‘Q’ series track relays (QBAT & QTA2), due to its slow to pickup character. Provision of a copper slug between the core and the heel piece behind and a magnetic shunt between the core and the armature at the front contact make this relay slow to pickup. Features of QSPA1 relay are: (i) Slow to pick up by 540 /600 milli seconds.(ii) Less slow to release by 140/200 milli seconds and immune to AC. This made to BR specification no. 933A. (f) QL1 relay: This is a magnetically latched DC line relay. This relay remains in full operated condition though the feed to the relay is cut off. This relay has two coils namely operate coil (R) and release coil (N) and a permanent magnet. This made to BR specification no. 935A.Usage : these relays are used as latch relays in block instruments etc. 4.0 Track Relays Track relays shall always be of metal to carbon contact type & normally be of plug in type, unless otherwise specially permitted. In non electrified area, the following relays shall be used: 9 ohm DC non-AC immunized (plug-in type). In electrified area, the following relays shall be used:9 ohm DC neutral, AC immunized.9 ohm DC biased, AC immunized. Double element motor type relay, operating on 83 & one third Hz in AC traction area and 50 Hz in DC traction area shall be used. Vane type relays may continue in use till replacement. Relays for track circuit provided with coded, pulsed, electronic (audio frequency or high frequency track circuit), shall be of an approved type of track/line relay or as recommended by manufacturer. (a) QT2: The construction of this relay is similar to that of a Q - Series line relay except that its contact load is reduced drastically. The relay is more sensitive and workable on a low voltage.QT2 relay has only one core and 2F - 1B contacts. The back contact is used for cross protection for TPR circuit. This has a single coil unlike the shelf type relay, which has two coils with open ends. Usage: it is used as track relay in Non-RE area. (b) QTA2: Copper slug is provided on the core to achieve AC immunity. It's pick up voltage is 1.4v and pick up current is 140 ma approximately.QTA2 relays are available in 9 Ohms coil resistance with 2F/1B contact configuration. This relay requires more D.C. operating power and it take more time to pick up and drop due to the copper slug. New Installations: This can be used Upto 450 meters track Circuit Lengths in RE Areas with Choke at both ends. ii. Existing installations: This can be used Upto 450 meters track Circuit Lengths in RE Areas with Choke at the Relay end with high traction return current of 1000 Amps and up to 350 meters track circuit length without choke at the Relay end with low traction return current of 600 amps. Usage: used as track relay in RE area. Chapter 21: Relay & Electronic Interlocking Page 466 of 530 (c) QBAT: It's pick up voltage is 1.75 V and pick up current is 175 ma approximately. This is achieved by the provision of a biasing permanent magnet on its core along with its copper slug. It has only one core and 2F-2B contacts. This can be used Upto 750 meters track Circuit Lengths with choke in RE Areas. This is made to RDSO specification. No. 84/88. Usage: it is used as track relay in RE area. 5.0 Timer Relays (a) Types & Usage of Timer Relays: These relays are used in the signaling circuits to release interlocking after certain period of time to ensure safety. Following types of Time Element Relays are in use (i) DC Thermal type (ii) Siemens Motorised Clock Work time relay (iii) Motor type (iv) Electronic type (b) DC Thermal Type Element Relay (QJ1): This type of relay employs heat operated contact associated with an ordinary DC Neutral Relay. It has a heating element (H) and a neutral line relay (R) which together energise an external line relay after a pre- set time delay. One of such type is “QJI” type relay. Features of this relay are: (i)