CH 19 Sections 4-7 PDF - Signalling Equipment
Document Details
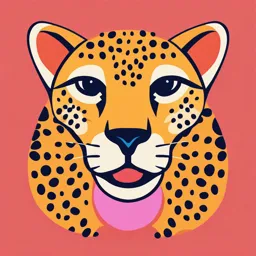
Uploaded by SolicitousOklahomaCity
null
Tags
Summary
This document details different sections of signalling equipment, including thick web switches, spring setting devices, and electrical point detectors. It also covers testing procedures crucial to the safety and efficient operation of signalling systems.
Full Transcript
Section 4: Thick Web Switches (TWS) 19.4.1 Conventional over-riding type of switches suffer from geometrical deficiencies like: (a) Weakness of tongue rail due to severe reduction of section by heavy machining. Tongue rails are further weakened by heavy wear and tear by...
Section 4: Thick Web Switches (TWS) 19.4.1 Conventional over-riding type of switches suffer from geometrical deficiencies like: (a) Weakness of tongue rail due to severe reduction of section by heavy machining. Tongue rails are further weakened by heavy wear and tear by traffic. So these are to be replaced frequently. (b) Obstruction to the wheel flange at the actual toe of the switch due to thickness of the tongue rail as well as due to switch entry angle. Hence a jerk is experienced by vehicles on account of these obstructions. (c) Twist in the track over a short distance on tongue rails machined from rail of same cross section, due to overriding nature of the tongue rail. (d) Structural weakness of the entire switch assembly to withstand lateral forces at higher speeds. 19.4.2 Thick Web Switches (TWS) overcome deficiencies of conventional over-riding type of switches. These are non-over riding type: (a) Thick web switch has wider switch opening of 160 mm (as against of 115 mm of conventional over riding type of switches). (b) Ground connection along with clamp lock used for operation of TWS and direct locking of tongue rail with stock rail shall be of approved type. (c) For operation and clamp locking of TWS, electric point machine of approved type with requisite throw shall be used. 19.4.3 For ground connection and clamp lock as per RDSO Drg. No. RDSO/S-3454 for 60 Kg rail and RDSO/S-3455 for 52 Kg rail, IRS point machine of 220 mm throw is used. (a) Out of 220 mm throw, during first 60 mm throw closed switch rail gets unlocked and open switch rail moves towards stock rail. During subsequent 100 mm throw both switch rails move simultaneously thereby open switch gets closed and closed switch gets opened by 100 mm. During final 60 mm throw, closed switch gets locked and open switch rail moves 60 mm further resulting in total opening of open switch by 160 mm. (b) Provides direct locking between tongue rail and stock rail in closed and open position. (c) No stretcher bar is used and both the tongue rails move independent of each other. Chapter 19: Installation, Testing & Maintenance of Signalling Equipment Page 394 of 530 19.4.4 Spring Setting Device (SSD) SSD of approved type shall be provided at junction of Rail head (JOH) to assist in proper setting of switch up to junction of Rail head (JOH). (a) SSD is placed between sleeper number 13 and 14. (b) SSD is insulated from both the rails. (c) SSD installation and maintenance is responsibility of Engineering Department. 19.4.5 Ground connection and clamp lock for Thick web switches shall be installed as per concerned RDSO drawings/approved drawings and installation guidelines. 19.4.6 Obstruction Test The detector slides, lock slides and drive rod must be so adjusted with 5 mm thick test piece placed between the switch and gauge face of stock rail at 150 mm from the toe of the point. The following to be observed: (a) Friction clutch de-clutches the motor from mechanism. (b) The point cannot get locked either by clamp lock or by locking segment inside the point machine. (c) Lock segment does not enter into the notches of locking slides. (d) Switch detection contacts do not make. (e) The slipping current is not exceeding twice of the normal working current. 19.4.7 Insulation Test (a) Point machine: Check that point machine is insulated from ground connection. (b) Spring setting device: Insulated from both the rails. (c) Clamp lock assembly: Check that it is insulated from both the rails. Chapter 19: Installation, Testing & Maintenance of Signalling Equipment Page 395 of 530 Section 5: Installation of Electrical Point Detector (EPD) 19.5.1 Electrical point detector of approved type shall be used. Normally it shall be installed beside the close switch leading to high-speed movement, clear of all infringements as per approved plan and drawing. (a) Detectors shall be mounted either on the left or on the right-hand side of a point layout clear of infringements. (b) The detectors shall be mounted on extended sleepers or as per any other approved arrangement. (c) Contacts shall be adjusted so that they make or break at the same time. Shunt contacts shall be adjusted so that they do not make before the detector contacts break. In AC traction area shunt contact shall not be used. Care shall be exercised to check that the detection contacts flex a little after they are closed. (d) All nuts and screws shall be tightened. Check nuts with spring washer shall be provided. (e) After installation before connecting the detector slide, the slides shall be pulled by hand to check for free movement. Binding, if any shall be attended to. (f) The lock slide shall be pulled and it shall be checked that as soon as the roller is lifted above the slot in the lock slide, the normal or reverse contacts are open and the shunt contacts are made. The electrical detector must be so adjusted that with 3.25 mm thick test piece obstruction placed between the switch and the stock rail at 150 mm from toe of the switch - The electrical detector contacts shall not make. (g) To keep the slides in correct position the locating marks on the switch and lock slides shall be made use of. 19.5.2 Circuit Controller: These shall not be newly installed normally (except in few Installations like LC Gates) and the existing one to be replaced in phased manner. Railways still having these equipments may please refer the earlier version of SEM Part-II, September 2001. Section 6: Signalling Relays For information on Signalling Relays, Refer to Annexure: 21-A1. 19.6.1 Relays – General Requirements: Refer to para 21.2.1 19.6.2 Installation of Relays: Refer to para: 21.2.2 19.6.3 Sealing of Plug-in Relays: Refer to para 21.2.3 19.6.4 Maintenance of Relays: Refer to para 21.2.4 19.6.5 Periodical Inspection of Relays: Refer to para 21.2.5 19.6.6 Replacement of Relays: Refer to para 21.2.6 Chapter 19: Installation, Testing & Maintenance of Signalling Equipment Page 396 of 530 Section 7: Fuses 19.7.1 (a) Fuses shall be of approved type and appropriate rating. When fuse is not provided with fuse blown off indication, additional indication circuit may be provided. (b) At the time of commissioning of any signalling installation, the normal load current of every circuit shall be measured and recorded. These recorded values shall be checked with the theoretically obtained values. Fuse of correct capacity which should be not less than 2.5 times the rated current, shall be provided. (c) When there is a case of fuse blowing off, the concerned circuit current shall be measured and compared with the original recorded value. If there is a variation, action shall be taken to locate and remove the defect before a new fuse is inserted. (d) For LED signal aspects, fuse of prescribed rating (0.6 Ampere if not prescribed otherwise) shall be used. 19.7.2 Fuse change over system: Fuse Auto Changeover System with monitoring panel and alarm facility along with audio & visual indications suitable for signaling installations of Railways may be used for minimising failures due to fuse blown off. The changing over of circuit operation from main fuse to spare fuse shall be automatic, without affecting the functioning of signaling circuits, when main fuse is blown off. At every change-over, audio/visual indication shall appear and Equipment shall work either on 24 V DC, 60 V DC or 110 V AC, Reverse polarity protection and overload protection voltage may also be provided in the power supply circuit. The system shall be of approved type. These shall be maintained as per Annexure: 19-MS5. Note: Electrical signalling equipment shall be painted in accordance with the approved Colour Scheme Section 8: Testing of Signalling Circuits 19.8.1 General The checking and testing of signalling installations may be divided into five different groups as detailed below: (a) Physical inspection of the installation. (b) Checking of the wiring and cables. (c) Testing of the individual circuits. (d) Testing of the individual apparatus. (e) System testing of the installation. Chapter 19: Installation, Testing & Maintenance of Signalling Equipment Page 397 of 530