Ceramics PDF
Document Details
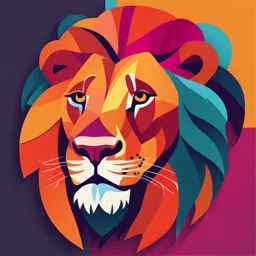
Uploaded by IntimatePyramidsOfGiza
UC Irvine
Tags
Summary
This document covers the different types of ceramics, their properties, and manufacturing processes. It details the process of manufacturing ceramics from raw materials to finished products.
Full Transcript
CERAMICS Ceramics: Picture -Crystalline ceramics some similar to PM (Powder metals). -ceramics don’t deform, they break; essentially they are brittle -can withstand large compressive forces, but not tensile or bending forces (due to the tensile component) -ceramics tend to be...
CERAMICS Ceramics: Picture -Crystalline ceramics some similar to PM (Powder metals). -ceramics don’t deform, they break; essentially they are brittle -can withstand large compressive forces, but not tensile or bending forces (due to the tensile component) -ceramics tend to be a very hard material -crystalline structures in general have a higher melting point than metals -three types ceramic materials: traditional, new, and glasses traditional: made from minerals occuring in nature EEE new ceramics: synthetically produced raw materials and embrace a wide spectrum of items such as cutting tools, arti cial bones, etc. IEaaitinal a consistencyofpastedetermines the itfor neitnatep tif Techniques reducingparticle sizeforceramicscrushing grinding Plastic meaning that material is malleable Process: the moldedintoobjects Prepare materials canbe -Materials tend to be natural (obtained from earth and crushed into clay and glass), synthetic (mined but heavily processed to change characteristics), -Mining and processing to powder is similar to that of powder metals Form green (weak; as strong as the chemical coat) shape: used to classify by material families; either crystalline, clay based, or glass Sinter ( ring; Glass → Heat treat) Finishing (any other process needed ) whendried beforefiring crystalline Slip casting: used to form a green shape for a ceramic from a slurry that contains the powder ceramic material in it. -This is used to for crystalline ceramics but also for some clay ceramic applications Picture thatanowwaters meaningmecontapsit.bg E A suspension of ceramic powders in water called a slip is poured into a porous plaster of Paris mold so water from the mix is gradually absorbed into the plaster to form a rm layer of clay at the mold surface. Thecompositionoftheslipistypically25 40 water remainderisclaymixedwithotheringredients ceramics t.aeEa i ii t.Ii ee newSome also water such as slip casting, extrusion, injection Ceramics: Crystalline: molding. -shaping processes can be divided according to the consistency of the mixture slipcastingmixtureis a slurrywith25 40 water inplastic condition ds 15 25 water clay shape I.BE ampi11fytho Ceramics: Clay based (and Very viscous crystalline mixtures): plastic forming, extrusion. -Clay and water is a very plastic mixture, and it can be deformed using applied forces, which methods are typically similar for those used for metal -extrusion: practiced with most materials with di erent variations. For granular IT materials, the preblended materials will be placed into a extruder which will compact it and produce a uniform shape, called a preform slug. Once the slug is produced, it is placed in a mold where it proceeds to be deformed similarly to the process of metals. For the nishing step, it is jiggered (tool use to shape the mold) and sent to be sinter -used in ceramics processing to produce long sections of uniform cross sections, which are then cut to required length. The extrusion equipment utilizes a screw type action to assist in mixing the clay and pushing the plastic material through the1die opening. This process is typically used to make hollow bricks, shaped tiles, drain pipes, tubes, and insulators - ALSO USED FOR STARTING CLAY SLUGS (PRESLUGS) FOR OTHER CERAMICS PROCESSES LIKE JIGGERING OR PLASTIC PRESSING Plastic forming: Deforming of the plastic mixture of clay and water which can be used to make ceramic objects; the mixtures typically have 15-25% water. The two methods within plastic forming, manual which is done by hand, and mechanized which is by a machine Jiggering: mechanized of potter’s wheel method (round table that rotates on a vertical spindle, powered by either motor or foot operated treadle, methods of hand modeling, throwing, and molding are used) It is used to produce large number of identical items Ceramics: Drying and ring: similar to PM. -When ceramics dry, the water that occupies a given volume leaves and evaporates. This causes shrinkage within ceramics parts and can up to 20% smaller dimensions Watermustberemovedfromthebodyofclaybeforefiringbutdoingreducesthe volumeofthe piece Tryingftp aYy accomplished theredfamishedaEcontried toacheive ayhfchaimiersifnitnenountetmhp.fr Afterdrying ceramtic issaidto be in a GRL L N S 1111 FIII.FI mentprocessthat Insintering the sinters bondsaredeveloped ceramic between material itisperformed in afurnace orkiln theceramicgrainswhichisaccompaniedby densification reductionof porosity shrinkagealsooccursin firing Ceramics: way in which glass parts are made: Flat sheet: Float, rolling, drawing, blow molding (parison pressing, blowmolding), pressing, centrifugal casting. Blow molding: glass is melted in a furnace to a viscous state (not completely liquid) and forms a blob of glass or the gob. The gob is then placed into the mold that will form the neck geometry of the bottle. It is then forced into the mold through vast amount of methods (such as compressed air) which it then eventually forms the parison (the pre bottle shape that has a cavity in the gob and the neck geometry). The parison is placed into the mold with the full shape of the bottle and compressed air is blown in and the glass assumes the shape of the mold fully. As the glass cools, it will need to be reheated in order to keep pliable and formable. Pressing: gob a glass is fed into mold from the furnace and pressed into a shape by a plunger. The plunger is retracted and the nished product is removed Centrifugal glass casting: viscous glass is placed on a mold, then mold is rotated and the glass ows towards the sides of the mold. As the rotational speed increases, the curvature of the glass will become more pronounced Rolling: starting glass is squeezed through opposing rolls whose separation determines the thickness of the sheet Float: glass ows directly from its melting furnace onto the surface of a molten tin bath. The highly uid glass spreads evenly across the molten tin surface, achieving a uniform thickness and smoothness. After moving into a cooler region of the bath, the glass hardens and travels through an annealing furnace Danner Process: DRAWING process for glass tubing. Molten glass ows around a rotating hollow mandrel through which air is blown while the glass is being drawn. The air temperature and its volumetric ow rate and drawing velocity determine the diameter and wall thickness of the tubular cross section include windowglass containers lightbulbs etc majorcategories ofglassproducts Ceramics: Glass: Tempering (residual stresses), laminated glass (bulletproof), annealing. Residual Stresses: tempered glass is typically produced over annealed glass because it tends to break in smaller pieces compared to the latter -the method to produce tempered glass is to induce compressive residual stresses in the surface by heating the glass then cooling surfaces quickly - Annealinginvolvesheatingtheglasstoanelevated temperature itforacertain periodtoeliminate holding glassto coolingthe supressstress stresses temperaturegradientsthen formationfollowed slowly bymorerapidcooling tempering increasestoughness oftheglass laminated glass by twopiecesofglassoneithersideofatoughpolymer bulletprooffabricated sanwiching sweet Ceramics: Design: No sharp corners, no tensile loading, good for wear resistance, manufacture to desired shape and wide tolerances (machining very di cult and expensive). yiompression