CENG 110 Construction Estimating PDF
Document Details
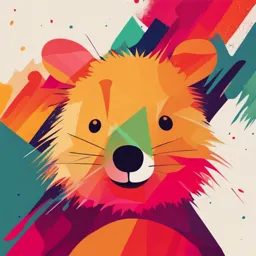
Uploaded by ReasonablePraseodymium
Cavite State University
2024
Tags
Summary
This document provides a learning hand-out introducing construction estimating, including construction phases, processes, cost estimation methods, and more. It's intended for use in a course or class related to construction.
Full Transcript
1 Lesson 1 Introduction to Construction Estimate (Quantity Survey) Learning Objectives: Upon completion of the lesson, the learners will be able to: 1. Define construction cost estimates. 2. Identify the various construction...
1 Lesson 1 Introduction to Construction Estimate (Quantity Survey) Learning Objectives: Upon completion of the lesson, the learners will be able to: 1. Define construction cost estimates. 2. Identify the various construction phases and processes. 3. Differentiate how construction estimates are classified. 4. Enumerate the elements of construction estimates. 5. Discuss technical specification 6. Explain the steps in construction estimating Construction Cost Estimate Construction cost estimating is the process of forecasting the cost of building a physical structure. Project owners use cost estimates to determine a project’s scope and feasibility and to allocate budgets. Contractors use them when deciding whether to bid on a project. You usually prepare estimates with the input of architects and engineers to ensure that a project meets financial feasibility and scope requirements. Construction Phases and Processes 1. Commissioning a Project: Commissioning is essentially a verification process that ensures a builder designs, constructs, and delivers a project according to the owner’s requirements. It begins early in the construction process and can last until up to a year of occupancy or use. A commissioning provider carries out commissioning, usually a firm with experience in commissioning buildings that serve particular functions. 2. Determining Requirements: The first real step in constructing a project is a pre-design phase or planning phase. The pre-design phase involves defining a project’s requirements: what its function(s) will be, how much it should cost, where it will be located, and any legal requirements it must comply with. 3. Forming a Design Team: The project owner contracts with an architect who will then select other specialized consultants to form a design team. Complex projects and projects which require meeting specific design requirements — such as acoustics or housing hazardous materials — will have more specialized consultants on board to ensure the design meets requirements. The architect is generally responsible for overseeing and coordinating the design process, though for some projects (such as industrial construction), an engineer may be one of the people overseeing design. 4. Designing the Structure: This step deals with the architect creating a series of designs. The architect works first with the owner to decide on the broad strokes of the design and then increasingly closely with the other members of the design team to flesh out the structure’s design in accordance with requirements. Designing thus progresses from a schematic design phase, when the architect presents a high-level design to the owner for CENG 110 2024-2025 2 approval, to a design development phase, when the architect works with the design consultants to decide on specifics of the construction design. The last step is the construction documents phase, i.e., creating construction drawings and specifications from which the contractor will build. 5. Bidding Based on the Scope of Work: Once the construction documents are finalized, they are released to contractors who wish to bid on the project. Along with these bidding documents, they include instructions on how to submit bids, a sample of the contract agreement, and financial and technical requirements for contractors. These documents, which effectively define the scope of the work, are the basis on which contractors prepare their estimates. For more on how to develop a statement of work, consult this guide. To ensure fair bidding, all contractors receive the same information, and the project owner usually selects the lowest qualified bidder. This bid tabulation template can help you compile your estimate. 6. Signing the Contract: Once the contractor has been selected, they execute a set of contract documents with the owner. The contract documents encompass the bidding documents, which now function as a legal contract between owner and contractor. Contracts can follow a number of models, depending on how complete the construction design is and how the owner and contractor bear risks. One of the basic models is a lump sum (also called a stipulated sum or turnkey) contract, which involves the contractor bidding a fixed sum for the total project and agreeing upon it when the project’s design is virtually complete. A unit price contract allows for more flexibility in design by having the owner pay the contractor per number of units they build. A cost-plus contract, signed when the design is incomplete, has the owner pay for all costs plus a predetermined fee for the contractor. A variation of this is cost plus a fee with a guaranteed maximum. 7. Construction: During the construction phase, the contractor oversees building in accordance with the construction documents. A general contractor will hire specialized subcontractors for different sets of construction tasks, such as plumbing or foundation work. Throughout the construction process, the contractor engages in careful cost control, comparing actual expenditure with forecasted expenditure at multiple points in the construction process. Cost control ensures that the contractor is actually able to turn a profit. This budget template can help you compare actual costs to estimated costs. 8. Close-Out: When the builder comes close to finishing a structure, the contractor requests the architect perform a substantial completion inspection in which the architect verifies the near-complete status of the project. At this stage, the contractor provides the architect with a document called the punch list, which lists any incomplete work or needed corrections. After the architect inspects the structure, they will add any additional incomplete items to the punch list. CENG 110 2024-2025 3 9. Completion: After the contractor completes all the incomplete work detailed on the punch list, the architect performs a final inspection. If the contractor has completed the structure according to construction drawings and specifications, the architect will issue a certificate of final completion, and the contractor is entitled to receive the full payment. Note: An alternative method of project delivery is the design-build process, which integrates building design and building construction. Instead of contracting first with a design team and then with a contractor, the owner contracts with a design-build firm, which handles both functions. The main strength of this approach is greater alignment and coordination between design and construction and a reduction of construction missteps. Accountability rests with a single party, which owners may appreciate. It can also save time and increase efficiency, and design-build processes are likely to be significantly cheaper than conventional design-bid-construct processes like the one detailed above. Types of Construction Cost Estimates Construction cost estimates can be classified into three primary categories according to their functions: design estimates, bid estimates, and control estimates. Each category reflects the way in which you use the estimates. Design Estimates: These estimates, prepared during a project’s pre-design and design phases, start with an order of magnitude estimate, or screening estimate, which determines which construction methods and types are most feasible. Next comes the preliminary estimate, or conceptual estimate, which you base on the schematic design. Then comes the detailed estimate, or definitive estimate, which you base on design development. The last of the design estimates is the engineer’s estimate, which you base on the construction documents. A simple template can help give an initial assessment of costs involved in a project. Bid Estimates: Contractors prepare bid estimates when bidding to construct the project. Contractors will draw from a number of data points to prepare their estimates, including direct costs, supervision costs, subcontractor quotes, and quantity take-offs. Control Estimates: Prepared after the signing of a contract agreement and before construction gets under way, the control estimate functions as a baseline by which you assess and control actual construction costs. The control estimate also allows contractors to plan ahead to meet upcoming costs and determine the project’s cost to completion. CENG 110 2024-2025 4 Elements of Construction Estimate The following are key terms and concepts in creating an estimate, but be aware that there’s a large degree of overlap between some of them. 1. Quantity Take-Off: Developed during the pre-construction phase, a quantity take- off measures the materials and labor needed to complete a project. 2. Labor Hour: The labor hour, or man hour, is a unit of work that measures the output of one person working for one hour. 3. Labor Rate: The labor rate is the amount per hour one pays to skilled craftsmen. This includes not just the basic hourly rate and benefits, but the added costs of overtime and payroll burdens, such as worker compensation and unemployment insurance. 4. Material Prices: Since the cost of materials is prone to fluctuation based on market conditions and such factors as seasonal variations, cost estimators may look at historical cost data and the various phases of the buying cycle when calculating expected material prices. 5. Equipment Costs: Equipment costs refer primarily to the cost of running, and possibly renting, heavy machinery, such as cement mixers and cranes. It’s important to note that the equipment in use influences how quickly you can complete the project, so the use of equipment actually impacts many costs outside of those directly associated with running the equipment. 6. Subcontractor Quotes: Most contractors will hire multiple specialist subcontractors to complete parts of the construction. You add these subcontractors’ quotes to the contractor’s total estimate. 7. Indirect Costs: Indirect costs are expenses not directly associated with construction work, like administrative costs, transport costs, smaller types of equipment, temporary structures, design fees, legal fees, permits, and any number of other costs, depending on the particular project. 8. Profits: To make a profit, the contractor adds a margin on to the cost of completing the work. Subcontractors do the same when preparing their own quotes. 9. Contingencies: Since even the most accurate estimate is likely to be affected by unforeseeable factors, such as materials wastage, an estimate will usually have a predetermined sum of money built in to account for such added costs. 10. Escalation: Escalation refers to the natural inflation of costs over time, and it’s especially vital to take into account for long-running projects. Some projects have escalation clauses that address how to handle this inflation. 11. Bonds: An owner will usually require a contractor to arrange for the issuance of a performance bond in favor of the project owner. The bond functions as a kind of CENG 110 2024-2025 5 guarantee of delivery. Should the contractor fail to complete the project according to the terms of the contract, the owner is entitled to compensation for monetary losses up to the amount covered by the performance bond. 12. Capital Costs: Capital costs are simply the costs associated with establishing a facility. These include the following: the cost of acquiring land; the cost of conducting feasibility studies and the pre-design phase; paying the architect, engineer, and specialist members of the design team; the total cost of construction, which covers not just materials, equipment, and labor, but also administrative, permitting, and supervision costs, as well as any insurance fees or taxes; the cost of any temporary equipment or structures that are not part of the final construction; the cost of hiring a commissioner; and the cost of inspecting the structure when it’s near completion. 13. Operations and Maintenance Costs: More a concern for the owner than the contractor, one accounts for operations and maintenance costs during the design phase. Making choices that lower the total lifetime cost of a building may result in higher construction costs. Operating costs include land rent, the salaries of permanent operations staff, maintenance costs, renovation expenses (as needed), utilities, and insurance. 14. Variances: Owners will often allocate construction budgets that are larger than cost estimates because even good, thorough cost estimates have a tendency to underestimate actual construction costs. This can happen for a number of reasons. For example, wage increases, which can be difficult to forecast, will make construction costs rise. Seasonal or natural events, such as heavy rainfall, may call for action to protect construction or restore the construction site. Large projects in urban areas may face regulatory or legal issues, such as a demand for additional permitting. And lastly, owners who begin construction without finalizing the project’s design will over-budget to account for design changes and the inevitable cost increases that result from throwing a project off schedule Requirements in Estimating Bill of Materials 1. Have on hand all the things required: o Complete set of working drawings/plans of the project o Technical specifications of the project o Architect’s scale o Electronic calculator or adding machines o Pencils, erasers, paper, ballpens o Data about building materials preferably their current prices CENG 110 2024-2025 6 o Estimating worksheets o Construction contract, if necessary 2. Study carefully all the plans and specification to get a clear understanding of the various elements of the project and to know the materials required. 3. The plans and the specifications are meant to complement each other, but should there be discrepancies between the two, these should be referred to the architect/engineer in charge of the project. 4. If in the building plans, there are discrepancies between the scaled distances and the measurements indicated, it is usually the latter that prevails. Construction Specifications and Working Drawings The calculations of the bill of materials (the total listing of materials needed in building a project with corresponding current prices) are based on working drawings of the project (also known as the construction plans) and its construction specifications. Working drawings are the graphical presentation on paper that enable the reader to visualize and understand how the building would be constructed and how it functions. They contain details, measurements and how the various structural parts are to be put together to form the whole structure. The construction specifications are written provisions stating among others the construction methods to be followed, standards of workmanship and the kinds and quality of materials to be used. (There are varied examples from the internet of construction specifications, however, an example can be viewed in an estimate book by Tagayun, V. Estimating Bill of Materials. pages A.35 to A.41). The components of the working drawings/construction plans: Perspective drawing of the building Site development plan Vicinity map/Location plan Floor plans Elevations Transverse and longitudinal section Foundation plan including details of footings, columns, CHB walls Floor framing plans including details of beams, girders and slabs Roof framing plans including details of trusses/rafters Plumbing plan including details of septic tank and catch basin Electrical plan including load computations Mechanical plans as required Details of cabinets and closets, as required Details of stairs and handrails, as required CENG 110 2024-2025 7 Details of doors and windows, as required Interior designs, etc, as required Work Breakdown Structure A work breakdown structure (WBS) is a key project deliverable that organizes the team's work into manageable sections. The work breakdown structure is a hierarchical decomposition of the total scope of work to be carried out by the project team to accomplish the project objectives and create the required deliverables. A WBS also provides the necessary framework for detailed cost estimating and control along with providing guidance for schedule development and control. (https://online.visual-paradigm.com/diagrams/templates/work-breakdown-structure) 8 Steps in Construction Estimating https://www.procore.com/library/construction-estimating Construction estimators follow the same basic steps whether they work for a general contractor, specialty contractor, or owner. When making a construction estimate, estimators are typically working to come up with an accurate price for a specific project as part of a competitive or negotiated bidding process. In general, construction estimators follow a process that begins with reviewing bid documents, including construction specifications and contract documents, and includes steps to account for every known cost, including materials, labor, insurance, and overhead. By the time an estimator is finished, they will have prepared a construction estimate that takes into account all required costs as well as a markup for profit and contingency. 1. Review the bid package. The bid package contains all of the documents necessary for bidding: owner- contractor agreements, bond forms, general conditions, supplementary general conditions, and construction specifications. Contractors who bid on a project are bound to complete the work laid out in the bid package, so a professional estimator spends a significant amount of time to ensure they are familiar with every aspect of the project. Drawings are typically subdivided according to their purpose: site, architectural, structural, mechanical, electrical, and more. Both general contractors and specialty contractors will review the documents, but specialty contractors often refer only to the documents that are relevant to the work they will perform on the project. When reviewing the bid package, construction estimators generally follow a standard process. 1. Ensure that all drawings and specifications are present. CENG 110 2024-2025 8 Documents may be numbered sequentially or subdivided according to the preference of the design firm, so estimators take care that they have everything necessary for an accurate estimate. 2. Get an overview of the project. With a quick scan through the specs, estimators get a rough idea of the scope of a project, its material needs, and the quality of finishes. 3. Evaluate structural requirements. By reviewing structural drawings, estimators begin to understand the material and equipment needs of the building. 4. Review mechanical, electrical, and plumbing (MEP) requirements Estimators take into account the ways in which a building’s MEP needs will influence the construction process for the building, including potential underground work. 5. Identify any nonstandard items. Contractors tend to specialize in certain types of work, so estimators need to pay special attention to unusual floor plans, features, or finishes that could affect the project’s cost. Throughout the estimating process, the estimator will continually refer back to the bid documents to ensure that their estimate encompasses every aspect of the stated specifications and requirements. By getting an overview of the documents, the estimator takes their understanding of the project through every phase of building a comprehensive and accurate estimate. After getting an overview of the documents, an estimator for a general contractor will also subdivide the project into work packages. Work packages may be later assigned to specialty contractors, and they also serve the important purpose of ensuring that all work is accounted for and no work is assigned twice. By reviewing the technical specifications (also called construction specifications or specs), the estimator can clearly see the scope of work according to various divisions of the Construction Specification Institute (CSI)’s MasterFormat: concrete, masonry, metals, finishes, plumbing, and dozens more. For example, the estimator may create one work package that includes the materials and labor for rough-in plumbing and another that covers windows and installation. Many such work packages will be created for a single construction project. Dividing the project into work packages requires extreme attention to detail: The estimator must be careful that every aspect of the project is included in a work package, or there will be work that has not been assigned to a contractor. Later in the project, the general contractor will be on the hook for these unaccounted project costs. CENG 110 2024-2025 9 The estimator must also be sure that no project detail is included in multiple work packages, or the ultimate bid may be too high to be competitive since costs are multiplied unnecessarily. In cases where an aspect of the project is divided into multiple work packages, the estimator must clearly define the scope of each work package to ensure that each portion is adequately completed by the parties responsible. Once an estimator has divided all of the work into packages, the general contractor can solicit bids from specialty contractors for some or all of the required construction work. 2. Conduct a site visit. In some cases, a site visit is required before submitting a bid. However, a site visit is recommended in nearly all cases, as estimators can get a better sense about site conditions from a thorough visit rather than simply relying on elevation drawings or photographs of the proposed construction site. Depending on the type of project, a specialty contractor may be less likely to perform site visits, relying instead on the documentation provided by the project’s owner and general contractor. The main purpose of a site visit is for the estimator to better understand the conditions of the site and how those are likely to influence the project costs. For example: A site with poor drainage, difficult subsurface soil conditions, or adjacent buildings could add complexity and cost to a project. A site lacking easy access could make it more difficult to maneuver equipment and materials, increasing costs. A site with poorly located utilities (water, electricity, etc.) could add underground work requirements that raise the cost. During a site visit, an estimator will make notes, take photographs, and collaborate with contractors to determine the potential influence the site may have on delivering the project successfully. In addition to the site itself, the estimator should also familiarize themselves with the surrounding area if they aren’t already aware of: Local requirements (codes, permits) or regulations (noise, working hours, parking) Availability of specialty contractors and construction equipment rentals Nearby roadways, which may need to accommodate heavy equipment or delivery vehicles Overall, the site visit is critical for estimators, who must determine the feasibility and cost of delivering the project according to specifications in a set location. 3. Perform a material takeoff. CENG 110 2024-2025 10 Estimators perform a material takeoff (also called a quantity takeoff) by reviewing the construction documents and counting every item that is required for the project. Material needs are typically listed according to the way they are measured. For example: Quantity (e.g. doors) Area (e.g. drywall or flooring) Volume (e.g. concrete) Length (e.g. wire) On large construction projects, the owner or engineer may create a bill of quantities (BOQ) to simplify the bid leveling process. This document breaks down the scope of work into an itemized list of activities and materials. Even when a BOQ is provided, most contractors still perform a takeoff to verify the quantities and identify discrepancies. General contractors will typically do a takeoff in order to create accurate work packages— either to complete themselves or assign to specialty contractors. A specialty contractor typically reviews the specifications to perform their own material takeoff in order to ensure they have an accurate count before reaching out to suppliers and vendors. After completing a takeoff, estimators have a comprehensive list of every material that will be required to complete the project. Additionally, estimators will use information from the takeoff to determine what equipment will be needed for each work package. Estimators may perform a manual takeoff, which involves using paper copies of drawings, rulers, highlighters, digital measuring tools, and pencils to count and measure the required materials using the specifications. Nowadays, most estimators rely on digital takeoffs using construction estimating software, which greatly speeds up the process. Nonetheless, many estimators still double-check the accuracy of the digital takeoff to ensure that their estimate is accurate. With this information, contractors are able to work with material and equipment suppliers to get pricing information that they can use while creating a bid. 4. Solicit pricing from suppliers and vendors. With a definitive list of materials and equipment, specialty contractors begin to work with suppliers and vendors to get pricing information. Specialty contractors have to be mindful of a few things when pricing materials. Material waste requires ordering extra materials. Contractors should work to eliminate unnecessary material waste, but some waste (due to material sizing, for example) is inevitable. Ideally, a contractor will be able to look back at past projects to calculate the expected amount of waste. Bulk pricing may dictate order sizes. For instance, a contractor may need 37,000 cubic yards for a project but find it is more cost-effective to purchase 40,000 cubic yards due to supplier pricing structures. CENG 110 2024-2025 11 Quotes have limited lifespans. A specialty contractor who receives a quote for materials needs to ensure that quote is valid long enough to have their bid accepted and order materials for the project. Contractors who do not already own equipment essential for the project will also need to reach out to equipment vendors to determine pricing for leasing or renting for the duration of the project. Since equipment may be owned, purchased, leased, or rented, contractors must determine how the project affects associated equipment costs (for example depreciation or maintenance) and build this information into their estimate. At this point in the estimating process, contractors will have the first definitive dollar figures that need to be included as project costs. From here on out, estimators will add more direct, indirect, and overhead costs to understand the true financial burden of the project from the contractor’s perspective. 5. Evaluate labor requirements. With information from the takeoff, estimators can also determine the labor necessary for a project. In short, the estimator needs to specify: Which roles are required for the project? How many hours of labor will be used to complete the project? How productive the crew will be given data past projects and information about the current project? For specialty contractors, the crew mix usually consists of tradespeople, laborers, and assistants. For general contractors, there may be project-specific managers or other professionals whose roles are considered direct costs because they are tied to one specific project. In either case, estimators must be sure to calculate the loaded labor rate for wages rather than simply multiplying total hours by hourly wage. The loaded labor rate includes: Wages Taxes Insurance (including health, dental, vision, or life insurance as well unemployment and worker’s compensation insurance) Retirement contributions Union dues Sick or vacation leave Estimators must include all of the costs associated with employing someone for the duration of a construction project, otherwise the estimate will not reflect the true cost of labor. 6. Determine insurance and bonding costs. CENG 110 2024-2025 12 Insurance and bonding mitigate risk for owners and contractors alike, but this benefit comes with a cost that must be included in project estimates. Nearly all construction companies require general liability insurance, and depending on company size, scope, and role, they may also have other policies, including: Builder’s risk insurance Errors and omissions or professional liability insurance Inland marine insurance Commercial auto insurance In addition to insurance, contractors working on public projects (and some commercial projects) may require a variety of construction bonds, including: Payment bonds Performance bonds Bid bonds Both bonds and insurance cost money for contractors, which means that the costs must be covered by the projects they complete. Generally speaking, bond and insurance coverage have annual costs, which contractors then spread across projects throughout the year. However, contractors may need to secure additional bonding capacity or insurance coverage for a specific job. In any case, estimators must add the cost of bonding and insurance requirements to the project estimate. 7. Calculate overhead and indirect costs. In addition to the direct project costs, estimators must also consider the indirect field costs associated with construction as well as the overhead costs required for running a construction business. Indirect field costs could include: Permits Trailers or temporary offices Site cleaning Professional services Equipment costs (depreciation, insurance, maintenance, taxes, and fuel) Software These costs, while not clearly laid out in the bid package, are necessary for the construction of a project. Therefore, estimators consider the rate for each of these items as well as the duration for which they’ll be needed (for example, in the case of a temporary site office). CENG 110 2024-2025 13 In addition to these indirect project costs, there are also general overhead costs, also known general and administrative (G&A) expenses. These are the cost of doing business— whether or not a contractor has projects to work on, they need to pay these expenses. To ensure that the business can keep operating, contractors need to wrap overhead costs into their estimates by spreading them out over all of their projects annually. A few common overhead expenses include: Rent for office space Administrative salaries Software subscriptions Utilities Taxes Depreciation Insurance Generally speaking, estimators consider the total expected annual revenue of the company as well as the total expected annual overhead cost. With these two figures, the estimator can allocate with reasonable accuracy a specific percentage of the overhead cost to each project. 8. Account for profit and contingency. After calculating all of the costs for a construction project, the estimator will adjust the total to account for both profit margin and contingency. The profit is the fee that the contractor earns for the contract—and that money can be reinvested to continue growing the business. Contingency, on the other hand, is a portion of the contract set aside for overruns and waste—which are generally to be expected on a construction project. Each construction business determines its own minimum attractive profit margin by considering growth goals, market conditions, and more. Similarly, contingency numbers vary significantly across the industry depending on type of construction, company size, and project risk. Many construction businesses usually add anywhere from 5-10% of the contract price to account for contingency. At the end of this process, the estimator has determined the sales price that covers all of the project costs—materials, labor, equipment, indirect field costs, overhead costs, and contingency—and returns a healthy profit. With this number in hand, contractors are prepared to submit a competitive bid or begin negotiations with a project owner or general contractor. CENG 110 2024-2025 14 Please take note that this Lesson 2 covers only partial topics advisable for the midterm exam! AY2024-2025 Lesson 2 Detailed Quantity Survey Learning Objectives: Upon completion of the lesson, the learners will be able to: 1. Discuss the methods in determining the quantities of materials needed per scope of work/elements. 2. Apply techniques in computing for quantities of materials An estimator must know how to compute the length of lines, areas of plain figures and volume of solids which may represent parts of building for which quantities of materials are to be estimated. (Tagayun, 2002). It is to take note that consistency in using dimensions is a must. One can adopt the metric system (meter, centimeter, millimeter). When computing, see to it that the considered measurements are in just a single unit. Conversions can be made as needed by using conversion tables (refer to Fajardo. Simplified Construction Estimate, Charter 1-3. Latest Ed.) In estimating quantities of materials, center line measurements are advisable. Other references consider inside dimensions. Allowances for wastage may be added to computed quantities. Lesson 2.1. EARTHWORKS Earthworks are engineering works created through the moving and/or processing of massive quantities of soil or unformed rock. Earthwork is done to reconfigure the topography of a site to achieve the design levels. Earthwork involves cutting and filling to achieve the required topography.(https://esurveying.net/land-survey/earthwork-volume- calculation) Cutting is the process of excavating earth material from a work location or borrow pits to achieve the desired topography. Filling is the process of moving excavated material or additional earth material to a work location to achieve the desired topography. Earthwork in excavation and backfilling of soil up to required depth is required for construction of foundation and trenches. Excavation and backfilling of soil is a very important part of construction process, and care must be taken. Correct measurement of excavation and backfilling is required because excavation cost is major part of the foundation construction. (https://theconstructor.org/practical-guide) CENG 110 2024-2025 15 VOLUME OF EXCAVATION: Volumes are computed from cross-section measurements by the average end area method. By the Average-End-Area method: Volume = L x (A1+A2)/2 where: Volume (metric) (m3) L is in meters A1 and A2 are in square meters. Also, where not practical to measure material by the cross-section method due to erratic location of isolated deposits, acceptable methods involving three dimensional measurements may be used to measure material in the original position. Equations for these measurements are: Volume (m3) = Length x Width x Depth (http://www.state.in.us/indot/files/Earthworks_Chapter_06.pdf) Measurements for volume are nothing more than applying basic distance and elevation measurements to determine the locations and elevations of points where the volume is to be determined. The key to volume calculation is the determination of area. Most volume calculation formulas contain within them the formula for an area, which is simply multiplied by the height to determine the volume. For instance, the area of a circle is pi times the radius squared. The volume of a cylinder is the area of the circle times the height of the cylinder. If an area can be determined, it is generally easy to determine the volume. (https://civilblog.org/) VOLUME OF EARTHFILL To estimate the quantity of earth fill needed to fill up hollow spaces in the building, compute its volume and multiply by 1.25. The 25% is added as allowance for compaction of the loose soil to be delivered. That is, Volume of earth fill required = volume of space to be filled x 1.25 Lesson 2.2. CONCRETE WORKS & METAL REINFORCEMENT Lesson 2.2.1. Concrete Works Estimating concrete components (that is the quantity of cement, sand and gravel) can be done through two methods. by volume method by using tables (tables from the required text book from the syllabus and other references) The volume method is generally used and can be applied in estimating the materials for all concrete members employed in a construction project. The concrete volume is being multiplied by factors appropriate for a specified class of concrete mixture in order to obtain the estimated quantities of cement, sand and gravel. CENG 110 2024-2025 16 To use tables from the text book and other references, the estimated quantities of cement, sand and gravel can be computed. However, this is only limited to concrete members with sizes specified on tables. In concrete proportioning, from Simplified Construction Estimate by Max B. Fajardo, the following table is suggested. Table 1. Concrete proportioning Note: the current common available cement in the market is 40 kgs/ bag Consider this sample problem 1: A concrete post 4.00 meters high with cross sectional dimensions of 40 cm x 40 cm is supported by a footing slab 20 cm thick by 1.20 meters square. Using a class A concrete, find the quantity of cement, sand and gravel if there are 12 posts. By volume method: 1. To find the total volume of 12 posts; V = (0.40)*(0.40)*(4.0)(12 units) V = 7.68 cu.m. 2. To find the total volume of 12 footing slabs; V = (1.20)*(1.20)*(0.20)(12 units) V = 3.456 cu.m. 3. To find the total volume of concrete, add no 1 & 2 Total Volume = 7.68 + 3.456 V = 11.136 cu.m. 4. To get the required quantities of cement, sand and gravel, refer to table 1. Cement = (11.136)*(9.0) = 100.22 bags say 101 bags Sand = (11.136)*(.50) = 5.57 cu.m. 5.75 cu.m. Gravel = (11.136)*(1.0) = 11.14 cu.m. 11.25 cu.m. Lesson 2.2.2. Metal Reinforcement Review the different deformed bar classifications from Building System Design. Estimation of steel reinforcement quantity for concrete slab, footing and column, beams CENG 110 2024-2025 17 etc. is crucial for the cost evaluation for the construction. Design drawings are used as a base for computing rebar quantity in different structural elements. The quantity and length of the main reinforcement is determined by the ‘Direct Counting Method’ that is, counting the number of reinforcement on one structure then multiplied by the total number of the same type or category in the plan. Under the direct counting method, the vertical and horizontal reinforcement are counted individually in the plan with due considerations on the hooks, bends, lap, splices and development lengths. For this learning guide, hooks, bends and splices length to be added, use (note: d= diameter of the bar): a. Hook/bend for main reinforcements for 180 and 135 degrees – add 13.5 d b. Splice length = 40d For other reinforcement parts such as lateral ties, stirrups, dowels, cut bars and others, steel bars should be selected from the various commercial lengths of bars (6.0m, 7.5m,9.0m, 10.5m and 12m). Keep in mind that unnecessary cuts/extra cuts should be minimized to avoid wastes. Tie wire for reinforcement joints should be cut to the minimum required length. The length of the tie wire depends upon the size of the bars to be tied on. Usual length ranges from 0.25m to 0.40m. Hence, there are 53 meters in a kilogram of tie wire. Hence, the following are some suggested steps in computing each structure. Calculate Steel for Footing Size of footing and its reinforcement details (bar size and spacing) shall be known from design drawings. After that, the following steps will be taken to compute steel quantity. 1. If spacing is given and not the number of bars, calculate the required number of bars for both directions. No. of bars = {(L or w – concrete cover for both sides) ÷ spacing} +1 where L or W: length or width of footing 2. Find the length of one cut bar Length of bar =(L or W–concrete cover for both sides) + 2*bend length where L or W is length or width of footing 3. Consider a commercial length of one bar and divide it by the result of step 2. Use the whole number. 4. Find the total number of cut bars needed. 5. Divide the result of #4 by #3. The answer is the number of deformed bars required. (Always mention the bar diameter and its commercial length when referring to deformed bars) CENG 110 2024-2025