Casting Technology – Part I PDF
Document Details
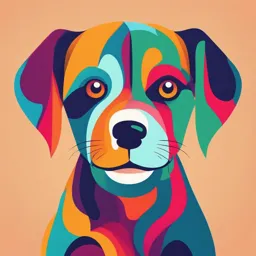
Uploaded by AccurateBoltzmann
Sabaragamuwa University of Sri Lanka
Amalka Samarathunga
Tags
Related
- Manufacturing Processes II PDF - Forming Technology - Part I
- Manufacturing Technology for Mechatronics - Casting and Welding (PDF)
- Manufacturing Technology Casting PDF
- Assiut National University Production Technology Final Exam 2023/2024 PDF
- Production Technology Lecture 1 PDF
- TDF Zusammenfassung WiSe 2021/22 Industrielle Revolution (PDF)
Summary
This document covers manufacturing processes, specifically focusing on casting technology. It details types of casting, materials, and process steps. It also discusses the advantages and limitations of casting materials, and explores where cast products are used and not used.
Full Transcript
Manufacturing Processes II ET22033 Casting Technology – Part I Eng. (Mr) Amalka Samarathunga BSc Eng Mechanical Engineering, M...
Manufacturing Processes II ET22033 Casting Technology – Part I Eng. (Mr) Amalka Samarathunga BSc Eng Mechanical Engineering, Mphil (Reading) Department of Engineering Technology, Sabaragamuwa University of Sri Lanka Manufacturing Processes II Module ET Module Title Manufacturing Processes 2 Code 22033 Credits 3 Lectures 2.0 Pre – Hours/Week Lab/ None GPA/NGPA GPA 2.0 requisites Assignments The aim is to identify and assess the capability of basic manufacturing processes for meeting product specifications, select and sequence Module machinery, tooling and accessories required for manufacturing simple Aim: products. Learning Outcomes LO-1: Describe types of material processing technologies LO-2: Describe types of material joining technologies LO-3: Demonstrate the knowledge the capability of manufacturing processes and determine processing parameters LO-4: Demonstrate the knowledge of methods of preventing process defects Relevant Learning Syllabus Outline Outcomes Casting Technology 1 Sand casting, process and accessories, Shell moulding, Slurry processes, Investment casting, LO-1, LO-3, LO-4 Die-casting, Centrifugal casting, Continuous casting, Melting practice, Casting properties and defects, Basic mould design. Casting defects and prevention Forming Technology 2 Cold and hot forming, press work, punching, blanking, piercing, rolling, extrusion, cup LO-1, LO-3, LO-4 drawing, wire drawing, drawing parameters, Forming defects and prevention Fabrication and welding technology 3 Fitting, limits and fits, tolerances, Joining and welding methods, process parameters for gas LO2, LO-3, LO-4 and arc welding, welding fixtures, welding defects and prevention Polymer moulding 4 Introduction to Injection moulding, Compression moulding, blow moulding, GRP moulding, LO-1, LO-3, LO-4 moulding defects and prevention Assessments Continuous Assessments (30%) Four (04) Quizzes (consider only 3 highest marks for final grade) Practical Assignments No cover-up assignments Final Examination (70%) Physical Examination 3 hour essay paper Reading Materials 1. Materials and Processing in Manufacuturing, E. Paul DeGarmo, J.T. Black, Ronald A, Kohser, Prentice Hall, Inc., 2003, 9 th Edition 2. Manufacturing Technology: Today and Tomorrow, Robert A Daiber, Erekson Thomas,L. , McGrawHill, 1991, 8th Edition 3. Introduction to Basic Manufacturing Process and Workshop,Technology, Rajender Singh, New Age International 4. Production EngineeringTechnology, J.D. Radford and D,B, Richardson, McMillan Press, Latest Edition. 5. Workshop Technology Chapman, Part III Casting Process Pouring molten metal into a mold cavity to create a specific shape. A process based on the property of liquid to take up the shape of the vessel containing it. A cavity of desired shape is made, contained in a mold. Carried out in a foundry. Process Selection 2 1 3 4 History of Casting Ancient process, started 5000 years ago. Jaivana- 50 tons cannon was built in 17th century in Jaipur. Used for making arrows, coins, knives etc. History of casting Foundry Shop Specialized facility where metal casting processes are carried out Common Casting Metals Gray iron Ductile iron Aluminum Steel Copper Zinc Lead Gray iron The most frequently used casting materials in industrial manufacturing Can be machined easily, tested for quality without using destructive methods Used for housings where the stiffness of the component is more important than its tensile strength. Cost-effective at high volumes Damping or vibration control High strength to weight ratios Dimensional stability Ductile Iron Casting For processes requiring greater strength than that provided by gray iron casting Improved wear resistance Stronger toughness Superior ductility Reduced weight Reduced shrinkage Lower cost Aluminum Casting Corrosion resistance High thermal/electrical conductivity Good mechanical properties and strength at high temperatures Steel Casting Exceptional wear resistance Resistant to shock or heavy loads. Corrosion resistance in aqueous environments and for applications involving elevated temperatures. Steel is often mixed with chromium, iron, and nickel to further improve its corrosion or heat resistance. Copper Casting Excellent electrical conductivity - electrical components. Good malleability Superior ductility Good conduction of heat However, copper and castings can be subject to surface cracking, porosity and formation of internal cavities - often mixed with other metals (silicon, nickel, zinc, chromium, tin and silver) to alleviate these issues. Copper Casting Only for Metals ? Thermo Plastic moulding Glass casting Concrete Resin casting Plaster of paris Wax casting Things to Consider When Choosing Casting Materials Level of volume required Fluidity Cost-effectiveness Melting temperature Cooling speed Wear resistance Weight Damping capabilities Where cast products are used? Automobile industry Ship-building industry Aerospace industry Manufacturing industry Household appliances Where cast products are not used??? CNC/ Products with high Machining dimensional accuracy Products subjected to Die Forging considerable cyclic loads CNC/ Products require good surface Machining finish 2 3 Metal Casting Steps Making mould cavity Material is first liquefied by properly heating it in a suitable furnace. Liquid is poured into a prepared mould cavity Allowed to solidify Product is taken out of the mould cavity, trimmed and made to shape Why Casting? Intricate shapes can be made by this process – Minimized Operations Wide Material range Tools required for casting molds are very simple and inexpensive. There are certain parts (like turbine blades) made from metals and alloys that can only be processed this way Size and weight of the product is not a limitation Good Engineering properties Limitations Surface finish & dimensional accuracy. Limitations in toughness & strength. Limitations in making thin & complex structures. Shrinkage & porosity. Casting defects. labour intensive process End Any Question?