BSD-REVIEWER PDF
Document Details
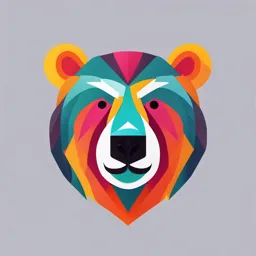
Uploaded by KeenHeptagon
Tags
Related
- Lei no 113-1992 - Codigo de Obras PDF
- National Building Code of the Philippines PDF
- Philippines National Building Code Implementing Rules and Regulations (2005) PDF
- مقـررات ملی ساختمان ایران - مبـحث اول - تعاریف - PDF
- Building Regulations and Authorities Having Jurisdiction PDF
- National Building Code of the Philippines PDF
Summary
This document discusses the National Building Code of the Philippines (NBCP), which governs building construction, design, and occupancy. It covers key provisions, enforcement mechanisms, and challenges in implementing the code. It further explores architectural codes and regulations in the Philippines.
Full Transcript
GROUP 1: BUILDING CODES Department of Health (DOH) I.The National Building Code of the Philippines Environmental Management Bureau (EMB) (NBCP), known as Presidential Decree No. 1096, is Housing and Land Use Regulatory Board a crucial legal framework that g...
GROUP 1: BUILDING CODES Department of Health (DOH) I.The National Building Code of the Philippines Environmental Management Bureau (EMB) (NBCP), known as Presidential Decree No. 1096, is Housing and Land Use Regulatory Board a crucial legal framework that governs the (HLURB) construction, design, and occupancy of buildings National Commission for Culture and the Arts and structures within the Philippines. (NCCA) 2.ENFOREMENT MECHANISMS PURPOSE OF NBCP -methods and processes used to ensure that 1. Ensure Structural Integrity individuals, businesses, and organizations comply 2. Promote Public Safety with regulations, standards, or laws of NBCP. 3. Encourage Energy Efficiency Permit and Licensing Requirements(Building 4. Regulate Building Use and Occupancy Permits, Licensing of Professionals) 5. Facilitate Compliance and Enforcement Inspections (Routine Inspections, Special Inspections) CRITICAL AREAS Compliance Monitoring and Reporting 1. General Provisions (Compliance Reports, Documentation) 2. Administration and Enforcement Penalties and Sanctions (Fines and Penalties, 3. Design and Construction Requirements Revocation of Permits or Licenses) 4. Occupancy Requirements Legal Action (Enforcement Actions, Appeal 5. Accessibility Procedures) 6. Fire Safety Public Awareness and Education (Training Programs, Information Dissemination) KEY PROVISIONS Technological Tools (Digital Platforms, Building I.Chapter 1: General Provisions. Section 104. Information Modeling (BIM)) General Building Requirements 3. CHALLENGES IN NBCP II.Chapter 3 Permits And Inspection. Section 304. Lack of Awareness Issuance Of Building Permits Inconsistencies in Enforcement III.Chapter 4 Types Of Construction. Section 401. Corruption and Non-Compliance Types Of Construction Resource Constraints IV.Chapter 5 Requirements For Fire Zones. Rapid Urban Development Section 502. Buildings Located In More Than One Fire Zone II. ARCHITECTURAL CODE V.Chapter 7 Classification And General -The United Architects of the Philippines (UAP) is a Requirement Of All Buildings By Use Or recognized organization under PD 223 and RA Occupancy. Section 701. Occupancy Classified 545, responsible for overseeing and implementing VI.Chapter 8 Light And Ventilation. Section 801. the National Building Code (PD 1096). General Requirements Of Light And Ventilation VII.Chapter 9 Sanitation. Section 901. General RELATIONSHIP WITH OTHER CODES Requirements 1.National Building Code (NBC) VIII.Chapter 11 Protection Of Pedestrians During 2.Fire Code Construction Or Demolition. Section 1105. Walkway 3.Electrical Code IX.Chapter 12 General Design And Construction 4.Plumbing Code Requirements. Section 1201. General 5.Accessibility Codes Requirements 6.Environmental and Sustainability Codes X.Chapter 12 General Design And Construction Requirements. Section 1202. Excavation, SPECIFIC CHAPTERS AND SECTIONS CODES Foundation, And Retaining Walls RELATED TO CE XI.Chapter 20 Signs. Section 2003. Design And I. Chapter 5: Types of Construction Construction -classifies buildings based on their construction materials and structural components IMPLEMENTATION AND COMPLIANCE Types of Buildings: 1.Regulatory bodies 1. Type I (Fire-Resistive): Buildings made of -bodies that are responsible for the implementation, fire-resistive materials, ensuring maximum safety enforcement, and compliance of building against fire hazards. standards. 2. Type II (Steel, Iron, Concrete): Buildings using Department of Public Works and Highways non-combustible materials like steel, iron, and (DPWH) concrete with limited combustible elements. Local Government Units (LGUs) 3. Type III (Wood with Fire-Resistive Materials): Professional Regulation Commission (PRC) Wooden structures with added fire-resistant National Building Code Development Office features like cladding. (NBCDO) Bureau of Fire Protection (BFP) 4. Type IV (Wood and Masonry): A mix of masonry (non-combustible) walls and wood-framed III. NATIONAL STRUCTURE CODE OF THE interiors. PHILIPPINES 5. Type V (Wood Construction): Structures made - is a comprehensive set of regulations that guide predominantly of wood or similar combustible the design, construction, and maintenance of materials. structures in the Philippines II. Chapter 6: General Design and Construction Requirements PUPOSE -fundamental guidelines for the design, To ensure the structural integrity and safety construction, and overall safety of buildings. To provide a uniform set of guidelines and Main Points: standards 1. Safety Standards: Emphasizes the importance To incorporate the latest advancements of safety in design 2. Accessibility: Buildings must be accessible to SCOPE OF NSCP all individuals, including persons with disabilities 1. Design Criteria: It covers the design criteria for 3. Space Planning: Guidelines on proper space various types of structures. allocation for different building functions 2. Materials: It specifies the standards for 4. Environmental Considerations: Promotes construction materials such as concrete. sustainable design practices, such as proper 3. Load Requirements: It includes guidelines for ventilation, natural lighting, and energy efficiency. calculating loads and forces that structures must 5. Aesthetics and Functionality: Ensures that withstand. buildings are not only functional but also 4. Construction Practices: It outlines best aesthetically pleasing practices for construction methods and techniques 6. Compliance with Other Codes: The design and to ensure quality and safety. construction must comply with other relevant codes 5. Maintenance: It provides guidelines for the III. Chapter 12: Protection of Pedestrians and maintenance and inspection of structures Property During Construction and Demolition -guidelines to ensure safety during building LOAD SPECIFICATIONS construction and demolition activities. 1. Dead Loads (DL): These are permanent loads Requirements: due to the weight of the structure itself and any 1. Safety Barriers and Signage: Requires the fixed elements installation of protective barriers, fences, and 2. Live Loads (LL): These are temporary loads warning signs that the structure must support, 2. Temporary Walkways and Protection: 3. Roof Live Loads (RLL): These are live loads Mandates the construction of temporary walkways, specifically for roofs, accounting for maintenance canopies, or protective coverings activities and potential accumulation of water or 3. Debris Containment: Ensures that construction snow and demolition debris are properly contained and 4. Wind Loads (WL): These loads account for the disposed of to prevent hazards effects of wind pressure on the structure 4. Protection of Adjacent Properties: Requires 5. Earthquake Loads (EQ): These loads consider measures to safeguard neighboring properties from the seismic forces that a structure must resist. damage due to construction activities, 5. Equipment and Materials Management: MATERIAL STANDARDS Stipulates the proper storage and handling of 1. Chapter 4: Concrete construction equipment and materials 2. Chapter 5: Structural Steel 6. Compliance and Enforcement: Provides 3. Chapter 6: Wood guidelines for ensuring that construction and 4. Chapter 7: Masonry demolition activities comply with safety regulations SAFETY FACTORS INTEGRATION IN PRACTICE WITH NBCP AND Formula: FoS = Ultimate (or failure) strength NSCP Expected or actual load 1. Coordination Architects-must work closely with 1. Load and Resistance Factor Design (LRFD) structural engineers to ensure that their designs -method involves applying load factors to account comply with both architectural and structural codes for various types of loads 2. Compliance Checks-During the design and Load Factors: These are typically greater than approval process, building plans are reviewed to 1.0 ensure compliance with both the NBCP and NSCP Resistance Factors: These are less than 1.0 a 3. Harmonization-There may be instances where 2. Factor of Safety (FS) for Allowable Stress the Architectural Code's requirements need to be Design (ASD balanced with the technical specifications of the -method, which is also covered in NSCP 2015, NBCP and NSCP uses a Factor of Safety (FS) to ensure that the actual stresses in structural members remain within GROUP 2: PHILIPPINE SAFETY CODE allowable limits. Typical factors of safety may range from 1.5 to I.NATIONAL ELECTRICAL CODE OF THE 3.0 PHILIPPINES -(PEC) is a set of standards and regulations that COMMON ISSUES AND RESOLUTIONS govern the safe and proper installation, operation, 1. Delays in Project Timeline and maintenance of electrical systems in the Resolutions: Philippines. Thorough Planning Buffer Time PEC I - Electrical Installation inside buildings Effective Communication PEC II - Electrical Installation outside buildings Contingency Plans MANDATORY RULES- characterized by the used 2. Budget Overruns of the word SHALL Resolutions: ADVISORY RULES -characterized by the used of Detailed Cost Estimation the word SHOULD Change Management Regular Financial Monitoring IMPORTANCE OF PEC Value Engineering Safety 3. Poor Quality of Work Standardization Resolutions: Legal Compliance Hiring Qualified Professionals Quality Assurance Clear Contracts Regular Inspections ORIGIN OF PEC Use of Quality Materials 1. P.D. 1096 - National Building Code 4. Safety Hazards 2. P.D. 1185 - Fire Code of the Philippines Resolutions: 3. Structural Code R.A. 7920 Safety Training Safety Audits APPLICATION OF PEC Clear Safety Protocols Installation, operation and maintenance of electrical Proper Site Management systems within buildings and structures. 5. Communication Issues Resolutions: SCOPE OF PEC Clear Communication Channels 1. Public and Private Buildings Regular Progress Reports 2. Electrical Generating Plant Single Point of Contact 3. Industrial Plant Collaborative Tools 4. Temporary and Permanent Substation 5. Transformer Station NBCP BEST PRACTICES 6. Railway Switchyard Compliance with Safety Standards 7. Carnivals, Parking lots, Yards etc. Permit Acquisition 8. Watercraft Structural Integrity and Load Compliance 9. Dockyard Universal Accessibility 10. Airfields Fire Code Compliance 11. Quarries and Mines 12. Mobile homes and recreational vehicles NSCP BEST PRACTICES 13. Offshore facilities Seismic Design 14. Trailers Load Consideration Material Standards TYPES OF INSTALLATION COVERED Structural Analysis and Testing Residential Installations: The code provides Quality Assurance guidelines for electrical systems in homes, apartments, and other residential buildings. ACP BEST PRACTICES Commercial Installations: It governs electrical Design Aesthetics and Functionality installations in commercial establishments such as Sustainable Design offices, shops, and malls. Space Planning Industrial Installations: The PEC includes Cultural and Historical Contex provisions for factories, plants, and other industrial Green Architecture Compliance facilities. Public and Institutional Buildings: The code also applies to electrical systems in schools, hospitals, government buildings, and other public institutions. TYPES OF WIRING METHODS 1.Outlets - Must be rated for the appropriate 1. Cleat Wiring - is a temporary wiring technique voltage and current. that is not advisable for residential use. 2.Switches - Must have ratings that correspond to 2. Casing and capping wiring - employs VIR or the voltage and current that they are able to PVC cables, as well as any other approved manage. insulated cables. 3.Lighting Fixtures – Must ensure that the voltage 3.Batten wiring - Insulated wires are routed rating of the lighting fixtures matches the circuit through the straight teak timber battens in this they are linked to and install them in accordance system. with the manufacturer's instructions. 4. Lead sheathed wiring - Conductors are insulated with VIR and coated with an outer sheath SPECIFIC REQUIREMENTS FOR DIFFERENT of a lead aluminum alloy that contains ENVIRONMENTS approximately 95% lead in this wire form. 1.Wet and Damp Locations 5. Conduit Wiring - Electrical wires are routed - Appropriate IP rating through metal or PVC conduits, which are either - Corrosion resistance exposed (surface) or concealed within walls 2.Hazardous Locations (concealed). - Explosion -Proof Equipment PROTECTION REQUIREMENTS 3.Outdoor Installations *OVERCURRENT PROTECTION - Weatherproofing Overcurrent is defined as any current that exceeds - UV Protection the rated current capacity of the equipment or the rated ampacity of the conductor. SPECIAL OCCUPANCIES - It covers specific requirements for electrical The causes of overcurrent are: installations in hazardous locations, swimming 1. Overload in the equipment conductors. pools, medical facilities, marinas, agricultural 2. Short circuit or ground fault buildings, and other special occupancies. 1. Hazardous (Classified) Locations Overcurrent Protection Devices ○ Class I Locations: Areas where flammable 1. Fuses – are protection mechanisms in electrical gasses or vapors may be present systems designed specifically to protect circuits ○ Class II Locations: Areas with combustible dust against excessive current, sometimes known as ○ Class III Locations: Areas where easily ignitable overcurrent. fibers or flyings are present 2. Circuit Breakers - are electrical devices that 2. Healthcare Facilities automatically interrupt the flow of electricity in a ○ Hospitals and Clinics circuit in the event of an overload or short circuit ○ Operating Rooms and Intensive Care Units detection. (ICUs): 3. Educational Institutions *GROUNDING AND BONDING ○ Schools and Universities 1. Grounding- is essential for reducing electrical shocks and equipment damage by allowing any INSPECTION, TESTING, AND MAINTENANCE energized metal surfaces to be linked to a 1.Inspection Requirements: The PEC mandates grounding electrode or system. inspections by qualified personnel before an 2. Bonding -refers to the act of linking multiple electrical system conductive items using a conductor to achieve a 2.Testing Protocols: The code specifies the types shared static potential. of tests that should be conducted on electrical systems to verify their safety STANDARDS FOR ELECTRICAL EQUIPMENT 3.Maintenance Guidelines: The PEC provides 1. General Requirements guidelines for the ongoing maintenance of electrical Examples of those equipment: systems Circuit Breakers and Fuses Switches and Disconnectors ELECTRICAL INSPECTION AND TESTING Lighting Fixtures FACTORS Transformers 1. Reliability Wiring and Cables 2. Stability 2. Voltage Rating 3. Suitability of the design 3. Environmental Considerations 4. Mechanical Strength 4. Disconnecting Means 5. Spaces and dimensions 5. Markings and Labels 6. Grounding 7. Insulation 8. Heating effect DEVICE REQUIREMENTS 9. Arcing effect 10. Availability of replacement Fire escape stairs: These are separate 11. Safety stairways that are designed to provide an escape 12. Class type, sizes, ampacity, voltage and route in case of a fire. specific use Fire Extinguishers:s are portable devices used to put out small fires. LEGAL OBLIGATIONS Class A Extinguishers-Used for ordinary Design and Installation combustibles like wood, paper, and cloth. Professional Responsibility Class B Extinguishers-Used for flammable liquids Permits and Inspections like gasoline, oil, and grease. Use of Approved Materials Class C Extinguishers-Used for electrical fires. Safety Measures Class D Extinguishers-Used for combustible Updates and Revisions metals like magnesium, sodium, and potassium. CONSEQUENCES OF NON-COMPLIANCE 4.FIRE DRILLS Legal Consequences -are practice evacuations conducted to prepare Safety Risks individuals and organizations for a real fire Operational Impact emergency Reputation Damage Alarms: Sounding the fire alarm to alert Regulatory Consequences everyone in the building. Evacuation: Guiding people to safe exit points COMMON ISSUES IN IMPLEMENTATION IN PEC and assembly areas. 1. Not following the Philippine Electrical Law. Roll call: Taking attendance to ensure everyone 2. Incorrect sizing of wires and corresponding is accounted for. circuit breakers. Emergency response: Coordinating with fire 3. Not using PPE (Personal Protective Equipment). departments and other emergency services. FUTURE TRENDS FIRE PREVENTION MEASURES 1. Nuclear Energy 1.Fire prevention- measures are steps taken to 2. Hydroelectric Energy reduce the risk of a fire occurring. 3. Wind Energy 2.Public education-plays a crucial role in promoting fire safety and preventing fires. II. FIRE CODE OF THE PHILIPPINES EX: -is a comprehensive set of laws and regulations Curriculum integration: Incorporating fire safety that govern fire safety standards and practices in into school curricula across various subjects, such the Philippines. as science, health, and social studies. Guest speakers: Inviting firefighters or fire safety KEY PROVISIONS experts to speak to students about fire prevention. 1.FIRE RESISTANT MATERIALS Fire drills: Conducting regular fire drills to - materials are designed to resist the effects of fire familiarize students with emergency procedures. for a specified period. 3.Fire inspections-help identify potential fire Fire-resistant concrete: This is made by hazards incorporating fire-resistant aggregates and EX: additives into the concrete mix. Building Inspections:ensuring the safety, Fire-resistant insulation: This can be made structural integrity, and compliance with building from materials such as mineral wool, fiberglass, or codes of structures. vermiculite. Fire Protection Systems Inspections: Regular 2.FIRE ALARMS AND DETECTION SYSTEMS inspections of these systems help to ensure their -designed to detect the presence of fire or smoke proper functioning and compliance with fire codes. and alert occupants of the danger EXMPLES: AMENDMENTS AND UPDATES OF FCP Smoke Detectors: These detect changes in the 1.Higher Fire Resistance Requirements for ionization of air caused by smoke particles. Buildings Heat Detectors: These activate when the Increased fire rating requirements temperature reaches a predetermined level. Enhanced fire protection systems 3.EMERGENCY EXITS Improved evacuation routes - designed to provide safe and accessible escape 2.Enhanced Regulations for Hazardous Material routes in case of a fire or other emergency. High-rise buildings EXAMPLES: Buildings with high occupancy Fire-rated doors: These are designed to resist Buildings in high-risk areas the spread of fire and smoke for a specified period. 3.Strengthened Enforcement Mechanisms Increased penalties Regular inspections Public awareness campaigns Water closet bowls for public use shall be Collaboration with local governments elongated bowl types equipped with openfront seats. IMPORTANCE OF COMPLIANCE FCP 2.Installation Public safety Planning: Gather tools and materials. Property protection Shut Off Water: Turn off the main water supply. Legal consequences Install Fixtures: Mount sinks, toilets, or showers/tubs, and connect them to water supplies III. NATIONAL PLUMBING CODE OF PH and drainage. Plumbing -System of pipes and fixtures installed in Connect Pipes: Attach and secure water supply a building for the distribution of potable water and lines. the removal of waterborne wastes. Test: Turn water back on, check for leaks, and ensure proper operation. BASIC PRINCIPLES OF PCP Finish: Seal gaps and clean up. 1.Sanitation and Health: This is the foremost principle, ensuring that plumbing systems protect WATER SUPPLY public health by preventing contamination and 1.General Requirements: maintaining a safe water supply. maintain at least 305 mm clearance between 2.Safety: Plumbing installations must prevent plumbing and the ground or floor. For installations accidents and protect users from hazards such as above 1.52 meters, provide a supporting platform. explosions, fires, and exposure to harmful Discharge through an approved air gap of 2 pipe substances. diameters minimum and 25 mm maximum from the 3.Adequate Water Supply: Ensuring a reliable supply outlet and drainage inlet. and sufficient supply of potable water is critical for 2.Specific Requirements: the functioning of any plumbing system. Install an atmospheric vacuum breaker at least 4.Efficient Drainage: Proper removal and disposal 152 mm above the overflow rim of water closets or of wastewater and sewage are essential to prevent urinals. health hazards and environmental contamination. Equip with a ballcock, with a critical level 25 mm 5.Prevention of Cross-Contamination: Avoiding above the overflow pipe. cross-connections between potable water and Install at least 152 mm above the discharge side contaminated sources is crucial to preventing for tanks, pools, potable water outlets with hoses, backflow and ensuring water safety. and water-supplied aspirators. 3.Materials: ADMINISTRATION OF PCP Use Brass, Copper, Cast Iron, Galvanized Steel, 1.Permit Required (Section 100): Ensures that all or approved PE & PVC for cold water; CPVC for plumbing work is authorized and regulated, hot and cold water. maintaining safety and compliance with standards. Galvanize cast iron fittings up to 51 mm and all 2.Inspection (Section 105): Critical for ensuring small malleable iron fittings. Avoid lead pipes with that all plumbing installations and repairs meet the more than 8% lead for potable water. code's safety and quality standards. 4.Installation: 3.Approval (Section 106): Ensures that all Keep at least 0.3 meters below ground. connections to the public water supply and sewer Water pipes must be 0.3 meters above sewers systems are properly executed, preventing and placed with 0.3 meter clearance on a solid contamination and system failures. Plumbing shelf. 4.Fixtures Required (Section 108): Mandates the Install within 0.3 meters from equipment needing installation of essential plumbing fixtures, ensuring servicing. that buildings are adequately equipped for sanitation and hygiene. EXCRETA DRAINAGE SYSTEMS 1.Materials: HANGERS AND SUPPORT Drainage pipes for excreta should be made of 1.Vertical Piping - Any pipe or fitting that is Cast Iron, Ductile Iron, Galvanized Steel, installed in a vertical position or that makes an Galvanized Wrought Iron, Lead, Copper, Brass, angle of not more than 45 degrees with the vertical. Series 1000 PVC DWV, Extrastrength Vitrified Clay 2.Horizontal Piping - is used to keep pipes that Pipe, or other approved smooth and uniform run horizontally (flat) stable and secure. materials. Galvanized Wrought Iron and Galvanized Steel Pipes: These should not be PLUMBING FIXTURES used underground and must be at least 152 mm 1.Materials - General Requirements above ground. All porcelain enamel surfaces on plumbing Vitrified Clay Pipes: These should not be used fixtures shall be acid resistant above ground or where pipes are under pressure from pumps or ejectors. They should be at least 0.3 meters below ground level. Drainage Fittings: Should be made from Cast ○ Install no more than 15 meters apart and at Iron, Malleable Iron, Lead, Copper, Brass, ABS, changes over 135 degrees. PVC, Vitrified Clay Pipe, or other approved ○ Manholes can replace cleanouts, spaced up to materials. They should have a smooth interior and 91 meters apart. match the diameter of the pipes they connect to. Sewer & Water Pipes: ABS and PVC DWV Pipes: These types of pipes ○ Water pipes must be at least 0.3 meters above are suitable for high-rise buildings. sewer lines. Drainage of Fixtures (LOCATED BELOW THE ○ Water pipe joints must be at least 3 meters from UPSTREAM MANHOLE OR BELOW THE MAIN sewer lines. SEWER LEVEL ) Abandoned Sewers & Sewage Disposal Pump Discharge: Any pump or discharge pipe Facilities from a sump (a pit that collects wastewater) that is ○ Abandoned sewers must be capped within 1.5 connected to a water closet must be at least 50.8 meters of the property line. mm in diameter. ○ Drainage pipes must be at least 15.2 meters from Automatic Discharge: Pumps and receiving tanks water supply wells. must discharge automatically. For public use, these systems should have dual pumps or ejectors. The TYPES OF JOINTS lowest inlet to the tank must be at least 51 mm 1.Caulked Joints: Used for cast iron pipes; packed above the high water level where the pump starts with oakum or hemp and filled with lead. working. 2.Threaded Joints: For iron pipes; use standard Ventilation: Vents for sump and receiving tanks taper threads. Plastic pipes should be Schedule 80. must go separately to the roof and be at least 51 3.Wiped Joints: For lead and brass or copper mm in diameter. pipes; must be fully wiped with a lead joint. Air Pressure: Air tanks for ejectors must have a 4.Solder & Sweat Joints: For copper pipes; use pressure of at least 3 kg per meter of sewage eight approved brass or copper fittings. Avoid solders they need to raise. with more than 0.002% lead for potable water. Fixture Outlets: Fixtures must not be connected to 5.Flared Joints: For soft copper tubing. ○ Cement the horizontal drainage pipes within 2.4 meters of Mortar Joints: Used for repairs, but not for new any vertical-to-horizontal pipe change in stacks that building sewers. contain fixtures using soaps or detergents. 6.Burned Lead Joints: Fused lead sheets to form Vent Diameter: Each vent must be at least 32 mm a uniform weld. in diameter or half the diameter of the drain it’s 7.Asbestos Cement Sewer Pipe Joints: Use connected to, whichever is larger. sleeve couplings or compression couplings with neoprene rubber rings. INDIRECT WASTE PIPING, WET VENTED 8.Mechanical Joints: For centrifugal cast iron SYSTEMS & SPECIAL WASTES water pipes. 1.Indirect Waste Conditions 9.Molded Rubber Coupling Joints: Use molded 2.Indirect Waste Piping neoprene rubber, especially for soil with oil 3.Indirect Waste Receptors intrusion. 4.Chemical Waste 10.Elastomeric Gasketed & Rubber-Ring Joints: Follow IAMPO standards; use neoprene gaskets STORM DRAINAGE SYSTEMS for oil handling. 1.Rainwater Systems: 11.Pressure-Lock Type Connections: Use internal 2.Roof Drain: retention devices to prevent separation. Strainers: 12.Shielded Coupling & Hubless Cast Iron Pipe Vertical Wall Areas: Joints: Not considered slip joints. Vertical Piping USES OF JOINTS HOUSE DRAINS & HOUSE SEWERS 1.Clay Sewer Pipes: Use neoprene gaskets for Sewer Required: hub and spigot joints. ○ Public sewer is unavailable if more than 61 2.Screwed Pipe to Cast Iron Pipe: Use either meters from the building. caulked or threaded joints. ○ Building sewer starts 0.6 meters from the wall. 3.Lead to Other Metals: Use wiped joints for lead Size of Building Sewers: to cast iron, wrought iron, or steel. ○ Must be at least 150 mm in diameter. 4.Copper Water Tube: Join with brass fittings Grade, Support, & Protection of Building using solder or brazing. Sewer: ○ Grade must be at least 2% (or 1% in special SPECIAL JOINTS cases). 1.Copper Tubing to Screw Pipe Joints: Use ○ Install at least 0.6 meters from the building and brass adaptors; joints should be sweated or 0.3 meters below ground level. soldered. 2.Slip Joints: Allowed in fixture drains and traps. 3.Expansion Joints: Used in high-rise buildings to GROUP 4: QUANTITY SURVEY AND COST manage pipe expansion and contraction. ESTIMATES, BUILDING PERMIT FLANGED FIXTURE CONNECTION I.QUANTITY SURVEYING 1.Gasket Material: Use graphite-impregnated -ensuring construction projects are financially asbestos, felt, or similar approved types feasible and cost-effective. Quantity Surveyors (QS)-manage project costs PLUMBING MATERIALS from start to finish. ABS: Acrylonitrile-Butadiene-Styrene DWV: Drain, Waste, and Vent QUANTITY SURVEYOR AND ITS ROLES CPVC: Chlorinated Polyvinyl Chloride -is a professional in the construction industry UPVC: Unplasticized Polyvinyl Chloride responsible for managing the costs and contracts CPE: Chlorinated Polyethylene of building projects. IV. SANITATION CODE OF THE PH KEY RESPONSIBILITIES OF QUANTITY -. Promoting and protecting public health in the SURVEYOR country through proper sanitation practices. 1. Cost Estimation:prepares detailed cost plans by analyzing project blueprints and specifications to KEY CONCEPT OF SCP outline anticipated expenses 1.Food Safety-It establishes regulations on food 2. Budget Management:tracking and managing handling, storage, preparation, and serving to expenditures throughout the project to ensure they prevent foodborne illnesses. stay within the approved budget. 2.Water Quality-Ensuring access to clean and 3. Contract Preparation:drafts, negotiates, and potable water is a fundamental objective of the administers contracts between clients, contractors, code and suppliers. 3.Waste Management-The code lays down 4. Risk Assessment:identifies potential financial guidelines for waste segregation, collection, risks in a project, such as cost fluctuations and transport, treatment, and disposal to prevent unforeseen challenges. environmental pollution and health hazards. 4.Environment Sanitation-The code emphasizes ESSENTIAL SKILLS OF A QUANTITY the importance of maintaining clean and healthy SURVEYOR environments in both residential and public areas. 1. Numerical and Analytical Skills: must be skilled in mathematics and data analysis to perform CHALLENGES OF SCP accurate cost estimates, measurements, and Resource Limitations budgeting. Public Awareness and Compliance 2. Project Management:coordinate teams (contractors, architects, suppliers), monitor costs, timelines, and resources, 3. Negotiation Skills:negotiate prices, payment terms, and contract conditions to secure the best financial outcomes 4. Attention to Detail:as small errors in measurements or cost estimates can lead to significant financial discrepancies. METHODS OF MEASUREMENT IN QUANTITY SURVEYING 1. Standard Method of Measurement (SMM): A widely used approach that provides guidelines on how to measure various elements of construction work. 2. Civil Engineering Standard Method of Measurement (CESMM): Used for civil engineering projects like roads and bridges. 3. International Construction Measurement Standards (ICMS): A global framework for measuring construction projects. 4. Building Information Modelling (BIM) Measurement: Integrates 3D models with quantity take-offs for more accurate and real-time measurements, enhancing collaboration and 3. Bottom-Up Estimating: A more granular precision. approach is bottom-up estimating, which uses estimates of individual tasks and then adds those II. COST ESTIMATES up to determine the overall cost of the project. Cost estimation-is the process of accurately 4. Three-Point Estimate: Another approach is the forecasting the time, cost and resources required three-point estimate, which comes up with three for a project. scenarios: most likely, optimistic, and pessimistic Cost estimator-is tasked with figuring out the ranges. duration of the project in order to deliver it successfully. STEPS IN ESTIMATING PROJECT COST 1.Review the bid package: PURPOSE OF COST ESTIMATION The bid package contains all of the documents 1. Budgeting and Financial Planning: Cost necessary for bidding estimation provides a financial roadmap for the 2.Conduct a site visit: project. 3.Perform a material takeoff. 2. Decision Making: Accurate cost estimates allow 4.Solicit pricing from suppliers and vendors: stakeholders to make informed decisions about the 5.Evaluate labor requirements feasibility of a project. 6.Determine insurance and bonding costs: 3. Cost Control and Management: serve as a Direct project costs, estimators must also benchmark to monitor expenses, identify variances, consider the indirect field costs associated with and implement corrective actions to keep the construction as well as the overhead costs required project on track financially. for running a construction business. 7.Account for profit and contingency: TYPES OF COST The profit is the fee that the contractor earns for 1. Direct costs: are those that occur in a project the contract and are attached to specific activities. (raw Contingency, on the other hand, is a portion of materials, labor, supplies, etc. the contract set aside for overruns and 2. Indirect costs: in a project are those that are in waste—which are generally to be expected on a support of the project, such as administrative construction project. fee(rent to salaries of the administrative staff to utilities, etc.) SOFTWARE TOOLS USED IN QUANTITY 3. Fixed costs:don’t change throughout the life SURVEYING AND COST ESTIMATION cycle of a project.(setup costs, rental costs, 1. Microsoft Excel: Widely used for data entry, insurance premiums, property taxes, etc.) calculations, and cost estimates. 4. Variable costs: are costs that change due to the 2. CostX: Offers 2D and 3D/BIM takeoffs, with amount of work that’s done in the project and are advanced estimating features. variable in nature. (hourly labor wages, materials, 3. PlanSwift: Ideal for digital takeoffs with easy fuel costs) measurement tools. 4. Revit: A BIM tool that integrates quantity TYPES OF ESTIMATES takeoffs with 3D modeling. 1. Conceptual Estimate: A conceptual estimate is 5. AutoCAD: Used for creating detailed 2D and 3D normally produced from merely the notion the drawings, with measurement integration. owner has of what he or she would like to see constructed. III. BUILDING PERMIT 2. Preliminary Estimate: As the design develops, TYPES OF PERMITS a number of preliminary estimates can be prepared 1. Ancillary permits-duly signed and sealed by the informing the designers that their proposed design corresponding professionals and the plans and does or does not meet the project budget. specifications shall be submitted together with the 3. Detailed Estimate: A detailed estimate of the duly notarized application for Building Permit. cost of a project is prepared by determining the ARCHITECTURAL PERMIT costs of materials, labor, equipment, subcontract CIVIL/STRUCTURAL PERMIT work, overhead, and profit. ELECTRICAL PERMIT MECHANICAL PERMIT COST ESTIMATION TECHNIQUES SANITARY PERMIT 1. Analogous Estimating: Seek the help of PLUMBING PERMIT experts who have experience in similar projects or ELECTRONICS PERMIT use your own historical data. 2. Accessory permits-e issued by the Building 2. Parametric Estimating: also uses historical Official for accessory parts of the project with very data of key cost drivers and then calculates what special functions those costs would be if the duration or another of the project is changed. EXEMPTION FROM BUILDING PERMITS a. Minor Constructions b. Repair Works Step 11: Final Inspection and Approval REQUIREMENTS FOR BUILDING PERMIT IMPORTANCE OF BUILDING PERMITS IN THE 1. Ownership of the lot property PHILIPPINES: a. In case the applicant is the owner of the lot 1. Safety Assurance where construction will take place: 2. Compliance with Zoning Laws a1. Certified true copy of Transfer Certificate of 3. Environmental Protection Title, on file with the Registry of Deeds. 4. Legal Requirement a2. Tax Declaration 5. Property Value a3. Latest Real Property Tax Receipt b. In case the applicant is not the registered owner of the lot: b1. Duly notarized copy of the Contract of Lease or Deed of Absolute Sale 2. Application forms a. Application for Building Permit (5 copies) b. Electrical Permit Forms (3 copies) c. Sanitary Permit Forms (3 copies) 3. Five sets of complete detailed plan a. For construction of two-storey building: Structural Design Analysis – signed and sealed by Civil Engineer at every page b. For construction of more than two-storey building Boring and Plate Load Test Seismic Analysis 4. Proof of Property Photocopy of Transfer Certificate if Title (TCT) Photocopy of tax Declaration of Property-lot (Certified True Copy) – 5 copies Photocopy of Current Tax Receipt (5 copies) 5. Copy of License of Engineers and Architects PROCEDURE OF SECURING A BUILDING PERMIT IN THE PHILIPPINES 1. Prepare the list of requirements while you secure a checklist and application forms from the Office of the Building Official. 2. Along with the filled out forms and required documents and clearances as outlined in the checklist, submit them to the Office of the Building Official. 3. If the submitted requirements are complete, you will be granted an acknowledgement/follow-up slip. 4. Within 10 working days, you will receive an order of payment from the Releasing Section of the building office. Settle the charge at the cashier’s office. 5. After five days, the building permit will be released after the submission of proof of payment (official receipt). STEPS IN OBTAINING BUILDING PERMIT Step 1: Determine Project Scope and Type Step 2: Research Local Regulations Step 3: Develop Detailed Plans and Compile Application Materials Step 4: Submit the Application Step 5: Application Review Step 6: Pay Fees Step 7: Await Approval Step 8: Obtain a Building Permit Step 9: Start Construction Step 10: Schedule Inspections GROUP 5:BUILDING ENVELOPE SYSTEMS MOISTURE SOURCES AND ASSEMBLIES 1.External- Rain, groundwater,humidity 2. Internal- cooking, bathing, human activities I.BUILDING ENVELOPE SYSTEM -the enclosure, barrier and separator of the outdoor MODE OF MOISTURE TRANSFER environment 1.Diffusion- water vapor moves from area of high concentration to low concentration TYPES OF ENVELOPE 2.Capillary Action- moisture can be drawn into 1. Loose Envelope Design- allow natural airflow porous materials 2. Tight Envelope Design - minimize air gaps 3. Air movement- air leakage through cracks, openings or gaps PARTS OF BUILDING ENVELOPE SYSTEM 4. Bulk water flow- direct water infiltration through 1.Below grade- space that is below the ground leaks in roofs level 2. Exterior walls- Separate the indoor and outdoor MOISTURE CONTROL STRATEGIES environment of a building 1.Proper ventilation- ensuring good airflow to 5.Atrium- a large open or skylight covered space expel excess moisture from inside. within a building provides ventilation and light. 2. Insulation and vapor barriers- using materials 4.Roof- serve as barrier against air, rain, snow to limit moisture diffusion through walls and ceilings 3.Sealants- sealing cracks, gaps, and joints II. FUNDAMENTALS OF PERFORMANCE IN 4.Drainage system- directing water away from the BUILDINGS building foundation through gutters 1.Support function- enclosures must handle internal and external forces EFFECTS OF POOR MOISTURE CONTROL 2.Control function- ability of a building envelope 1.Mold growth- excessive mixture can lead to to control and moderate the exchange of mass mold 3. Finish function- is the aesthetics of the finished 2. Structure damage- moisture can weaken surface. building materials leading to rot, rust 4.Distribution function- distribution of services 3. Energy efficiency- moisture can reduce the through a building (power, communication,water) effectiveness of insulation III. BUILDING AESTHETICS BUILDING ENVELOPE DESIGN Aesthetics- involve the material finish, color, 1.Material selection- choose material that can texture and overall appearance. resist moisture absorption 2Fs 2. Design details- overhang, flashing, and proper -Form detailing at joints prevent water penetration -Function DURABILITY OF BUILDINGS FACTORS THAT AFFECT THE AESTHETICAL -ability to withstand wear, decay and weathering PERFORMANCE over time 1.Weathering- physical and chemical breakdown of materials over time ELEMENTS OF DURABILITY a.Physical weathering - breakdown of a material -moisture through mechanical processes. -sunlight b. Chemical weathering- degradation of materials -material failure due to chemical reactions. -heat 2.Decay- associated with organic materials like -insects wood or materials exposed to moisture - building function 3.Waterlogging- happens through faulty seals, -styles insufficient drainange. MOISTURE-a major cause of building MITIGATION STRATEGIES damage,leading to decay 1.Material selection HEAT- can cause material to contract 2.Protective coatings SUNLIGHT-Breaks down materials like plastics 3.UV resistant finishes INSECTS-termites are common threat in ph 4. Maintenance damages to wooden structures 5. Drainage System MATERIAL FAILURE-some materials have shorter lifespan than others IV. MOISTURE TRANSFER IN BUILDINGS BUILDING FUNCTION-changes in building use - critical factor affecting the durability, energy can affect its durability and lifespan efficiency and indoor air quality STYLES-attractive buildings are more likely to maintained and repaired FUNDAMENTAL PRINCIPLES THAT ENSURES A SUSTAINABLE DESIGN 1. Optimize energy use -optimize thermal insulation -analyze envelope performance with energy simulation -employ effective solar shading devices 2. Optimize site potential -consider climatic conditions -reduce urban heat sounds 3. Use greener material -eliminate the use of material that pollute or are toxic -maximize recycled content -use wood for suistanable