Diesel Engine Fundamentals and Working Principles PDF
Document Details
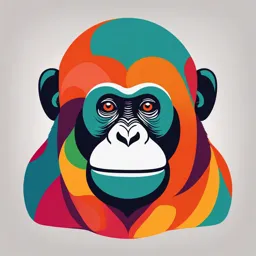
Uploaded by ImaginativePeachTree
STC/JHS
Tags
Summary
This document provides a foundational overview of diesel engine basics, including working principles, classification, and the cycle of operation. It explains the differences between internal and external combustion engines and the key concepts of compression ignition engines.
Full Transcript
## DIESEL ENGINE FUNDAMENTALS AND WORKING PRINCIPLES ### OBJECTIVE - Understand about the basic working principle and fundamentals of Diesel Engine. - Learn about working principle. - Learn about classification of Diesel Engine. - Understand working cycle through valve timing diagram. - Understandi...
## DIESEL ENGINE FUNDAMENTALS AND WORKING PRINCIPLES ### OBJECTIVE - Understand about the basic working principle and fundamentals of Diesel Engine. - Learn about working principle. - Learn about classification of Diesel Engine. - Understand working cycle through valve timing diagram. - Understanding process of combustion in Diesel Engine. ### STRUCTURE: - Introduction - Cycle of Operation - Valve Timing Diagram - Cylinder arrangement and Engine Layout. - Natural aspiration and Supercharging - Firing Order - Combustion in Diesel Engine ### INTRODUCTION - There are two types of engines: External Combustion Engine and Internal Combustion Engine. - Examples of External Combustion Engines are coal or oil fired steam engines. - Internal Combustion engine examples are Petrol, Diesel and Gas engine. - In External Combustion Engines, coal or liquid fuel is burnt outside the cylinder. - In Internal Combustion Engines, fuel burns inside the cylinder. - Internal Combustion Engines are again divided into two groups: Spark Ignition Engines, and Compression Ignition Engines. - Petrol and Gas Engine are examples of Spark Ignition Engines. - Diesel engine is an example of Compression Ignition Engine. - The basic purpose of an Internal Combustion Engine is to develop power by burning fuel. - The performance of an engine is dependent on how quickly and completely the fuel can be burnt. - The burning of hydrocarbons is called combustion, which is a chemical process (oxidation), accompanied by emission of light and heat. - Petrol or gas engines are called Spark Ignition Engines because electric spark is required for ignition of fuel air mixture, which is injected in the mixture form in the combustion chamber. ### COMPRESSION IGINITION ENGINE - Combustion in the Compression Ignition Engine differs widely from that of Spark Ignition Engine. - Only fuel in liquid state is injected at a very high pressure in the combustion chamber. - The heat of the compressed air starts the combustion process and no agency like electric spark is required. - The name 'COMPRESSION IGINITION ENGINE' is derived from the fact that the air drawn in the suction stroke is compressed to such a degree that the heat generated due to compression goes much above the self ignition or auto-ignition temperature of the liquid fuel. - The abbreviation 'IC Engine' (Internal Combustion Engine) and CI Engines (Compression Ignition Engine) sometimes causes confusion. - Both petrol and diesel engines are 'IC Engines', only diesel engines work on Compression Ignition principle and should be termed as 'CI Engines'. - In other words all 'CI Engines' are 'IC Engines' but all 'IC Engines' are not 'CI Engines'. ### Compression Ratio - The compression ratio is the ratio between total volume (clearance volume + swept volume.) and clearance volume. - It is indicative of the degree of compression of the trapped air. - Higher the compression ratio, higher will be the compression pressure and consequently higher the temperature. - Compression ratio is usually lesser in Spark Ignition Engine (around 8:1) than in Compression Ignition Engine (12:1 and above). ### CYCLE OF OPERATION - Pre-requisites must be fulfilled in Compression Ignition Engine: - (a) Suction or Induction - Fresh cool air must take place for the purpose of providing oxygen for combustion of fuel and for the scavenging of burnt gases and for taking away heat from the combustion chamber components. - (b) Compression: - The air inlet passage is closed after the air is drawn in. - The air is compressed due to the upward movement of pistons. - At this stage, fuel is injected just before the T.D.C. for combustion to start. - (c) Firing of power: - The firing takes place very shortly after the fuel injection - The expansion of gas provides the force or power, which drives the piston back, thus rotating the crankshaft. - (d) Exhaust: - The burnt gas has to find passage to atmosphere after the fuel is burnt out. ### TWO STROKE CYCLE - In Four-stroke cycle engines, suction, compression, fuel injection, exhaust and scavenging are completed in four strokes of the piston or two revolutions of the crank. - In two-stroke engines, all these are completed in two strokes of the piston or one revolution of the crankshaft. - Compressed air is essential for scavenging in two-stroke engines. - In four-stroke engines, it works as naturally aspirated engine at lower power ranges. ### VALVE TIMING DIAGRAM #### VALVE TIMING - TWO STROKE CYCLE - Fuel injection starts just before the TDC, and the power stroke begins just after the TDC. - The exhaust valves pen allowing the exhaust to escape after the piston has moved down partly from the BDC. - The pressure in the combustion chamber falls. - The piston uncovers inlet port on the sides, as the piston has gone further down before TDC. - The scavenging air finds access into the cylinders and tries to push out the exhaust gases. - This process continues after the BDC. - Both exhaust valves and the inlet ports remain open for a period, after BDC. - The inlet ports close, but the exhaust ports still remain open, after the BDC. - The combustion chamber is full of fresh air, as the crank is at the BDC, and the exhaust valves close. - The trapped gas contains mostly pure air, and compression takes place. - Fuel is injected at a high pressure against hot compressed air, as compression is taking place before the TDC. - The firing starts with peak pressure being reached just after the TDC. ### VALVE TIMING DIAGRAM - 4 STROKE CYCLE - This type of engine needs four strokes of piston or two revolutions of the crank to cover all events of the cycle. - Each stroke is distinctly for one major event, but in actual practice it is not quite so, as the events sometimes over lap between two strokes for better performance. - The inlet valve opens before the TDC, as the exhaust stroke is almost complete and the piston is still moving upwards. - The supercharged air, which is above the atmospheric pressure, reaches through the inlet valves, and pushes out the burnt gas. - This process continues after TDC when the exhaust valve closes. #### SUCTION - Exhaust valve closed, and piston continuing to move downwards. - More and more fresh cool air is sucked in through the inlet valves. - The suction does not end at the BDC and continues after BDC when Inlet valve closes. - This extra movement of the crank by this amount provides some more time for more air to find access in cylinder due to "wire drawing" or inter alia effect. - This extra time is not necessary if the size of the valve was as large as the size of the piston. - This can’t be possible due to obvious reasons. - More time is required to get more air through the restricted air inlet passage. - The first downward stroke is partly for scavenging and the rest for suction . #### COMPRESSION - Air inlet valve closing after BDC. - The air drawn in the cylinder gets trapped, as the exhaust valve also is closed from before. - Compression takes place, as the piston is moving upwards in the second stroke, until it reaches close to TDC. - Just before the TDC, the compressed air is well compressed and heated up, and combustion of the fuel compressed starts. - Peak pressure is achieved a little after TDC. - Fuel injection also starts, in the later part of upward stroke. #### POWER - In the 3rd (downward) stroke, the high pressure developed in the combustion chamber forces the piston down, which is called power stroke, but little before the end of this stroke the exhaust valve opens, and the burnt gases under some pressure find outlet through the exhaust valve. - Residual pressure and energy helps in driving turbo charger, although it is not much consequence in developing power in the cylinder. - Extra time with the exhaust valves open avoids back pressure in the exhaust stroke. - The third (downward) stroke is mainly a power stroke, and a part in the later and is used for exhaust of burnt gases. #### EXHAUST - The 4th (upward) stroke starts after the piston passes the BDC. - The inlet valves open before the TDC, with exhaust valve already in open condition. - Pressure of exhaust gas has come down considerably. - The pressurized inlet air scavenges the burnt gas, which thus completes the full cycle. - The 4th (upward) stroke is mainly exhaust stroke, but the later part of it is used for scavenging. ### FIRING ORDER - There is only one power stroke in the four strokes of pistons or every two revolutions of the crankshaft, in a four-stroke cycle engine. - Flywheel is necessary to ensure a 'carry over' for the three "waste" strokes and to generate a smoother power output. - Multi-cylinder engines are used to increase the power output. - The firing strokes on different cylinders are suitably spaced in relation to the crank angles so that during the revolutions of , the crankshaft, firing of the cylinders takes place one by one, at regular intervals. - One cylinder must be allowed to fire during each of the four strokes and, therefore the crankshaft arranged at 7200/4=1800 intervals. ### CYLINDER ARRANGEMENTS AND ENGINE LAYOUT - Cylinders can be arranged vertically, horizontally, and in V formation. - Vertical inline engines are used for rail traction. - V-engines are used for higher hp, and are also used in rail traction. - Horizontal engines are used for low hp shunters. ### NATURAL ASPIRATION AND SUPERCHARGING - Naturally aspirated engines draw air into the cylinder at a pressure slightly lower than the atmospheric pressure when a partial vacuum is created in the cylinder by the outward motion of the piston in the suction stroke. - Charging of the cylinder with pressurized air is done to increase power output, as there is a restriction of air flow, which results in the cylinder air pressure, being below atmospheric pressure. - The pressure charging of inlet air can be done by: - Engine crankshaft driven centrifugal blower - Roots blower - Exhaust gas driven turbocharger ### ENGINE SIZES AND SPEED - Diesel engines are used in various types of applications, depending on usage. - Engines are classified in three groups, depending on the speed and size, however there is considerable overlap between adjacent groups. - Low speed engines are not used for traction purposes due to being too heavy and bulky. - Medium and high-speed engines are used for rail traction purposes. ### FIRING ORDER - The crankshaft is arranged at 7200/16=450 intervals in a 16-cylinder engine for even firing. - The firing order is used to prevent damage arising from vibrations set up in the crankshaft. - The sequence of firing is arranged so that the vibrations tend to cancel out as far as possible. - Vibration dampers are mounted on the crankshaft, if the firing order is not sufficient to prevent the build up of vibrations in large engines, running at high speeds. ### EXPLANATION OF TERMS - **FREE END:** The Turbo supercharger end of the engine. - **GENERATOR END:** The power take-off end of the engine. - **RIGHT AND LEFT SIDE:** The right or left side of the engine determined by viewing the engine from the power take –off end (i.e. viewer's' right is right side and left is left side of engine). - **CYLINDER LOCATION:** The engine cylinders are numbered from the free end. No. 1 right and left (IR & IL) are the cylinders nearest to the Turbo. ### CRANKSHAFT ROTATION - The crankshaft rotates counter clockwise viewed from the power take – off end or clockwise as viewed from the free end during engine operation. ### FIRING ORDER - **16 Cylinder engine:** 1R- 1L-4R-4L-7R-7L-6R-6L-8R-8L-5R-5L-2R-2L-3R-3L - **12 Cylinder engine:** 1R- 1L- 4R-4L-2R-2L-6R-6L-3R-3L-5R-5L ### TDC & BDC - The dead centre is the position of a piston in which it is farthest from, or nearest to, the crankshaft. - **TDC:** Top Dead Centre. - **BDC:** Bottom Dead Centre. - The dead centre is any position of a crank where the applied force is straight along its axis, meaning no turning force can be applied. ### ENGINE BLOCK - The engine block is the most important structure on which important fittings are fitted like crank shaft, cam shaft, cylinder heads, cylinder liners, piston of con. rod, fuel injection pumps, and crosshead, turbo support, governor etc. - It is fabricated from low carbon steel. - The fabrication is done in a definite sequence to minimize distortion and build up of stresses. - Continuous welding is done in the process of automatic submerged arc welding. - X-ray of welding is done to ensure quality of fabrication. - Stress relieving and shot blasting is done after fabrication. - The block is marked and then machined. - The sides and the top faces are machined. - The saddle faces are machined. - Serration milling of saddle faces and bearing caps is done. - The depth of serration, and the distance between two consecutive pitch as also the distance between cumulative pitch are measured with the help of special dial gauges. - The bearing caps are assembled and tightened to the specified torque value. - The engine blocks are placed on the horizontal boring cum milling machine. - The machining of the bearing housing is done in one setting. - The maximum possible misalignment permitted are: - Horizontal misalignment: 0.002" between adjacent bores. 0.004" between any to any bore. - Vertical misalignment: 0.001" between adjacent bore. 0.003" between any to any bore. ### CRANKSHAFT - The engine crankshaft is the costliest item in a diesel engine. - It is the medium of transforming reciprocating motion to rotary motion. - It may be assembled type, two piece bolted type or may be single piece forging. - Balance weights can be either bolted up or welded. - Locomotives of Indian Railways are with single piece crankshaft with welded counter weights. - Crankshafts are manufactured from chrome-molybdenum steel equivalent to SAE 4140. - The sequence of operation in crankshaft manufacturing is: - Forging and forming operation - Rough machining - Drill of oil holes. - Ultrasonic & Mechanical testing. - Welding of counter weights & shot blasting. - Stress relieving & Shot blasting. - Final machining & radius sing of crank journal corners and oil holes. - Nit riding - Grinding Lapping - Static & dynamic balancing - Final inspection - There are two processes of surface hardening: - Induction hardening: C-40, 0.124". - Nitriding: C-60, 0.012 to 0.015" - Low HP engines prefer Induction hardening as depth of case is more, and crank journals and man bearing journals can be ground down to next step size. - High and high-speed engines prefer Nitriding as it gives long life, with the wear rate being negligible. - Checking of crank shaft deflection ensures correct alignment of crankshaft as well as engine bearing housing bore central line. - The crankshaft is bent/misaligned, if the distance between the related crank web faces vary when the crankshaft is rotated . - This also indicates that the engine block bore is out of alignment. - Crankshaft deflection is measured at the crank web nearest to the generator. . - In Locomotives of Indian Railways, the maximum deflection of + 0.008" is permissible. - Excess deflection is corrected by adding or removing shims between magnet frame distance piece and engine block. ### CAM SHAFT - The cam shaft performs the vital role of opening and closing inlet and exhaust valves and allowing timely injection of fuel inside the cylinder. - It is usual practice for each cylinder to have 3 cams, with two outer cams being for exhaust and inlet valves, and the central cam being for fuel injection. - Each camshaft section takes care of two cylinders in most Diesel engines, where the cams are integral with camshaft. - The cam lobes are subjected to induction hardening after profile killing, and then placed on profile grinding machine. - The individual camshafts are joined together by bolting. - The location of the dowel hole determines the relative angular position of one cam shaft section with respect to the adjacent one. - Catalogue numbers are punched onto the shaft to avoid wrong assembly. - The rifle hole in the center of the shaft provides lubrication of cam bearings. - Oil from valve lever mechanism via the push rod lubricates the cam lobes. - Except for a slight difference in the angularity of exhaust cam the camshafts are identical. - Cam shafts are made from the following metallurgical composition: - Carbon - Maganese - Silicon - Nickel - Chromiuns - Phoshporus - Sulpher ### CYLINDER HEADS - Cylinder head is held on to the cylinder liner by hold down studs or bolts. - It is subjected to high shock stress and combustion temperature at the lower face. - The lower face forms a part of the combustion chamber, and is a complicated casting. - Cooling passages are cored for the purpose of cooling the cylinder head. - Space is provided for passage of inlet air and exhaust gas. - Space is also left for fuel injection nozzles, valve guides and valve seat inserts. - Cylinder heads valve seat inserts are used as replaceable wearing parts. - They are made of stellite, are frozen in ice, and the cylinder head is heated before the insert is pushed into recess in cylinder head. - Valve seat inserts are ground to 80o angle, whereas the valve is ground to 90o angle to ensure line contact. - The valve guides are interference fit to the cylinder head with an interference of 0.008" to 0.0018". - Cylinder heads are hydraulically tested at 70 psi and 190 F. - The cylinder heads are done engines with a specific torque value, and have a metal to metal joint on to cylinder. - Cylinder head castings are made from special alloy cast iron with the following composition: - Carbon - Silicon - Sulpher - Phosphorous - Manganese - Chromiums - Silicon - Nickel - Molybdenum ### VALVES - The valves are the important components of a Diesel engine. - They operate at a very high temperature. - Inlet valves get cooled by fresh flow of cool air. - Exhaust valves give passage to hot exhaust gases. - The path of dissipation of heat for both inlet and exhaust valves is: - From valve face to seat and then to cylinder head. - From valve stem to valve guide and then to cylinder head. - The valve seat angle between the seat surface and cylinder head surface can be either 30 degree or 45 degree. - The desirable angle is dictated by individual engine design, with 45 degree seat having about 20% greater seating force, which assists in preventing the accumulation of valve seat deposits but increases seat deformation due to pounding. - Opening for gas flow is approximately 20% greater with 30 degree seat for the same valve lift. - A narrow seat between valve and valve seat is preferred as it provides less chance of being lift open by foreign material. - Such narrow seat reduces heat dissipation from valve to cylinder head through valve seat. - Valves have a stem of alloy steel, and austenitic steel head flash which are welded together into a composite unit. - Austenitic steel has high level of stretch resistance and is capable of hardening above Rockwell C-34. - Valve head is made of special heat resistant austenitic material (21-4N) with the following composition: - Carbon - Maganese - Silicon - Nickel - Chromiuns - Phoshporus - Sulpher ### PISTONS - The piston is the most important component in a diesel engine because it takes direct part in transmission of power. - The combustion of fuel results in large amount of heat being developed. - About 18% of the heat is absorbed by piston only. - There are two types of Pistons: - Trunk type - Crosshead type - Crosshead type pistons have more or less gone out of use except for large size of marine or stationery engines. - Functions of Pistons: - Compresses the air to required pressure & temperature. - Receives the thrust of expanding gases and transmits the force through connecting rod (for rotating crankshaft). - Forms the crosshead through which side thrust due to angularity of connecting rod is transmitted to the cylinder wall. - Prevents leakage of gas from combustion chamber to crank case with the help of piston rings. - Guiding factors for piston dimensions: - Top portion of the piston is in direct contact with the heat of combustion. - More clearance is required due to expansion. - Relief has to be provided at the piston pin to prevent seizure of piston due to bulging of material at this location. - Top most ring bears the maximum brunt of high pressure hot gases. - NI-resist ring inserts are re-fitted in the ring carrier and the ring groove is made in the insert, which are dovetailed in Aluminium casting/forging, and molecularly bounded to the Aluminium body by AI-FIN-process. - Cast iron is best suited material for manufacture of piston. - Advantages of using cast iron rather than Aluminium in pistons: - Co-efficient of expansion matches with cylinder liner whereas Aluminium has got twice the co-efficient of cast iron. - Heat conductivity is 3 times better than Aluminium. - Compression strength is much more than Aluminium at high temperature. - Wear is less than Aluminium. - Disadvantages of using cast iron rather than Aluminium in pistons: - Weight of Aluminium is 0.097 1bs. per cubic inch, which is much less than cast iron (0.284 1bs., per cubic inch), making cast iron piston about 3 times heavier than Aluminium piston in weight - Cylinder liner being scored is more likely to happen with cast iron piston. - Aluminium alloy pistons are favoured due to the high speed of the modern diesel engines, and are used because it is lighter. - The composition of Aluminium alloy used in pistons is: - Copper - Zinc - Manganese - Titanium - Vanadium - Zirconium - Silicon - Iron - Magnesium - Other - Pistons have two parts: - Piston body (or skirt) - Ring carrier - The ring carrier and piston body have an interference fit, and are welded at the crown by inert gas welding. - Older designs where both the ring carrier and piston body were of cast aluminium alloy had problems due to dislodging of ring carrier from skirt, because not enough interference could be provided. - Modifications made to overcome this issue: - Forged ring carrier shrunk onto cast piston body. - Both ring carrier and body are of high density aluminium alloy forging, with increased interference between ring carrier and piston body. - This resulted in the increased weight of the piston, which caused a balancing problem due to the higher density of the alloy. - The problem was solved by cutting out approximately 5/8” from the skirt. - This resulted in the lack of space for the third oil scrapper ring, which reduced the number of piston rings from 6 to 5 . - The crown of the piston is cooled by flowing of lube oil, which travels from piston pin reaches the piston, passes through the vertical oil hole, and then travels through the 4 circular grooves machined on the spigot portion of the piston body. - The hot oil falls down through the second vertical hole back to the sump, after passing through the grooves and absorbing heat all the way. ### STEEL CAP PISTONS - Steel cap pistons are in use. - Features: - Body of aluminum alloy forging but a cap of steel is placed in place of forged aluminum ring carrier. - The steel cap only takes 3 compression rings, and the top groove does not have any hi-resist insert like that of aluminum alloy ring carrier. - Steel cap piston needs more lube oil pressure, and more mass flow of oil so that more heat is absorbed, which are provided by increased flow of lube oil and increase in oil passage dia due to better heat transfer. - The steel cap is assembled and dis-assembled with hydraulic pressure - Steel cap pistons have 5 rings - The steel caps are hydraulically pressed and secured. - The cap is provided with a spigot and screw arrangement for additional hold on piston body. - Steel cap pistons are giving reasonable good service in Indian Railways. ### STEEL CAP PISTON IMPROVED CROWN DESIGN ### MAHLE PISTON - It is supplied by the firm M/s Mahle of West Germany. - It is a one piece cast aluminium piston cast with hollow tube coil for providing cooling oil passage. - It is trouble free due to no question of dis-loading of the ring carrier. - The disadvantage of this type is that no reclamation by changing ring carrier as in other piston can be done. - They have six piston rings, and Niresist ring inserts fitted to take the top ring. - The metal composition of the Mahle piston material is: - Silicon - Copper - Nickel - Magnesium - Aluminium - remainder ### PISTON RINGS - Piston rings along with cylinder liner present the major wear and maintenance problem for a diesel engine . - Functions of piston rings: - Preventing blow by air and high temperature combustion gases & prevent same from getting access to crank case. - Preventing excessive amount of lube oil from reaching combustion chamber. ### TYPES OF PISTON RINGS - There are many varieties of piston rings: - Compression rings - Square face - Taper face - Inside bevel - Key stone. - Oil P scraper rings or oil rings - Wide channel double lip - Special bevel single lip. - Comformable rings. - The piston ring material is cast iron with open graphite structure and a硬 pearlitic matrix. - The piston rings generally have following two types of coatings: - Scuff resisting and quick seating coating - Wear and corrosion resistant coatings. ### LINER - There are two types of Liners: - Dry liner - Wet liner - Dry liners never come in contact with coolant, but have slight interference in cylinder, and are used only in very small engines. - Wet Liners are those where synthetic rubber seals of suitable qualities are to be used, and have slight interference fit in the cylinder on upper and lower decks. - The liner bore has chrome plated surface and is honey chromed by electrolytic process. - Some liners have no step size in the bore. - The liner has only one standard size permitting a wear of 0.009 inch. - MAK cylinder liner is not interference fit with the cylinder decks, and only has a sliding fit, and is prevented by gaskets. - General Motor cylinder liners are fabricated type embodying the water jacket. - The piston rings are chrome plated instead of liner bore chrome plated in General Motor liners. - Cylinder liners are made of high strength close grained alloy cast iron, which is heat treated to relieve stresses. - The composition of the cylinder metal is: - Carbon - Silicon - Sulpher - Phosphorus - Manganese - Chromium - Molybdenum - The cylinder liners suffer from the following major defects: - Wear in the bore - Loss of interference in the top & bottom decks - Cavitation erosion of outside circumference. - Cylinder liners can be reclaimed by re-chrome plating in case of wear in the bore up to a certain limit. - Liners have to be taken out of use if the cavity due to Cavitation and erosion, is more than 1/8” deep. ### CONNECTIING ROD - A member connecting piston and crankshaft. - It is the medium for converting the reciprocating motion to rotary motion. - In four-stroke engines, the connecting rod is subject to high compressive load during the compression and power stroke, and tensile stress during the suction stroke. - In two-cycle engine, the connecting rod is only subject to compressive load. - The connecting rod length is usually about 4 to 5 times of the crank radius. - Most connecting rods are made of ‘section having a file drilled hole. - Parts of a connecting rod: - Connecting rod - Connecting - rod cap - Piston pin bushing - Shell upper - Shell power - Connecting rod bolts - and nuts. - Connecting rods are mostly made of carbon steel or alloy steel forgings. - The metal composition of connecting rods is: - Carbon - Manganese - Phosphorous - Sulphur - Silicon - Nickel - Chromium - Molybdenum - Boron - The bolts are tightened with specified torque during assembly. ### CRANKSHAFT BEARINGS - Crankshaft bearings are used in diesel engines during installation. ### Engine bearings structure - There are two types of bearings: - Bi-metal bearing - Tri-metal bearing - **Bi-metal bearing:** - Consists of Aluminium bearing alloy, and Aluminium bonding layer. - The back is steel. - **Tri-metal bearing:** - Consists of Nickel barrier, Copper alloy, and Overlay. - The back is steel. ### Thinwall Bearing - It is a prefinished precision made steel backed component lined with an appropriate bearing material. - It is capable of withstanding the applied load. - It is compatible with the crankshaft. - Thin wall bearings offer a range of materials, and allow good repeatability of a bearing assembly. - Bearings will conform to the profile of the housing bore. ### Bearing Lining - It is made up of various layers of materials. - The lining is bonded to the steel backing. - The most common lining materials are tin-aluminium and lead bronze materials. - The typical bearing lining thickness will lie in the range of 0.5 — 1.00 mm. ### Overlay - It is a thin soft overlay plate applied to the lining material. - It provides better conformability and embed ability, which improves wear rate and bearing life. - The common overlays are lead-tin and lead-tin-copper. - Overlay protects against corrosion by degraded or contaminated oils. ### Interlayer - A thin interlayer of nickel (no more than 5 m) is applied between the bearing lining and overlay plate. - It ensures satisfactory bond of the overlay in tin-aluminium bearings. - It reduces the rate of tin diffusion and wear rate and increases the corrosion resistance of the overlay, in lead bronze bearings. ### Flash - A thin "flash" of either tin or lead tin is applied to the bearing bore and back. - It provides protection against corrosion prior to the installation of the bearing. - The typical thickness of flash is 1-2 m. ### Freespread - It is the difference across the joints of a bearing in its free state and the housing diameter. - It is applied so that the bearing is positively located radially when assembled into the housing. - Free spread allows an assembly to be inverted. - Bearings may show a loss of free spread after a period of operation. - A bearing with positive free spread can be refitted. - Bearings with negative free spread must not be refitted as this could lead to the bearing being trapped against the shaft. ### Nick, Tang or Lug - Its sole purpose is to locate the bearing axially, ensuring correct alignment of the oil transfer passages and to allow clearance between the ends of the bearing and the crankshaft fillets. - The nick recess in the housing must allow for sufficient clearance to minimize bearing distortion and rapid wear. - The nick is located below the joint face of the bearing. This feature is called nick relief. ### Nip or Crush - Interference fit is achieved by making the peripheral length of the bearing greater than that of the housing. - Nip generates a hoop stress in the bearing, and contact pressure between the bearing back and the housing bore. - Contact pressure prevents rotation or relative movement of the bearing. - Reduction of nip can result in fretting and even rotation of the bearings. ### Bore Relief - A step is created at the joints, as a variation of wall thickness occurs between the two bearings of any assembly within the manufacturing tolerance. - Local relief of the bore surface at the joint faces (termed “bore relief”) is incorporated in most medium speed diesel engine bearings,to overcome the possibility of this step disrupting the oil film. ### General Design Recommendations - 265—320 HV5 (25— 32 HRc) is the recommended crankshaft hardness for medium speed diesel engines. - Higher values of hardness will improve the wear rate, but will be more prone to thermal cracking, particularly above 425 HV5 (43 HRc). - Lower values of hardness will have a higher wear rate. ### Acceptable Surface Roughness - The housing with an inferior surface finish can result in poor contact between bearing back and housing. - Poorly machined journal can lead to excessive wear of the bearing bore. ### Clearance - The optimum clearance for each engine is established by experience. - Theoretical load carrying capacity reduces as clearance between the crankshaft and the bearing bore increases. - An increased quantity of oil can be pumped through a larger clearance, which keeps the temperature lower. - The recommended minimum diametral clearance is 0.00075 of the bearing diameter. ### Assembly of Crank Shaft Bearings - Any protective coating should be removed from bearings before assembly, by washing with a suitable solvent and wiped with a clean cloth. - Check part number on the bearing back, and visually check for correct design, oil holes, nick position, and burrs or sharp edges. - Do not rub or scrape the bore or joint faces. - The crankshaft, housing bore and joint faces should be checked for oil, dirt, burrs and sharp edges. - Clean the oil ways thoroughly. - Check for fretting or bruising damage. - Light rub the housing bore with an abrasive stone or burnishing tool if the damage is minor, but ensure the refurbishing does not create a depression. - Check for wear on the joint faces of used housings. - Light rub the protrusions if the damage is minor. - Used housings can be re-used only if the joints are re-machined and re-bored if the damage is severe. - Ensure that location dowels are satisfactory and free from burrs in used assemblies. ### Bearing Identification - The bearings should be clearly marked to show their position in the engine prior to installation. - It is recommended to etch or scribe an identification mark into a groove or nick. - It is not advisable to mark the joints or bearing back. ### Housing Identification - A clear identification mark is recommended on one end of both the cap and rod or block either side of one joint. - The identification marks should line up with each other during reassembly. ### Bearing Assembly - Before assembly, ensure all parts are free from oil, dirt and burrs. - Do not apply oil between the bearing back and housing bore. - Liberally coat with oil between the bearing bore and crankshaft surfaces. - Position the nick of the bearing in the recess first, and carefully rotate and press the bearing into its housing. - The nick should not protrude above the joint line to prevent excessive stress. - The nick is relieved below the bearing joint face to reduce the possibility of this happening. - When refitting into field or service engines, enter the un-nicked end of the bearing first, and rotate it around the housing. - Ensure the joint face of the nick is below the level of the joint face of the housing. - Apply oil to bearing bores before assembling the two halves together. - Ensure any location dowels are correctly positioned when assembling the main and large end caps. - Renew any damaged dowels in used assemblies. - Inspect and ensure the bolts conform to the accepted standard.