TAPMOTION® MD-III Operating Instructions PDF
Document Details
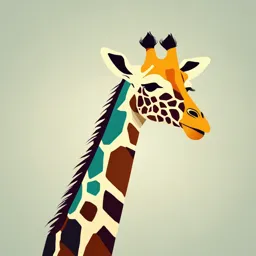
Uploaded by BestSellingBeige
null
Tags
Summary
This document is a comprehensive operating manual for a TAPMOTION® MD-III motor-drive unit. It includes detailed information about the device's safe use, features, and safety procedures. The manual covers product descriptions, safety procedures, and operational characteristics.
Full Transcript
Motor-Drive Unit TAPMOTION® MD-III Operating Instructions 3913897/02 EN © All rights reserved by Maschinenfabrik Reinhausen Dissemination and reproduction of this document and use and disclosure of its content are strictly prohibited unless expressly permitted. Infringements will result in liabili...
Motor-Drive Unit TAPMOTION® MD-III Operating Instructions 3913897/02 EN © All rights reserved by Maschinenfabrik Reinhausen Dissemination and reproduction of this document and use and disclosure of its content are strictly prohibited unless expressly permitted. Infringements will result in liability for compensation. All rights reserved in the event of the granting of patents, utility models or designs. The product may have been altered since this document was published. We reserve the right to change the technical data, design and scope of supply. Generally the information provided and agreements made when processing the individual quotations and orders are binding. The original operating instructions were written in German. Table of contents Table of contents 1 Introduction......................................................................................................................... 6 1.1 Validity................................................................................................................................................ 6 1.2 Manufacturer....................................................................................................................................... 6 1.3 Subject to change without notice........................................................................................................ 6 1.4 Completeness..................................................................................................................................... 6 1.5 Supporting documents........................................................................................................................ 7 1.6 Safekeeping........................................................................................................................................ 7 1.7 Notation conventions.......................................................................................................................... 7 1.7.1 Symbols................................................................................................................................................................ 7 1.7.2 Information system................................................................................................................................................ 8 1.7.3 Hazard communication system............................................................................................................................. 8 2 Safety................................................................................................................................. 11 2.1 General safety information................................................................................................................ 11 2.2 Appropriate use................................................................................................................................ 11 2.3 Inappropriate use.............................................................................................................................. 11 2.4 Personnel qualification...................................................................................................................... 12 2.5 Operator's duty of care..................................................................................................................... 12 2.6 Personal protective equipment......................................................................................................... 12 2.7 Protective devices in the motor-drive unit......................................................................................... 13 3 Product description.......................................................................................................... 15 3.1 Motor-drive unit................................................................................................................................. 15 3.1.1 Function description of motor-drive unit.............................................................................................................. 15 3.1.2 Performance features.......................................................................................................................................... 15 3.1.3 Scope of delivery................................................................................................................................................. 15 3.1.4 Design................................................................................................................................................................. 16 3.2 Monitoring system (VIM)................................................................................................................... 18 3.2.1 Function description of monitoring system.......................................................................................................... 19 3.2.2 Monitoring system design................................................................................................................................... 20 3.2.3 Monitoring system displays and controls............................................................................................................ 21 3.2.4 Maintenance mode.............................................................................................................................................. 21 3.2.5 Test function........................................................................................................................................................ 22 3.2.6 Overview of monitoring system operating statuses............................................................................................. 22 Maschinenfabrik Reinhausen GmbH 2019 3913897/02 EN TAPMOTION® MD-III 3 Table of contents 4 Packaging, transport and storage.................................................................................. 23 4.1 Packaging......................................................................................................................................... 23 4.1.1 Suitability............................................................................................................................................................. 23 4.1.2 Markings.............................................................................................................................................................. 23 4.2 Transportation, receipt and handling of shipments........................................................................... 24 4.3 Storage of shipments........................................................................................................................ 25 4.4 Unpacking shipments and checking for transportation damages..................................................... 26 4.5 Things to note when putting back into storage................................................................................. 26 5 Fitting motor-drive unit.................................................................................................... 27 5.1 Preparatory work.............................................................................................................................. 27 5.2 Fitting motor-drive unit to on-load tap-changer................................................................................. 30 5.3 Fitting motor-drive unit to transformer tank....................................................................................... 35 5.4 Installing electrics for motor-drive unit.............................................................................................. 39 6 Checks after assembly..................................................................................................... 41 6.1 Preparations..................................................................................................................................... 41 6.2 Electrical test operations................................................................................................................... 41 6.3 Testing monitoring system................................................................................................................ 43 7 Drying procedure.............................................................................................................. 46 8 Commissioning at the transformer manufacturer's site............................................... 47 8.1 High-voltage tests on the transformer............................................................................................... 48 8.2 Dielectric tests on transformer wiring................................................................................................ 49 9 Transporting transformer to installation site................................................................. 50 9.1 Transport with removed drive........................................................................................................... 50 10 Commissioning motor-drive unit at the operating site................................................. 51 11 Actuating motor-drive unit with hand crank.................................................................. 53 12 Monitoring during operation........................................................................................... 54 12.1 Annual check.................................................................................................................................... 54 12.1.1 Checking motor-drive unit................................................................................................................................... 54 12.1.2 Checking return to starting position..................................................................................................................... 54 12.2 Occasional visual checks.................................................................................................................. 55 4 TAPMOTION® MD-III 3913897/02 EN Maschinenfabrik Reinhausen GmbH 2019 Table of contents 13 Fault elimination............................................................................................................... 56 13.1 General information.......................................................................................................................... 56 13.2 Fault elimination overview................................................................................................................ 57 14 Maintenance...................................................................................................................... 58 14.1 Maintenance intervals....................................................................................................................... 58 14.2 Taking on-load tap-changer out of service....................................................................................... 58 14.3 Maintaining motor-drive unit............................................................................................................. 59 14.4 Maintaining monitoring system......................................................................................................... 59 15 Technical data................................................................................................................... 60 15.1 Technical data for TAPMOTION® MD-III......................................................................................... 60 15.2 Technical data for position transmitter equipment............................................................................ 61 Maschinenfabrik Reinhausen GmbH 2019 3913897/02 EN TAPMOTION® MD-III 5 1 Introduction 1 Introduction This technical file contains detailed descriptions on the safe and proper in- stallation, connection, commissioning and monitoring of the product. It also includes safety instructions and general information about the prod- uct. This technical file is intended solely for specially trained and authorized per- sonnel. 1.1 Validity This technical file is valid for the TAPMOTION® MD-III product. Drawings and illustrations in this technical file are provided for reference only. For specific details please refer to drawings submitted with each indi- vidual customer order. 1.2 Manufacturer This product is manufactured by: Reinhausen Manufacturing Inc. 2549 North 9th Avenue, 38343 Humboldt, Tennessee, USA Tel.: +1 731 784 7681 Fax: +1 731 784 7682 Further information on the product and copies of this technical file are avail- able from this address if required. 1.3 Subject to change without notice The information contained in this technical file comprises the technical speci- fications approved at the time of printing. Significant modifications will be in- cluded in a new edition of the technical file. The document number and version number of this technical file are shown in the footer. 1.4 Completeness This technical file is incomplete without the supporting documentation. 6 TAPMOTION® MD-III 3913897/02 EN Maschinenfabrik Reinhausen GmbH 2019 1 Introduction 1.5 Supporting documents The following documents also apply in addition to this technical file: ▪ Technical data and drawings which are provided upon order confirmation and delivery Also observe generally valid legislation, standards, and guidelines as well as specifications on accident prevention and environmental protection in the re- spective country of use. 1.6 Safekeeping This technical file and all supporting documents must be kept ready at hand and accessible for future use at all times. 1.7 Notation conventions This section contains an overview of the symbols and textual emphasis used. 1.7.1 Symbols Symbol Meaning Wrench size Tightening torque Number and type of fastening materials used Fill with oil Cut open, cut through Clean Visual inspection Use your hand Maschinenfabrik Reinhausen GmbH 2019 3913897/02 EN TAPMOTION® MD-III 7 1 Introduction Symbol Meaning Adapter ring Apply a coat of paint Use a file Grease Coupling bolt Use a ruler Use a saw Hose clip Wire eyelet, safety wire Use a screwdriver Table 1: Symbols 1.7.2 Information system Information is designed to simplify and improve understanding of particular procedures. In this technical file it is laid out as follows: Important information. 1.7.3 Hazard communication system Warnings in this technical file are displayed as follows. 8 TAPMOTION® MD-III 3913897/02 EN Maschinenfabrik Reinhausen GmbH 2019 1 Introduction 1.7.3.1 Warning relating to section Warnings relating to sections refer to entire chapters or sections, sub-sec- tions or several paragraphs within this technical file. Warnings relating to sections use the following format: WARNING Type and source of danger Consequences ► Action ► Action 1.7.3.2 Embedded warning information Embedded warnings refer to a particular part within a section. These warn- ings apply to smaller units of information than the warnings relating to sec- tions. Embedded warnings use the following format: DANGER! Instruction for avoiding a dangerous situation. 1.7.3.3 Signal words and pictograms The following signal words are used: Signal word Meaning DANGER Indicates a hazardous situation which, if not avoided, will result in death or serious injury. WARNING Indicates a hazardous situation which, if not avoided, could result in death or serious injury. CAUTION Indicates a hazardous situation which, if not avoided, could result in injury. NOTICE Indicates measures to be taken to prevent damage to property. Table 2: Signal words in warning notices Pictograms warn of dangers: Pictogram Meaning Warning of a danger point Warning of dangerous electrical voltage Maschinenfabrik Reinhausen GmbH 2019 3913897/02 EN TAPMOTION® MD-III 9 1 Introduction Pictogram Meaning Warning of combustible substances Warning of danger of tipping Table 3: Pictograms used in warning notices 10 TAPMOTION® MD-III 3913897/02 EN Maschinenfabrik Reinhausen GmbH 2019 2 Safety 2 Safety 2.1 General safety information The technical file contains detailed descriptions on the safe and proper in- stallation, connection, commissioning and monitoring of the product. ▪ Read this technical file through carefully to familiarize yourself with the product. ▪ Particular attention should be paid to the information given in this chapter. 2.2 Appropriate use The product and associated equipment and special tools supplied with it comply with the relevant legislation, regulations and standards, particularly health and safety requirements, applicable at the time of delivery. If used as intended and in compliance with the specified requirements and conditions in this technical file as well as the warning notices in this technical file and attached to the product, then the product does not present any haz- ards to people, property or the environment. This applies throughout the product's entire life, from delivery through installation and operation to disas- sembly and disposal. The operational quality assurance system ensures a consistently high quality standard, particularly in regard to the observance of health and safety re- quirements. The following is considered appropriate use ▪ Only operate the product in accordance with this technical file and the agreed delivery conditions and technical data ▪ Use the equipment and special tools supplied solely for the intended pur- pose and in accordance with the specifications of this technical file ▪ Use the product only with the transformer specified in the order ▪ The serial numbers of the on-load tap-changer and drive must match. 2.3 Inappropriate use Use is considered to be inappropriate if the product is used other than as de- scribed in the Appropriate use section. Reinhausen Manufacturing does not accept liability for damage resulting from unauthorized or inappropriate changes to the product. Inappropriate changes to the product without consultation with Reinhausen Manufacturing can lead to personal injury, damage to property and operational disruption. Maschinenfabrik Reinhausen GmbH 2019 3913897/02 EN TAPMOTION® MD-III 11 2 Safety 2.4 Personnel qualification The product is designed solely for use in electrical energy systems and facili- ties operated by appropriately trained staff. This staff comprises people who are familiar with the installation, assembly, commissioning and operation of such products. 2.5 Operator's duty of care To prevent accidents, disruptions and damage as well as unacceptable ad- verse effects on the environment, those responsible for transport, installa- tion, operation, maintenance and disposal of the product or parts of the prod- uct must ensure the following: ▪ All warning and hazard notices are complied with. ▪ Personnel are instructed regularly in all relevant aspects of operational safety, the operating instructions and particularly the safety instructions contained therein. ▪ Regulations and operating instructions for safe working as well as the rel- evant instructions for staff procedures in the case of accidents and fires are kept on hand at all times and are displayed in the workplace where applicable. ▪ The product is only used when in a sound operational condition and safety equipment in particular is checked regularly for operational reliability. ▪ Only replacement parts, lubricants and auxiliary materials which are au- thorized by the manufacturer are used. ▪ The specified operating conditions and requirements of the installation lo- cation are complied with. ▪ All necessary devices and personal protective equipment for the specific activity are made available. ▪ The prescribed maintenance intervals and the relevant regulations are complied with. ▪ Installation, electrical connection and commissioning of the product may only be carried out by qualified and trained personnel in accordance with this technical file. ▪ The operator must ensure appropriate use of the product. 2.6 Personal protective equipment Personal protective equipment must be worn during work to minimize risks to health. ▪ Always wear the personal protective equipment required for the job at hand. ▪ Follow information about personal protective equipment provided in the work area. 12 TAPMOTION® MD-III 3913897/02 EN Maschinenfabrik Reinhausen GmbH 2019 2 Safety Always wear Protective clothing Close-fitting work clothing with a low breaking strength, with tight sleeves and with no protrud- ing parts. It mainly serves to protect the wearer against being caught by moving machine parts. Do not wear any rings, necklaces or other jew- elry. Safety shoes To protect against falling heavy objects and slip- ping on slippery surfaces. Table 4: Personal protective equipment to be worn at all times Wear the following in special Special personal protective equipment is environments needed in special environments. The choice of equipment depends on the cir- cumstances. Safety glasses To protect the eyes from flying parts and splash- ing liquids. Hard hat To protect from falling and flying parts and mate- rials. Hearing protection To protect from hearing damage. Table 5: Personal protective equipment to be worn in special environments 2.7 Protective devices in the motor-drive unit The following protective devices are fitted in the motor-drive unit: ▪ End stop device (mechanical and electric) ▪ Device protecting against unintentional passage ▪ Motor protection device Maschinenfabrik Reinhausen GmbH 2019 3913897/02 EN TAPMOTION® MD-III 13 2 Safety ▪ Protection against accidental contact ▪ Electronics of monitoring system to monitor the vacuum interrupters in the on-load tap-changer 14 TAPMOTION® MD-III 3913897/02 EN Maschinenfabrik Reinhausen GmbH 2019 3 Product description 3 Product description This chapter contains an overview of the design and function of the motor- drive unit and monitoring system. 3.1 Motor-drive unit 3.1.1 Function description of motor-drive unit The motor-drive unit adjusts the operating position of on-load tap-changers in regulating transformers to the individual operating requirements. The tap-change operation is activated by starting the motor-drive unit (a sin- gle control impulse triggered, for example, by a voltage regulator of the TAPCON®-series). This operation is always completed regardless of any other control pulses emitted during the tap-change operation. In the standard design, the next tap-change operation can only proceed once all control de- vices have reached their rest positions. Behavior in the event of a voltage interruption Should the voltage be interrupted during an on-load tap-change operation, once the voltage supply returns, the motor-drive unit completes the started on-load tap-change operation. 3.1.2 Performance features The motor-drive unit is particularly characterized by the following properties: ▪ Hand crank with interlocking switch ▪ Protection against accidental contact when doors are open ▪ Tap position indicator which is clear and easy to read ▪ TAPCON® 250 voltage regulator can be integrated ▪ Rapid replacement of the position transmitter modules since the functions of the position transmitter board and position transmitter module are sepa- rate ▪ Panel heater as anti-condensation heater ▪ Monitoring system to monitor vacuum interrupters in the on-load tap- changer 3.1.3 Scope of delivery The motor-drive unit is packaged with protection against moisture and is de- livered as follows: ▪ Motor-drive unit with hand crank and hand lamp ▪ Product documentation Maschinenfabrik Reinhausen GmbH 2019 3913897/02 EN TAPMOTION® MD-III 15 3 Product description Please note the following: 1. Check the shipment for completeness on the basis of the shipping docu- ments. 2. Store the parts in a dry place until installation. 3. The product must remain in its airtight, protective wrapping and may only be removed immediately before installation. 3.1.4 Design This chapter contains an overview of the design of the MD-III motor-drive unit. The actual motor-drive unit equipment and the arrangement of the individual elements may differ from those shown. Figure 1: View of MD-III motor-drive unit 1 Motor protective switch 8-2 9 Hand lamp 2 Circuit breaker (optional) 10 Voltage regulator (optional) 3 VIM-OK signal lamp (86GL) 11 Monitoring circuit board 4 Alarm signal lamp (86RL) 12 Transmission gear cover plate 5 LOCAL/REMOTE/AUTO pivot 13 Name plate switch 6 RAISE/LOWER pivot switch 14 Indication field 16 TAPMOTION® MD-III 3913897/02 EN Maschinenfabrik Reinhausen GmbH 2019 3 Product description 7 Spring lock 15 Hand crank aperture with guide lever 8 Front cover on swing frame 16 Hand crank The front cover on the swing frame and the transmission gear cover plate ensure protection against accidental contact when the doors are open. 3.1.4.1 Indication field A clear indication field is fitted in the motor-drive unit. Pointer and operations counter are mechanically driven and indicate the tap-change operation se- quence of the motor-drive unit. The reset wheel on the operations counter is lead-sealed at the factory. Figure 2: Indication field 1 Tap position indicator 3 The tap-change indicator: Shows the current position of the control cam 2 The two drag hands indicate the 4 The mechanical operations regulating range currently used counter shows the overall number of tap-change operations 3.1.4.2 Hand crank lock (optional) An optional mechanical hand crank lock can be used to block the hand crank in cases where the monitoring system reports a fault or is not ready for oper- ation. 3.1.4.3 Anti-condensation heater The anti-condensation heater is designed as a panel heater which also acts as the front cover of the swing frame. Maschinenfabrik Reinhausen GmbH 2019 3913897/02 EN TAPMOTION® MD-III 17 3 Product description The design of the motor-drive unit and panel heater ensures that air circu- lates inside the motor-drive unit and therefore that there is a constant interior temperature which is always higher than the outside temperature. 3.1.4.4 Swing frame/terminal rail The swing frame protects all electrical and mechanical parts of the motor- drive unit behind the swing frame against accidental contact. The terminal rail behind the swing frame facilitates an easy electrical con- nection of the motor-drive unit. The wiring is easily connected using vertically arranged cap rails with the corresponding installed terminal bars. 3.1.4.5 Position transmitter equipment The position transmitter equipment is used to remotely indicate the operating position of the on-load tap-changer when idle. The remote display is available in various versions. The position transmitter module for connection by the customer is located on the terminal rail. For more information about the position transmitter equipment, see Installing electrics for motor-drive unit [►Section 5.4, Page 39] section. 3.1.4.6 Transmission gear cover plate The touch-protected transmission gear cover plate features an opening for the hand crank used in manual mode. For operation, observe the information provided in the Actuating motor-drive unit with hand crank [►Section 11, Page 53] chapter. 3.2 Monitoring system (VIM) The monitoring system is also known as the VIM module (Vacuum Inter- rupter Monitoring). 18 TAPMOTION® MD-III 3913897/02 EN Maschinenfabrik Reinhausen GmbH 2019 3 Product description 3.2.1 Function description of monitoring system WARNING Danger of death, severe injury and damage to property! Danger of death, severe injury and damage to property due to incorrect op- eration of hand crank and monitoring system! ► Never actuate on-load tap-changer with the hand crank if the transformer is energized. When the hand crank is operated, the monitoring system no longer provides protection so failure of a vacuum interrupter may result in injuries to operating staff and/or damage to the transformer. ► Check the on-load tap-changer when the monitoring system trips during operation. ► Before resetting the monitoring system, always first establish the cause and remedy the fault. ► The monitoring system improves operating reliability, but cannot cover all operating statuses. There is a high probability that the monitoring system will detect a vacuum interrupter malfunction in the following operating modes: ▪ Electric on-load tap-change operation resulting from manual actuation of the RAISE/LOWER pivot switch ▪ Electric on-load tap-change operation resulting from automatic activation by a voltage regulator If the hand crank is operated, the monitoring system does not provide pro- tection. An optional mechanical hand crank lock can be used to block the hand crank in cases where the monitoring system reports a fault or is not ready for oper- ation. In the event of an error, the monitoring system triggers the following actions: ▪ The on-load tap-changer is stopped and returned to its starting position ▪ The motor protective switch 8-2 is tripped ▪ Further electrical on-load tap-change operations are blocked ▪ In designs with an appropriate hand crank lock: Hand crank operations are also blocked ▪ The error indication on the monitoring circuit board lights up – Yellow LED for errors in the signal transmission – Red LED for errors in a vacuum interrupter ▪ Error messages are indicated by illumination of the red Alarm signal lamp (86RL) on the swing frame of the motor-drive unit. Maschinenfabrik Reinhausen GmbH 2019 3913897/02 EN TAPMOTION® MD-III 19 3 Product description 3.2.2 Monitoring system design Figure 3: Monitoring system (VIM), schematic diagram The monitoring system evaluates the current signals in the on-load tap- changer. For fail-safe transmission, the current signals are converted into optical signals and transferred via fiber-optic cables. The monitoring system carries out the following checks: 1. After the by-pass switch has opened and before the vacuum interrupter opens, there must be a current signal. 2. Once the vacuum interrupter opens, there must be no current signal present. If one is present, the monitoring system generates an alarm signal. The monitoring system is also fitted with self-monitoring, which checks the internal circuits. At the input, the electronics are protected by a Zener diode and an interchangeable fuse. 20 TAPMOTION® MD-III 3913897/02 EN Maschinenfabrik Reinhausen GmbH 2019 3 Product description 3.2.3 Monitoring system displays and controls Figure 4: Monitoring system (VIM) displays and controls 1 Green TEST push-button 3 1 yellow and 1 red LED per phase for signaling errors 2 Green Power LED 4 Red RESET push-button The following displays and controls of the monitoring system (Vacuum Inter- rupter Monitoring VIM) are located behind the motor-drive unit's door: ▪ The green TEST push-button is used to check the internal circuitry of the monitoring system. ▪ 1 green LED indicates the control voltage supply present ▪ 3 red LEDs (1 per phase) indicate when a vacuum interrupter malfunction has been recorded – The monitoring system performs this check during every diverter switch operation ▪ 3 yellow LEDs (1 per phase) indicate the loss of the current-transformer signal – The monitoring system repeats this check after every 2 tap-change op- erations for network applications and after every 32 tap-change opera- tions for industrial applications. ▪ The red RESET push-button is used to activate the monitoring system af- ter an inspection. 3.2.4 Maintenance mode When performing test tap-change operations with a de-energized trans- former, it may be useful to put the monitoring system into maintenance mode. The integrity test for the fiber-optic cable is suspended in this case. To switch to maintenance mode, proceed as follows: 1. DANGER! Maintenance mode must not be activated if the transformer is energized. Maschinenfabrik Reinhausen GmbH 2019 3913897/02 EN TAPMOTION® MD-III 21 3 Product description 2. Press and hold the RESET push-button for around 6 seconds to disable the verification system for 10 hours. ð The 3 yellow LEDs on the monitoring circuit board flash slowly ð At the end of the 10 hours, the yellow LED go out and the unit returns to its normal function 3. You can press the TEST push-button at any time to exit maintenance mode, instead of waiting for the time to expire. 3.2.5 Test function An error can be simulated by pressing the green TEST push-button, e.g. to check that the on-load tap-changer returns to its starting position during an on-load tap-change operation. The alarm status can be reset by pressing the red RESET push-button. You will find a description of this function in the In- service monitoring system verification section. 3.2.6 Overview of monitoring system operating statuses In the motor-drive unit, LEDs on the monitoring circuit board and on the swing frame indicate various operating states or events: Monitoring display Swing frame display Operating status Green LED Yellow LED Red LED 86GL 86RL Power Fault Alarm VIM ok VIM Alarm Normal operation ON OFF OFF ON OFF Control voltage supply fault OFF OFF OFF OFF ON Loss of current transformer signal ON ON OFF ON ON Vacuum interrupter error ON OFF ON ON ON Maintenance mode ON FLASHING OFF ON OFF Test mode ON OFF ON ON ON 22 TAPMOTION® MD-III 3913897/02 EN Maschinenfabrik Reinhausen GmbH 2019 4 Packaging, transport and storage 4 Packaging, transport and storage 4.1 Packaging The products are sometimes supplied with a sealed packaging and some- times also dried depending on what is required. A sealed packaging surrounds the packaged goods on all sides with plastic foil. Products that have also been dried are identified by a yellow label on the sealed packaging. The information in the following sections should be applied as appropriate. 4.1.1 Suitability NOTICE Property damage due to incorrectly stacked crates! Stacking the crates incorrectly can lead to damage to the packaged goods! ► Only stack up to 2 equally sized crates on top of one another. The packaging is suitable for undamaged and fully functional means of transportation in compliance with local transportation laws and regulations. The packaged goods are packed in a stable crate. This crate ensures that the packaged goods are secure when in the intended transportation position and that none of the parts touch the loading surface of the means of trans- port or touch the ground after unloading. The packaged goods are stabilized inside the crate to prevent impermissible changes in position. A sealed packaging surrounds the packaged goods on all sides with plastic foil. The packaged goods are protected from humidity using a desiccant. The plastic foil is bonded after the drying agent is added. 4.1.2 Markings The packaging bears a signature with instructions for safe transport and cor- rect storage. The following symbols apply to the shipment of non-hazardous goods. Adherence to these symbols is mandatory. Protect against Top Fragile Attach lifting Center of mass moisture gear here Table 6: Shipping pictograms Maschinenfabrik Reinhausen GmbH 2019 3913897/02 EN TAPMOTION® MD-III 23 4 Packaging, transport and storage 4.2 Transportation, receipt and handling of shipments WARNING Danger of death and damage to property! Danger of death and damage to property due to tipping or falling load! ► Transport crate only when closed. ► Do not remove the mounting material used in the crate during transport. ► Only trained and appointed persons may select the sling gear and secure the load. ► Do not walk under the hanging load. ► Use means of transport and lifting gear with a sufficient carrying capacity in accordance with the weight stated on the delivery slip. In addition to oscillation stress and shock stress, jolts must also be expected during transportation. In order to prevent possible damage, avoid dropping, tipping, knocking over and colliding with the product. If a crate tips over, falls from a certain height (e.g. when slings tear) or expe- riences an unbroken fall, damage must be expected regardless of the weight. Every delivered shipment must be checked for the following by the recipient before acceptance (acknowledgment of receipt): ▪ Completeness based on the delivery slip ▪ External damage of any type. The checks must take place after unloading when the crate or transport con- tainer can be accessed from all sides. Visible damage If external transport damage is detected on receipt of the shipment, proceed as follows: ▪ Immediately record the transport damage found in the shipping docu- ments and have this countersigned by the carrier. ▪ In the event of severe damage, total loss or high damage costs, immedi- ately notify the sales department at Maschinenfabrik Reinhausen and the relevant insurance company. ▪ After identifying damage, do not modify the condition of the shipment fur- ther and retain the packaging material until an inspection decision has been made by the transport company or the insurance company. ▪ Record the details of the damage immediately onsite together with the carrier involved. This is essential for any claim for damages! ▪ Photograph damage to packaging and packaged goods. This also applies to signs of corrosion on the packaged goods due to moisture inside the packaging (rain, snow, condensation). ▪ NOTICE! Be absolutely sure to also check the sealed packaging. If the sealed packaging is damaged, do not under any circumstances install or commission the packaged goods. Either dry the dried packaged goods again as per the operating instructions for the relevant on-load tap- 24 TAPMOTION® MD-III 3913897/02 EN Maschinenfabrik Reinhausen GmbH 2019 4 Packaging, transport and storage changer/de-energized tap-changer or contact Maschinenfabrik Rein- hausen GmbH to agree on how to proceed with drying. If this is not done, the packaged goods may be damaged. ▪ Name the damaged parts. Hidden damage When damages are not determined until unpacking after receipt of the ship- ment (hidden damage), proceed as follows: ▪ Make the party responsible for the damage liable as soon as possible by telephone and in writing, and prepare a damage report. ▪ Observe the time periods applicable to such actions in the respective country. Inquire about these in good time. With hidden damage, it is very hard to make the transportation company (or other responsible party) liable. Any insurance claims for such damages can only be successful if relevant provisions are expressly included in the insur- ance terms and conditions. 4.3 Storage of shipments Packaged goods dried by Maschinenfabrik Reinhausen Upon receipt of the shipment, immediately remove the packaged goods dried by Maschinenfabrik Reinhausen from the sealed packaging and store air-tight in dry insulating oil until used. Non-dried packaged goods Non-dried packaged goods but with a functional sealed packaging can be stored outdoors when the following conditions are complied with. When selecting and setting up the storage location, ensure the following: ▪ Protect stored goods against moisture (flooding, water from melting snow and ice), dirt, pests such as rats, mice, termites and so on, and against unauthorized access. ▪ Store the crates on timber beams and planks as a protection against ris- ing damp and for better ventilation. ▪ Ensure sufficient carrying capacity of the ground. ▪ Keep entrance paths free. ▪ Check stored goods at regular intervals. Also take appropriate action after storms, heavy rain or snow and so on. Protect the packaging foil from direct sunlight so that it does not disintegrate under the influence of UV rays, which would cause the packaging to lose its sealing function. Maschinenfabrik Reinhausen GmbH 2019 3913897/02 EN TAPMOTION® MD-III 25 4 Packaging, transport and storage If the product is installed more than 6 months after delivery, suitable mea- sures must be taken without delay. The following measures can be used: ▪ Correctly regenerate the drying agent and restore the sealed packaging. ▪ Unpack the packed goods and store in suitable storage space (well venti- lated, as dust-free as possible, humidity < 50 % where possible). 4.4 Unpacking shipments and checking for transportation damages ▪ NOTICE! Transport the packaged crate to the place where installation will take place. Do not open the sealed packaging until just before installation. If this is not done, damage to the packaged goods may occur due to inef- fectively sealed packaging. ▪ WARNING! When unpacking, check the condition of the packaged goods.Secure packaged goods in an upright crate from tipping out. If this is not done, the packaged goods may be damaged and serious injuries may result. ▪ Check completeness of supplementary parts on the basis of the delivery slip. 4.5 Things to note when putting back into storage NOTICE Damage caused by storage in unheated buildings or outdoors If the on-load tap-changer and drive are to be stored in unheated buildings or outdoors: ► Fill on-load tap-changer tank with clean, dry oil and refill gas space with dry nitrogen to a maximum pressure of 0.275 bar (4 psi). ► Weather-proof outside of tank and terminal board. ► Heat drive by connecting the built-in space heater to power. 26 TAPMOTION® MD-III 3913897/02 EN Maschinenfabrik Reinhausen GmbH 2019 5 Fitting motor-drive unit 5 Fitting motor-drive unit 5.1 Preparatory work WARNING The motor-drive unit may be started by accident if the motor protective switch is not tripped! Risk of injury from starting the motor-drive unit by accident! ► Trip motor protective switch before starting to fit the drive shafts! NOTICE Damage to on-load tap-changer and motor-drive unit due to in- correct operation! The on-load tap-changer and motor-drive unit are shipped on separate pal- lets in the neutral position. Prior to assembly check the serial numbers of the on-load tap-changer and motor-drive unit to ensure they belong to- gether. If the on-load tap-changer and motor-drive unit are not connected, mechani- cal damage will result from both the drive shaft of the on-load tap-changer turning and the output shaft of the motor-drive unit turning! ü Prior to shipment the on-load tap-changer is locked in the neutral position by a cotter pin. This cotter pin is inserted through the hub and drive shaft extension on the bottom of the tank. It may only be removed just before assembly. Keep the cotter pin. ► Check the neutral position on the on-load tap-changer and motor-drive unit as described below. ► Only join shafts that have been perfectly aligned. ► If you detect deviations, contact Reinhausen Manufacturing. Maschinenfabrik Reinhausen GmbH 2019 3913897/02 EN TAPMOTION® MD-III 27 5 Fitting motor-drive unit Checking neutral position Check the on-load tap-changer's neutral position with the door open as fol- lows: 1. Both change-over selector contacts are in the top position. Figure 5: Change-over selector contacts 28 TAPMOTION® MD-III 3913897/02 EN Maschinenfabrik Reinhausen GmbH 2019 5 Fitting motor-drive unit 2. The adjustment markings on the by-pass switch are aligned to one an- other. Figure 6: Adjustment markings on the by-pass Check the motor-drive unit's neutral position as follows: 1. The tap position indicator is at neutral. 2. The pointer on the the tap-change indicator is in the mid-position of the area marked in gray. Figure 7: Indication field Maschinenfabrik Reinhausen GmbH 2019 3913897/02 EN TAPMOTION® MD-III 29 5 Fitting motor-drive unit Assembly variants When assembling the motor-drive unit, a distinction is made between 2 vari- ants: 1. Standard assembly means that the motor-drive unit is fitted directly be- neath and secured to the on-load tap-changer. 2. Offset assembly (assembly on the floor) means that there is a gap be- tween the motor-drive unit and the on-load tap-changer beneath which it is fitted and that the motor-drive unit is secured to the transformer on the main tank. This variant requires a mounting support on the main trans- former tank, which is provided by the transformer manufacturer. 5.2 Fitting motor-drive unit to on-load tap-changer With the standard assembly, the motor-drive unit is fitted directly beneath and secured to the on-load tap-changer. Figure 8: Standard assembly 30 TAPMOTION® MD-III 3913897/02 EN Maschinenfabrik Reinhausen GmbH 2019 5 Fitting motor-drive unit To do so, proceed as follows: 1. Secure the two assembly plates supplied to the brackets below the on- load tap-changer oil compartment using the relevant fastening materials. Tightening torque: 60 ft·lb (80 Nm). Figure 9: Fitting assembly plates on on-load tap-changer 2. Move motor-drive unit into position and align. 3. Insert shims between brackets on motor-drive unit housing and assembly plates in order to correctly align the drive shaft and prevent any clearance. Maschinenfabrik Reinhausen GmbH 2019 3913897/02 EN TAPMOTION® MD-III 31 5 Fitting motor-drive unit 4. Connect assembly plates with brackets on top of motor-drive unit housing. Tightening torque: 60 ft·lb (80 Nm). Figure 10: Fitting assembly plates on motor-drive unit Fitting drive shaft The drive shaft is the mechanical connection between the motor-drive unit and the on-load tap-changer. It consists of a square tube and is connected at both ends to the motor-drive unit and on-load tap-changer with 2 coupling brackets and 1 coupling bolt each. If the standard assembly is selected, the square shaft is supplied in the length required. When assembling the drive shaft, proceed as follows: 1. Ensure that the shaft ends to be connected are correctly aligned. The mo- tor-drive unit and on-load tap-changer unit must remain exactly in the as- sembly position during the entire drive shaft assembly process. 2. Prior to assembly, grease coupling bolts, coupling brackets and ball heads, e.g. with ISOFLEX TOPAS L32 or Shell 6432. 3. Loosely screw together coupling part and slide onto square tube until stop is reached. 32 TAPMOTION® MD-III 3913897/02 EN Maschinenfabrik Reinhausen GmbH 2019 5 Fitting motor-drive unit 4. Insert coupling bolt into shaft end on motor-drive unit. Slide square tube with coupling part on to coupling bolt. 5. Secure vertical drive shaft to drive. Tightening torque of screws: 7 ft·lb (9 Nm). Figure 11: Mounting drive shaft Maschinenfabrik Reinhausen GmbH 2019 3913897/02 EN TAPMOTION® MD-III 33 5 Fitting motor-drive unit 6. Secure drive shaft with coupling bolts and coupling brackets on shaft end of on-load tap-changer. Set a unilateral axial clearance of 0.12" (3 mm) between the coupling bolt and upper coupling piece. Tightening torque of screws: 7 ft·lb (9 Nm). Figure 12: Setting axial clearance 7. Connect protective covers supplied to form a protective tube. 8. Fasten protective tube with relevant hose clips to drive's bearing collar and to on-load tap-changer's adapter. After assembling the drive shaft: 1. A pre-assembled connection cable for the monitoring system is led out on the left side of the motor-drive unit housing. Plug the connector on this connection cable into the bushing on the underside of the on-load tap- changer. 2. Establish grounding connection between motor-drive unit housing and transformer tank. The square shaft, coupling lugs, pins and locking washers are made from corrosion-resistant steel. Despite this, these parts should be painted/coated together with the transformer tank after assembly. 34 TAPMOTION® MD-III 3913897/02 EN Maschinenfabrik Reinhausen GmbH 2019 5 Fitting motor-drive unit 5.3 Fitting motor-drive unit to transformer tank If the motor-drive unit is supplied in the version for offset assembly, the drive housing is fitted on the main tank of the transformer. The on-load tap- changer and motor-drive unit are connected by a longer drive shaft in this in- stance. The length of the drive shaft depends on the order specification (maximum length 98.4" (2,500 mm)). This assembly variant requires a mounting support, provided by the trans- former manufacturer, for securing to the main tank on the transformer. Pro- ceed as follows: 1. Attach mounting support to rear of drive housing. Figure 13: Rear of motor-drive unit 2. Move motor-drive unit into position and align. 3. Fasten motor-drive unit to transformer's main tank using mounting sup- port. Use shims on mounting support so that the drive shaft can be aligned correctly. Fitting drive shaft The drive shaft is the mechanical connection between the motor-drive unit and the on-load tap-changer. It consists of a square tube and is connected at both ends to the motor-drive unit and on-load tap-changer with 2 coupling brackets and 1 coupling bolt each. Maschinenfabrik Reinhausen GmbH 2019 3913897/02 EN TAPMOTION® MD-III 35 5 Fitting motor-drive unit The square shaft is supplied longer than required. During assembly it has to be cut to the desired length. Proceed as follows: 1. Ensure that the shaft ends to be connected are correctly aligned. The mo- tor-drive unit and on-load tap-changer unit must remain exactly in the as- sembly position during the entire drive shaft assembly process. ð The deviation from the vertical must not exceed 2 °. 2. Determine dimension A between tap changer and shaft end of drive. Figure 14: Shortening square tube 3. Cut square shaft to dimension A-0.35" (A-9 mm) and remove burrs. 4. Prior to assembly, grease coupling bolts, coupling brackets and ball heads, e.g. with ISOFLEX TOPAS L32 or Shell 6432. 5. Loosely screw together coupling part and slide onto square tube until stop is reached. 6. Insert coupling bolt into shaft end on motor-drive unit. Slide square tube with coupling part on to coupling bolt. 36 TAPMOTION® MD-III 3913897/02 EN Maschinenfabrik Reinhausen GmbH 2019 5 Fitting motor-drive unit 7. Secure vertical drive shaft to drive. Tightening torque of screws: 7 ft·lb (9 Nm). Figure 15: Mounting drive shaft Maschinenfabrik Reinhausen GmbH 2019 3913897/02 EN TAPMOTION® MD-III 37 5 Fitting motor-drive unit 8. Secure drive shaft with coupling bolts and coupling brackets on shaft end of on-load tap-changer. Set a unilateral axial clearance of 0.12" (3 mm) between the coupling bolt and upper coupling piece. Tightening torque of screws: 7 ft·lb (9 Nm). Figure 16: Setting axial clearance 9. Shorten protective covers supplied if necessary, deburr and connect to form a protective tube. 10. Fasten protective tube with relevant hose clips to drive's bearing collar and to on-load tap-changer's adapter. After assembling the drive shaft: 1. A pre-assembled connection cable for the monitoring system is led out on the left side of the motor-drive unit housing. Plug the connector on this connection cable into the bushing on the underside of the on-load tap- changer. 2. Take suitable protective measures to ensure that this cable cannot be damaged. 3. Establish grounding connection between motor-drive unit housing and transformer tank. The square shaft, coupling lugs, pins and locking washers are made from corrosion-resistant steel. Despite this, these parts should be painted/coated together with the transformer tank after assembly. 38 TAPMOTION® MD-III 3913897/02 EN Maschinenfabrik Reinhausen GmbH 2019 5 Fitting motor-drive unit 5.4 Installing electrics for motor-drive unit WARNING Danger of death or severe injury! An energized transformer and energized on-load tap-changer components could cause death or serious injuries when installing the electrics! ► Adherence to the following safety precautions is mandatory. The drive may only be connected to circuits with an external overcurrent pro- tection device and isolating device with all poles disconnected so the equip- ment can be fully de-energized if required (service, maintenance etc.). Suitable equipment includes isolating devices in accordance with IEC 60947-1 and IEC60947-3 (e.g. circuit breaker). When stating the circuit breaker type, note the properties of the relevant circuits (voltage, maximum currents). The following should also be noted during installation: ▪ It must be easy for the operator to access the isolating device ▪ The isolating device must be labeled for the motor-drive unit and circuits to be isolated ▪ The isolating device must not be part of the power line ▪ The isolating device must not interrupt the main grounding conductor Unless otherwise specified, the connections for the supply current circuits must have a conductor cross-section of at least 1.5 mm2 (16 AWG). NOTICE Damage to the on-load tap-changer and motor-drive unit! Damage to on-load tap-changer and motor-drive unit due to incorrect use of position transmitter equipment! ► Only circuits stated in the chapter Technical data for position transmitter equipment [►Section 15.2, Page 61] may be connected to the position transmitter module connections. ► The switchover point of the position transmitter equipment in the motor- drive unit is not the same as the switchover point of the diverter switch. This depends on the type of diverter switch. This fact should be noted when project planning the locking circuits between the motor-drive unit and external equipment (e.g. transformer circuit breaker). ► For external monitoring, locking and control purposes, it is not therefore the position transmitter equipment but the "Tap changer in operation" po- sition transit contact shown in the connection diagram that should be used. To electrically connect the motor-drive unit proceed as follows: 1. Switch off voltage supply. 2. Lock voltage supply to prevent unintentional restart. 3. Make sure everything is de-energized. 4. Visibly ground and short circuit motor-drive unit. 5. Cover or cordon off adjacent energized parts. Maschinenfabrik Reinhausen GmbH 2019 3913897/02 EN TAPMOTION® MD-III 39 5 Fitting motor-drive unit 6. Connect motor-drive unit following connection diagrams provided in the document pocket. Note the supply voltage stated in the connection dia- gram. 7. Connect main grounding conductor to grounding conductor terminal on terminal bar X1 (minimum connection cross-section 14 AWG (2.5 mm2)). 8. Once the electrical connections are complete, ensure protection against accidental contact. To do this, close swing frame and check that transmis- sion gear cover plate is fastened correctly. 9. WARNING! Never start up motor-drive unit without transmission gear cover plate. 10. Close motor-drive unit doors. 11. To connect the monitoring system, plug cable connector of motor-drive unit into the bushing on the underside of the on-load tap-changer oil compartment. 40 TAPMOTION® MD-III 3913897/02 EN Maschinenfabrik Reinhausen GmbH 2019 6 Checks after assembly 6 Checks after assembly Please contact Reinhausen Manufacturing if any aspect of the tests is not clear. 6.1 Preparations WARNING Danger of death and damage to property! Danger of death and damage to property due to electrical voltage! ► The relevant safety instructions must be observed. ► Ensure that the motor-drive unit and on-load tap-changer are correctly coupled in accordance with instructions in the Fitting motor-drive unit [►Section 5, Page 27] chapter. ► Ensure that the motor-drive unit is connected in accordance with the con- nection diagrams provided. ► Provide protection against accidental contact before energizing the drive. The transmission gear cover plate must be fitted and the swing frame closed. Perform the checks described above before filling the on-load tap-changer with oil. 6.2 Electrical test operations NOTICE Damage to motor-drive unit! Too many tap-change operations in succession will damage the motor! ► Perform no more than 120 tap-change operations in succession to avoid damaging the motor. NOTICE Damage to the on-load tap-changer! Performing too many operations without complete oil filling will damage the on-load tap-changer! ► Do not perform more than 120 tap-change operations on the on-load tap- changer without oil before drying. With electric on-load tap-changer actuation, the pointer on the tap-change indicator remains in the gray area. Maschinenfabrik Reinhausen GmbH 2019 3913897/02 EN TAPMOTION® MD-III 41 6 Checks after assembly To perform tap-change operation tests and check the limit position locks, proceed as follows: 1. Switch on motor protective switch 8-2. ð The green Power LED on the monitoring circuit board lights up. 2. Ensure that the hand crank is in the storage bracket. 3. On the monitoring system, press and hold the red RESET push-button for approx. 5 seconds (three yellow LEDs flash slowly) to activate mainte- nance mode and deactivate the verification system for 10 hours. ð At the end of the 10 hours, the LEDs go out and the unit automatically returns to normal function. Instead of waiting for the specified time to expire, you can also press the green TEST push-button to exit mainte- nance mode prematurely. 4. Switch the on-load tap-changer one step in the LOWER direction (16L) using the RAISE/LOWER rotary switch. Check movement of tap position indicator. ð The drive starts up and remains in the gray area of the tap-change indi- cator. 5. Switch further in the same direction and stop in the lowest position (dis- play showing 16L). 6. Place one hand on the motor protective switch and again move the RAISE/LOWER rotary button in the LOWER direction. ð The drive must not start up. If it does, switch off the motor protective switch straight away because either the limit switch timing or the con- nections aren't right. 7. CAUTION! Do not turn hand crank with force. Switch off motor protec- tive switch, insert hand crank and move on-load tap-changer in the LOWER direction. ð Mechanical blocking should occur after around 2.5 hand crank revolu- tions. This can be clearly felt on the hand crank. 8. Fit hand crank in bracket. Switch on motor protective switch and move on- load tap-changer back into adjustment position (display shows N) by mov- ing the RAISE/LOWER rotary switch. To check the second limit position lock, proceed as follows: 1. Move on-load tap-changer another step in the RAISE direction (16R) and repeat the verification process described above for the other switching di- rection ð The drive starts up and remains in the gray area of the tap-change indi- cator after every switching operation. ð If the guide lever on the hand crank is raised, the on-load tap-changer must not start up. ð Once the limit position is reached (display shows 16R), the drive must not start up when the RAISE/LOWER rotary switch is moved. ð When the hand crank is moved in the limit position, mechanical block- ing occurs after around 2.5 revolutions. 42 TAPMOTION® MD-III 3913897/02 EN Maschinenfabrik Reinhausen GmbH 2019 6 Checks after assembly 2. Return the on-load tap-changer to its adjustment position (display shows N). 3. Fit hand crank in bracket and close drive housing. 4. Exit maintenance mode by pressing the green TEST push-button on the monitoring system. 6.3 Testing monitoring system Figure 17: Monitoring system displays and control elements 1 Green TEST push-button 3 1 yellow and 1 red LED each for indicating errors 2 Green Power LED 4 Red RESET push-button Tripping test For the tripping test, open the on-load tap-changer oil compartment and mo- tor-drive unit doors. Three insulating material plates are arranged vertically next to one another in the front of the on-load tap-changer oil compartment. The vacuum interrupters are each mounted on the front of the insulating ma- terial plates. 1. Switch off motor protective switch 8-2 in the motor-drive unit Maschinenfabrik Reinhausen GmbH 2019 3913897/02 EN TAPMOTION® MD-III 43 6 Checks after assembly 2. Connect external source of power to busbar connection P2 and fixed con- tact A of one of the vacuum interrupter assemblies, e.g. left phase ð The power source must be able to produce a current of at least 20 A Figure 18: Vacuum interrupter assembly 3. Switch on motor protective switch 8-2 4. On the monitoring system, press and hold the red RESET push-button for approx. 5 seconds (three yellow LEDs flash slowly) to activate mainte- nance mode and deactivate the testing system for 10 hours ð At the end of the 10 hours, the LEDs go out and the unit automatically returns to normal function. ð Instead of waiting for the specified time to expire, you can also press the green TEST push-button to exit maintenance mode prematurely 5. Switch on input voltage at power source and slowly increase until a pri- mary current of around 20 A flows through the current transformer. 6. Start motor-drive unit by moving RAISE/LOWER pivot switch in one direc- tion ð A red LED on the monitoring system and the Alarm signal lamp (86RL) on the swing frame light up ð The drive stops and goes back to its starting position 7. Check the blocking: ð The drive cannot now be moved in either direction 8. Reset monitoring system by pressing the RESET push-button ð All red alarm displays go out. 9. Perform same test procedure with the vacuum interrupter assemblies of the center and right phases. 10. Reset monitoring system by pressing RESET push-button. 11. Close motor-drive unit and on-load tap-changer oil compartment doors. 44 TAPMOTION® MD-III 3913897/02 EN Maschinenfabrik Reinhausen GmbH 2019 6 Checks after assembly Tighten nuts on access door to on-load tap-changer to a maximum tighten- ing torque of 11 ft·lb (15 Nm). Maschinenfabrik Reinhausen GmbH 2019 3913897/02 EN TAPMOTION® MD-III 45 7 Drying procedure 7 Drying procedure NOTICE Damage to drive and on-load tap-changer! If the drive is dried in an autoclave, the drive and on-load tap-changer may be damaged. ► Do not dry drive in an autoclave. ► Remove the drive if the transformer is dried in an autoclave. ► If the transformer is dried in its own tank, the drive can remain in place. Also observe the information about drying provided in the on-load tap- changer's operating instructions. 46 TAPMOTION® MD-III 3913897/02 EN Maschinenfabrik Reinhausen GmbH 2019 8 Commissioning at the transformer manufacturer's site 8 Commissioning at the transformer manufacturer's site WARNING Danger of death or severe injury! Danger of death or severe injury from explosive gases in the on-load tap- changer, in the pipework system, at the dehydrating breather opening and from flying parts and hot oil splashing! ► Make sure that only trained technicians perform work on the transformer. ► Use suitable personal protective equipment/clothing. ► Ensure that there are no naked flames, hot surfaces or sparks (for exam- ple caused by static charging) in the immediate surroundings and that none occur. ► Only use conductive and grounded hoses, pipes, and pump equipment that are approved for flammable liquids. ► Ensure that the oil compartment of the on-load tap-changer is correctly filled with oil as per the instructions. ► Ensure that all the on-load tap-changer's safety equipment is ready for use. ► Keep away from the danger area during the transformer test. ► Observe applicable fire protection regulations. WARNING Danger of death and damage to property! Danger of death and damage to property due to incorrect operation during commissioning! ► Only start up transformer if the functions described in the Checks after assembly chapter are satisfied. ► Only actuate on-load tap-changer with the hand crank if the transformer is de-energized and the motor protective switch switched off. ð Otherwise damage to the transformer and/or personal injury may result if any of the vacuum interrupters fails to interrupt. ► During operation, if the monitoring system trips, do not reset until the on- load tap-changer has been inspected and the cause of the problem cor- rected. ► Contact Reinhausen Manufacturing for assistance if needed. Maschinenfabrik Reinhausen GmbH 2019 3913897/02 EN TAPMOTION® MD-III 47 8 Commissioning at the transformer manufacturer's site 8.1 High-voltage tests on the transformer WARNING Danger of death or severe injury! Danger of death or severe injury from explosive gases in the on-load tap- changer, in the pipework system, at the dehydrating breather opening and from flying parts and hot oil splashing! ► Make sure that only trained technicians perform work on the transformer.