On-Load Tap Changer Type R and RM Inspection Instructions (PDF)
Document Details
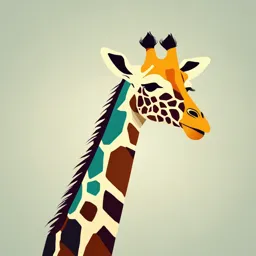
Uploaded by BestSellingBeige
null
2000
Tags
Related
- OILTAP® M On-load Tap-Changer Installation & Commissioning Instructions PDF
- On-load tap-changer Installation and Commissioning Instructions PDF
- VACUTAP® VM 300 On-load tap-changer Operating Instructions PDF
- OILTAP® R On-load Tap-Changer Installation and Commissioning Instructions PDF
- VACUTAP® VV® On-load tap-changer Operating Instructions PDF
- On-load tap-changer VACUTAP® VV Maintenance Manual WA 241/05 PDF
Summary
This document provides inspection instructions for on-load tap changers type R and RM. It details procedures for cleaning, checking contact wear, and reinstallation. The document is intended for professional use in industrial settings.
Full Transcript
On-Load Tap Changers Type R and RM Inspection Instructions M = — GERMANY MASCHINENFABRIK...
On-Load Tap Changers Type R and RM Inspection Instructions M = — GERMANY MASCHINENFABRIK MR REINHAUSEN C1 I | IA 126/01 e n — 0896/2000 Maschinenfabrik Reinhausen GmbH Printed in Germany Postfach 12 03 60 D-93025 Regensburg Phone: +49-941-4090-0 Fax: +49-941-4090-111 Telex: 6 5 8 8 1 ON-LOAD TAP CHANGERS TYPE R and RM Inspection Instructions No. 126/01 Contents Page 1. [ T =a T= =| UT 3 1.1 Function principle of the on-load tap changer 1.2 Tap changer designation 1.3 Components of the on-load tap changer 14 Inspection intervals 15 Summary of inspection work 2. Preparations...........ooececierercrrnrrrrressnrrer rss cresser ee ressnesessssssenenanes 7 2.1 Required tools a n d equipment 2.2 Safety precautions 2.3 Operating position 3. Removal of the diverter switch unit...........cccoiviiiiiiiiiiiiinnrinnrrerreeeenns 9 4, Cleaning of the oil compartment, the oil conservator for the tap changer a n d the diverter switch unit.............cccooovevieeninicn ene 10 5. Inspection of the diverter switch unit...........ccovvveere nici 11 5.1 Withdrawal position 5.2 Measurement of the transition resistors 5.3 Contact wear at main switching and transition contacts. 5.4 Measurement of contact wear at main switching and transition contacts Please note: 5.5 Removal and cleaning of the supporting cylinder and the insulating shaft... 5.6 Removal of the contact shells Drawings and Hustrations c o n - 5.7 Cleaning of the diverter switch unit tained herein may differ i n detail 58 Attachment of the contact shells from the tap changer equipment 5.9 Attachment of the supporting cylinder delivered. 5.10 Check of the protective resistors They are for reference only and are subject to change without 6. Reinstallation of the diverter switch unit 17 notice. 7. Filling With Oil.......ooiiiiiere errr reece reese 17 126/01/01/0 1 Contents Page 8. FURNEE CREEKS «cei einer rece venta eteerste sie esseeran sereaeeaes 1 8 8.1 Drive shaft 8.2 Functional checks of motor drive and tap changer 8.3 Protective relay RS 2001 8.4 Voitage regulator ADPPENIX evita reenter barter ennaniea 19 9.1 Assessment of the contact wear 9.2 Replacement of the diverter switch contacts 9.3 Measurement of the protective resistors 9.4 Coupling of the tap changer and the motor drive unit 9.5 Inspection tools 9.6 Lifting device 9.7 Parts of the diverter switch unit 9.8 Spare parts list 9.9 Adjustment plans 126/01/01/0 1. GENERAL Then, the diverter switch transfers the current from the tap in service to the 1.1 Function principle of the preselected tap. on-load tap changer (fig. 1) During this quick change-over, ohmic A tap-change operation is initiated by resistors are temporarily inserted into the tap selector which preselects the the circuit to ensure no-break transfer desired tap o n the transformer of the current. winding. Motor drive unit T a p selector Diverter switch Time i n seconds Circuit diagram AB — main contacts EE —— a h obs - main switching o Varia S e z fr Jub R1IR2 R2R1 ! _RIR2 R2R1 i iTti A aala2z|b2bl b B MI N | A aala2|b2bl I b B In A BERR. aala2ib2bl bB Contact movement Fig. 1 Tap-change operational sequence KHW 216/1 126/01/01/0 1.2 Tap changer designation (fig- 2) Every tap changer is available in different models. These models vary On-load tap changer according to their number of poles, max. rated through-current, insulation to ground, tap selector size and basic circuit diagram. The designation of a R Hi 1 2 0 0 Y - 1 2 3 / C - 1 0 1 9 1 W ka specific tap changer model therefore Type | Basic circuit diagram incorporates all these characteristics Number of and permits easy and distinctive poles Tap selector size identification of the tap changer. Max. rated through- The basic circuit diagram code in current in amperes ~~ — and additional identification the model designation identifies: of model number of tap selector contacts, Star connection number of operating positions, number of mid-positions, and type Highest voltage for equipment Uyy, of change-over selector. Insulation to ground Example in fig. 2: On-load tap changer type R Three-pole design, 1200 A current, star-connection, insulation to ground Basic circuit diagram according to highest voltage for equip- 10 1 wr ment Up, =123 kV, tap selector size C, basic circuit diagram 10 19 1W, i.e. 10 contacts, 19 operating positions with one mid-position, change-over Pitch of / tap selector Max. number of service positions NN Mid-positions | Change-over selector selector designed a s reversing switch. contact circle Change-over LN Coarse tap selector Reversing switch 1.3 Components of the on-load selector tap changer (fig. 3) without with G Ww | 7 N\ 10 10 09 19 *)} No designation without The main components of the on-load 12 12 11 23 change-over selector tap changer are: 14 14 13 27 16 16 15 31 — tap changer head 18 18 17 35 — diverter switch unit diverter switch oil compartment tap selector All tap changer parts subject to Fig. 2 inspection are clearly marked in grey Designation of tap changer model and basic circuit diagram in fig. 3. 126/01/01/0 Fig. 3 21 Components of the on-load tap changer 15 13 Tap changer head gasket 24 14 Position indicator 15 Inspection glass 25a 16 Drive shaft for position indicator 21 Tap changer head 22 Cover bolt 23 Cover gasket 24 T a p changer cover 25 Upper gear unit with drive shaft 25a 26 Pipe connection R for protective relay 27 Pipe connection S for suction pipe 28 Pipe connection Q for oil return pipe (with oil filter unit only) 29a Bleeder valve on the tap changer cover 54 29b Bleeder facility for transformer oil tank 53 29c Bleeder screw for suction pipe 31 Diverter switch oil compartment (inside) 32 Oil compartment bottom 33 Screening ring 34 Oil compartment terminal 35 Tap changer take-off terminal 36 Suction pipe 51 41 Tap selector suspension facility 42 Tap selector gearing 43 Fine tap selector 56 44 Change-over selector 29¢c 45 Fine tap selector terminal 27 46 Change-over selector terminal 51 Diverter switch insert 13 52 Supporting cylinder 21 53 Supporting plate 33 54 Fixing screw 31 55 Lifting lug 56 Transition resistor 36 34 41 42 43 45 | i A | I | I (I I PE | KHW 711-3 126/01/01/0 1.4 Inspection intervals IMPORTANT: The tap changing MN WARNING: equipment must b e inspected at Disregard of the inspection regular intervals t o maintain a high intervals puts at a risk the level of operating reliability. trouble-free operation of tap The inspection can be carried out by changer and transformer. qualified and MR-trained personnel usually within one day, provided it has been well prepared a n d organized. W e strongly recommend to have in- spections carried out by our Technical Standard values for oil testing according to CIGRE report 12-13 (1982) apply to Service. This ensures a professional transformer oil at service temperature: performance of the inspection and the Water content*) Dielectric strength**) updating of specific components to the latest operational state. Neutral-point tap changers < 40 ppm > 30 kVv/2.5 mm When preparing an inspection that will Single-phase tap changers < 30 ppm > 40 kV/2.5 mm not be carried out by MR personnel, we recommend to enquire for the *} measured according to Karl-Fischer method based on IEC Publication 814 necessary spare parts (please indicate **) measured according to DIN VDE 0370 Teil 1 the tap changer serial number and the number of tap change operations performed). On-load Transformer Number of tap change operations The numbers of tap change operations tap changer rated current without MR oil filter with MR oil filter determining the inspection intervals indicated i n table | are figures based RM ill 600 Y upto B00A 80,000 100,000 on experience with usual oil qualities. R11 1200 Y u p t o 600A 80,000 100,000 T h e tap selector of the on-load tap u p t o 1200 A 60,000 100,000 changer is basically maintenance-free. In particular cases, however, e.g. if RM | 601 upto 600A 80,000 100,000 installed in industrial transformers with RM 1 1201 upto 600A 80,000 100,000 a high number of switching opera- up to 1200 A 60,000 100,000 tions, our Technical Service should be RM 1 1502 upto 1000 A 60,000 100,000 contacted when about 1,000,000 up to 1500 A 50,000 100,000 switching operations have been reached. The diverter switch unit must R 11201 u p t o 600A 80,000 100,000 be replaced after 800,000 switching u p t o 1200 A 60,000 100,000 operations at the latest. R 12002 up to 2000 A 40,000 80,000 if the number of tap change opera- R 12402 u p to 2400 A 40,000 80,000 tions per year exceeds 15,000 we recommend the use of our stationary R 1 3000 up to 3000 A 40,000 80,000 oil filter unit type 51 with a paper filter R 1 3600 up to 3600 A 40,000 80,000 (see Operating Instructions No. 18). The use of an oil filter unit type 51 with Table! Inspection intervals a combined filter cartridge is obliga- tory for all tap changers type R and R M with Uy, > 245 k V of the tap changer. Regardless of the number of tap change operations listed i n table | , a n inspec- tion must b e carried out after 6 t o 7 years. Filtering of the switching oil allows t h e inspection intervals to b e extended. In case of U m = 245 kV of the tap changer (auto-transformer or regulation at the line end of the transformer winding), the following inspection intervals apply. The insulating oils in the transformer are to b e monitored b y the operator First inspection: after 20,000 tap change operations or after 2 years of service, according to the relevant regulations. whichever comes first. If inspections are not carried out by Further inspections: Either after half the numbers of tap change operations MR personnel, we request a report indicated in table 1 or after 4 years of service without MR oil filter or 6 years of to supplement our inspection data. service with M R oil filter (with combined filter cartridge), whichever comes first. 6 126/01/01/0 1.5 Summary of inspection work 2. PREPARATION The inspection includes the following JAN WARNING: 2.1 Required tools and equipment: work: The inspection must be carried empty vessels for the dirty oil and — Removal and reinstallation of the out b y qualified, skilled person- new transformer oil for cleaning diverter switch unit nel only. All instructions stated and oil change (for oil filling quan- — Cleaning of the diverter switch oil i n the Inspection Instructions tity see table Il) compartment and diverter switch manual must be strictly an oil pump for changing the oil unit. In the course of a tap changer observed. If any damage i s inspection it is also necessary to detected during inspection, a drip p a n clean the oil conservator for the tap immediately contact MR for brushes and absorbent, non- changer. assistance. I n this case the tap fuzzing rags changer must not be put into — Changing of the switching oil a work table service. Do not alter or modify — Check of the diverter switch oil the tap changer equipment a lifting device: compartment and the diverter without prior consultation with either a crane or an MR lifting switch unit MR. improperly performed o r device (see appendix, section 9.6), — Determining of the contact wear incomplete inspection work can weight of diverter switch unit max. affect the trouble-free operation 120 kg, required lifting force is — Measuring of the transition o f t a p changer a n d transformer. max. 2200 N (for lifting height refer resistors Under certain circumstances to table l l ) — Measuring of the protective this can cause damage t o life. resistors inspection tools (see section 9.5) Always use genuine MR spare - Check of the protective relay, the parts for replacement. Parts of spare parts (see section 9.8) drive shaft, the motor drive unit and, other origin can affect the Please note: Lock tabs, self-locking if existing, the oil filter unit and the trouble-free operation of tap nuts a n d screws should never b e voltage regulator. changer and transformer. used twice; after removal they have to The diverter switch unit should be ex- be replaced by new ones. posed to air no longer than 10 hours For the evaluation of the contact at the most. wear M R should b e asked for the The inspection work should not be values of the contact distance K interrupted. Care and cleanliness (see page 21) prior to the begin- should be observed. ning of the inspection. If the values for the contact distance K are not known at the beginning of the in- spection, then the value K = 3 4 m m should be used. I n this case the measured values X (see page 12, fig. 17) as well as the tap changer serial number and the number of tap change operations should b e advised to M R for examination. Highest voltage for equipment U,,, at the tap changer 72.5 kV 123 kV 170 kV 245 kV Oil filling quantity in litres (approx.) 160 180 195 210 Length of the diverter switch insert in m m 1147 1277 1377 1477 Lifting height in mm (incl. lifting device) 1350 1480 1580 1680 Table I l Oil filling quantity and lifting height 126/01/01/0 2.2 Safety precautions /\ ATTENTION: Make sure that the following safety precautions have been carried out b y the user of the p l a n t : T h e transformer must b e disconnected and secured against reclosing. All terminals must be grounded visibly (ground cables, ground switches). The working area must b e clearly marked out. Start with the inspection only after a l l these safety measures have been carried out. Disregard endangers lives. 2.3 Operating position 10 The diverter switch unit can be with- drawn in any operating position. Take note of the operating position when removing the unit. It is recommended, however, to with- draw the diverter switch unit in the adjustment position which is marked KHW 905-4 by an arrow on the position indicating dial of the motor drive (fig. 4). Fig. Tap changer head (view from top) Drive shaft (square tube) 7 Pipe connection S with = Coupling bracket with bolt bleeder screw for suction pipe WON Upper gear unit 8 Bleeder screw for suction pipe Tap changer cover 9 Pipe connection Q for oil return pipe OA Bleeder valve of the tap changer 10 Inspection glass for position Pipe connection R for indicator 500000 protective relay RS 2001 11 Protective relay RS 2001 JAN CAUTION: D o n o t operate t h e motor drive while the tap changer i s un- coupled. To prevent electrical operation the motor drive must be blocked b y tripping the motor protective switch. 126/01/01/0 3. REMOVAL OF THE DIVERTER SWITCH UNIT Lowering the oil level: Close the stop valve between oil conservator and tap changer head. Lower the oil level in the tap changer head by opening the drain valve of the tap changer head a n d the bleeder valve o n the tap changer cover, see f i g. 5 (remove screw c a p M30/ wrench size 36, lift the valve tappet with the help of a screwdriver). Proceed with disassembling i n the following order: MN CAUTION: Remove the position indicator dial The switching oil of the tap (fig. 7). Take off the clip from the shaft changer should always be end. T h e coupling pin allows reinstal- handled as a flammable liquid. lation of the position indicator dial in Moreover, explosive gases can its correct position only. accumulate under t h e t a p Take note o f t h e m a r k s o n t h e t a p changer cover, i n the switching changer head and the support o i l o r i n t h e o i l compartment. plate. They have t o match i n the Therefore, strictly avoid o p e n fire. adjustment position (fig. 7). Use only pumping equipment suitable for flammable liquids. Loosen the fixing screws of the support plate: Standard design: 4 screws M8 x 20 If an oil filter unit is installed: (w.s.13), fig. 8. Open the sample valve of the return Special design for installation into a pipe a n d take the oil filter unit into bell-type tank: 5 studs M 8 with nuts operation. Drain approx. 1 0 litres from (w.s.13), fig. 9. the oil in the tap changer head until In both cases take care not t o lose the the support plate of the diverter switch spring washers. unit is free of oil (check through the inspection glass in the tap changer cover). Uncoupling t h e d r i v e shaft at t h e JANATTENTION: D o not loosen the stud nuts u p p e r gear unit: located i n t h e red-marked area Loosen 6 screws M6/w.s.10 at the of the tap changer head. coupling bracket. Take care not t o Otherwise the tap changer could lose coupling bolts, nuts a n d lock fall into the transformer tank and tabs. Normally the drive shaft can be cause serious damage t o parts of moved to one side for clearance. t h e t a p c h a n g e r a n d transformer. If not, remove the other coupling on the bevel gear from the square tube (screws, nuts a n d lock tabs a s above) Now, carefully lift out the diverter until the horizontal drive shaft c a n b e switch unit using the lifting lugs removed. (fig. 10). Place it on a flat and clean Removal o f t h e t a p c h a n g e r c o v e r surface. (fig. 5, fig. 6): Unscrew the cover screws M10/ w.s. 17, take note of the spring washers. Lift off the cover and make sure not to damage the gasket ring in the tap changer cover. 126/01/01/0 4. CLEANING THE OIL COM- PARTMENT, THE TAP CHANGER OIL CONSERVA- TOR AND THE DIVERTER SWITCH UNIT Oil compartment, oil conservator: Pump out the oil from the diverter switch oil compartment. Open t h e stop valve between tap changer head and tap changer oil conservator and drain the oil until only ciean oil flows. If necessary, flush the oil conservator with new transformer oil. Drain the diverter switch oil compart- ment completely. Flush it thoroughly with transformer oil and drain again until it is absolutely empty (fig. 11). Remove the suction pipe (fig. 12) and thoroughly flush it with transformer oil inside and outside. Then reinstall the suction pipe. Make sure that no parts fall into the oil compartment until installation of the diverter switch unit, by closing the tap changer head with the cover using all cover screws M10/ w.s. 17. Fig. 11 Tap changer head open, inside view of the diverter switch oil compartment 1 — Suction pipe 5 — Kerosene drain screw 2 — Drive shaft for position indicator 6 - Main switching contact 3 — Position indicator gear (stationary) 4 - Coupling for tap selector drive Diverter switch unit (fig. 13): Visually check the outside of the diverter switch unit. Perform a prepa- AN ATTENTION: ratory cleaning of the diverter switch Use only new transformer oil by flushing it with new transformer oil. when cleaning the diverter switch Thorough cleaning of the diverter o i l compartment. Other liquids switch unit will be carried out after (e.g. organic solvents, cleaning removal of the contact shells petrol) are not suitable. The use (section 5.3). of other cleaning agents may put at risk the trouble-free operation of tap changer and transformer. 10 126/01/01/0 5. INSPECTION OF THE DIVERTER SWITCH UNIT 5.1 Withdrawal position Before starting the inspection, take note of the switched position (= with- drawal position) of the diverter switch. Note the position of the trip lever of the spring energy accumulator (fig. 14) so that this position is regained after reassembly of the diverter switch unit. 5.2 Measurement of the transition resistors (fig. 15) Measure the value of each transition resistor. The values are between 0.3 a n d 3 0 ohms. Measure at the open side of the diver- ter switch sector. For this purpose set the diverter switch to the opposite position using the operating key (see section 9.5). Perform measurement a s described above (fig. 16a, 16b). Compare the measured values with the values given on the rating plate. A + 10 percent deviation is permis- Fig. 1 3 sible. Diverter switch unit 1 — Supporting plate 2 — Supporting cylinder 3 — Spring energy accumulator R1 R2 R2 R i a — Pawl WW b — Trip lever al a2|b2 b1 b B Diverter switch | ODO — Transition resistor — Protective resistor R1 R2 R2 R1 KHW 699-41 { " R1 R2 R2 R i KHW 6399-4b 126/01/01/0 5.3 Contact wear at the main switching and transition contacts The admissible wear of the diverter switch contacts is determined by two criteria: a) by the contact volume (see fig. 17). The max. admissible contactwear o n the individual contact i s ¢ = 6 mm. This results in a maxi- mum admissible total wear of 2 ¢ =12 mm at one pair of contacts or i n a minimum thickness of 22 mm (= dimension X), respectively. The contacts need to b e replaced if this value has been reached or i s expected to be reached before the next inspection. b) by the kinematically correct tap change operations sequence (see section 1.1) of main contact (A, B), main switching contact (a, b) and transition contacts ( a i , b1, a2, b2). The correct switching sequence of [" Measurement of ’ contact wear the diverter switch can only b e en- KHW 701-3 sured if the differences in contact wear between main switching and transition contacts do not exceed certain limits. /N\ ATTENTION: Make sure that the permissible Unfavourable operating conditions difference i n contact thickness may cause increased contact wear i s never exceeded. Continued at the transition contacts. operation of the diverter switch The max. permissible difference in unit with greatly differing contact contact wear related to the total wear layer t h i c k n e s s c a n l e a d t o se- (= 2c): vere damage of tap changer and transformer. Between main switching contact (a, b) and transition contact 1 (a1, b1) and between main switching contact (a, b) a n d transition contact 2 (a2, b2) —3 mm < ( 2 c a- 2cal) — 1 m m , unit before disassembling the sectorial (2cb1 -2¢cb2) > ~ 1 mm. contact shells. For this purpose each contact shell has a through-hole at If this difference has been reached or half height which allows to measure a i s expected to b e reached before the reference value X between the out- next inspection, the contacts must be side of the contact shell and the con- replaced or matched t o the other tact bridge (see f i g. 17). T h e contacts contact b y interchanging o r b y milling. have to b e closed when measuring. 12 126/01/01/0 The total wear (= 2¢) of a pair of If necessary, replacement of the contacts can be calculated as follows: diverter switch contacts has to b e 2c = K - X, where K = contact carried out a s described in section distance of the pair of contacts at the 9.2. time of delivery. Normally the contact wear (c) at the If the values for the contact distance K upper and lower contact tips as well are not known at the beginning of the as at the stationary and movable con- inspection, then the value K = 34 mm tact tips of a pair of contacts should be should be used which results in equal. Make sure by checking the 2c = 34 - X. In this case the measured thickness of all pairs of contacts. values X (see page 12, fig. 17) as well as the tap changer serial number and Proceed a s follows: the number of tap change operations a) Measure the value S (see fig. 17) should be advised to MR for examina- between contact bridge and bear- tion. ing support counterpiece of each When determining the contact wear contact while the contact is closed. proceed as follows (see appendix, The value of S should be 3 £1 mm. section 9.1): b) After disassembly of the sectorial —Note the actual diverter switch contact shells (section 5.6) visually position, e.g. right side switched on check all contact tips. If any contact (fig. 18). tip of a pair of contacts (stationary and movable contact) shows greatly —Determine the value X on b (see differing wear (difference > 2 mm), fig. 19) and on b1 (see fig. 20) in all it is permissible to replace single sectors of the diverter switch insert contact tips. I n this case the contact and enter the values into table l l l of layer thickness must be matched the section 9.1 (appendix). according to the criteria explained — Set the diverter switch to the other in section 5.3. position, e.g. to the left, using the operating key. 5.5 Removal and cleaning of the — Determine the value X on a and a1 support cylinder and the i n all diverter switch sectors and insulating shaft enter the values into table lil. Removal of the support cylinder —To measure the transition contacts 2 Undo the 8 screws M8 x 20/w.s.13 (a2, b2) the diverter switch has to be each with 1 lock nut and 2 washers at set to its mid-position. T o d o this, the 4 lugs of the spring energy accu- unlock the spring energy accumula- mulator housing (fig. 24). tor and turn the drive shaft with the operating key (fig. 22) until wind-up and cocking sledge have reached a stable position just about in the middle (fig. 23). i n the diverter switch mid-position JAN ATTENTION: the transition contacts a2 and b2 of Strictly avoid dropping any each diverter switch sector are parts into the diverter switch closed. unit. Otherwise there i s the risk —Determine the value X on a2 and b2 t h a t t h e diverter s w i t c h b l o c k s in all sectors (see fig. 21) and enter a n d t h e t a p changer a n d trans- the values into table I l l of section former are damaged. 9.1. Therefore, make sure that the number o f small parts i s com- — Evaluate the measured values in plete when disassembling and table Hl according to the criteria reinstalling. stated i n section 5.3. Count them t o b e sure. Replacement and matching of con- tacts i s necessary when t h e limit values specified i n section 5. 3 have Take off the support cylinder (fig. 25). been reached. 126/01/01/0 13 Removal of the insulating shaft Take off the insulating shaft from the splined shaft of the eccentric (fig. 26). Cleaning Clean the support cylinder inside a n d outside with a brush and new trans- former oil. Clean the insulating shaft in the same way. Finally, flush all parts with transformer oil and wipe them dry. 5.6 Removal of the contact shells To remove the contact shells set the diverter switch to the intermediate position i n which the two transition contacts 2 (a2, b2) of each diverter switch sector are closed. Unlock the spring energy accumulator and turn the drive shaft by using the operating key until winding-up and cocking sledge have reached a stable position in the middie (see fig. 27 and section 5.4). The contact shells are marked with L1, L2, L3. The same designations are found o n top of the guide plate. When reinstalling the contact shells make sure to mount them at their original location. Loosen the connections at the transition resistors (the leads remain at the contact shells): 6 screws M5/w.s. 8, 1 lock nut M6/ w.s. 10 (fig. 28, 29). Unlock and loosen the fixing screws of the contact shell: Firstly, the 4 outer screws M6 x 16/ w.s. 4 (fig. 30), then the 2 inner screws M6 x 16/w.s. 4. Take off the lock washers. When taking off the contact shell (fig. 31) take note of the arrangement of the arc chutes for later reinstalla- tion (fig. 32). Remove the arc chutes ( f i g. 33). 14 126/01/01/0 5.7 Cleaning of the diverter switch Fix the resistor leads (6 lock screws M5/w.s. 8, max. torque 5 Nm, 1 lock Clean the contact shells, the movable nut M6/w.s.10, max. torque 9 Nm). contact system, the arc chutes, the transition resistors a n d the protective When all contact shells have been resistors of the diverter switch mounted (fig. 36), reset the spring thoroughly with transformer oil. energy accumulator in a definite Take special care when cleaning the diverter switch position. Lock the insulating parts. spring energy accumulator by placing the insulating shaft onto the eccentric; Flush all parts carefully with trans- then turn by using the operating key former oil. until the pawl locks in (fig. 37). After cleaning it is necessary that the surfaces of the insulating materials Please note: which are subjected to voltage stress, When placing the insulating shaft viz: o n t h e eccentric make s u r e that the — oil compartment inside, marks of both match properly. — indicator drive shaft, — suction pipe inside and outside, — support cylinder inside and outside, 5.9 Mounting of the support — diverter switch insulating shaft, cylinder — contact shells inside and outside, Position the support cylinder on the are carefully checked for mechanical spring energy accumulator housing. or electrical damages (traces of Make sure that the triangle marks of discharges). the supporting plate (top) and the If any insulating parts are damaged spring energy accumulator housing they must be replaced. coincide (fig. 38, 39). Continued operation with damaged insulating material can lead to Fix by 8 screws M8 x 20/w.s. 13 with flashovers which can cause damage 2 washers each and one lock nut, to the tap changer and transformer. max torque 22 Nm. 5.8 Reinstallation of the contact shells Install every contact shell at its original location. T o facilitate fastening of the shells, press back the transition contacts 2 and insert tensioning bolts (e.g. 2 bolts M5 x 70) into the two holes of the top guide plate (fig. 34). B y this measure the spring pressure of the movable contact system to the outside i s counterbalanced. Reinstall the arc chutes. They are of different shape. Therefore, m a k e sure to position them correctly (outer arc chute, inner arc chute, long/short/long). Use a piece of string to fix the arc chutes provisionally (fig. 35). Fix the contact shell with the two central screws. Check correct position of the arc chutes in the grooves in the contact shell. Remove the string. Then screw-in all other screws and lock them: 6 screws M 6 x 16/w.s. 4 with lock washers, max. torque 9 Nm. Withdraw the tension bolts. 126/01/01/0 Check the mechanical function by operating the diverter switch several times between the two positions. Check that the pawls are correctly engaging. Repeat measurement of t h e transition resistors as described in section 5.2. Set t h e diverter switch t o its removal position (see section 5.1). The diverter switch is in its adjustment position when the triangle marks of insulating shaft and support piate coincide (fig. 40). Since d.c. voltages of at least 7... 10 kV are required, the diverter switch unit 5.10 Check of the protective must b e put o n a n insulated base. resistors The feet of the diverter switch unit are made of insulating material. Each diverter switch sector is Current and voltage measurements on provided with one protective resistor the varistor elements should be carried (fig. 41). out with an accuracy of less than 1.5 % The protective circuit of the diverter error (for possible measuring equip- switch (connection as per fig. 42) ment see appendix, section 9.3). serves to limit transient overvoltages Enter the measured voltage values into between the diverter switch contacts table V of the appendix, section 9.3. (= between selected and preselected The measurements are to be carried taps). out within a temperature range from The protective resistor consists of +15°C to +26 °C (temperature non-linear resistors (varistor elements) measured on the varistor element). connected in series and additional Otherwise the voltage values have to linear ceramic resistors. be adjusted by using the corrective factors according to table V, section 9. Checking includes: Compare the measured voltages in kV a) A visual inspection with the original values shown o n the Check the general condition of the varistor elements. Differences of + 6 % assembly, of the resistor elements are permissible. In the event of larger and of the electrical connections. differences contact Maschinenfabrik b) Measurement of the linear resistors Reinhausen since replacement of the protective resistors might become with an ohmmeter (see fig. 43). necessary. If no original values are The value of a single linear resistor indicated on the varistor elements, use element i s either 8 ohms + 2 0 % o r the values measured during the initial 1 0 ohms = 2 0 %. Enter the total inspection as reference values. resistance value into t a b l e V of the appendix, section 9.3. T o enable u s to keep our records for statistical evaluation u p to date please c) Measurement of the varistor ele- send all measured values directly to: ments (see appendix, section 9.3) Measure the voltage drop on each varistor element (see fig. 44) at Maschinenfabrik Reinhausen G m b H imAd.c. Technical Service Postfach 1 2 0 3 6 0 D-93025 Regensburg Phone: +49-941-4090-0 Fax: +49-941-4090-111 Telex: 6 5 881 16 126/01/01/0 6. REINSTALLATION OF THE 7. OIL FILLING DIVERTER SWITCH UNIT Proceed as follows: /A\ CAUTION: Take off the tap changer head cover. The diverter switch oil Lift the diverter switch unit over the compartment and the associated open tap changer head. Lower it down oil conservator must be filled into the oil compartment slowly and only with new mineral insulating carefully. oil for transformers according t o Ensure alignment of marks on the IEC 296 (1982). The use of other support plate of the diverter switch oil puts at risk the trouble-free unit and in the tap changer head operation of tap changer and (fig. 7). transformer. When coupling the diverter switch unit turn, if necessary, the insulating shaft Fill new oil into the diverter switch oil slightly until the coupling engages. compartment up to the level of the Fix the diverter switch unit by the support plate. Put the cover on the tap screws of the support plate. changer head making sure that the gasket fits properly; if necessary, Standard design: replace the O-ring. 4 screws M 8 x 20/w.s. 13. The head cover is attached by Special design for installation into a 2 4 bolts M10/w.s. 17, max. torque bell-type tank: 5 nuts M8/w.s. 13. 34 Nm, secured by spring washers. Both types are secured by spring Open the stop valve between pro- washers, max. torque 22 Nm. tective relay and oil conservator. Vent the tap changer head through Reinstall the position indicating dial the bieeder valve in the tap changer (slide clip onto the shaft end). head cover (remove screw cap M30/ w.s.36 a n d lift valve tappet b y means of a screwdriver), fig. 45. Bleed the suction pipe (screw cap M16/w.s. 22, bleeder screw M6 with cheese head, max. torque 2 Nm), see fig. 46. In case of an existing stationary oil filter unit: operate the oil filter unit and bleed. Fill the oil conservator with new oil up to its original level. JAN CAUTION: The transformer must b e ener- gized only after a rest period of at least 1 hour after oil filling. 126/01/01/0 17 8. FURTHER CHECKS Check the electrical and mechanical end position stops of the motor drive (see Operating Instructions No. 40 for AN ATTENTION: motor drive M A 7 and No. 8 0 for After a response of the protec- M N CAUTION: motor drive M A 9). tive relay, d o not reset until the The transformer must not be tap changer a n d the transformer energized without prior checks have been checked. For this pur- carried out according t o sec- 8.3 Protective relay RS 2001 (see pose withdraw t h e tap changer tions 8.1 t o 8.4. Operating Instructions No. 59) insert and check i t according t o our Inspection Instructions. A response of the protective relay Proceed i n detail according to 8.1 Drive shaft must cause the circuit breakers to Operating Instructions No. 59 immediately switch off the trans- for the protective relay RS 2001. Couple the horizontal drive shaft to former. the upper gear unit and the bevel gear Before returning t o operation,. max. torque (6 screws M 6 / w. s10, T h e operational test of the protective make sure that the cause of the 9 Nm, lock tabs). relay should, therefore, include a trouble h a s been corrected a n d check of the proper function of the that tap changer and transfor- Check the horizontal! and the vertical circuit breakers. mer are free of damage. drive shaft, especially at their coupling points (check tightness of bolts and Make sure that the transformer can- Reconnection o f the transformer nuts, locking function of lock tabs). not be energized and its ground con- without prior checking i s not If necessary, grease the coupling bolts nections cannot be removed during allowed a n d c a n lead t o severe and O-rings (e.g. with SHELL 6432), testing. Furthermore, m a k e sure that, damage of tap changer and adjust the axial clearance to 3 mm. if existing, the fire-extinguishing transformer. equipment coupled with the tripping of Check the bellows and greasing of the protective relay cannot operate. ball joints (only special designs with I n case of major faults of tap changer ball joints). Proceed as follows: or motor drive which cannot be easily Check the upper gear unit on the tap 1. Close the circuit breakers with the overcome on the spot and in case of a changer head cover and the bevel isolating switches open and the response of the protective relay, gear (add lubricating grease if neces- transformer terminals grounded. please contact the authorized MR sary). representative, the transformer 2. Open the hood for access to the manufacturer or directly test push-buttons ( 3 screws M6/ 8.2 Functional tests of motor drive w.s. 10. Press the push-button Maschinenfabrik Reinhausen G m b H and tap changer »OFF«. Technical Service The circuit breakers must open. Postfach 12 03 60 Check coincidence of position indica- tions of tap changer and motor drive. « 3. With the protective relay in » O F F D-93025 Regensburg position, it must be impossible Phone: +49-941-40 90-0 to close the circuit breakers. Telefax: +49-941-40 90-501 Check! Telex: 6 5 881 JAN WARNING: 4. Reset the protective relay to A coupling fault between tap position »SERVICE« and lock changer a n d motor drive unit the hood (3 screws M6, 8.4 Voltage regulator (see exists, if tap changer a n d m o t o r max. torque 5 Nm). Operating Instructions No. 66 d r i v e u n i t s h o w different operat- for voltage regulator MK 20 or ing positions. Misalignment of No. 114 for MK 30, respec- c o u p l i n g between t a p c h a n g e r tively) and motor drive unit can lead t o severe damage of tap changer If the tap changer is controlled by an a n d transformer, i f operation i s automatic voltage regulator: continued. Check settings of voltage level, sen- sitivity (bandwidth) and delay time Check symmetrical coupling of the according to the Operating Instruc- motor drive to the tap changer. tions i n order to avoid unnecessary Proceed as described in the appendix, tap change operations. section 9.4. Perform trial operations across the whole tapping range. 18 126/01/01/0 9. APPENDIX 9.1 Evaluation of Measurement Of CONTACT WEAK.........cccuerrieiriiiiirecciiir reer erence reneeeennrareeaaas 895 053 the contact wear Contact positions of the diverter switch during measurement Of CONACt WEAN.....c...o.cceviiiii icici cere beee 894 594 Registration of contact Wear.............cccvv einer Table HII Sis i 58; l_j E: m= f FT iE= 3 ——| S |-_— | Hy H i r i 8,518,5 mri c| cH | 2; Sty I — — — — — TT Bu X = 4 TTT I 5 / 1 LY] Z; 777 2; 1 _ J Z :a 1 ml || % 7 Al = pn 1} A | — SLED = Total contact wear 2c = K - x (mm) 2c..=12mm Reference dimension S=3+ 1 mm MASCHINENFABRIK REINHAUSEN O n - l o a d t a p c h a n g e r s type R a n d R M Measurement of contact wear 895 053:1E 126/01/01/0 19 RIGHT DIVERTER SWITCH ® \ SIDE SWITCHED ON: MEASUREMENT OF CONTACT \ WEAR ON ns MAIN SWITCHING CONTACT b TRANSITION CONTACT b1 DIVERTER SWITCH IN INTERMEDIATE POSITION: MEASUREMENT OF CONTACT WEAR ON TRANSITION CONTACT b2 TRANSITION CONTACT a2 -— - LEFT DIVERTER SWITCH / ; SIDE SWITCHED ON: / MEASUREMENT OF CONTACT WEAR ON < TRANSITION CONTACT a t MAIN SWITCHING CONTACT a ail MASCHINENFABRIK On-load tap changers type R and RM REINHAUSEN Positions of t h e diverter switch during 894 594:3E measurement of contact wear 20 126/01/01/0 Measurement and evaluation of the contact wear of the on-load tap changer types R & RM On-load tap changer type: Serial no: Date: Operation counter reading: Number of operations of the contacts: Transformer data: Transformer no.: Substation: Ask MR for this value. Contact wear inmm Evaluation and check Diverter | Contact | Dimen- K A Total [Individual | Check | Difference Difference Difference switch function | sion X | Contact wear wear Total Check Total Check Total Check eo ametme| of delivery | TE | amar | 2cb-2cb1 | demomz| 2cb-2cb2 7 | eaten 2cb1-2cb2 | 1 2 3 3a 4 5 6 7 8 9 10 11 12 L1 a O k.( ) [4 Ok. ( ) O k.( ) al i Not o.k. Not o.k. Not o.k. az () |« () J () b2 Ok. ( ) | Ok. ( ) Ok. ( ) bi I Not o.k. Not o.k. i Not o.k. b 0 |e () () L2 a Ok. ( ) | Ok. () Ok. () al I Not o.k. Not o.k. Not o.k. az () |« () | () b2 Ok. ( ) | Ok. ( ) Ok. ( ) b1 Not o.k. Not o.k. \ Not o.k. b | () [+ () () L3 a Ok () | Ok. ( ) Ok. ( ) ai I Not o.k. Not o.k. Not o.k. a2 0 | 0 J (0) b2 Ok. ( ) | Ok. () O k.( ) b1 Not o.k. Not o.k. i Not 0.k. b A 0 |e () () Table l l l Determination of contact wear In the following example it is assumed that the existing operating conditions (e.g. partial-load duty) cause the main switching contacts and transition contacts to show different contact wear. Measurement and determination of the contact wear is demonstrated with the contacts a, a1 and a2 of the sector L1. The same values may be expected with the contacts b, b1 and b2 as well as with the corresponding contacts of the sectors L2 and L3. 1. Measurement of contact wear after 80,000 switching operations; the values are still within the admissible range of tolerance: 2. The projection on 160,000 switching operations under the same operating conditions shows double wear on all contacts so that the difference in wear A 2 ¢ in columns 9 and 11 exceed the admissible limits. 3. Therefore, it is recommended to interchange the stationary and movable contacts a and a2. This is permissible because of the contact thickness difference a - a 2 < 2.0 m m (see section 5.3). Otherwise the contacts a and a 2 must b e properly matched in thickness. 4. With a new projection on 160,000 operations in the same way as under point 1. an optimum utilization of the contact value is obtained. 5. Another projection on 240,000 operations shows the same wear (A 2c) as under point 1. so that after 240,000 operations it will be necessary to interchange contacts a and a2 again. 126/01/01/0 21 Evaluation of the contact wear of the on-load tap changer types R & RM On-load tap changer type: Serial no.: Date: Operation counter reading: Number of operations of the contacts: Transformer data: Transformer no.: Substation: Ask MR for this value. Contacts a t i n : mm Evaluation a n d check Diverter | Contact |Dimen- K Total novice Check [Difference Difference Difference switch function| sion X | Contact wear wear Total Check Total Check Total Check sector distance | 2c¢=K-X | c=2c/2 c