AS/NZS 3788:2006 Pressure Equipment - In-service Inspection (PDF)
Document Details
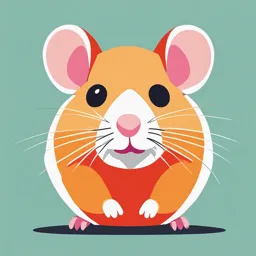
Uploaded by WellConnectedCornflower
2006
Tags
Summary
This document is a licence agreement for AS/NZS 3788:2006, a standard for the inspection of pressure equipment. It outlines the terms and conditions for using the document, including restrictions on redistribution.
Full Transcript
LICENCE for AS/NZS 3788:2006 Pressure equipment - In-service inspection Licensee: ARL Laboratory Services P/L Date: Wednesday, July 07, 2010 11:48 AM Licence Agreement This is an agreement between the end user of the Product ("Licensee") and SAI Global Limited, 286 Sussex Street, Sydney NSW 2000 AUS...
LICENCE for AS/NZS 3788:2006 Pressure equipment - In-service inspection Licensee: ARL Laboratory Services P/L Date: Wednesday, July 07, 2010 11:48 AM Licence Agreement This is an agreement between the end user of the Product ("Licensee") and SAI Global Limited, 286 Sussex Street, Sydney NSW 2000 AUSTRALIA, ABN 67 050 611 642. 1. Definitions and Interpretations Australian Standards means Australian Standards and includes Joint ISO/Australian Standards, Joint NZ/Australian Standards, current Draft Australian Standards, and amendments to Australian Standards. Concurrent Users means the maximum number of people able to access the Product at any one time, and is limited to the number of Licences purchased. ISO Standards means Standards published by the International Organization for Standardization (ISO), for which SAI Global is an authorised distributor. IEC Standards means Standards published by the International Electrotechnical Commission (IEC), for which SAI Global is an authorised distributor. Internal use means use of the Product within the Licensee’s organization. Licence means the right to access and use the Product. Licensee means the purchaser and user of the Product. Product means Australian Standards, ISO Standards and IEC Standards ordered and purchased through the infostore, and downloaded as electronic PDF files. 2. Product Availability 2.1. The Product is available Click via the Wide the the useLicence of a web browser.scroll Documents are provided as PDF files, onWorld the red box Web abovethrough to activate Agreement bar. viewable through the use of Adobe ® Acrobat ® Reader Version 7 and above. 3. Licence Agreement WEB LINKS 3.1. By using the Product the Licensee agrees to be bound by the Licence Agreement for the Product. 3.2. The Licensee is granted a non-exclusive and non-assignable Licence is to current use the Product. Check if this document 3.3. Licensees are permitted to use the Product following extent: Findthe similar documents 3.3.a. Purchasers of personal user Licences for the may locally install and use the Product on the number of individual Visit ourProduct website computers corresponding to the number of personal users specified in the SAI Global Infostore order. Licensees are permitted to make paper copies of the Product for Internal use limited to the number of personal users specified in the SAI Global Infostore order only ( excludes electronic pads of forms ). Licensees are permitted to make one electronic copy of the Product for backup International Standards on-line at infostore.saiglobal.com/store purposes. 3.3.b. Purchasers of network Licences for the Product may install and use the Product on a network with the number of Concurrent Users permitted corresponding to the number of users specified in the SAI Global Infostore order. Licensees are permitted to make paper copies of the Product for Internal use limited to the number of network users specified in the SAI Global Infostore order only. Licensees are permitted to make one electronic copy of the Product for backup purposes. 3.4. SAI Global will not in any way provide the Licensee with an updating service for the Product. The Licensee agrees that SAI AS/NZS 3788:2006 Purchased By : Ms Renu Renu. Licensed to ARL Laboratory Services P/L on 7 July 2010. 1 user personal user licence only. Storage, distribution or use on network prohibited (10129524). AS/NZS 3788:2006 Australian/New Zealand Standard™ Pressure equipment—In-service inspection Purchased By : Ms Renu Renu. Licensed to ARL Laboratory Services P/L on 7 July 2010. 1 user personal user licence only. Storage, distribution or use on network prohibited (10129524). AS/NZS 3788:2006 This Joint Australian/New Zealand Standard was prepared by Joint Technical Committee ME-001, Pressure Equipment. It was approved on behalf of the Council of Standards Australia on 27 June 2006 and on behalf of the Council of Standards New Zealand on 7 July 2006. This Standard was published on 27 July 2006. The following are represented on Committee ME-001: ACT WorkCover Australasian Institute of Engineer Surveyors Australian Aluminium Council Australian Building Codes Board Australian Chamber of Commerce and Industry Australian Industry Group Australian Institute for the Certification of Inspection Personnel Australian Institute of Energy Australian Institute of Petroleum Bureau of Steel Manufacturers of Australia Department for Administrative and Information Services, SA Department of Consumer and Employment Protection, WorkSafe Division, WA Department of Infrastructure, Energy and Resources, Tas. Department of Labour New Zealand Electricity Engineers Association New Zealand Energy Networks Association Engineers Australia Institution of Professional Engineers New Zealand Insurance Council of Australia Land Transport Safety Authority New Zealand LPG Australia Materials Australia National Association of Testing Authorities, Australia New Zealand Engineering Federation New Zealand Heavy Engineering Research Association New Zealand Petrochemical Users Group Pressure Equipment Association Victorian WorkCover Authority Welding Technology Institute of Australia WorkCover NSW Keeping Standards up-to-date Standards are living documents which reflect progress in science, technology and systems. To maintain their currency, all Standards are periodically reviewed, and new editions are published. Between editions, amendments may be issued. Standards may also be withdrawn. It is important that readers assure themselves they are using a current Standard, which should include any amendments which may have been published since the Standard was purchased. Detailed information about joint Australian/New Zealand Standards can be found by visiting the Standards Web Shop at www.standards.com.au or Standards New Zealand web site at www.standards.co.nz and looking up the relevant Standard in the on-line catalogue. Alternatively, both organizations publish an annual printed Catalogue with full details of all current Standards. For more frequent listings or notification of revisions, amendments and withdrawals, Standards Australia and Standards New Zealand offer a number of update options. For information about these services, users should contact their respective national Standards organization. We also welcome suggestions for improvement in our Standards, and especially encourage readers to notify us immediately of any apparent inaccuracies or ambiguities. Please address your comments to the Chief Executive of either Standards Australia or Standards New Zealand at the address shown on the back cover. This Standard was issued in draft form for comment as DR 05161. Purchased By : Ms Renu Renu. Licensed to ARL Laboratory Services P/L on 7 July 2010. 1 user personal user licence only. Storage, distribution or use on network prohibited (10129524). AS/NZS 3788:2006 Australian/New Zealand Standard™ Pressure equipment—In-service inspection Originated as AS 3788—1990. Previous edition AS/NZS 3788:2001. Fourth edition 2006. COPYRIGHT © Standards Australia/Standards New Zealand All rights are reserved. No part of this work may be reproduced or copied in any form or by any means, electronic or mechanical, including photocopying, without the written permission of the publisher. Jointly published by Standards Australia, GPO Box 476, Sydney, NSW 2001 and Standards New Zealand, Private Bag 2439, Wellington 6020 ISBN 0 7337 7657 4 Purchased By : Ms Renu Renu. Licensed to ARL Laboratory Services P/L on 7 July 2010. 1 user personal user licence only. Storage, distribution or use on network prohibited (10129524). AS/NZS 3788:2006 2 PREFACE This Standard was prepared by the Joint Standards Australia/Standards New Zealand Committee ME-001, Pressure Equipment to supersede AS/NZS 3788:2001, Pressure equipment—In-service inspection. The objective of the revision is to align the Standard with current equipment integrity management and assessment practices and to address some of the problems currently experienced in industry. To achieve this, the Standard has been significantly revised throughout. While the Standard still sets out minimum inspection intervals, it now allows those intervals to be varied in response to a thorough risk-based engineering assessment. This is intended to allow the efficient use of integrity management programs by large-scale industry. As such assessments require significant resources to consider all the relevant factors, it is expected that the majority of the users of this Standard will continue using the prescribed intervals. It should be noted that the previous Clause 4.4.4.3(c), Further extended period, has been removed to ensure that variations to inspection intervals are properly assessed. More emphasis has been placed on the responsibility to use competent bodies and personnel for all aspects of the inspection and assessment processes—a reflection of the current philosophy of occupational health and safety regulations. Guidance material is included to aid industry in assessing the competence of bodies and people for different tasks. The Committee noted that poorly-marked or unidentifiable equipment is a significant issue facing inspectors, and has provided some guidance on dealing with such situations. The appendices have also been revised, including a review of the normative or informative status of each. Appendix O (regarding fracture mechanics) has been significantly revised. A new appendix has been added regarding the inspection of support structures. This Standard provides inspection requirements to assist in assuring the continued safe operation of pressure equipment. In some circumstances additional inspection may be necessary for adequate performance or safety. The material contained in this Standard may be used as an aid in the training of inspection personnel. Users of this Standard are reminded that it has no legal authority in its own right, but acquires legal standing where adopted by government or other authority having jurisdiction, or if specified as part of a commercial contract. Statements expressed in mandatory terms in notes to tables and figures are deemed to be requirements of this Standard. The terms ‘normative’ and ‘informative’ have been used in this Standard to define the application of the appendix to which they apply. A ‘normative’ appendix is an integral part of a Standard, whereas an ‘informative’ appendix is only for information and guidance. Purchased By : Ms Renu Renu. Licensed to ARL Laboratory Services P/L on 7 July 2010. 1 user personal user licence only. Storage, distribution or use on network prohibited (10129524). 3 AS/NZS 3788:2006 CONTENTS Page SECTION 1 SCOPE AND GENERAL 1.1 SCOPE........................................................................................................................ 5 1.2 APPLICATION........................................................................................................... 5 1.3 REFERENCED AND RELATED DOCUMENTS...................................................... 6 1.4 DEFINITIONS............................................................................................................ 6 1.5 RISK MANAGEMENT AND RISK BASED INSPECTION...................................... 9 1.6 SAFETY...................................................................................................................... 9 1.7 SPECIAL CONDITIONS AND VARIATIONS.......................................................... 9 1.8 REFERENCED STANDARDS................................................................................... 9 SECTION 2 INSPECTION REQUIREMENTS 2.1 OBJECTIVES OF INSPECTION.............................................................................. 10 2.2 ASSET INTEGRITY LIFE CYCLE.......................................................................... 10 2.3 INSPECTION PROCESS.......................................................................................... 11 SECTION 3 INSPECTION PERSONNEL AND ADMINISTRATION 3.1 OWNER’S RESPONSIBILITIES.............................................................................. 12 3.2 RESPONSIBILITIES AND CAPABILITIES OF PERSONS CARRYING OUT IN-SERVICE INSPECTION..................................................................................... 13 3.3 RESPONSIBILITIES OF INSPECTION BODIES.................................................... 13 3.4 SUPPORT ORGANIZATIONS................................................................................. 14 SECTION 4 PRESSURE EQUIPMENT INSPECTION 4.1 GENERAL................................................................................................................ 15 4.2 COMMISSIONING OR RECOMMISSIONING INSPECTION............................... 15 4.3 OPERATING SURVEILLANCE AND MONITORING........................................... 16 4.4 PERIODIC INSPECTION......................................................................................... 16 4.5 RISK BASED INSPECTION.................................................................................... 29 4.6 INSPECTION OF IDLE PRESSURE EQUIPMENT................................................. 29 4.7 PRESSURE-RELIEF DEVICES............................................................................... 30 4.8 CONTROLS CRITICAL FOR SAFEGUARDING EQUIPMENT............................ 37 4.9 INSTRUMENTATION AND CONTROLS............................................................... 37 4.10 EMERGENCY SHUTDOWN SYSTEMS................................................................. 37 4.11 AUTOMATIC FIRE-FIGHTING SYSTEMS USED TO PROTECT PRESSURE EQUIPMENT............................................................................................................ 38 4.12 LOW TEMPERATURE VESSELS........................................................................... 38 4.13 PRESSURE PIPING.................................................................................................. 38 SECTION 5 ASSESSMENT OF PRESSURE EQUIPMENT INTEGRITY 5.1 GENERAL................................................................................................................ 40 5.2 FITNESS FOR SERVICE ASSESSMENT................................................................ 40 5.3 DETERMINATION OF REMAINING LIFE............................................................ 45 5.4 DE-RATING............................................................................................................. 45 SECTION 6 REPAIRS, ALTERATIONS AND RE-RATING 6.1 GENERAL................................................................................................................ 47 6.2 REPAIRS................................................................................................................... 47 6.3 RE-RATING.............................................................................................................. 49 Purchased By : Ms Renu Renu. Licensed to ARL Laboratory Services P/L on 7 July 2010. 1 user personal user licence only. Storage, distribution or use on network prohibited (10129524). AS/NZS 3788:2006 4 SECTION 7 INVESTIGATION OF DETERIORATION AND FAILURES 7.1 GENERAL................................................................................................................ 51 7.2 FAILURE ANALYSIS.............................................................................................. 51 7.3 RECORDING OF INCIDENTS AND FAILURES.................................................... 52 SECTION 8 PRESSURE EQUIPMENT DOCUMENTATION AND IDENTIFICATION 8.1 INFORMATION FILES............................................................................................ 53 8.2 REGISTER OF PRESSURE EQUIPMENT.............................................................. 53 8.3 PRESSURE EQUIPMENT IDENTIFICATION........................................................ 53 8.4 PRESSURE EQUIPMENT MARKING.................................................................... 55 8.5 PRESSURE EQUIPMENT DATA............................................................................ 56 8.6 PRESSURE EQUIPMENT HISTORY...................................................................... 57 APPENDICES A REFERENCED AND RELATED DOCUMENTS.................................................... 59 B RISK MANAGEMENT............................................................................................. 66 C SAFETY DURING INSPECTION............................................................................ 70 D METHODS OF INSPECTION.................................................................................. 74 E INSPECTION AND REPAIR OF TRANSPORTABLE VESSELS........................... 87 F INSPECTION OF BOILERS..................................................................................... 95 G INSPECTION OF UNFIRED PRESSURE VESSELS—STATIONARY.................. 99 H INSPECTION OF HEAT EXCHANGERS, COOLERS AND CONDENSERS...... 102 I INSPECTION OF PRESSURE PIPING.................................................................. 104 J INSPECTION OF FIRED HEATERS..................................................................... 118 K EXAMPLE INSPECTION REPORTS..................................................................... 121 L PRESERVATION AND INSPECTION OF IDLE PRESSURE EQUIPMENT....... 123 M COMMON MODES AND CAUSES OF DETERIORATION AND FAILURE...... 126 N ASSESSMENT OF LOCALIZED WALL THINNING OF CYLINDRICAL, CONICAL, AND SPHERICAL SHELLS................................................................ 131 O ASSESSMENT OF PLANAR DEFECTS................................................................ 141 P PRESSURE RELIEF VALVES—SUPPLEMENTARY INFORMATION.............. 156 Q INSPECTION OF PRESSURE EQUIPMENT WITH QUICK-ACTUATING CLOSURES AND SWING BOLT DOORS....................... 160 R INSPECTION OF BURIED OR MOUNDED PRESSURE VESSELS.................... 161 S INSPECTION OF DEAERATORS......................................................................... 162 T INSPECTION OF STORAGE TANKS TO API 620 OR EQUIVALENT............... 163 U REMAINING LIFE ASSESSMENT....................................................................... 166 V COMPETENCY OF IN-SERVICE INSPECTION BODIES AND PERSONNEL.. 177 W INSPECTION OF DRUMS FOR TRANSPORT OF LIQUEFIED GAS................. 181 X TESTING OF SOFT SEATED POP ACTION RELIEF VALVES FOR LIQUEFIABLE GAS SERVICE....................................................................................... 186 Y INSPECTION OF HERITAGE BOILERS AND PRESSURE VESSELS............... 187 Z INSPECTION OF FOUNDATIONS AND STRUCTURES................................... 195 Purchased By : Ms Renu Renu. Licensed to ARL Laboratory Services P/L on 7 July 2010. 1 user personal user licence only. Storage, distribution or use on network prohibited (10129524). 5 AS/NZS 3788:2006 STANDARDS AUSTRALIA/STANDARDS NEW ZEALAND Australian/New Zealand Standard Pressure equipment—In-service inspection SECT ION 1 SCOPE AND GENERA L 1.1 SCOPE This Standard specifies the minimum requirements for the inspection, repair and alteration of in-service boilers, pressure vessels, piping, safety equipment, and associated safety controls (hereafter referred to as pressure equipment), and gives guidance in the execution of such activities. Guidance is included for the inspection of ancillary equipment such as structures. This Standard also specifies the requirements for the initial inspection after installation and prior to commissioning. The inspection flow diagram (see Figure 1.1) illustrates the various types of inspection covered by this Standard. This Standard provides information to facilitate grounds for agreement between interested parties, and the establishment of uniform minimum requirements for in-service inspections, including inspection intervals and procedures, to assist in assuring safe and economic operation. Information is provided on mechanisms of deterioration, the assessment of defects, and the assessment of fitness for service of pressure equipment. No rules can be written in sufficient detail to cover all aspects of the inspection of in-service pressure equipment. The owner is responsible for ensuring that the extent and frequency of inspection is appropriate and adequate for the continued safe operation of the pressure equipment. This may require the seeking of expert advice. Duty of Care is now prescribed by Occupational Health and Safety Legislation. This Standard does not supersede such Duty of Care, but is intended to complement and contribute to it. 1.2 APPLICATION This Standard applies to, but is not limited to, pressure equipment covered by AS/NZS 1200. Typically it includes the following: (a) Boilers and associated pressure parts, controls and pipe work covered by AS 1228, BS 1113, BS 2790, AS 2593 and ASME BPV-I. (b) Pressure vessels and associated pressure parts, controls and pipe work covered by AS 1210, BS PD 5500, EN 13445, ASME BPV-VIII, AS 2971 (serially produced pressure vessels) and EN 286-1. (c) Pressure piping covered by AS 4041, NZS/BS 806, ASME B 31.1 and ASME B 31.3. (d) Pressurized storage tanks built to API 620 or equivalent. (e) Fired heaters. (f) Heritage boilers and pressure vessels. Although pressure equipment with Hazard Level E (to AS 4343) is within the scope of this Standard, no specific requirements have been included. To ensure safety, in-service inspection of such equipment should follow the principles of this Standard, along with good engineering practice. COPYRIGHT Purchased By : Ms Renu Renu. Licensed to ARL Laboratory Services P/L on 7 July 2010. 1 user personal user licence only. Storage, distribution or use on network prohibited (10129524). AS/NZS 3788:2006 6 This Standard does not specifically deal with the following equipment, but provides information which may be used as guidance. (i) Storage tanks covered by AS 1940 and built to API 650, AS 1692 or equivalent (refer API 653). (ii) Miniature boilers to the AMBSC codes. (iii) Pressurized machines, e.g. turbines, compressors, etc. (iv) Pipelines as per AS 2885 or equivalent. 1.3 REFERENCED AND RELATED DOCUMENTS 1.3.1 Referenced documents A list of the documents referred to in this Standard is given in Appendix A. NOTE:Where reference is made to a Standard by its number only, the reference applies to the current edition of the Standard including any amendments. Where reference is made to a Standard by number, year and, where relevant, an amendment number, the reference applies to that specific document. 1.3.2 Related documents Related documents and guidance references are listed in Appendix A. 1.4 DEFINITIONS For the purposes of this Standard, the definitions given in AS 4942 and the following apply. NOTE: Definitions for terms such as ‘owner’, ‘competent person’ and ‘inspector’ may differ slightly from State OHS regulations or codes of practice. For calculations and reports AS ISO 1000, the International System of Units, shall be applied. 1.4.1 Inspector A person able to inspect pressure equipment for the purpose of establishing conformity with the specified requirements. 1.4.2 Inspection body A body corporate, firm or person external to that of the owner, or an owner’s inspection department, able to provide the inspection services of pressure equipment. 1.4.3 Competent person A person who, due to their knowledge and skills, is acceptable to the owner/user/responsible person to perform a required task. The appropriate knowledge and skills may be acquired through training, experience, qualifications, or some combination of these. NOTES: 1 The term ‘competent person’ is used in this Standard to address a variety of technical requirements. Guidance on competency requirements is provided in Appendix V. 2 In New Zealand the ‘competent person’ for inspection activities is the ‘inspector’ or ‘design verifier’. COPYRIGHT Purchased By : Ms Renu Renu. Licensed to ARL Laboratory Services P/L on 7 July 2010. 1 user personal user licence only. Storage, distribution or use on network prohibited (10129524). 7 AS/NZS 3788:2006 1.4.4 Inspection Activities such as viewing, measuring, examining, testing, gauging, calculating, checking, verifying one or more characteristics of a product design, material, manufacture, product, service, process, plant or reports and determination of their conformity with specific requirements or, on the basis of professional judgement, with general requirements. NOTES: 1 The above activities may require multiple parties. 2 For inspection the ‘competent person’ should be the ‘in-service inspector’ or a person with equivalent qualifications and experience. 1.4.5 Surveillance Activities which observe the general condition of equipment, including on-line inspection, monitoring, planned or un-planned condition audits, etc. 1.4.6 Pressure equipment and ancillaries Equipment as defined in Clause 1.2, including boilers, pressure vessels, pressure piping, and pressurized storage tanks. In New Zealand, the regulations also include certain fired heaters, hot water boilers, gas and steam turbines, steam engines, pumps and compressors. See AS/NZS 1200. Pressure equipment also includes ancillaries such as interconnected parts and components, valves, gauges and other fittings, headers, bolting, gaskets, supports and pressure-retaining accessories. Unless noted, it does not normally include items such as pumps, fans, and similar machinery. 1.4.7 Owner/User/Responsible person A body corporate, firm or person who has right of title to, or management of, or control over, pressure equipment. This includes a person exercising such management or control as an agent of the owner and the user, operator and controller, as appropriate. Where these are different parties, the owner is responsible for clarifying the respective roles, and is responsible to ensure overall compliance with this Standard. NOTE: Control is taken to encompass the operational life cycle, ie. operation, inspection and testing, repair and alteration, maintenance, re-rating, mothballing or preservation, decommissioning and abandonment. 1.4.8 Defects Imperfections, damage, deterioration or deficiencies in pressure equipment. NOTE: The presence of a defect in pressure equipment does not necessarily imply that the equipment is unfit for service (see Clause 5.2). 1.4.9 In-service The period during the life of pressure equipment from the beginning of commissioning until disposal. COPYRIGHT Purchased By : Ms Renu Renu. Licensed to ARL Laboratory Services P/L on 7 July 2010. 1 user personal user licence only. Storage, distribution or use on network prohibited (10129524). AS/NZS 3788:2006 8 Commissioning i n s p e c ti o n ( i.e. o n-s i te a u th o r i s ati o n to u s e a n d re g i ste r Pe r i o d i c i n s p e c ti o n (s h u td ow n o r o n l i n e) I n s p e c ti o n fo r p ro p o s e d changed p ro c e s s i n -s e r v i c e c o n d i ti o n s I n s p e c ti o n fo l l ow i n g serious exc u r s i o n o r d a m ag e I n s p e c ti o n fo l l ow i n g re pa i r o r a l te rati o n I n s p e c ti o n of i d l e e q u i p m e nt I ns p e c ti o n fo r re m a i n i n g l i fe d ete r m i n ati o n o r p u rc h a s e C O M PE T EN T I N S PECT I O N PER SO N N EL i.e. i n s p e c to r s, o r c o m p ete nt p e r s o n s (fo r s e l e c te d d u ti e s) SC O PE A N D C O N D I T I O N S O F I N S PECT I O N S I N S PECT I O N PRO C ED U R ES A N D FAC I L I T I ES I N S PECT I O N O PER AT I O N I N S PECT I O N R ES U LTS 1. 2. 3. 4. Ev i d e n c e of o r i g i n a l d e s i g n a n d c o n s tr u c ti o n D et a i l s of d etete d d efe c ts ( by v i s u a l o r N D E ) D et a i l s of d e g rad e d m ate r i a l ( by v i s u a l, N D E, s a m p l i n g a n d o p e rati n g d at a) D et a i l s of d ef i n c i e n c i e s i n p rote c ti ve e q u i p m e nt o r c o ntro l s I N S PECT I O N AS S ES S M EN T (C o m p a r i s o n w i th a c c e pt a n c e c r i te r i a) 1. C o m pa r i s o n w i th c o d e re q u i re m e nts fo r ac c e pt a n c e 2. D ete r m i n e i f d efe c ts o r d e g rad e d m ate r i a l a re ac c e pt a b l e 3. D ete r m i n e i f p rote c ti ve e q u i p m e nt a n d c o ntro l s a re ac c e pt a b l e Ac c e pta b l e Ye s No Repair Re -rate a n d possibly m o d i f y p ro c e s s A l te r R e m ove f ro m ser vice R e pa i r/a l te rati o n i n s p e c ti o n Recommissioning i n s p e c ti o n S u i ta b l e fo r c o nti n u e d u s e u nti l n ex t d ef i n e d i ns p e c ti o n N ex t i ns p e c ti o n, s c o p e a n d d u e d ate FIGURE 1.1 IN-SERVICE INSPECTION FLOW DIAGRAM COPYRIGHT Purchased By : Ms Renu Renu. Licensed to ARL Laboratory Services P/L on 7 July 2010. 1 user personal user licence only. Storage, distribution or use on network prohibited (10129524). 9 AS/NZS 3788:2006 1.5 RISK MANAGEMENT AND RISK BASED INSPECTION Risk management techniques may be used to achieve the objectives of the pressure equipment inspection program (see Clause 2.1). In order to operate pressure equipment at an acceptable level of risk, the extent and frequency of inspection, the quality of process control and monitoring and the potential consequence of failure shall be taken into account. NOTE: Guidance on risk management is given in Appendix B. 1.6 SAFETY Appendix C sets down principles and procedures to be followed to ensure the safety of personnel during the inspection of pressure equipment. 1.7 SPECIAL CONDITIONS AND VARIATIONS It is not possible to write requirements to cover all cases of in-service inspection of pressure equipment. In special cases there may be a need to depart from the requirements in this Standard. Where departure from this Standard is necessary, the departure shall— (a) be justified and fully documented by a competent person; and (b) give a level of safety and quality that is no less than that specified in this Standard. Any departure from this Standard is the subject of agreement between the parties concerned. 1.8 REFERENCED STANDARDS Where this Standard makes reference to other Standards, these referenced Standards are not intended to be limiting or exclusive and alternative standards may be substituted for the referenced standards, where these give an equivalent level of safety and equipment quality. A list of pressure equipment Standards used in Australia and New Zealand and procedures for their use are included in AS/NZS 1200. COPYRIGHT Purchased By : Ms Renu Renu. Licensed to ARL Laboratory Services P/L on 7 July 2010. 1 user personal user licence only. Storage, distribution or use on network prohibited (10129524). AS/NZS 3788:2006 SECT I ON 10 2 I N SPE CT I O N RE Q U I RE M E N T S 2.1 OBJECTIVES OF INSPECTION The objectives of in-service inspection are to— (a) promote the safety and health of persons in the workplace and of the public; (b) comply with occupational health and safety legislation; (c) limit the potential damage to property; and (d) protect the environment, through the control, reduction or elimination of risk associated with the pressure equipment. These objectives are achieved by— (i) verifying that fabrication and operation comply with design conditions; (ii) verifying that pressure equipment is safe and fit for service under the specified operating conditions until the next planned inspection; (iii) verifying that maintenance, repairs, and alterations are carried out in a manner which maintains the integrity of the pressure equipment; (iv) indicating repairs, replacements or alterations which may be needed, and assessing remaining safe life of the pressure equipment. Additional inspections may be carried out for a number of reasons, including, but not limited to— (A) assessment of the early performance of new design, material, fabrication, and testing; and (B) investigation and assistance in determining the causes of failure, hazards, reduced performance, or abnormal conditions which may lead to failure, and to determine what consequent temporary or long-term action is required to ensure continued safe operation or life commensurate with commercial requirements. 2.2 ASSET INTEGRITY LIFE CYCLE Fitness for service during the overall life cycle of pressure equipment is determined by activities at the stages listed as follows: (a) Concept—initially when many main decisions which affect ultimate safety (and inspection) are made. (b) Design—usually design review and verification. (c) Material—usually examination, marking and certificate correlation. (d) Fabrication. (e) Installation. (f) Commissioning—including identification and registration. (g) Operation—on line. (h) Periodic in-service inspection. (i) Maintenance. COPYRIGHT Purchased By : Ms Renu Renu. Licensed to ARL Laboratory Services P/L on 7 July 2010. 1 user personal user licence only. Storage, distribution or use on network prohibited (10129524). 11 (j) AS/NZS 3788:2006 Special in-service activity, as follows: (i) Repair. (ii) On-line maintenance or monitoring. (iii) Alteration. (iv) Idle or mothballed pressure equipment. (v) Failure or changed performance. (vi) Determination of remaining life. (vii) Assessment of new materials and designs. NOTE: This Standard deals only with inspection and assessment at stages (f) to (j). 2.3 INSPECTION PROCESS The inspection scope is the subject of agreement between all parties concerned and shall be planned and executed by competent persons. The inspection scope may include items other than pressure equipment. The overall inspection plan shall establish the equipment to be inspected, methods of inspections, requirements for surface preparation, safety requirements, and other relevant matters. The extent and frequency of inspection elements shall be sufficient to provide a high level of assurance that the integrity of the pressure equipment is adequate. Inspection at each stage shall provide some overlap of inspections, e.g. at the initial inspection, fabrication inspection shall be supplemented by visual inspection as a check to detect any damage in transit or installation. Inspection personnel shall make use of personal experience, information from plant records and information from other sources. Communication between all parties concerned shall be clear, prompt and effective at all times. Inspection and surveillance shall be performed while the plant is operational to detect signs of deterioration, damage or evidence that suggests damage or deterioration may exist, e.g. leaks, vibration, settlement, piping movement, adequate performance of piping supports, etc. Integrity assessment shall include review of the control system, pressure safety system, and pressure relief valves in accordance with this and other applicable Standards. A competent person shall assess the findings of the inspections and provide a report to the owner which includes the following: (a) Summary of the inspections performed, the inspection methods used and the findings. (b) Detailed inspection reports for all inspections carried out. (c) The criteria for assessment of the inspection findings. (d) The results of the assessment of the inspection findings. (e) The recommended intervals to the next external and internal inspections. (f) Special comments, e.g. defect monitoring requirements, recommended future inspections, recommended repairs, or recommended changes to current operating practices and parameters. Should defects be found the fitness for service of the pressure equipment shall be assessed by a competent person. COPYRIGHT Purchased By : Ms Renu Renu. Licensed to ARL Laboratory Services P/L on 7 July 2010. 1 user personal user licence only. Storage, distribution or use on network prohibited (10129524). AS/NZS 3788:2006 SECT ION 12 3 I NSPECT I ON PERSONNE L ADM I N I STR AT I ON AND 3.1 OWNER’S RESPONSIBILITIES There shall be a management system sufficient to ensure the continuing integrity and safety of items of pressure equipment. Such a system shall be documented to a level determined to be appropriate in consultation with a person competent in pressure equipment inspection. In determining the appropriate level of documentation issues including the Hazard Level, location, physical condition, maintenance practices, s.ervice history, number of items to be covered, and any other relevant issues, shall be considered. NOTE: For example, a complex chemical processing facility with a number of pressure vessels will warrant a comprehensive, well-developed and well-documented management system. In contrast, for a single small boiler in a commercial laundry where there is a history of good operation, maintenance and inspection, a simple management system with minimal documentation may be appropriate. The management system should include information on all important safety issues, including: (a) Organization structure and defined roles and responsibilities for personnel interfacing with pressure equipment. (b) Safety and Risk Management policy. (c) Critical safety instructions. (d) Alterations, maintenance, and repair procedures. (e) Overall inspection and test plan (see Section 2). (f) Procedures for reporting and investigation of dangerous occurrences. (g) Identification of the personnel responsible for inspection. (h) The competency of the inspector carrying out the inspection. (i) The acceptability of the inspection body. (j) Periodic operational inspection and audit of pressure equipment, ie. compliance with Section 2. (k) Periodic reporting and certificates of inspection, ie. compliance with the requirements of this Standard and any regulatory requirements. (l) Training requirements and schedules for periodic assessment of operating, maintenance and inspection staff. (m) Defined limits of design and critical operating parameters (such as temperature, pressure and chemical composition) and methods for recording and reporting of any excursions and, where required, assessment of significance to integrity. (n) Preparation of equipment for inspection, where appropriate, in accordance with the requirements of AS/NZS 2865 (see also Appendix C). (o) Corrective action where non-conformances with this Standard are found. (p) Re-rating where undertaken. All persons involved in undertaking inspection and assessment of the integrity of pressure equipment shall be competent. COPYRIGHT Purchased By : Ms Renu Renu. Licensed to ARL Laboratory Services P/L on 7 July 2010. 1 user personal user licence only. Storage, distribution or use on network prohibited (10129524). 13 AS/NZS 3788:2006 3.2 RESPONSIBILITIES AND CAPABILITIES OF PERSONS CARRYING OUT INSERVICE INSPECTION 3.2.1 General Personnel involved in in-service inspection shall be experienced, competent, trained, instructed and equipped at the level necessary for their particular task. NOTES: 1 Guidance on the competency of personnel and bodies involved in in-service inspections is given in Appendix V. 2 In New Zealand, inspectors are required to be a signatory or be supervised by a signatory of an accredited inspection body and are required to meet the requirements of the Certification Board for Inspection Personnel (CBIP), or an equivalent body, for in-service inspectors. 3 In New Zealand non-destructive testing is required by legislation to be carried out by a signatory or be supervised by a signatory of an accredited inspection body. 3.2.2 Particular responsibilities In-service inspections shall address the following items: (a) Performing and recording inspections in accordance with this Standard. (b) Acting only within areas of competency. (c) Being mindful of the objectives of this Standard. (d) Communicating clearly. (e) Undertaking inspection in a safe manner. (f) Verifying, as far as practicable, that the equipment meets the requirements of either— (i) the specified Standards designated by the original design code; or (ii) the Standards specified for any re-rating or modifications. (g) Ensuring that appropriate methods of inspection, including non-destructive testing, are provided by competent personnel. (h) Identifying any remedial work required to be undertaken in the interests of safety. (i) Issuing a certificate of inspection and report to the owner in accordance with this Standard and requirements of the owner. 3.3 RESPONSIBILITIES OF INSPECTION BODIES Bodies managing inspection shall operate a documented system which sets down the necessary actions to be taken to ensure that the requirements of this Standard are met. Inspection bodies and personnel shall declare any conflict of interest with bodies undertaking NDT or maintenance or repair. NOTE: In New Zealand, inspection may be undertaken by the owner only if the inspection body is accredited as a Type B or Type C accredited inspection body as set out in AS/NZS ISO/IEC 17020. The system should comply with the requirements of AS/NZS ISO/IEC 17020 or equivalent, and, as a minimum, comprise of the following: (a) A statement indicating commitment to the conditions of this Standard. (b) An organization chart, showing the reporting line of the inspection and/or integrity management function and demonstrating its independence from operations. (c) The identification and duties of staff involved in in-service inspection. COPYRIGHT Purchased By : Ms Renu Renu. Licensed to ARL Laboratory Services P/L on 7 July 2010. 1 user personal user licence only. Storage, distribution or use on network prohibited (10129524). AS/NZS 3788:2006 14 (d) Lines of communication to be followed on inspection and integrity matters including reporting procedures and interface points. (e) Where relevant, procedures for— (i) hazard categorization to AS 4343; (ii) inspection requirements for repairs, replacements and alterations for equipment not exempted by this Standard and/or the relevant regulatory requirements; (iii) shut-down, preservation and storage; (iv) commissioning and authorization for use; (v) on-line inspection and monitoring; (vi) periodic in-service inspections (internal and external), with acceptance criteria for each class of pressure equipment as per this Standard; (vii) repairs, overhauling, resetting and in-service inspection of all pressure relief safety devices; (viii) assessment of pressure equipment integrity; and (ix) failure analysis. (f) The maintenance and management of pressure equipment records and data, documentation and document flow. (g) Definition of other relevant (e.g. company) terms and descriptions relating to pressure equipment which fall outside this Standard or other Standards. (h) Internal and external auditing procedures and schedules to ensure compliance. 3.4 SUPPORT ORGANIZATIONS Internal or external organizations carrying out support activities such as design, design verification, testing, examining and measuring (e.g. non-destructive examination, mechanical tests and chemical analysis), assessment of fitness for service, maintenance and repair, or heat treatment shall comply with the appropriate specifications and Standards. COPYRIGHT Purchased By : Ms Renu Renu. Licensed to ARL Laboratory Services P/L on 7 July 2010. 1 user personal user licence only. Storage, distribution or use on network prohibited (10129524). 15 SECT ION 4 AS/NZS 3788:2006 PRESSURE EQU IPME NT I NSPECT I ON 4.1 GENERAL This Section sets out requirements for commissioning or recommissioning inspections, operational surveillance and periodic inspection of pressure equipment. Inspections referred to in this Section shall be scoped and executed by a suitably competent person. An in-service inspector, or person with equivalent qualifications and experience, shall certify or report that the inspections referred to in this Section have been carried out in accordance with this Standard, and that equipment is suitable for continued operation or otherwise. Competent persons shall be used to assess the fitness for service of pressure equipment. Table 4.1 sets out inspection intervals for pressure equipment. 4.2 COMMISSIONING OR RECOMMISSIONING INSPECTION Pressure equipment requiring inspection as per column 2 of Table 4.1 shall be inspected— (a) prior to being placed in service for the first time; (b) following repairs (excluding minor repairs) or alterations; (c) following a change of duty outside the design parameters which could affect safety; (d) following a relocation of static (i.e. non-‘transportable’) equipment; and (e) prior to a return to service after being mothballed or idle. The purpose of such inspection is to ensure that— (i) work has been properly executed; (ii) all necessary documentation has been completed; and (iii) the pressure equipment is safe to operate. Commissioning or re-commissioning inspections shall include, but not be limited to, the following: (A) Checking all necessary safety devices are fitted and operate correctly. (B) Supervision, witnessing or verification of pressure tests. (C) Checking that each item of pressure equipment is clearly identified by marking and or stampings, as required by Section 8 and as required by other relevant Standards, such as AS 1210. This identification shall, where appropriate, consist of a nameplate with a registered number (as issued by the relevant regulatory authority) and functional description and shall be prominently displayed and permanently fixed to the pressure equipment. (D) Updating existing pressure equipment files or setting up new files, as appropriate. (E) Establishing that all statutory and relevant Standard requirements for inspection during design, manufacture and installation have been completed and that evidence of the design identification (where required by regulations) is readily available. (F) Checking that the correct corrosion management system has been applied. (G) Checking that no extraneous material is left in the pressure equipment. COPYRIGHT Purchased By : Ms Renu Renu. Licensed to ARL Laboratory Services P/L on 7 July 2010. 1 user personal user licence only. Storage, distribution or use on network prohibited (10129524). AS/NZS 3788:2006 16 (H) Where appropriate, ensuring that the pressure equipment has been inspected. (I) For pressure equipment designed to operate in the temperature creep range, carrying out an accurate ‘base line’ dimensional check and metallurgical assessment for future reference. (J) Verifying that all operational and performance tests specified by the manufacturer and owner have been successfully completed. (K) Verifying, as far as practicable, the accuracy and completeness of the manufacturer’s data report (MDR) and piping fabrication and construction quality assurance documentation. Consideration should be given to checking original thickness measurements of new pressure equipment to obtain baseline data. Where there is a delay between installation and commissioning, there may be deterioration of the equipment which is inconsistent with the deterioration mechanisms and rates when in service, and this should be allowed for. 4.3 OPERATING SURVEILLANCE AND MONITORING Regular operational surveillance is an essential part of the operation of all pressure equipment to detect deterioration so that remedial action can be taken at an early stage. This shall be carried out by the person responsible for the operation of the pressure equipment and shall consist of periodic visual observation of pressure equipment and ancillaries. Operating conditions should be monitored to detect and record any significant change which may affect the integrity of the pressure equipment, see Clause 5.4.3. Any abnormality such as operation outside the limits of the design criteria, unusual odors or noise, and extremes of temperature or vibration shall be investigated and reported to the owner. NOTE: AS 3873 covers the operation and maintenance of pressure equipment. For some pressure equipment, an understanding of the corrosion mechanisms and rate of corrosion around the plant is paramount in order to maintain integrity. A variety of on-line inspection, monitoring techniques and/or devices may be required. Information gained by thickness testing, chemical sampling, radiography, thermal imaging, defect growth monitoring, metallurgical on-line analysis (replications), or corrosion rate monitoring using corrosion probes or coupons, should be combined as appropriate to achieve overall integrity management. On-line monitoring offers the potential of correlating process events (such as start ups) and process chemistry (iron count, pH, CO 2 content, etc.) with corrosion rate so that adjustment in operating parameters or addition of inhibitor may be made to modify shutdown intervals, maintenance scope or operational life. 4.4 PERIODIC INSPECTION 4.4.1 Basis and types of inspection 4.4.1.1 General Pressure equipment shall be periodically inspected to assist in assuring safe operation until the next scheduled inspection. These inspections shall assess the condition of the pressure equipment for integrity and its fitness for service until the next scheduled inspection at the design conditions and normal operational parameters. Inspection may be both internal and external and may include supplementary non-destructive techniques or pressure tests. Inspection may be performed when the pressure equipment is operating or depressurized. As a result of periodic inspection, a certificate or report of inspection shall be issued to the owner. COPYRIGHT Purchased By : Ms Renu Renu. Licensed to ARL Laboratory Services P/L on 7 July 2010. 1 user personal user licence only. Storage, distribution or use on network prohibited (10129524). 17 AS/NZS 3788:2006 4.4.1.2 External inspection An external inspection gathers information about the condition of external surfaces of pressure equipment and includes inspection of fittings, protective devices, protective coatings, insulation, bolting, supports, pressure equipment identification and attachments. The purpose of external inspection is to detect anomalies or defects such as corrosion, leaks, bulging, signs of excessive heat or cold, or signs of cracking. External inspection requires comprehensive visual inspection, which may be supplemented by non-destructive examination methods such as dye penetrant or magnetic particle inspection. Appendix D provides requirements and information on methods of inspection. Periodic external inspection and on-line non-destructive examination may be carried out while pressure equipment is in operation to obtain information for future maintenance or to save time when the plant is shut down. 4.4.1.3 Internal inspection An internal inspection gathers information about the condition of internal surfaces and usually requires confined space vessel entry or visual inspection using equipment such as boroscopes or video scopes. However, internal inspection may also be executed by appropriate non-intrusive means (e.g. ultrasonic or radiographic testing), where a high degree of confidence can be demonstrated in the reliability of such techniques. Care is needed to ensure that sampling is truly representative of the condition of equipment. Where practical internal inspection may be carried out whilst the equipment is operating. 4.4.2 Periodic inspection of pressure equipment Requirements for the periodic inspection of specific types of pressure equipment are given in the following appendices: (a) Heritage boilers and pressure vessels..................................................... Appendix Y. (b) Unfired pressure vessels: (i) Transportable vessels.....................................................................Appendix E. (ii) Vessels with quick actuating openings.......................................... Appendix Q. (iii) Deaerators..................................................................................... Appendix S. (iv) Drums for transport of liquefied gas............................................. Appendix W. (c) Buried or mounded vessels.................................................................... Appendix R. (d) Storage tanks..........................................................................................Appendix T. Guidelines for the periodic inspection of specific types of pressure equipment are given in the following appendices: (A) Boilers—General.................................................................................... Appendix F. (B) Unfired pressure vessels: (i) Stationary vessels......................................................................... Appendix G. (ii) Heat exchangers........................................................................... Appendix H. (C) Pressure piping........................................................................................Appendix I. (D) Fired heaters........................................................................................... Appendix J. (E) Pressure relief valves.............................................................................. Appendix P. (F) Structures...............................................................................................Appendix Z. NOTE: Typical check lists to assist in the inspection of pressure equipment are given in Appendix K. COPYRIGHT Purchased By : Ms Renu Renu. Licensed to ARL Laboratory Services P/L on 7 July 2010. 1 user personal user licence only. Storage, distribution or use on network prohibited (10129524). AS/NZS 3788:2006 18 4.4.3 First in-service inspection When indicated by Column 3 of Table 4.1, new pressure equipment shall be inspected internally and externally after its first year of service. The purpose of the first yearly inspection is to confirm the suitability of the design and materials used for the service conditions and to pick up any quality assurance defects that may have been either overlooked during fabrication or construction, or which may have developed or become significant during operation. The interval to the next inspection shall then be determined. Alternatively, the first in-service inspection may be deferred if it is determined safe to do so by using a Risk Based Inspection (RBI) process (refer also Clause 4.5 and Paragraph B5). The maximum interval between commissioning and the first in-service inspection shall be the nominal inspection interval given in Table 4.1. Any deferment shall be documented in a transparent and auditable manner. 4.4.4 Intervals for periodic inspection 4.4.4.1 Inspection intervals Inspection intervals are shown in Table 4.1. Inspection intervals may be varied by the in-service inspector, or persons with equivalent qualifications and experience, in consultation and agreement with all parties concerned. Requirements for determining shortened or extended inspection intervals are given in this Clause (4.4.4). For non-typical pressure equipment not identified in Table 4.1, the inspection interval shall be determined by a competent person, and agreed by the parties concerned. Nominal external inspection intervals are listed in Table 4.1, Column 4. Where external inspection intervals are extended in accordance with Clause 4.4.4.4, they shall not exceed the internal inspection interval (as determined using either Table 4.1 or RBI analysis). The internal inspection intervals listed in Table 4.1 are as follows: (a) Nominal interval The internal inspection intervals (Column 5) define nominal maximum inspection intervals based on industry experience. These intervals should be used only when operating experience or condition monitoring gives confidence that no significant deterioration will occur in that period. (b) Extended interval The intervals shown in Column 6 shall only be used after at least one ‘nominal interval’ inspection has been undertaken in addition to the first yearly inspection (if applicable) and assessment has clearly demonstrated that such extended intervals are safe. Such a change shall be justified and documented with respect to the correct operating parameters. Changes to these parameters should be preceded by review of the proposal with a competent person. Refer also to Clause 4.4.4.4. Operating with extended inspection intervals requires a formal process to be in place which advises changes to process conditions which impact on pressure equipment integrity, such as operating temperature, process fluid composition or process fluid velocity. The information justifying an extended inspection interval shall be documented by a competent person. An alternative to the inspection intervals listed in Table 4.1 is to use Risk Based Inspection (RBI, alternatively known as Risk Directed Inspection, RDI). RBI is discussed in Clause 4.5 and Appendix B. COPYRIGHT Purchased By : Ms Renu Renu. Licensed to ARL Laboratory Services P/L on 7 July 2010. 1 user personal user licence only. Storage, distribution or use on network prohibited (10129524). 19 AS/NZS 3788:2006 RBI may also be used to optimize the scope and extent of the inspection program for groups of pressure equipment of the same or equivalent design and materials which are installed in parallel, in series, or otherwise operated under similar process conditions and with similar process environments. An inspection program based on inspection of sample equipment selected from those at the site may be used if soundly based on competently applied risk based inspection techniques, and on adequate historical data regarding corrosion and other active causes of deterioration. 4.4.4.2 Wastage rate Where the observed wastage rate is the controlling factor for pressure equipment life, due to mechanisms such as corrosion or erosion, the maximum interval between inspections based on measured wastage rates shall typically not exceed half the calculated remaining life of the pressure equipment. Determination of the actual interval shall also take into account other time dependent mechanisms such as hydrogen attack, stress corrosion and fatigue, which may influence pressure equipment life. The adoption of a procedure to monitor the condition of a wasting vessel ensures that the frequency of inspection increases as the pressure equipment approaches the end of its service life. For example, where the calculated remaining life of a vessel is four years, the maximum inspection interval is 2 years. Following that inspection, if the calculated remaining life is now 2 years the maximum inspection interval is 1 year. The wastage rate and corrosion mechanism may be determined directly by thickness testing or visual inspection and measurement or indirectly by using corrosion probes or coupons. COPYRIGHT Purchased By : Ms Renu Renu. Licensed to ARL Laboratory Services P/L on 7 July 2010. 1 user personal user licence only. Storage, distribution or use on network prohibited (10129524). AS/NZS 3788:2006 20 TABLE 4.1 INSPECTION INTERVALS 1 Pressure equipment 1 2 3 4 Commissioning First yearly inspection inspection required? required? (see (see Clause 4.4.3) Clause 4.2) 6 Inspection interval, years External Internal inspection inspection Nominal Extended (see Notes 2 interval (see interval (see and 3 and Clause Clause 4.4.4.1) Clause 4.4.4.1) 4.4.4.1) BOILERS (see Note 12) 1.1 Electric boilers Y N 2 1.2 Coil-type forced circulation boilers Y N 2 1.3 All other boilers Y Y 1 2 STEAM PRESSURE VESSELS 2.1 Jacketed vessels pV ≤ 30 MPa.L N N pV > 30 MPa.L Y Y 2.2 5 4 8 (see Note 15) 1 4 (see Note 4) (See Note 14) 2 4 8 Other steam pressure vessels (see Appendix S for deaerators) pV ≤ 30 MPa.L N N (See Note 14) (See Note 14) 30 < pV ≤ 100 MPa.L Y N (See Note 14) (See Note 14) pV > 100 MPa.L Y Y pV ≤ 15 MPa.L N N pV > 15 MPa.L Y Y pV ≤ 100 MPa.L N N pV > 100 MPa.L Y Y 2 4 8 4 FIRED HEATERS OR CONVECTION BANKS Y Y 2 4 8 5 WATER HEATERS Y N 4 12 12 6 COMPRESSED AIR CONTAINING VESSELS pV ≤ 100 MPa.L N N (See Note 14) 100 < pV ≤ 150 MPa.L Y N (See Note 14) pV > 150 MPa.L Y N 2 4 12 3 VESSELS WITH QUICKACTUATING CLOSURES 3.1 Containing gases (including steam) 3.2 2 4 8 (See Note 14) 2 4 8 Containing liquids (See Note 14) 7 STATIC STORAGE VESSELS (see Notes 5 and 17) 7.1 Gases (non-corrosive condition) including above-ground LPG storage vessels Y N 2 10 12 7.2 Gases (other conditions) including anhydrous ammonia Y Y 2 2 4 8 STORAGE TANKS TO API 620 OR EQUIVALENT (See Appendix T) (continued) COPYRIGHT 21 AS/NZS 3788:2006 Purchased By : Ms Renu Renu. Licensed to ARL Laboratory Services P/L on 7 July 2010. 1 user personal user licence only. Storage, distribution or use on network prohibited (10129524). TABLE 4.1 (continued) 1 Pressure equipment 2 3 Commissioning First yearly inspection inspection required? required? (see (see Clause 4.4.3) Clause 4.2) 4 5 6 Inspection interval, years External Internal inspection inspection Nominal Extended (see Notes 2 interval (see interval (see and 3 and Clause Clause 4.4.4.1) Clause 4.4.4.1) 4.4.4.1) 9 PROCESS VESSELS (see Note 6) 9.1 Hazard Level A Y Y 2 4 8 9.2 Hazard Level B Y Y 2 4 12 9.3 Hazard Level C Y Y 2 4 12 9.4 Hazard Level D Y N 4 10 AUXILIARY VESSELS (see Note 7 and 17) 10.1 Accumulators N N 100 < pV ≤ 200 MPa.L Y N pV > 200 MPa.L Y Y 2 12 12 10.2 Other auxiliary vessels containing corrosive, toxic or flammable contents and except those covered Note 19. Y Y 2 4 12 10.3 Particular auxiliary vessels (See Note 19) Y Y (See Note 19) 11 REFRIGERATION AND AIRCONDITIONING VESSELS (see Note 13) 11.1 Group A1 refrigerants to AS/NZS 1677.1 pV ≤ 100 MPa. L N N (See Note 14) 100 < pV ≤ 200 MPa.L Y N (See Note 14) pV > 200 MPa.L Y Y 2 12 12 11.2 Groups A2, A3, B1 and B2 refrigerants to AS/NZS 1677.1 Y Y 2 12 12 12 STATIC LOW TEMPERATURE VESSELS (BELOW –10°C) (See Clause 4.12) 12.1 Insulated, non-vacuum, non-jacketed, non-toxic contents Y N (see Note 14) 4 12 12 12.2 Insulated non-vacuum, non-jacketed, toxic contents Y N 4 12 12 12.3 Vacuum insulated: pV ≤ 100 MPa.L 12.4 (a) inner vessel Y N (b) outer vessel Y N (See Note 14) (See Note 14) (See Note 14) (See Note 14) (see Clause 4.12.1) 4 (see Clause 4.12.1) Jacketed non-vacuum vessels: (a) inner vessel Y N (b) outer vessel Y N (see Clause 4.12.2) 4 (see Clause 4.12.2) (continued) COPYRIGHT AS/NZS 3788:2006 22 Purchased By : Ms Renu Renu. Licensed to ARL Laboratory Services P/L on 7 July 2010. 1 user personal user licence only. Storage, distribution or use on network prohibited (10129524). TABLE 4.1 (continued) 1 Pressure equipment 2 3 Commissioning First yearly inspection inspection required? required? (see (see Clause 4.4.3) Clause 4.2) Y 4 5 6 Inspection interval, years External Internal inspection inspection Nominal Extended (see Notes 2 interval (see interval (see and 3 and Clause Clause 4.4.4.1) Clause 4.4.4.1) 4.4.4.1) (see Paragraph D6.2.2 and Appendix R) In accordance with Table 4.1 for particular type of vessel 13 BURIED OR MOUNDED PRESSURE EQUIPMENT 14 PRESSURE PIPING (see Notes 20 and 21) 14.1 Hazard Level A Y Y 2 4 8 14.2 Hazard Level B or C confirmed to be in corrosive, vibrating or elevated temperature service after 1st yearly inspection Y Y 2 4 8 14.3 Hazard Level D piping (See Note 14); or Hazard Level B or C piping confirmed to be in non-corrosive, nonvibrating service and non-creep service after 1 st yearly inspection Y Y 8 15 TRANSPORTABLE VESSELS (see Appendix E and Notes 1, 8, 9, 10, 11, 16, and 17) 15.1 Service conditions 15.1.1 Cargo (Refer to AS 4343) 15.1.1.1 Lethal Y Y 1 2 2 15.1.1.2 Very harmful Y Y 1 5 5 15.1.1.3 Harmful Y Y 1 5 5 15.1.1.4 Non-harmful Y N 3 6 9 (a) Non-harmful powder discharge vessel. (Aluminium construction) Y N 2 2 4 (b) Non-harmful powder discharge vessel. (Steel construction) Y N 3 6 9 (c) Non-harmful powder discharge vessel. (Other material construction) Y Y 1 5 5 Y Y 1 6 6 15.1.2 Low-temperature ( 40 MPa(m) 1/2 may be used. This further assessment should also take into account the limits given in Figure O2(b). O6.6.2.5 Crack D Crack length = 5 mm Effective crack length = 5 + 25 = 30 mm Axial stress (σ L ) = pD 4t = 2.4 × 2000 4 × 24 = 50 MPa For critical size crack: KI = K IC KI = 1.1 σ L (πa c) 1/2 (see Figure O2(b)) = 1.1 × 50(πa c) 1/2 = 40 MPa(m)1/2 K IC COPYRIGHT Purchased By : Ms Renu Renu. Licensed to ARL Laboratory Services P/L on 7 July 2010. 1 user personal user licence only. Storage, distribution or use on network prohibited (10129524). AS/NZS 3788:2006 154 Therefore 1.1 × 50(πa c) 1/2 ac = = = = Critical crack length (ac) 40 0.17 m 170 m 170 mm Applying factor 2 (Paragraph O6.5), Allowable crack length = 85 mm Effective crack length = 30 mm Conclusion: Comparing this length against the actual effective length of 30 mm, we see that there is no concern. This example illustrates the importance of the location of a crack around a nozzle. Further note that this example referred to an opening without any reinforcement whatsoever. O6.6.2.6 Effect of design stress To further illustrate the relationship between stress and critical crack length, consider that the vessel investigated above was a higher design stress vessel operating at p = 4.80 MPa. Then the hoop stress (σ H ) = pD 2t = 4.8 × 2000 2 × 24 = 200 MPa The critical length of the crack at location A now becomes: KI = K IC KI = σ H (πa c ) 1/2 = 200(πa c)1/2 = 40 MPa(m)1/2 K IC Therefore 200(πa c)1/2 = 40 ac = 10 m = 20 mm Allowable crack length = 10 mm Actual crack length (2a) = 20 mm Critical crack length (2ac) Apply factor 2 (Paragraph O6.5), The critical crack is less than the length of the actual assumed crack. Therefore the crack is unacceptable unless further investigation shows that it is acceptable. For example, again reassess the conservative assumption that the actual crack is a through crack. Further, materials used for modern pressure vessels, particularly higher design stress vessels, have K IC values usually much higher than 40 MPa(m)1/2. Better data for K IC values may be ascertained from literature or actual test. O6.6.2.7 Crack growth due to fatigue at crack A To investigate how fast the crack will grow due to pressure cycling: COPYRIGHT Purchased By : Ms Renu Renu. Licensed to ARL Laboratory Services P/L on 7 July 2010. 1 user personal user licence only. Storage, distribution or use on network prohibited (10129524). 155 From Equation O6.4: da dN = AS/NZS 3788:2006 C(∆K I)M and consider crack at location A which is subject to higher stresses (hoop stress) than crack at location B. Where p = 0.4 MPa σ1 = pD 2t = 0.4 × 2000 2 × 24 = 16.7 MPa p = 2.4 MPa σ2 = pD 2t = 2.4 × 2000 2 × 24 = 100 MPa = (K I)2 − (K I)1 = σ 2 (πa c) 1/2 − σ 1(πa c) 1/2 = (πa c)1/2 (σ 2 − σ 1 ) = (π × 0.01) 1/2 (100 − 16.7) = 14.8 MPa(m) 1/2 when Now ∆K I From Paragraph O6.4, for carbon steel: C1 = 1.74 × 10−13 M = 5.95 da dN = C 1(∆K I)M (From Equation O6.4) = 1.74 × 10−13 (14.8)5.95 1.6 × 10 −6 m/cycle 1.6 × 10 −3 mm/cycle Thus the full crack, 2a, grows at a rate of 2 × 1.60 × 10−3 = 3.2 × 10−3 mm cycle. Therefore in two months the crack will grow 3.2 × 10−3 × 500 = 1.6 mm. Actual crack length would have grown from 2a = 2 × 10 or 20 mm to 21.6 mm approximately (i.e. less than the 10% recommended in Paragraph O6.4). This new length is used to determine further growth which will be at an accelerated rate. These growth rates and new crack sizes can be compared with the calculated maximum allowable crack length of 50 mm. COPYRIGHT Purchased By : Ms Renu Renu. Licensed to ARL Laboratory Services P/L on 7 July 2010. 1 user personal user licence only. Storage, distribution or use on network prohibited (10129524). AS/NZS 3788:2006 156 APPENDIX P PRESSURE RELIEF VALVES—SUPPLEMENTARY INFORMATION (Informative) P1 GENERAL Safety valves should be mounted with the spindle vertical and pointing upwards. Other spindle positions may be used if the installation complies with the valve manufacturer’s recommendations. Pressure relief devices are mounted with the spindle vertical to ensure true concentric alignment of the disc and seat/nozzle. If mounted horizontally, in larger valves the mass of the disc may cause it to slip against the seat/nozzle causing binding or leakage during operation. Pressure relief valves should be installed on full bore fittings to avoid restriction of flow. Single right-angled outlet valves are preferred because they pose less risk of injury to personnel operating the valves. Circumferentially vented relief valves tend to accumulate dust, debris and water through the vents onto the top of the disc, which may increase susceptibility to fouling and binding. It is recommended this type of valve be installed in a clean, undercover area, or with provision made to deflect dust, debris and water. Where appropriate, discharge vents should be designed to prevent ingress of foreign material and vermin. Where caps are used for sealing, these should be press-fitted into position, and should be easily ejected on discharge of the pressure relief device, so as not to cause injury to personnel or equipment. In cryogenic applications pressure relief valves are installed in piping between isolatable points. This is to allow the venting of expanding vapours. Periodic inspections should check such pressure relief valves for— (a) correct installation; (b) mechanical damage of coiled pigtail with poppet relief fitted; (c) mechanical damage of the coiled pig-tails; (d) tamper-proof sealing and mandatory markings. Icing up of vent valves may occur under conditions where insufficient ‘heat sink’ is achieved via multiple coils terminating at the vent valve. Valves should be tested at intervals not exceeding 5 years, as soft seats tend to harden and stick. A systematic approach to the management of pressure relief valves is useful to ensure equipment integrity. An example of a flowchart for relief or safety valve maintenance and testing is shown in Figure P1. All valves should be effectively packed to restrict shock and impact whilst in transit. All valves above 40 mm NB should be physically restrained in an upright position in a dedicated box or suitable lifting jig that may be manipulated by proprietary lifting equipment i.e. forklift, overhead crane, pallet lifter. Easing gear should be secured so as to prevent upsetting during transport and installation. The words ‘Ship upright’ should be clearly visible on all shipping containers and documentation. COPYRIGHT Purchased By : Ms Renu Renu. Licensed to ARL Laboratory Services P/L on 7 July 2010. 1 user personal user licence only. Storage, distribution or use on network prohibited (10129524). 157 Is PSV i n clean service AS/NZS 3788:2006 Ye s No Is th e re o p p o r tu n i t y to te st i n-s i tu Ye s No R e m ove a n d te s t Ins p e c t i nte r n a l l y fo r c o r ro s i o n, fo u l i n g, etc Te st i n-s i tu Does PSV pas s te st? Ye s No Does PSV re q u i re ove r h au l Ye s Eva l u ate o pti o ns fo r c o nti n u e d s e r v i c e No Is a l te r n ate p re s s u re re l i ef ava i l a b l e No Shut d ow n Ye s R e m ove PSV S tr i p d ow n, ove r h au l, re a s s e m b l e. C o n d u c t te st Ye s D o e s th i s PSV n e e d to b e re - i n s t a l l e d No D o e s PSV pas s te st? No Ye s Re insta ll PSV Wa s e q u i p m e nt s to p p e d? Ye s R e s t a r t e q u i p m e nt S et n ex t te s t d ate No R etu r n to s to c k Ca ptu re d at a FIGURE P1 TYPICAL PRESSURE RELIEF VALVE TEST PROCEDURE COPYRIGHT Purchased By : Ms Renu Renu. Licensed to ARL Laboratory Services P/L on 7 July 2010. 1 user personal user licence only. Storage, distribution or use on network prohibited (10129524). AS/NZS 3788:2006 158 P2 GUIDANCE ON TEST INTERVAL Typical test intervals for valves in different types of service are provided in Table P1. A typical maintenance report for pressure relief valves is shown in Figure P2. TABLE P1 TYPICAL TEST/OVERHAUL INTERVALS FOR PRESSURE RELIEF VALVES Commissioning inspection 1 st yearly inspection Typical interval for overhaul & bench test (years) Boilers Y Y 1 (see Note 1) Air receivers Y Y 5 Hydraulic accumulators Y N 5 (see Note 3) High vibration equipment e.g piston compressors Y Y 2 Steam systems Y Y 2 Corrosive systems Y Y 1 Inert gases Y Y 5 Vacuum e.g. deaerators, tanks Y Y 2 Petroleum (clean service) Y Y 5 Oil & tar (sticky service) Y Y 2 Ammonia Y Y 5 Chlorine Y Y 3 Cryogenic equipment Y Y 5 Water Y Y 2 Soft seated valves Y Y 3 Burst discs — — 2 (see Note 2) Fusible plugs Y Y — Application NOTES: 1 See AS 2593 for requirements for boiler safety valves. 2 Bursting discs should be replaced, rather than tested or overhauled. 3 Risk assessment should consider the types of loading (e.g. cyclic, shock, etc) placed on the accumulator due to normal hydraulic operation. COPYRIGHT 159 AS/NZS 3788:2006 Purchased By : Ms Renu Renu. Licensed to ARL Laboratory Services P/L on 7 July 2010. 1 user personal user licence only. Storage, distribution or use on network prohibited (10129524). SAFETY/RELIEF VALVE DATA VALVE CONDITION BEFORE DISMANTLING Valve No:................................................................. Equip. No:................................................................. Leaking (Yes) (No) Leaked too badly to (Yes) (No) pop Max. test pressure used................................ kPa Tightness after reseat (Yes) (No) Manufacturer:............................................................ Manufacturer’s Serial No:........................................... Model/Fig No:........................................................... Bonnet Type............................................................. Pressure began leaking................................ kPa Size..................... Inlet...................... Outlet..................... Initial pop pressure........................................ kPa Inlet Connection.................... Outlet connection................... Reseat pressure............................................. kPa Medium:............................... Class/table............................ Test gauge identification No:................................. Type of Valve: (Safety) (Relief) Test gauge recalibration due date:............................ Gagged: (Yes) (No) Bellows: (Yes) (No) Tested by.............................. Date........................ Reqd SHOP SET PRESSURE......................... kPa REASON FOR OVERHAUL Scheduled Failure Notice to owner Change set pressure Change service Did the valve lift? Inlet nozzle Outlet nozzle Disc seat Nozzle seat Stem Bellows Body Bonnet/bolts Cap Easing gear Body drain Protective Coating Spring (Yes) (No) (Yes) (No) (Yes) (No) (Yes) (No) (Yes) (No) (Yes) (No) VALVE CONDITION ON DISMANTLING (Tick appropriate box) Good Pitted Cracked Seized Blocked Scaled OD = ID= Wire Dia= Free Spring Length= Rate (Yes) Would the valve have protected equipment? REPAIRS CARRIED OUT (Yes) (No) (Yes) (No) (Yes) (No) (Yes) (No) (Yes) (No) (Yes) (No) Other parts....................................................................................................................................... Condition: (No) FINAL TEST DATA AFTER REPAIRS Machined nozzle seat: (Yes) (No) To manufacturer’s specifications (Yes)(No) If No, ID....................mm OD................ mm Machined disc seat: (Yes) (No) To manufacturer’s specifications (Yes)(No) If No, ID.................... mm OD................ mm Measuring tool calibration No: Measuring tool calibration due date............................. Replaced nozzle seat Replaced disc seat Lapped nozzle seat Lapped disc seat Replaced spring Replaced bellows No Turns Comments Body/nozzle seat test: (Yes) Nozzle Hydro test: (Yes) Spring identification No: (No) (No) Pres.............. kPa Pres.............. kPa Test medium (circle) Air Water Nitrogen On–line Final pop pressure............................................... kPa Final reseat pressure........................................... kPa Tightness after reseat (Yes) (No) Bubbles Per Min = Nozzle ring setting.................................................... Guide ring setting.................................................... Lead seal and servicing tag attached (Yes) (No) Test gauge identification No........................................ Test gauge recalibration due date................................ Final Test by.........................................Date............. Final Test witnessed by : FIGURE P2 TYPICAL MAINTENANCE REPORT—PRESSURE RELIEF VALVES COPYRIGHT Purchased By : Ms Renu Renu. Licensed to ARL Laboratory Services P/L on 7 July 2010. 1 user personal user licence only. Storage, distribution or use on network prohibited (10129524). AS/NZS 3788:2006 160 APPENDIX Q INSPECTION OF PRESSURE EQUIPMENT WITH QUICK-ACTUATING CLOSURES AND SWING BOLT DOORS (Normative) Q1 INSPECTION This Appendix applies to pressure equipment with quick-actuating closures and swing bolt doors within the pV limits set for Item 3 of Table 4.1. In addition to normal inspection activities for the relevant vessel service, the following additional inspection is necessary for vessels equipped with quick-actuating closures and swing bolt doors. Quick-actuating closures or swing bolt doors are provided on certain types of pressure equipment to facilitate loading and unloading of materials, products or goods which are being processed under pressure and elevated temperature, e.g. autoclaves, sterilizers and transportable vessels. There are different designs of locking mechanisms; some of the more commonly used can be classified as follows: (a) Interlocking lug-type door. (b) Expanding or contracting ring-type door. (c) Clamp-type door. (d) Cam-latch-type door. (e) Bar-locking-type door. (f) Swing-bolt-type door. AS 3873 provides details on the operation, maintenance and inspection of quick-actuating closures and swing bolt doors. Reference to that Standard by owner-users and inspection personnel is highly recommended. Q2 RECORDS Records of the inspection and test, maintenance, repair and operation activities shall be maintained and shall be available for review by inspection personnel. COPYRIGHT Purchased By : Ms Renu Renu. Licensed to ARL Laboratory Services P/L on 7 July 2010. 1 user personal user licence only. Storage, distribution or use on network prohibited (10129524). 161 AS/NZS 3788:2006 APPENDIX R INSPECTION OF BURIED OR MOUNDED PRESSURE VESSELS (Normative) R1 EXTERNAL INSPECTION OF PRESSURE VESSELS WITHOUT CATHODIC PROTECTION Every five years, the vessel shall be subjected to a 100% examination of the external surface. Ultrasonic thickness testing (UTT) mapping from within the vessel may be used as an alternative to external inspection. R2 EXTERNAL INSPECTION OF PRESSURE VESSELS WITH CATHODIC PROTECTION If vessels are installed to the requirements of AS/NZS 1596, (i.e. with 150 mm of inert sand, satisfactory protective coating, cathodic protection) and the protective system continues to perform satisfactorily, then the vessels shall be externally inspected every 25 years. If it is necessary to uncover the vessel for other reasons, then an external inspection shall be performed at this time. The integrity shall then be determined by uncovering the vessel and applying 10% visual examination. At this time, consideration shall be given to replacing the coating. Design of the cathodic protection system shall incorporate sufficient monitoring points (reference cells/corrosion probes and the like as appropriate) to ensure that the cathodic protection system covers the entire vessel surface. Routine testing of the cathodic protection system is to be carried out by a competent person. Minimum testing intervals shall be as follows: (a) (b) Impressed current system: (i) Monthly — Ensure that the system is operating. (ii) 6-monthly — Full potential check. Galvanic system: 6-monthly — Full potential check. Protection criteria shall be in accordance with AS 2832.2. If the cathodic protection system fails, it shall be reinstated as soon as possible. If the vessel is unprotected for a period longer than six months, then the vessel shall be treated as a vessel without cathodic protection. The inspection interval shall be set as 5 years from the last known time that the cathodic protection was functioning correctly. Ultrasonic thickness testing (UTT) mapping may be used as an alternative to external inspection. R3 RECORDS Records shall be maintained of all cathodic protection testing performed as well as the records required by Section 8 of this Standard. COPYRIGHT Purchased By : Ms Renu Renu. Licensed to ARL Laboratory Services P/L on 7 July 2010. 1 user personal user licence only. Storage, distribution or use on network prohibited (10129524). AS/NZS 3788:2006 162 APPENDIX S INSPECTION OF DEAERATORS (Normative) S1 GENERAL Deaerators may suffer corrosion fatigue and this may be associated with stress induced corrosion. Generally, cracks initiate on the inside surface at welds, heat-affected zones or corrosion pits. High local stresses may result from use of— (a) the equivalent of Class 1 or 1H vessels; (b) higher strength steels, e.g. Grade 490 MPa or higher; (c) large diameters where external loads induce significant bending stresses; (d) design and operating procedures which result in thermal stress; (e) local stress concentrations on the inside surface resulting from internal or external attachments or poor quality welds; or (f) non-stress relieved welded joints. Fluctuations in flow and water level, vibration, water hammer and startups and shutdowns provide cyclic stresses sufficient to fracture magnetite scale and expose fresh metal to corrosion and further cracking. Water chemistry appears to contribute especially where oxygen and chlorides are high. In some cases, stress corrosion cracking has been the mechanism of cracking, resulting from caustic carry over in condensation return and high local stress. S2 INSPECTION AND REPAIR All internal surfaces at significant stress concentrations, e.g. welds and pitting particularly in near supports, attachments and openings or areas of high bending stress, should be subject to magnetic particle examination, after approximately five to eight years service. High quality surface preparation, e.g. grit blasting, is essential. Wet fluorescent magnetic particle examination (AC yoke) is preferred. If cracking is not detected, inspections should be repeated at approximately four-yearly intervals. Longer intervals may be used when two or more sequential inspections have not detected cracking and stress concentrations are considered small. If cracks are detected, they shall be removed. Cracks less than 10% of the wall thickness may be dressed smooth. Larger cracks shall be repaired by welding and dressing. Other welds which are similar to repaired welds, both in surface and position, should be dressed smooth—not necessarily flush. After weld repairs, magnetic particle inspection shall be used to check the vessel integrity. Post weld heat treatment to reduce residual welding stresses or the use of protective coatings may be beneficial. Weld repairs should be rechecked after one to two years of operation. As an alternative to repair by welding, the design pressure of the vessel may be derated and fracture mechanics used to prove the vessel is safe. Cracks should be monitored, if necessary, by external angle probe ultrasonics. COPYRIGHT Purchased By : Ms Renu Renu. Licensed to ARL Laboratory Services P/L on 7 July 2010. 1 user personal user licence only. Storage, distribution or use on network prohibited (10129524). 163 AS/NZS 3788:2006 APPENDIX T INSPECTION OF STORAGE TANKS TO API 620 OR EQUIVALENT (Normative) T1 SCOPE This Appendix applies to large low pressure storage tanks such as tanks complying with API 620 or equivalent and falling above the curves for— (a) ‘Vessels subject to internal pressure’; and (b) ‘Vessels subject to external pressure’ in the relevant section of AS 1210. T2 AMBIENT TEMPERATURE AND HEATED TANKS Tanks which normally operate at a temperature warmer than −10°C shall be internally and externally inspected in accordance with the Table of AS 1940 regarding the tank inspection schedule for Category 6 tanks. NOTE: The Australian Institute of Petroleum (AIP), has developed an industry code of practice, CP 16. Reference should also be made to API 653. T3 LOW TEMPERATURE STORAGE TANKS (tanks normally operating below −10°C) T3.1 Internal inspection of low temperature storage tanks A common use of API 620 Tanks is for the bulk storage of liquefied refrigerated gases, such as LNG, LP Gas and ammonia. Because of potential damage mechanisms which can occur if these tanks are brought out of service (e.g. due to the thermal stress cycling and the possible introduction of corrosive contaminants or corrosive mechanisms, such as stress corrosion), it is good practice to avoid internally inspecting them during their lifetime. Due to the operational temperatures involved, low temperature storage tanks are not usually subject to the risk of internal corrosion during normal operation. These tanks are therefore generally only internally inspected if there is some specific concern that damage may have occurred based on external inspections or operational monitoring. If a tank is brought out of service for other reasons, consideration shall be given to internally inspecting the tank at that time. To establish the acceptability of delaying the internal inspection of low temperature storage tanks (for a long interval or indefinitely) a detailed review of the specific factors associated with each tank shall be performed. The review shall consider the following factors: (a) Product characteristic History of product storage behaviour, particularly identified internal corrosion mechanisms. (b) Tank design The following Items related to tank design shall be considered: (i) Containment integrity—current best practice is to design these tanks with double or full containment systems to contain the liquid and liquid/vapour, respectively, in the event of tank leakage. (ii) Material toughness—the low temperature properties of the tank shell shall ensure a leak-before-break design demonstrated by a fracture mechanics assessment. COPYRIGHT Purchased By : Ms Renu Renu. Licensed to ARL Laboratory Services P/L on 7 July 2010. 1 user personal user licence only. Storage, distribution or use on network prohibited (10129524). AS/NZS 3788:2006 164 (c) Construction inspection and quality control (d) Operational history The following items related to operational history shall be considered: (i) Product purity (i.e. potential for corrosive contaminants). (ii) Metal temperature (areas of higher temperature (e.g. greater than −10°C) can be subject to corrosion). (iii) Number of fill-empty cycles (tanks subject to greater than 7000 cycles shall be given particular attention). (iv) Number of significant thermal cycles. (v) Abnormal loads—seismic, over-pressure (e.g. due to a malfunctioning relief valve or ‘roll over’ phenomena). (vi) Operational monitoring and checking (relief valve overhauls, instrumentation calibration/checking, on-line recording/monitoring of bund gas space and underfloor temperature). (vii) External environment—(e.g. effect of marine environment and effect of testing of the fire deluge systems). (e) External on-line inspection (Refer to Paragraph T3.2.) (f) Other risk, hazard factors or hazard levels The following factors shall be considered: (i) Location of tank relative to other plant, personnel, residential areas or public space. (ii) Emergency system and other mitigating features. (iii) Toxicity, volatility and flammability of product. It is anticipated that a low temperature storage tank designed, constructed and operated in accordance with current best practice could be assigned a continuous 20-year operational interval without an internal inspection based on satisfactory findings from the above review. If adverse evidence comes to light relating to specific product behaviour during the operational life of the tank, this interval should be reviewed. Further extensions beyond 20 years may be considered following an additional review of the above listed factors and world best practice current at that time. In the event that a potential internal damage mechanism is identified which requires investigation on a particular tank, inspection methods which do not require tank decommissioning may be considered, e.g. acoustic emission testing during a normal filling cycle. T3.2 External inspection of low temperature storage tanks The interval and extent of inspections of low temperature storage tanks shall be as for ambient temperature tanks (see Paragraph T2) with the additional specific requirements listed in Table T1. COPYRIGHT 165 AS/NZS 3788:2006 Purchased By : Ms Renu Renu. Licensed to ARL Laboratory Services P/L on 7 July 2010. 1 user personal user licence only. Storage, distribution or use on network prohibited (10129524). TABLE T1 TANK INSPECTION SCHEDULE FOR LOW TEMPERATURE TANKS Part of tank Type of inspection Purpose Interval Interspace (of double wall or double containment tanks) Gas sampling To check for product leakage 1 month Insulation system Cold patch observation (visual or using thermography) To check for insulation breakdown and moisture ingress 1 year Visual check of vapour barrier and cladding 1 year Bottom heating facilities Operational check To avoid ‘frost heave’ Tank settlement Visual and survey To check for tank distortion and foundation movement 1 year Anchorage Where required; visual check of bolts, straps and floor clearance with tank at low level. To check for moisture ingress 1 year Tanks external surface Where required; removal of insulation patches and visual check of external tank surface particularly above the liquid level To check for external corrosion in warmer tank parts 1 year Maintenance check 1 week 1 year COPYRIGHT Purchased By : Ms Renu Renu. Licensed to ARL Laboratory Services P/L on 7 July 2010. 1 user personal user licence only. Storage, distribution or use on network prohibited (10129524). AS/NZS 3788:2006 166 APPENDIX U REMAINING LIFE ASSESSMENT (Informative) U1 BACKGROUND Pressure equipment may have a finite life that depends on the inherent limitations of materials, the amount of conservatism used in design and the nature of operation. A cost effective alternative to plant replacement is remaining life assessment, which if carried out conservatively, has the potential to allow plant to be run safely beyond the original design life. Life assessment is used to determine the operating time (remaining life) for the equipment to reach an unsafe condition, based on progressive degradation during operation. The aim of assessment of remaining life is to determine the amount of conservatism embodied in the original design life and calculate the actual remaining life based on actual rather than design operating parameters. The information in this Appendix is intended to provide an overview of a life assessment methodology that would allow a pressure equipment user to obtain an estimate of pressure equipment remaining life. The testing and analysis methods described in this Appendix often require specialist knowledge. Careful consideration needs to be given to ensuring that the persons undertaking the life assessment are suitably competent and that they have access to the appropriate reference data and resources. Paragraph U6 provides an example of a life assessment for an item of pressure equipment operating in the creep range. This example aims to provide an understanding of the generic steps involved in life assessment. Whilst the underlying damage mechanisms are relatively few, the particular requirements for a life assessment of any one item of pressure equipment may require consideration of significant additional constraints. A suitably competent person will be aware of the methods used to address these constraints and to provide a robust analysis. U2 FACTORS AFFECTING REMAINING LIFE Many metallurgical and operational factors can extend the actual life beyond the design life. To enable rational run, repair or replace decision-making, sufficient information is required, so that the assessment of plant life can be progressively undertaken with increasing detail as retiring dates are approached. Factors that may result in an actual life being greater than the design life include: (a) Built-in safety factors in the original design. (b) Materials property data (i) Invariably subject to scatter, resulting in a broad band of behaviour. Designs are generally based on minimum or mean values of mechanical properties. (ii) Conservatism in the manner in which reference materials data was obtained. This can result in conservatism in design. For example, in the case of the determination of creep rupture properties, extrapolation of short term data or testing of small specimens in air results in conservative estimates of long term creep strength. Factors that may lead to the premature failure of pressure equipment often include: (A) Operating stresses that exceed the design stresses as a result of unanticipated residual stresses, system stresses and local stress concentrations. COPYRIGHT Purchased By : Ms Renu Renu. Licensed to ARL Laboratory Services P/L on 7 July 2010. 1 user personal user licence only. Storage, distribution or use on network prohibited (10129524). 167 AS/NZS 3788:2006 (B) Operating temperatures that exceed design temperatures, for either long or short duration. (C) Start up and shut down stresses that are not anticipated and which cause additional fatigue damage. (D) Environmental effects that result in corrosion rates in excess of the corrosion anticipated. (E) In-service deterioration of materials due embrittlement or unexpected creep damage). to microstructural changes (e.g. U3 THREE STAGE REMAINING LIFE ASSESSMENT U3.1 General Remaining life assessment consists of identifying the active and potentially active damage mechanisms, and requires information on— (a) the degree of damage that has occurred to date; (b) the ongoing rate of damage accumulation; and (c) the degree of damage to cause failure. A ‘cost effective’ three-stage remaining life assessment process is shown in Figure U1. The logic diagram indicates transition points from one assessment stage to the next. Such an approach will ensure the best chance of avoiding a major unscheduled outage or an accident and may well give information to assist more efficient plant operation. The information from each stage feeds into the next. Each successive stage is more comprehensive and less conservative, providing a remaining life estimate closer to the actual remaining life. Progressively greater cost is involved in successive assessment stages and therefore each stage is performed only as required. Prediction of remaining life may be sensitive to the accuracy of the data used in the life estimate. For example in the case of creep life assessment: (i) Errors as little as 10°C in the assumed temperature can lead to an error of −50% to +100% in calculated life. (ii) Error in the assumed pressure (and hence pressure stress) of 5% can result in errors of ± 35% in calculated life. (iii) Uncertainty in the assumed materials behaviour can change life estimates by one order of magnitude. If records are inadequate, or damage mechanisms are not understood, or the component has operated outside design parameters, or the remaining life is less than that required before replacement of the equipment is possible, the next stage of assessment is used. The data requirements of the three stages are shown in Table U1. In broad terms the stages are as described below. U3.2 Stage 1—Review of remaining life—design based Stage 1 employs simple stress analysis as given in the design standards (e.g. circumferential stress calculations) and uses design operational parameters. Stage 1 systematically identifies the critical components which may require remaining life analysis. Experience is a valuable input into remaining life assessment and before a critical component reaches the end of the design life, advice may be sought from the original equipment designer or 3rd party expert regarding the extent and location of non-destructive inspection required towards the end of the design life. The original equipment designer may also be able to provide data on the extent of conservation embodied in the original design. COPYRIGHT Purchased By : Ms Renu Renu. Licensed to ARL Laboratory Services P/L on 7 July 2010. 1 user personal user licence only. Storage, distribution or use on network prohibited (10129524). AS/NZS 3788:2006 168 Stage 1 life assessment involves— (a) review of design calculations or reassessment of components in respect of service life, temperature and cyclic loads, using applicable pressure equipment Standards; and (b) review of experience with other similar or related pressure equipment. A simple alternative approach to determine when equipment needs replacing involves tracking maintenance and failure rates over time and noting the point when this rate becomes economically unacceptable. U3.3 Stage 2—Review of remaining life—operational data and history based Stage 2 refines the life assessment by using actual operational data such as temperatures and pressures obtained from either existing installed instruments or from test sensors installed on the equipment. Stage 2 is supplemented by conventional inspection data such as that defined by this Standard, and by analytical stress calculations. Stage 2 life assessment typically involves the following: (A) Non-destructive or visual examination. Note that conventional NDT techniques often fail to detect incipient creep damage and microstructural damage which can be the precursors to rapid, unanticipated failures. (B) Measurement or review of current actual temperatures and strains and of known specific defects. (C) Review or estimation of pressure and temperature history, to allow assessment of the effect of design/service temperature differences and external forces. (D) Measurement of important geometric features, including wall thickness and out of roundness. (E) Review of inspection, maintenance, repair or replacement records. (F) Surface micro-examination by direct or replica methods. (G) Review of the manufacturing data reports to identify actual material properties and chemical composition. U3.4 Stage 3—Review of remaining life—testing and inspection based Stage 3 makes extensive use of more sophisticated inspection data such as replication and mechanical test data, and is supplemented by data gained from monitoring (e.g. thermocouple or strain gauging or vibration monitoring). Stage 3 may require sophisticated stress analysis (e.g. finite element method) and perhaps accelerated creep testing or fracture toughness testing. Stage 3 life assessment typically involves the following: (a) Mechanical testing and metallurgical examination of samples removed from service. Testing may include accelerated creep testing and fracture toughness testing. (b) Other special tests, e.g. accelerated corrosion or erosion. (b) Assessment using detailed stress information, e.g. strain gauging and finite element analysis. COPYRIGHT Purchased By : Ms Renu Renu. Licensed to ARL Laboratory Services P/L on 7 July 2010. 1 user personal user licence only. Storage, distribution or use on network prohibited (10129524). 169 AS/NZS 3788:2006 0.6 x D e s i g n l i fe or i f n o d e s i g n l i fe ava i l a b l e S tag e 1 Ca l c u l ati o n of l owe st tot a l l i fe 1 ( T L1- C re e p, T L1- Fati g u e, T L1-Wa s t a g e, T L1- C o m m o n) S tag e 1 Ca l c u l ati o n Is re m a i n i n g l i fe g re ate r th a n d e s i re d l i fe? Ye s RUN Ins p e c t at 0.6 x tota l l i fe 1, th e n at 0.75 x tot a l l i fe 1, o r i n ac c o rd a n c e w i th AS/ N ZS 378 8 (w h i c h eve r i s s m a