Advanced Ceramics Homework Exam Study PDF
Document Details
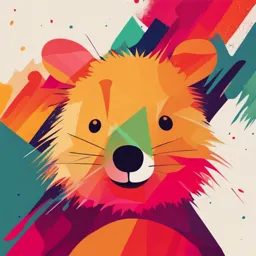
Uploaded by ReliableFoxglove6177
Tags
Summary
This document provides a study method on the advanced topic of ceramic matrix composites (CMCs). It covers the materials and composition of CMCs, along with applications including aerospace, automotive, and defense. The document is a study guide, rather than an exam paper.
Full Transcript
Advanced Ceramics Homework-Exam Method Study Ceramic Matrix Composites (CMCs) CMCs are a significant advancement in materials science and engineering because they combine the remarkable characteristics of ceramics with the strength and toughness of fiber. They aim to combine the benefits of cerami...
Advanced Ceramics Homework-Exam Method Study Ceramic Matrix Composites (CMCs) CMCs are a significant advancement in materials science and engineering because they combine the remarkable characteristics of ceramics with the strength and toughness of fiber. They aim to combine the benefits of ceramics (high-temperature stability, hardness) with enhanced toughness and damage resistance. CMCs are renowned for their ability to tolerate extremely high temperatures and corrosion, and their lightweight and robust chemical stability, which means that they do not react with other chemicals or materials. CMCs are used in applications where high thermal resistance, wear resistance, and lightweight properties are essential, such as in aerospace, automotive, and power generation. Composition of CMCs - Matrix Material In CMCs, the matrix material is often a ceramic compound that provides structural integrity and protects the reinforcement material. Oxide matrix materials: aluminum oxide (alumina), aluminosilicate (mullite), zirconium oxide (zirconia), and yttria-stabilized zirconia (YSZ). Non-oxide matrix materials: Carbon matrix (C), SiC, silicon nitride (Si3N4), zirconium carbide (ZrC), boron nitride (BN), and aluminum nitride (AlN). - Reinforcement Material The reinforcement material in LCMCs (Lightweight Ceramic Matrix Composites) gives the composite strength and rigidity. Fibers, whiskers, or particles are common forms of these materials. Common reinforcement materials used in LCMCs are continuous fibers, discontinuous fibers and particles. - Interface Material In CMCs, the interphase material links the matrix and reinforcement, enhancing interface adhesion and effectively transferring stress. CMCs, primarily SiC fiber/SiC matrix composites containing either carbon (C) or BN interphases, have been shown to have exceptional characteristics. Classification of CMCs A C/SiC CMC is a SiC matrix and C fibers. CMCs can be categorized based on the nature of the matrix material such as oxide CMC and non-oxide CMC. - Oxide Ceramic Matrix Composites (O-CMC): They often combine ceramic fibers with ceramic matrices, specifically utilizing an oxide matrix. O-CMC enables various applications with severe thermal and mechanical requirements because it combines high-temperature stability, low density, high strength and superior corrosion resistance with a damage tolerant quasi-ductile fracture behavior. - Non-Oxide Ceramic Matrix Composites: They contain a non-oxide base CMC and a filler or reinforcement (ceramic, metallic, polymer, plastic, etc.). Technical ceramics with covalent bonds, such as conductive carbides and non-conductive nitrides, comprise non-oxide CMCs. Even though the components of non-oxide CMCs are incredibly brittle, their composition allows for excellent durability. Non-oxides have a low resistance to oxidation and corrosion when exposed to high temperatures. Combinations of non- oxide CMCs exhibit diverse material qualities and demand specific manufacturing techniques, restricting their applicability to various sectors. Based on the existing literature, non-oxide CMCs emerge as the predominant choice for high-temperature applications. Application Areas Aerospace: CMCs are used in advanced aerospace applications such as hypersonic flight vehicles, spacecraft re-entry thermal protection systems, and turbine engine components. The primary properties of CMCs required for aerospace applications include a reduced density, extreme temperature strength, hardness, superior performance-to-weight ratio, refractoriness, excellent insulating properties, energy collection, and reduced thermal conductance. Fiber-reinforced CMCs (FRCMC) of C/SiC, SiC/SiC, and various other composite manufactured with CVI have been extensively used in aviation and aerospace applications due to their resistance to exceptional temperatures, higher treating point (>1400 C), and strong mechanical properties, as well as toughness and excellent corrosion resistance (turbine blades, thermal protection systems) Automotive: CMC products must have vital attributes connected to the automotive sector, such as superior strength, high resistance to wear, reduced CTE, refractoriness, self-lubrication characteristics, excellent insulation, energy storage, and high conductivity to heat. CMCs used in automotive and industrial parts include turbines for gas thermal engines, powertrain elements, converters for catalytic reduction, turbocharging systems, fixed barrier recuperators, gaskets for water pumps, and lower heat dissipation diesel. (brake disks, exhaust systems) Defence: Defense components must have several essential characteristics, including low weight, high specific strength, excellent fracture resilience, high wear resistance, and high heat conductivity. Tank power trains, enhanced armor, propeller systems, ground-based support vehicles, elements of fuel injectors, armed forces weaponry, combat aircraft, submarine shaft seals, and tear-resistant accurate bearings are just a few examples of CMC parts used in the defense industry. Nuclear: To use CMCs in the nuclear industry, materials must have extreme temperature strength and excellent mechanical, chemical, thermal and radiation properties. SiCf/SiC composites are emerging as promising materials for application in the nuclear industry. These composites exhibit remarkable properties such as extreme temperature strength, resistance to fracture, creep, corrosion and thermal shock. Within the nuclear sector, various components of CMC application include nuclear fuel cladding for nuclear fuel, control materials, materials for moderation and components for reactor containment. Raw Materials Reinforcement Fibers: 1. Silicon Carbide Fibers: They provide high strength, thermal conductivity and excellent corrosion resistance. Cost: $200–$400/kg Suppliers: SGL Carbon (Germany), UBE Industries (Japan), Nippon Carbon (Japan) 2. Oxide Fibers (Alumina, Zirconia): They provide high resistance to oxidation and corrosion, and they are also suitable for oxidative environments. Cost: $150–$300/kg Suppliers: 3M (USA), Goodfellow (UK) 3. Carbon Fibers: They are lightweight and suitable for high-temperature non- oxidative environments. Cost: $20–$60/kg for standard grades Suppliers: Toray Industries (Japan), Hexcel (USA) Alternative fibers: Natural fibers (e.g. basalt) or hybrid reinforcements for cost-sensitive applications. Matrix Precursors: 1. Polymer Precursors: Polysilazanes, polycarbosilanes, and other polymer-based systems pyrolyze into SiC or other ceramics. Cost: $50–$200/kg Suppliers: Starfire Systems (USA), Silaprene GmbH (Germany) 2. Powdered Ceramic Matrices: Fine powders of SiC, alumina, or zirconia are used in techniques like sintering or hot pressing. Cost: $10–$50/kg Suppliers: Saint-Gobain (France), Washington Mills (USA) Alternatives: Sol-gel systems which provide lower cost and easy infiltration. Binders and Additives: 1. Organic Binders: To enhance initial green body strength. 2. Additives: To improve mechanical and thermal properties. Boron or carbon nanotubes can be used. Cost: $10–$100/kg Suppliers: Cabot Corporation (USA), Showa Denko (Japan) Production Methods 1. Precursor Infiltration and Pyrolysis (PIP): PIP is a technique for creating CMCs that involves introducing a low-viscosity polymer into a fabric-like ceramic reinforcement, which is then heated in an oxygen-free environment until the polymer breaks down and turns into a ceramic. - Fiber preform is prepared and then the preform is infiltrated with a liquid polymer precursor. Pyrolysis at 1000-1500 °C under an inert atmosphere converts the polymer to ceramics like SiC. Repeated cycles improve density and reduce porosity. - Advantages include formation of ceramic matrices at comparatively low temperatures, thereby mitigating fiber damage, precise control over the microstructure and composition of the ceramic matrix. - Presence of residual porosity within the matrix microstructure (impacts the mechanical properties of the composite) and lengthy fabrication times due to the multiple infiltration and pyrolysis cycles are some of the disadvantages. 2. Chemical Vapor Infiltration (CVI): The interphase and matrix are progressively deposited from gaseous precursors inside the pore network of a fiber performed during CVI. - This time a preform is placed in a reactor. Gaseous precursors (like e.g., SiCl₄ + CH₄ for SiC) are introduced under controlled pressure and temperature. The matrix forms through chemical reactions and deposits within the preform. - Advantages: The matrices exhibit high purity and good thermal shock resistance, the matrices display favourable creep and oxidation resistance at elevated temperatures (1400 °C), The matrices demonstrate excellent mechanical properties, including strength, elongation and toughness. - Disadvantages: The process duration is extended, often spanning several weeks. The capital and production costs associated with the method are considerable. The residual porosity levels are relatively high. 3. Slurry Infiltration and Sintering: A slurry is a mixture of ceramic particles suspended in a liquid carrier that may also include fillers and wetting agents. A slurry percolates into a porous reinforcing preform while creating ceramic matrix composites using the slurry infiltration technique. Capillary forces are what propel the infiltration process. The preform is dried and heat-pressed to create a CMC when the infiltration process is complete. - A slurry is prepared of ceramic powders (like SiC) in a liquid medium, and then the fiber preform is infiltrated with the slurry. Finally, drying and sintering at temperatures between 1200–1800°C is applied. - Advantages: The resulting CMC demonstrates relatively low porosity and exhibits commendable mechnical properties. - Disadvantages: Hot pressing operations entail high pressures and it poses a risk of fiber damage. Hot pressing necessitates costly equipment and the fabrication of large and intricate shapes proves challenging. Required Equipment 1. Fiber Preparation Equipment: Its purpose is to produce and treat the reinforcement fibers (e.g., SiC, carbon, or oxide fibers) before incorporation into the matrix. Fiber Spinning and Coating Machine: Used for producing and coating fibers with materials like carbon or boron nitride to enhance compatibility with the matrix. Approx. Cost: $50,000–$150,000. Supplier: Tsubaki Nakashima (Japan), Harper International (USA) 2. Impregnation and Infiltration Systems: To introduce matrix precursors into the fiber preform. Autoclaves: Used for polymer impregnation under pressure and controlled temperatures. Approximate Cost: $100,000–$500,000. Suppliers: ASC Process Systems (USA), Taricco Corporation (USA). Chemical Vapor Infiltration (CVI) Reactors: Used for gaseous precursor infiltration into porous preforms. Approximate Cost: $500,000–$2,000,000. Suppliers: Mersen (France), PVA TePla (Germany). 3. Pyrolysis Furnaces: To convert polymer precursors into a ceramic matrix by pyrolysis. High-Temperature Furnaces: Operate in an inert atmosphere up to 1500°C. Approximate Cost: $50,000–$200,000. Suppliers: Carbolite Gero (UK), L&L Special Furnace Co. (USA). 4. Sintering and Hot-Pressing Equipment: To densify the ceramic matrix and reduce porosity. Hot Presses: Combine heat and pressure to densify composites. Approximate Cost: $200,000–$800,000. Suppliers: FCT Systeme (Germany), Thermal Technology LLC (USA). Vacuum Sintering Furnaces: Used for sintering in controlled environments. Approximate Cost: $100,000–$300,000. Suppliers: ECM Technologies (France), Ipsen (Germany). Detailed Production Steps 1. Raw Material Preparation: Crushing, milling, and drying raw materials. 2. Fiber Preform Fabrication: Aim is to create a structural framework for the composite, providing reinforcement. Firstly, the selection of fibers is made, this is made depending on the application. And then, the preforms are created in desired shapes using weaving, braiding or filament winding techniques. Lastly, coating is applied to improve fiber- matrix bonding and prevent crack propagation. 3. Matrix Infiltration: It is for filling the voids in the fiber preform with a ceramic matrix. This step can be done using a variety of methods such as polymer impregnation and pyrolysis (PIP), chemical vapor infiltration (CVI) or slurry infiltration. 4. Sintering or Heat Treatment: To densify the composite and enhance the bonding between the matrix and fibres. 5. Machining and Finishing: Done in order to achieve final dimensions and surface finish. 6. Quality Control and Testing: To ensure the product meets mechanical, thermal and structural requirements. Non-destructive testing methods such as ultrasonic testing or mechanical testing can be applied. Engineering Characteristics High-Temperature Stability: Can operate at temperatures between 1000 - 1700°C, depending on the matrix material. Lightweight: The density of CMCs is typically in the range of 2.5–3.0 g/cm³, which is significantly lower than the traditional metals like steel or even titanium alloys. This makes them suitable for applications where weight reduction is required. High Toughness: Fiber reinforcement significantly increases the toughness compared to traditional ceramics, allowing CMCs to endure higher mechanical loads and resist brittle fracture. Oxidation and Corrosion Resistance: Oxide-based CMCs and SiC/SiC CMCs resist oxidation and chemical attack. Thermal Shock Resistance: Unlike monolithic ceramics which can crack under rapid temperature changes, CMCs exhibit high resistance to thermal shock due to their fiber reinforcement. Fatigue Resistance: CMCs maintain mechanical integrity under cyclic loading at elevated temperatures, which is a critical characteristic for components like turbine blades. Engineering SWOT Analysis Strengths 1. High Strength-to-Weight Ratio: Excellent performance in applications requiring low weight such as aerospace and automotive. 2. Thermal Stability: Can operate effectively in temperatures exceeding 1200°C. 3. Thermal Shock Resistance: Can handle sudden and rapid changes in temperatures. 4. Oxidation and Corrosion Resistance: Can be utilized in harsh environments such as space or in other industrial environments. Weaknesses 1. High Cost: Expensive raw materials such as SiC fibers and manufacturing techniques such as CVI and PIP. 2. Complex Manufacturing: Increases the time and the cost with multi-step processes (fiber preform preparation, matrix infiltration, densification). 3. Limited Repairability: Damage to CMCs is difficult to mend compared to metals, which can be welded or reshaped. Opportunities 1. Growing Aerospace Industry: The demand for lightweight and heat-resistant materials for next-gen aircraft and spacecraft. 2. Defence Applications: Increasing interest in hypersonic missiles and thermal protection systems. 3. Advancements in Manufacturing: Possibility to lower the costs with emerging techniques such as automated fiber placement (AFP) and 3D printing. Threats 1. Supply Chain Risks: Dependence on specific high-cost materials (SiC) with limited suppliers globally. 2. Competition with Other Materials: Metal Matrix Composites (MMCs) and advanced alloys offer alternatives in some applications. Global Economic Outlook The global ceramic matrix composites market size was estimated at USD 3.40 billion in 2022 and is expected to grow at a compounded annual growth rate (CAGR) of 12.8% from 2023 to 2030. High-temperature stability in addition to reduced weight and high strength is expected to propel the growth. Major markets: North America (U.S., Canada), Europe (Germany, U.K., Italy, France), and Asia- Pacific (China, Japan, South Korea). Some prominent players in the global ceramic matrix composites market include: 3M Company COI Ceramics, Inc. Coorstek, Inc. General Electric Company Kyocera Corporation Lancer Systems LP SGL Carbon Company Ultramet, Inc. Ube Industries, Ltd. Ultra-High Temperature Ceramics (UHTCs) Ultra-high temperature ceramics (UHTCs) refer to a number of special materials which are chemically stable at ultra-high temperatures (above 2000 ℃) and in reactive atmosphere (i.e., atomic oxygen environment), usually including borides, carbides, and nitrides of transition metals, and other high-melting point compounds. UHTCs are designed for extreme environments, such as hypersonic flight and re-entry vehicles. Types of UHTCs 1. Borides: Zr and Hf are chemically similar, leading to similar properties in their diborides, which have hexagonal crystal structures resembling the AlB₂ prototype. These materials exhibit very high hardness and temperature stability due to the strong B-B rings and M-B bonds (where M is Zr or Hf). Their strength is influenced by processing and microstructure, with smaller grain sizes generally leading to increased strength (Hall- Petch relationship). ZrB₂ and HfB₂ have high thermal conductivities, comparable to copper at room temperature, which remains stable up to 2500°C. This property is crucial for applications involving thermal stress, such as rocket motor nozzles. The oxidation resistance of these diborides is a primary focus of research. The addition of silica-forming species, such as silicon carbide (SiC), enhances their oxidation resistance by forming a protective borosilicate glass layer that impedes oxygen diffusion. An optimal composition of ZrB₂ with 20-30 vol% SiC has shown the best oxidation resistance up to 2000°C. Due to their properties, ZrB₂ and HfB₂ are considered for use in hypersonic vehicles and missile components, where they can withstand extreme temperatures and oxidative environments. 2. Carbides: Transition-metal carbides, such as zirconium carbide (ZrC) and hafnium carbide (HfC), are of interest due to their extremely high melting points, which exceed those of the borides. This makes them suitable for applications in extreme environments. The unique properties of transition-metal carbides make them suitable for various high-temperature applications, including aerospace and defense sectors, where materials must withstand extreme thermal and mechanical stresses. 3. Nitrides: The primary transition metal nitrides discussed include zirconium nitride (ZrN), hafnium nitride (HfN), and tantalum nitride (TaN). These materials are recognized for their potential applications in high-temperature environments. UHTC nitrides possess a range of thermal and mechanical properties that are advantageous for structural applications. They are known for their hardness and strength, which are critical for load-bearing applications. The oxidation behavior of nitrides varies among different materials. For instance, HfN has shown promising oxidation resistance, although it may not be as stable as some carbides. The formation of oxide scales during high-temperature exposure can affect their performance, with HfN demonstrating a dense, adherent oxide layer under certain conditions. Transition metal nitrides are utilized in various applications, including microelectronics (as diffusion barriers) and structural ceramics. Application Areas Aerospace: UHTCs are used in aerospace applications, particularly in components that experience extreme temperatures, such as leading edges and nozzles of hypersonic vehicles and re-entry spacecraft. Their high melting points and thermal stability make them ideal for these demanding conditions. Hypersonic Vehicles: The materials are critical for hypersonic flight applications, where they can withstand the intense heat generated during high-speed travel through the atmosphere. Plasma Arc Electrodes: UHTCs are employed in plasma arc applications due to their ability to maintain structural integrity and resist oxidation at high temperatures. Nuclear Applications: Some UHTCs may find applications in nuclear environments due to their stability and resistance to radiation damage. Defense: UHTCs are also considered for various defense-related applications, where their high-temperature capabilities can enhance the performance and durability of military equipment. Raw Materials Primary Materials: ZrB₂ ($100–$500/kg), HfB₂ ($300–$1000/kg). Additives: SiC, TiB₂, and carbon ($20–$100/kg). Suppliers: Saint-Gobain, Advanced Ceramics Corp. (global). Production Methods 1. Synthesis Methods - Carbothermal Reduction: This is the most commercially viable method for producing ZrB₂. It typically involves the reaction of zirconium oxide (ZrO₂) and boron oxide (B₂O₃) at high temperatures, which can leave impurities such as B₂O₃ and carbides. - Self-Propagating High-Temperature Synthesis (SHS): This method utilizes the highly exothermic reactions between the pure elements to produce borides. While effective, controlling these reactions can be challenging due to their intensity. 2. Densification Techniques - Hot Pressing: Traditionally, densification of boride powders has been achieved through uniaxial hot pressing in graphite molds at temperatures exceeding 1800°C. This method helps achieve high density and strength in the final product. - Spark-Plasma Sintering: Recent advancements have introduced spark-plasma sintering as a technique to minimize grain growth during hot pressing, which can enhance the mechanical properties of the borides. - Pressureless Sintering: Research from various groups has explored pressureless sintering methods, which could lower processing temperatures and allow for larger and more complex shapes to be produced commercially. Required Equipment 1. Ball Mills and Mixers: Approximate Cost for mills: $10,000–$50,000. 2. Shaping Machines: Hot presses or cold presses; Approximate Cost: $150,000– $500,000. 3. Sintering Equipment: For high-temperature sintering, approximate cost: $300,000– $1,000,000. For spark plasma sintering, approximate cost: $500,000–$2,000,000 4. Coating Equipment: CVD Reactors, approximate Cost: $250,000–$750,000. 5. Characterization Equipment: SEM, Approximate Cost: $100,000–$500,000. XRD, Approximate Cost: $100,000–$300,000. Detailed Production Steps 1. Powder Preparation: The raw materials are chosen depending on the application area and then these raw materials are ground to fine powders. Mixers ensure the uniform distribution of the powders. 2. Shaping: To obtain green bodies, cold or hot pressing can be used. In cold pressing, the mixed powders are placed into molds and pressed at room temperature whereas in hot pressing the green bodies are heated and pressed at the same time to achieve a higher density and better mechanical properties. 3. Sintering - High-Temperature Sintering: The shaped bodies are heated in a high-temperature furnace to a temperature above 2000°C. This process densifies the material and enhances its mechanical properties. - Spark Plasma Sintering (SPS): An advanced technique where an electric current is passed through the material to rapidly heat and sinter it, resulting in fine grain sizes and improved properties. 4. Coating: A coating may be utilized after the sintering process to enhance UHTCs’ oxidation resistance. Chemical Vapor Deposition (CVD) or Physical Vapor Deposition (PVD) are two methods that can be used for coatings. 5. Testing and Characterization: Thermogravimetric Analysis (TGA) for change in physical and chemical properties as a function of temperature, Dilatometry for the thermal expansion of the material, Scanning Electron Microscopy (SEM) for the microstructural analysis of the material and X-ray Diffraction (XRD) for the crystallographic analysis of the material. Engineering Characteristics Extreme Temperature Resistance: UHTCs can withstand temperatures exceeding 2000°C, making them suitable for environments like hypersonic vehicles and re-entry spacecraft. ZrB₂: Stable up to ~3000°C and HfB₂: Stable up to ~3300°C. High Hardness: UHTCs have exceptional hardness, typically in the range of 20–30 GPa, making them ideal for wear-resistant applications like cutting tools and armor. Good Chemical Resistance to Oxidation and Ablation: UHTCs form a protective oxide layer (e.g., ZrO₂ or HfO₂) at high temperatures, which provides some resistance to oxidation, though it may degrade over time in extreme environments. Critical for aerospace applications, UHTCs can resist material loss due to ablation under extreme heat and pressure, as seen in hypersonic and re-entry vehicles. Electrical Conductivity: Many UHTCs, such as ZrB₂ and HfB₂, are electrically conductive, allowing their use in electrodes and other high-temperature electronic components. Brittleness: Despite their excellent high-temperature properties, UHTCs remain inherently brittle, which limits their structural applications under mechanical stress. Engineering SWOT Analysis Strengths 1. Extreme Temperature Stability: Can withstand temperatures exceeding 2000°C, making UHTCs critical for hypersonic and space applications. 2. High Hardness: Borides and carbides exhibit hardness levels between 20–30 GPa, ideal for wear-resistant applications. 3. Oxidation and Ablation Resistance: Makes UHTCs suitable for re-entry vehicles and plasma-facing components in fusion reactors. Weaknesses 1. High Processing Costs: Materials like HfB₂ are expensive, and processing techniques (e.g., Spark Plasma Sintering) are capital-intensive. 2. Brittleness: UHTCs are inherently brittle, leading to challenges in handling and machining. Opportunities 1. Hypersonic and Space Technologies: UHTCs are essential for the leading edges of hypersonic vehicles and thermal protection systems. 2. Fusion Energy Development: Increased investment in fusion reactors where UHTCs can serve as plasma-facing components. Threats 1. High Competition: Metals and advanced composites may serve as alternatives in less demanding applications. 2. Environmental and Health Concerns: Dust from borides and carbides can be hazardous during production, leading to stricter regulations. Global Economic Outlook Projected Growth: The UHTCs market is expected to grow significantly from 2024 to 2030. This growth is fueled by advancements in aerospace, defense, and energy sectors. CAGR: The ceramics market, including UHTCs, is projected to grow at a compound annual growth rate (CAGR) of around 5% to 8% over the next few years. Leading regions: US, China, and Europe. Some companies: Morgan Advanced Materials Unifrax Dynamic Ceramic Bnz Materials Inc. Pyrotek Inc. Hi-Temp Insulation Inc. Cotronics Corporation Adl Insulflex Inc. Insulcon Group M.E Schupp Industriekeramik GmbH & Co. Skamol A/S