Location, Facilities, and Capacity Planning, Layout Strategy (PDF)
Document Details
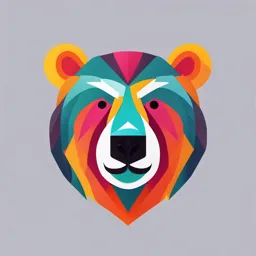
Uploaded by FelicitousMetaphor482
Manuel L. Quezon University
Tags
Summary
This document provides a comprehensive overview of facility planning, covering topics like capacity planning, location planning, and layout strategy. It explores various aspects of these topics, including different strategies and considerations. This document appears to be a presentation or lecture material.
Full Transcript
LOCATION, FACILITIES AND CAPACITY PLANNING, LAYOUT STRATEGY LOCATION, FACILITIES AND CAPACITY PLANNING, LAYOUT STRATEGY Del Rosario, Angela Escuro, Carl Andrew Olaviaga, Xivyl Padoga, Efren Pedrosa, Rechelle CAPACITY PLANNING CAPACITY specific ability of an enti...
LOCATION, FACILITIES AND CAPACITY PLANNING, LAYOUT STRATEGY LOCATION, FACILITIES AND CAPACITY PLANNING, LAYOUT STRATEGY Del Rosario, Angela Escuro, Carl Andrew Olaviaga, Xivyl Padoga, Efren Pedrosa, Rechelle CAPACITY PLANNING CAPACITY specific ability of an entity (person or organization) or resource, measured in quantity and level of quality, over an extended period. CAPACITY PLANNING Capacity planning process is used by organizations to determine their production capacity in order to meet the changing needs of their products. A design capacity is an organization's maximum ability to complete a specified amount of work in a given time period, in the context of capacity planning. IMPORTANCE Capacity planning is essential to be determining optimum utilization of resource and plays an important role in decision-making process. CAPACITY PLANNING STRATEGIES Lead Strategy Lead capacity strategy, or lead strategy, is the process of increasing production capacity when you're in anticipation of a high demand. Lag Strategy Lag strategy planning is the process of increasing production capacity when you’re experiencing a real-time demand. Match Strategy Match strategy planning is a combination of lead capacity planning and lag strategy planning. The process of match strategy planning requires slowly increasing capacity in small increments until you reach the desired resource utilization. MEASUREMENT OF CAPACITY PLANNING involves evaluating different capacity levels to understand an organization's operational limits. The maximum output a system is designed to achieve under Design Capacity optimal conditions. The actual output under real-world conditions, System Capacity accounting for inefficiencies. The production or operational limit Licensed Capacity permitted by regulatory authorities. total potential output based on Installed Capacity the equipment and resources installed. The maximum output a Rated Capacity facility or machine is expected to produce under specific conditions. PROCESS OF CAPACITY PLANNING LONG TERM CAPACITY STRATEGIES Long-term capacity requirements are more difficult to determine because the future demand and technology are uncertain. Following parameters will affect long range capacity decisions MULTIPLE PRODUCTS PHASING IN CAPACITY PHASING OUT CAPACITY PROCESS OF CAPACITY PLANNING SHORT TERM CAPACITY STRATEGIES Managers often use forecasts of product demand to estimate the short-term workload the facility must handle. INVENTORIES BACKLOG EMPLOYMENT LEVEL EMPLOYMENT TRAINING SUBCONTRACTING PROCESS DESIGN LOCATION DECISION THE VALUE OF LOCATION The growing popularity of mapping web sites and handled GPS (Global Positioning Satellite) devices is indicative of the continuing recognition of the value of location. And even with the growth of online shopping and virtual commerce, all business transactions and events still take place with the parties located at some physical location. LOCATION PLANNING Location planning involves selecting optimal sites for your business operations. It uses data and analytics to evaluate factors like competitor locations, customer demographics, and transportation hubs. LOCATION INTELLIGENCE Location intelligence blends the analysis of objects (such as people, business, points of interest, or geographic regions) with their spatial attributes (such as average age, median income, average driving distance, or average educational attainment) to inform decision-making for operational efficiencies, revenue growth, or more effective management. MAKING LOCATION DECISIONS: PROCESS ANALYSIS SHOULD FOLLOW STEP PROCESS: 1 Identify dominant location factors 2 Develop location alternatives. 3 Evaluate location alternatives TYPES OF LOCATION The type of location you choose depends largely on the type of business you're in, but there are enough mixed-use areas and creative applications of space limit that you should give some thought to each type before making a final decision. HOME-BASED Many businesses start from home, such as using a spare room or even the kitchen table, and may move to commercial space as they grow. RETAIL This includes spaces like malls, shopping centers, or standalone buildings, but could also be in unique spots like airports, hotels, or sports stadiums. MOBILE If you bring your products or services to your customers, your business might operate out of a vehicle like a car, van, or truck. COMMERCIAL These are traditional office spaces in business parks or city centers, used by businesses that don't rely on lots of customer foot traffic. INDUSTRIAL For manufacturing or large-scale distribution, businesses need warehouses or plants, often located in industrial parks or areas with access to transportation like rail or ports. FACTORS THAT AFFECT LOCATION DECISIONS COSTS LABOR PRODUCTIVITY EXCHANGE RATE AND CURRENCY RISK TANGIBLE COSTS: EASILY INTANGIBLE COSTS: HARDER-TO- MEASURABLE COSTS, LIKE MEASURE FACTORS LIKE QUALITY OF RENT OR UTILITIES. LIFE OR GOVERNMENT SUPPORT. ATTITUDES PROXIMITY TO MARKETS PROXIMITY TO SUPPLIERS PROXIMITY TO COMPETITORS IMPORTANCE OF LOCATION DECISION Location decisions significantly impact overall business strategy and operational efficiency in production and operations management Choosing the right location aligns with company goals, market access, and resource availability Poor location choices can lead to increased costs, reduced competitiveness, and operational challenges Cost Control Access to Talent and Resources Competitiveness LAYOUT STRATEGY LAYOUT STRATEGY Layout strategy in operations management refers to the deliberate arrangement of physical resources within a facility to optimize efficiency, productivity, and customer satisfaction. LAYOUT DESIGN CONSIDERATION Higher utilization of space, equipment and people Improved flow information, materials or people Improved employee morale and safer working conditions Improved customer/clients’ interaction Flexibility TYPES OF LAYOUTS OFFICE LAYOUT RETAIL LAYOUT WAREHOUSE LAYOUT FIXED-POSITION LAYOUT PROCESS-ORIENTED LAYOUT TYPES OF LAYOUT Office layout - positions workers, their equipment, and spaces/offices to provide for the movement of information Retail layout - allocates shelf space and responds to customer behavior Warehouse layout - addresses trade-offs between space and material handling Fixed-position layout - address the layout requirements of large, bulky projects such as ships and buildings Process-oriented layout - deals with low-volume, high variety production (also called job shop or intermittent production) FACILITY PLANNING FACILITY PLANNING Smart companies employ a methodical process called facility planning to make sure they have the buildings and related resources needed to accomplish their short- and long-term objectives. Sometimes referred to as strategic facility planning, it’s the primary decision-making that firms utilize to future-proof their workspaces. WHO IS RESPONSIBLE FOR FACILITY PLANNING? The intricate process of facility design necessitates close teamwork in the workplace. Having stated that, a facility manager (FM) or a facility management team usually handles facility demands. Because they usually have the information and tools needed to make wise decisions for the workplace, FMs are excellent planners. And since their ultimate objective is to anticipate demands and keep everything operating properly. THE FOUR STEPS IN FACILITIES PLANNING 1 Understand your goals 2 Analyze and set benchmarks 3 Start planning 4 Start acting THE FOUR STEPS IN FACILITIES PLANNING 1 Understand your goals Aligning corporate objectives with existing facilities and any planned additions is the aim of facility planning. Therefore, the planning task force must determine the demands being made on them by the business in addition to the limitations of their current building before any actual planning takes place. 2 Analyze and set benchmarks 3 Start planning 4 Start acting THE FOUR STEPS IN FACILITIES PLANNING 1 Understand your goals Planning requires knowing which objectives are most essential right now. This is a crucial initial step. Every member of the facility planning team must comprehend the company's goal, vision, and culture for this process to be successful. 2 Analyze and set benchmarks 3 Start planning 4 Start acting THE FOUR STEPS IN FACILITIES PLANNING 2 Analyze and set benchmarks Aligning corporate objectives with existing facilities and any planned additions is the aim of facility planning. Therefore, the planning task force must determine the demands being made on them by the business in addition to the limitations of their current building before any actual planning takes place. 3 Start planning 4 Start acting THE FOUR STEPS IN FACILITIES PLANNING 2 Analyze and set benchmarks To be more precise, FM requires three tools in order to proactively assess their current workplace and develop change management plans: Extensive reports and analytics, such as vacancy and portfolio reports, that offer practical insights into the current demands of employees and the real-time utilization of existing space Software for scenario planning, which facilitates the easy virtual testing of reconfigurations' effects prior to their human implementation 3 Start planning Stack plans, which give a broad overview of how space is being used at 4 Start acting the moment THE FOUR STEPS IN FACILITIES PLANNING 3 Start planning FMs may start actually working on their master plan if they have a clear understanding of their objectives and benchmarks. This is the point at which converting a facilities plan into a business strategy becomes difficult. Depending on what your organization's business drivers are, it will seem different. 4 Start acting THE FOUR STEPS IN FACILITIES PLANNING 4 Start acting It would be simpler for FMs to implement their plans if they can make the most of the first phases of facilities planning. The correct tools become crucial at this point as well. With the correct facility management software, implementing any new modifications to a workplace or facility is at its finest. This should ideally be able to interface with the integrated workplace management system (IWMS) that your business now uses. THE IMPORTANCE OF FACILITIES PLANNING The following advantages of strategic facility planning may be expected by businesses when implemented correctly and with the appropriate resources: Reduced expenses and enhanced sustainability, typically through the need for fewer office spaces enhanced engagement and experience among employees as a result of innovative work arrangements that optimize office space and improve the digital workspace— extremely crucial at this point in the Great Resignation Increased effectiveness as a result of the careful examination of resource optimization