Warping Process PDF
Document Details
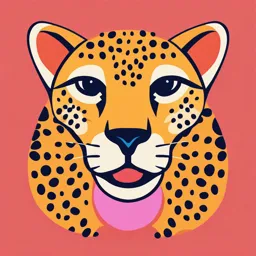
Uploaded by ImmaculateBasilisk
Textile Institute of Pakistan, Karachi
Shakeel Ahmad Paracha
Tags
Summary
This document provides an overview of the warping process in textile manufacturing. It describes different types of warping, such as high-speed and sectional warping. It also details the objectives and key components of warping machines.
Full Transcript
Textile Institute of Pakistan, Karachi. TEXT202 (Fabric Technology) The Warping Process Definition o “Warping is transferring of many yarns from a creel of single-end packages forming a parallel sheet of yarn and wound it onto a beam”. o...
Textile Institute of Pakistan, Karachi. TEXT202 (Fabric Technology) The Warping Process Definition o “Warping is transferring of many yarns from a creel of single-end packages forming a parallel sheet of yarn and wound it onto a beam”. o To combine the yarn from individual packages in the form of a sheet on to a warper’s beam is called warping. o Raw material: Cone/cheese/spool. o Final product: Warper’s beam/ball. Objectives of the Warping Process The main objectives of the warping process are: o To collect large number of required yarns from the winding package onto the beam. o By means of warping, different nature or different colours of yarns can be collected on the beam according to the required arrangement. o Winding of a specific type of package as required by the subsequent process, i.e. warper’s beam, ball. Types of the Warping Process or Warping Machines There are four types of warping, which are as follows: o High-speed (direct) warping o Sectional (indirect) warping o Ball (for denim) warping o Draw (heat set) warping High-speed (Direct) Warping In high-speed (direct) warping, the yarns are withdrawn from the single-end yarn packages on the creel and directly wound on a beam. In simple warping, yarns of same colour and type are collected directly on the beam. Since, this type of warping deals with the same type of yarns, so, its speed is quite high and that is why it is also called as high-speed warping. In simple or high-speed warping, a single warper’s beam contains a fraction of the total ends required in the weaver’s beam. So, more than one warper’s beams are made which are collected together later in the sizing process to get the required ends. For Example, 9000 warp yarns are required in a fabric and each warper’s beam has 1000 yarns then we will have to make total 9 warper’s beam. Later on, these warper’s beams are collected together in sizing. Prepared By: Shakeel Ahmad Paracha Page 1 of 23 Textile Institute of Pakistan, Karachi. TEXT202 (Fabric Technology) Prepared By: Shakeel Ahmad Paracha Page 2 of 23 Textile Institute of Pakistan, Karachi. TEXT202 (Fabric Technology) Major parts of High-speed (Direct) Warping Machine Nowadays, the most commonly used direct warping machine is “Karl Mayer” (previously named as “Benninger”). High-speed (direct) warping machine is classified into two portions: o Creel o Headstock Creel It is an arrangement (frame) to hold the supply packages for warping onto a beam. There are two types of creel w. r. t. shape. o V-shape creel o H-shape creel V-shape creel is used for high-speed warping. The major parts of creel in “Karl Mayer” warping machine are: o Vertical columns (rods) o Spindles o Tension rods o Yarn brake o Stop-motion sensors o Cutters o Drive arrangement Vertical Columns (Rods) Each wing of creel consists of number of vertical rods. Number of rods are approximately double than the creel capacity in duplicate creel. Creel capacity is determined with the help of number of rods & spindles/rod. Prepared By: Shakeel Ahmad Paracha Page 3 of 23 Textile Institute of Pakistan, Karachi. TEXT202 (Fabric Technology) Spindles It is support for fixing the yarn package on a creel. It is fitted at certain angle ranges from 2 - 3 degrees. Tension Rods It is a device which keeps the yarn under constant tension so that yarn is kept stretched. Two tension rods are used for tensioning mechanism; one is movable & the other one is stationary. The movable rods are fitted in metallic rails. Multiplicative tension is applied with these rods. Tension is applied or released with the help of movable rod. The relative distance b/w two rods is controlled with the help of pneumatic cylinder & piston arrangement. Prepared By: Shakeel Ahmad Paracha Page 4 of 23 Textile Institute of Pakistan, Karachi. TEXT202 (Fabric Technology) Yarn Brake It is used to stop the movement of an individual yarn when any warp yarn is broken. One thread brake is used for one thread. It avoids entanglement of yarn at breakage. It is fitted in stop motion assembly. Signal lamps are used on the front of creel and relevant tensioner post to indicate the broken warp yarn so that it can be identified and replaced/repaired easily. Stop-motion Sensors These can be either in lever type or optical type sensors. o Lever type sensor The lever has soft surface to reduce friction on yarn. It is fitted in the stop-motion assembly, which is connected to the photoelectric cell. When yarn breaks, lever falls, the circuit is completed & the machine is stopped. o Optical type sensor This sensor consists of a transmitter and a receiver. The yarn passes between the two. Due to the movement of yarn, there will be no change in the intensity of light, which indicates the presence of yarn. When yarn breaks, there is a change in the intensity of light due to the absence of yarn, and ultimately machine will stop. Cutters Two cutter levers are used to separate the yarns from the packages when creel exhausts. The cutter lever is moved from the front of the creel to the back of the creel. Creel Movement Drive The empty portion of creel is replaced by the loaded portion by drive arrangement. Prepared By: Shakeel Ahmad Paracha Page 5 of 23 Textile Institute of Pakistan, Karachi. TEXT202 (Fabric Technology) Each vertical rod is connected to a sprocket chain, at top and bottom of the vertical rod. These vertical rods are given drive from two slow speed motors through sprocket gears. Spindle Pitch It is the distance (horizontal & vertical) between two consecutive spindles. It determines the maximum package size that can be used. Headstock The major component of the warping machine that helps to rotate and winds the warp sheet on warper’s beam is called headstock. Prepared By: Shakeel Ahmad Paracha Page 6 of 23 Textile Institute of Pakistan, Karachi. TEXT202 (Fabric Technology) Objectives of Headstock Main objectives of the headstock are: o To wind the warp sheet onto the beam. o To control the tension on warp yarns. o To control warping speed. o To apply the brake to get the desired beam hardness (compactness). o To do even yarn distribution over the whole width of the beam. Major parts of the headstock in “Karl Mayer” warping machine are: o Comb o Guide roller o Warping beam o Pressing drum Comb It is of zig-zag shape, used to cover the whole width of warper’s beam with yarns. It also separates the warp yarns uniformly. Three types of movements are performed by the comb to increase its life: o Up & down movement o Horizontal movement o Traversing movement Guide Roller The guide roller has smooth polished surface and helps to direct the warp sheet from creel towards the beam. A hydraulic brake system is fitted on one side of it to stop the guide roller. Prepared By: Shakeel Ahmad Paracha Page 7 of 23 Textile Institute of Pakistan, Karachi. TEXT202 (Fabric Technology) Warping beam/Warper’ s beam It is the yarn package on which warp sheet is wounded. It is directly driven by a motor and a hydraulic brake system is installed on both sides to stop on any yarn breakage. Pressing Drum/Warping Drum The pressing drum is used to make the beam compact and helps in the cylindrical build-up of the beam. It also measures the length of yarn wounded on the beam. It can move forward or backward to attach or detach with the beam. This movement is facilitated by a hydraulic system. The pressing drum lifts-off immediately at the beam brake, to avoid friction with the yarn sheet, eliminating the chances of damage to yarn. Wind Shield It is used to protect the warper’s beam during the warping process from any foreign element like fluff, dust etc. It also protects the warping operator from headstock during the warping process. It starts its operation automatically as soon as the warping machine starts. Prepared By: Shakeel Ahmad Paracha Page 8 of 23 Textile Institute of Pakistan, Karachi. TEXT202 (Fabric Technology) Creel Capacity It is the maximum number of yarn packages that can be mounted on the creel in running position. Creels with a capacity of up to 1296 are available currently. No. of rods No. of spindles Creel capacity = 2 x x Wing Rod The zig-zag comb can expand or contract, which defines the maximum and minimum creel capacity. Max. Creel Capacity The number of comb dents in the front of warping beam, when the comb is compressed maximum. Min. Creel Capacity The number of comb dents in the front of warping beam, when the comb is expanded maximum. Creel Angle (θ) It is the angle between two wings of V-type creel and normally ranges from 30° - 35°. Wing Angle (α) It is the angle of one wing of creel with the central axis of machine or creel. It is half of the creel angle. Set The required number of warper’s beams with required number of ends and the specific length is called as set of warp/warp set. Prepared By: Shakeel Ahmad Paracha Page 9 of 23 Textile Institute of Pakistan, Karachi. TEXT202 (Fabric Technology) Sectional (indirect) Warping Sectional warping is also known as indirect, pattern, band warping or drum warping. It is suitable for all patterned warp fabrics, e.g., stripes and checks. Sometimes, this process is carried out for 2-ply synthetic yarns where no sizing is needed. It is a two-stage warping method (namely as warping and beaming) in which yarns of required length are first collected on the drum (swift) and are then transferred onto a beam in required arrangement mostly used for yarn dyed fabrics. This special arrangement of the coloured yarns such collected is called as stages, sections or pattern. Warping is done from the creel to drum. Beaming is done from drum to warper’ s beam. Creel capacity is small as compared to direct warping. The drum/swift is tapered at a slight angle to prevent slippage of yarn. A higher taper angle will reduce the package stability. The yarns are laid section-wise starting from the conical base side. The taper of the base supports the first section and the subsequent sections are supported by the taper formed by the preceding section. Each section has specific number of ends depending upon the repeat. There can be more than one count/colour in one section. The sections are traversed on the drum during warping along the width of the section to form an angle. Length of yarn is measured with measuring roller. The amount of yarn wound on the beam is proportional to: o Length of yarn (direct relation) o Number of ends/section (indirect relation) o Cone angle (direct relation) Number of sections depends upon: o Creel capacity (indirect relation) o Total number of ends in warp sheet (direct relation) When all the sections have been wounded, they are removed simultaneously and wounded on warper’s beam which may or may not be taken for sizing. Prepared By: Shakeel Ahmad Paracha Page 10 of 23 Textile Institute of Pakistan, Karachi. TEXT202 (Fabric Technology) Sectional (indirect) Warping Machine Major parts of Sectional Warping Machine The sectional warping machine just like the direct warping machine has two portions: o Creel o Headstock Creel Parallel (H-type) type creel is mostly used for this warping machine as it is a slow speed process. Usually, mobile creel is preferred due to a patterned/coloured repeat of yarns. Special care is required while loading the cones on creel according to repeat. Prepared By: Shakeel Ahmad Paracha Page 11 of 23 Textile Institute of Pakistan, Karachi. TEXT202 (Fabric Technology) Headstock Headstock of sectional warping machine is different from that of direct warping machine. Here, the yarn passage is from creel through the leasing rod to the leasing comb (reed) and then to the section comb (traversing or final comb). From final (warping) comb, the yarn passes over the guide or measuring roller then onto the sectional warping drum (swift/drum/dresser). When all the required number of ends in the shape of sections are wounded on the drum or the swift, the upper ends of all the sections are taken out from the drum in the shape of a sheet. This warp sheet is then transferred onto the weaver’s or the warping beam. Prepared By: Shakeel Ahmad Paracha Page 12 of 23 Textile Institute of Pakistan, Karachi. TEXT202 (Fabric Technology) The headstock of the section warping machine has the following parts: o Leasing/dividing rods o Leasing comb o Carriage o Swift/drum/dresser Leasing/Dividing Rods Its function is only to separate the yarns into two portions to ease out the leasing process. Leasing Comb This reed is to permit the warp yarns passing through it to be separated into sheets suitable for lease formation. It has alternate open and block dents. Sometimes, more complicated arrangements are used to segregate yarns specially the coloured/fancy yarns, into more than 2 sheets. Carriage Sometimes, it is also termed as section carrier trolley. It is a movable arrangement carrying the following parts: o Section reed o Measuring roller o Tension and guide roller o Touch screen panel o Oil box Prepared By: Shakeel Ahmad Paracha Page 13 of 23 Textile Institute of Pakistan, Karachi. TEXT202 (Fabric Technology) Section Reed Section reed is used to control the section width and to avoid threads overlapping in between the completion of one section and starting the other section. It’s another function is to move the section laterally along with the drum surface for section building. Measuring Roller It measures the length of the section wound on the swift. It is always necessary that the length of each section wound on the swift should be equal. Tension and Guide Roller This is a set of two chromium plated rollers which give proper tension to the sections. An evener roller is also present to compress the warp section over the drum to achieve perfect and even warp layer during warping. Touch Screen Panel It is used to feed the warp specifications like section ends, length, width, etc. Oil Box It is used to apply spindle oil in 100% polyester filament and terry towel just like waxing. Motions of Carriage Carriage has two types of motions: o Traverse motion o Movement of section Prepared By: Shakeel Ahmad Paracha Page 14 of 23 Textile Institute of Pakistan, Karachi. TEXT202 (Fabric Technology) Traverse Motion Slow traverse motion parallel to the drum axis. It is called “feed,” and it makes the yarn layer (section) to climb up the cone. It allows the leasing of yarn on cone and leasing of next section on the previous section. Movement of Section It causes to move the carriage along section width at section change. Swift/Drum/Dresser It is composed of a steel cylinder, hollow from inside, with a diameter of about 50"- 60". In old machines, wooden swifts were used. Its main function is to wrap the small sections before transferring onto the beam. It’s one side is tapered at some angle. The taper angle depends upon: o Yarn count o Yarn type o Ends/cm Machine Parameters Parameters Specifications Working width 2300 mm - 3600 mm Warping speed 600 m/min Beaming speed 160 m/min Drum diameter 1000 mm Section width 20 mm - 360 mm Creel capacity 720 Cone angle 7◦, 9◦, 12◦ Package Withdrawal and Beam Doffing All the sections that are wounded over the drum are doffed onto the beam by beaming process as follows: o Turn the switch from warping to beaming. o Set an empty beam in the beaming section and an adhesive tape is applied/pasted over the beam barrel and rotate the beam manually. o Set beam flange (beam space) according to measured/calculated beam space. o Set winding tension (1 - 6 Newtons). o Run at crawl speed to see alignment by drum alignment switch. Prepared By: Shakeel Ahmad Paracha Page 15 of 23 Textile Institute of Pakistan, Karachi. TEXT202 (Fabric Technology) o Set the winding speed within a range of 1 - 160 m/min, depending on yarn quality. o Run the m/c with run switch/start button. o Doff the beam by unloading switch. o Warping data sheet is filled as a production record. o A warping data sticker is pasted on each beam for the identification purpose in the next process. Differences between Direct & Sectional Warping Parameters Direct warping Sectional warping It is generally used to produce warp It is generally used to produce warp Object /Use beam for griege fabric or solid colour beam for yarn dyed (check/stripe) fabric. fabric. Method of Several warper’s beams are produced One warper’s beam is produced here production here for getting one weaver's beam. for getting one weaver's beam. Ends/beam is less here. Direct Ends/beam is higher. Sectional No. of warping beams contain 1/N No. of warping beam contains equal no. of Ends/beam ends of weaver’s beam. ends as weaver’s beam. (N = Number of warping beam/set). Two-stage Production (yarns are Stage of One-stage Production (yarns are directly wound on warping drum production directly wound on warper’s beam). section by section; then the sheet is transferred to warper’s beam). Yarn tension is comparatively higher Yarn tension is comparatively lower Yarn tension than sectional warping. than direct warping. Length of yarn in the beam is Yarn length Higher length of yarn is wound on a comparatively lower than direct on beam beam. warping. Creel Usually higher than sectional warping. Usually lower than direct warping. capacity Sizing One sized beam is produced from One sized beam is produced from one operation several No. of warper’s beam. warper’s beam. Efficiency is comparatively lower than Efficiency is higher than sectional Efficiency direct warping (one additional warping (single stage operation). operation beaming-off is required). Prepared By: Shakeel Ahmad Paracha Page 16 of 23 Textile Institute of Pakistan, Karachi. TEXT202 (Fabric Technology) Ball Warping “Ball warping is the process in which warping is performed in rope form onto balls.” A ball warped beam is prepared for subsequent process. It is suitable for denim fabric manufacturing, involving rope dyeing process. It is also a 2-stage process. Ball Warping Machine In ball warping, 350 - 500 yarn ends are pulled from the creel. The yarns then pass through a comb-like device (reed), which keeps each warp yarn separate and parallel to its neighbouring ends. At intervals of every 1000 or 2000 yards, a lease string is placed across the sheet of warp yarns to aid yarn separation. The yarns then go through a funnel-shaped device called a trumpet or condenser, which collapses and condenses the sheet of yarn into rope form. The rope is wound onto a long cylinder called as “log” on a machine called as a ball warper. Indigo/Sulphur dyeing will take place in rope form. Re-beaming is done to convert the rope dyed warp yarn, stored in cans, into warper’s beams. Prepared By: Shakeel Ahmad Paracha Page 17 of 23 Textile Institute of Pakistan, Karachi. TEXT202 (Fabric Technology) Prepared By: Shakeel Ahmad Paracha Page 18 of 23 Textile Institute of Pakistan, Karachi. TEXT202 (Fabric Technology) Prepared By: Shakeel Ahmad Paracha Page 19 of 23 Textile Institute of Pakistan, Karachi. TEXT202 (Fabric Technology) Warping Production Calculations Production by Length Calculated Production yds = Warping Rate( yds / min ) x 60 x th Warping Rate( yds /min) x 60 x th x Eff. Actual Production yds = 100 Production by Weight Warping Rate( yds / min) x 60 x th x Ew Calculated Production lbs = 840 x Ne Warping Rate( yds / min) x 60 x th x Ew x Eff. Actual Production lbs = 840 x Ne x 100 Where, th = Time in hours Ew = No. of Ends of a warped beam Eff. = Machine Efficiency for the said time period in hours Ne = English Count Warping Rate = DN Where, D = Diameter of Warping Drum ( yards ) N = R.P.M. of Machine (Warping Drum ) Actual Production Efficiency % = x 100 Calculated Production Q. Calculate the calculated , and actual production of a warping machine in Length and Weight , if Warping Rate = 1200 mtrs / hr., Efficiency = 90% , English Count ( Ne ) = 30 S , Time = 8 Hours , Total Ends = 9000 1200 x 1.0936 Warping Rate = yds / min 60 Warping Rate = 21.872 yds / min Calculated Production yds = Warping Rate( yds / min.) x 60 x th Calculated Production yds = 21.872 x 60 x 8 Calculated Production yds = 10498.56 yds Warping Rate( yds /mins.) x 60 x t h x Eff. Actual Production yds = 100 21.872 x 60 x 8 x 90 Actual Production yds = 100 Actual Production yds = 9448.704 yds Warping Rate( yds / min) x 60 x th x Ew Calculated Production lbs = 840 x Ne 21.872 x 60 x 8 x 9000 Calculated Production lbs = 840 x 30 Calculated Production lbs = 3749.485 lbs Warping Rate( yds / min) x 60 x th x Ew x Eff. Actual Production lbs = 840 x Ne x 100 21.872 x 60 x 8 x 9000 x 90 Actual Production lbs = 840 x 30 x 100 Actual Production lbs = 3374.537 lbs Prepared By: Shakeel Ahmad Paracha Page 20 of 23 Textile Institute of Pakistan, Karachi. TEXT202 (Fabric Technology) Types of Creels W.r.t Shape o H-shaped creel (rectangular/parallel) o V-shaped creel W.r.t Construction o Mobile creel (truck/trolley) o Swivel creel (rotating frame creel) o Magazine creel H-shaped Creel (rectangular/parallel) Wings are parallel to each other. Yarns may touch each other. Suitable for slow speed warping. V-shaped Creel Wings/arms are placed at a certain angle. Yarns do not touch. Suitable for high-speed warping. Prepared By: Shakeel Ahmad Paracha Page 21 of 23 Textile Institute of Pakistan, Karachi. TEXT202 (Fabric Technology) Mobile Creel (truck/trolley) This creel type is similar to the standard creel but is formed by trolleys which can be taken individually out of the creel. The bobbins are creeled up on each trolley outside the creel. During the creeling up of a series of trolleys, the second series of trolleys is brought back to the outside of the creel to feed the warper. This reduces considerably the waiting time. The mobile creel comes in handy especially when there is insufficient room to permit the use of two standard creels. Magazine Creel This kind of creel is used when several warps of similar type are prepared in sequence. Level with each tensioner, two bobbins are positioned: one operating and the other as reserve. Swivel Frame Creel (rotating frame creel) This type of creel was designed as a variation of mobile creel to enable the creeling up of heavy weight cones, which cannot be pinned on trolleys. Each bobbin holder is double-sided. The threads are unwound from one side, while a new series of bobbins is creeled on the other side. Prepared By: Shakeel Ahmad Paracha Page 22 of 23 Textile Institute of Pakistan, Karachi. TEXT202 (Fabric Technology) Prepared By: Shakeel Ahmad Paracha Page 23 of 23