Typical Electronic/Digital Aircraft Systems I (5.15) PDF
Document Details
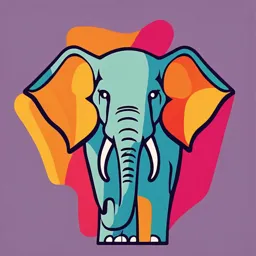
Uploaded by AccomplishedPlumTree
Tags
Summary
This document provides learning objectives related to typical electronic digital aircraft systems, the arrangement of Aircraft systems, and BITE testing capabilities.
Full Transcript
Typical Electronic / Digital Aircraft Systems I (5.15) Learning Objectives 5.15.1 Describe the general arrangement of typical electronic/digital aircraft systems and associated Built-In Test Equipment (BITE) (Level 2). 5.15.1.1 Describe the general arrangement and BITE testing capa...
Typical Electronic / Digital Aircraft Systems I (5.15) Learning Objectives 5.15.1 Describe the general arrangement of typical electronic/digital aircraft systems and associated Built-In Test Equipment (BITE) (Level 2). 5.15.1.1 Describe the general arrangement and BITE testing capabilities of the Aircraft Communications Addressing and Reporting System (ACARS) (Level 2). 5.15.1.2 Describe the general arrangement and BITE testing capabilities of the Electronic Centralised Aircraft Monitoring (ECAM) system (Level 2). 5.15.1.3 Describe the general arrangement and BITE testing capabilities of theElectronic Flight Instrument System (EFIS) (Level 2). 5.15.1.4 Describe the general arrangement and BITE testing capabilities of theEngine Indicating and Crew Alerting System (EICAS) (Level 2). 5.15.1.5 Describe the general arrangement and BITE testing capabilities of the Fly-By- Wire (FBW) control system (Level 2). 5.15.1.6 Describe the general arrangement and BITE testing capabilities of the Flight Management System (FMS) (Level 2). 5.15.1.7 Describe the general arrangement and BITE testing capabilities of the Global Positioning System (GPS) (Level 2). 5.15.1.8 Describe the general arrangement and BITE testing capabilities of theInertial Reference System (IRS) (Level 2). 5.15.1.9 Describe the general arrangement and BITE testing capabilities of theTraffic Alert and Collision Avoidance (TCAS) (Level 2). 2022-07-22 B1-05b Digital Techniques / Electronic Instrument Systems Page 99 of 172 CASA Part 66 - Training Materials Only Integrated Test Equipment Aircraft Diagnostics Today’s aircraft are so complex that design engineers must consider the ability to troubleshoot a system as equally important as the ability to repair or inspect that system. Troubleshooting a complex digital aircraft would be nearly impossible without self-diagnostic systems. Self-contained diagnostics used for electronic/avionics systems troubleshooting became known as BITE (Built-In Test Equipment). LRU housing BITE 2022-07-22 B1-05b Digital Techniques / Electronic Instrument Systems Page 100 of 172 CASA Part 66 - Training Materials Only BITE Systems There are several versions of built-in test equipment which are in use today. Simple BITE systems typically incorporate a go/no-go red or green LED on the equipment black box or LRU. More complex systems use a multi-character display and monitor more than one LRU. Some BITE can also test the associated wiring. The current generation of self-diagnostics equipment incorporates the use of a centralized monitoring system which incorporate flight deck displays from which tests can be activated. Faults detected through several BITE systems are monitored in one location, include paper printouts of test results, and have a means to transmit data from the aircraft to the maintenance facility during flight. BITE Information The advanced built-in troubleshooting system used by Boeing is known as CMCS (Central Maintenance Computer System). The advanced diagnostic system used by Airbus is called Centralized Fault Display System (CFDS). Each of these advanced systems incorporate enhanced BITE features that aid in troubleshooting. In general, the advanced systems are more easily accessible and understood than older systems. A commercial airliner may contain several BITE units used to monitor a variety of systems. Each BITE unit receives inputs from several individual components of the system being tested. A Boeing 757 or 767 aircraft, for example, utilizes built-in test equipment systems on approximately 50 LRUs located throughout the aircraft. Other individual systems also contain their own dedicated Built-In Test Equipment. These BITE systems are relatively simple and are contained within the LRU being monitored. This meant early BITE systems were accessed in the electronics equipment bay or similar area. 2022-07-22 B1-05b Digital Techniques / Electronic Instrument Systems Page 101 of 172 CASA Part 66 - Training Materials Only BITE Philosophy Most aircraft systems are composed of several individual units called Line Replaceable Units (LRUs). A LRU can refer to a black box, a sensor, an actuator, a probe, or similar item. Line Replaceable Units (LRU) Most LRUs are controlled by digital computers and for safety reasons these LRUs are permanently monitored so that testing and troubleshooting procedures can be performed. The example used below is an Airbus A330 On Board Maintenance System (OBMS). In each system, a particular section of a computer is dedicated to these functions. The section is referred as the BITE section. Where a system uses multiple computers, one computer may be dedicated to managing BITE. During normal operation BITE is continuously monitoring the internal LRU circuits, the LRU inputs and outputs, and the links between system LRUs. When a failure occurs, BITE can identify the possible failed LRU and determine if the failure is intermittent or permanent. Additionally, it can give a snapshot of the system environment at the time of the failure and save the details in a non-volatile memory for later analysis. 2022-07-22 B1-05b Digital Techniques / Electronic Instrument Systems Page 102 of 172 CASA Part 66 - Training Materials Only © Aviation Australia Block diagram of BITE philosophy BITE Function The BITE information stored in the system BITE memory is sent to a centralised maintenance device. Some BITE tests can be initiated via this centralised maintenance device with advantages including: A single interface location (cockpit). Easy fault identification. Reduction of trouble shooting duration. Simplification of technical documentation. Standardisation of equipment. BITE can be divided into 4 groups. Power Up Test The power up test is first a safety test to ensure compliance with safety objectives. The test duration is a function of the system which is currently not operational. It is executed only on the ground after any power cut the exceeds a nominal 200 milliseconds. If the aircraft is airborne, the power up test is limited to a few items to enable a quick return to the operation of the system. A power up test typically includes the following tasks: Test of the microprocessor. Test of the memories. Test of the data lines and various input/output circuits. A configuration test. 2022-07-22 B1-05b Digital Techniques / Electronic Instrument Systems Page 103 of 172 CASA Part 66 - Training Materials Only Cyclic Tests Cyclic tests (also known as In Operation Tests) are carried out permanently without disturbing system operation. Tasks include: A watchdog test (a watchdog is a device capable of restarting the microprocessor if the software fails). A RAM test. Data line (ARINC 429) message validity. System Test The purpose of this test is to offer the maintenance crew the ability to test the system for troubleshooting purposes. The test is performed after system restoration, following replacement of an LRU, to check the integrity of the system. It is like a power up test. 2022-07-22 B1-05b Digital Techniques / Electronic Instrument Systems Page 104 of 172 CASA Part 66 - Training Materials Only Specific Tests For some systems, specific tests are available. The purpose of these tests is to generate stimuli to various command devices such as actuators or valves. They can have a major effect on the aircraft, e.g., movement of slats or flaps, engine dry cranking. Use of the LRU and BITE concepts greatly reduce aircraft maintenance down time. After the appropriate repairs have been made, the system should be run through a complete operational check. The BITE will once again monitor the system and verify correct operation if the system has been properly repaired. © Aviation Australia BITE Flowchart 2022-07-22 B1-05b Digital Techniques / Electronic Instrument Systems Page 105 of 172 CASA Part 66 - Training Materials Only Maintenance Control Display Unit (MCDU) The MCDU contains a screen for data display, a keyboard, function keys, mode keys, and line keys, used to send commands to the connected systems. The MCDU allows access to the following system components: FM (Flight Management System) ACMS (Aircraft Condition Monitoring System) CMS (Central Maintenance System) SAT (Satellite Communication System) ATSU (Air Traffic Service Unit). © Aviation Australia Multifunction Control Display Unit (MCDU) 2022-07-22 B1-05b Digital Techniques / Electronic Instrument Systems Page 106 of 172 CASA Part 66 - Training Materials Only MCDU Utilisation Using the MCDU to access a specific system to review its status or perform tests requires a series of keystrokes as given in the example below and shown on the graphics. When powered up the MCDU displays the STATUS PAGE. Select MCDU Menu to display the MCDU MENU page. Aviation Australia Accessing the MCDU Status page Select the line key next to