4BE3.4 C4 Obj 4 PDF
Document Details
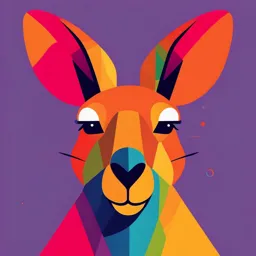
Uploaded by Reusl
Tags
Summary
This document provides specifications and codes for fittings on hot water heating boilers, covering pressure gauges, thermometers, safety relief valves, and other important components.
Full Transcript
OBJECTION 4 Describe the code requirements for fittings on hot water heating boilers. BPVC IV HOTWATER HEATING BOILER FITTINGS ASME BPVC IV distinguishes between hot water heating and hot water supply boilers. The followings fittings are required by ASME BPVC IV, on every hot water heating boiler:...
OBJECTION 4 Describe the code requirements for fittings on hot water heating boilers. BPVC IV HOTWATER HEATING BOILER FITTINGS ASME BPVC IV distinguishes between hot water heating and hot water supply boilers. The followings fittings are required by ASME BPVC IV, on every hot water heating boiler: • Pressure or altitude gauge • Thermometer • Safety relief valve • Temperature controls • Low water fuel cut-offs • Stop valves • Blowoff or drain connections • Expansion tanks Safety relief valves, temperature controls, low water fuel cut-offs, and expansion tanks have been covered elsewhere in detail. However, they deserve some brief mention here. Pressure or Altitude Gauges ASME BPVC IV Part HG-611 covers the requirement for pressure indicators for hot water heating boilers. This section includes the following: Each hot water heating boiler shall have a pressure or altitude gage connected to it or to its flow connection in such a manner that it cannot be shut off from the boiler except by a cock with tee or lever handle, placed on the pipe near the gage. The handle of the cock shall be parallel to the pipe in which it is located when the cock is open. The design and operation of pressure and altitude gauges is the same as that of steam pressure gauges. However, in hot water service, no siphon is required between the gauge and the boiler. This is because hot water boilers are completely filled with water, and generate no steam. Page 24 of 33 The term “altitude” gauge refers to pressure gauges that are calibrated in terms of height of water. These gauges indicate whether the hot water system is full. An altitude gauge has one pointer that is operated by the bourdon tube assembly, and another that is manually placed in a fixed position, to show the normal height of water in the system. In closed hot water heating systems, the pressure should always be greater than the altitude. If the pressure is less, the system is not full. As with steam heating boilers, the scale on the dial of the pressure or altitude gauge must be graduated to between 1 ½ and 3 ½ times the safety relief valve set pressure. Pressure gauges are also found before and after hot water circulation pumps. These gauges can be filled with a liquid that dampens the needle movement in the gauge. Thermometer ASME BPVC IV Part HG-612 requires all hot water heating boilers to have an easily read thermometer or temperature sensor (with display). The thermometer or sensor must indicate the hot water temperature at or near the boiler outlet. The thermometer must have a minimum reading of at least 20°C, and a maximum reading of at least 160°C, but not more than 205°C. Pressure and temperature gauges are commonly Figure 8 – Combination Temperature and Pressure Gauge combined into a single gauge, as shown in Figure 8. These gauges are available for numerous combinations of temperature and pressure. The gauge shown is designed for a hot water boiler with a normal operating pressure near 900 kPa, and a normal operating temperature of around 90°C. During normal operations, both needles are vertical. If the gauge includes an altitude scale, it is commonly referred to as a tridicator gauge. Page 25 of 33 Safety Relief Valves Safety relief valves have been covered extensively in Chapter 1 Pressure Relief Valves. However, hot water heating boilers have some unique requirements worthy of further discussion. ASME BPVC IV Part HG-400.2 covers the safety relief valve requirements for hot water boilers. Each hot water heating boiler must have at least one automatic reseating type safety relief valve, set to relieve at or below the maximum allowable working pressure of the boiler. However, when more than one safety relief valve is used, the additional valves may be set to higher than the MAWP. The higher set safety relief valve must not exceed the MAWP by: • 40 kPa, for boilers up to and including 400 kPa, or • 5%, for boilers exceeding 400 kPa Safety relief valves must be between DN 20 and DN 100 (NPS ¾ and NPS 4) in size. When a single safety relief valve is used, it must have sufficient relief capacity so that, with the fuel burning equipment operated at maximum capacity, the pressure cannot rise more than 10% above the MAWP. If two safety relief valves are installed, the overpressure cannot go higher than 10% above the set pressure of the highest set valve. Stop Valves ASME BPVC IV Part HG-710.2 states that stop valves must be placed in the supply and return pipe connections on all hot water heating boilers. This allows the boiler to be drained without emptying the entire piping system. However, in down feed hot water systems, it is possible to drain only the boiler, without draining the system. Therefore, Part HG710.2 says that when the boiler is located above the system, and can be drained without draining the system, stop valves are not required. For multiple boilers connected to a common system, Part HG-710.3 requires a stop valve in the supply and return pipe connection of each boiler, regardless of whether the system is up feed or down feed. Type of stop valves is covered under HG-710.4. The minimum pressure rating of all valves must be at least equal to the pressure stamped on the boiler. The temperature rating must not be less than 120°C. Page 26 of 33 During operation, the stop valves in the supply and return pipes should be wide open, and offer a minimum of resistance to the circulating water. A full port opening valve, such as the gate valve, ball valve, or butterfly is suitable for this purpose. Drain Valves Each hot water heating boiler must have a bottom connection fitted with a drain valve. This permits draining of the boiler for maintenance or extended layup. Expansion Tank The purpose of the expansion tank is to provide storage space for excess water (due to expansion) in the heating system. When the system is heated, the water expands. Excessive pressure buildup is prevented by allowing the excess water to flow into an expansion tank. When the water in the system cools down and decreases in volume, the water in the expansion tank flows back into the system again, keeping the system filled and under the correct pressure. ASME BPVC IV Part HG-709 covers the provisions for thermal expansion in hot water systems. Open Expansion Tank Open expansion tanks are rarely used today. They were limited to systems with a maximum water temperature of 80°C. They were, by necessity, installed above the highest point of the piping system. Page 27 of 33 Closed Expansion Tank Closed expansion tanks can be used in systems with high operating temperatures and pressures. They may be located anywhere in the heating system, but are often located in the boiler room. Expansion tanks are connected to the supply main, or directly to the top of the boiler. When the water in the boiler and system increases in temperature, it expands. The expanding water moves into the tank, compressing the air cushion inside the tank. For this reason, expansion tanks are also called cushion or compression tanks. ASME BPVC IV Part HG-709.2 addresses expansion tanks. It states that “an expansion tank shall be installed that will be consistent with the volume and capacity of the system.” HG-709.2 includes calculations for determining the required volume of the expansion tank, given the system volume, operating pressure, and operating temperature. If the system is designed for a working pressure of 200 kPa or less, the tank must be designed for a minimum hydrostatic test pressure of 520 kPa. This permits hydrostatic testing of the system without damaging the tank. Expansion tanks for systems designed to operate above 200 kPa must be pressure vessels, designed and constructed in accordance ASME BPVC VIII, Division 1. Page 28 of 33 Provisions must be made for draining the tank without emptying the system, except for prepressurized (bladder-style) tanks. Though not a requirement, installing isolation and drain valves in the piping to a bladder-style expansion tank is good practice. This permits servicing, replacing, and repairing the expansion tank without draining the heating system. Figure 9 shows an arrangement of a closed expansion tank. This tank is connected to the supply main by means of an air separator, which separates air bubbles from the water flow, and directs them into the tank. Figure 9 – Required Fittings and Controls for Hot Water Heating Boilers The expansion tank shown is equipped with a gauge glass and a drain valve. A shutoff valve is placed in the connecting line between the tank and the hot water supply header. This allows the tank to be drained without draining the system. Side Track Expansion tank operation and maintenance is covered extensively in Part B, Unit 4, Chapter 3 Operational Checks. Non-bladder style expansion tanks bring air into direct contact with the water. Over time, oxygen dissolves into the water in the expansion tank. When the heating system temperature drops, some oxygenated water enters the heating system as the water contracts. This can cause corrosion of steel piping and heating units. Bladder-style tanks and nitrogen-charged tanks eliminate this problem. Page 29 of 33