Boiler Fuel Supplies Control & Safety Devices PDF
Document Details
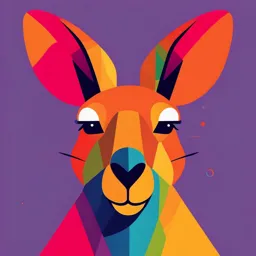
Uploaded by Reusl
CSA
Tags
Related
- ASME BPVC Section VI - Recommended Rules for Care and Operation of Heating Boilers PDF
- Boiler Low Water Level Fuel Cut-Off Equipment PDF
- CSA B51 Boiler, Pressure Vessel, and Piping Code PDF
- 4th Class Edition 3 Part B Boiler Plant Startup Chapter 1 PDF
- Session 01 Combustion Technologies for Bioenergy PDF
- Marine Engg Midterm Reviewer PDF
Summary
This document describes the operation of control and safety devices for boiler fuel supplies. It focuses on natural gas and oil fuel trains, outlining components and their functions, emphasizing safety regulations and codes from organizations like CSA, ASME, and NFPA. The information pertains to professional engineering.
Full Transcript
Objective 1 Describe the operation of control and safety devices found on the boiler fuel supplies Burner systems are comprised of numerous parts that function systematically to ensure combustion safety. The existence of these components is mandated by various construction and design codes, publish...
Objective 1 Describe the operation of control and safety devices found on the boiler fuel supplies Burner systems are comprised of numerous parts that function systematically to ensure combustion safety. The existence of these components is mandated by various construction and design codes, published by organizations such as CSA, ASME, and NFPA. NATURAL GAS FUEL TRAIN Figure 1 shows a single line diagram of a natural gas fuel train, assembled according to CSA B149.3 Code for the Field Approval of Fuel-Related Components on Appliances and Equipment. This code does not cover appliances (including boilers) that are constructed and designed to meet an approved standard. Rather, it covers: 1. Natural gas and propane burners installed on appliances for which no approval standard exists. 2. Existing certified burners that are upgraded or modified. For this reason, CSA B149.3 serves as a very good guideline for the layout of combustion safety components, especially those found on boilers. Note that Figure 1 differs from other fuel trains shown in the PanGlobal Fourth Class text. There are several reasons for this. Fuel trains become more complex as fuel pressures increase, and as fuel-firing capacity increases. Other fuel trains in the Fourth Class text have been for smaller or larger capacity burners, and may have been configured to meet different codes. The differences may be due to the fact that the ASME CSD-1, NFPA-85, and CSA B149.3 codes, though similar in many respects, differ somewhat in the requirements for, and placement of, fuel train components. Page 3 of 49 The diagram in Figure 1: 1. Is based on a Canadian code, which (in Canada) takes precedence over international codes. 2. Is a fuel train configuration suitable for burners with inputs greater than 3.663 MW (12 500 000 Btuh input or 300 BoHP output). Boilers of this size are common in Third and Second Class plants. In these plants, Fourth Class Power Engineers can serve as Shift Engineers and Assistant Shift Engineers. It is therefore reasonable for those studying Fourth Class Power Engineering to be familiar with these fuel trains. Figure 1 – Natural Gas Fuel Train for Boilers over 3000 kW Output (CSA B149.3) Page 4 of 49 The following comments refer to Figure 1. Note that each component shown serves a critical safety role. Nothing is required that does not serve a specific purpose. Side Track Manual fuel train valves are discussed in Part A Unit 7 Chapter 2 Introduction to Energy Plant Valves. Automatic fuel safety shut-off valves are covered in Part A Unit 12 Chapter 2 Fuel Delivery and Firing Systems. Gas Supply and Piping For burners to operate correctly, they must be supplied with fuel at the correct pressure. The CSA B41 149.1 and Propane Installation code limits the maximum fuel pressure inside buildings of various occupancies. Fuel piping must be properly sized to deliver the amount of fuel the burner can consume, without excessive pressure drop through the fuel train. Gas piping is, with few exceptions, constructed of steel pipe. Smaller diameter pipe may use threaded connections. Welded connections are used for larger diameter and higher-pressure pipe. Main and Pilot Manual Shut-Off Valves (A and K) Manual fuel cocks are quarter-turn lubricated plug valves. These valves serve as isolation points for fuel train maintenance. As well, the main manual shut-off valve can be used to test the operation of the low gas pressure cut-off switch. Caution Never open the main shut-off valve when the pilot manual shut-off valve is closed! Fuel Strainer (B) Often, existing fuel lines are modified for the installation of new equipment. Drilling, threading, and cutting may introduce debris into fuel lines, which may affect the operation of fuel pressure regulators and control valves. The fuel strainer catches debris before it can have a negative effect. Page 5 of 49 Fuel Pressure Regulators (C) The pressure regulators ensure the proper fuel pressure at each of the main and pilot burners. Excessive pressure could lead to over firing. Inadequate pressure may lead to flame instability. Pressure Relief Valves (D) If the pressure regulators fail to reduce the fuel pressure, the burner piping components can over pressurize and fail. The pressure relief valves protect the pilot and main burner controls from excessive fuel pressure. Low (PSLL) and High (PSHH) Gas Pressure Cut-off Switches (E and H) These switches shut down and lock out the burner if the fuel pressure rises above, or drops below, that required by the burner manufacturer. This prevents flame instability, over-firing, and lifting flames. All unstable flame conditions may lead to furnace explosion. The PSHH high gas pressure cut-off switch (HGPCO) is located just upstream of the input flow control valve. The PSLL low gas pressure cut off switch (LGPCO) is located downstream of the pressure regulator and pressure relief valve. Page 6 of 49 The following is paraphrased from CSA B149.3 parts 9.5.1 and 9.5.2: For appliances with inputs in excess of 120 kW (400 000 Btuh), a low gas pressure safety device shall be installed and shall shut off if the supply of gas if the pressure at the point of connection drops below 50% of the lowest normal operating pressure. The device shall be installed downstream of the pressure regulator, upstream of the safety shut-off valve or valves, and upstream of the flow control valve. Where the failure or an outlet pressure adjustment of the pressure regulator results in unsafe operation, a high gas pressure safety device shall be installed downstream of the pressure regulator and shall initiate shut-off of the supply of gas when the gas pressure at the high gas pressure safety device exceeds 125% of the normal operating pressure at the maximum firing rate. Figure 2 shows a gas pressure cut-off Figure 2 – Fuel Pressure Cut-off Switch switch. A pressure gauge is installed on the test port so that operators can monitor the pressure while the burner is in operation, and observe the pressure at which the cut-off trips. Main Fuel Safety Shut-Off Valves (SSOVs) (F) Safety shut-off valves (SSOVs) are essential components on the fuel supply system. SSOVs prevent the accumulation of explosive fuel-air mixtures in furnaces when they are not in operation. In accordance with CSA requirements, these valves must be certified to CSA 6.5 CSA 6.5-2015 Automatic Valves for Gas Appliances. When selecting an SSOV, the valve must bear this approval symbol. Main fuel SSOVs may be slow-opening diaphragm, solenoid, or Hydramotor valves. Though they are slow-opening, they respond to unsafe conditions by closing quickly. Figure 3 shows an SSOV on a main gas fuel train. An indicator at the front of the actuator indicates whether the valve is open or closed. A high gas pressure cut-off switch and a pressure gauge can be seen upstream of the SSOV. Page 7 of 49 Figure 3 – Main SSOV Main SSOVs shut off the fuel flow to the main burner under the following conditions: a) Normal operating limits (boiler pressure or temperature) are satisfied. b) An unsafe condition exists (low water, high pressure, high temperature, loss of combustion air, flame failure, and so on). The fuel train shown in Figure 1 requires two SSOVs with proof-of-closure switches to meet CSA B149.3. These switches are sensitive to the valve stem position. If the SSOV fails to close completely, fuel gas may leak into the combustion chamber. The proof-ofclosure switches prevent the boiler from proceeding with an ignition sequence if an SSOV does not fully close. Safety Vent Valve (G) The safety vent valve is located between the main fuel SSOVs. Safety vent valves are typically fast-acting, normally-open solenoid valves. Depending on the burner capacity and fuel pressure, fuel trains must be equipped with a double block-andbleed arrangement on the main (and sometimes the pilot) fuel lines. When the main SSOVs shut, the safety vent valve fails open, and bleeds trapped fuel to the atmosphere. In this way, if the upstream SSOV leaks fuel, its pressure is immediately reduced to atmospheric. At atmospheric pressure, the fuel cannot leak past the downstream SSOV and accumulate in the furnace. Page 8 of 49 Figure 4 shows a normally-open solenoid valve, used as the pilot safety vent valve for a large natural gas-fired boiler. Figure 4 – Pilot Safety Vent Valve Input Flow Control Valve (Firing Rate Control) (I) Fully modulating burners must control fuel in accordance with the load demand. The inlet flow control valve is not strictly speaking a safety device. However, its location is important to permit the correct operation of other safety controls. The firing rate control valve is placed downstream of the low gas pressure cut-off switch. This is so that the LGPCO does not actuate at low firing rates. The firing rate control valve is also located downstream of the HGPCO. If it was not, the high gas pressure cut-off could not detect high fuel pressure conditions due to the pressure drop across the firing rate control valve. Main Test Firing and Pilot Test Firing Valves (J and M) Test firing valves are lubricated quarter-turn plug valves. They are used to test the operation of the flame detection devices, and the high fuel pressure cut-off. As well, the test firing valve is often used as a fuel train isolation point. Page 9 of 49 The main test firing valve shown in Figure 5 has a switch that detects whether the test firing valve is open or closed. The burner cannot begin a start-up sequence when this valve is open. It must be kept closed during the purge period and the pilot flame trial for ignition period. It is opened by hand (gradually) at the beginning of the main flame trial for ignition period. Figure 5 – Main Test Firing Valve with Supervisory Switch Caution Never open the main shut-off valve when the pilot manual shut-off valve is closed! Pilot Safety Shut-Off Valves (L) Pilot SSOVs are usually fast-acting automatic solenoid valves. They shut off the fuel flow to the pilot burner under the following circumstances: a) Flame failure during the pilot or main flame trial for ignition period. b) Normal pilot interruption at the end of the pilot flame trial for ignition period. The valves shown in Figure 1 do not have proof of closure. They are arranged as “double blocks” without a bleed. This is considered adequate because pilot burners have a small fuel throughput compared to the main burner (less than 5%). Therefore, the amount of fuel that can bleed into the furnace through a pilot fuel train is quite small compared to the amount of gas that can enter through the main fuel line. Page 10 of 49 Fuel Pressure Test Ports (N) Test ports are located at various locations on the fuel train, so that instruments can be connected to check, adjust, or monitor the fuel pressure. Each port is equipped with a quarter-turn isolation valve and a pipe cap. Pressure gauges or electronic instruments can be installed at these points. In this way, the fuel pressure conditions can be monitored, and adjustments made, when the burner is in operation. Often, these test ports have permanently installed pressure gauges. Figure 6 shows the main fuel train of a boiler with a similar configuration to the requirements shown in Figure 1. Two main SSOVs are visible. The bleed line between the SSOVs is obscured by the piping between the main SSOVs. Figure 6 – Natural Gas Fuel Train Suitable for Boilers over 3000 kW (300 BoHP) Page 11 of 49 OIL FUEL TRAIN Fuel oil train components are similar in function to those used in natural gas service. A pressure regulator maintains fuel pressure at the nozzle. A pressure relief valve diverts excessive fuel pressure back to the oil tank or suction line. A low fuel pressure cut-off shuts down the burner if the fuel pressure drops below that required for flame stability. Safety shut-off valves stop the flow of oil to the burner when operating limits are reached, or under adverse combustion conditions. However, fuel oil trains may have unique components not found on fuel gas trains. These include: • Fuel filter • Fuel pump • Low oil temperature cut-off switch • Low atomizing media cut-off switch. Figure 7 shows a fuel oil train acceptable to ASME CSD-1 Controls and Safety Devices for Automatically Fired Boilers. This code covers all automatically fired heating and power boilers up to 3.663 MW input (300 BoHP output). Figure 7 – Fuel Oil Train for Automatically Fired Boilers (ASME CSD-1) Page 12 of 49 Fuel Filter Oil burner nozzles are very sensitive to plugging from suspended fuel contaminants. Contaminants can adversely affect the spray pattern and quality of atomization. Poor atomization leads to incomplete combustion, and create toxic and explosive carbon monoxide. The resulting poor flame patterns can cause flames to impinge on heat transfer surfaces or refractory, and cause damage. Strainers do not provide adequate protection for oil burners. Therefore, filters are used. Fuel Pump Oil trains must have fuel pumps to provide the necessary flow and pressure for proper atomization at the maximum firing rate. Low Oil Temperature Cut-off Switch The low temperature cut-off switch is a temperatureactuated device. It stops the flow of fuel to a burner that fires oil which requires preheating, such as number 6 fuel oil. This fuel must be preheated to reduce its viscosity so that it can be properly atomized by the burner. If the viscosity is too high, poor atomization will result. Poor atomization leads to incomplete combustion, and the creation of toxic and explosive carbon monoxide. The resulting poor flame patterns can cause flames to impinge on heat transfer surfaces or refractory, and cause damage. The low oil temperature cut-off is a pre-ignition interlock. It prevents the burner from starting when the fuel oil temperature falls below the lower end of the viscosity range of the fuel, as recommended by the burner manufacturer. For an operating boiler, this switch causes safety shutdown. This allows the fuel to recirculate through the oil heater, in order to re-establish the necessary oil temperature. Page 13 of 49 Low Atomizing Media Cut-Off Switch Atomizing media is essential for burners designed to use atomizing air or steam. Poor atomization leads to incomplete combustion and the creation of toxic and explosive carbon monoxide. Resulting poor flame patterns can cause flames to impinge on heat transfer surfaces or refractory, causing damage. For a steam or air atomized burner, the atomizing media pressure is supervised by an interlock switch. If the atomizing media pressure falls below the manufacturer’s design pressure, this switch causes safety shutdown and lockout. Page 14 of 49