Welding Inspection Technology PDF
Document Details
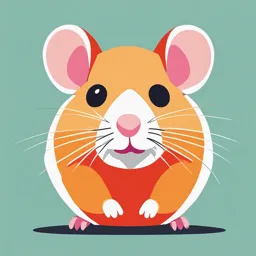
Uploaded by BestPerformingPlateau
null
Tags
Summary
This document explains different types of metal welding processes, including GMAW (Gas Metal Arc Welding), FCAW (Flux Cored Arc Welding), and GTAW (Gas Tungsten Arc Welding). It provides operational details and advantages of each.
Full Transcript
WELDING INSPECTION TECHNOLOGY CHAPTER 3—METAL JOINING AND CUTTING PROCESSES Figure 3.14—Modes of Metal Transfer: (a) Spray, (b) Globular, and (c) Short Circuiting (Pulsed Arc Not Shown) overall operator productivity is greatly improved. This efficiency is further increased by the fact that the co...
WELDING INSPECTION TECHNOLOGY CHAPTER 3—METAL JOINING AND CUTTING PROCESSES Figure 3.14—Modes of Metal Transfer: (a) Spray, (b) Globular, and (c) Short Circuiting (Pulsed Arc Not Shown) overall operator productivity is greatly improved. This efficiency is further increased by the fact that the continuous spool of wire doesn’t require changing nearly as often as the individual electrodes used in SMAW. All of this increases the amount of time in which actual production welding can be accomplished. increased flow rates may actually draw atmospheric gases into the weld zone. Another disadvantage is that the equipment required is more complex than that used for shielded metal arc welding. This increases the possibility that a mechanical problem could cause weld quality problems. Such things as worn gun liners and contact tubes can alter the feeding and electrical characteristics to the point that defective welds can be produced. The chief advantage of GMAW is lbs/hr of metal deposited, which reduces labor costs. Another benefit of gas metal arc welding is that it is a relatively clean process, primarily due to the fact that there is no flux present. With the existence of numerous types of electrodes, and equipment which has become more portable, the versatility of gas metal arc welding continues to improve. One additional benefit relates to the visibility of the process. Since no slag is present, the welder can more easily observe the action of the arc and molten puddle to improve control. The primary inherent problems have already been discussed. They are: porosity due to contamination or loss of shielding, incomplete fusion due to the use of short circuiting transfer on heavy sections, and arc instability caused by worn liners and contact tips. Although such problems could be very harmful to weld quality, they can be alleviated if certain precautions are taken. To reduce the possibility of porosity, parts should be cleaned prior to welding and the weld zone protected from any excessive wind using enclosures or windbreaks. If porosity persists, the gas supply should be checked to assure that there is not excessive moisture present. While the use of shielding gas instead of flux does provide some benefits, it can also be thought of as a limitation, since this is the primary way in which the molten metal is protected and cleaned during welding. If the base metal is excessively contaminated, the shielding gas alone may not be sufficient to prevent the occurrence of porosity. GMAW is also very sensitive to drafts or wind which tend to blow the shielding gas away and leave the metal unprotected. For this reason, gas metal arc welding is not well suited for field welding. The problem of incomplete fusion is a real one for GMAW, especially when short circuiting transfer is used. This is due in part to the fact that this is an “open arc” process since no flux is used. Without this layer of shielding from the arc heat, the increased heat intensity can lead the welder to believe that there is a tremendous amount of heating of the base metal. Such a feeling can be very deceiving, so the welder must be aware of this condition and assure that the arc is being directed to ensure melting of the base metal. It is important to realize that simply increasing the gas flow rate above recommended limits will not necessarily guarantee that adequate shielding will be provided. In fact, high flow rates cause turbulence and may tend to increase the possibility of porosity because these 3-13 CHAPTER 3—METAL JOINING AND CUTTING PROCESSES WELDING INSPECTION TECHNOLOGY Flux Cored Arc Welding (FCAW) Finally, equipment should be well maintained to alleviate the problems associated with unstable wire feeding. Each time a roll of wire is replaced, the liner should be blown out with clean compressed air to remove particles which could cause jamming. If a wire feed problem persists, the liner should be replaced. The contact tube should be changed periodically as well. When it becomes worn, the point of electrical contact changes so that the electrode extension is increased without the welder knowing it. The electrode extension is also referred to as the contact tube to electrode end distance, as illustrated in Figure 3.15. Gas Nozzle It shows the tubular electrode being fed through the contact tube of the welding gun to produce an arc between the electrode and the workpiece. As the welding progresses, a bead of solidified weld metal is deposited. Covering this solidified weld metal is a layer of slag, as occurs for shielded metal arc welding. With flux cored arc welding, there may or may not be an externally-supplied shielding gas, depending upon what type of electrode is used. Some electrodes are designed to provide all of the necessary shielding from the internal flux, and are referred to as self-shielding. Other electrodes require additional shielding from an auxiliary shielding gas. With FCAW, as with other processes, there is a system for identification of the various types of welding electrodes, illustrated in Figure 3.18. A review of each electrode type shows that the designations refer to the polarity, shielding requirements, chemical composition and welding position. Contact Tube Contact Tube Setback Workpiece The next process to be described is flux cored arc welding. This is very similar to gas metal arc welding except that the electrode is tubular and contains a granular flux instead of the solid wire used for gas metal arc welding. The difference can be noted in Figure 3.16, which shows a weldment welded with the self shielded FCAW process and a close-up of the arc region during welding, and Figure 3.17 shows the dual shielded FCAW process. Standoff Distance Electrode Extension Stickout Consumable Electrode Identification begins with the letter “E” which stands for electrode. The first number refers to the minimum tensile strength of the deposited weld metal in ten thousands of Figure 3.15—Gas Metal Arc Welding Gun Nomenclature WIRE GUIDE AND CONTACT TUBE TUBULAR ELECTRODE SOLIDIFIED SLAG MOLTEN SLAG POWDERED METAL, VAPOR FORMING MATERIALS, DEOXIDIZERS AND SCAVENGERS ARC SHIELD COMPOSED OF VAPORIZED AND SLAG FORMING COMPOUNDS ARC AND METAL TRANSFER WELD POOL WELD METAL Figure 3.16—Self-Shielded Flux Cored Arc Welding 3-14 DIR WE ECT LD ION ING OF WELDING INSPECTION TECHNOLOGY CHAPTER 3—METAL JOINING AND CUTTING PROCESSES Figure 3.17—Dual-Shielded Flux Cored Arc Welding Strength Electrode the letter “T” which refers to a tubular electrode. This is followed by a hyphen and then another number which denotes the particular grouping based upon the chemical composition of deposited weld metal, type of current, polarity of operation, whether it requires a shielding gas, and other specific information for the category. Tubular Position Chemical/Operating Characteristics With this identification system, it can be determined whether or not a certain classification of electrode requires an auxiliary shielding gas. This is important to the welding inspector since flux cored arc welding can be performed with or without an external shielding gas. Figure 3.19 shows the two nozzle types. Figure 3.18—FCAW Electrode Identification System Some electrodes are formulated to be used without any additional shielding other than that contained within the electrode. They are designated by the suffixes 3, 4, 6, 7, 8, 10, 11, 13, and 14. However, those electrodes having the numerical suffixes 1, 2, 5, 9, or 12 require some external shielding to aid in protecting the molten metal. Both types offer advantages, depending upon the appli- pounds per square inch, so a “7” means that the weld metal tensile strength is at least 70 000 psi. The second digit is either a “0” or a “1.” A “0” means that the electrode is suitable for use in the flat or horizontal fillet positions only, while a “1” describes an electrode which can be used in any position. Following these numbers is 3-15 CHAPTER 3—METAL JOINING AND CUTTING PROCESSES WELDING INSPECTION TECHNOLOGY Figure 3.19—FCAW Guns for Gas-Shielding (Top) and Self-Shielding Electrodes (Bottom) cation. Additionally, the suffixes G and GS refer to multiple-pass and single-pass respectively. For example, the self-shielded types are better suited for field welding where wind could result in a loss of gaseous shielding. Gas shielded types are typically used where the need for improved weld metal properties warrants the additional cost. Gases typically used for flux cored arc welding are CO2, or 75% Argon—25% CO2, but other combinations of gases are available. FCAW is further defined as FCAW-G, (gas shielded) and FCAW-S, (self shielded). The equipment used for FCAW is essentially identical to that for GMAW, as shown in Figure 3.20. Some differences might be higher current capacity guns and power sources, lack of gas apparatus for self-shielded electrodes, and knurled wire feed rolls. Like GMAW, FCAW uses a constant voltage direct current power supply. Depending on the type of electrode, the operation may be DCEP (1, 2, 3, 4, 6, 9, 12) or DCEN (7, 8, 10, 11, 13, 14) or both DCEN or DCEP (5). Figure 3.20—Gas-Shielded (Top) and Self-Shielded (Bottom) Flux Cored Arc Welding Equipment The flux cored arc welding process is rapidly gaining acceptance as the welding process of choice in some industries. Its’ relatively good performance on contaminated surfaces and increased deposition rates have helped flux cored arc welding replace SMAW and GMAW for many applications. The process is used in many industries where the predominant materials are ferrous. It can be used with satisfactory results for both shop and field applications. Although the majority of the electrodes produced are ferrous (for both carbon and stainless steels), some nonferrous ones are available as well. Some of the stainless types actually employ a car- bon steel sheath surrounding the internal flux which contains the granular alloying elements such as chromium and nickel. FCAW has gained wide acceptance because of the many advantages it offers. Probably the most significant 3-16 WELDING INSPECTION TECHNOLOGY CHAPTER 3—METAL JOINING AND CUTTING PROCESSES feeding apparatus. As is the case for GMAW, lack of maintenance can cause wire feeding problems which may affect the quality of the weld. FCAW is also subject to typical discontinuities including incomplete joint penetration, slag inclusions, and porosity. advantage is that it provides high productivity in terms of the amount of weld metal that can be deposited in a given period of time. It is among the highest for a hand-held process. This is aided by the fact that the electrode comes on continuous reels which increases the “arc time” just as with gas metal arc welding. The process is also characterized by an aggressive, deeply penetrating arc which tends to reduce the possibility of fusion-type discontinuities. Since it is typically used as a semiautomatic process, the skill required for operation is somewhat less than would be the case for a manual process. With the presence of a flux, whether assisted by a gaseous shield or not, FCAW is capable of tolerating a greater degree of base metal contamination than is GMAW. For this same reason, FCAW lends itself well to field situations where the loss of shielding gas due to winds would greatly hamper GMAW quality. Gas Tungsten Arc Welding (GTAW) The next process to be discussed is gas tungsten arc welding, which has several interesting differences when compared to those already discussed. Figure 3.21 shows the basic elements of the process. The most significant feature of GTAW is that the electrode used is not intended to be consumed during the welding operation. It is made of pure or alloyed tungsten which has the ability to withstand very high temperatures, even those of the welding arc. Therefore, when current is flowing, there is an arc created between the tungsten electrode and the work. It is important to realize that this process does have certain limitations of which the inspector should be aware. First, since there is a flux present, there is a layer of solidified slag which must be removed before depositing additional layers of weld or before a visual inspection can be made. Due to the presence of this flux, there is a significant amount of smoke generated during welding. Prolonged exposure in unvented areas could prove to be unhealthy for the welder. This smoke also reduces the welder’s visibility to the point where it may be difficult to properly manipulate the arc in the joint. Although smoke extractor systems are available, they tend to add bulk to the gun which increases the weight and decreases visibility. They also may disturb the shielding if an external gas is being used. DIRECTION OF WELDING BACK CAP ELECTRODE LEAD TORCH BODY SHIELDING GAS IN COLLET BODY GAS NOZZLE NONCONSUMABLE TUNGSTEN ELECTRODE GAS SHIELD FILLER METAL Even though FCAW is considered to be a smoky process, it is not as bad as SMAW in terms of the amount of smoke generated for a given amount of deposited weld metal. The equipment required for FCAW is more complex than that for SMAW, so the initial cost and the possibility of machinery problems may limit its acceptability for some situations. MOLTEN WELD METAL ARC SOLIDIFIED WELD METAL As with any of the processes, FCAW does have some inherent problems. The first has to do with the flux. Due to its presence, there exists a possibility that the solidified slag could become trapped in the finished weld. This could be due to either improper interpass cleaning or improper technique. With FCAW, it is critical that the travel speed is fast enough to maintain the arc on the leading edge of the molten puddle. When the travel speed is slow enough to allow the arc to be toward the middle or back of the puddle, molten slag may roll ahead of the puddle and become trapped. Another inherent problem involves wire Figure 3.21—Gas Tungsten Arc Welding 3-17 CHAPTER 3—METAL JOINING AND CUTTING PROCESSES WELDING INSPECTION TECHNOLOGY typically used for the welding of aluminum because the alternating current will increase the cleaning action to improve weld quality. Square Wave AC welding power sources have been developed for welding Aluminum. Square Wave machines with AC balance control feature adjustable penetration and cleaning action while increasing arc stability on aluminum alloys, and help eliminate tungsten spitting and arc rectification. DCEN is most commonly used for the welding of steels. Figure 3.22 illustrates the effects of these different types of current and polarity in terms of penetration ability, oxide cleaning action, heat balance of the arc, and electrode currentcarrying capacity. When filler metal is required, it must be added externally, usually manually, or with the use of some mechanical wire feed system. All of the arc and metal shielding is achieved through the use of a gas (typically inert) which flows out of the nozzle surrounding the tungsten electrode. The deposited weld bead has no slag requiring removal because no flux is used. As with the other processes, there is a system whereby the various types of tungsten electrodes can be easily identified. The designations consist of a series of letters starting with an “E” which stands for electrode. Next comes a “W” which is the chemical symbol for tungsten. These letters are followed by letters and numbers which describe the alloy type. Since there are only several different classifications, they are more commonly differentiated using a color code system. Table 3.3 shows the classifications and the appropriate color code. As mentioned, most GTAW utilizes inert gases for shielding. By inert, we mean that the gases will not combine with the metal, but will protect it from contaminants. Argon and helium are the two inert gases used in GTAW. Some mechanized stainless steel or nickel welding applications use a shielding gas consisting of argon and a small amount of hydrogen, but this represents a very minor portion of the gas tungsten arc welding which is performed. The presence of the thoria or zirconia aids in improving the electrical characteristics by making the tungsten slightly more emissive. This simply means that it is easier to initiate an arc with these thoriated or zirconiated types than is the case for pure tungsten electrodes. Pure tungsten is quite often used for the welding of aluminum because of its ability to form a “ball” end when heated. With a ball end instead of a sharper point, there is a lower concentration of current which reduces the possibility of damaging the tungsten. The EWTh-2 type is most commonly used for the joining of ferrous materials. The equipment required for GTAW has as its primary element a power source like the one used for SMAW, that is, a constant current type. Since there is a gas present, it is now necessary to have apparatus for its control and transmission. Figure 3.23 shows a typical gas tungsten arc welding setup. The filler metals for GTAW have the same designation as for GMAW filler metals (ER70S-3, ER70S-6, etc.). The bare, solid filler wire usually is purchased in 36 in lengths, with identification on each end. An added feature of this welding system, which is not shown, is a high frequency generator which aids in the initiation of the welding arc. In DCEN the high frequency aids in arc initiation, and after the arc is initiated it turns off. When using AC current the high frequency remains on all the time to help initiate the arc every half cycle during current reversals. In order to alter the welding heat during the welding operation, a remote current control may also be attached. It can be foot-operated or controlled by some device mounted on the torch itself. This is particularly useful for welding thin materials and open root pipe joints, where instantaneous control is necessary. GTAW can be performed using DCEP, DCEN, or AC. The DCEP will result in more heating of the electrode, while the DCEN will tend to heat the base metal more. AC alternately heats the electrode and base metal. AC is Table 3.3 AWS Tungsten Electrode Classification Class EWP EWCe-2 EWLa-1 EWLa-1.5 EWLa-2 EWTh-1 EWTh-2 EWZr Alloy Pure tungsten 1.8%–2.2% cerium oxide 1% lanthanum oxide 1.5% lanthanum oxide 2.0% lanthanum oxide 0.8%–1.2% thorium oxide 1.7%–2.2% thorium oxide 0.15%–0.40% zirconium oxide There are numerous applications for GTAW in many industries. It is capable of welding virtually all materials because the electrode is not melted during the welding operation. Its ability to weld at extremely low currents makes gas tungsten arc welding suitable for use on the thinnest (down to 0.005 in) of metals. It’s typically clean and controllable operation causes it to be the perfect choice for extremely critical applications such as those found in the aerospace, food and drug processing, petrochemical, and power piping industries. Color Green Orange Black Gold Blue Yellow Red Brown 3-18 WELDING INSPECTION TECHNOLOGY CHAPTER 3—METAL JOINING AND CUTTING PROCESSES DC - s on Ion s + + + ctr s - on - Ele - ctr + + + s - on - Ele - ctr + + + AC (balanced) Positive Ele ELECTRON AND ION FLOW Negative Ion s ELECTRODE POLARITY DC Ion s CURRENT–TYPE PENETRATION CHARACTERISTICS OXIDE CLEANING ACTION HEAT BALANCE IN THE ARC (approx.) PENETRATION ELECTRODE CAPACITY NO YES YES - Once every half cycle 70% At work end 30% At electrode end 30% At work end 70% At electrode end 50% At work end 50% At electrode end Deep; narrow Shallow; wide Medium Excellent (e.g., 1/8 in [3.18 mm]–400 A) Poor (e.g., 1/4 in [6.35 mm]–120 A) Good (e.g., 1/8 in [3.18 mm]–225 A) Figure 3.22—Effect of Welding Current Type on Penetration for Gas Tungsten Arc Welding The principal advantage of GTAW lies in the fact that it can produce welds of high quality and excellent visual appearance. Also, since no flux is used, the process is quite clean and there is no slag to remove after welding. As mentioned before, extremely thin sections can be welded. Due to the nature of its operation, it is suitable for welding most metals, many of which are not as easily welded using other welding processes. If joint design permits, these materials can be welded without the use of additional filler metal. When required, numerous types of filler metals exist in wire form for a wide range of metal alloys. In the case where there is no commercially-available wire for a particular metal alloy, it is possible to produce a suitable filler metal by simply shearing a piece of identical base metal to produce a narrow piece which can be hand-fed into the weld zone just as if it were a wire. Contrasting these advantages are several disadvantages. First, GTAW is among the slowest of the available welding processes. While it produces a clean weld deposit, it is also characterized as having a low tolerance for contamination. Therefore, base and filler metals must be extremely clean prior to welding. When used as a manual process, gas tungsten arc welding requires a high skill level; the welder must coordinate the arc with one hand while feeding the filler metal with the other. GTAW is normally selected in situations where the need for very Figure 3.23—Gas Tungsten Arc Welding Equipment 3-19 CHAPTER 3—METAL JOINING AND CUTTING PROCESSES WELDING INSPECTION TECHNOLOGY high quality warrants additional cost to overcome these limitations. Nozzle Contact Tube Electrode One of the inherent problems associated with this method has to do with its inability to tolerate contamination. If contamination or moisture is encountered, whether from the base metal, filler metal or shielding gas, the result could be porosity in the deposited weld. When porosity is noted, this is a sign that the process is out of control and some preventive measures are necessary. Checks should be made to determine the source of the contamination so that it can be eliminated. Slag Molten Flux Flux in from Hopper Granular Flux Blanket Solidified Weld Metal Molten Weld Metal Arc Path Base Metal Direction of Travel Another inherent problem which is almost totally confined to the GTAW process is that of tungsten inclusions. As the name implies, this discontinuity occurs when pieces of the tungsten electrode become included in the weld deposit. Tungsten inclusions can occur due to a number of reasons, and several are listed below. Figure 3.24—Submerged Arc Welding 1. Contact of electrode tip with molten metal; electrode to facilitate the protection of the molten metal. As the welding progresses, in addition to the weld bead, there is a layer of formed slag and still-granular flux covering the solidified weld metal. The slag must be removed and is usually discarded. The granular flux that has not been used in the weld can be salvaged and mixed with new flux for reuse. Care must be taken to maintain the original flux granular composition. 2. Contact of filler metal with hot tip of electrode; 3. Contamination of the electrode tip by spatter; 4. Exceeding the current limit for a given electrode diameter or type; 5. Extension of electrodes beyond their normal distances from the collet, resulting in over-heating of the electrode; Since SAW uses a separate electrode and flux, there are numerous combinations available for specific applications. There are two general types of combinations which can be used to provide an alloyed weld deposit: an alloy electrode with a neutral flux, or a mild steel electrode with an alloy flux. Therefore, to properly describe the filler material for SAW, the American Welding Society identification system consists of designations for both the electrode and flux. Figure 3.25 shows what the various parts of the electrode/flux classification system signify, with two examples. 6. Inadequate tightening of the collet; 7. Inadequate shielding gas flow rates or excessive wind drafts resulting in oxidation of the electrode tip; 8. Defects such as splits or cracks in the electrode; 9. Use of improper shielding gases; and 10. Improper grinding of the electrode tip. Submerged Arc Welding (SAW) The equipment used for submerged arc welding consists of several components, as shown in Figure 3.26. Since this process can be used as a fully mechanized or semiautomatic method (see Figure 3.27), the equipment used for each is slightly different. In the semiautomatic method the wire and flux is feed through a gun and the operator provides the travel along the joint. This is called “hand held SAW.” In either case, however, some power source is required. Although most submerged arc welding is performed with a constant voltage power source, there are certain applications where a constant current type is preferred. As with gas metal arc welding and flux cored arc welding, a wire feeder forces the wire through the cable liner to the welding torch. The last of the more common welding processes to be discussed is submerged arc welding. This method is typically the most efficient one mentioned so far in terms of the rate of weld metal deposition. SAW is characterized by the use of a continuously-fed solid wire electrode which provides an arc that is totally covered by a layer of granular flux; hence the name “submerged” arc. Figure 3.24 shows how a weld is produced using this process. As mentioned, the wire is fed into the weld zone much the same way as with gas metal arc welding or flux cored arc welding. The major difference, however, is in the method of shielding. With submerged arc welding, a granular flux is distributed ahead of or around the wire 3-20