Air-jet Picking - Weaving Mechanisms PDF
Document Details
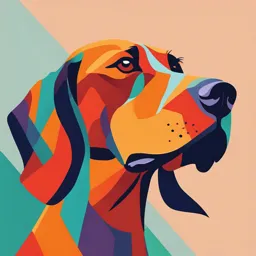
Uploaded by MercifulKazoo
Textile Institute of Pakistan, Karachi
Shakeel Ahmad Paracha
Tags
Summary
This document provides a detailed technical study of air-jet picking, a weaving mechanism. It describes the process, major components, and diagrams associated with the process including the supply package, cone stand, pre-winder, and various nozzles. It is likely part of a textile engineering or technology curriculum.
Full Transcript
Textile Institute of Pakistan, Karachi. TEXT312 (Weaving Mechanisms) The Air-jet Picking Definition o The process of drawing filling yarn from the supply package & inserting this filling yarn through warp shed with the help of air stream/air-jet is c...
Textile Institute of Pakistan, Karachi. TEXT312 (Weaving Mechanisms) The Air-jet Picking Definition o The process of drawing filling yarn from the supply package & inserting this filling yarn through warp shed with the help of air stream/air-jet is called air-jet Picking. The timing diagram of main & sub-nozzles Prepared By: Shakeel Ahmad Paracha Page 15 of 29 Textile Institute of Pakistan, Karachi. TEXT312 (Weaving Mechanisms) Air-jet Picking Major Parts Supply Package o The package may cone or cheese and fitted on cone stand. o The yarn is unwounded by over end withdrawal. o The weight of supply package may be 2.5 - 6.25 lbs. depending upon count of yarn. o The weight of filament yarn package may be 8 - 10 lbs. Cone Stand o It is used to keep the cones to feed the yarn to the pre-winder. o The cones are mounted on rubber pegs on cone stand. o There is a disc tensioner through which yarn is passed through before feeding to the pre- winder. o The function of disc tensioner is to provide the necessary tension to yarn during unwinding from the cone. o The disc tensioner is also used as a guide for the passage of yarn. Supply Package Cone Stand Rubber Peg Disc Tensioner Pre-winder/Weft Accumulator/Weft Feeder o It is used to feed the yarn to the main nozzle/fixed nozzle. o There is a magnetic pin which detects the number of windings on the pre-winder dial and starts the pre-winder to wind the yarn on pre-winder dial when the number of windings on dial are reduced to a fixed number of windings. o Usually 2 - 3 picks yarn is stored on dial. o The number of windings depend upon the pick length (fabric width). o Number of windings on pre-winder dial can be increased or decreased by adjusting the fingers. o There is a nut mounted on the finger which is loosen or tighten to adjust the dial diameter. Prepared By: Shakeel Ahmad Paracha Page 16 of 29 Textile Institute of Pakistan, Karachi. TEXT312 (Weaving Mechanisms) o There is a red colour light on magnetic pin assembly which starts to blink when winding process is carried out on the pre-winder dial. o There are two buttons which are used to unwind the windings from the dial. Pre-winder Side View Pre-winder Front View Pre-winder Dial Finger Magnetic Pin Electromagnetic Pin Assembly ABS (Automatic Brake System) o This system is used to ensure the continuous weft yarn supply to the main nozzle/fixed nozzle. o It vibrates continuously to detect the yarn supply. o It stops the loom when the yarn breaks. It also smoothens the yarn supply by providing the specific tension to the yarn. Main Nozzle/Fixed Nozzle o It is used to feed the yarn to tandom/movable nozzle. o Number of main nozzles depend upon the Number of pre-winders used. o Proper alignment at specific angle, of main nozzle is very necessary. Prepared By: Shakeel Ahmad Paracha Page 17 of 29 Textile Institute of Pakistan, Karachi. TEXT312 (Weaving Mechanisms) o If main nozzle is not properly aligned at any specific angle it will cause weft breakage. Tandom Nozzle/Movable Nozzle o Tandom nozzle is used for blowing of weft yarn during pick insertion. o It passes the weft yarn to the sub-nozzles. o Number of tandom nozzles depend upon the number of pre-winders used. o This nozzle is fixed on sley and move along reed during beat-up. o The distance between the tandom nozzle and weft cutter (LHS cutter) should be so much that during beat-up the tandom nozzle should not strike with the weft cutter. o Number of main nozzles and number of tandom nozzles are always equal. Relay Nozzles o These are also known as sub-nozzles. o Sub-nozzles are fitted on the sley. o Sub-nozzles are arranged over the entire length of the reed & assist the main nozzle in blowing the pick through guide channel. o The sub-nozzles are divided into groups. o Each group of sub-nozzles consists of 5 sub-nozzles and works after certain interval of time in such a way that second group (valve) starts working during the operation of first group (valve). o Air is supplied to the sub-nozzles via solenoid valves. o Each solenoid valve supplies air pressure to 2 - 5 sub-nozzles. o These solenoid valves receive the air pressure from main air supply pipe. o The amount of air pressure increases from left to right in sub-nozzles. o The distance between sub-nozzles is kept 10 - 15 mm depending on the count of weft yarn. o The jets of any sub-nozzle should not be choke otherwise it will cause weft breakage and cause weft loose. Prepared By: Shakeel Ahmad Paracha Page 18 of 29 Textile Institute of Pakistan, Karachi. TEXT312 (Weaving Mechanisms) o The sub-nozzles have varying pitch i.e., the distance b/w two consecutive nozzles and this distance decreases from picking to receiving side to compensate the drop in air pressure. Solenoid Valve o One end of solenoid valve is connected to relay nozzle while other end is connected to air tank. o It regulates the amount of air by electromagnetic function. o Sub-nozzles have the solenoid valves in such a way that one valve operates a group of 2 - 5 sub-nozzles. o The main nozzle has its own solenoid valve. Cutters o There are two cutters, one on picking side & other on receiving side. o The picking side cuter is called as weft cutter & receiving side is known as leno cutter or waste cutter. o The weft cutter cuts the weft yarn after insertion of pick near the selvedge leaving 5 - 10 mm yarn on selvedge. o While the leno cutter separates the leno waste on receiving side. o Following parameters are important for the cutters: Cutting position Cutting degree (250˚ - 300˚) Condition of cutter o There are two types of cutters. o Electrical cutter which is operated with the help of electric motor and other is mechanical cutter, which is operated with the help of lever, which gets drive from loom shaft. Prepared By: Shakeel Ahmad Paracha Page 19 of 29 Textile Institute of Pakistan, Karachi. TEXT312 (Weaving Mechanisms) Catch Cords o These are mostly the synthetic yarns, which grip the weft waste on receiving side of machine. o Number of catch cords ranges from 8 - 12. o These have independent shedding and are used directly without size. Weft Sensors (FD1, FD2) o There are two sensors on receiving side of machine having a distance of 120 - 130 mm b/w them. o These sensors sense the arrival of weft yarn. o The 1st sensor (FD1) ensures the presence of weft yarn if weft yarn is present, the machine will continue to run if yarn is absent then machine will stop. o The 2nd sensor (FD2) has reverse function and ensures the absence of yarn, if weft yarn reaches up to 2nd sensor the machine stops otherwise it will continue to run. Prepared By: Shakeel Ahmad Paracha Page 20 of 29 Textile Institute of Pakistan, Karachi. TEXT312 (Weaving Mechanisms) Stretch Nozzles o The stretch nozzles ensure that the filling yarn remains stretched during closing of shed at beat-up position. o It is mounted at receiving side. Profile Reed o The reed having grooves in it called as profile. o The profile creates a path for traveling of filling yarn from picking to receiving side. o The profile should be in such position that warp yarn should not be in the way during traveling from picking to receiving side. o The reed should be properly cleaned to avoid breakage of warp & weft yarns. Temples o Temples are used to hold the fabric during fabric formation. o Temples also stretch the fabric. o Different types of temples can be used depending upon the fabric quality. o For light weight fabrics ring type temples are used and for heavy weight fabrics pin types temples are used. o Temples are used on both sides of fabric. Prepared By: Shakeel Ahmad Paracha Page 21 of 29