Emerging Trends in Mechanical Engineering PDF
Document Details
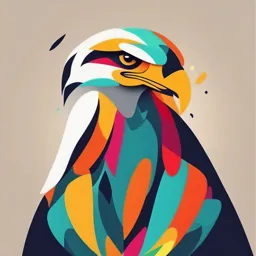
Uploaded by CooperativeArlington
Maharashtra State Board of Technical Education
Learning Manual Development Team
Tags
Summary
This learning manual is designed to aid students, teachers, and instructors in understanding emerging trends in mechanical engineering, specifically focusing on automobile engineering, HVAC, energy management, and advanced manufacturing technologies. The course content is outcome-based, intended to provide students with industry-relevant competencies.
Full Transcript
A Learning Manual for Emerging Trends in Mechanical Industry A Learning Manual for Emerging Trends in Mechanical Engineering (Course Code 22652) Semester– (VI) (Diploma in Mechanical Engineering, Automobile Engineeri...
A Learning Manual for Emerging Trends in Mechanical Industry A Learning Manual for Emerging Trends in Mechanical Engineering (Course Code 22652) Semester– (VI) (Diploma in Mechanical Engineering, Automobile Engineering and Production Engineering) Maharashtra State Board of Technical Education, Mumbai (Autonomous) (ISO-9001-2008) (ISO/IEC 27001:2013) 1 A Learning Manual for Emerging Trends in Mechanical Industry 2 A Learning Manual for Emerging Trends in Mechanical Industry Maharashtra State Board of Technical Education, Mumbai (Autonomous) (ISO-9001-2008) (ISO/IEC 27001:2013) 4th Floor, Government Polytechnic Building, 49, Kherwadi, Bandra (East), Mumbai -400051. 3 A Learning Manual for Emerging Trends in Mechanical Industry 4 A Learning Manual for Emerging Trends in Mechanical Industry Preface The primary focus of any engineering work in the technical education system is to develop the much needed industry relevant competencies and skills. With this in view, MSBTE embarked on this innovative ‗I‘ Scheme curricula for engineering diploma programmes with outcome-base education. This Learning manual is designed to help all stakeholders, especially the students, teachers and instructors to develop in the student the pre-determined outcomes. The manual begins by identifying the competency, course outcomes,. The students will become aware about the emerging Trends in The Mechanical Engineering. This manual also provides guidelines to teachers to effectively facilitate student-centered activities through each chapter by arranging and managing necessary resources ensuring the achievement of outcomes in the students. Over the coming years, technological developments such as Robotics, IOT, Artificial intelligence, smart controls are likely to have a significant impact on the world of work and employment as well as to trigger far reaching changes. Looking towards the era in Technology advancement, Mechanical/Automobile/Production Engineering offers addition of new Dynamic subjects and new versions of core subjects. Diploma Mechanical/Automobile/Production Engineers should be familiar with new technologies from the fields of Automobile Engineering, HVAC, Energy Management, Advanced Manufacturing Processes, Agriculture and Farm Machines and many more. This Dynamic course will give insight to the recent practices adopted by the Mechanical Industries and awareness of these techniques will enhance career opportunities of Diploma Mechanical/Automobile/Production Engineers. The Learning manual development team wishes to thank MSBTE who took initiative in the development of curriculum re-design project and implementation and also acknowledge the contribution of individual course experts who have been involved in Learning manual as well as curriculum development (I scheme) directly or indirectly Although all care has been taken to check for mistakes in this learning manual, yet it is impossible to claim perfection especially as this is the first edition. Any such errors and suggestions for improvement can be brought to our notice and are highly welcome. Learning Manual Development Team 5 A Learning Manual for Emerging Trends in Mechanical Industry 6 A Learning Manual for Emerging Trends in Mechanical Industry List of Content S. Page Name of Topic No No. 1 Recent Trends in Automobile Industry 09 1.1 Hybrid cars-manufactures, Types- Micro Hybrid, Mild Hybrid, Full Hybrid, Series hybrid, Parallel Hybrid 1.2 E-vehicles- Manufacturers, specifications, Types of Batteries, Li-ion batteries, Sodium Nickel Chloride Batteries, Sodium Sulphur Batteries, Fuel Cell, Charging- Charging Methods and Modes. Issues with e-vehicles 1.3 Safety in Automobile- Air bags, Electronic stability programme (ESP), Anti Collision system 1.4 Autonomous Vehicle- Introduction, Necessity, Level, Manufacturers 2 Recent Trends in Process Industry 35 2.1 Process Boilers, Introduction to Combi-Boilers 2.2 Waste heat recovery-process industry 2.3 Process layout of; a. Food Industry b. Pharmaceutical Industry c. Textile Industry 2.4 Process Automation – Need, Basic Elements, Types 3 Recent Trends in Manufacturing Industry 67 3.1 Smart Factory - Introduction, Elements and applications 3.2 Industrial robotics - Robot anatomy and control systems, end effectors, sensors in robotics 3.3 Industrial Robot applications a. Welding Robots b. Assembly Robots 3.4 Introduction to Immersive Technology a. Virtual Reality b. Augmented Reality c. Mixed Reality 4 Energy Audit and Management 89 4.1 Standards and Labelling 4.2 Energy Monitoring and Targeting 4.3 Energy Management and Audit 4.4 Home Energy Audit 5 Agriculture Equipment and Post-Harvest Technology 135 5.1 Farms Tools and Equipment 5.2 Advanced Technology in Post Harvesting 5.3 Elements of Cold Chain 5.4 National Cooling Action Plan (NCAP) 7 A Learning Manual for Emerging Trends in Mechanical Industry 8 A Learning Manual for Emerging Trends in Mechanical Industry Unit –I Recent Trends in Automobile Industry 1.1 Hybrid Cars Definition: A hybrid electric vehicle (HEV) is a type of hybrid vehicle that combines a conventional internal combustion engine (ICE) system with an electric propulsion system (hybrid vehicle drivetrain). There are three main reasons for which the automotive manufacturers are developing and selling HEVs: Reduction of the CO2 emissions (by reduction of the fuel consumption) Reduction Of the Exhaust Gas Toxic Emissions Improvement of the powertrain dynamics (by increasing total power and torque) There is a variety of HEV types, and the degree to which each functions as an electric vehicle (EV) also varies. The most common form of HEV is the hybrid electric car, although hybrid electric trucks (pickups and tractors) and buses also exist. The powertrain of a HEV is quite complex because it contains all the components of an ICE vehicle plus most of the components of a pure electric vehicle (EV). Also, depending on the level of hybridization, it needs two energy sources, the fuel tank for the engine and a battery for the electric machine. Main components of a Hybrid vehicle: 1. An internal combustion engine (i.e., Petrol engine / Diesel engine): In most of the hybrid vehicles, IC engine acts as the main source of power. 2. Electric motor: It transforms the electric energy stored in a battery into mechanical energy i.e. it drives wheels with the help of electricity stored in a battery. 3. Electric battery: Its function is to store electric energy and supply it whenever necessary. 4. Inverter: Electricity stored in an electric battery is in the form of Direct Current (DC) while the majority of the motors used in the present-day hybrid vehicles require Alternating Current (AC) to run. So, an Inverter performs the function of converting the DC from the battery to AC for the motor. 5. Electric Generator (Exclusive for series & series-parallel hybrids): The function of a generator is to produce electricity when driven by an external power source. Series hybrids use this component where an IC engine drives a generator to produce electricity which then charges the battery. 6. Control Module: It is the most important component of the hybrid vehicle. It controls the entire operation of the vehicle by synchronizing all the power sources employed. Types of Hybrid Cars: Classification of Hybrids: Hybrids are mainly classified based on the following criteria: 1. The structure of drive-train 2. The degree of hybridization 9 A Learning Manual for Emerging Trends in Mechanical Industry Classification based Classification based on Structure of on Degree of Drive Train Hybridization Parallel Hybrid Micro Hybrid Series Hybrid Mild Hybrid Series Parallel Hybrid/ power split hybrid Strong Hybrid/ Full Hybrid Figure 1.1: Classification of Hybrid Vehicles 1. Depending upon the structure of drivetrain, hybrid vehicles are further classified as: Series Hybrid: In this type of hybrid vehicle, wheels are powered only by an Electric motor which ultimately derives its power from the electric battery. The IC engine installed in the vehicle does not supply power to wheels directly. So, these vehicles need large capacity batteries. The series hybrid vehicle is more efficient in low-speed driving involving frequent start- stop. 10 A Learning Manual for Emerging Trends in Mechanical Industry FUEL Internal Combustion Engine Generator Electric Battery Electric Motor Transmission Wheels Parallel Hybrid: In this type of a hybrid vehicle, wheels get power from both the IC engine and an Electric Motor. The drivetrain of these Figure 1.2: Blockvehicles diagramisofsoSeries designed thatVehicle Hybrid it can receive power from both the IC engine and Battery simultaneously. However, the IC engine serves as the main source of power in the Parallel hybrid vehicle. As electric battery‘s role is only to support the engine, these vehicles need a smaller capacity battery. A parallel hybrid is more effective in high-speed driving. Electric Battery Fuel Internal Electric Motor Combustion Engine Transmission Wheels Figure 1.3: Block diagram of Parallel Hybrid Vehicle Series-Parallel Hybrid/ Power split Hybrid: This recently developed system is a combination of a series hybrid system and parallel hybrid system. Thus, it takes the best from both the worlds. Depending upon the load on 11 A Learning Manual for Emerging Trends in Mechanical Industry the vehicle, it can act like a parallel hybrid vehicle or a series hybrid vehicle. The control module governs the selection of the most suitable mode. Almost all the modern hybrid vehicles belong to this category. E.g. Toyota Prius, Toyota Camry, Honda Civic etc. 2. The degree of hybridization Based on the degree of hybridization, hybrids are classified as follows: a. Micro hybrid: Micro hybrid technology is the lowest level of vehicle hybridization. It contains mainly start stop technology. Here, energy stored in an auxiliary battery is used to quickly start a vehicle at the traffic signal. In India, a common example of micro hybrid is the Mahindra Scorpio. b. Mild Hybrids: These hybrids cannot run on electric battery alone. They always need the support of an IC engine to run as the battery used in these vehicles is of a small capacity. c. Strong Hybrids/ Full Hybrid: This vehicle can run on either the IC engine or the electric battery alone as the battery used in them is of a higher capacity. The next level of hybridization is the mild hybrid where electrical energy is used for start stop and also for driving vehicle for short distance at low speed or to aid in acceleration. Above this there are full hybrid and plug in hybrid vehicles where the vehicle can move considerable distance using batteries Plug-in hybrids (PHEVs) A plug-in hybrid electric vehicle (PHEV), also known as a plug-in hybrid, is a hybrid electric vehicle with rechargeable batteries that can be restored to full charge by connecting a plug to an external electric power source. A PHEV shares the characteristics of both a conventional hybrid electric vehicle, having an electric motor and an internal combustion engine; and of an all-electric vehicle, also having a plug to connect to the electrical grid. PHEVs have a much larger all-electric range as compared to conventional gasoline-electric hybrids, and also eliminate the "range anxiety" associated with all-electric vehicles, because the combustion engine works as a backup when the batteries are depleted. Hybrid Vehicle Manufacturers: 1. Mahindra e-Verito Mahindra is now integrating electric technology in almost every future car. The Verito sedan is the perfect combination of electric and conventional cars. 2. BMW i8 The BMW i8 is not just an electric-hybrid car. It is a sports car that has an all-electric range of 37 km, with 0-100 kmph ability in less than 4.5 seconds. 3. Volvo XC90 T8 12 A Learning Manual for Emerging Trends in Mechanical Industry It is the first hybrid SUV across Indian soils when launched. The most distinguished features of the car include individual electronically-adjustable reclining rear seats with massage & ventilation functions. Furthermore, the car also offers increase legroom with footrests. Additionally, the car also has ambient lighting and illuminated storage in addition to a regal design. 4. Lexus LS500h Lexus is ever-present in luxury segments. It recently launched a range of hybrid cars in various segments. The cars were under ES (mid-size sedan), LS (full-size sedan), RX (mid-size crossover), and NX (compact SUV) categories. 5. Toyota Camry Toyota is hailed as the pioneer for hybrid technology in cars. The Camry sedan by Toyota has enjoyed spectacular success elsewhere in the world. It is now poised to enter the Indian market. Technical Specifications of Mahindra E Verito The Main Limitations of a HEV are: It adds more weight to the vehicle due to additional electric components, It is more difficult to build and 13 A Learning Manual for Emerging Trends in Mechanical Industry The total price of purchasing and ownership increases (compared to a ICE vehicle).In most of the HEVs the electric propulsion is done using permanent-magnet electric machines. The main Benefits of an electric machine, compared to an ICE, are: Constant high torque at low speeds Very high efficiency Instant torque delivery Energy recovery capability Compared with a conventional powertrain, by putting together an electric machine with an ICE we get the following advantages: By providing torque assistance with the electric motor, the ICE can work in the most fuel efficient point (speed and torque) The ICE can be downsized, retaining in the same time a constant overall torque and power of the powertrain, thanks to the electric motor assistance The kinetic energy of the vehicle during braking can be recovered and stored in the high voltage battery, with the help of the electric machine operating as a generator The torque response of the powertrain can be improved, because of the instant torque delivery of the electric motor The gear ratios of the transmission can be lowered, to keep the engine at lower speed operating points (better fuel efficiency), because the electric motor can deliver instant torque request from the driver o Having two sources of power, the hybrid control system needs to decide the torque split between the Internal Combustion Engine and electric machine, depending on the driver input and vehicle operating state. A hybrid electric vehicle performs at least one or more of the following functions: Engine idle stop/start Electric torque assistance (fill and boost) Energy recuperation (regenerative braking) Electric driving Battery charging (during driving) Battery charging (from the grid) 1.2 Electric Vehicles Definition: An electric vehicle (EV) is one that operates on an electric motor for vehicle propulsion, instead of an internal-combustion engine that generates power by burning a mix of fuel and gases. 14 A Learning Manual for Emerging Trends in Mechanical Industry Battery based Electric vehicle includes electric 2-wheeler, 3-wheeler, cars and electric buses. Electric vehicle is seen as a possible replacement for current-generation automobile, in order to address the issue of rising pollution, global warming and depleting natural resources. Battery electric vehicle (BEV) and plug-in hybrid electric vehicle (PHEV) offer the potential to reduce the CO2 emissions of the traffic sector and the dependence on mineral oil. The reasons for this are the higher efficiency of electric power trains and the possibility of using renewably generated electricity for transportation. As BEVs and PHEVs in electric mode are operated locally emission-free, they also reduce the pollution in densely populated areas. Besides ecological reasons, economic reasons will facilitate the introduction of electric vehicles. Increasing prices for mineral oil and decreasing batteries prices are the drivers for this. An advantage of battery electric vehicles is that batteries can be charged at off-peak times - enhances options to make grid electricity less costly and more efficient. Though the concept of electric vehicles has been around for a long time, it has drawn a considerable amount of interest in the past decade amid a rising carbon footprint and other environmental impacts of fuel-based vehicles. Indian Government Policies/ Programmes: In India, the first concrete decision to incentivize electric vehicles was taken in 2010. According to a Rs 95-crore scheme approved by the Ministry of New and Renewable Energy (MNRE), the government announced a financial incentive for manufacturers for electric vehicles sold in India. The scheme, effective from November 2010, envisaged incentives of up to 20 per cent on ex-factory prices of vehicles, subject to a maximum limit. However, the subsidy scheme was later withdrawn by the MNRE in March 2012. In 2013, Indian Government unveiled the 'National Electric Mobility Mission Plan (NEMMP) 2020' to make a major shift to electric vehicles and to address the issues of national energy security, vehicular pollution and growth of domestic manufacturing capabilities. Though the scheme was to offer subsidies and create supporting infrastructure for e-vehicles, the plan mostly remained on papers. While presenting the Union Budget for 2015-16 in Parliament, then finance minister announced Faster Adoption and Manufacturing of Electric Vehicles (FAME), with an initial outlay of Rs 75 crore. The scheme was announced with an aim to offer incentives for clean-fuel technology cars to boost their sales to up to 7 million vehicles by 2020. In 2017, Transport Minister made a statement showing India‘s intent to move to 100 per cent electric cars by 2030. However, the automobile industry raised concerns over the execution of such a plan. The government subsequently diluted the plan from 100 per cent to 30 per cent. In February 2019, the Union Cabinet cleared Rs 10,000-crore programme under the FAME-II scheme. This scheme came into force from April 1, 2019. The main objective of the scheme is to encourage a faster adoption of electric and hybrid vehicles by offering upfront incentives on purchase of electric vehicles and also by establishing necessary charging infrastructure for EVs. 15 A Learning Manual for Emerging Trends in Mechanical Industry EV manufacturers and their product offering: 1. Okinawa Okinawa is one of the fastest growing Electric Vehicle two-wheeler manufacturers in India. Okinawa is the first Indian company that launched electric scooters in the market with the highest speed. Okinawa Praise (Scooter) Specifications Motor Warranty 3 Years or 20000 km (Whichever is earlier)** Battery Warranty 3 Years or 20000 km (Whichever is earlier)** Rated Power 1000watt, BLDC Motor(Waterproof) Max. Power 2500watt Speed Economy:30-35kmph, Speed:50-60kmph, Turbo:60-70kmph Range/Charge 160 km/per charge* Climbing 15 Degrees Brake System FR-Big/Small Disc | RR-Disc Brake Seat Height 800mm Dimensions 1970X745X1165mm Loading Capacity 150Kg Tyre 90/90-12 Tubeless (Front/Rear) Speedometer Digital Voltage 72V Battery 3.3kwh Lithium-ion (Detachable Battery) Controller E-ABS (Electronic- Assisted Braking System) with Regenerative Energy Ageing Protection Battery with automatic sleep mode Charger Specification Micro Charger with Auto Cut Charging Time 3-4hrs* Ground Clearance 175mm Boot Space 7ltr Suspension Front- Hydraulic Telescopic, Rear- Double Shocker with dual tube technology Key Feature Central Locking with Anti-theft Alarm, Keyless Entry, Find My Scooter Function, Mobile Charging USB Port, Motor Walking Assistance (Front/Reverse Motion), Geo-Fencing, Immobilization, Trips, Secure Parking, Tracking & Monitoring, Maintenance/Insurance Reminder, Battery information, Speed Alerts and Driver Score 16 A Learning Manual for Emerging Trends in Mechanical Industry Side Stand Sensor Sensor Enabled - Vehicle Will Not Start Headlight LED with DRL (Day Running Light) Function Back light Unique Design with LED Rear Winkers Wheel Stylish Aluminium Alloy Wheel Mobile App Yes Connectivity Floor Mat Stylish Body Coloured Brake Lever CNC Machined with Lever Adjustment Roadside Assistance Yes (RSA) 2. Mahindra Electric The Indian Automobile manufacturer Mahindra Electric made its green move towards eco- friendly transportation. Mahindra Electric has released 4 electric vehicles in the Indian market, which indirectly supporting the Govt. of India Mission 2030 Electric. 3. Tata Motors Tata Motors is building an EV ecosystem for greener future. In 2017, company won the tender to supply 10,000 Tigor EVs to Energy Efficiency Services Ltd (EESL). In March 2018 company provided a fleet of Tata Starbus‘ to MMRDA in Mumbai. Later, company signed a MoU with the Government of Maharashtra to deploy 1000 EVs across PVs and CVs. In February 2019, company flagged off the first 9/9m AC Electric bus in Lucknow as part of a larger order for 40 electric buses for Lucknow City Transport Services Ltd. 4. Hyundai Electric Hyundai Kona Electric is the electric SUV to zoom under the Indian skies. The Kona has a torque of 325 km. It takes anywhere between 6-9 hours to be completely charged. 5. Ather Energy Ather Energy is currently building India‘s first smart and electric scooter, the S340. Along the way, we plan to setup charging infrastructure for EVs and redefine the consumer experience in the automobile industry. Types of Batteries Table: Relation between Electric vehicle performance parameters and Battery Vehicle Performance Battery specifications parameter Range Energy density in Wh/ kg, Volumetric energy density in Wh/ L, Self- discharge in percentage / day. Refuelling Recharge time, rapid recharge capability Acceleration Specific power in W/ kg Service life of Number of recharges and discharges, number of cycles according battery to test specifications 17 A Learning Manual for Emerging Trends in Mechanical Industry Reliability Battery behaviour when subjected to shock and vibration, effect of temperature, protection against overcharging and excessive discharge 1. Li-Ion batteries: In the lithium-ion system, a lithium-carbon electrode acts as the negative electrode material. The lithium is not present in the form of metal, but either as an ion in the electrolyte or chemically bound to the positive or negative electrode. The carbon electrode is characterized by its high life-cycle stability. Small cells using lithium-ion systems have so far displayed energy density of 120 Wh/kg. The lithium-ion system used at the moment for portable batteries already satisfies two key conditions for an electric vehicle i.e. high specific energy and a long service life. Cobalt, the main element in the positive electrode, is a relatively expensive metal. The cobalt is replaced by manganese oxide. Cells using these new materials achieve comparable specific energy and specific power. The next generation of lithium-ion is expected to contain a solid polymer electrolyte. Estimation of material costs show that there is a possibility of producing batteries for electric vehicle at costs considerably more favorable than those of Ni-MH. Specifications: Specific energy : 100 to 120 Wh/kg Energy density : 200 to 250 Wh/L Maximum power : 200 W/kg Charge time : 4 hours 2. Sodium Nickel Chloride Batteries: Sodium–nickel-chloride batteries are under development but not yet widespread, because the high operating temperature currently still results in too high self-discharge losses. These batteries show energy density over 80 Wh/ kg and specific power over 110 W/kg at full charge. The battery has the potential to meet a life goal of 5 years. 3. Sodium Sulphur Batteries: Research is underway to improve battery technology to have a higher energy density for electric vehicles. A potential contender however is the sodium sulphur (NaS) battery, which has reached the production state in near past. The NaS battery offers high specific energy 100 Wh/kg with relatively low-cost battery materials. Specific power value is 130 W/kg. The sodium sulphur (NaS) battery uses a cathode of liquid sodium into which a current collector, a solid electrode of B-alumina is placed. The complete assembly is surrounded by a metal can, which is in contact with the anode, a sulphur electrode. A running temperature of 300ºC is necessary with NaS system, which is the major problem. A heater in the capacity of a few hundred watts forms part of the charging circuit, which maintains the battery temperature when the vehicle is not running. The battery temperature is maintained when it is in use due to losses in the battery. Each cell of this battery is very small, using only about 15 gm of sodium. This is a safety feature because if the cell is damaged the sulphur on the outside causes the potentially 18 A Learning Manual for Emerging Trends in Mechanical Industry dangerous sodium to be converted into poly-sulphides, which are comparatively harmless. The additional advantage is that the cells can be located around the car. The capacity of each cell is about 10 Ah with an output voltage of about 2 V. These cells fail in an open circuit condition and hence this must be taken into account. A problem yet to be solved with this system is its casing material, which is prone to fail due to the very corrosive nature of the sodium. Presently an expensive chromised coating is used. This type of battery combined with an electric motor, seems to be a very good competitor to the internal combustion engine. The servicing and charging infrastructure needs to be developed but looks promising. It is estimated that the cost of running an electric vehicle may be little around 15% of the petrol version, which may absorb the extra cost of production. 19 A Learning Manual for Emerging Trends in Mechanical Industry Table: Characteristics of commonly used rechargeable batteries. The figures are based on average ratings of commercial batteries. 4. Fuel Cell: 20 A Learning Manual for Emerging Trends in Mechanical Industry The energy of oxidation of conventional fuels, which it usually manifested as heat, may be converted directly into electricity, in a fuel cell. The process of oxidation involves a transfer of electrons between the fuel and oxidant and in a fuel cell works on this principle where the energy is directly converted into electricity. All battery cells involve an oxide reduction at the positive pole and an oxidation at the negative pole during some part of their chemical process. For the separation of these reactions in a fuel cell an anode, cathode and electrolyte are required. The electrolyte is fed directly with the fuel. When hydrogen fuel is combined with oxygen it is found to be a most efficient design. Fuel cells are very reliable and silent in operation, but at present are very expensive to construct. Figure shows a simplified representation of a fuel cell. In one type of fuel cell hydrogen is passed over an electrode (the anode) of porous nickel, which is coated with a catalyst, and the hydrogen diffuses into the electrolyte. This causes electrons to be stripped off the hydrogen atoms. These electrons then pass through the external circuit. Negatively charged hydrogen anions (OH-) are formed at the electrode over which oxygen is passed, such that they also diffuse into the solution. These move through the electrolyte to the anode. The electrolyte used is a solution of potassium hydroxide (KOH). Water is formed as the by-product of a reaction involving the hydrogen ions, electrons and oxygen atoms. If the heat generated by the fuel cell is used, then an efficiency of over 80% is possible together with a very good energy density. The working temperatures of these cells varies but about 300–400°C. High pressure 2.4–40 MPa is also used. The pressures and storage of hydrogen are the main problems to overcome with fuel cells before they can be realistic alternatives to other forms of storage for the mass market. It is believed that hydrogen fuel cell cars will hardly become commercially viable / economically competitive with other technologies because they have inefficiency of producing, transporting and storing hydrogen and the flammability of the gas. Charging: Electric Vehicle Supply Unit (EVSE): EVSE stands for electric vehicle supply equipment and its function is to supply electric energy to recharge electric vehicles. EVSEs are also known as EV charging stations, electric recharging points or just charging points. EVSEs can provide a charge for the operation of electric vehicles or plug-in hybrid electric-gasoline vehicles. The Public charger makes communication that need to occur between the EVSE and an electric vehicle. Charging Methods and Modes: Following are the charging modes for EV batteries. AC Slow Charging Mode AC Fast Charging Mode DC Fast Charging Mode Home / Private charger 21 A Learning Manual for Emerging Trends in Mechanical Industry The home private chargers are generally used with 230V/15A single phase plug which can deliver a maximum of up to about 2.5KW of power. Thus, the vehicles can be charged only up to this rate. The billing for the power is part of home-metering. Public charger For charging outside the home premises: the electric power needs to be billed and payment needs to be collected. Further, the charges may depend on state of grid (whether it is power- surplus or is in power-deficit state). The power utilities may also want to manage power drawn by these chargers from time to time. Under AC Charging there are 2 categories of charging. Normal AC charging Electric 2-wheelers, 3-wheelers and 4-wheeler vehicles in India has on-board charger that charge at rate of around 2.5kW. These AC 2.5KW Chargers could fast charge a 2-wheeler (for a battery with an energy density of 2KWh) in an hour‘s time; 4-wheeler or larger vehicles with batteries of 12 KWh or more will be charged in about six hours. Fast AC charging. Worldwide, electric cars like the Nissan Leaf or the Tesla have on board chargers with higher power ratings. This enables AC charging at a faster rate, from 7.7 kw to 22 kw. DC Fast Charging: In this method of charging, DC current is sent to the electric car's battery directly via the DC charge port. Fast charge rate (usually 50 KW or more outside India) can supply 100 or more km's of range per hour of charging. DC Charging Specifications: Power rating of fast chargers are 10kW/15kW/30kW/50kW or even higher capacity. Voltage rating at which fast charging has to be carried out. 48V/72V for Indian electric cars like the Mahindra e2o Plus P8, Mahindra e-Verito and upcoming Tata electric cars. Up to 750V or even higher used by global electric cars like Nissan Leaf and others. Level 1 DC Chargers Public DC Chargers at output voltage of 48V / 72V, with power outputs of 10 kW / 15 kW with maximum current of up to 200A. Level 2 DC Chargers Public DC Chargers at output voltage up to 1000V, with power outputs of 30 kW / 150 kW. Issues with e-vehicles 1. Cost of Electric Vehicle /Battery Pack: The reduction in GST rate for electric vehicles (EVs) has helped Indian automobile industry to reduce cost to certain extent, but still they are expensive. The cost of a battery amounts to 40 percent of the total vehicle cost. The cost of the battery is expected to fall from Rs 20,000 per kilowatt hour (kWh) to Rs 5,500 per kilowatt/hour. The cost of electric vehicles is expected to be at par with combustion (engine) cars in the next 3-4 years. 22 A Learning Manual for Emerging Trends in Mechanical Industry The concept of battery swapping essentially enables reduced wait time for charging and significantly lower up-front cost for two and three-wheelers (since they would be sold without the battery). 2. Charging Station Infrastructure: Without an accessible infrastructure that can re-charge an EV in a reasonable period of time, most motorists will be unwilling to purchase one, even if it is cheaper and its performance is better. Owners of a conventional vehicle are unlikely to switch to an electric car, if the fueling process is more difficult, time consuming, and uncertain. If charging facilities are to be deployed at scale, they will need to be accessible to all electric car models, and will require viable business plans—plans that will provide an opportunity for investors to make a positive return on their investments. All of this is possible, but the uncertainties around technologies, regulations, and costs will have to be substantially reduced. 3. Range satisfaction: Expectation of EV range depends on user. For personalized transport needs, with adequate charging infrastructure, present day electric vehicles provide adequate range. For intercity transport, there is a requirement of fast charging facility at every 50 km. Using artificial intelligence and navigation systems, driver can be well informed about the charging facility. 4. Prediction of Electric Vehicle Range: EV research related to the possibility of providing a more accurate prediction of range is required. Range prediction is a complex problem because it depends on a number of factors (internal, external, constant, variables- Vehicle design, the driver and the environment.) 1.3 Safety in Automobiles: 1. Air bags: It is a safety restraint system of an automobile. It consists of air bags, sensors, inflation system / air bag module unit. The purpose of using an air bag is to cushion occupants during a crash, reduce their speed in collision without getting injured and provide protection to their bodies when they strike interior objects such as the steering wheel or window in passenger compartment. Air bag is made of thin nylon fabric, folded into a steering wheel or dashboard or the door or seat. Sensors are used to trigger the inflation of air bag. Working of Air bags: During collision a mechanical switch is flipped and an electrical contact takes place. Sensors send an electric current to the air bag module. The impact sensor senses impacts. The sensors are set to a sensitivity level where they will only deploy in an accident that is equal to or greater than a 20 kmph crash into a concrete wall. The sensor functions by detecting automobile deceleration. When the automobile decelerates at a rapid rate, the sensors are tripped. This deceleration detecting is the job of two or more deceleration sensors, placed at the front of the car. When the sensors go off, they send an electrical current to the inflation system, causing it to deploy the airbag. The air bag module unit consists of an inflator assembly, a nylon bag and a breakaway 23 A Learning Manual for Emerging Trends in Mechanical Industry cover. Inflation system contains sodium azide and potassium nitrate. The electrical current from the sensors travels to the inflator assembly, where it causes a tiny initiator to be fired. This initiator creates a spark which ignites a propellant, which is generally sodium oxide. The reaction creates nitrogen gas. The gas expands quickly and inflation of air bags takes place, which literally bursts from its storage site like the steering wheel. Side air bags are also offered in certain vehicles. It provides protection during side collisions. This prevents the air bag on the undamaged side of the car from inflating. Curtain airbags inflate in front of windows to provide passengers better head and neck protection. It is more efficient at tipping and side impacts. Door air bag has more space, allowing for a bigger bag that provides more coverage. Door mounted side air bags deploy in just 5 to 6 milliseconds. Cinders are removed and the gas is cooled through a filtration screen also inside the assembly. The nitrogen gas is what causes the air bag to inflate. This inflation occurs in a average of only 30 milliseconds. When an occupant plunges into the air bag, the gas if forced backwards through vents, a process which takes another 45 milliseconds. The whole sequence from initial detection of a crash, until the air bag is fully deployed, happens very quickly. This is to protect those inside of the vehicle. Once an air bag is used, it needs replacement. 2. Electronic Stability Programme (ESP) Electronic Stability Programme (ESP) is a computerized technology that improves a vehicle's stability by detecting and reducing loss of traction (known as skidding). Some ESP systems also reduce engine power until control is regained. ESP system is designed to stabilize the vehicle during cornering maneuvers. Electronic stability control works in conjunction with a vehicle‘s anti-lock braking system (ABS), traction control and electronic power steering system. Components of ESP include steering wheel angle sensor, yaw rate sensor, lateral acceleration sensor, wheel speed sensor, roll rate sensor and longitudinal acceleration sensor. ESP checks where you are steering and where the vehicle is actually going. If there is difference in the direction of steering and vehicle direction of movement, the ESP will intervene in a number of ways. Typically, the vehicle ESP will communicate with Traction control system (TCS) and engine control unit (ECU) to reduce power, if the driver is applying throttle. This helps keep the vehicle from worsening its situation. ESP decides what wheel to brake applies the brake at individual wheels with varying degrees of pressure and duration. ESP also decides whether to reduce engine torque to stabilize the vehicle. By doing so, the system can help the vehicle correct its path and prevent it from leaving the roadway, straying across a divided highway, or even rolling over. It allows for higher speeds at cornering with reduced skidding or better traction. Working of ESP: ESP is always active. A microcomputer monitors the signals from the ESP sensors and checks 25 times a second, whether the driver‘s steering input corresponds to the actual direction in which the vehicle is moving. If the vehicle moves in a different direction ESP detects the critical situation and reacts immediately – independently of the driver. It uses 24 A Learning Manual for Emerging Trends in Mechanical Industry the vehicle‘s braking system to ―steer‖ the vehicle back on track. With these selective braking interventions ESP generates the desired counteracting force, so that the car reacts as the driver intends. ESP not only initiates braking intervention, but can also intervene on the engine side to accelerate the driven wheels. So, within the limits of physics, the car is kept safely on the desired track. 3. Anti-collision System Today‘s vehicles have high speed and high performance. Due to reasons like human error, misjudging, driving dynamics, weather, distraction, inexperience, tiredness and alcohol - road accidents are increasing. As a result, various anti-collision systems are designed for safety. These systems reduce severity of an accident that may result in loss of lives and/ or severe property damages. Traffic collisions can be classified as follows. Head-on Road departure Rear end Side collision Rollovers So, anti-collision systems are designed to avoid all relevant collisions. An anti-collision system generally has camera sensors and radars or laser to detect and warn the driver of any danger lying ahead on the road. The danger could be a car, a pedestrian, an animal, a stationary object such as a pole or tree. Several advanced features like audio warning the driver, pre-charging of brakes, automatic partial or full braking are available to avoid any fatalities. Following are major emerging anti-collision systems and their purpose. Forward collision warning system: uses an electronic system with sensors- cameras, radar or Light detection and ranging (LIDAR) to detect a vehicle or object in the front and warn the driver of possible collision. Lane departure warning system: has a camera that tracks the vehicle‘s position on the land and alerts the driver via warning signal such as steering wheel or seat vibration, when the vehicle steers off its lane. Adaptive cruise control: that allows the driver to drive vehicle at the desired speed, in which the system will control vehicle speed as per traffic and maintain safe distance with the leading vehicle. Automatic braking system: avoids collision by automatically applying a brake on sensing an immediate collision with a nearby vehicle. Electronic Stability Program: featuring sensors and a microcomputer, it detects and reduces the loss of traction (skidding) of a vehicle, while also applying brake automatically to stabilize the vehicle and help steer the vehicle on the desired path. Blind spot monitor system: integrates sensors that monitor vehicle sides for approaching blind spots and warns the driver of any dangers during lane changes or turning. 25 A Learning Manual for Emerging Trends in Mechanical Industry Automotive night vision system: uses infrared imaging for enhanced vision in dim lighting or poor weather conditions when headlights fail to reach drivers‘ viewing distance. 1.4 Autonomous Vehicle Introduction to Autonomous Vehicles: Another name for an autonomous vehicle is a self-driving, driverless, or robotic car (Robo-car). It is a vehicle that incorporates vehicular automation, or a ground vehicle that can sense its surroundings and move safely with little to no human intervention. Self-driving cars use a combination of sensors to understand their environment, including Radar, Lidar, Sonar, Thermo graphic cameras, GPS, Odometers, and inertial measurement units. Modern control systems analyze sensory data to determine the best routes to take, as well as impediments and pertinent signage. They are expected to have a significant impact on a variety of industries, including the motor industry, health and welfare, urban planning, transportation, insurance, the labor market, and others as a future technology. Timeline of Autonomous vehicle development and history: Automated driving systems (ADS) have been the subject of experiments since at least the 1920s; trials started in the 1950s. Japan's Tsukuba Mechanical Engineering Laboratory created the first semi-automated car in 1977. This vehicle needed specifically marked roadways that were interpreted by two cameras on the vehicle and an analogue computer. With the aid of an elevated rail, the car was able to go at up to 30 kph (19 mph). The Navlab and ALV projects at Carnegie Mellon University, funded by the US Defense Advanced Research Projects Agency (DARPA), began in 1984. In 1987, the EUREKA Prometheus Project at Mercedes-Benz and the Bundeswehr University Munich was launched. The ALV showed self-driving speeds of 31 kph (19 mph) on two-lane roads by 1985. Obstacle avoidance was added in 1986, and off-road driving in day and nighttime situations was demonstrated in 1987. In 1995, CMU's NavLab 5 successfully completed the first coast-to-coast autonomous drive of the United States, marking a significant advancement. The 2,797 mi (4,501 km) between Pittsburgh, Pennsylvania, and San Diego, California, which was accomplished at an average speed of 63.8 mph (102.7 km/h), were entirely autonomous (98.2%). DARPA, the US Army, and the US Navy provided the majority of funding for automated vehicle research in the US from the 1960s through the second DARPA Grand Challenge in 2005, resulting in small improvements in speeds, driving prowess in increasingly challenging situations. The National Automated Highway System, which demonstrated automated, driving by combining automation embedded in the highway infrastructure, automated technology in vehicles, and cooperative networking between the vehicles and the highway infrastructure, received US$650 million in research funding from the US in 1991. 26 A Learning Manual for Emerging Trends in Mechanical Industry Despite lacking a clear direction or financing to execute the system on a bigger scale, the programme ended in 1997 with a successful demonstration. The Carnegie Mellon University Navlab travelled a total of 4,584 kilometers (2,848 miles) across America in 1995, with 4,501 kilometers (2,797 miles) or 98% of the distance being driven autonomously. This project was partially supported by the National Automated Highway System and DARPA. In 2015, Delphi broke Navlab's record by driving an Audi equipped with Delphi technology over 5,472 kilometers (3,400 miles) through 15 states while operating in self-driving mode 99% of the time. This feat had previously remained unchallenged for two decades. In addition to Washington, DC, the US states of Nevada, Florida, California, Virginia, and Michigan permitted the testing of automated vehicles on public highways in 2015. Through the Coordination Actions CARTRE and SCOUT from 2016 to 2018, the European Commission provided funding for the creation of an innovation strategy for connected and autonomous driving. Additionally, the Roadmap for Connected and Automated Transport under the Strategic Transport Research and Innovation Agenda (STRIA) was released in 2019. Waymo reported in November 2017 that it had started testing autonomous cars without a safety driver sitting in the driver's seat; however, there was still an employee in the vehicle. The $80 billion indicated as having been invested in all areas of self-driving technology up to that date, according to a Brookings Institution analysis from October 2017, although it is "fair to believe that total worldwide investment in autonomous vehicle technology is much higher than this." Waymo announced in October 2018 that its test vehicles had logged over 10 million miles (16 million km) of automatic driving, with that number rising by around 1 million miles (1,600,000 km) every month. In Phoenix, Arizona, Waymo made history by becoming the first business to commercialize a fully autonomous taxi service in the US in December 2018. In Phoenix, Waymo will debut a geo-fenced driverless ride-hailing service in October 2020. A group of remote engineers are keeping an eye on the automobiles in real-time, and occasionally they must take action. Robocar established the Guinness World Record for being the fastest autonomous car in the world in March 2019, ahead of the robotic racing series Roborace. Robocar exceeded the speed limitations of autonomous vehicles by averaging 282.42 km/h (175.49 mph), which was verified by the UK Timing Association at Elvington in Yorkshire, UK. According to the chairman of the National Transportation Safety Board, there won't be any SAE level 3+ self-driving cars on the market for US consumers in 2020: There isn't a self-driving car now on the market for US consumers. On March 5, 2021, Honda began leasing a limited run of 100 Legend Hybrid EX sedans in Japan. These cars were outfitted with Level 3 automated driving technology, which had just received safety certification from the Japanese government. This technology allows drivers to legally take their eyes off the road while using "Traffic Jam Pilot" to navigate traffic jams. 27 A Learning Manual for Emerging Trends in Mechanical Industry Definition of Autonomous Vehicle: "An autonomous car is a vehicle capable of sensing its environment and operating without human involvement. A human passenger is not required to take control of the vehicle at any time, nor is a human passenger required to be present in the vehicle at all. "An autonomous car can go anywhere a traditional car goes and do everything that an experienced human driver does." Need of Autonomous Vehicles: Smart actuators, sophisticated control systems, and sensor technology: Complex technology is needed for a variety of applications, including automation and autonomous driving. But it's not only a matter of whether automated vehicles can start moving on their own. Future plans will keep passenger comfort a key focus while maintaining safety as the top objective. Autonomous vehicles are supposed to be safer to ride in addition to being more convenient to be driven around in. A driverless car won‘t put its driver or others at risk in accidents caused by potentially dangerous human behaviors or conditions like speeding, reckless driving, drowsiness, distracted driving, or impairment due to alcohol or drugs. Due to their ability to communicate with one another and adjust their routes in response to traffic, accidents, or construction, autonomous vehicles may also result in decreased traffic congestion on the highways. All-electric, purpose-built autonomous vehicles, maybe including shuttles, appear to be the next big thing. Levels of Autonomous Vehicles: The Society of Automotive Engineers (SAE) currently defines six levels of driving automation, ranging from Level 0 (fully manual) to Level 5 (fully autonomous). As the levels increase, the extent of the driverless car‘s independence regarding operation control increases. These levels have been adopted by the U.S. Department of Transportation. Figure 1.4: Block Diagram indicates the Levels of Driving Automation 28 A Learning Manual for Emerging Trends in Mechanical Industry 1. At level 0, the car has no control over how it operates; the entire driving is done by the human driver. 2. At level 1 (driver‟s assistant), the vehicle‘s ADAS (advanced driver assistance system) has the ability to support the driver with either steering or accelerating and braking. 3. At level 2 (partial automation), the ADAS can manage steering, accelerating, and braking in some circumstances, but the human driver is still required to do the remaining functions while maintaining full attention to the driving environment throughout the route. 4. At level 3 (conditional automation), the advanced driving system (ADS) can complete all aspects of the driving task under certain circumstances, but a human operator must be able to take over when the ADS requests it. The human driver performs the essential actions in the remaining scenarios. 5. At level 4 (high automation), the vehicle's ADS is capable of handling all driving duties on its own in circumstances where human involvement is not necessary. 6. Finally, level 5 (Full automation), entails full automation, when the vehicle's ADS is capable of performing all functions in all circumstances and no human driver assistance is needed. The use of 5G technology will make it possible for complete automation because it will allow vehicles to interact not only with one another but also with traffic lights, signs, and even the roads itself. Working of Autonomous Vehicle: The software that autonomous cars use to operate is executed by sensors, actuators, sophisticated algorithms, machine learning systems, and robust processors. Based on a range of sensors placed in various places of the automobile, autonomous vehicles build and update a map of their environment. Radar sensors monitor the position of nearby vehicles. Video cameras detect traffic lights, read road signs, track other vehicles, and look for pedestrians. Lidar (light detection and ranging) sensors bounce pulses of light off the car‘s surroundings to measure distances, detect road edges, and identify lane markings. Ultrasonic sensors in the wheels detect curbs and other vehicles when parking. Sophisticated software then processes all this sensory input, plots a path, and sends instructions to the car‘s actuators, which control acceleration, braking, and steering. Hard-coded rules, obstacle avoidance algorithms, predictive modeling, and object recognition help the software follow traffic rules and navigate obstacles. 29 A Learning Manual for Emerging Trends in Mechanical Industry Figure 1.5: Important components of an Autonomous Vehicle The objective of self-driving cars (SDC) is to be able to control a vehicle similarly to a human driver. There isn't a driver behind the wheel, which is the only drawback. You‘re undoubtedly asking how a computer (or a car, in this scenario) manages to accomplish something so difficult without approaching human intellect. We must understand the five elements that make up an SDC in order to respond to that. Figure 1.6: Computer Vision system un AV‘s Computer Vision: We need to be able to see the environment around us, just like a human driver, whether that means scanning the horizon for oncoming traffic or reading road signs. Similar to how a person observes their environment, a car uses computer vision. The objective of computer vision for SDC is to be able to recognize objects close to the car. Convolutional neural networks, a type of image categorization network, are used in this process. Sensor Fusion: Imagine that the car is trapped in heavy traffic. By examining his surroundings, the motorist is aware of this. This is analogous to the concept of sensor fusion. It involves being able to understand 30 A Learning Manual for Emerging Trends in Mechanical Industry the environment in great depth. The term "sensor fusion" was coined since an SDC has many sensors installed, allowing us to gather all the required information and combine it to provide our automobile a better diagram. Localization: Autonomous vehicles are able to observe and understand their surroundings. In SDC, we want to be able to locate our automobile in the actual world so that we can decide how to drive from A to B more effectively. Here, things become challenging and sophisticated mathematical techniques are needed. Consider localization like you would your phone's GPS for the time being. Path Planning: Autonomous vehicles have the ability to observe, understand their surroundings, and find themselves. The journey's planning is now the following step. Take a human driver as an example. The human driver is probably considering which streets to avoid and the anticipated arrival time as they go. Exactly the same thing a SDC does. Control: Once we determine our path, the car only has to be able to operate the steering wheel. The only difficult part of driving the car is to do so in a human-like manner rather than robotically. Additional Features of SDC: With the aid of GPS satellites, the Global Positioning System (GPS) enables us to establish a vehicle's position in space. The GPS data can be used to determine the vehicle's latitude and longitude. The kind of sensor used can affect how accurate GPS is. Figure 1.7: Block Diagram of Software integration used in an Autonomous Vehicle Inter-process communication (IPC) or shared memory can be used by each block to communicate with others in the block diagram above. This situation is ideal for ROS messaging middleware. A publish/subscribe system was used in the DARPA Challenge to carry out these functions. 31 A Learning Manual for Emerging Trends in Mechanical Industry Adaptive Cruise Control: Adaptive cruise control, sometimes known as ACC, is a feature of the vehicle technology utilized in driverless automobiles. This system has the ability to automatically change the speed of the car so that it keeps a safe distance from the cars in front of it. This feature makes use of data collected by sensors on the car to enable the car to carry out actions like braking when it detects any vehicles ahead. Following processing of the data, the correct commands are transmitted to the vehicle's actuators, which manage the vehicle's responsive movements including steering, acceleration, and braking. Highly automated vehicles can react to traffic light signals and other non-vehicular activities thanks to fully automated speed control. Advantages of Autonomous Vehicles: Comparing autonomous vehicle technology to human-driven vehicles, there may be certain benefits. 1. They might boost safety for drivers; car accidents claim the lives of many people every year, but autonomous cars might reduce the number of fatalities because their software is more likely to be error-free than that of humans. 2. Another potential benefit of autonomous vehicles is a reduction in traffic congestion brought on by fewer accidents. Autonomous driving can also do this by eliminating human actions that clog up traffic, particularly stop-and-go traffic. 3. Another potential benefit of autonomous driving is that it may provide more convenient transportation for those who are unable to drive due to age or physical limitations. 4. Additional advantages that come with an autonomous car are the elimination of driving fatigue and being able to sleep during overnight journeys. 5. In a recent research, experts highlighted three trends: (a) Vehicle automation (b) Vehicle electrification, and (c) Ridesharing; that, if implemented simultaneously, would fully realize the potential of autonomous vehicles. These "three revolutions in urban mobility" by 2050 might be able to: Reduce traffic congestion (30% fewer vehicles on the road) Cut transportation costs by 40% (in terms of vehicles, fuel, and infrastructure). Improve walkability and livability. Free up parking lots for other uses (schools, parks, community centers). Reduce urban CO2 emissions by 80% worldwide. Challenges with Autonomous Vehicles: Several regions of the world are testing fully autonomous (Level 5) vehicles, although none are presently accessible to the general public. A few of them are discussed here in brief. Radar and Lidar: Lidar is more expensive and keeps trying to balance resolution and range. Would Lidar signals from different autonomous vehicles on the same route interfere with one another? Will the frequency range be wide enough to facilitate the mass production of autonomous 32 A Learning Manual for Emerging Trends in Mechanical Industry vehicles if multiple radio frequencies are available? These are the complex issues that scientists and technologists must resolve. Weather Conditions: What happens when a self-driving vehicle drives through a lot of rain? When the road is snow-covered, lane markers disappear. How will the cameras and sensors be able to identify the lane lines if they are obscured by water, oil, ice, or debris? These are the difficulties the researchers must overcome. Traffic Conditions and Laws: Will driverless vehicles encounter difficulties on bridges or in tunnels? How will they perform in heavy traffic? Will autonomous vehicles be limited to a particular lane? Will they be permitted to use the carpool lane? And what about the fleet of vintage vehicles that will continue to circulate on the roads for the next 20 or 30 years? These are the difficulties that policymakers dealing with SDC have to deal with. Accident Liability: When an autonomous vehicle causes an accident, who is responsible? The manufacturer? The human passenger? The latest blueprints suggest that a fully autonomous Level 5 car will not have a dashboard or a steering wheel, so a human passenger would not even have the option to take control of the vehicle in an emergency. Artificial Vs Emotional Intelligence: Human drivers rely on subtle cues and non-verbal communication, like making eye contact with pedestrians or reading the facial expressions and body language of other drivers, to make split-second judgment calls and predict behaviours. Will autonomous cars be able to replicate this connection? Will they have the same life-saving instincts as human drivers? Major Players involved in Manufacturing of Self-Driving Car‟s: Over 250 companies are actively working to make self-driving or driverless cars a reality, including automakers, technology providers, services providers, and tech start-ups. The businesses below are just a few of the many that want to use fully autonomous car technology. Microsoft Apple Motional Magna International AutoX Cruise Waymo Swift Navigation Embark Trucks CARMERA Zoox 33 A Learning Manual for Emerging Trends in Mechanical Industry Nauto Cruise Tesla Baidu Alphabet Inc's (GOOGL. O) Waymo Aurora Innovation Inc (AUR. O) Sample Multiple Choice Questions 1. Micro hybrid technology is the --------- level of vehicle hybridization a. Highest b. lowest c. moderate d. nano 2. Plug in Hybrid vehicles are known as ---- a. PHV b. PIMV c. PHEV d. EV 3. Okinawa is one of the fastest growing Electric Vehicle two-wheeler manufacturers in India. a. Ather b. Mahindra Scooter c. Bajaj Scooter d.Okinawa 4. -------------- battery has high specific energy. a. Lithium b. Sodium Sulphur c. Ammonia d.lead acid 5. TCS stands for ------ a. Torque Centralized Sensor b. Torque Cell sensor c. Traction Control System d. Tyre Control System 34 A Learning Manual for Emerging Trends in Mechanical Industry Unit 2 Process Engineering 2.1 Process Boilers Overview A process boiler is a type of boiler with a capacity (rated maximum input) of 90KW or more, that serves a process. A process is an activity or treatment that is not related to the space conditioning, service water heating, or ventilating of a building as it relates to human occupancy. Process Boilers used in various Industries Process boilers are used in various industries such as dairy, sugarcane, pulp & paper, chemical, beverages and textile industries also in thermal power station etc. Process boilers are having application in following areas Agriculture Electrical industry Refineries Animal food Food packaging industry Spinning mills industry Automotive Fruit processing Tobacco industry industry Bakeries Glass fiber production Tyre manufacturing Ceramic industry Metal-working industry Weaving mills Cheese and dairies Pharmaceutical industry Wood processing Distilleries Dyeing factories Plastics manufacturing Figure2. 1: Process Boiler 35 A Learning Manual for Emerging Trends in Mechanical Industry Working of Process Boiler Figure 1 shows Basic features of process boiler. A process boiler system is a hot water or steam boiler operated with a certain kind of fuel. The boiler heats up or evaporates the water inside it, which is then transported to the consumers via pipe systems. In case of hot water the transport energy is generated by pumps, in case of steam the transport is based on inherent pressure. The cooled water or the condensed steam returns to the boiler where it can be heated again. Loss of water is compensated by makeup water pump. Flue gases created by combustion are discharged into the atmosphere through a chimney. In process boilers steam generation capacity ranges from 175 kg/h to 55 000 kg/h are available for industrial applications. High-quality equipment with intelligent control systems, modern burner technology and efficient heat recovery devices ensure environmentally friendly, economic and fully automatic boiler operation. These boilers are welded from thick steel plates that are up to 35 mm thick, making pressures of 30 bar and more possible. A thermal output of up to 38 MW is possible from a single boiler. The use of process boiler systems in practice Food industry Food must often be heated or boiled during processing. Thus this industrial sector obviously needs plenty of thermal energy. However, some steam applications are still stunning; a good example is potato processing. Cold potatoes are filled in a big pressure vessel and hot steam is abruptly injected. The abrupt heat supply causes the potato peels to fall off so they do not have to be peeled by hand any more Breweries In complex production process of breweries, malt has to be ground coarsely and mixed with water. The brewer calls this mashing. The mash must be heated to various temperatures in two to four hours for which the steam previously generated with the steam boiler is used. Subsequently, hops are added and the mixture has to cool down. Then yeast is added and triggers the fermentation so that the breweries get the desired effect. Depending on the type the breweries still has to mature for up to three months until it can be filled in bottles or barrels. Dairy Process Boilers are mostly used in dairy industry for milk pasteurization and UHT. Milk Boiler ensures good shelf life and destroys disease-causing microorganisms. This emphasizes the requirement for flexible and reliable heat sources, which may keep the dairy milk systems running without any hurdle. Dairy Industry use steam for various purposes, Such as Heat Treatment of dairy products & Dairy Processing Industrial milk boiler used to generate steam for following processes in dairy Industry (1) Milk powder (2) Cheese (3) Liquid milk pasteurization 36 A Learning Manual for Emerging Trends in Mechanical Industry (4) Ultra-heat treatment (UHT) Milk Figure 2.2:- Process Boiler used in dairy industry Sugar Industry Electricity and steam are almost required in every step of raw sugar process, especially in juice extraction, clarification, evaporation and sugar drying, good quality steam takes a crucial role. Thus selection of steam boilers becomes very important for sugar plant. Bagasse, nearly 30% fiber contained in sugar cane, is produced during the processing of sugarcane, is burned as fuel for the generation of steam and power required for the operation of sugar mill. In fact, most cane sugar factories have been designed to be energy self-sufficient, with sugar as the primary product and bagasse as the primary fuel. A bagasse-fired cogeneration system, made of steam boilers and steam driven turbo- alternators, provides all the steam and electricity needed to run the cane mills and factory, leaving little surplus bagasse. The bagasse is fired in the boiler for producing steam at high pressure, which is extracted through various single high capacity turbines and used in the process. The installation of high pressure boilers and high pressure turbo-generators has provision for the operation of co-generation plant during the off-season also that enhances the power generation from 9 MW to 23 MW. 37 A Learning Manual for Emerging Trends in Mechanical Industry Figure 2.3:- Process boilers used in sugar industry Paper & Pulp Industry Boilers in the paper industry are used to generate steam for power and process systems. High pressure steam is generated for steam turbine generator sets to produce electric power. Medium and low pressure steam is used for various process heating applications such as heating and softening pulp wood chips for further reduction by chemicals to make wood pulp. Steam is also used to heat chemicals and other processes. In the paper making process, steam is used to evaporate moisture from pulp and to heat rotating dryer drums to dry the paper stock. Depending on the location and type of pulp wood used, bark chips can be burned as fuel for boilers. Introduction to Combi-Boilers A combination boiler or commonly known as a Combi Boiler is the combination of both Water Tube boiler and Smoke Tube Boiler. Thermo dyne Engineering Systems has a vast experience in manufacturing Combi Boilers. Combitherm models and Ultra models are both classified under Combi Boilers. Generally, the design of a Combi Boiler is an amalgamation of both Water wall (Membrane) as well as Shell and tube design. Combi-Boilers are very common in India and can be used to produce and utilize steam in various industries such as Rice Mills, sugar mills, Rubber industries and many more. 38 A Learning Manual for Emerging Trends in Mechanical Industry Figure22. 4: Combi-Boiler In Combi-boilers water wall acts as a furnace enclosure where combustion of fuel takes place. Here the tubes surround the furnace and water flows inside membrane tubes. The fuel is fed on the grates of the furnace and air is supplied through the Forced Draft Fan below the grates and as the fuel comes in contact with air and heat, combustion process takes place. This is the zone where the maximum radiation heat transfer takes place between the flue gases and the water. After the combustion process, flue gases enter the shell and tube zone where flue gases travel through high velocity inside the tubes and water is on the shell side. This is the zone where convection heat transfer takes place between the flue gases and the water. Combi boilers are the most efficient boilers in terms of cost savings and fuels savings. Their unique water wall membrane and smoke tube shell have the benefits of both water tube boiler as well as the smoke tube boiler and so it has a combined feature of both of these designs. High furnace volume in Combi Boilers extracts maximum radiation heat from the flue gases at high temperatures while at low temperatures high velocity of flue gases is responsible for extracting maximum convection heat. During its course of motion, it transfers heat to the – (i)Water present in the tubes in the Water Wall Membrane (ii) Water present in the Boiler shell through tubes This type of steam boiler offers a high degree of reliability and trouble-free operation. They effectively operate at moderately high pressures and steam flow capacities, unlike packaged type smoke tube boilers. 2.2 Waste Heat Recovery System (WHR) Waste heat recovery‖ is the process of ―heat integration‖, that is, reusing heat energy that would otherwise be disposed of or simply released into the atmosphere. By recovering waste heat, plants can reduce energy costs and CO2 emissions, while simultaneously increasing energy efficiency. Typical Examples of Waste Heat Recovery 39 A Learning Manual for Emerging Trends in Mechanical Industry Several common consumer items recover waste heat. For example, consider turbocharged cars, which are provided by multiple car manufacturers. In regular, non-turbocharged cars, the internal combustion gasoline engine expels hot gas through the car‘s exhaust after its fuel is burned. That gas contains both heat and kinetic energy a portion of which can be recovered. Turbocharged engines divert the hot gas to a turbine, which is used to spin an air compressor. The compressed air is routed to the engine‘s combustion chamber with the vaporized gasoline, resulting in a more efficient ignition and greater power made with lower fuel consumption. Necessity of waste Recovery System Waste heat recovery (WHR) is essential for increasing energy efficiency in the chemical process industries (CPI). Presently, there are many WHR methods and technologies at various stages of implementation in petroleum refineries, petrochemical, chemical and other industry sectors. Increasing energy costs and environmental concerns provide strong motivation for implementing more and newer methods and technologies for WHR. Waste heat is energy that is rejected to the environment. It arises from equipment and operating inefficiencies, as well as from thermodynamic limitations on equipment and processes. Often, part of waste heat could potentially be used for some useful purpose. At present, about 20 to 50% of energy used in industry is rejected as waste heat. A significant part of this wasted energy is low- temperature heat that is sent to the atmosphere mainly from cooling water, fin-fan coolers and flue gases. WHR can be defined as the process of capturing some portion of the heat that normally would be wasted, and delivering it to a device or process where it can be used as an effective, economical and environmentally friendly way to save energy. Large investments are presently incurred to exhaust waste heat to the atmosphere in the form of cooling towers, fin-fan coolers and very tall stacks for the disposal of flue gases. WHR has the potential to minimize these costs, and to reduce environmental impact along with several other benefits. Development of an optimum WHR system depends on the following factors: Quantity and temperature of waste heat: The quantity of waste heat should be large enough to make WHR economical. Costs of WHR systems are lower with increased availability of waste heat. Usually, waste heat at high temperatures can be utilized with a higher efficiency and with better economics. Also, more technology options are available for converting waste heat at high temperatures into other useful energy forms than waste heat at low temperatures Uses of recovered waste heat: The end use of recovered heat has a large influence on the implementation of WHR. For example, if the WHR project generates low-pressure steam that is already available in excess supply, then there will be little or no payout Cost of energy: This will be greatly influenced by the presence or absence of a cogeneration facility in the company Availability of space: In operating plants, space availability can be the biggest constraint. It is beneficial to place WHR equipment close to the heat sink to minimize piping and operating costs 40 A Learning Manual for Emerging Trends in Mechanical Industry Minimum allowable temperature of waste heat fluid: For the case of flue gases heat recovery using carbon-steel equipment and ducting, the flue gases temperature should not be lower than the flue gases acid dew point Minimum and maximum temperature of the process fluid: If WHR generates steam and exports it to a steam header in a petroleum refinery, then WHR and steam temperature are dictated by the steam header pressure, since petroleum refineries generally operate steam headers at fixed pressures. Low-temperature steam generation will result in more WHR compared to high-temperature steam generation Chemical compositions of waste heat process fluids: These will dictate the materials of construction for the WHR system, and consequently affect the costs. Facility‟s heat-to-power ratio: If the heat-to-power ratio in the facility is higher than that for the cogeneration plant, the excess steam demand is usually met by utility boilers. Any saving in steam demand (by better heat recovery) saves fuel in the utility boilers and leaves the operation of the cogeneration plant unchanged. However, if the cogeneration plant meets the entire site‘s heat load, the value of savings from better heat recovery can be considerably reduced. Saving a ton of steam not only saves the fuel required to raise it, but also eliminates the associated power output that is produced at 80–90% marginal efficiency Features of Condensate Recovery Pump: Uses inexpensive steam, air or gas to pump the condensate Negligible steam consumption Zero Maintenance, no cavitation, no leaking seals, impeller wear or motor problems Only one moving part (SS float) increases reliability Superior build quality and rugged construction Pre-wired, pre-piped packaged Skid Mounted for easy installation Widest range of steam-operated pumps Skid Mounted Unit which is easy to install 41 A Learning Manual for Emerging Trends in Mechanical Industry Figure 2.5 Condensate Recovery Pump Advantages of Condensate Recovery Pump 1. Reduction in Fuel Bill: 2. Reduction in Water charges: 3. Reduction in Exhaust Treat plant (ETP) load: 4. Maximizing boiler output: 5. Reduction in Blow down Loss: Condensate is pure water, which contains almost no total dissolved solids (TDS). Returning more condensate to the feed-tank reduces the need for blow-down & thus reduces the energy lost from the boiler. Flash Steam Separator as WHR unit The steam is used in the process plants at various pressures depending upon the temperature requirements. The Condensate Recovery Pump from the high pressure steam when comes to low pressure, some part of the condensate get evaporated which is called as flash steam. Recovering the maximum possible flash steam back to the feed water tank reduces the fuel consumption of steam boiler. Flash steam has substantial amount of heat which is ignored & vented to atmosphere in most of the process plants. Heat recovery steam generators (HRSG) A heat recovery steam generator (HRSG) is a solution, when it is necessary recover heat from a hot gas stream. One can produce steam that can be used in a process (cogeneration) or used to drive a steam turbine (combined cycle). The HRSG boilers are manufactured either in horizontal or vertical types. The vertical boiler is more compact in structure and can be fit in smaller plants and even indoor facilities. The horizontal boiler is used mainly in larger plants. Supplementary firing can be added to both boiler types so that the required energy volume can be produced with gas turbine running on partial loads. 42 A Learning Manual for Emerging Trends in Mechanical Industry Saving Calculation 1000 kg/hr condensate recovered can save Rs. 45, 00,000/- per year as fuel considering 20 hrs a day & 300 days a year operational.1000 kg/hr condensate recovered can save Rs. 700,000/- per year on Coal as fuel considering 20 hrs a day & 300 days a year operational. The payback for the complete system comes out to be less than 6 months. Engine waste heat recovery Technology Rising fuel prices and the increasing demand for high fuel economy make the improvement of the working efficiency of engines become necessary, thus resulting in the application of waste heat recovery (WHR) technologies. For light duty passenger vehicles, tight packaging constraints and the relatively low duty cycle of combustion engines make waste energy recovery difficult. Thus, the most promising WHR technology application lies in engines that operate steadily at high load for sustained periods, such as that found in heavy-duty diesel trucks. The efficiency of a heavy truck diesel engine is generally less than 42%. Approximately 15% of fuel energy is wasted in the coolant heat transfer, whereas 8% is consumed through the air charging cooler. Friction and radiation account for 3% of fuel energy consumption. Exhaust gas accounts for the largest amount of waste energy: approximately 19% of the total fuel energy. Finally, approximately 13% of fuel energy is consumed during the exhaust gas recirculation period. Among the various types of waste heat, the heat contained in exhaust gas and coolant is generally the most promising for recovery. WHR technologies can be classified into Electric turbo-compounding (ETC) systems Thermodynamic organic Rankine cycle (ORC) Thermoelectric generators (TEG) Hydrogen generation (HG) by using exhaust gas heat energy Hybrid pneumatic power systems (HPPS), Advanced WHR Technology Various methods have recently been adopted in internal combustion engines (ICE) to meet increasingly stringent emission regulations, such as diesel particulate filters, three-way catalytic converters, and selective catalytic reduction. The different advanced methods are listed & discussed below 1. Hydrogen generation by using exhaust gas waste heat 2. Thermoelectric generators 3. Thermodynamic cycle of organic Rankine cycle 4. Hybrid pneumatic power systems (HPPS) 5. Electric turbo compounding (ETC) systems. 1. Hydrogen generation by using exhaust gas waste heat Engine exhaust heat energy has been used to heat and decompose methanol and other auxiliary fuels into hydrogen to improve the original heat value of fuels, increase combustion rate, and reduce emissions. For example, hydrogen can be used for homogeneous charge compression 43 A Learning Manual for Emerging Trends in Mechanical Industry ignition (HCCI) combustion. Because ignition timing control is crucial in the application of HCCI combustion in engines, ignition timing control can be addressed by adjusting the proportion of dimethyl ether and hydrogen gas. Engine exhaust gas waste energy can be used for hydrogen production without any changes in operating conditions. An HG system is shown in Figure 6. Figure 2.6 Hydrogen Generation WHR System 2. Thermoelectric generators Thermoelectric materials are semiconductor materials that enable the conversion between heat energy and electric energy based on the thermoelectric effect. The thermoelectric effect refers to a phenomenon whereby a temperature difference creates an electric potential or an electric potential creates a temperature difference, including the Seebeck effect, the Peltier effect, and the Thomson effect. A schematic setup of a thermoelectric generator is shown in Figure 7. Figure 2.7 Thermoelectric generators 44 A Learning Manual for Emerging Trends in Mechanical Industry 3. Thermodynamic cycle of organic Rankine cycle Because of the low temperature of engine exhaust gas, the traditional Rankine cycle using the water as the working fluid cannot obtain ideal working performance. So, Organic Rankine Cycle has become very popular method to improve the performance WHR because it works well with low- grade energy at a low flow rate. 4. Hybrid pneumatic power systems (HPPS) HPPS generally consists of an ICE, an air compressor, a pressure tank, and a high-efficiency turbine. A concept schematic setup of HPPS is shown in Figure 7. Figure 2.8 A concept setup of hybrid pneumatic power systems The main working principle of pneumatic hybridization engines is to recover energy from a braking phase or from a combustion phase by pumping the exhaust gas or the pressurized air into the air tank, then the air tank can then be restored to start the engine or charge the engine during the strong transient accelerations or short-term high-power output period. An advantage of the pneumatic hybridization engine is that the pressurized air can be pumped into the combustion chamber to overcome the turbo-lag problem during the speedup period of the turbocharger, which can maximize the performance of the turbocharger. Pneumatic hybridization engines also offer improved fuel economy and reduced emissions. 5. Electric turbo compounding (ETC) systems Considering the high temperature, relatively high pressure, and kinetic energy of exhaust gas, we classify waste energy of exhaust gas as thermal energy, pressure energy, and kinetic energy, with pressure energy accounting for the main part of the waste energy. ETC systems, which are mainly based on the Brayton cycle, are a very useful way to recover waste pressure energy. Figure 45 A Learning Manual for Emerging Trends in Mechanical Industry 11 presents the setup of ETC system. The compound turbine mechanical-driven energy recovery prototype was originally proposed by the Volvo Corporation. Figure 2.9 Electro turbo Compounding The exhaust gas energy is transformed into shaft work through the turbine. Exhaust gas energy recovery of up to 20% is possible; this value is equal to a 5% decrease in fuel costs. However, efficient fuel consumption is possible only when the process is applied to high-load applications. More research attention was thus given to compound turbine power generation systems. Fuel economy can be improved by up to 10%, whereas power density can be increased by 20%. Waste Heat Boiler (WHB) Using a principle similar to economizers, waste heat boilers recover heat generated in furnaces or exothermic chemical reactions at industrial plants. These locations may contain significant energy that should not be wasted up a stack. Instead, this energy can be captured to generate low-to- medium pressure steam in a waste heat boiler (WHB). A WHB can also be used to remove the heat from a process fluid that needs to be cooled for either transport or storage, and generate steam from that heat. The steam generated in WHB may be used for heating applications, or to drive turbines that generate electricity, compress vapors, or pump liquids. WHB steam may contain significant wetness, so it is recommended that a high efficiency separator and steam trap combination is installed to ensure that the WHB delivers optimal quality steam to the recipient process. 46 A Learning Manual for Emerging Trends in Mechanical Industry Figure 2.10 – Waste Heat Boiler Absorption Chiller Some energy efficient CHP systems may add refrigeration by incorporating absorption chillers that use steam created from waste heat. The mechanism of absorption chillers can be broken down into the following stages: 1. Diluted absorbent liquid (60% lithium bromide salt, 40% water) is preheated with condensate as it moves from the absorber to the generator. 2. In the generator, the absorbent liquid is heated by steam, which causes some of the water contained within it to vaporize, making the liquid more concentrated. 3. The concentrated absorbent liquid flows downward back to the absorber to capture more water in its continuous loop. At the same time, the water vapor moves to the condenser. 4. In the condenser, cooling water causes the vapor to liquify and flow downward toward the evaporator, which has near vacuum pressure. 5. Just prior to entering the evaporator, the condensed water flows through an orifice or expansion valve. This restriction limits flow, and the water again vaporizes to a cold mist at 4.5°C [40°F]. This is where refrigeration occurs. The low temperature vapor pulls heat out of the chilled water loop, lowering its temperature by about 5°C [9°F]. 6. The mist is heated when it absorbs heat from the chilled water loop, but the strong attraction of the concentrated salt solution pulls the water into the concentrated absorbent into the absorber, creating near vacuum pressure in the evaporator in the process. 47 A Learning Manual for Emerging Trends in Mechanical Industry Figure 2.11 Absorption Chiller Evaporator: Actual refrigeration occurs here. Water passes through a valve, creating a low temperature mist. Sprayed over the chilled water loop, it absorbs heat and cools the refrigerant. Absorber: Concentrated absorbent attracts water mist from the evaporator, creating near vacuum pressure while diluting the absorbent. Generator: The 60/40% mixture absorbent is heated, evaporating the water, with the concentrated (regenerated) absorbent returning to the absorber. Condenser: The water vapor supplied from the generator is condensed by transference of heat to cooling water. 2.3 Process Layout of Process Industry Process layout is a design layout of processing plant for the floor plan of a plant to improve efficiency by arranging machinery and equipment according to its function. Advantage of Process Layout: a. Lower initial capital investment. b. The optimum level of degree machine use. a. Food Industry- A food industry involves various processes like sourcing, preparing, production, food packaging, and distribution. The food manufacturing process includes many elements similar to other products such as clothing and cars. However, food manufacturers pay close attention to details like food safety, flavor, and shelf life. Some of the most common functions by which food processing equipment are grouped include: Preparation Mechanical processing 48 A Learning Manual for Emerging Trends in Mechanical Industry Heat processing Preservation Packaging Example :- Stages of Potato Chips Making Figure 2.12: - Stages of Potato Chips Making 1.Potato washing peeling machine:- Fig.2.13 1. This potato washing peeling machine is for medium & large potato chips plants. It integrates the function of washing & peeling. This machine equipped with a spiral discharge 7 spraying device, the machine has str