CSA W47.1:19 PDF - Certification of Companies for Fusion Welding of Steel
Document Details
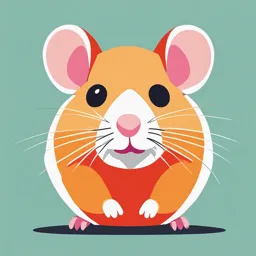
Uploaded by BestPerformingPlateau
Tags
Related
- CSA W47.1:19 Fusion Welding of Steel PDF
- CSA W47.1:19 Fusion Welding of Steel PDF
- Welding of Pipelines and Related Facilities PDF
- Welding of Pipelines and Related Facilities PDF
- Welding of Pipelines and Related Facilities PDF
- AWS B5.16:2006 PDF Specification for the Qualification of Welding Engineers
Summary
This document outlines the certification procedures for companies involved in fusion welding of steel, detailing personnel qualifications, test assemblies, and record-keeping requirements. It covers various welding types and positions.
Full Transcript
CSA W47.1:19 d) Certification of companies for fusion welding of steel robotic welding operators whose qualifications have not expired may extend their qualifications for a two-year period from the expiry date of the current qualifications by successfully completing a check test as specified in F...
CSA W47.1:19 d) Certification of companies for fusion welding of steel robotic welding operators whose qualifications have not expired may extend their qualifications for a two-year period from the expiry date of the current qualifications by successfully completing a check test as specified in Figure 35. 8.4.2 Welders may be granted an exemption from the two-year check testing requirement if the company can verify to the CWB's satisfaction that: a) the welder has continued to use the process in the class held throughout the previous two years and has used it in production within the last three months; and b) the welder maintains the requisite skills for the process. This can be demonstrated by providing radiographs or other suitable documentation to verify the welder’s ability to deposit sound weld metal consistently. Note: Suitable documentation may be in the form of UT, MT, RT, or Macro-etch reports issued by an organization as described in Clauses 8. 2 and 8.2.4.6. 8.5 Extent of qualification 8.5.1 Welding personnel qualifying on the test assemblies shown in Figures 6, 7, 8, 9, 11, and 12 shall be qualified for welding materials 3 mm (1/8 in) and above. Fillet weld tests shall qualify for all sizes of fillets (see Clause 8.5.5). 8.5.2 Welding personnel qualifying for sheet steel shall use the test assemblies specified in Annex J. Each position tested shall qualify for the range of positions as specified in Annex J. 8.5.3 For welding personnel qualifying for arc spot welding of decking, the range of qualification obtained for each deck thickness tested shall be as specified in Annex J. For thicknesses where a steel washer is used to prevent burnback, the welder shall not require a separate qualification. A steel washer shall be required for steel decking less than 24 gauge. The welder’s transferable qualification identification document shall show that the qualification was made with a washer. 8.54 A welder who has successfully completed an arc spot welding procedure qualification test will be considered qualified as a welder for arc spot welding of decking within the limitations of the procedure. The qualification shall be considered transferable unless the conditions of the test are unique to the company, in which case the qualification shall be nontransferable. 8.5.5 Welding personnel qualifying for stainless steel shall use the test assemblies specified in Annex K. Each position tested shall qualify for the range of positions as specified in Annex K. 8.5.6 Robotic welding personnel qualifying on the test assemblies shown in Figure 35 shall be qualified for welding materials 3 mm (1/8 in) and above. October 2019 Licensed to/autorisé A CSWind Viecnam, nnhaigmacswind.com, CSWind Vi L. Tax cods: 3500785873 So1d by/vendu par CSA Group/Groupe CSA on/ 9-21. -Single user 1li Storage, copying, d network pronibited. Le steckage. reproduction, ia distributien oa Lrucilisation ser le péecku eet 29 CSA W47.1:19 for fusion welding of steel Certification of companies 8.5.7 If the assemblies designated in Clauses 8.5.1, 8.5.2, 8.5.5, and 8.5.6 are not applicable, the company may submit alternative welder or welding operator test assembly configurations to be approved by the CWB. However, for such qualifications, when successful, nontransferable qualification identification documents shall be issued by the CWB and shall be valid only for the range of materials, thicknesses, joint types, or procedures, etc., as approved for use by means of the test assembly configuration. For welders, the qualification shall remain valid for a two-year period. Renewal of the qualification shall be granted after successfully welding the same alternative welder test assembly. 8.5.8 If the testing requirements of Clause 8.5.1 are not appropriate for the company’s type of welding operations, the company may qualify welders and welding operators for welding in the appropriate position(s) only. The test assembly configurations shown in Figures 6, 7, 8,9, 11, and 12, as appropriate, shall be used for the test. Such qualification shall qualify the welder or welding operator for welding in the appropriate classification and class only. The qualification shall be nontransferable. 8.6 Records of qualification 8.6.1 The CWB shall issue appropriate documentation to the welding personnel who pass the qualification tests defined in this Standard. 8.6.2 The documentation shall show as a minimum the following: a) tack welder’s, welder’s, welding operator’s, robotic welding programmer’s, or robotic welding operator’s name; b) qualification and expiry dates; c) welding process and mode of transfer for GMAW; d) position; e) mode of process application; f) electrode or electrode group or electrode/flux combination; g) thickness range; h) material limitations; i) testresults; and j) signature of the authorized CWB representative. 8.6.3 One of the following qualification identification documents, showing the qualification of the tack welder, welder, or welding operator, shall be issued by the CWB: a) atransferable identification card when qualification is based on standard test assemblies; b) anontransferable identification card when qualification is for specific process applications; or c) if deemed more suitable, under exceptional circumstances, a letter in lieu of an identification card. 8.6.4 The cards are the property of the CWB and shall be returned upon request. The company shall be responsible for ensuring that these cards or copies thereof can be produced as proof that a tack welder, welder, welding operator, robotic welding operator, or robotic welding programmer in its employ has a valid qualification or qualifications. October 2019 30 Licensed to/autorisé A CSiind Vietnam, nnhaiguicswind.com, CSWind Vietnam Co., LTD. Tax code: 3500785873 So1d by/vendu par CSA Group/Groupe CSA on/le 2023-09-21. -Single user license oaly. Storage, copying, distribution or use on fetuork prohibited. Le stockage, reproduction, la distribution, ou l'urilisation sur le réseau est interdit. CSA W47.1:19 Certification of companies for fusion welding of steel 9 Qualification of welding personnel 9.1 General Welding personnel shall weld only in the classification, class, thickness range, and process in which they have been qualified. The qualification of welding personnel shall be governed by the following: a) the process; b) the mode of transfer where applicable; c) the mode of process application; d) the classification (e.g., S, T, FW, or WT); e) the class (position of welding); f) the consumables; g) the thickness range; h) the ability to load and unload the system, for the operator; i) the ability to launch a production cycle; j) the ability to stop the production cycle if problems occur during the production cycle; and k) knowledge of the process. 9.2 Processes 9.2.1 This Standard covers the qualification of welding personnel for the following processes: a) shielded metal arc welding (SMAW); b) flux cored arc welding (FCAW) and metal cored arc welding (MCAW); c) d) e) f) gas metal arc welding (GMAW); submerged arc welding (SAW); gas tungsten arc welding (GTAW); and electroslag welding (ESW) and electrogas welding (EGW). Other welding processes may be used for qualification. In such cases, the company shall adapt the general provisions of this Standard to the process being used. 9.2.2 If multiple processes are used during the qualification test, each process shall be recorded on the welder’s or welding operator’s qualification record and qualification identification document, together with the sequence in which each is used (e.g., GTAW root and SMAW fill). 9.2.3 For the GMAW process, metal transfer includes the short-circuiting, globular, spray, and pulsed arc modes. A change to short-circuiting from globular, spray, or pulsed arc, or vice versa, shall require a separate qualification. 9.3 Consumables Electrodes used for the test shall be certified to the requirements of the latest edition of CSA W48 or the appropriate standards in the AWS A5 Series of Standards. October 2019 Licensed to/autorisé a viecnam, nnhaigmecswind am Co., LTD. Tax code: 3500785873, S0ld by/vendu par CSA Group/Groupe CSA on/le 2023-09-21, -8 e only. Storage, copying, distribucion or use on necuork prohibited. Le stockage, reproduction, 1a Giscribution, o L:urilisation sut Lo résehu s 31 CSA W47.1:19 Certification of companies for fusion welding of steel 9.4 Test assemblies 9.4.1 General 9.4.1.1 Full details of the standard test assemblies are shown in Figures 5 to 12. For S classification, three options available for testing are shown in Figures 8 and 9. Options 2 and 3 shall also require the welder or welding operator to qualify with a fillet weld for the same test position. 9.4.1.2 For welding operators qualifying with the ESW and EGW processes, the test assembly shall be as shown in Figure 10. 9.4.2 Fillet weld test assemblies 9.4.2.1 Tack welds shall be made on the back of the qualification assembly and shall not extend more than 20 mm (3/4 in) from the end of the fillet weld test assembly. Distortion or misalignment caused by tacking may be corrected before the test weld is deposited. 9.4.2.2 For the welder or.welding operator qualification fillet weld test, there shall be one stop and restart in the fillet as indicated in Figure 6. The fillet size shall not exceed 8 mm (5/16 in). 9.4.2.3 The fillet weld shall be fully welded and cleaned in the required position of welding. 9.4.24 For the tack welder qualification fillet weld test, a single-pass fillet weld, not less than 50 mm (2 in) long, shall be made in the centre of the test assembly as shown in Figure 7. 9.4.3 Plate test assemblies 94.3.1 Tack welds shall be made on the side of the joint opposite to the location for the test weld. The tack weld shall be not more than 20 mm (3/4 in) from the end of the assembly. Distortion or misalignment caused by tack welding may be corrected before the test weld is deposited. 9.4.3.2 The groove shall be fully welded and cleaned in the required position of welding. 94.3.3 There shall be one stop and restart in the root pass of each weld in the locations indicated in Figures 8, 9, and 12, and in the root pass of the fillet weld in the location indicated in Figures 8 and 9 if the joint configuration in Option 1 is used. If Option 2 or 3 is used, there shall be one stop and restart in the root pass of each weld location indicated in Figure 8. October 2019 Licensed to/autorisé A CSWind Vietnan, nnhaigmecswind.com, CSWind Vietnam Co., LTD Tax code: 3500785873, Sold by/vendu par CS Group/Groupe CSA on/le 2023-09-21. -Single user license only. Storage, copyins, distribucion or use on network pronibited. Le stockage, reproduction, la distribution, ou l'utilisation sur le réseau est interdit 32 CSA W47.1:19 Certification of companies for fusion welding of steel 9.4.3.4 For S qualification using Option 3 of Figures 8 and 9, the back gouged groove contour shall typically be U shaped. Its depth and width shall be uniform and sufficient to allow the back pass to adequately penetrate into the previously deposited weld metal. 9.4.3.5 Welding of the back pass shall not be allowed until a visual examination has been performed by the CWB's representative. If in the opinion of the CWB's representative an excessive amount of material has been removed (more than the root pass), the test assembly shall be considered a failure and a new assembly shall be welded. 9.4.3.6 The surface of the back gouged groove shall show no evidence of cracks or visible lack of fusion between the weld and base metals. Inclusions or porosity shall not exceed 2 mm (1/16 in) in the greatest dimension. The sum of the greatest dimensions of all inclusions and porosity shall not exceed 10 mm (3/8 in) in the 150 mm (6 in) length of the test assembly. 9.4.4 Pipe test assemblies 9.4.4.1 Pipe test assemblies shall have a joint configuration as shown in Figure 11. 9.4.4.2 Pipes shall be aligned with four tack welds, 90° apart, located where they will not be part of a test specimen. 9.4.4.3 For welding in the 1G position, the axis of the pipe shall be horizontal and shall be rotated during welding. The weld shall be deposited from above. Only one-half of the pipe’s circumference shall be welded during the test. 9.444 For welding in the 2G position, the pipe shall be fixed during welding. Only one-half of the pipe’s circumference shall be welded during the test. Qualification in the 2G position shall qualify for the 1G position. 9.44.5 One pipe assembly may be used for qualifying in the 1G and 2G classes. Only one-half of its circumference shall be welded in each of the respective positions during the test. 9.4.4.6 For making the flat, vertical, or overhead welds in the 5G position, the axis of the pipe shall be horizontal and shall not be rotated during welding. To make the horizontal weld in the 2G position, the axis of the pipe shall be vertical and fixed during welding. October 2019 Licensed to/ Sold by/vendu network 33 Tax cods: 3500785373 scribuzion or use on CSA W47.1:19 Certification of companies for fusion welding of steel 9.44.7 One combined pipe test assembly in positions 5G and 2G, as shown in Figure 3, shall be used for qualification for O class; otherwise, the same qualification may be obtained by successfully welding the test assembly in position 6G, as shown in Figure 3. 9.44.8 For welding in the 6G position, the pipe shall be inclined with its axis 45° to the horizontal. The joint groove shall be in a plane perpendicular to the pipe axis. Welding shall be done with the pipe fixed in that position (see Figure 3). 9.4.4.9 There shall be one stop and restart in the root pass in each of the locations indicated in Figure 13. 9.5 Test assembly base material The test assembly base material used for qualification shall have a specified minimum yield point of not less than 250 MPa (36 ksi) and not greater than 345 MPa (50 ksi). 9.6 Welding personnel classification 9.6.1 The welding personnel shall be qualified in one or more of the following classifications (see Clause 3): a) T classification; b) S classification; c) FW classification; and d) WT classification. Note: See Clause 9.14 for classification requirements. 9.6.2 Qualification for T classification shall also qualify for the S, FW, and WT classifications in the same process, class, and mode. Qualification for S classification shall also qualify for the FW and WT classifications in the same process, class, and mode. Qualification for FW classification shall also qualify for WT classification in the same process, class, and mode. Qualification for WT classification shall qualify for WT classification only. Qualification in S classification shall not be required before qualification forT classification. Qualification in FW classification shall not be required before qualification in the S or T classification. See Clause 9.7 for the definition of mode of process. 9.7 Modes of process application 9.7.1 The four modes of process application are listed below (separate qualification shall be required for each mode used by the welder or welding operator): a) manual welding; b) semiautomatic welding; c) mechanized welding; and d) automatic welding. See Clause 3. October 2019 Licensed to/autorisé A CSWind Vietnam, nnhaigmdcswind.com, CSWind Vietnam Co., LTD. Tax code: 3500785873 So1d by/vendu par CSA Group/Groupe CSA on/le 2023-09-21. ~Single user license only. Storage, copyins, distribution or use on network prohibited. Le stockage, reproduction, 1a distribution, ou l'utilisation sur le réseau est incerdit 34 CSA W47.1:19 Certification of companies for fusion welding of steel 9.7.2 Welders qualified for semiautomatic welding shall be considered qualified for single electrode mechanized and automatic welding in the same process(es), subject to the conditions and limitations of their welder qualifications, except that the period of validity will be indefinite. 9.8 Class and positions of welding Welding personnel shall be qualified demonstrated their ability as follows: a) flat — capable of welding in the b) horizontal — capable of welding c) vertical — capable of welding in d) overhead — capable of welding in and permitted to weld in the position in which they have flat position and of making a fillet weld in the horizontal position; in the flat and horizontal positions; the flat, horizontal, and vertical positions; and in the flat, horizontal, vertical, and overhead positions. 9.9 Tests and qualification 92.9.1 Depending on the classification, the welding personnel’s tests shall consist of a fillet weld, groove plus fillet welds, or other types of welds as applicable, executed with the applicable welding process in qualifying positions. These assemblies shall follow the test conditions and objectives of Clause 9 with respect to type of welds, stop/restart, etc. 9.9.2 Welding personnel may be qualified for a higher* class within one classification by performing the tests required for the higher qualification. However, the tests already passed for the lower qualification need not be repeated. * Horizontal is higher than flat; vertical is higher than horizontal; and overhead is higher than vertical. 9.9.3 For welding personnel qualifying in the vertical position, the progression of the welding shall be vertically up. Vertical-down progression of welding shall require separate qualification except as noted herein. Welding personnel successfully qualified for vertical-up welding need not be separately qualified for a) b) cover passes welded vertically down; root passes welded vertically down, if the root passes are completely removed by back gouging and back welded vertical-up; or vertical-down single-pass non-calculated stress welds less than 150 mm (6 in) in length on material not exceeding 3.0 mm (1/8 in). c) Welding personnel qualified for vertical-down progression of welding shall be issued a separate transferable identification document. 9.94 Welding personnel shall be qualified in the appropriate classes in accordance with the requirements given in Table 2. The extent of validity of a qualification with a given F group designation of electrodes for the shielded metal arc welding process shall be in accordance with Table 1. October 2019 Licensed to/autorisé A CSWind Vietnam, nnhaigmicswind.com, CSWind Vietaam Co., LTD. Tax code: 350078; Sold by/vendu par CSA Group/Groupe CSA o user License only. Storage, copying, di netuork prohibited. Le stockage, ucion, ou 1'ucilisacion sur le réseau est interdit 35 CSA W47.1:19 Certification of companies for fusion welding of steel 9.9.5 For qualification with the F4 electrode group designation, the first pass may be deposited with an electrode from a different group. In such cases the welder shall only be qualified for the sequence in which the electrodes were used. The sequence shall be noted on the welder’s qualification record and qualification identification document. 9.9.6 Welding personnel qualified with a certified electrode and shielding medium combination shall be considered qualified to weld or tack weld with any other certified electrode and shielding medium combination for the process used in the qualification. For the FCAW process, a qualification obtained with a) any self-shielded electrode also qualifies for all flux-cored and metal-cored gas-shielded electrodes; and b) any gas-shielded flux-cored or metal-cored electrode also qualifies for self-shielded electrodes. 9.9.7 Welding on galvanized surfaces shall require separate qualification. In such a case all provisions of Clause 9.4 shall be applicable except that the test assembly shall be of galvanized material. 92.9.8 Where Option 1 of Figures 8 and 9 is used, the fillet weld shall be visually inspected for the leg size, undercut, and profile before the groove is welded. 9.10 Test methods 9.10.1 Radiographic examination 9.10.1.1 Welds that are subject to radiographic testing in addition to visual inspection shall have no cracks and shall meet the acceptance criteria detailed in Table 21. 9.10.1.2 Radiographic examination may be used at the discretion of the company for all processes except for semiautomatic GMAW, in which case only bend tests may be used. In cases where radiographic examination indicates lack of fusion at the junction between either of the two plates and the backing, the company may, at its discretion, have root-bend tests conducted, the results of which shall take precedence. Three specimens shall be cut from the test assembly, with the area(s) in question situated within the specimen. 9.10.1.3 For radiographic examination, where permitted, only the 150 mm (6 in) centre portion of the plate assembly shall be subject to quality appraisal as specified in Figure 9. For the SMAW, FCAW, MCAW, and GTAW processes, the length shall be 115 mm (4-1/2 in) as specified in Figure 8. 9.10.14 For radiographic examination, the reinforcement shall be substantially flat and smooth. The backing need not be removed. October 2019 36 Licensed co/autorisé A Cswind Vietaam, nmhaigmecswind.com, CSWind Vietnam Co., LTD. Tax code: 3500785873 S01d by/vendu par CSA Group/Groupe CSA on/le 2023-09-21. -Single user license only. Storage, copying, discribucion or use on necuork prohibited. Le stockage, reproduction, la distribution, ou 1'ucilisacion sur le résesu est incerdit. CSA W47.1:19 Certification of companies for fusion welding of steel 9.10.1.5 When radiography is to be used, the permitted imaging system(s), procedure, and technique shall be in accordance with CSA W59. 9.10.1.6 Personnel performing radiography on welder and welding operator qualification test assemblies shall be qualified in accordance with the regulatory requirements of the jurisdiction where the radiographic testing is to be conducted. 9.10.2 Root- and face-bend specimens 9.10.2.1 Each test specimen shall be bent in a jig substantially in accordance with one of the jigs shown in Figure 18. Any suitable means may be used for moving the plunger member in relation to the die member with the weld at midspan for jigs as shown in Figure 18. Root-bend specimens shall be placed with the root of the weld directed toward the gap for jigs as shown in Figure 18 a) and b) or shall have the root side of the specimen contacting the roller for the jig as shown in Figure 18 c). Face-bend specimens shall be placed with the face of the weld directed toward the gap for jigs as shown in Figure 18 a) and b) or shall have the face side of the specimen contacting the roller for the jig as shown in Figure 18 c). The two members of the jig shall be forced together or moved in relation to one another until the specimen is bent through an angle of 180°. 9.10.2.2 ForT a) b) c) classification the bend tests shall be performed as follows: the odd-numbered specimens shall be subjected to the root-bend test; should the root-bend test fail, the test shall be considered a failure; and inthe case of satisfactory root-bend tests, the even-numbered specimens shall be subjected to the face-bend test. 9.10.3 Macro-etch specimens 9.10.3.1 For fillet weld test assemblies, two transverse sections of the weld shall be cut from the test assembly as shown in Figure 6 and polished and etched with a suitable etchant to clearly reveal the weld fusion boundary. 9.10.3.2 Both macro-etched test specimens, when inspected visually with a maximum magnification up to 5 power, shall conform to the following requirements: a) fillet welds shall have fusion to the root of the joint, but not necessarily beyond unless required; b) minimum leg size shall meet the specified fillet weld size; no leg size more than 3 mm (1/8 in) larger than the minimum specified shall be allowed; and c) the fillet welds shall have the following: i) no cracks; October 2019 Licensed to/autorisé A CSWind Vietnam, anhaigmicswin Sold by/vendu pa 21 network pronibited. Le stockage, raproduction, 37 CsHind Vietnam Co., License on LTD. Tax code: 350078; rage, copying, discribution Sur le réseau ect interdic