Silicone Encapsulants and Gels Selection Guide PDF
Document Details
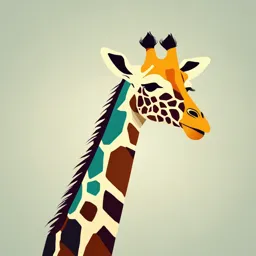
Uploaded by ImprovedXylophone5638
Tags
Summary
This document is a guide to Dow Performance Silicones encapsulants and gels, suitable for electronics and advanced assembly. It covers various aspects, including their unique properties and benefits in comparison to organic-based encapsulants and gels. The document details reasons for choosing encapsulants or gels over conformal coatings and the role of Dow Performance Silicones in supporting these applications.
Full Transcript
EL EC T RO N I C S AN D A DVA NCE D A S SE MBLY Imagine minimizing stress to maximize reliability with proven silicone encapsulants and gels Encapsulants and gels selection guide Encapsulants and gels selection guide Why choose Dow Performance Silicones...
EL EC T RO N I C S AN D A DVA NCE D A S SE MBLY Imagine minimizing stress to maximize reliability with proven silicone encapsulants and gels Encapsulants and gels selection guide Encapsulants and gels selection guide Why choose Dow Performance Silicones? Dow Performance Silicones has been a global leader in silicone- Extensive know-how based technology for more than seventy years. Headquartered Dow Performance Silicones multiplies the value of its products in Michigan, USA, we maintain manufacturing sites, sales and with deep in-house expertise and an extended network of customer service offices, and research and development labs industry resources. in every major geographic market worldwide to ensure you receive fast, reliable support for your processing and application Collaborative culture development needs. Dow Performance Silicones works closely with you to help reduce Unique product technology time and cost at every stage of your new product development. To describe Dow Performance Silicones is to describe the history Stability and evolution of silicone technology, which generated a legacy of For over seven decades, Dow Performance Silicones has been innovative and reliable products under the Dow Corning label for a global leader who invests in manufacturing and quality to help more than seven decades. Today that legacy continues under the fuel customer innovation through a consistent supply of proven DOWSIL™ brand name, which encompasses more than 7,000 silicone products. proven silicone products and services. Few companies offer an encapsulant portfolio with comparable breadth and proven performance, and none match our history in silicone technology. Why choose a silicone encapsulant or gel versus a conformal coating? Encapsulants offer better protection and faster, simpler cure options than coatings when: PCB features and components are taller than 200 microns A PCB presents a more complicated landscape, or thin sensitive wires or solder joints 2 Encapsulants and gels selection guide Why choose silicones versus organic-based encapsulants and gels? As a class of materials, silicones generally offer demonstrable Reduce or eliminate special precautions related to typical benefits over urethane and epoxy solutions, including: safe-handling of organics Maximum protection – especially from silicone gels – against Cure schedule variation of silicones impose a significantly mechanical stress caused by thermal cycling or mismatched lower impact on end properties coefficient of thermal expansion Simpler processing without the need for oven drying or Extraordinary protection against shock and vibration concerns about exotherms Superior thermal stability for more reliable performance at Ease of repair when module rework is necessary sustained temperatures between -45°C and 200°C A wide selection range of special features, targeting multiple Greater hydro-stability and stronger resistance to chemicals functions like thermal management, improved processing and UV radiation efficiency and others What’s best for your application, an encapsulant or a gel? DOWSIL™ encapsulants and gels offer many of the same benefits, including excellent dielectric protection, strong seals against environmental contaminants, and excellent thermal stability and stress relief ranging from good to outstanding. Yet each material class offers distinguishing advantages. Encapsulants Gels Greater resistance to abrasion Maximum stress relief and damage Easily repairable for rework Self healing Unique options for: Unique options for: – Self-priming adhesion – Solvent and fuel resistance – Optical and space grade – Rapid UV cure – Thermal management Easy processing Most encapsulants and gels in our portfolio are two-part Dow Performance Silicones’ portfolio of encapsulants and gels addition cure silicones that, as a class of materials, offer several offers a wide variety of viscosities before cure, allowing either processing advantages over organic materials. Silicones can help shorter cycle times or longer, more controlled flow according to to reduce or eliminate special handling precautions required for your needs. Our broad selection also offers flexible options for organics related to their toxicity. Unlike urethanes, they do not simple, room-temperature cure or accelerated heat curing for require the costly use of ovens to thoroughly dry components enhanced productivity. before processing. Unlike epoxies, silicones impose no concerns about exotherms. 3 Choosing an encapsulant Encapsulants from Dow Performance Silicones generally fall proven solutions for any application. Our specialty grades offer into three categories: standard, primerless self-adhering, and unique properties and benefits, such as thermal conductivity, specialty grades. Standard encapsulants require a priming step high transparency, or compliance with military specifications. if strong adhesion is needed for extra protection. In contrast, This product selection tree will help you quickly narrow your self-priming encapsulants adhere to many common surfaces search for an optimal encapsulant for your application. Further when heated to temperatures above 100°C during the cure details and properties of each product can be found in the process. With hardness ranging from Shore 00 20 to Shore A 65, product table starting on page 6. encapsulants from either category offer a versatile selection of DOWSIL™ 3-8264 Encapsulant Medium hardness (Shore A 20~50) DOWSIL™ 3-8264 DOWSIL™ SE 1816Encapsulant CV Encapsulant High flow Medium hardness Heat cure SYLGARD™ DOWSIL™ SE567 Primerless 1816 Silicone Encapsulant CV Encapsulant (Shore A 50) DOWSIL™ CN-8760 Thermally Conductive Encapsulant DOWSIL™ EE-1840 Encapsulant Medium hardness SYLGARD™ 170 Silicone Elastomer (Shore A 20~50) DOWSIL™ EE-1840 Encapsulant Medium hardness SYLGARD™ 170 SYLGARD™ 170 Silicone Fast Cure Silicone Elastomer Elastomer High flow (Shore A 20~50) Standard (Shore A 50) Medium hardness DOWSIL™ CN-8760 G Thermally Conductive Encapsulant (Shore A 20~50) Medium hardness SYLGARD™ DOWSIL™ 184 Silicone CN-8760 Elastomer G Thermally (Clear) Encapsulant Conductive Room-temperature / Controlled flow (Shore A 20~50) SYLGARD™ 184 Silicone Elastomer (Clear) heat-accelerated cure (3,000-10,000 cps) Room-temperature / Controlled flow SYLGARD™ 160 Silicone Elastomer heat-accelerated cure (3,000-10,000 cps) High hardness SYLGARD™ 160 SYLGARD™ 164 Silicone Silicone Elastomer Elastomer (>Shore A 50) High hardness SYLGARD™ 164 182 Silicone Silicone Elastomer Elastomer (Clear) SYLGARD™ (>Shore A 50) SYLGARD™ 182 Silicone Elastomer (Clear) Limited flow Medium hardness DOWSIL™ 3-6121 Low Temperature Elastomer (>10,000 cps) (Shore A 20~50) Limited flow Medium hardness SYLGARD™ DOWSIL™ 186 Silicone 3-6121 Elastomer Elastomer Low Temperature (>10,000 cps) (Shore A 20~50) SYLGARD™ 186 Silicone Elastomer Medium hardness (Shore A 20~50) DOWSIL™ 93-500 Space Grade Encapsulant Medium hardness Space grade (Shore A 20~50) DOWSIL™ 93-500 Space Grade Encapsulant Space grade High hardness DOWSIL™ 93-500 Thixotropic Encapsulant (>Shore A 50) High hardness DOWSIL™ 93-500 Thixotropic Encapsulant (>Shore A 50) Room-temperature / High hardness Specialized heat-accelerated cure Optical grade (>Shore A 50) DOWSIL™ EI-1184 Optical Encapsulant Room-temperature / High hardness Specialized heat-accelerated cure Optical grade (>Shore A 50) DOWSIL™ EI-1184 Optical Encapsulant Shore 00 20 DOWSIL™ EE-3200 Low Stress Silicone Encapsulant Soft Shore 00 20 DOWSIL™ EE-3200 Low Stress Silicone Encapsulant Soft Shore 00 40 DOWSIL™ 3-6512 Elastomer Shore 00 40 DOWSIL™ 3-6512 Elastomer PRIMERLESS PRIMERLESS 4 Encapsulants and gels selection guide Encapsulants viscosity/hardness Viscosity/cure profile 70 8 7 11 10 60 45 14 13 7 6 13 12 17 16 50 16 15 Shore points 15 14 6 5 3 2 18 17 4 3 40 2 20 19 12 11 1 30 19 18 20 89 10 9 10 1,000 2,000 3,000 4,000 5,000 6,000 7,000 8,000 9,000 10,000 20,000 60,000 Viscosity, mPa.S 1 DOWSIL™ 3-6121 Low Temperature Elastomer 8 DOWSIL™ EE-1840 Encapsulant 15 SYLGARD™ 170 Silicone Elastomer 2 DOWSIL™ 3-8264 Encapsulant 9 DOWSIL™ EE-3200 Low Stress Silicone Encapsulant 16 SYLGARD™ 182 Silicone Elastomer 3 DOWSIL™ 93-500 Space Grade Encapsulant 10 DOWSIL™ EI-1184 Optical Encapsulant 17 SYLGARD™ 184 Silicone Elastomer 4 DOWSIL™ 93-500 Thixotropic Encapsulant 11 DOWSIL™ SE 1816 CV Encapsulant 18 SYLGARD™ 186 Silicone Elastomer 5 DOWSIL™ CN-8760 G Thermally Conductive Encapsulant 12 SYLGARD™ 160 Silicone Elastomer 19 SYLGARD™ 567 Primerless Silicone Encapsulant 6 DOWSIL™ CN-8760 Thermally Conductive Encapsulant 13 SYLGARD™ 164 Silicone Elastomer 20 7 DOWSIL™ EE-1010 Low Viscosity Encapsulant 14 SYLGARD™ 170 Fast Cure Silicone Elastomer Standard encapsulants Primerless encapsulants Specialty encapsulants Shore 00 5 Standard encapsulants Dieletric strength temperature cure Tensile strength Specific gravity Enlongation (%) Working time Viscosity Cure system Heat Agency Durometer Product name Features & benefits Color (mPa (Mixing ratio) cure listing* (Shore A) sec) (kV/mm) (Pot life) Room- (MPa) DOWSIL™ 3-6121 Remains a soft elastomer down to Addition cure; 20 min @ 100°C Low Temperature -65°C, with a higher refractive index Translucent 19,000 Two-part >2 hrs 48 hrs 1.12 35 4.3 275 18 — 10 min @ 150°C Elastomer compared to standard silicones (10:1) DOWSIL™ CN-8760 G Designed for fast fill rates and Addition cure; Thermally reworkability, with moderate Gray 3,200 1 hr 40 24 hrs 30 min @ 60°C 1.58 45 1.8 85 24 UL 94 V-0 Two-part (1:1) Conductive thermal conductivity Encapsulant DOWSIL™ CN-8760 Even higher flow version of Addition cure; Thermally Dark gray 2,700 1 hr 30 — 40 min @ 50°C 1.6 55 2.7 80 33 UL 94 V-0 DOWSIL™ CN-8760 G Encapsulant Two-part (1:1) Conductive Encapsulant Capable of improved throughput DOWSIL™ EE- speeds with one of our highest flow 1010 Addition cure; 3 min @ 100°C rates to rapidly fill around complex Gray 850 50 min 24 hrs 1.26 65 3.1 40 18 — Low Viscosity Two-part (1:1) 2 min @ 150°C board architectures and a fast Encapsulant heat cure Proven reliability with a higher SYLGARD™ 160 Dark gray Addition cure; Standard encapsulants thermal conductivity and heat 4,500 20 min 24 hrs 4 min @ 100°C 1.61 55 4.2 100 19 UL 94 V-0 Silicone Elastomer to black Two-part (1:1) stability SYLGARD™ 164 Fast, room-temperature cure version Addition cure; Gray 9,100 — 35 min Heat accelerable 1.57 60 — — 19 UL 94 V-0 Silicone Elastomer of SYLGARD™ 160 Elastomer Two-part (1:1) UL 94 V-0 Mil Spec: 45 min @ 50°C MIL-PRF- SYLGARD™ 170 An industry standard, with moderate Dark gray Addition cure; 25 min @ 70°C 2,100 15 min 24 hrs 1.37 50 2.8 150 19 23586F Silicone Elastomer thermal conductivity to black Two-part (1:1) 15 min @ 85°C EN 10 min @ 100°C 45545-2 HL3 SYLGARD™ 170 Much faster curing version of Addition cure; Fast Cure Silicone Black 2,300 24 hrs NA 1 hr @ 100°C 1.35 35 2.9 225 26 UL 94 V-0 CV Encapsulant flexibility with UL recognition Two-part (1:1) Part A: 3 hrs @ 70°C UL 94 V-0 SYLGARD™ 567 One of our fastest fill rates with 2,100 Addition cure; 2 hrs @ 100°C Mil Spec: Primerless Silicone enhanced high-temperature Black >3 days NA 1.24 40 — — 21 Part B: Two-part (1:1) 85 min @ 115°C MIL-PRF- Encapsulant stability 550 15 min @ 150°C 23586F Highly transparent with very low DOWSIL™ 93-500 Addition cure; levels of volatile condensable 2 hrs 10 min @ 100°C Space Grade Clear 8,100 Two-part 24 hrs 1.03 45 6.7 125 19 — materials – proven for space- 45 4 min @ 150°C Encapsulant (10:1) grade applications Specialty encapsulants DOWSIL™ 93-500 Addition cure; 15 min @ 100°C Non-flow version of DOWSIL™ Translucent Non-flow/ Thixotropic Two-part 50 min 24 hrs 10 min @ 125°C 1.08 60 8.5 125 18 — 93-500 Space Grade Encapsulant white thixotropic Encapsulant (10:1) 5 min @ 150°C One of our most stress relieving DOWSIL™ EE-3200 encapsulants with fast processing, 20 UL 94 V-0 Addition cure; 2 hrs Low Stress Silicone moderate thermal conductivity Dark gray 1,700 30 min 20 min @ 50°C 1.48 Shore 0.2 350 14 EN 45545-2 Two-part (1:1) 45 Encapsulant and proven reliability in outdoor 00 HL3 applications Highly transparent with reduced DOWSIL™ EI-1184 yellowing for optical application Addition cure; UL 94 V-1 Clear 4,600 10 min 4 hrs 15 min @ 100°C 1.04 65 8.3 75 18 Optical Encapsulant reliability – in a convenient 1:1 Two-part (1:1) UL 746C f1 mix ratio *Visit UL.com for specific details 7 Encapsulants and gels selection guide Choosing a gel Offering the ultimate in stress relief, most gels also exhibit This product selection tree will help you quickly narrow your a tacky surface that adheres naturally to common surfaces, search for an optimal gel for your application. Further details without the need for primers. Dow Performance Silicones’ broad and properties of each product can be found in the product selection of gels are organized into four families: standard, low- table starting on page 10. temperature, toughened, and specialty. Product specification is typically determined by the application’s need for stress relief, viscosity, or cure time versus working time. 1- part SYLGARD™ 535 Thixotropic Dielectric Gel Low DOWSIL™ 3-4154 Dielectric Gel Heat cure viscosity DOWSIL™ 3-4170 Dielectric Gel SYLGARD™ 527 Silicone Dielectric Gel 2- part Extreme Hardness High DOWSIL™ 3-4118 Gel stress relief viscosity 300 grams~ Shore 00 Room- DOWSIL™ 3-4207 Dielectric Tough Gel temperature 2- part cure DOWSIL™ 3-4222 Dielectric Firm Gel DOWSIL™ 3-6635 Dielectric Gel 1- part DOWSIL™ EG-3810 Gel Heat cure High/low temperature 2- part DOWSIL™ Q3-6575 Dielectric Gel application Room- temperature DOWSIL™ 3-4155 HV Dielectric Gel cure 1- part FLUOROGEL™ 4-8022 Gel Solvent and Heat cure Specialized fuel resistant 2- part FLUOROGEL™ Q3-6679 Dielectric Gel UV curable Standard 1- part DOWSIL™ X3-6211 Encapsulant THIXOTROPIC PRIMERLESS 8 Gels viscosity/hardness 600 2 500 300 23 275 250 225 14 200 21 18 175 Hardness (gram) 150 125 19 3 20 16 100 4 90 10 22 80 6 11 13 12 70 9 15 60 7 5 50 17 1 40 8 30 20 10 300 400 500 600 700 800 900 1,000 2,000 3,000 7,000 Viscosity, mPa.S 1 DOWSIL™ 3-4118 Gel 9 DOWSIL™ 3-4241 Dielectric Tough Gel 17 FLUOROGEL™ 4-8022 Gel 2 DOWSIL™ 3-4133 Dielectric Gel 10 DOWSIL™ 3-4680 Silicone Gel 18 FLUOROGEL™ Q3-6679 Dielectric Gel 3 DOWSIL™ 3-4150 Dielectric Gel 11 DOWSIL™ 3-6635 Dielectric Gel 19 SYLGARD™ 3-6636 Silicone Dielectric Gel 4 DOWSIL™ 3-4154 Dielectric Gel 12 DOWSIL™ EG-3000 Thixotropic Gel 20 SYLGARD™ 527 Silicone Dielectric Gel 5 DOWSIL™ 3-4155 HV Dielectric Gel 13 DOWSIL™ EG-3810 Gel 21 SYLGARD™ 528 Firm Gel 6 DOWSIL™ 3-4170 Dielectric Gel 14 DOWSIL™ EG-3896 Gel 22 SYLGARD™ 535 Thixotropic Dielectric Gel 7 DOWSIL™ 3-4207 Dielectric Tough Gel 15 DOWSIL™ Q3-6575 Dielectric Gel 23 SYLGARD™ 537 Silicone Gel 8 DOWSIL™ 3-4222 Dielectric Firm Gel 16 DOWSIL™ X3-6211 Encapsulant Standard gels High/low temperature gels Tough gels Specialty gels Shore 00 9 Standard and high/low temperature gels Working time Hardness strength (kV/mm) Specific gravity Agency listing* Room- Cure system Heat hardness (g) Penetration Product name Features & benefits Color Gel temperature (Mixing ratio) cure Dielectric (1/10 mm) (mPa sec) Pot Viscosity time cure life (min) Gel DOWSIL™ 3-4118 Addition cure; Controlled flowability Clear 7,000 30 min — Possible 1 hr @ 125°C 0.97 50 110 18 — Gel Two-part (1:1) 4 min @ 100°C DOWSIL™ 3-4133 Long working time with fast Addition cure; Clear 450 6 hrs — Possible 2.2 min @ 125°C 0.97 600 10 19 — Dielectric Gel heat cure Two-part (1:1) 1.6 min @ 150°C Blue + yellow that turns to green DOWSIL™ 3-4150 Transparent Addition cure; when mixed, fast cure version of 470 6 min 30 90 min — 0.97 110 50 15 — Dielectric Gel green Two-part (1:1) SYLGARD™ 527 Dielectric Gel Longer processing time DOWSIL™ 3-4154 Addition cure; 3 hrs @ 80°C version of DOWSIL™ 3-4150 Clear 550 30 min — NA 0.97 100 50 18 — Dielectric Gel Two-part (1:1) 1.75 hrs @ 100°C Dielectric Gel 9 min @ 100°C DOWSIL™ 3-4170 Fast heat cure with UL Addition cure; >24 UL 94 Clear 460 — NA 5 min @ 125°C 0.97 80 65 20 Dielectric Gel recognition Two-part (1:1) hrs HB 3 min @ 150°C DOWSIL™ 3-4680 One of our highest flow rates Transparent Addition cure; Standard gels 260 — 10 30 min 1 min @ 125°C 0.97 90 60 16 — Silicone Gel for fast filling and processing blue Two-part (1:1) DOWSIL™ Thixotropic to allow selective Slightly Addition cure; EG-3000 2,300 6 hrs 8 NA 1 hr @ 150°C 0.99 80 60 22 — and cost-effective protection hazy/clear Two-part (1:1) Thixotropic Gel SYLGARD™ 3-6636 Addition cure; 1 wk 1.25 hrs @ 125°C 0.95 115 — 17 Two-part (1:1) HB Gel processing flexibility 35 min @ 150°C SYLGARD™ 528 Intermediate modulus with a Addition cure; Clear 400 6 hrs — Possible Possible 0.97 200 — — — Firm Gel long working time Two-part (1:1) SYLGARD™ 535 One-part version of DOWSIL™ Addition cure; Thixotropic Translucent 3,000 — — — 1 hr @ 150°C 0.97 85 60 11 — EG-3000 Thixotropic Gel One-part Dielectric Gel SYLGARD™ 537 One-part, harder version of Addition cure; Clear 360 — — — 1 hr @ 120°C 0.98 290 20 22 — Dielectric Gel SYLGARD™ 528 Firm Gel One-part Proven automotive grade with DOWSIL™ 3-4155 blue + yellow that turns to green Transparent Addition cure; 1,850 — 8 60 min — 1 60 90 16 — High/low temperature gels HV Dielectric Gel when mixed, and designed for green Two-part (1:1) use down to -80°C DOWSIL™ 3-6635 Fast filling automotive grade, Addition cure; UL 94 Clear 650 — 11 NA 2 hrs @ 100°C 1 80 85 20 Dielectric Gel designed for use down to -80°C One-part HB DOWSIL™ Enhanced use temperature Addition cure; 15 min @ 125°C 0.97 Clear 690 — — NA 80 80 21 — EG-3810 Gel range from -60 to + 200°C One-part 10 min @ 150°C Uncured DOWSIL™ Extended shelf life, two-part Addition cure; 40 min @ 70°C Q3-6575 version of DOWSIL™ 3-6635 Clear 670 20 min 6 24 hrs 1.02 65 80 10 — Two-part (1:1) 20 min @ 100°C Dielectric Gel Dielectric Gel *Visit UL.com for specific details 10 Encapsulants and gels selection guide Tough and specialty gels Working time Hardness strength (kV/mm) Specific gravity Agency listing* Room- Cure system Heat hardness (g) Penetration Product name Features & benefits Color Gel temperature (Mixing ratio) cure Dielectric (1/10 mm) (mPa sec) Pot Viscosity time cure life (min) Gel Designed as a toughened gel for additional strength, with blue + DOWSIL™ 3-4207 10 min @ 50°C 60 yellow that turns to green when Translucent Addition cure; UL 94 Dielectric Tough 410 — 7 90 min 3 min @ 100°C 0.98 Shore NA 17 mixed, conditional primerless green Two-part (1:1) V-1 f2 Gel 3 min @ 150°C 00 adhesion at room temperature, and a UV indicator Enhanced stress relief version 35 Tough gels DOWSIL™ 3-4222 Translucent Addition cure; 2 min @ 100°C of DOWSIL™ 3-4207 Dielectric 340 3 min 13 30 min 0.97 Shore NA 14 — Dielectric Firm Gel green Two-part (1:1) 1 min @ 125°C Tough Gel 00 DOWSIL™ 3-4241 Enhanced working life version 60 Translucent Addition cure; UL 94 Dielectric Tough of DOWSIL™ 3-4207 Dielectric 410 >1h — 11 hrs 2 min @ 125°C 0.98 Shore NA 17 green Two-part (1:1) V-1 Gel Tough Gel 00 Designed as a toughened gel 30 min @ 70°C DOWSIL™ for improved crack resistance at Slightly Addition cure; UL 94 520 >4 hrs — — 10 min @ 100°C 0.98 220 30 22 EG-3896 Gel operating temperatures as high hazy/clear Two-part (1:1) V-1 5 min @ 150°C as 185°C 5 sec @>3000 DOWSIL™ X3- Extremely fast line-of-sight UV cure; Clear 850 — — mJ/cm2 NA 0.99 105 50 17 — 6211 Encapsulant UV cure One-part (12 mm thick) Specialty gels Automotive grade with solvent FLUOROGEL™ Addition cure; 1 hr @ 125°C and fuels resistance, in a one- Translucent 600 30 days — NA 1.23 50 105 — — 4-8022 Gel One-part 30 min @ 150°C part formulation FLUOROGEL™ Two-part, enhanced processing, Addition cure; Q3-6679 flexibility version of Clear 1,100 >4 hrs 7 >1 week 2 hrs @ 100°C 1.26 180 30 — — Two-part (1:1) Dielectric Gel FLUOROGEL™ 4-8022 Gel **Visit UL.com for specific details. 11 Learn more We bring more than just an industry-leading portfolio of advanced silicone-based materials. As your dedicated innovation leader, we bring proven process and application expertise, a network of technical experts, a reliable global supply base, and world-class customer service. To find out how we can support your applications, visit consumer.dow.com/pcb. Images: Page 1 - dow_40963479529, GettyImages-956923940; Page 2 - dow_41027725967; Page 3 - dow_40370590708; Page 7 - GettyImages-96361318; Page 11 - GettyImages-748325537 NOTICE: No freedom from infringement of any patent owned by Dow or others is to be inferred. Because use conditions and applicable laws may differ from one location to another and may change with time, Customer is responsible for determining whether products and the information in this document are appropriate for Customer’s use and for ensuring that Customer’s workplace and disposal practices are in compliance with applicable laws and other government enactments. The product shown in this literature may not be available for sale and/or available in all geographies where Dow is represented. The claims made may not have been approved for use in all countries. Dow assumes no obligation or liability for the information in this document. References to “Dow” or the “Company” mean the Dow legal entity selling the products to Customer unless otherwise expressly noted. NO WARRANTIES ARE GIVEN; ALL IMPLIED WARRANTIES OF MERCHANTABILITY OR FITNESS FOR A PARTICULAR PURPOSE ARE EXPRESSLY EXCLUDED. ® ™ Trademark of The Dow Chemical Company (“Dow”) or an affiliated company of Dow © 2022 The Dow Chemical Company. All rights reserved. 2000020944 Form No. 11-3922-01-0822 S2D