Pharmaceutical Manufacturing PDF
Document Details
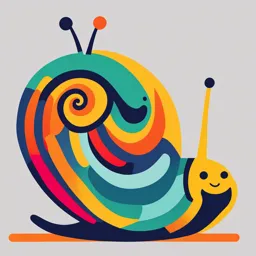
Uploaded by NavigableFallingAction
Our Lady of Fatima University
Tags
Related
- Solid Dosage Forms PDF
- Oral Liquid Dosage Form (Emulsion) PDF
- Sesión de Aprendizaje 06 - Buenas Prácticas de Elaboración, rotulado y Envasado de Fármacos y Productos Orales PDF
- Solid Oral Dosage Form I PDF
- Oral Solid Dosage Forms PDF
- Quality Control in Pharmaceutical Manufacturing: Solid Dosage Forms PDF
Summary
This document outlines pharmaceutical manufacturing, focusing on oral dosage forms, liquids, and solutions. It discusses various container types (glass, plastic, metal), their properties, and selection factors. The document also touches upon stability issues and formulation considerations.
Full Transcript
PHARMACEUTICAL MANUFACTURING (with Regulatory Pharmacy, Quality Assurance and cGMP) Unit Outcomes OUTLINE A...
PHARMACEUTICAL MANUFACTURING (with Regulatory Pharmacy, Quality Assurance and cGMP) Unit Outcomes OUTLINE Advantages and disadvantages Liquids At the end of discussion, student should be able to: Components of containers 1. Identify the different types of oral dosage forms. Types of containers (Glass, Plastic, Rubber, Metal) 2. Understand the different processes involved in the Factors in choosing containers manufacture of oral dosage forms: Liquids and Solutions. 3. Apply different methods of production of oral dosage forms: Special techniques for poorly soluble drugs Liquids and Solutions. Formulation of liquids 4. Generate new designs for drug formulations. Manufacturing considerations in liquids 5. Manipulate machines and equipment used for production of oral dosage forms: Liquids and Solutions. WEEK 7: COMMERCIAL MANUFACTURING (ORAL DOSAGE FORMS) Instability as a technical problem may be Advantages Disadvantages caused by the following conditions : Ease of administration Technical problems (instability) 1. pH Immediate availability for absorption Special techniques required for 2. Temperature – It is more rapidly and efficiently poorly soluble drugs. 3. Concentration of the Reactants absorbed, compared to tablets or Requires pharmaceutical elegance 4. Light or Radiation capsules. with regards to taste, appearance 5. Packaging Components and viscosity. Factors that affect Light/Radiation: Container Components Glass Containers a. intensity of the wavelength of light Glass it has been the container of b. size of the container Plastic choice, because of the following c. shape of the container Metal reasons: ⮚Flint/ Colorless glass container 1. Resistance to decomposition by – light transmission above 300 nm. Rubber atmospheric conditions ⮚Amber/ Light resistant glass container – light transmission above 470 nm 2. Resistance to decomposition by solid or liquid contents of varying composition. Glass has two (2) principal faults or Glass Containers And, these can be accomplished by: undesirable properties: it has been the container of 1. decreasing the soda content in 1. Release alkali to liquids stored in choice, because of the following the glass the glass container. reasons: 2. replacing Sodium oxide with 2. Releases insoluble flakes 3. By modifying the chemical other oxides to overcome the composition of glass, it may be possible to adjust the: undesirable property of glass. ⮚ chemical behavior of the glass ⮚ radiation properties of the glass Classification of glass used in packaging pharmaceuticals depend upon: Types of Glass containers Types of Glass containers 1. chemical constituents Type I Type II 2. ability to resist deterioration – generally suitable for all parenterals – treated with sulfur dioxide; suitable for – Constituent: SiO2 + B2O3 parenterals solutions, which is buffered; – Description: Highly Resistant has a pH below 7; not reactive with the Borosilicate Glass glass – Constituent: Na2O + CaO silicon dioxide – SO2 Treatment boron trioxide – Description: Treated Soda Lime Glass Types of Glass containers Types of Glass containers Test for Glass Containers Type III Type IV Powdered Glass Test – suitable for anhydrous parenterals – not for parenterals use; suitable only for – Performed on ground or powdered glass liquids or dry substances tablets, capsules, suspensions, to expose internal surface – Constituent: Na2O + CaO ointments and extractives. – Tests the leaching potential of the glass – Description: Soda lime Glass for Dry – Constituent: Na2O + CaO – Alkali treated with 0.02 N sulfuric acid Products – Description: General Purpose Soda lime (acidimetry) Glass Test for Glass Containers Plastic Containers Plastic Containers Water Attack Test These are high molecular weight These are high molecular weight – Exposure of the glass with sulfur dioxide polymers, such as: polymers, such as: at 121°C –Polyethylene –Polystyrene – Specifically performed with TYPE II Cannot be autoclaved –Polypropylene GLASS. Low density = droppers and sprays autoclavable High density = solid oral preparations Plastic Containers Plastic Containers Metal Containers These are high molecular weight These are high molecular weight Disperse systems having a polymers, such as: polymers, such as: consistency of a soft paste, gel, cream, or ointment can be –Polyvinyl chloride –Polyethylene terephthalate conveniently packed into “collapsible Rigid and has good clarity For beverages tubes”, which are commonly made of: Used for blister packaging Have transparency and luster a. Tin b. plastic coated tin CARCINOGENIC Gamma radiation sterilization c. tin coated lead d. Aluminum e. plastic coated aluminum Problems encountered in the use Metal Containers Rubber Containers of rubber closures: Rubber of varying composition is designed to release pressurized Absorption of the active used in pharmaceuticals and contents ingredient, preservative or other biologicals as: it may contain toxic metals component or leaching ⮚stoppers “container may explode if heated” The extraction of one or more ⮚cap liners ⮚parts of dropper assemblies components of the rubber closure ⮚components of drip sets/ infusion sets into the solution. These problems may be corrected by: Factors In Choosing Containers Factors In Choosing Containers ⮚using epoxy clinging material 1. Advantage of plastic over glass 3. The interest and convenience in (a resin that glues) containers utilizing low and medium density a. lightness of weight polyethylene in the formation of ⮚use of teflon in rubber stoppers b. resistance to impact squeeze bottles (dual function) (tetrafluoroethylene polymer or c. lower transportation costs plastic). 4. The advent of newer techniques in d. lower losses due to less container damages drug distribution, dispensing and inventory control. 2. The versatility in container dosage and consumer acceptance afforded by plastics. Variety of dosage forms maybe found The disadvantages of plastic packaging The disadvantages of plastic packaging packaged in plastic containers, such as Collapsible polyethylene bags 1. Permeability of the container to 3. Sorption (ab or ad) of the drugs atmospheric gases and to moisture. from the contents to the plastic Collapsible plastic tubes 2. Leaching of the constituents; container. Plastic film Compounds leached from the plastic 4. Transmission of light through the Plastic vials containers are generally polymer container. additives, such as: plasticizers, 5. Container deformation. Compact type container stabilizers, antioxidants II. Special techniques required for poorly soluble drugs Formulation of Liquids 1) Solubility Co-solvency To avoid problems on formulation of Co-solvents may be used in the liquids, the following considerations should formulation of aqueous liquid, pH control be studied: Solubilization 1. Solubility such as alcohol, sorbitol, glycerin, propylene glycol Complexation 2. Stability 3. Organoleptic characteristics Hydrotrophy 4. Preservatives Chemical Modification of the drug 5. Sweetening agents 6. Viscosity 2) Stability 2) Stability 3) Organoleptic charateristics Physical stability is shown by the Chemical stability is also Taste (flavoring) maintenance of the physical considered in the formulation The process of choosing flavoring properties such as the color, because the instability is agents may be divided into two major categories, such as: clarity, taste, viscosity and odor magnified in solution as against throughout its shelf life or until the solid and suspension systems. 1. Selection expiry date is reached. 2. Evaluation Appearance depends on the color and clarity. 4) Preservatives Classification of Preservatives Classification of Preservatives Characteristics of an Ideal Acidic – examples are alkyl Neutral – examples are benzyl Preservative: esters of p-hydroxybenzoic acid alcohol, and phenylethyl alcohol. 1. broad spectrum (PABA), benzoic acid and its 2. physically, chemically and microbiologically stable until the salts. For external use – boric benzyl alcohol expiry date of the product acid and phenols are used. phenylethyl alcohol 3. Should be non-toxic, non- alkyl esters of p-hydroxybenzoic acid (PABA) sensitizing, adequately soluble and benzoic acid and its salts compatible, as well as acceptable to the taste and odor at the amounts used. Classification of Preservatives Classification of Preservatives 4) Preservatives Mercurials – examples are Quaternary Ammonium The most useful preservatives are the thimerosal, nitromersols, phenyl Compounds – examples are esters of p-hydroxybenzoic acids (PABA or parabens), because they mercuric acetate/ nitrate. benzalkonium chloride and cetyl are; pyridinium chloride. a. chemically stable thimerosal nitromersols benzalkonium chloride b. neutral in pH phenyl mercuric acetate/ nitrate cetyl pyridinium chloride c. non-toxic, non-irritating, non- allergenic d. possess both antifungal and antibacterial properties 5) Sweetening agents 5) Sweetening agents 5) Sweetening agents A. Sucrose – had a long history of A. Sucrose B. Liquid Glucose use due to the following advantages: Disadvantage: is an extremely sweet viscous ⮚can be obtained in highly purified ⮚“cap locking” (wherein the sucrose substance, which imparts both form Content crystallizers along the body (viscosity) and sweetness to ⮚chemically and physically stable at thread of the bottle cap which liquid formulations pH 4 to 8 interferes with the cap removal) ⮚can be used in conjunction with polyols to prevent crystallization of sucrose 5) Artificial sweetener 5) Artificial sweetener 6. Viscosity saccharin and cyclamates are Cyclamates – 15 to 30 x sweeter If high concentrations of commonly used. Some characteristics than sucrose carboxymethylcellulose (CMC) are as follows: are used, incorporation of AI+3, Saccharin – 250 to 500 x sweeter ⮚Sodium and Calcium salts of Fe+3, and Ca+2 are done. than sucrose saccharin are soluble in water, alcohol and polyols. Viscosity controlling agents are PVP, methylcellulose and sodium ⮚Stable at pH 3 to 8. CMC ⮚Produce the desired sweetness at a much lower concentration than sucrose. Manufacturing Considerations in Liquids References The rate at which the equilibrium is Allen, L.V. & Ansel, H.C. (2014). Ansel’s Pharmaceutical Dosage Forms and Drug Delivery achieved, is highly dependent in the Systems 10th Ed. Lippincott Williams and Wilkins: details of the following: Baltimore, USA Remington’s Pharmaceutical Sciences Latest Edition 1) equipment 2) compounding procedure Any questions? 3) packaging methods 4) labeling 5) storage Unit Outcomes OUTLINE At the end of discussion, student should be able to: Dispersed systems Identify the different types of oral dosage forms. Pharmaceutical application of colloids Understand the different processes involved in the manufacture of oral dosage forms: Liquids and Solutions. Importance of synthetic polymers in Colloids Apply different methods of production of oral dosage pharmaceutical practice forms: Liquids and Solutions. Types of colloidal systems PMQA311 WEEK 7: COMMERCIAL Generate new designs for drug formulations. Optical properties of colloids MANUFACTURING (ORAL DOSAGE FORMS) Manipulate machines and equipment used for production of oral dosage forms: Liquids and Solutions. Colloidal stability Colloids ∙ Defined as the intermediate A colloid, also called a colloidal For example, homogenized between solutions and dispersion, is a two-phase milk is a colloid made up of precipitates. heterogeneous mixture made up tiny particles of liquid ∙ They are larger than the of a dispersed phase of tiny butterfat (the dispersed molecules and ions that make up particles that are distributed phase) suspended in water the solutions. evenly within a continuous phase. (the continuous phase) Speckle image recorded at 2.5 cm Dispersed systems from the sample (colloidal dispersion of silica particles, diameter 500 nm). Dispersed particles Three size classification (dispersed phase) Dispersing medium – Molecular dispersion (dispersing phase) – Colloidal dispersion – Coarse dispersion Size and Shape of Ultrafiltration ∙ Through the semi permeable Colloidal Particles membrane of collodion or ∙ Because of their size, cellophane, the small Used to separate and purify colloidal particles may be molecules and ions of urea, colloidal material; this can be separated from molecule and glucose and NaCl can pass conducted under negative ion particles by dialysis. through the pore size that pressure (suction) through a prevents the passage of dialysis membrane supported colloidal particles. in a Buchner Funnel. Electrodialysis Pharmaceutical Application of Colloids Colloidal silver chloride, silver A purification process by which it is done by the removal of Certain medicinal have been iodide and silver protein are charged impurities such as ionic found to possess unusual or effective germicides and do contaminants in dialysis or not cause the irritation that ultrafiltration through the use of increased therapeutic properties when formulated is characteristic of ionic an electronic potential across the silver salts. membrane. in the colloidal state. Importance of synthetic Coarsely powdered sulfur is polymers in pharmaceutical poorly absorbed when practice administered orally, yet the Colloidal copper has been Proteins are important same dose of colloidal sulfur used in the treatment of natural colloids and are found may be absorbed may be cancer, colloidal gold as a in the body as components of absorbed so completely as to diagnostic agent for paresis muscle, bone and skin. cause toxic reaction and even and colloidal mercury for death. syphilis. macromolecules (as adjunct): The plasma proteins are Starch Hydroxyethyl starch (HES): a responsible for binding Cellulose macromolecule used as a certain drug molecules to plasma substitute. such an extent that the Dextran: Plasma expander. pharmacologic activity of the drug is affected. As coatings to solid dosage Colloidal electrolytes (Surface- ∙ Defined as the intermediate forms to protect drugs that active agents) are sometimes between solutions and are susceptible to used to increase the solubility, precipitates. atmospheric moisture or stability, and taste of certain ∙ They are larger than the degradation under the acid compounds in aqueous and oily molecules and ions that make up pharmaceutical preparations. the solutions. conditions of the stomach. 1. Lyophilic Colloids System This is based on the interaction of Colloidal particles that the particles, molecules or ions of TYPES OF COLLOIDAL interact to an appreciable the dispersed phase with the extent with the dispersion SYSTEM molecules of the dispersion medium. medium referred to as lyophilic (solvent-loving) colloids. Example 2. Lyophobic Colloids ∙ Acacia or gelatin in water or Most lyophilic colloids are This second class of colloids celluloid in amyl acetate leads organic molecules of gelatin, is composed of materials that to the formation of a sol. acacia, insulin, albumin, have little attraction, if any, rubber, and polystyrene. for the dispersion medium. 3. Association Colloids: When present in a liquid medium at low concentrations, Lyophobic colloids are Includes Micelles and the CMC the amphiphiles exist Association, or amphiphile, colloids generally composed of separately and are of such a Amphiphiles or surface-active agents inorganic particles dispersed are characterized by having two size as to be subcolloidal. in water namely: gold, silver, distinct regions of opposing solution sulfur, arsenous sulfide and affinities within the same molecule or silver iodide. ion. CMC and As the concentration is increased, Aggregate number aggregation occurs over a narrow Since the diameter of each The concentration of monomer at concentration range. micelle is of the order of 50 which micelles form is term the These aggregates, which may °A, micelles lie within the size critical micelle concentration, or contain 50 or more monomers, are cmc. The number of monomers range we have designated as called micelles. that aggregate to form a micelle colloidal. is known as the aggregation number of the micelle 1 OPTICAL PROPERTIES OF COLLOIDS A solution, on the other hand, will appear clear even when a light is shown through it. The particles in a colloidal dispersion remain dispersed in the liquid and will not settle out Tyndall Effect in a beaker of water to which a few drops of milk had been added The bright green line that crosses the beaker is the actual laser beam, reflected by the colloidal dispersion. The green laser pointer is bright enough that the scattered light Colloidal Stability illuminates the rest of the contents of the beaker as well. The term “stability” can have This will depend upon the balance different connotations to different of the repulsive and attractive applications. When applied to colloids, a stable forces that exist between colloidal system is one in which the particles as they approach one particles resist flocculation or another. aggregation and exhibits a long shelf- life. If all the particles have a mutual repulsion then the dispersion will remain stable. In certain circumstances, the An initially formed aggregate is called a particles in a colloidal disperson may floc and the process of its formation However, if the particles adhere to one another and form flocculation. have little or no repulsive aggregates of successively increasing The floc may or may not separate out. If the aggregate changes to a much force then some instability size that may settle out under the denser form, it is said to undergo mechanism will eventually influence of gravity. coagulation. take place e.g. flocculation, An aggregate usually separates out either by sedimentation (if it is more dense than aggregation etc. the medium) or by creaming (if it less dense than the medium). The term’s flocculation and coagulation have often been used interchangeably. Usually coagulation is irreversible whereas flocculation can be reversed by the process of deflocculation. PHARMACEUTICAL MANUFACTURING (with Regulatory Pharmacy, Quality Assurance and cGMP) Unit Outcomes Reference: At the end of discussion, student should be able to: Allen, L.V. & Ansel, H.C. (2014). Ansel’s Pharmaceutical Dosage Forms and Drug Delivery Systems 10th Ed. Lippincott Williams and Wilkins: Baltimore, USA Suspensions 1. Identify the different types of oral dosage forms. 2. Understand the different processes involved in the manufacture of oral dosage forms: Suspension 3. Apply different methods of production of oral dosage forms: Suspension Remington’s Pharmaceutical Sciences 4. Generate new designs for drug formulations. 5. Manipulate machines and equipment used for production Latest Edition of oral dosage forms: Suspension WEEK 8: COMMERCIAL MANUFACTURING (ORAL DOSAGE FORMS) OUTLINE Suspensions Suspensions ❖ Purposes of suspensions It is a disperse system in which solid, These liquids are heterogeneous ❖ Properties of a good suspension ❖ Problems encountered when formulating insoluble vehicle-insoluble particles (internal systems consisting of two phases: solid to suspension phase) are uniformly suspended by The continuous phase – also called ❖ Types of suspension system ❖ Methods of preparation of suspensions mechanical agitation and formulation the external phase or dispersion ❖ Factors in suspension formulation design throughout the liquid vehicle system. Suspending agents ❖ ❖ Formulation adjuvant (external phase). The discontinuous phase – also ❖ Equipment used called the internal phase or dispersed phase Purposes of Suspension Purposes of Suspension Purposes of Suspension 1)Sustaining effect 2) Stability 3) Taste – For a sustained release – Drug degradation in suspension or – A drug with unpleasant taste can preparation, a suspension solid dosage forms occurs much be converted into an insoluble form necessitates drug dissolution prior more slowly than degradation in and then prepared as suspension to absorption solution form In general, three steps in ensuring Purposes of Suspension Properties of a good suspension formulation of suspension: 4) Basic solubility Ready dispersion of any sediment Control particle size produced on storage – When suitable solvents are not Use of thickeners available. After gentle shaking, the medicament stays in suspension long enough for a Use of wetting agent – For example, ophthalmic dose to be accurately measured suspensions provide an alternative Pourable to ophthalmic solutions Particles are small and relatively uniform in size Problems encountered when formulating Insoluble medicament Indiffusible solids insoluble solid to suspension Diffusible solids (dispersible Not easily wetted Sedimentation solids) Examples: – The greater the density, the greater Example: light kaolin, magnesium ▪ Internal use - aspirin, chalk, the descent phenobarbitone, sulphadimine, trisilicate, light magnesium carbonate, bismuth carbonate ▪ External use – calamine, hydrocortisone, sulphur, and zinc oxide Flocculation Wetting Preservatives used Aggregation will determine the To prevent air trapping Chloroform water, benzoic acid, type of suspension hydroxybenzoates Type of Suspension system Flocculated System Flocculated System A. FLOCCULATED SYSTEM ⮚ Particles appear as floccules like ⮚ Appears to be coarse, because of B. DEFLOCCULATED SYSTEM tufts of wool with loose fibrous the floccules formed. structure ⮚ Exhibits minimum serious separation, ⮚ When the system settles two distinct depending on the solid content and layers form a clear particle free the degree of flocculation that took supernatant liquid and a sediment. place. ⮚ Also known as Coagulated or Colloidally Unstable system. Deflocculated System System Differences in Terms of: Methods of Preparation of Suspensions ▪ Particles settles as a dense 1) PARTICLE SIZE (floccules, sediments) A. By discipitation method sediment, which becomes more 2) RATE OF SETTLING B. By precipitation method Compact after a given time interval. 3) DISTINCTION AND CLARITY OF LAYERS 1. Organic Solvent Precipitation ▪ Also known as Peptized or colloidally 4) VISCOSITY OF SUSPENSION 2. Precipitation effected by changing Stable system, which Frequently 5) POURABILITY the pH results to a pharmaceutically poor suspension. 3. By Double Decomposition Method I. By Discipitation Methods II. By Precipitation Methods This process is done by dispersing This is performed by effecting Examples of organic solvents used the finely divided powders in an precipitation in the liquid vehicle. are ethyl alcohol, methyl alcohol, appropriate liquid vehicle. The methods are: propylene glycol, acetone and The use of surfactants is desirable to A. Organic Solvent Precipitation polyethylene glycol. ensure uniform wetting of the – Water insoluble drugs are precipitated by dissolving them in a water miscible hydrophobic surfaces. organic solvent. Then adding the organic phase to purified water under standard conditions. B. Precipitation effected by C. By Double Decomposition changing the pH Method A number of important considerations This is applicable to those drugs in Where simple chemistry is involved. are involved if this method is used: which its solubility is dependent on pH Example is the preparation of White ⮚Particle size control value. Lotion USP (made by interacting ⮚Correct form of crystals obtained. zinc sulfate with sulfurated potash ⮚For suspensions intended for parenterals or inhalation use, the solution to form zinc polysulfide). particle size should be between 1 to 5 microns range Factors in Suspension Formulation Formulation 1) Type of Suspension desired I. Flocculated system ⮚ NON-IONIC SURFACTANTS a. assumes negative charge in solution 2) Formulation adjuvant Requirement: therefore acts as flocculating agent 3) Preparation techniques a.Dispersion in aqueous vehicle or ✔SLS and sodium dioctyl sulfoccinate Goal of formulator: other vehicles b. aid in dispersion of insoluble phase ✔TWEENS- Polyoxyethylene esters of mixed fatty ⮚Decrease the rate of settling b.Presence of surfactants acid esters of sorbitol anhydride ⮚Permit resuspendability – Negative charges prevents flocculation ✔SPANS- Mixed fatty acid esters of sorbitol in the presence of positive ions anhydride ✔Carbowax- Higher molecular weight polyethylene glycols Formulation Protective colloids II. Deflocculated system I. Flocculated system MAIN USE: form mechanical sheath or Requirement: barrier around particles Ideal dispersing agent act as a viscosity Requirement: Do not reduce interfacial tension imparting agent and also to lower c. intended for oral parenterals, Differ in viscosity, thus used in high interfacial tension concentration GENERAL CHOICE: ophthalmic or topical use may not EXAMPLES: appear elegant, due to poor ✔Protective colloids ✔Silica gel (10%) gelled with surfactants - for drainage from vials or bottles, due to topical suspensions ✔Surfactants clusters of flocculated particles. ✔Aluminum hydroxide – triple sulfonamide ✔viscosity builders suspension ✔dispersing agents - protective colloids can improve this Suspending Agents Suspending Agents Suspending Agents A. Hydrophilic colloids A. Hydrophilic colloids A. Hydrophilic colloids (hydrocolloids) (hydrocolloids) (hydrocolloids) – increase the viscosity of water by – Anionic hydrocolloids are – Natural polysaccharides (acacia incompatible with quarternary and tragacanth) binding water molecules, limiting antibacterial agents and other – Acacia is usually 35% dispersion in their mobility or fluidity positively charged ions water (mucilage). Its viscosity is – mostly anionic, except – Chitosan is incompatible with greatest between pH 5 and 9. methylcellulose (neutral) and negatively charged drugs and – Acacia is susceptible to microbial chitosan (cationic) excipients. decomposition – Most hydrocolloids are insoluble in alcoholic solutions Suspending Agents Suspending Agents Suspending Agents A. Hydrophilic colloids A. Hydrophilic colloids A. Hydrophilic colloids (hydrocolloids) (hydrocolloids) (hydrocolloids) – Tragacanth is usually used as 6% – Methylcellulose is a polymer that is – CMC is anionic material that is dispersion in water (mucilage). nonionic and stable to heat and light. soluble in water. – It has an advantage over acacia in – It is available in several viscosity that less is needed, and does not – Prolonged exposure to heat grades contain oxidase. causes loss of viscosity – Because it is soluble in cold water, but – The viscosity of tragacanth is not in hot water, dispersions are greatest at pH 5. prepared by adding to boiling water, and then cooling the preparation until Suspending Agents Suspending Agents Suspending Agents A. Hydrophilic colloids B. Clay Group B. Clay Group (hydrocolloids) – EXAMPLE: bentonite, Veegum, – Official form of bentonite is 5% – Modified cellulose polymers magnesium aluminum alginate magma (SCMC, Avicel, Carmellose Na) These are silicates that are anionic – Veegum is hydrated to a greater – Synthetic polymers/thickeners eg, in aqueous dispersions. degree than bentonite. Thus, it is Carbopol [polyacrylic acid] (lotions – They are strongly hydrated and more viscous at the same and gels), polyvinyl alcohol, exhibit thixotropy concentration. colloidal silicon dioxide Suspending Agents Suspending Agents Preparation C. Other Agents C. Other Agents 1) Solids are wetted initially to separate – Agar, chondrus (carageenan), – Xanthan gum is used in many individual particles and coat them with gelatin (also viscositer), pectin, and modern suspensions because of: a layer of dispersion medium. gelatinized starch. Co-solvent compatibility Wetting is accomplished by levigation to the solid material, followed by – Their use is limited by their Stability blending to form a paste, using a glass susceptibility to bacterial attack, Solution’s high viscosity relative to mortar and pestle or an ointment slab their incompatibilities, and their cost concentration Preparation Preparation Formulation Adjuvant Surfactant can also be used. A. The aqueous dispersion is added to Preservatives, colorants, perfume 2) Suspending agents are then added the solid (or levigated solid) by The required amount of methyl-and as dry powder along with active geometric dilution propyl paraben combinations as ingredient. For best results, the B. The preparation is brought to the preservatives employed in suspending agent is added in the form desired volume by stirring in the pharmaceutical products is: of its aqueous dispersion appropriate vehicle 0.1- 0.2% Main concern of adjuvant Main concern of adjuvant Main concern of adjuvant Compatibility between vehicle and Compatibility between vehicle and Compatibility between vehicle and active ingredient active ingredient active ingredient PACKAGING: PACKAGING: PACKAGING: 3) Modern: Collapsible bags of 1) Flint glass : clear, colorless, brilliant 2) Parenteral multi-dose vials: polyethylene containers glass; – flint, amber or silicone-coated Disadvantage: highly color free soda lime – Silicone coating: steroids, combination ✔loss of flavor silica glass lead-free of penicillin & dihydropstreptomycin, ✔perfume or preservatives as a result of adsorption and leaching high solids Preparation Techniques Equipment used Certain kinds of pharmaceutical suspensions: Consider choice of ingredients and type of Homogenizer or colloid mill: particle 1) Gels equipment size of less than 1 micron –These are semi solid systems If dispersion is made, pulverization is Rotor Stator: Type of mill used for the recommended thru: consisting of fine dispersions made reduction of solid particles size and up of either small inorganic particles MICRONIZATION: 45% of the total weight - Water is dispersed as droplets in an oil or oleaginous medium phase, and water or an aqueous solution is the continuous phase and hydrophilic emulsifier is used - Used for external preparations when emollient, lubricating, or ⚫Oil is dispersed as droplets in an aqueous medium. ⚫O/W emulsions are used topically, orally, or parenterally. protective properties are desired. Types of Emulsion Types of Emulsion Types of Emulsion 3. Multiple emulsions 4. Microemulsion 4. Microemulsion o/w/o or w/o/w - appear as translucent or transparent and have droplet - Use for more rapid and efficient delivery of drugs following diameter in the nanometer range (100Å - 1000Å) oral or transdermal drug delivery system - are thermodynamically stable, optically transparent isotropic mixtures of a biphasic o/w system stabilized with surfactants. Means of Detecting type of emulsion General Considerations of Emulsification General Considerations of Emulsification 1) Dilution test First Consideration: Second Consideration: 2) Dye solubility ⮚Knowledge of the various processes involved in emulsification to ⮚Influence in viscosity 3) Conductivity test approach the formulation with some degree of confidence. ▪ Emulsification process ⮚Droplet formation, formation of interfacial barrier, tendency of ▪ Types of emulsion formed 4) Staining test (filter paper) the particles to aggregate or coalesce 5) Miscibility test ❖Viscosimeter (Brookefield) 6) Fluorescence test - Determines the viscosity of disperse system General Considerations of Emulsification Coalescence of droplets Flocculation Third Consideration: Coalescence refers to the rapid formation of aggregates or It is the result of the interaction of relativity weak particles, ⮚Emulsion Stability emulsion droplets, due to: which may have sufficient emulsifier coverage and therefore ▪ Coalescence of droplets ⮚ no protective barrier is present at the interface of the water and prevent coalescence. ▪ Flocculation oil droplets is differentiated from coalescence, by the fact that the ▪ Creaming ⮚ Very low/ insufficient emulsifier coverage interfacial film remains intact, and therefore aggregation ▪ Sedimentation maybe reversed Creaming Creaming Sedimentation It refers to the separation of the concentrated emulsified Factors: It is the reverse of Creaming, wherein the less concentrated droplets – Difference in densities of the internal and external phase emulsified droplets (the external phase) separates from the (the internal phase) from the continuous phase. – Increase in particle size of the internal phase as compared to the external discontinuous phase in the container. phase It usually “floats” on top of the continuous phase in the – Increased viscosity of the internal phase, more dilute external phase container Pharmaceutical Applications: Pharmaceutical Applications: 1) Oral, rectal, and topical administration of oils and oil- 4) IM injections of some water-soluble vaccines to provide soluble drugs slow release and therefore a greater antibody response and longer lasting immunity 2) Enhance palatability of oils 5) TPN. Sterile o/w emulsion are used to deliver oily 3) Increase absorption of oils and oil-soluble drugs through nutrients IV using non toxic emulsifying agents eg, lecithin intestinal walls Example: Griseofulvin suspended in oil in an o/w emulsion Pharmaceutical Applications: Formulation of Emulsions Formulation of Emulsions For ORAL use: Emulsifying agents help the production of stable dispersion by If the emulsifying agent is more soluble in oil (lipophilic), then oil Cod liver oil emulsion, Liquid Paraffin (Mineral oil) Oral reducing interfacial tension and then maintaining the separation of will be the continuous phase, and w/o type emulsion will be formed. emulsion, Castor oil emulsion the droplets by forming a barrier at the interface. If a substance is added which alters the solubility of the emulsifying For external use: Turpentine Liniment BP, Oily Calamine – If the emulsifying agent is more soluble in water (hydrophilic), then agent, this balance may be altered and the emulsion may change Lotion BP water will be the continuous phase and an o/w emulsion will be formed. type. IV and oral: o/w type This is called phase inversion. IM: may be w/o when intended for depot therapy Formulation of Emulsions Desirable properties of emulsifying agent Desirable properties of emulsifying agent The ideal emulsifying agent is colorless, odorless, tasteless, non- Surface active and reduce surface tension to 10 dynes/cm Impart droplets an adequate electrical potential so that toxic, non-irritant and able to produce stable emulsions at low Absorb quickly around the dispersed drops as a condensed non- mutual repulsion occur concentration. adherent film which will prevent coalescence Increase viscosity of emulsion Effective even at low concentration Naturally Occurring Emulsifying Agents Polysaccharides Polysaccharides Polysaccharides ACACIA TRAGACANTH Semi-synthetic polysaccharides – the best emulsifying agent for extemporaneously prepared oral – Increase the viscosity of an emulsion and prevent creaming emulsions as it forms a thick film at the o/w interface to act as a Sterol-containing substances barrier to coalescence. It is too sticky for external use – Does not contain oxidase and advantage of few amount needed in – Forms a good, stable emulsion of low viscosity. formulation – It tends to cream easily, acidic and stable at pH 2-10 – Coarser than acacia emulsion. – Anionic and difficult to hydrate, used mainly for its effect in viscosity Polysaccharides Polysaccharides PECTIN GELATIN Other polysaccharides eg starch, pectin, and – Provides good emulsion stabilization in a concentration of 0.5 to –Emulsifier that is used in the same proportion as tragacanth. 1% carrageenan are used to stabilize emulsion. – May be anionic or cationic, depending on its isoelectric point ⮚Type A gelatin (+) prepared from an acid treated precursor, used in acidic media ⮚Type B gelatin (-) prepared from an alkali-treated precursor, used in basic media Semi-synthetic Polysaccharides Methylcellulose Carboxymethylcellulose Low viscosity grades of methylcellulose and CMC will form Methylcellulose is nonionic and induces viscosity CMC is anionic and is usually used to increase viscosity o/w emulsion Used as a primary emulsifier with mineral oil and cod liver It tolerates alcohol up to 40% oil, and yields an o/w emulsion. Forms basic solution Usually in 2% concentration Precipitates in the presence of free acids Sterol-containing Substances Surfactants 1) Anionic surfactants These act as w/o emulsifying agents. Classification according to ionic characteristics: – These are organic salts, which, in water have a surface active Examples: Beeswax, woolfat, wood alcohols 1) Anionic surfactants anion – They are compatible with some inorganic cations and with large 2) Cationic surfactants organic cations eg cetrimide 3) Non- ionic surfactants 1) Anionic surfactants 1) Anionic surfactants 2) Cationic surfactants – Widely used in external preparations eg, o/w emulsifying agents EXAMPLES: – These are usually quarternary ammonium compounds which – Must be in ionized form to be effective – Alkali metal/monovalent soap and ammonium soaps eg sodium have a surface active cation and so are sensitive to anionic – Generally stable at alkaline pH stearate (o/w) surfactants eg soaps – Soaps of divalent and trivalent metals eg calcium oleate (w/o) – Used in the preparation of o/w emulsion for external use emulsion – Amine soaps eg triethanolamine oleate (o/w) – Alkyl sulfate eg sodium lauryl sulfate (o/w) 2) Cationic surfactants 3) Non- ionic surfactants 3) Non- ionic surfactants – Must be in their ionized form to be effective – Synthetic materials and largest group of surfactants EXAMPLES: – Emulsion formed are generally stable at acidic pH – Used to produce o/w or w/o emulsions for both external and Glycol and glycerol esters, polysorbates, macrogol ethers and – Have antimicrobial activity internal use. esters, sorbitan esters, EXAMPLES: – These are compatible with both anionic and cationic substances higher fatty alcohols, and polyvinyl alcohols – Cetrimide, benzalkonium chloride, CPC – Highly resistant to pH change – Emulsion formed depends on HLB number SPANS and TWEENS Finely Divided Solids Finely Divided Solids HLB number substances adsorbed in the water interface to form a coherent EXAMPLES: It is usually between 1 and 20 is allocated to an emulsifying agent film. and represents the relative proportions of lipophilic and hydrophilic Bentonite, aluminum magnesium silicate, hectonite. molecule, and produce an o/w emulsion. If particles are preferentially wetted by oil or by water, a w/o and an o/w emulsion formed, respectively Colloidal aluminum and magnesium hydroxides are used HLB 3-6 indicate lipophilic molecule, produce w/o emulsion O/W has a good stability which are less prone to microbial for internal preparations HLB 8-18 indicate hydrophilic molecule, produce o/w emulsion contamination than those naturally derived agents HLB Values of Emulsifying Agents HLB Values of Emulsifying Agents Acacia 8.0 Polysorbate 80 15.0 Sorbitan monolaurate 8.6 Sodium lauryl sulfate 40.0 Sorbitan monostearate 4.7 Sodium oleate 18.0 Polysorbate 20 16.7 Tragacanth 13.2 Polysorbate 60 14.9 Triethanolamine oleate 12.0 Considerations: Choosing an Emulsifying Agent Choosing an Emulsifying Agent Oils and waxy materials have a required “HLB number” which 1) Emulsifying agent used for internal preparations should be 3. Polysorbates have disagreeable taste, therefore flavorants are helps in the selection of appropriate emulsifying agents when necessary formulating emulsions. non-toxic and non-irritant. Non-ionic emulsifying agent and Example is liquid paraffin has a required HLB of 5 to obtain w/o natural polysaccharides are useful. 4. Non-ionic emulsifying agents which are useful for parenterals emulsion, and HLB of 12 for an o/w emulsion include: lecithin, polysorbate 80, methylcellulose, gelatin and serum 2) The taste should be bland and palatable Two or more surfactants can be combined to achieve a suitable HLB albumin value and often give a better results than one surfactant alone General Considerations in the Preservatives and Mechanism of preservatives Use of Preservatives Concentration Combinations of preservatives are made to increase the Preservatives should first, meet the following general Benzoic acid: 0.1% at a pH are prepared agglomerates of smaller particles of powder ⮚ passed through no. 4-12 sieves WET GRANULATORS: (SSSH) ❖Dusting powders – sifter top container 1. Wet Granulation aka: Wet Massing 1. Shear granulators ❖Powders for ear, nose, throat, tooth Types: 2. High speed mixers/granulators 3. Spray dryers For flowability for tableting A. wet massing with the use of sockets, or vagina – dispensed with Method of Preparation: water- (MSD) 4. Spheronizers/pelletizers 1. moistening the powders to insufflators or powder blower, for 1.) Dry granulation produce a wet mass administration 2.) Wet granulation 2. screening the wet mass to break into granules of desired size 3. dry the granules to remove solvent B. fluid bed granulation liquid is sprayed on suspended powders 2. Dry Granulation -- particles are aggregated using high pressure FLUID BED GRANULATION GRANULATIO process in which primary powder particles are made Types: N to adhere to form larger, multiparticle entities A.roll-compaction B. slugging method (SGS) A method of tablet production method (RGS) -- slugging the powders a multistep process used to make uniformly -- powders are rolled (formation of a large wherein a granulation solution is Spheronization– spherical particles (for controlled release into dense sheets tablet called slug) sprayed onto the suspended application -- sheets are granulated -- slugs are granulated using an appropriate using a mechanical particles which would then be granulator equipment -- sieve granules to dried rapidly in the suspending -- sieve granules to obtain the desired size obtain the desired size air Improvement of Powder / Granule Flowability 1. Alteration of particle size and size distribution Qualities of a Good - use larger particles Types of Granules Granulation - Reduce the amount of fines a. Good Granules particles that pass 1. as spherical as possible 2. Alteration of particle shape or texture - The more spherical and smoother the particles, the EQUIPMENTS USED FOR through sieve 20 and are 2. uniform in content retained at sieve 40 b. Fines particles that 3. normal or bell- shaped distribution of more flowable 3. Alteration of surface forces POWDERS AND pass sieve 40 particle sizes - Properties of Granules for Tablet - reduce/increase electrostatic charges - reduce moisture content GRANULES Production 1. fluidity / flowability 4. Alteration of process conditions 2. compressibility 5. Use of flow activators (GAL) -- Use glidants, lubricants and antiadherents Requirements for equipment used in pharmaceuticals… Additional Requirements Closed Circuit Milling Of fabricated materials Dust free operation It combines the milling equipment with some type Chemically compatible Durability of classifier Mechanically compatible Simplified construction It is advantageous in cases wherein, ____________ distribution and _________ is Easy to disassemble for cleaning (preventing cross Operation desired contamination) Suitable feed Outlet capacities Three Broad Categories of Basic Actions of Comminuting Closed Circuit Milling Comminution Equipment SCREEN is used to make the separation 1. Coarse crushers Attrition Oversized particles are returned to the mill on a continuous basis ex. Jaw, gyratory, roll, and impact crushers This involves breaking down of the While, particles of desired size pass through the screen 2. Intermediate grinders material by __________ between two and out of grinding chamber surfaces. ex. Rotary cutters, disk, hammer, roller, and chaser mills 3. Fine grinding mills ex. Ball, rod, hammer, colloid, and fluid- energy mills high-speed mechanical screen and centrifugal classifier Basic Actions of Comminuting Basic Actions of Comminuting Equipment Equipment Fine Grinding Mills Rolling Impact 1. Roller Mills This uses a heavy rolling member to This involves the operation of _______ at high speeds. - in their basic form consist of two These strike the lumps of material and throw them crush and pulverize the material. against each other or against the walls of the rollers revolving in the same direction Theoretically, only a rolling-crushing type containing chamber. of action is involved, but in actual at different rates of speed. practice some slight attrition takes place - it is quite versatile and can be between the face of the roller and the used to crush a variety of materials. bed of the mill. Fine Grinding Mills Fine Grinding Mills Fine Grinding Mills 2. Hammer Mills 2. Hammer Mills 3. Centrifugal-Impact Mills and Sieves - consist of a rotating shaft on which - are useful to minimize the are mounted either rigid or swing FEED HOPPER Material enters CHAMBER production of fine particles, because hammers (beaters). their design combines ____________ - This unit is enclosed with a into a single operation chamber containing a grid or removable - The mill consists of a nonrotating Rapidly rotating screen through which the material must Swept down into the screen with additional hammer strikes bar or stator that is fixed within a pass hammering action to against the material rotating sieve basket. reduce particle size * and breaks it into smaller fragments Fine Grinding Mills Fine Grinding Mills 3. Centrifugal-Impact Mills and Sieves 4. Cutter Mills - the particles or agglomerates larger than the - are useful in reducing the particle hole size are directed by centrifugal force to impact size of fibrous materials and act by a with the stator combined ____________ action - The sieve baskets also can be constructed to - consist of a horizontal rotor which have a cutting edge that can aid in particle-size turns within a housing, and into it are set reduction without impact with the stator. stationary bed knives or blades. The feed is from the top and perforated plate or screen is set into the bottom of the housing through which the finished product is discharged. Fine Grinding Mills Fine Grinding Mills 5. Attrition Mills 6. Chaser Mills - make use of two stone or steel - are so called because two heavy grinding plates, one or both of which granite stores, or chasers, mounted revolve to provide grinding mainly vertically like wheels and connected by a through attrition. short horizontal shaft, are made to revolve or chase each other upon a granite base surrounded by a curb Fine Grinding Mills Fine Grinding Mills Fine Grinding Mills 6. Chaser Mills 7. Pebble or Ball Mills 7. Pebble or Ball Mills - Revolution of the chasers - sometimes called ____________, - These cylindrical vessels revolve produces an upward current of air; this are operated on the principle of horizontally on their long axis and the carries over the lighter particles, which attrition and impact. tumbling of the pebbles or balls over fall outside the curb and subsequently - The grinding is effected by placing one another and against the sides of the are collected as a fine powder. the substance in jars or cylindrical cylinder produces pulverization with a vessels that are lined with porcelain or a similar hard substance and containing minimum loss of material. pebbles or balls of flint, porcelain, steel or stainless steel. Fine Grinding Mills Fine Grinding Mills Fine Grinding Mills 8. Vibrating Ball Mills 9. Fluid Energy Mills 9. Fluid Energy Mills - which also combine attrition and - are used for pulverizing and - The material to be pulverized is impact, consist of a mill shell containing classifying _____________ of many swept into violent turbulence by the a charge of balls similar to rotating ball materials. sonic and supersonic velocity of the mills. - The mills have no moving parts, streams. grinding being achieved by subjecting the solid material to streams of high- velocity elastic fluids, usually air, steam, or an inert gas. Fine Grinding Mills Large Scale Mixing Equipment Large Scale Mixing Equipment 10. Centrifugal Impact Pulverizers 1. Rotating-Shell Mixers 2. Fixed-Shell Mixers - have been found to be effective - The drum-type, cubical shaped, - The ribbon mixer, one of the for the reduction of the particle size of a double-cone, and twin-shell blenders oldest mechanical solid-solid blending wide variety of materials ranging from are all example of this class of mixers. devices, exemplifies this type of mixer. very soft, organic chemicals to hard, abrasive minerals. Large Scale Mixing Equipment Large Scale Mixing Equipment Large Scale Mixing Equipment 3. Sigma-Blade and Planetary Paddle 4. Vertical Impeller Mixers 5. Motionless Mixers Mixers - have the advantage of requiring - These are in-line continuous - are also used for solid-solid little floor space, employ a screw-type processing devices with no moving blending impeller that constantly overturns the parts. They consist of a series of fixed batch. flow-twisting or flow-splitting elements. Large Scale Mixing Equipment Large Scale Mixing Equipment Large Scale Mixing Equipment 6. Propeller Mixers 6. Propeller Mixers 6. Propeller Mixers - most often used mixing - Propeller mixers, typically, are - lower speed units with larger implement; Often called a “prop” mixer operated around 300-400 rpm or at high impeller diameters are the best choices for short speeds around ______, depending on for blending applications - these machines use a rounded, the manufacturer’s standards. - However, a high speed propeller, pitched, three- (or four-) blade design may provide the higher shear rates that produces mostly axial flow. required for a level of emulsifying or of - provide good flow and, hence,