Weft Knitting Machines PDF
Document Details
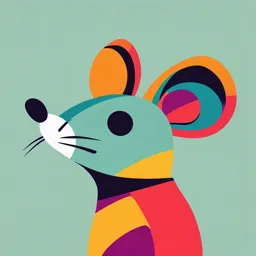
Uploaded by SimplestSaxhorn
Engr. Shakeel Ahmad Paracha
Tags
Summary
This document provides an introduction to the various types of weft knitting machines, including their classifications and features. It covers different machine types, their working mechanisms, and their applications in the textile industry. It is designed for professionals in the textile field.
Full Transcript
Textile Institute of Pakistan, Karachi. TEXT302 (Knitting Technology) Introduction A knitting machine is a device used to create knitted fabrics in a semi or fully automated fashion. There are numerous types of knitting machines, ranging from the...
Textile Institute of Pakistan, Karachi. TEXT302 (Knitting Technology) Introduction A knitting machine is a device used to create knitted fabrics in a semi or fully automated fashion. There are numerous types of knitting machines, ranging from the simple, and non- mechanical, to the highly complex and electronic. All, however, produce single jersey fabrics to complicated jacquard knitted fabrics, usually either flat or tubular, and of varying degrees of complexity. Pattern stitches can be selected by hand manipulation of the needles, or with push-buttons and dials, mechanical punch cards, or electronic pattern reading devices and computers. These knitting machines also ranges from high production to limited production capacity. Weft Knitting Machines according to End Product Weft knitting machines may be broadly grouped according to end product as either: o Circular machines, knitting tubular fabric in a continuous uninterrupted length of constant width. o Flat and circular machines, knitting garment- length sequences, which have a timing or counting device to initiate an additional garment-length programming (machine control) mechanism. o This co-ordinates the knitting action to produce a garment length structural repeat sequence in a wale-wise direction. The garment width may or may not vary within the garment length. Fabric Machines Large diameter, circular, latch needle machines, knit fabric, at high speed, that is manually cut away from the machine (usually in roll form) after a convenient length has been knitted. Most fabric is knitted on circular machines, both single cylinder (single jersey) or cylinder and dial (double jersey), of the revolving needle cylinder type, because of their high speed and productive efficiency. Garment-length Machines Garment-length machines include straight bar frames, most flats, hosiery, leg wear and glove machines, and circular garment machines including sweater strip machines, producing knitwear, outerwear & innerwear. On these machines, the garment sequence control with the timing / counting device, collectively termed ‘the machine control’, automatically initiates any alteration to the other facilities on the machine needed to knit a garment-length construction sequence instead of a continuous fabric. Prepared By: Engr. Shakeel Ahmad Paracha Page 1 of 19 Textile Institute of Pakistan, Karachi. TEXT302 (Knitting Technology) Garments may be knitted to size either in tubular or open-width; in the latter case more than one garment panel may be knitted simultaneously across the knitting bed. Large-diameter circular machines and wide V-bed flat machines can knit garment blanks that are later split into two or more garment widths. Weft Knitting Machines according to their Frame Design and Needle Bed Arrangement The three main groups of weft knitting machinery may broadly be classified as either straight bar frames, flats, or circulars, according to their frame design and needle bed arrangement. The simplest weft knitting machinery has one set of needles, arranged either in a straight line (flat bar / straight bar) or around cylinder (circular). These machines are capable of producing single jersey fabrics, but not double jersey fabrics, and can use a combination of three types of stitches: knit, miss or tuck. With two needle beds, double jersey fabrics such as rib and interlock can be produced on both flat bar machines and circular machines. Classification of Weft Knitting Machines w.r.t Needles Prepared By: Engr. Shakeel Ahmad Paracha Page 2 of 19 Textile Institute of Pakistan, Karachi. TEXT302 (Knitting Technology) Classification of Weft Knitting Machines w.r.t Frame Design and Needle Bed Arrangement Straight Bar Knitting Machine Straight bar frame is a specific type of machine having a vertical bar of bearded needles whom movement is controlled by circular engineering cams attached to a revolving cam-shaft in the base of the machine. The three directions of motion required for the knitting action are provided from two separate sources. The rotary motion of the cam-shaft produces the vertical and horizontal movement of the needle bar. The sideways reciprocating movement for the yarn carriers and for introducing the sinkers in serial sequence via the slurcock (a cam for operating the jacks and jack-sinkers in a knitting- machine) is obtained from draw cam attached to a shaft, set at right angles to the main cam- shaft at the back of the machine, which oscillates a draw lever. A variable draw ensures that the stroke of the draw is related to the varying knitting width. Thus, more courses per minute are knitted on narrower widths. Operating speeds of a hundred courses per minute can be achieved. The length of the machine is divided into a number of knitting heads (‘sections’ or ‘divisions’) and each head is capable of knitting a separate but identically-dimensioned fashion-shaped garment panel. Characteristics of Straight Bar Knitting Machine Straight bar frames are long and expensive machines that are highly productive in a very narrow sphere of garment manufacture. The machines have limited knitting width, and current fashion does not fully utilize their ability to shape fashion or transfer patterns through stitching. Straight bar machines are known for their production of high-quality garments as a result of the gentle knitting action, low fabric tension and fashion shaping, which reduces the waste of Prepared By: Engr. Shakeel Ahmad Paracha Page 3 of 19 Textile Institute of Pakistan, Karachi. TEXT302 (Knitting Technology) expensive yarn during cutting and is emphasized on the garments by carefully-positioned fashion marks. The straight bar frame is the only bearded needle weft knitting machine that is still commercially viable, although it now faces serious competition from electronically controlled flat machines. Parts of Straight Bar Knitting Machine A (Bearded needle): Having a cranked end for location in the tricked and drilled needle bar. B (Sinker): Only one between every other needle space with a reinforced back and, at the front, a ‘catch’ to sink the yarn around the needles, and a ‘neb’ to separate the old and new loops until knock-over. C (Divider): Occupying each remaining space, usually having the same shaped front as the sinker but with an extended tail at the back. D (Knocking-over bit): One directly beneath each sinker and divider - having a ‘throat’ for holding the loops and a ‘nose’ for knocking-over. E (Needle bar): Having a compound horizontal and vertical movement. F (Striking jack): Fulcrummed at its lower end, each one with its ‘nose’ resting on a sinker back, and a ‘spring’ exerting pressure on its ‘tail’. G (Catch bar): Extending the full width of the knitting head having forward and backward as well as vertical movement. H (Yarn carrier): Which traverses in alternate directions across the head from one course to the next-up to six carriers may be available. The carrier is connected to a reciprocating carrier rail by friction, and when the carrier is arrested by its carrier stop, the carrier rail completes its full traverse, driven by the coulier cam and punching through the carrier friction. J (Falling bar): Which is a stop that cushions the advance of the sinkers and dividers. Knitting Action of Straight Bar Knitting Machine Thread laying (a): The carrier moves across the knitting head, laying the yarn on the noses of the sinkers and dividers and on the beard side of the needles to form the new course in the fabric. Prepared By: Engr. Shakeel Ahmad Paracha Page 4 of 19 Textile Institute of Pakistan, Karachi. TEXT302 (Knitting Technology) Sinking (b): The slurcock (one for each knitting head), travelling behind the carrier, contacts the jacks it is shaped so that each jack in turn pushes the sinker forwards to kink a loop around every two adjacent needles. Dividing (c): The catch bar moves the dividers forwards, collectively, whilst the needle bar tips slightly outwards to allow the double loops to be divided into equal-sized needle loops around every needle. Pressing (d): The needle bar descends, placing the new loops inside the hooks of the beards. The catch bar is now lowered so that the sinkers, as well as the dividers, are collectively controlled by it for the rest of the knitting cycle. Landing (e): They now start to withdraw. The needle bar moves towards the sinker verge, causing the beards to be pressed. A further downward movement of the needle bar ‘lands’ the previous course of loops, resting on the knock-over bits, onto the closed beards. Drop-off: As the needle bar moves away from the pressing-edge, the sinkers and dividers withdraw so that the newly-formed course of loops drops off their noses onto the knocking- over bits. Completion of knock-over (f): The needle bar descends to its lowest position. As the heads descend below the belly of the knocking-over bits, the old course of loops is collectively knocked-over. Holding-Down: As the sinkers and dividers move collectively forward to hold down the fabric, the needle bar rises to the thread-laying position. The catch bar is slightly raised to release the sinkers for individual movement at the start of the next course. Prepared By: Engr. Shakeel Ahmad Paracha Page 5 of 19 Textile Institute of Pakistan, Karachi. TEXT302 (Knitting Technology) Flat Knitting Machine Two types of flat machine evolved. The slower, more specialized flatbed purl or links-links machine and the widely used V-bed rib machine. Flatbed purl (links-links) machines have horizontal needle beds. They use double-headed latch needles that are transferred to knit in either of two directly opposed needle beds. On a v-bed machine, the two needle beds are arranged in a ‘V’ configuration. Link-link machine Needles in link-link V-bed machine Needles in V-bed V-Bed Knitting Machine V-bed machines have two rib gated (the tricks in the opposing beds are arranged so that the needles can pass between each other during loop formation, this arrangement of the beds is called rib gaiting), diagonally approaching needle beds, set at between 90° - 104 ° to each other, giving an inverted V-shape appearance. The interactions between the yarn and the knitting elements that create the fabric occur at the apex of the “V” and the fabric moves away downward between the two beds, drawn down by the take down system. This knitting machine stitch potential includes needle selection on one or both beds, racked stitches, needle-out designs, striping, tubular knitting, changes of knitting width, and loop transfer. The carriage or “CAM box” traverses across the needle beds and selects needles to be knitted as it reciprocates side to side. Prepared By: Engr. Shakeel Ahmad Paracha Page 6 of 19 Textile Institute of Pakistan, Karachi. TEXT302 (Knitting Technology) Rib gaiting Carriage Carriage Carriage Characteristics of V-Bed Knitting Machine The flat knit (V-bed) machines are the most versatile of the weft knitting machines. The modern V-bed knitting machine is a highly engineered, fully automated, electronically controlled, precision knitting system. The number of garments or panels knitted across the machine depends upon the knitting width, yarn carrier arrangement, yarn path and yarn package accommodation. Needle bed length can vary from 1.0 m to 2.2 m width and each is designed for a specific task or purpose. Latch needles are used. Angular cam of a bi-directional cam system is used. A separate cam system is used for each needle bed. The two cam systems are linked together by a bridge, which passes across from one needle bed to the other. Cam system is attached to the bottom side of the carriage. The carriage effectively raises and lowers the needles on both beds simultaneously as it passes over them, depending on the desired pattern. Normally machine gauge is 3 to 18 needles per inch and machine width up to 79 inches. A wide range of yarn counts (finer to coarser) may be knitted for each machine gauge, including a number of ends of yarn at each knitting system; the stitch length range is also wide; and there is the possibility of changing the machine gauge. The operation and supervision of the machines of the simpler type are also less arduous (complex) than for other weft knitting machines. The modern flat knit machine also has its own on-board control and programming computer and the LCD monitor display built into the sliding machine covers. Normally, in a production environment these machines can be networked and knitting programmes can be downloaded from the CAD / programming stations directly to the machine's computer. Equally, production statistics can be collected centrally. Parts of V-Bed Knitting Machine Yarn package: The package may cone or cheese. The weight of supply package may be 2.5 - 6.25 lbs. depending upon count of yarn. The weight of filament yarn package may be 8 - 10 lbs. Yarn guide: It is used to maintain the path of the yarn. Prepared By: Engr. Shakeel Ahmad Paracha Page 7 of 19 Textile Institute of Pakistan, Karachi. TEXT302 (Knitting Technology) Passage of yarn from package to yarn carrier Torsion spring: It is used to maintain the tension in the yarn. Cymbal tension: It is a spring loaded tensioning device. It is used to maintain the uniform tension of yarn. Yarn take-up: It is used to take-up the yarn from package at a constant rate. Fabric comb & dead weighting system: The whole system is used to take-up the fabric from the knitting zone. Fabric is taken-up between the gaps of the two needle beds. Yarn feeders: The yarn supply is situated above the machine and the yarn is fed to the needles via yarn feeders that culminates in a tube or bore to precisely position the yarn. The feeder is fixed to a feeder block that slides along a feeder rail located above the needle bed. Modern machines typically have four feeder rails with 4 / 6 knitting feeders / rail. Yarn carrier: Yarn carrier is used to supply yarn to the needle hook. Back needle bed: Used for the movement of the back needles during the loop formation. Front needle bed: Used for the movement of the front needles during the loop formation. Needle spring: Push the needle upward to prevent the needle from going downward to a specific level. Latch needle: It is the basic knitting element. CAM System of V-Bed Knitting Machine CAM plate and knitting carriage Prepared By: Engr. Shakeel Ahmad Paracha Page 8 of 19 Textile Institute of Pakistan, Karachi. TEXT302 (Knitting Technology) The needle butts will enter the traversing cam system from the right during a left to right carriage traverse and from the left during a right to left traverse. For each needle bed there are two raising cams (R), two cardigan cams (C) and two stitch cams (S). The arrangement as shown in the following figure is referred to as a knitting system. A single system machine will knit one course of rib in one traverse whereas a double system machine will knit two courses of rib per traverse. Sometimes a set of cams in one bed is referred to as a lock. Knitting Action of V-Bed Knitting Machine 1. The rest position: The tops of the heads of the needles are level with the edge of the knock-over bits. The butts of the needles assume a straight line until contacting the raising cams R (R) because the leading stitch cams S and AS (L) are lifted to an in active position. The lifting action is an alternating action that always lowers the trailing stitch cams and raises the leading stitch cams in each system as the traverse commences. This action prevents needles from being unnecessarily lowered and a strain being placed on the old loops prior to the start-up of the knitting action. 2. Clearing: The needle butts are lifted as they contact the leading edge of cams R (R), which raises the needles to ‘tucking in the hook’ height with the under surface of cams S (L) acting Prepared By: Engr. Shakeel Ahmad Paracha Page 9 of 19 Textile Institute of Pakistan, Karachi. TEXT302 (Knitting Technology) as guard cams. The needles are lifted to full clearing height as their butts pass over the top of cardigan cams C (R) and C (L). 3. Yarn feeding: The yarn is fed as the needles descend under the control of guard cam (G). The required loop length is drawn by each needle as it descends the stitch cam S (R). 4. Knocking-over: To produce synchronized knocking-over of both needle beds simultaneously, the stitch cam S (R) in the front system is set lower than the auxiliary stitch cam AS (R), so that the latter is rendered ineffective. 5. Delayed timing of the knock-over: If, however, delayed timing of the knock-over is employed, knock-over in the front bed will occur after knock-over in the back bed. In this case, stitch cam S (R) is not set as low as AS (R) so that the depth setting of the latter cam produces the knock-over action. Delayed timing is only normally used on gauges finer than 8 npi and cannot be used for broad ribs. Prepared By: Engr. Shakeel Ahmad Paracha Page 10 of 19 Textile Institute of Pakistan, Karachi. TEXT302 (Knitting Technology) Circular Knitting Machine The term ‘circular’ covers all those weft knitting machines whose needle beds are arranged in circular cylinders and/or dials, including latch, bearded, or (very occasionally) compound needle machinery, knitting a wide range of fabric structures, garments, hosiery and other articles in a variety of diameters. Circular knitting machines are either of body size or larger, having a single cylinder or double cylinder, cylinder and dial arrangement, as is also the case with small diametre machines for hosiery. The modern circular knitting machine is a highly engineered, electronically controlled, precision knitting system capable of producing high quality fabric at very high speeds. Circular Knitting Machine Single Needle bed Double Needle bed Circular Knitting Machine Single Needle bed Double Needle bed The frame or body is circular according to needle bed shape that supports the majority of the mechanisms of the machine. All over the world, the majority of knit fabrics are manufactured on circular knitting machines. These machines have high level of performance. The different materials and the range of yarn counts that they are able to process on circular knitting machines. The wide variety of designs and stitches it can produce. The knitted fabrics can meet the needs of a very large end user market from the traditional outwear and innerwear sectors, hosiery, household, car interiors. Since, the needles are arranged in a circle on a circular knitting machine, the fabric is a tubular. It is usually slit open when used. Circular knitting machine is naturally the choice for the volume production. Since it is ideal for volume production, there are purposely built circular machines. For example, plain knit fabric is always in demand and large quantities. Circular with just one set of needles in the cylinder is available for plain knit only. Prepared By: Engr. Shakeel Ahmad Paracha Page 11 of 19 Textile Institute of Pakistan, Karachi. TEXT302 (Knitting Technology) All other knit structures requiring the second set of needles will be impossible but just producing plain fabric will be able to keep it occupied all the time. Circular knitting machine can be classified on following basis: o According to machine diameter Large-diameter circular knitting machines (from 24 to 40 inches). Medium-diameter circular knitting machines (from 8 to 22 inches). Small-diameter circular knitting machines (from 3 to 6 inches). o According to number of needle-beds Single-bed (for jersey and derived stitches: fleece, terry, piquet, floating Jacquard) Double-bed Dial-cylinder knitting machines with 90° needle-beds (for rib knit and similar: cardigan stitches (open vertically in the front), milanese rib (sets of ribs change angle), bourrelet, rodier, cable (groups of rib cross each other), eyelet (holes are produced) and jacquard stitches, as well as all interlock and interlock-derived stitches). Double-cylinder knitting machine knitting machines with 180° needle-bed (for stitches based on the links-links construction). Parts of Circular Knitting Machine 1, 2 {The top (1) and bottom (2) stop motions}: These are spring-loaded yarn supports that pivot downwards when the yarn end breaks or its tension is increased. This action Prepared By: Engr. Shakeel Ahmad Paracha Page 12 of 19 Textile Institute of Pakistan, Karachi. TEXT302 (Knitting Technology) releases the surplus yarn to the feeder, thus preventing a press-off, and simultaneously completes a circuit which stops the machine and illuminates an indicator warning light. 3 (Spring-loaded detector points): These are carefully positioned around the cylinder according to their particular function. A pointer is tripped to stop the machine by a fault or malfunctioning element such as a yarn slub, fabric lump, needle head, latch spoon, etc. 4 {The tape positive feed (4A)}: This provides three different speeds (course lengths) and is driven and can be adjusted from the drive arrangement (4B). 5 (The cylinder needle cam system for each feed): Contained in a single replaceable section and having an exterior adjustment for the stitch cam slide. 6 (The automatic lubrication system): It is used to lubricate the different moving parts of the knitting machine. 7 (Start, stop and inching buttons): These buttons are used to start, stop and run the knitting machine at slow speed. 8 (The cam-driven fabric winding down mechanism): Which revolves with the fabric tube. 9 (The revolution counters): For each of the three shifts and a pre-set counter for stopping the machine on completion of a specific fabric length (in courses). 10 Side creel (optional): Used to mount the supply packages. 11 (Lint blower): This reduces the incidence of knitted-in lint slubs, to improve quality when using open-end spun yarns. It also reduces cross contamination by fibres from other machines. Prepared By: Engr. Shakeel Ahmad Paracha Page 13 of 19 Textile Institute of Pakistan, Karachi. TEXT302 (Knitting Technology) Creel: Creel is a vertical aluminium stick for holding the yarn cone. It also known as side creel. Cone Holder: Cone holder is an inclined metallic stick where yarn cone is placed for feeding the yarn to the feeder easily. It is also known as cone carrier. Aluminium Telescopic Tube: This is the tube through which yarn is passed. It reaches the yarn to the memminger positive feeder. It works as a yarn cover. It protects the yarn from the excessive friction, dust and fly fibre. Creel and Cone Holder Aluminium Telescopic Tube MPF Device: MPF means memminger positive feed. It receives yarn from aluminium telescopic tube. As this device gives a positive feed of yarn to the needles, so it is called Memminger Positive Feed device. MPF provides uniform tension to yarn, reduces machine stoppage, identify and remove yarn knot and give a signal if yarn breaks. Memminger Positive Feeder Prepared By: Engr. Shakeel Ahmad Paracha Page 14 of 19 Textile Institute of Pakistan, Karachi. TEXT302 (Knitting Technology) Winding Wheel & Driven Pulley: Some yarn is rolled on the winding wheel so that if the yarn is torn off, the whole yarn does not need to be replaced again. Driven Pulley controls the speed of MPF. Yarn Tensioner: Yarn tensioner is a device that ensures the appropriate gripping of yarn. Stopper: Stopper is a part of MPF. Yarn is passed through the stopper and it is connected with the sensor. If yarn breaks, then stopper gets upwards and the sensor receives a signal to stop the machine. At the same time, a light also flashes. Generally, a stopper is two types. Top stopper and bottom stopper. Sensor: The sensor is located at MPF. If anyone of the stoppers gets upwards due to the breakage of yarn, the sensor automatically receives signal and stops the machine. Lycra Attachment Device: Lycra yarn is feed by the following device. Yarn Guide: Yarn guide receive yarn from the MPF. It is used to guide the yarn and sent yarn to the feeder guide. Lycra Attachment Device It maintains the smooth tension on the yarn. Feeder Guide: Feeder guide receive yarn from yarn guide and feed yarn to the needle. It is the last device which releases yarn to the knit fabric. Feeder Ring: This is a circular ring which holds all the feeder guide. Needle: Needle is the master part of the knitting machine. Needle receive yarn from the feeder, create a loop as well as release old loop and finally produce the fabric. Lycra Attachment Device Yarn & Feeder Guide Feeder Ring Needle VDQ Pulley: VDQ means Variable Dia. for Quality. As this pulley controls the quality of knitted fabric by adjusting GSM & stitch length during the knitting process, so it is called VDQ pulley. To increase the fabric GSM the pulley is moved towards the positive direction and to decrease the fabric GSM the pulley is moved towards the reverse direction. This pulley also called quality adjustment pulley (QAP) or Quality adjustment Disk (QAD). Pulley Belt: Pulley belt gives the motion to pulley. Cam: Cam is the device which converts the rotary motion into a definite reciprocating motion for the needles and some other devices. Cam Box: Cam box holds and supports cam. Knit, truck and miss cam are arranged horizontally according to fabric design in the cam box. Sinker: Sinker is another master part of the knitting machine. It supports yarn to form the desired loop. Sinker is located at each and every gap of the needle. Sinker Box: Sinker box holds and supports the sinker. Sinker Ring: This is a circular ring which holds all sinker box. Prepared By: Engr. Shakeel Ahmad Paracha Page 15 of 19 Textile Institute of Pakistan, Karachi. TEXT302 (Knitting Technology) VDQ Pulley & Pulley Belt Different types of CAM Cam Box Sinker Box Cylinder: Cylinder is another master part of the knitting machine. Cylinder adjustment is one of the most important technical work. The cylinder holds and carries needle, cam box, sinker, etc. Body: The body of the knitting machine covers the whole area of the machine. It holds base plate, cylinder, etc. Base Plate: Base plate is a plate that holds the cylinder. It located on the machine body. Air Blow Gun: A device connected with high-velocity pressurized air. It blows air to feed the yarn through the aluminium tube. It also used for cleaning purposes. Cylinder Machine Body Base Plate Air Blow Gun Automatic Needle Detector: A device placed very close to the needle sets. It gives a signal if it found any broken or damaged needle. Fabric Detector: If fabric torn off or fall down from the machine, fabric detector touch the cylinder and the machine becomes stopped. It also called fabric fault detector. Adjustable Fan: Generally two sets of running fans are continuously circulated from the centre of machine dia. These fans are faced with the needle points that remove dust, hairy fibre as well as keep needle cool. Adjustable fans are rotated in the opposite motion of the cylinder. Lubricating Tube: This tube supplies lubricants to the cam box, sinker box to remove excessive friction and heat. Lubricants are sent through the tube with the help of an air compressor. Automatic Needle Detector Fabric Detector Adjustable Fan Lubricating Tube Prepared By: Engr. Shakeel Ahmad Paracha Page 16 of 19 Textile Institute of Pakistan, Karachi. TEXT302 (Knitting Technology) Manual Jig: It is attached with the machine body. It used to adjust needle, sinker, etc. manually. Gate: Gate is situated under the machine bed. It keeps covered the knitted fabric, take-down motion rollers, and winding rollers. Spreader: Spreader is situated below the machine body. It receives fabric from the needle, spreads fabric and ensures uniform fabric tension. The spreader is adjusted as the fabric is open type or tube type. Take-Down Motion Rollers: These rollers are situated just under the spreader. They pull fabric from the spreader, grip fabric firmly and take fabric down. These rollers also called fabric withdraw rollers. Winding Roller: This roller is situated just under the take down motion rollers. It rolled the fabric itself. When this roller becomes bigger by the fabric layer it also moves upward. Manual Jig & Gate Spreader Take-Down Motion Rollers Winding Roller CAM System of Circular Knitting Machine Normally, circular knitting also adopts the same knitting principles as the flat bed machines. The circular machine starts to knit when the CAM systems on the needle beds (cylinder and dial) move along the surface quite similar to that of the carriage on a flatbed machine. The only difference is that the operation is continuous as CAM system of the circular machine does not need to stop during knitting because there is no beginning or end of a course. Circular knitting CAM systems only allow for unidirectional knitting. CAM systems generate both the needle and the sinker moment for single jersey machines and cylinder and dial moment for double jersey machines. Similar to a flatbed machine, multi-system circular knitting is also possible. Fig. 1 is a schematic diagram of a circular knitting machine having eight systems. Fig 1: Multi system circular machine As shown in figure, it is clear that every CAM system is knitting at the same time and each of CAM system is having its own supply of yarn for its own course. Prepared By: Engr. Shakeel Ahmad Paracha Page 17 of 19 Textile Institute of Pakistan, Karachi. TEXT302 (Knitting Technology) So, when the machine runs, all eight systems move together and hence eight courses of fabric are in knitting at the same time. In other words, at the end of one revolution of the CAM system, eight courses of fabric are completed. Similarly, if there is more CAM systems around the machine, there will be more fabric courses being produced in a single revolution of the machine, e.g., say if there are 30 CAM systems, 30 courses of fabric will be completed in one revolution of the CAM system. It may be noted that the number of systems around the machine is limited by the circumference of the needle cylinder. Usually, all the space on the circumference is issued up for placing CAM systems. The actual number of CAM systems depends on the cylinder diametre and the dimensions (width) of the CAM boxes. For example, a 30-inch diametre machine may have 72 to 90 CAM systems. Since, each CAM system must have its own yarn supply and hence a yarn feeder, such machine can be referred as 30-inch, 90-Feed machine. From above figure, further, it can be seen that whether there are eight systems or 80 systems, the space taken up by the machine will not be changed. As compared to a flatbed machine with a circular machine, the CAM systems of a circular machine always operate at their maximum speed. Also, circular machines always have much more CAM systems than flatbed machines. A double system machine with 100-inch needle bed produces about 45 courses per minute and a 30-inch, 90-feed circular machine produces about 2,700 courses per minute. Further, in circular knitting machine, needle action is a result of the relative motion between the CAM plates and the needle butt. The same needle action will be achieved whether the CAM plate is moving across the needle butt or the needle butt is moving across the CAM plate. So, basically, there are two types of circular machines distinguished by the rotation of the machine. o CAM box revolving machine o Cylinder revolving machine If the CAM plates are moving across the needle butts, the needle bed or the cylinder will be stationary keeping the needle butts in place while the CAM box carries the CAM plates, yarn feeders with their yarn packages are all rotating around the machine. This type of machine is called CAM box revolving machine. On the other hand, if the needle butts are moving across the CAM plates, the CAM boxes will be stationary keeping the cam plates in place. Prepared By: Engr. Shakeel Ahmad Paracha Page 18 of 19 Textile Institute of Pakistan, Karachi. TEXT302 (Knitting Technology) The needle bed will then have to move across the CAM boxes with the needle butts in the needle tricks. For a circular machine, the needle bed is cylinder and then it rotates and that will be the only moving part with the CAM boxes, yarn feeders and yarn packages all stationary. This type of machine is called cylinder revolving machine. It would be clear that cylinder revolving machine is simpler in construction and consumes less power than CAM box revolving machine since there are less moving components. As a matter of fact, most of the circular machines are cylinder revolving type. Only those machines such as the garment length machines are CAM box revolving because of their complexity. Those are machines with 6-18 feeds producing complex knitting structures which cannot be accomplished if the machine is cylinder revolving. Knitting Action of Circular Knitting Machine Following steps are performed during knitting action of the rib fabrics on the circular machine. 1. Clearing (a): In clearing position, the cylinder and dial needles move out to clear the plain and rib loops formed in the previous cycle. 2. Yarn feeding (b): The needles start their return moment and are withdrawn into their tricks so that the old loops are covered by the open latches and the new yarn is fed into the open hooks. 3. Knocking-over (c & d): The dial needle has retracted before the cylinder needle and is in the process of knocking-over the old loop. The needles are withdrawn into their tricks so that the old loops are knocked over and the new loops are drawn through them. Prepared By: Engr. Shakeel Ahmad Paracha Page 19 of 19