Packaging Materials PDF
Document Details
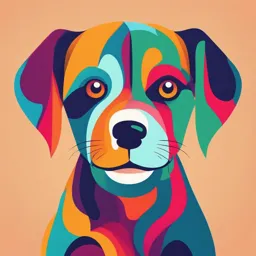
Uploaded by ThriftyCliff
Universiti Malaysia Terengganu
Tags
Related
- U12 Acondicionamiento y Dispensación PDF
- Food Packaging PDF
- Sesión de Aprendizaje 12: Especificaciones del Envasado de Fórmulas Magistrales y Preparados Oficiales PDF
- Fundamentals of Packaging PDF
- Pharmaceutical Packaging (PHARM 131) PDF
- Food Packaging Materials (Chemical Structure & Properties) PDF
Summary
This document provides an overview of different packaging materials, covering their properties, uses, and characteristics. It details various types of plastics and paper, explaining their respective strengths and weaknesses. This document discusses the properties and applications of different materials used for packaging purposes.
Full Transcript
Packaging materials Paper – Cellulose fibers – Strength and mechanical properties depend on fiber sources and processing treatment – Additives, surface coating, laminating – Rigid or semi-rigid – Low-barrier properties, unless modified – Primary or second...
Packaging materials Paper – Cellulose fibers – Strength and mechanical properties depend on fiber sources and processing treatment – Additives, surface coating, laminating – Rigid or semi-rigid – Low-barrier properties, unless modified – Primary or secondary packaging – Examples: paperboard folding cartons, composite paperboard cans (laminated paperboard), distribution cases, etc. Packaging materials Packaging materials, machinery and production processes Key properties of paper and paperboard: – Low-density materials. – Poor barriers to light without coatings or laminations. – Poor barriers to liquids gases and vapors unless they are coated, laminated or wrapped. – Can be grease resistant. – Good stiffness. – Can be creased, folded and glued. – Tear easily. – Not brittle, but not so high in tensile as metal. – Excellent substrates for inexpensive printing. Packaging materials, machinery and production processes Key properties of plastics: – Wide range of barrier properties. – Permeable to gases and vapors to varying degrees. – Low density materials with a wide range of physical and optical properties. – Tensile and tear strengths are variable. – Functional over a wide range of temperature depending of the type of plastics. – Usually have low stiffness. – Flexible and in certain cases can be creased. Packaging materials Plastic packaging – Thermoplastic, i.e. reversibly – LLDPE (linear low density fluid at high temperatures and polyethylene) solid at ambient temperatures Higher tensile and elongation- at-break, higher heat-seal – Characteristics can be modified temperature, higher impact by co-polymerization, blend and puncture resistance than additives, alloying, surface LDPE; similar moisture and treatment gas-barrier properties to LDPE Similar application with LDPE – LDPE (low density polyethylene) Slightly cloudy, high tensile – HDPE (high density strength, good moisture-barrier polyethylene) properties, high gas permeability More translucent, stiffer, Shrink and stretch bundling and higher gas and moisture pallet wrapping; drum and case permeability than LDPE; high liners; packaging of bread, fresh melting point vegetables and fruit, and stable Bottles food products Packaging materials – PP (polypropylene) Excellent water-vapor barrier, – Cellophane: medium gas-barrier, excellent clarity, good heat-seal Transparent, protection against properties. oxygen and aroma, wrinkle Often oriented improved resistance, stiff heat resistance and other Coated moisture proof physical properties – PET (polyethylene terephtalate) Heat-set: packaging of bakery or polyester products, pouches Good gas and water vapor Non-heat-set: transparent, properties, very high tensile and moisture barrier enhance impact strengths, fair aesthetic appeal temperature resistance Coating, vacuum metallization Properties can be improved with improve desirable properties coating or metallization – PVC (polyvinyl chloride) Soft drink bottles Film: transparent, soft, high gas Vacuum-metallized films: pouch permeation, low water-vapor packaging for wine, syrup, bulk transmission tomato, fruit products Wrapping of fresh red meat, poultry, vegetables Packaging materials – Nylon (polyamide) – Polystyrene Good oxygen barrier, tough, Blended with gas low density, thermoformable, fair moisture opaque labels barrier, high melting point, Thermoformed into trays chemical resistance, abrasion Film: clear, easily resistance thermoformable Often laminated or coated to improve heat seal-ability and – Coextruded films barrier properties Improved properties Pouches, external layer for E.g. LLDPE and EVA for aluminum foil packaging of frozen vegetables – PVDC (polyvinylidene chloride) and fruits Commercial: “Saran” – EVOH (ethylene vinyl alcohol) High oxygen, fat, aroma, and High oxygen barrier, but water-vapor resistance sensitive to moisture As high-barrier component in Used as oxygen-barrier layer lamination of aluminum foil – Polycarbonate Rarely used alone due to Returnable, reusable bottles difficulty in heat sealing Differences between HDPE, LDPE, and LLDPE Polyvinyl chloride (PVC) Clear, amorphous. Used mostly for films and containers. Often added with plasticizers (organic liquids with low volatility) - wide properties -Plasticized PVC films: limp, tacky (slightly sticky), stretchable commonly used for packaging of fresh meat and fresh produce. Concerns: risk of migration of plasticizers in plasticized PVC ‘cling’ film. -Unplasticized PVC sheet: rigid; often thermoformed to produce inserts for snacks e.g. chocolate and biscuits. PVC bottles: better clarity, oil resistance, and barrier properties than HDPE bottles, but poor thermal processing stability (thus, limits its use as bottles) and draws environmental concerns due to the chlorine content. Polypropylene (PP) Linear, crystalline, has the lowest density among all major plastics (0.9). PP has higher tensile strength, stiffness and hardness > PE higher melting temperature (1650C) more suitable for hot filling and retorting applications. Mostly used as films. – Oriented PP film (OPP): improved strength, stiffness and gas barrier, but not heat sealable. – Unoriented film: excellent clarity, good dimensional stability, good heat-strength. – Orientations can be achieved by stretching the film either uniaxially or biaxially during the film forming process. Other uses: containers and closures. Polystyrene (PS) Amorphous polymer excellent clarity. – PS films is often used as windows in paperboard boxes to display products that do not require a good gas barrier (e.g. windows on a box of baked goods). Solid PS: clear, low gas barrier, hard, low impact strength. Relatively low melting point (880C) it can be readily thermoformed or injection molded to make food containers, cups, closures, dishwares. Expanded polystyrene (EPS): formed by addition of foaming agents during extrusion process used to make cups, bowls, plates, meat trays, clamshell containers, egg cartons, as well as lightweight protective or thermal insulation packaging materials for shipping. – Concern: instant noodles cup risks of migration of styrene dimers and trimers (suspected as possible endocrine disorder materials) due to hot water + microwave applications. Polystyrene (PS) High Impact Polystyrene (HIPS): immiscible blend of polystyrene, polybutadiene, and grafted polystyrene-polybutadiene copolymer compared to PS, HIPS is more resilient and impact resistant due to the presence of polybutadiene. Polyvinylidene chloride (PVDC) Trade name: Saran. Copolymer of vinylidene chloride (85-90%) and vinyl chloride. Excellent oxygen and moisture barriers. Used in films, containers, coatings. – PVDC films have good clarity and grease/oil resistance. – Monolayer PVDC films: household wraps. Often coextruded or laminated with other lower cost polymers (e.g. OPP and PET) to form multilayer films or sheets. – Multilayer films: used to package food that require good oxygen barrier. – Multilayer sheets: often thermoformed into semi-rigid containers. PVDC films coextruded with polyolefins: used as shrinkable films for tightening meat and cheese products. In the form of latex: used for coating paper, film, cellophane better oxygen and moisture barrier, grease resistance, and heat sealability. More costly than most other commonly used food packaging. Has environmental concerns. Ethylene vinyl alcohol copolymer (EVOH) Crystalline copolymer of ethylene (27 – 48%) and vinyl alcohol properties are highly dependent on the ratio of the comonomers. Exceptional high oxygen barrier (even compared to PVDC) oxygen barrier increases with decreasing ethylene concentration and decreasing relative humidity. It also has good resistance to hydrocarbons and organic solvents. Mostly used as an oxygen barrier layer in multilayer structure, either laminated or coextruded. – The multilayer structures are used as films or containers for packaging oxygen sensitive foods. – Example: PP/adhesive/EVOH/adhesive/PP PP for strength and moisture barrier, EVOH for oxygen barrier suitable for hot filling and retorting applications. Most expensive of all commonly used packaging polymers. Ionomer Contains small but significant portion of ionic units. Example of trade name: Surlyn – Chemical structure: Nonpolar ethylene groups Polar methacrylic acid group Carboxylate ionic pairs – Good sealing performance, good formability, good clarity, oil/grease resistant, high hot draw strength. Good hot draw strength allows faster packaging line speeds & reduces packaging failures. The ionic crosslink is reversible once heated, the forces of ionic crosslink are diminished polymer chains are free to move. Ethylene vinyl acetate (EVA) copolymer Long chains of ethylene hydrocarbons with acetate groups randomly distributed along the chains. Used as heat seal layers for snacks and cheese, bags for ice and frozen food, lidding sealant and hot melt. – High versatility in hot-melt formulations EVA-based hot-melts: packaging, bookbinding, label sticking, glue sticks. EVA resins: packaging film, heavy duty bags, extrusion coating, wire and cable jacketing, hot melt adhesives, cross-linked foam. May be used as an extrudable adhesive resin or sealing layer for lidding applications to PE, PP, PET and PS. Polyamides (Nylons) Has amide groups [-CO-NH-] in the backbone chain. Most common: nylon 6,6 and nylon 6 – Good gas barrier, puncture resistance, heat resistance – Nylon 6: synthesized using monomer caprolactam (C6H11NO) with 6 carbon atoms. – Nylon 6,6: synthesized using adipic acid (C6H10O4) and hexamethylene diamine (C6H16N2), which each has 6 carbon atoms. Polycarbonate (PC) Amorphous thermoplastics It can be injection-molded, blow- molded, and thermoformed. Good replacement of glass (clear & tough, but lighter than glass). It can withstand temperature above 2000C. Usage: 5-gal reusable water bottles (tough and clear). Concerns: possible migration of bisphenol A (a monomer for PC; suspected endocrine disruptor) negligible for general adults. http://thestar.com.my/news/story.asp?file =/2012/3/1/nation/10834126&sec=nat ion Styrene butadiene (SB) SB co-polymer: tough, transparent, high-gloss surface finish, relatively low density ( gives a 20-30% yield advantage over other clear resins). SB blown film: high permeability to water vapour and gases ( suitable to pack fresh produce), heat sealable, good crease retention ( suitable for twist wrapping sugar confectionary). Injection-molded containers with an integral locking closure have a flexible hinge (similar to PP). It can also be made into thermoformable sheet, injection and blow molded bottles and other containers with impact resistance and glass-like clarity. Trade name: K-resin (in the USA). Acrylonitrile butadiene styrene (ABS) Co-polymer of acrylonitrile, butadiene, and styrene properties can be varied by altering the proportions of the 3 monomer components. Tough, good impact strength, good tensile strength, good flexing properties. Either translucent or opaque. Thermoformable and can be molded. Major use: large shipping and storage containers (tote boxes); thin-walled margarine tubs and lids. Polymethyl pentene Co-polymer of methyl pentene. Trade name: TPX. Low density (0.83), clear, heat resistant (can be used up to 200oC, since its crystalline melting point starts at 240oC), good chemical resistance, excellent transparency and gloss. Main use: trays, extrusion coating on paperboard for use in baking applications in the form of cartons and trays for bread, cakes and other cook-in-pack foods (it.s dual ovenable, so it may be heated in microwave and radiation ovens). High nitrile polymers (HNP) Co-polymers of acrylonitrile; used in the manufacture of other plastics (the nitrile component gives very good gas and odor barrier properties ( good flavor and aroma protection) as well as good chemical resistance). Trade name: Barex – Clear, tough, rigid material with very good gas barrier and chemical resistance. – Used as the inner layer in blow-molded bottles co-extruded with HDPE. – Barex films can be co-extruded as film and sheet or laminated with PE, PP and aluminum foil for flexible packaging. Fluoropolymers = fluoroplastics High performance polymers. Related to ethylene where some or all of the hydrogen atoms are replaced by fluorine. Trade names: Aclar and Neoflon. Highest water vapor barrier, very good gas barrier, high resistance to most chemicals at A tetra fluoroethylene monomer and low temperatures. Available as film or sheet. polytetrafluoroethylene polymer – Transparent; heat sealable; can be laminated, thermoformed, metalized and sterilized. – Suitable replacement for aluminum foil. Relatively expensive only used for blister packs for pharmaceutical tables, laminated with PVC. Polytetrafluoroethylene (PTFE) (trade name: Teflon): high melting point, inert, waxy used as tape and coatings on packaging machines to reduce adhesion and friction where they could be problems. Polyethylene naphthalene dicarboxylate (PEN) Relatively new. A condensation polymer of dimethyl naphthalene dicarboxylate (DNC) and ethylene glycol. Improved gas and water vapour barrier and strength properties compared to PET. UV resistant and has higher temperature resistance compared to PET. It can be made into film and blow moulded for bottles. Available as either a monopolymer PEN, a copolymer with PET, or a PET/PEN blend. Suggested applications: one-trip beer/soft drinks bottles, returnable/refillable beer/mineral water bottles, sterilisable baby feeding bottles, hot fill applications, sports drinks, juices and dehydrated food products in flexible packaging. More expensive than PET limit its applications industry prefer to use it only if it can be returned by costumers. PEN films can be vacuum metallised or coated with Al/Si oxides.