Knitting Needles PDF
Document Details
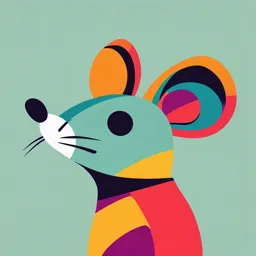
Uploaded by SimplestSaxhorn
Engr. Shakeel Ahmad Paracha
Tags
Summary
This document provides detailed information about knitting needles, including different types such as bearded, latch, and compound needles. It explains the characteristics of each type, including their parts, manufacturing process, and knitting actions. The document also covers the different types of knitting machines and their respective knitting actions.
Full Transcript
Textile Institute of Pakistan, Karachi. TEXT302 (Knitting Technology) Heart of Knitting In all knitting machines, the main element for intermeshing of loop is ‘the needle’. Needle is the heart of any knitting machine. The quality of the knitted fabri...
Textile Institute of Pakistan, Karachi. TEXT302 (Knitting Technology) Heart of Knitting In all knitting machines, the main element for intermeshing of loop is ‘the needle’. Needle is the heart of any knitting machine. The quality of the knitted fabric is largely dependent on the effectiveness and accuracy of the loop, which in turn largely depends on the needle. Small variations in the needle manufacture can lead to irregular fabric. The surface of needles should be highly polished allowing the yarn and the loop to slide free. The needle must have high strength and toughness to give durability. A typical needle must perform several million knitting actions without fault. There are three types of needles. These are: o Bearded needle o Latch needle o Compound needle Types of Needles The stages of knitting cycle slightly varies for all these types of needles. All needles must have some method of closing and opening its hook in order to catch and retain the yarn loop and to perform intermeshing. The latch needle is primarily used in weft knitting, and the other two (bearded and compound) are used for warp knitting. A coarse (large and thick) needle usually knits with a coarse yarn (large hook), whereas a fine (small and thin) needle usually knits with fine yarn (small hook). Bearded Needle These needles were the first ever type used in a knitting machine. The bearded needle was used by William Lee in 1589 in his stocking frame to enable a single needle to undertake the tasks achieved by hand knitters with two needles. Bearded Needle Parts The bearded needle consists of five main parts as follows: o Head: The point at which the stem is bent to form the hook, it helps to draw the new loop through the old loop. o Beard: Which is the curved downwards continuation of the hook that is used to separate the trapped new loop inside from the old loop as it slides off the needle beard. Prepared By: Engr. Shakeel Ahmad Paracha Page 1 of 7 Textile Institute of Pakistan, Karachi. TEXT302 (Knitting Technology) o Groove or eye: Cut in the stem to receive the pointed tip of the beard when it is pressed, thus enclosing the new loop. o Shaft or stem: Used with the jack sinkers to form new loops. o Shank: Which may be bent for individual location in the machine or cast with others in a metal ‘lead’. The shank is used to attach the needle to the frame. Bearded Needle Characteristics Bearded needle characteristics are as follows: o It is the cheapest and simplest type to manufacture as it is made from a single piece of metal. o The knitting section occupies a considerable amount of space, thus limiting productivity. o Depending upon the machine type, the needles can be set vertically or horizontally. o The needle has the disadvantage of requiring a pressing edge to close the bearded hook and enclose the new loop. o The presser may be in the form of a bar, blade, verge or wheel, with either the presser or the needle remaining stationary while the other element moves towards it. o In the case of warp knitting it is a presser bar. o Finer in cross section, therefore, more needles in unit space. Hence, finer gauge (60 needles / inch) can be achieved. o High wear and tear and can break easily the needle. o No possibility of fluff / lint accumulation on the needle. o Another feature of bearded needle knitting is that individual loop formation has to be achieved by a loop forming element. This leads to a more complicated knitting action but also provides for a more gentle and careful loop formation. o The majority of modern high speed warp knitting machines now use compound needles rather than bearded needles. o Strain on the yarn is less. o Bearded needles are prone to produce needle marks. Bearded Needle Knitting Action Figure shows the position of a bearded needle as it passes through the cam system, completing one knitting cycle or course as it moves up and in its trick or slot. 1. The rest position: The needle is in the (so-called) rest position, with the previously formed loop (a) held on its stem and covered by the beard. 2. Clearing height: The loop is cleared from the needle beard to a lower position on the needle stem. 3. Yarn feeding position: The new yarn (b) is fed to the needle beard at a higher position on the needle stem than the position of the previous (‘old’) loop. 4. Loop formation: The yarn is formed into a ‘new’ loop. 5. Beard closing: The beard is closed, enclosing the new loop and excluding and landing the old loop onto the outside of the closed beard. Prepared By: Engr. Shakeel Ahmad Paracha Page 2 of 7 Textile Institute of Pakistan, Karachi. TEXT302 (Knitting Technology) 6. Cast-off or knock-over: The new loop (b) is drawn through the head of the old loop (a). Simultaneously the old loop slides off the closed beard of the needle and is cast-off or knocked-over. 7. Loop length drawn: The old loop now hangs from the feet of the fully formed new loop and the knitting cycle starts again. Latch Needle Matthew Townsend, a Leicester hosier, patented the latch needle in 1849, and compared to the bearded needle, which evolved some 260 years earlier. Latch Needle Parts The latch needle consists of nine main parts as follows: o Hook: Which draws and retains the new loop. o Slot or saw cut: Which receives the latch-blade (not illustrated). o Cheeks or slot walls: Which are either punched or riveted to fulcrum the latch-blade (not illustrated). o Rivet: Which may be plain or threaded. This has been dispensed with on most plate metal needles, by pinching in the slot walls to retain the latch blade. o Latch-blade: Which locates the latch in the needle. o Latch spoon: Which is an extension of the blade, and bridges the gap between the hook and the stem covering the hook when closed. o Stem: Which carries the loop in the clearing or rest position. o Butt: Which enables the movement of the needle to be controlled by a cam mechanism. A track raises and lowers the needle. o Tail: Which is an extension below the butt, giving additional support to the needle and keeping the needle in its trick. Latch Needle Characteristics Latch needle characteristics are as follows: o The latch needle was a more expensive and intricate needle to manufacture than the bearded needle because of the assembly of the needle and latch. Prepared By: Engr. Shakeel Ahmad Paracha Page 3 of 7 Textile Institute of Pakistan, Karachi. TEXT302 (Knitting Technology) o It is self-acting or loop-controlled, and is sometimes termed the ‘automatic’ needle. o Precisely manufactured latch needles are widely used to produce high-quality fabrics. o Most widely used in weft knitting. o It can work at any angle. o It was more prone to making needle lines as it slides in its trick, particularly if the latch was damaged or there was dirt in the trick. o Needle depth determines the loop length. o Variation of the height of reciprocating action produces knit, tuck or miss stitch. o It is ideally suited for use with computer-controlled electronic selection devices. o It makes a longer stroke in the cycle of knitting. o Latch needles are thick and rigid. o The latch needle takes a longer time to knit a loop and hence, the knitting machine is generally found slower. o Needle deflection is difficult. o It imposes a certain strain on the yarn. o There is also a possibility of fluff or lint accumulation on the latch due to rubbing action of the yarn on the needle. Latch Needle Knitting Action Figure shows the position of latch needle as it passes through the cam system, completing one knitting cycle / course as it moves up and in its trick or slot. 1. The rest position: The head of the needle hook is level with the top of the verge of the trick. The loop formed at the previous feeder is in the closed hook. It is prevented from rising as the needle rises, by holding-down sinkers or web holders that move forward between the needles to hold down the sinker loops. 2. Latch opening: As the needle butt passes up the incline of the clearing cam, the old loop, which is held down by the sinker, slides inside the hook and contacts the latch, turning and opening it. 3. Clearing height: When the needle reaches the top of the cam, the old loop is cleared from the hook and latch spoon on to the stem. At this point the feeder guide plate acts as a guard to prevent the latch from closing the empty hook. 4. Yarn feeding and latch closing: The needle starts to descend the stitch cam so that its latch is below the verge, with the old loop moving under it. At this point the new yarn is fed through a hole in the feeder guide to the descending needle hook, as there is no danger of the yarn being fed below the latch. The old loop contacts the underside of the latch, causing it to close on to the hook. 5. Knocking-over and loop length formation: As the head of the needle descends below the top of the trick, the old loop slides off the needle and the new loop is drawn through it. The continued descent of the needle draws the loop length, which is Prepared By: Engr. Shakeel Ahmad Paracha Page 4 of 7 Textile Institute of Pakistan, Karachi. TEXT302 (Knitting Technology) approximately twice the distance the head of the needle descends, below the surface of the sinker or trick-plate supporting the sinker loop. The distance is determined by the depth setting of the stitch cam, which can be adjusted. Compound Needle Compound needles were designed by Jeacock of Leicester in 1856. Compound Needle Parts The compound needle consists of following main parts: o It consists of two separately controlled parts; these are - the open hook and the sliding closing element (tongue, latch, piston, and plunger). o Compound needles consist of hallow steel tube of finer gauge in which a hook closing element, which is also a steel tube of fine gauge, is inserted. o The two parts rise and fall as a single unit but at the top of the rise, the hook moves faster to open the hooks and at the start of the fall the hook descends faster to close the hook. o It is easier to drive the hooks and tongues collectively to form two separate bars as in warp knitting; than to move each hook and tongue individually as in weft knitting. Compound Needle Characteristics Compound needle characteristics are as follows: o Two types of compound needle have been employed in warp knitting machines: 1. Pusher type: The open stem “pusher type” or slide needle has a closing wire or tongue that slides externally along a groove on the edge of the flat hook member. This type of compound needle is cheaper, more compact and each of the two parts can be replaced separately. 2. Tubular pipe: The tubular pipe needle has its tongue sliding inside the tube of the open hook. Pusher type Tubular pipe Prepared By: Engr. Shakeel Ahmad Paracha Page 5 of 7 Textile Institute of Pakistan, Karachi. TEXT302 (Knitting Technology) o Compound needle is most popular in warp knitting machines. o The compound needle is expensive to manufacture. o Compound needle offers a much shorter, smoother and simpler knitting action in comparison to other needles. o Both parts of compound needle have a straight moment, thus the knitting speed can be increased. o Strain is not put on the yarn. o The slim construction and short hook of the compound needle make it particularly suitable for producing fine warp knitted structures at high speed. o It can knit chain stitches without the loops rising up the needles, and its sturdy construction resists the deflection generated by elastic yarns or thick places in spun yarns. Compound Needle Knitting Action Figure shows the position of a compound needle as it is completing one knitting cycle or wale as it moves. 1. The yarn laying: First of all the guide bars feed the yarn to the hook. 2. Bridge formation: The tongue closes the hook to catch the yarn. 3. Link-up: Then the needle action completes interlooping. Needles Orientation Needles in the knitting machine are usually oriented either vertically, horizontally, or at 45º. Needles are held in the position by the needle beds - pieces of metal into which slots or grooves have been cut. The beds can be rectangular or circular. Needles at 90º on cylinder (vertical) and dial (horizontal) Prepared By: Engr. Shakeel Ahmad Paracha Page 6 of 7 Textile Institute of Pakistan, Karachi. TEXT302 (Knitting Technology) Needles at rectangular or flat bed Needles at 45º on V-bed knitting machine Comparison of Needles Bearded Needle Latch Needle Required another element to close the Self-acting needle. hook. Less expensive. More expensive. Beard needles are thin and flexible. Latch needles are thick and rigid. Usually mounted on finer gauge. Usually mounted on coarser gauge. It wears and breaks easily. Strong in nature. No strain on yarn. Imposes certain strain on yarn. It makes a shorter stroke in the knitting It makes a longer stroke in the knitting cycle. cycle. Stitches are tight and minimum loop Stitches are loose. robbing. Due to rubbing, fly and fluff generation No fly and fluff generation. is high. Time required to knit the loop is less. Takes longer time to knit the loop. The speed of the machine is high. The speed of the machine is less. Latch Needle Compound Needle Consist of two separately-controlled Self-acting needle. parts. Less expensive. Very expensive. Preferred for Weft Knitting. Preferred for Warp Knitting. Short, smooth, simple harmonic Vibration is more. movement, so there is less vibration. Yarn is under stress. No stress on yarn. The vertical clearing height is not so The vertical clearing height is very good. good. Latch needles produces the long & The needle can knit tight, uniform narrow loops. stitches that tend to be rounder. Because of its slim construction and Latch needles are relatively thick. short hook fine warp knitted are possible. Speed is relatively less. Can work at high speed. Prepared By: Engr. Shakeel Ahmad Paracha Page 7 of 7