On-Load Tap Changer Type M and MS Inspection Instructions PDF
Document Details
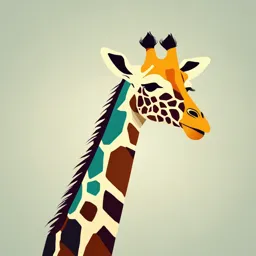
Uploaded by BestSellingBeige
null
Tags
Related
- On-Load Tap Changer Type M & MS Inspection Instructions PDF
- On-Load Tap Changer Type M and MS Inspection Instructions PDF
- On-Load Tap Changer Type M ∆ Inspection Instructions PDF
- On-Load Tap Changer Type T Inspection Instructions PDF
- On-Load Tap Changer Type V Inspection Instructions PDF
- On-Load Tap Changer Type H Inspection Instructions PDF
Summary
This document provides inspection instructions for on-load tap changers (types M & MS). It details the procedures, necessary equipment, safety precautions, and operational principles for proper operation and maintenance. The document is intended for professional use.
Full Transcript
On-Load Tap Changer Type M & MS Inspection Instructions M R REINHAUSEN GERMANY MASCHINENFABRIK...
On-Load Tap Changer Type M & MS Inspection Instructions M R REINHAUSEN GERMANY MASCHINENFABRIK MR REINHAUSEN IA 38/01 en — 0395/2000 Maschinenfabrik Reinhausen GmbH Printed in Germany Postfach 12 03 60 93025 Regensburg Phone +49-941-4090-0 Fax +49-941-4090-111 Telex 6 5 8 8 1 ON-LOAD TAP CHANGER TYPE M & MS Inspection Instructions No. 38/01 Contents Page T=4= LIS C1 - 1 HOOP 3 1.1 Operational principle of the on-load tap changer 1.2 Designation of on-load tap changer models 1.3 Principal parts of the on-load tap changer 1.4 Inspection intervals 1.5 Summary of inspection work 2. Preparation cco iconic serene esses sarees ss anaes 7 241 Necessary equipment for inspection 2.2 Safety precautions 2.3 Operating position when withdrawing the diverter switch unit Withdrawing the diverter switch unit..........ccocvovveiiiiniiiiiiiinnnnccenn 8 Cleaning the oil compartment a n d diverter switch unit.........cooonennnennne Inspection of the diverter SWitch Unit..........ccormereeereciiiiiiiirnnvssennes 11 5.1 Withdrawal position 5.2 Measuring the transition resistors 5.3 Removing the contact shells 5.4 Removing the arc chutes 5.5 Cleaning the diverter switch unit 5.6 Cleaning the diverter switch insulating drive shaft 5.7 Contact wear of main switching contacts and transition contacts 5.8 Determinatingcontact wear Please note: 6. Replacement of the diverter switch arcing contacts Drawings and illustrations con- A N A COMACT DIAIAS.euviiiiiiieiieeeeereecreeetsircesseseseeeessssssnsssasssesssessassanneeens 14 tained herein m a y differ i n detail 6.1 Diverter arcing switch contacts from the tap changer equipment 62 Contact braids delivered. They are for reference only and 7. Reattachment of the contact shells..c..coaeerimernieeece 17 are subject to c h a n g e without.. a. notice. ) 9 8. Diverter switch unit with support cylinder.......ccccecoriiirrecnnrircenene 18 9. Reinstallation of the diverter switch unit........cocceeoevriririiiercirecrrrrececeanns 19 Contents 10. OQil filling 11. Further checks 11.1 Drive shafts 11.2 Operational tests of motor drive and tap changer 11.3 Protective relay RS 2001 114 Voltage regulator 12. Appendix 12.1 Coupling of tap changer and motor drive 122 Inspection tools 12.3 Lifting device 124 Spare parts list 125 Parts of the diverter switch unit 126 Adjustment plans 1. GENERAL 1.1 Operational principle of the on-load tap changer (fig. 1) A tap-change operation begins with the tap selector preselecting the de- sired tap on the transformer winding. The diverter switch transfers the current from the tap in service to the preselected tap. During this quick change-over, ohmic resistors are inserted in the circuit to ensure no-break transfer of the current. Motor drive unit Tap selector Diverter s w i t c h Time in seconds 0,05 Circuit diagram A,B - main contacts Rah Ro 1" r a,b - main switching :. contacts wae oA fp aq, by — transition contacts hu Contact movement Fig. 1 Tap-change operational sequence 1.2 Designation of on-load tap changer models (fig. 2) -LOA Every tap changer type is available in a number of different models. M | 501-123 /B -10191W These designs vary according to: number of poles, max. rated through- current, insulation to ground, tap Type | Basic circult diagram selector size, and basic circuit diagram. Number of The designation incorporates all these poles Tap selector size characteristics and permits easy Max. rated through- identification of the tap changer. current in amperes — and additional indication The basic circuit diagram code in of model the model designation identifies: Highes voltage for number of tap selector contacts, equipment Up, - number of operating positions, insulation to ground number of mid-positions, and type of change-over selector. A I Example in fig. 2: On-load tap changer type M 10 19 single-pole, max. rated through- current 500 A, insulation to ground according to Uy, = 123 kV, tap / Pitch of Max. number of NN Mid-p ositions Change-over selector size B, basic circuit diagram tap selector service positions selector contact circle 0 code 10 19 1 W meaning: 10 1 contacts, 19 operating positions, with 3 Coarse Reversing one mid-position, change-over Change-over tap selector switch selector used as reversing switch. selector without with G w 1.3 Principal parts of the on-load 10 10 06 19 *) No designation without 12 12 11 23 change-over selector tap changer (fig. 3) 14 14 13 27 16 16 15 31 The principal parts of the on-load tap 18 18 17 35 changer are: - the tap changer head, - the diverter switch unit, - the diverter switch oil compartment and - the tap selector Fig. 2 Designation of tap changer model and basic circuit diagram Those parts of the tap changer which are subject to inspection are marked in colour in fig. 3. Fig.3 Principal parts of the on-load tap changer 13 Tap changer head gasket Diverter switch oil compartment 14 Position indicator Bottom of oil compartment 15 Inspection glass Grading rings 16 Drive shaft for position indicator Terminal of diverter switch oil compartment Suction pipe 21 Tap changer head Tap selector support 22 Cover bolt Tap selector gear 23 Head cover gasket Fine tap selector 24 Tap changer head cover Change-over selector 25 Upper gear unit with drive shaft 25a Tap selector terminal 26 Pipe connection R for protective relay 27 Pipe connection S for suction pipe Diverter switch unit 28 Pipe connection Q for return pipe Support bar (with oil filter unit only) Support plate 29a Bleeder valve of tap changer head cover Fixing screw 29b Bleeder facility for transformer oil Lifting lug 29¢ Bleeder screw for suction pipe Transition resistors 35 34 CL o—] 32 32 4— a 42 a2 43 : | 4 —aa 43 | | | _— J 45 Centric upper Eccentric upper gear unit gear unit 1.4 Inspection intervals The insulating oils in the transformer so that, in case of need, recommen- IMPORTANT: The tap changing are to be monitored by the operator dations for the next inspection can b e according to the appropriate given. equipment must b e inspected at regular intervals t o maintain a high directions. WARNING: Disregard of the level of operating reliability. If inspections are not carried out by inspection intervals puts at a risk The inspection can be carried out by MR personnel, we request a report the trouble-free operation of tap to supplement our inspection data, changer and transformer. qualified and MR-trained personnel usually within one day, provided it is well prepared and organized. We strongly recommend to have in- Standard values for oil testing according to CIGRE report 12-13 (1982) apply to spections carried out by our Technical transformer oil at service temperature: Service. This guarantees a professio- On-load tap changer Water content”) Dielectric strength**) nal performance of the inspection and ensures the updating of specific com- MS iif 300, M ill 350, < 40 ppm > 30 kV/2.5 m m ponents to the latest operational state. M III 500, M l i 600 We recommend requesting necessary M S 1301, M1351... MI11800 < 30 ppm > 4 0 kV/2.5 m m spare parts for preparation of an in- MS 11302, M 1 3 5 2... M I 602 < 30 ppm > 40 kV/2.5 mm spection which will not be carried out by MR personnel (please indicate tap *) measured according to Karl-Fischer method based on IEC Publication 814 changer number and number of tap **) measured according to DIN VDE 0370 Teil 1 change operations). The numbers of tap change opera- On-load Transformer Number of tap change operations®) tions determining the inspection inter- tap changer rated current without oil filter with oil filter vals indicated in table I are figures based o n experience with u s e of usual 100,000 150,000 MS [11 300 upto 300A oil qualities. M ill 350 upto 350A 100,000 150,000 The tap selector of the on-load tap M Ill 500 upto 350A 100,000 150,000 changer is generally maintenance- 500A 80,000 150,000 upto free. I n special cases, however, for M i l 600 upto 350A 100,000 150,000 example in industrial transformers upto 600A 80,000 150,000 where high numbers of tap change operations are to b e expected, our MS1301/MS 11302 upto 300A 100,000 150,000 technical service department must M1351 / M 11352 upto 350A 100,000 150,000 b e contacted after about 1,000,000 M1501 / M Ii 502 upto 500A 100,000 150,000 operations. M1601 / M I l 602 upto 600A 100,000 150,000 T h e diverter switch unit of the tap M1802 upto 500A 100,000 150,000 changer has to be replaced by a new upto 800A 80,000 150,000 one after about 800,000 operations M11200 upto 800A 80,000 150,000 the latest. upto 1200 A 70,000 140,000 If the number of operations per year M 11500 up to 1200 A 70,000 140,000 exceeds 15,000, w e recommend t h e u p t o 1500 A 60,000 120,000 use of our stationary oil filter unit M 1 1800 up to 1500 A 60,000 120,000 type 51 with a paper filter insert u p to 1800 A 50,000 100,000 (see Operating Instructions No. 18). If the the highest voltage for equipment Table 1 Inspection intervals Un, of any tap changer type M exceeds Note: *)If Ur, 2245 kV at the tap changer the indicated numbers of tap change 245 kV, the use of a stationary oil filter operations must be halved. unit type 51 with a combined filter cartrige is obligatory. Filtering of the switching oil allows the Regardless of the number of tap change operations listed in table 1, inspection inspection intervals to be extended. must be carried out after 6 to 7 years. Continuous oil filtering also increases In case of on-load tap changers with insulation to ground according to the mechanical life of the diverter = Up, 245 kV (autotransformer or regulation at the line-end of the transformer switch by immediately removing most winding), the first inspection must be performed after 20,000 switching opera- of the abrasive particles responsible tions o r after 2 years of service respectively, whichever comes first. for mechanical wear. Further inspections are required every 4 years. 1.5 Summary of inspection work 2. PREPARATION The working area should be marked clearly. A typical inspection includes the 2.1 Necessary equipment Start with inspection only after all following work: — empty vessels for dirty oil, these safety precautions have been — Withdrawing and reinstalling the carried out. Disregarding them the necessary quantity of diverter switch unit endangers lives. new transformer oil for — Cleaning the diverter switch oil cleaning and oil change; compartment and diverter switch kV 36 725 123 170 245 2.3 Operating position when with- unit and, where necessary, the drawing the diverter switch unit tap changer oil conservator tank. Litres 125 130 150 170 190 The diverter switch unit can be with- — Changing the switching oil Table l l Qil filling quantity in litres drawn in any operating position. — Checking the diverter switch oil Take note of the operating position compartment and diverter switch — an oil pump for draining when withdrawing the unit. unit and refilling; However, we recommend on principle — Determining the contact wear — adrip pan; to withdraw the diverter switch in the adjustment position which is marked — Measuring the transition resistors — miscellaneous brushes and by an arrow on the position indicating absorbent, non-fuzzing rags disc of the motor drive unit (fig. 4). — Checking the protective relay, for cleaning; drive shaft, motor drive unit and, where present, the oil filter unit —- a work table; CAUTION: Do not operate the mo- and voltage regulator. t o r drive unit while the tap changer — a lifting device: either crane or MR i s uncoupled, either manually o r The diverter switch unit should not be liting device (see appendix, electrically. To prevent electrical exposed to air longer than necessary section 11.3), weight of diverter operation b y remote control, it i s (at max. for 10 hours). switch unit max. 80 kg, required good safety practice t o isolate the lifting force is max. 1300 N; motor drive unit b y tripping the Inspection work should not be inter- rupted. Care and cleanliness should motor protec-tive switch. kV 36 7 2 5 123 170 245 be observed. mm 830 870 1000 113 1230 WARNING: Inspection must be carried out b y qualified, skilled Table li Withdrawal height in mm personnel only. The instructions should b e followed strictly. — inspection tools (see appendix, section 12.2); Damage which i s found during inspection needs immediate con- — spare parts (see appendix, tact with MR for assistance. D o not section 12.4). put the tap changer i n service until Please note: Lock tabs, self-locking the damage has been corrected. screws and nuts should never be used Do not alter o r modify the tap twice and should be replaced during changer equipment without prior reassembly. consulting MR. CAUTION: Always use MR-autho- Improper o r incomplete work car- rized replacement parts. Parts of ried out during inspection can other origin can affect the trouble- affect the trouble-free operation of free operation o f tap changer and tap changer and transformer. transformer. Under certain circumstances this can cause property damage and/or 2.2 Safety precautions personal injury. WARNING: The user of the plant should perform the following safety measures. The transformer must b e switched off, isolated and secured against reclosing. All terminals must b e grounded visibly (by means o f ground cables or ground switches). 3. WITHDRAWAL OF THE DIVERTER SWITCH UNIT (tig. 5) Lowering t h e oil level: Shut the stop valve between oil conservator and tap changer head. Lower the oil level in the tap changer head. To do this, open the bleeder valve in the head cover (remove screw cap M30 / wrench size 36, lift valve tappet by means of a screwdriver) and the drain valve. WARNING: The switching oil o f the tap changer should always b e handled as a flammable liquid. Moreover, explosive gases can accumulate under the tap changer head cover, i n the switching oil or i n the o i l compartment. Therefore, strictly avoid open fire. Use a pumping equipment suitable for flammable liquids. in case of an ail filter plant: open the return pipe sample valve and operate the filter unit, drain about 10 litres of oil from the tap changer head so that 3 2 the support plate is out of the oil (check through the inspection glass in the head cover). Fig. 5 Tap changer head Uncoupling the drive shaft of the upper gear unit: 1 Drive shaft (square tube) 5 — Bleeder valve of head cover Unscrew 6 screws M6 (w.s.10) from 2 — Coupling brackets and bolt 6 — Pipe connection R for protective the coupling. Take care not to lose 3 — Upper gear unit (centric relay coupling bolts, nuts and lock tabs. arrangement) 7 — Pipe connection S with bleeder Normally the drive shaft can be 4 — Tap changer head cover screw for suction pipe moved to one side for clearance. if not, remove the other coupling on the bevel gear from the square tube (screws, nuts and lock tabs as above) until the horizontal drive shaft can be removed. Take off the tap changer head cover (fig. 6a): Unscrew the cover bolts M10 (w.s.17). Take care not to lose spring washers. Remove the cover, take care not to damage the O-ring gasket of the head cover. Please note: These inspection instructions apply analogously to the special design with eccentric arrange- ment of t h e upper gear unit ( f i g. 6b). Disassemble i n the following order: Remove the position indicator disc (7a, 7b). Remove the clip from the shaft end. The coupling pin allows assemby in the correct position only. Take note o f the marks o n t h e tap changer head and the support plate. In the adjustment position the key in the diverter switch drive shaft matches with the triangle mark on the support plate. Undo the screws fixing the support plate. Standard design: 4 screws M8 x 20 (w.s.13), fig. 8a, 8b. Special design for bell-type trans- former cover: 5 studs M8 with nuts (w.s. 13), fig. 9a, 9b. In both cases take care of bolts or nuts and washers. WARNING: Do not remove t h e nuts from thread studs i n the red marked area of the tap changer head. Otherwise the tap changer may fall into t h e transformer tank and cause serious damage to the tap changer and parts of the trans- former. Carefully lift out the diverter switch unit using the lifting lugs (fig.10) and put it on a flat, clean place. 4. CLEANING THE OIL COMPARTMENT, THE OIL CONSERVATOR AND THE DIVERTER SWITCH UNIT Oil compartment, o i l conservator: Drain the oil compartment completely. Open the stop valve between tap changer head and oil conservator. Drain oil from the conservator until clean oil flows. If necessary, flush the oil conservator tank with clean trans- former oil. (2 Cc mrs entric upper gear unit Eccentric upper gear unit Drain the oil compartment, flush with clean oil, and drain again completely (tig.11). Remove the suction pipe (fig.12), flush its inside and outside with transformer oil and reinstall. To be safe, put on the tap changer head cover and secure it with all the cover bolts M10 (w.s.17) while the diverter switch unit is withdrawn. Diverter switch unit (fig.13): Fig. 11 Visually check the outside of the Tap changer head open, inside view diverter switch unit. Clean the of the diverter switch oil compartment diverter switch unit by flushing with clean transformer oil. Suction pipe = Drive shaft for position indicator WN Thoroughly clean the diverter switch after the contact shells have been re- Position indicator gear Coupling of tap selector drive | moved (see section 5.3). Kerosene drain screw DN Please note: In case of diverter Terminal contacts on oil switch unit with a support cylinder instead of the 4 support bars (= new design) refer to section 8. WARNING: To clean t h e diverter switch unit never use other clean- ing liquids than pure transformer oil. Other liquids, e.g. organic solvents o r cleaning petrol are improper. Their use can affect the Fig. 13 trouble-free operation o f tap chan- Diverter switch unit ger and transformer. 1 — Support plate 2 — Support bar 3 -— Insulating drive shaft 4 — Energy accumulator 4a — Pawl 4b — Trip lever 5 — Diverter switch 6 - Transition resistor 10 5. INSPECTION OF THE DIVERTER SWITCH UNIT 5.1 Withdrawal position Before starting the inspection take note of the switched position of the diverter switch (= withdrawal position). Note the position of the trip lever of the spring energy accumulator unit (fig.13) in order to regain this position after reassembly of the diverter switch unit. 5.2 Measuring the transition resistors (fig. 14) Measure the value of each transition resistor. The values are in the order of 0. 3... 3 0 ohms. Measure at the open side of the diverter switch sector between the stationary main switching contacts and transition contacts above and below. For this purpose set the diver- ter switch to the opposite position by means of the operating key (see ap- pendix, section 11.2). Then measure again (fig. 14). To remove the contact shells the Fig. 14 Compare the measured values diverter switch must be set to its mid- Measurement of transition resistors against the indications on the position where the transition contacts on distinct points of the contact shell nameplate. are closed: A 10 percent difference is permis- Release the spring energy accumula- sible. tor and turn the drive shaft by means of the operating key until the wind-up sledge and the cocking sledge have reached a stable position just about in the middle (fig. 15, 16, 17). 5.3 Removing the contact shells Remove and reinstall the contact shells consecutively on one diverter switch sector after the other. 11 Undo the fixing screws of the contact shells of one diverter switch sector: first the 4 outer screws, then the 4 inner screws, in total 8 screws M 6 x 2 0 (w.s.10), see f i g. 1 8 , 1 9 , 20. 54 Removing the arc chutes Withdraw the arc chutes (fig. 21). OLTCs MS 111300... M 1351: see fig. 21a. OLTCs M I I 500... M | 1800: see fig. 21b. The outer arc chutes have split sidewalls and must be refitted in exactly their initial position. 5.5 Cleaning the diverter switch unit The contact shell with transition re- sistors and stationary contact system must be cleaned thoroughly with trans- former oil. Special care should be taken when cleaning insulating parts. Flush all parts with clean oil. Since the contact shells and transition resistors are to be disassembled and reassembled one sector before the next perform cleaning of the diverter switch between these procedures. 5.6 Cleaning the diverter switch insulating drive shaft (to be carried out between or after diverter switch disassembly or reassembly procedure) In case of tubular design of the insu- lating shaft it is also necessary to clean the inside of the shaft (see 21a 21b fig. 22a & 22b). CAUTION: Take care not to drop The inside of the insulating shaft is to To remove the insulating drive shatt, any parts into t h e diverter switch. be cleaned by thoroughly flushing it the 4 support bars with support plate Otherwise the diverter switch can with new transformer oil. have to be detached from the energy block and cause severe damage t o accumulator case. Reassemble i n reverse order t o dis- the tap changer and transformer. assembly. Each support bar is fixed by 2 bolts Therefore, make sure that the M8 x 30 w. s.17, 6 dished washers number of small parts i s complete and self-locking nuts. when disassembling and reinstal- ling. Count them t o b e sure. Operate the spring energy accumu- lator to one side for clearance when unscrewing or inserting bolts. 12 (1) > / Fig. 22a: from 1972 Fig. 22b: from 1979 Fig. 22¢: from 1981 Design of diverter switch insulating drive shaft PLEASE OBSERVE: Assemble the diverter switch insulating shaft (design according to fig. 22b & 22¢) on the drive shaft with the shaft key pointing to the eccentric. Attach the support bars to the energy accumulator, that the triangle marks of support plate (fig. 23) and energy accumulator housing (fig. 24) line up. Install bolts a n d dished washers according to fig. 25, max. torque 22 Nm. Fig. 25 Attachment of support bar 13 5.7 Contact wear of main switching contacts and transition The admissible contact wear of the diverter switch contacts is determined by: Ul 2Pa%a%a! TX XA a) the contact volume (see fig. 26). XX] RKSX X 0. RTS RS ose) —T R I The max. admissible contact wear of bode RR bo%e; XS 939% R 2% > RX e tSoe R KKH the individual contact is 4 mm. be% QA rietooledeletetele ZS , X B E R R AxX LRRRRHKKS Contacts should be replaced if this value is reached or expected to be etree 0 a! R R SR x) ZXIIRIRIAKIRHES reached before the next inspection. 0.0.0.0. 0. AHHH tate’ b) the mechanical tap change 2 %2 29,Sotetas R CIRIIILIRI RR operation sequence (see section 1.1), ®SIRI 9s QD ers shunt contact (A, B), main switching XXS XO tes 2% ZS XX? ATR I N K X 2 X R ny C X> XX RXx 2>oe XPoto 5% contacts (a, b), transition contacts 5S 0%0 TRXTIILRS XX bd 2% ee: CX SSC (at, bt). PREKK 2% B O3X 0%" * If the difference between main PO switching and transition contacts R sl 2 ne! E0RRK] Releel could become greater than certain XXX boo 2 oe;2 RX RRR I L 3X x 0.0 given limits, the correct mechanical B x736 %"a3SXXX 0% 3bo} X XSX ». RARER TRAD switching sequence of the diverter 2Xes I to 9, SR 3X2 Ja%a%5 (03oot 2X X switch is no longer ensured. Unfavourable operating conditions can cause increased contact wear on MS 11300... M 1351 AN transition contacts. S200A > 200A WARNING: Continued operation o f the diverter switch with greatly a,b 051873 051873 differing contact layer thickness o n 017 355" : arcing contacts can lead t o severe a t , b l | 051873 008 859 damage o f tap changer and trans- M I I 5 0 0... M 1 1800 former. a,b 009 859 The max. permissible difference of al, bi 009 859 contact layer thickness between main switching and transition contacts is Note: 2.5... 2.6 mm. If this difference has V for furnace / electrolysis transfor- X=803mm y Z 4mm mer operation only been reached or is expected to be reached before the next inspection, the contacts shall be replaced or Fig. 26 Max. permissible contact wear of stationary and matched to the other contacts by movable contacts x —y = 4 mm, interchanging or milling. new condition x = 8 + 0.3 mm 5.8 Determination of contact wear 6. REPLACEMENT OF THE Replacement of the contact tips of the DIVERTER ARCING stationary and movable contact sys- Measure and note the thickness of CONTACTS AND CONTACT tem is simple (attachment: 1 screw the contact layers on the stationary BRAIDS M6 for each element). Note the and movable main switching and following details: transition contacts by vernier gauge. 6.1 Diverter switch arcing contacts Determine the contact wear by com- paring the difference between new Each diverter switch sector is fitted contact and measured value. with two main switching contacts (a, b) and two transition contacts ( a l , b1). Each of these contacts exists as stationary and a movable contact. Each stationary and movable contact consists of two contact tips. 14 Stationary contacts (see fig. 27, 28) Each contact tip is fixed by one hexagon socket screw M6 x 16 (w.s. 4 or 5), max. torque 9 Nm, locked by centre-punching the groove of the screw head. Movable contacts (see fig. 29, 30, 31) Each contact element is fixed by one hex head screw M6 x 16 (w.s. 10), 2 dished washers, max. torque 9 N m , locked by lock tab. OLTC MS Ill 300, M Ill 350, MS 1301, M1351: Before undoing contact tips remove the contact braids on top and bottom (see section 6.2). Note: I n case of through-current exceeding 200 A contacts of tungsten-copper are used for the transition contacts ( a t , b1). O L T CM HI 500, M111 600, M I 501, M1601, M1802, M11200, M I 1500, M | 1800: Before undoing the contact tips re- move the contact braids on top (see 6.2 Contact braids section 6.2). The contact braids connect the main As a precaution, the contact braids switching contacts and transition con- should be replaced after 250,000 tacts of the movable contact system to operations regardless of replacement the slide contact (= output terminal) of of diverter switch contacts. the diverter switch sector. These braids are fixed by a screw, washer and self-locking nut (fig. 32, 33). 15 Please note: OLTC MS 111300, M 1 350, M S| M 6 x 1 8 L M6x 16 301, M1351 (see fig. 34) L There are 8 sets of contact braids, LL two sets each on top and bottom as Sz well as two sets of two in the middle of a sector. a al b1 b The contact braids of the main switching contacts and transition contacts are joined together at the 093 326 (ra) M 6 x 18L M 6x 16 \) M6 x 28 (( aT Bl M 6x 16 M 6 x 18L 093 326. output terminal. 2 sets of contact braids (7 \ \) (on top and bottom) 012770 _[ A f ] 012 801 \ I Each fixed to the output terminal by M6 x 18L M5 x 22 M 6x 18L one bolt M6 x 28 (w.s.10) with self- locking nut and washer, max. torque (¢ \) ( r \) 9 Nm. Attachment to the main switching 012 801 Af M6 x 18L M5 x 22 1 li M 6x 18L 012770 contact (double braid) by one bolt M6 x 18L,attachment to the transition contact (single braid) by one bolt 093 326 ( \ (17 \ 093 3 326 M 6x 16. 7 [ {- ir + I! M 6x 18L M 6x 16 Me x 28 M 6x 1 6 M 6x 18L All bolts with self-locking nut and washer, max. torque 9 Nm. Fig. 34 Contact braids for MS 111 300... M | 351 4 sets o f double contact braids (schematic drawing) (in the middle) Attachment to the output terminal: each by one bolt M5 x 22 (w.s. 8) with self-locking nut and washer, max. torque 5 Nm. Each fixed to the main switching con- a al b1 tact by one bolt M6 x 18L (w.s.10) with self-locking nut and washer, max. torque 9 Nm. OLTC M11 500, M I l l 600, M1501, 093 325 { { M 6 x 16 M6x 16 ji =) Ll M 6x 28 M 6x 16 M 6x 16 M 1 6 0 1 , M 1 8 0 2 , MI11200, M I 1500, M 11800 (see fig. 35) Fig. 35 Contact braids for M 111 300... M11800 There are two sets o f contact braids o n top only, connected t o (schematic drawing) main switching and transition contacts. Attachment to the main switching The contact braid of the main switch- contact and transition contact: each ing contacts and transition contacts by one bolt M6 x 16 (w.s. 10) with are joined together at the output self-locking nut and washer, max. terminal. torque 9 Nm. Attachment to the output terminal by Always use new self-locking nuts. one bolt M6 x 28 (w.s. 10) with self- locking nut and washer, max. torque 9 Nm. 16 7. REATTACHMENT OF THE CONTACT SHELLS Reattach the contact shell in reverse order t o removal. The diverter switch is in the mid-position. Insert a chuck- ing wedge between epoxy segment and contact carrier t o hold back the movable contact system of the diver- ter switch (see appendix, section 12.2). This counters the pressure of the movable contact system (fig. 36, 37) and makes attachment of the contact shell easier. Refit the arc chutes and make sure that they are properly seated. Attachment of each contact shell by 8 screws M6 x 20 (w.s. 10), max. torque 5 Nm, with lock tabs (fig. 38). Use new self-locking screws and lock tabs. After tightening the screws, remove the chucking wedge in upward direc- tion (fig. 39). When all contact shells have been reinstalled, the spring energy accumu- lator must be set from the mid-posi- tion into a switched position of the diverter switch and locked-in. Insert a screwdriver between wind-up sledge and cocking sledge of the energy accumulator (fig. 40). Actuate the eccentric by means of the operating key until the pawl locks-in (see fig. 41, 42). Operate the diverter switch several times to check its mechanical function. Finally check again the transition resistors as described in section 5.2. Set the diverter switch t o its with- drawal position (see section 5.1). The diverter switch unit is now ready t o b e reinstalled. Fig. 41 Fig. 42 Pawl unlocked Pawl locked-in 17 8. DIVERTER SWITCH UNIT WITH SUPPORT CYLINDER In case of a diverter switch unit which has a support cylinder (fig. 43) in- stead of 4 support bars please note: (1) carry out procedures according to sections 5.1 and 5.2. (2) Detach the support cylinder. Undo 8 screws M8 x 20 (w.s.13) each with a self-locking nut, at the 4 fish-plates of the spring energy accumulator (fig. 44). When removing the screws take care not to drop parts into the diverter switch. Take off the support cylinder. Take off the insulating drive shaft. Clean the support cylinder inside and outside with a brush and transformer oil. Finally flush with transformer oil and dry. Clean the insulating drive shaft (3) Carry out procedures according to sections 5.3 t0 5.5. To set the diverter switch to its mid position insert the handle of the operating key into the groove of the eccentric drive shaft (fig. 45, 46) (4) Carry out procedures according to sections 5.7 and 5.8. If needed, replacement work according to section 6 should be performed. (5) Carry out procedures according to section 7. To lock in the spring energy accumulator use again the operat- ing key (fig. 47). Set up the insulating drive shaft (fig. 48). The shaft key must point to the eccentric. 18 (6) Reattach the support cylinder with support plate: 8 bolts M8 x 20 (w.s.13), each with 2 washers, max. torque 22 Nm. Ensure alignment of triangle marks on bottom at the spring energy accumulator housing and on top at the support plate (fig. 49, 50). Operate the diverter switch seve- ral times to check its mechanical function (fig. 51). Finally check again the transition resistors as described in section 5.2. Set the diverter switch to its withdrawal position (see section 5.1) The diverter switch unit is now ready to be reinstalled. 9. REINSTALLATION OF THE DIVERTER SWITCH UNIT Remove the tap changer head cover. Lift the diverter switch unit over the 10. OIL FILLING Vent the suction pipe (screw cap open tap changer head. Lower it down M16 / w.s. 22. bleeder screw M6 into the oil compartment slowly and CAUTION: The tap changer oil with cheese head, max. torque 2 Nm), carefully. compartment and the associated see fig. 52. When remounting the diverter switch oil conservator must only be filled Units with stationary oil filter unit: unit turn, if necessary, the insulating with new mineral insulating oil for operate the oil filter unit and bleed. shaft slightly until the coupling en- transformers according t o IEC 296 gages. (1982). The use of other o i l can Fill up the oil conservator with new oil affect the trouble-free operation o f to its original level. Ensure alignment of marks on the tap changer and transformer. support plate of diverter switch unit CAUTION: The transformer should and in the tap changer head. be energised not earlier than Fill new oil into the diverter switch oil 1 hour after the oil filling. Fix the diverter switch unit by the compartment up to the level of the screws of the support plate. support plate. Put the cover on the ‘Standard design: 4 screws M8 x 20 tap changer head making sure that (w.s.13). the gasket fits properly; if necessary, replace the O-ring. Special design for bell-type tank installation: 5 nuts M8 (w.s. 13). The head cover is attached by 24 bolts M10 (w.s.17), max. torque Both types secured by spring wash- 34 Nm, secured by spring washers. ers, max. torque 22 Nm. Reinstall the position indicating disc Open the stop valve between pro- {put on clip to shaft end). tective relay and oil conservator. Vent the tap changer head through the bleeder valve in the tap changer head cover (remove screw cap M30 / w.s.36 and lift valve tappet by means of a screwdriver). 19 11. FURTHER CHECKS 11.3 Protective relay RS 2001 (see In case of serious trouble with tap Operating Instructions No. 59) changer or motor drive — provided that CAUTION: The transformer must the repair cannot easily be done on The transformer must be immediately not be energised without prior site — and in case of a response of the switched off by the circuit breakers positive checks carried out ac- protective relay please contact the when the protective relay is ener- cording t o sections 11.1 t o 11.4. authorized MR representative, the gized. The operational test of the transformer manufacturer or protective relay should, therefore, 11.1 Drive shafts include checking the proper function Maschinenfabrik Reinhausen GmbH of the circuit breakers. Technischer Service Couple the horizontal drive shatt to Falkensteinstrasse 8 upper gear unit and bevel gear Make sure that the transformer can- Postfach 1 2 0 3 6 0 (6 screws M86, w.s.10, max. torque not be energized and its ground con- 2 9 Nm, lock tabs). nections cannot be removed during Telefon (09 41) 40 90-0 the test. Furthermore, make sure that Check horizontal and vertical drive the fire-extinguishing equipment, if Telefax (09 41) 4 42 03 shafts, especially the coupling points Telex 6 5 881 any, coupled with the tripping of the (check tightness of bolts and nuts, protective relay cannot operate. locking function of lock tabs). If ne- cessary, grease coupling bolts and Proceed as follows: 11.4 Voltage regulator (see O-rings (e.g. with SHELL 6432), Operating Instructions No. 66 1. Close the circuit breakers with adjust axial clearance to 3 mm. isolating switches open and for voltage regulator MK 20 or No. 114 for MK 30 respectively Check bellows and greasing of ball transformer terminals grounded. joints (only special designs with ball If the tap changer is controlled by a 2. Open the hood for access to the joints). test push-buttons (3 screws M6, voltage regulator: Check upper gear unit at tap changer w.s.10). Press the push-button Check settings of voltage level, sen- head cover and bevel gear (add TRANSFORMER OFF. sitivity (bandwidth) and delay time lubricating grease if necessary). The circuit breakers must open. according to the operating instructions 3. With the protective relay in in orderto avoid unnecessary tap TRANSFORMER OFF position, change operations. 11.2 Operational tests of motor drive it must be impossible to close the and tap changer circuit breakers. This is to be checked. Check coincidence of position indica- tion of tap changer and motor drive 4. Reset the protective relay to the unit. TRANSFORMER IN SERVICE position and lock the hood WARNING: Misalignment between (8 screws M6, max. torque 5 Nm). tap changer and motor drive unit exists, if tap changer and motor drive unit show different operating WARNING: If the protective relay positions. Misalignment of coup- operates, d o not reset until the tap ling between tap changer and changer and the transformer have motor drive unit can lead t o severe been checked. For t h i s purpose damage of tap changer and trans- also withdraw t h e diverter s w i t c h former, i f operation i s continued. unit. I n detail proceed according t o Check symmetrical coupling of motor our Operating Instructions No. 59 drive to the tap changer. for the protective relay RS 2001. The follow-up of the motor drive must Before returning t o energized be identical in both directions (adjust if operation, make sure that the necessary, see section 12.1 of appen- cause of t h e trouble has been dix). Finally screw and lock the corrected o r the tap changer and coupling as under 11.1. transformer are free of damage. Perform trial operations across the Never reconnect the transformer whole tapping range. without prior checking. Continued operation o f the tap changer can Check the electrical and mechanical result i n severe damage of tap end position of the motor drive (see changer and transformer. Operating Instructions No. 40 for mo- tor drive MA 7 and No. 80 for MA 9). 20 12. APPENDIX 12.1 Coupling of the tap changer and motor drive unit (see also @ Operating Instructions No.40 for motor drive MA 7 and No.80 0 5 10 15 20 25 for motor drive MA 9) | TT [LIES Itis absolutely necessary that the tap change operation | |i | | | | | | | | 1 1 1 | is finished before the motor drive stops.. ! ’ OPERATION OF This is ensured by setting the time of the diverter ~ D I V E R T E R SWITCH switch action (= on-load tap changing) at a distinct 25 20 15 10 5 0 interval before the end of the motor drive action | (1.5 - 2 sections before the red center mark on the tap TT T T change indication whee). This red center mark is used i s | | | | | | | TL 1 | b as reference when adjusting. One tap change operation corresponds to one rotation OFERATION OF DIVERTER SWITCH of the indication wheel. The tap change indication 10 15 20 25 30 33 wheel is divided into sections (TIW sections) with one section corresponding t o o n e rotation of t h e crank. i. TT | gm The number of sections counted from the beginning of | Ll | | | | | | | | | | 11 th | the tap change operation until the red center mark of the indication wheel faces the mark on the inspection [ O P E R A T I O N OF window, should be equal in both directions. DIVERTER SWITCH Minor asymmetry is admissible. Symmetrical coupling is achieved as follows: @ — When adjusting ensure that the position indication readings of motor drive and tap changer are equal. — Tap changer and motor drive have to be in the : adjustment position. UNCOUPLE TT d — Couple tap changer and motor drive. —~ Turn crank in one direction until diverter switch action occurs. Count the remaining TIW sections 0 3 until the red center mark of the tap change indi- cation wheel is visible in the middle of the inspec- tion window. | — Repeat this procedure in the opposite direction. — Ifthere is a difference between the numbers of sections counted in both directions, the motor drive must be readjusted in relation to the tap changer by half this difference of numbers. COUPLE | Example for motor drive MA 7 (see fig. 53); a) Tap changer is in operating position 10. Turn crank towards 1 1 until diverter switch action 5 10 15 20 occurs. Count number of TIW sections until red | b) center mark appears Tap changer is in operating position 11. | TERT] E0| Turn crank towards 10 untif diverter switch action EE pA occurs. Count number of TIW sections until red 33 30 25 20 15 10 5 center mark appears sen 1/2(7 sections — 1.5 sections) = 2.75 sections, ET _ | i ] chosen 3 sections. L — OPERATION OF DIVERTER SWITCH c) Turn crank towards 1 1 until r e d center m a r k appears. d) Uncouple vertical drive shaft. Sora TW soctanane direction { t o w a r d s 12) Fig. 53 Symmetrization of coupling between tap changer and motor drive f) Couple again. 9 o oceed in ihe same direction (as with e) unti a,b — Counting the TIW sections after diverter switch action in both directions Soneo e ofSW oars: until red center ¢ — Cranking in the direction of the bigger amount of TIW sections mark appears. d — Uncoupling Result: 4 sections. e — Cranking on by correction value. a f — Coupling h Check i n r e - PRosie direction. g — Completing operation, checking number of sections + 4-3 sections. h ~~ — Checking in the opposite direction 12.2 Inspection tools Tools for bolts & nuts for installation and inspection...............c.cc.c....... 890 478 Specail tools for the INSPECiON...........cccvviecveeeierrieceecreeeeereee c e e 890 479 = —p A B C D Hem No. Designation Fig. DIN | Wrench size In mm 1 1 Double-ended open-jaw wrench A 895 8x10 2 1 Ring & open-jaw wrench Cc 3113 10 3 1 Double-ended open-jaw wrench A 895 13x17 4 1 Double-ended socket wrench B 896 13x17 5 1 Double-ended open-jaw wrench A 895 17x19 6 1 Double-ended open-jaw wrench A 895 22x24 7 1 Hexagon socket screw key D 911 4 8 1 Hexagon socket screw key D 911 5 9 1 Hexagon socket screw key D 911 8 MR RaRRas™" Toolsor bake mt or etalonandinspection| 890 4TB:2E +01 25,2 82" ruse #48 f—35 WRENCH FOR ENERGY ACCUMULATOR 088 538 =20 7p 15 £3 CHUCKING WEDGE 560 131 MASCHINENFABRIK On-load tap changer type M and MS M R REINHAUSEN 890 479:2E Special tools for the inspection 12.3 Lifting device To be attached to the tap changer head. 897016 T o b e mounted o n the tank cover........ccoveeeeeeriiieerrccennees..... 8 9 7 042, sh.1 & 2 AN COLUMN TUBE 250MM COLUMN TUBE 500MM COLUMN TUBE 1000 Mi i] 112] 5] N C LOCKING BAR: SERVES FOR LOCKING AND UNLOCKING [71 THE TROLLEY. DURING RAISING OF THE DEVICE THE TRAVELLING CRAB MUST NOT BE LOCKED FOR OPERATING SAFETY. - WL = CTT FE: H h i 2. [EEN] |= A TAP CHANGER HEAD ASSEMBLY: © 3» = ATTACH THE SUPPORTING PLATE 1 1 ) ON TAP CHANGER HEAD WITH SCREWS. + MOUNT LOWER COLUMN TUBE [ 2 ] AND SECURE WITH LOCKING BOLT [ 3 ] AND COTTER PIN (4). + CONNECT THE UPPER COLUMN TUBE ( 5 ) AND LOWER COLUMN TUBE [ 2 ] AT THE JONT ~ WITH HINGE BOLT [ 6 ]. SECURE WITH COTTER PIN [ 41. [=] + MOUNT THE ADDITIONAL COLUMN [ 7 ] AND SECURE IT WATH LOCKING BOLT 8 1 AND ( O T T EPN R 14). + RAISE THE UPPER COLUMN TUBE { 5 1 BY MEANS OF STAYING THE HOLDNG ROBE [ 9 ]. m ACCORDING TO EXTENSION HEIGHT NECESSARY, PUT THE COLUMN TUBES OF 250, 500. = + 1000 N THE UPPER COLUMN TUBE [ 5 1 AND SECURE IT WITH LOCKING BOLTS [ 1 1 ) AND C O T TPNE[ R4). xx ea + MOUNT ARM AND SECURE IT WITH LOCKING BOLT [ 11) AND COTTER PN. + ATTACH THE TRAVELUNG CRAB [ 131 AND SCREWS [ 1 4 ] FOR LMTING THE END POSITION. + RAISE THE CHAN HOIST [ 15) BETWEEN THE TRAVELLING CRAB [ 1 3 ] AND THE ADDITIONAL - COLUMN [ 7 1 BY OPERATING THE CHAM HOIST. DO NOT LOCK WHLE RAISHG THE TRAVELLING CRAB. + (LOSE THE HINGES WITH SCREWS [ 6 1. [. H E I G H T OF NECESSARY FOR COLUMN TUBES EXTENSION TAP CHANGERS REQUIRED X TYPE 152 MMs | 179 R 750 204 M-DR 560 2096 SPECTAL LENGTH 250 + S00 $ e9 6 SlPECTAL A L LlLENGT H T0009 + 7 5 0 30.6 SPECIAL L E N G T H_ 1000 + 5 0 0 THE MAX. PERMISSABLE TOTAL HEIGHT OF THE DEWCE KS 3592 MM. REPRESENTATION FOR EXTENSION AT HEIGHT OF 1796 MM. MRRERANS INENFABRIK On-loa d t a p c h a n g e r type M a n d M S | 897 016:1E Lifting device to be attached to the tap changer head 24 — COLUMN TUBE 250 MM 101] coum Tuee 500 tm TUBE COLU MN t000 1 — m2) 125 r y -— [4) C tn / vi I £5) T— @- _ i [&:3) NC AR LOCKNG BAR: SERVES FOR [71 ii a A {Ny LOCKING AND UNLOCKING THE TROLLEY. a meg 1H rar. ed < i SP at = CO) i w | BS | us > \ ! | Neg Pi —F< El Dl DURNG RAISING OF THE DEVICE THE x TRAVELLING CRAB MUST NOT BE LOCKED = FOR OPERATING SAFETY. oo LL] 1H! \ HH 171 T X 1:1 > —t bo l i Le N v VAS ET N ZZY ps4 "ASSEMBLY : THIS SUPPORT ON A SLANTED TRANSFORMER COVER CAN BE LEVELLED BY WASHERS 073933: AND 073934:. A: SCREW SUPPORT [ 1 ) ON TRANSFORMER COVER. ( TIGHTENING T O R=Q80M) UE THIS SUPPORT [ 1 ] ON A SLANTED TRANSFORMER COVER CAN BE LEVELLED BY MEANS OF A WASHER. + MOUNT LOWER COLUMN TUBE £2) AND SECURE WITH LOCKING BOLT [31 AND COTTER PN [ 4 ]. © + CONNECT THE UPPER COLUMN TUBE ( 5 ) AND LOWER COLUMN TUBE [ 2 AT THE JONT ~ "WITH HINGE BOLT [ 6 1. SECURE WITH COTTER PIN [ 4 ]. + MOUNT THE ADDITIONAL COLUMN [ 7 ] [= AND SECURE IT WITH LOCKING BOLT [ 8 ) AND COTTER PIN [ 4 ]. E: RAISE THE UPPER COLUMN TUBE (S51) BY MEANS OF STAYING THE HOLDING ROBE [ 9 ]. F: ACCORDING TO EXTENSION HEIGHT NECESSARY, PUT THE COLUMN TUBES OF 250, 500, 1000 IN THE UPPER COLUMN TUBE [ 5 1 AND SECURE IT WITH LOCKING BOLTS [ 1 1 ] AND COTTER PIN [ 4 ]. + MOUNT ARM AND SECURE IT WITH LOCKING BOLT [ 17] AND COTTER PIN [ 4 ]. a + ATTACH THE TRAVELLING CRAB [131 AND SCREWS [ % 1 FOR LIMTING THE END POSITION. x + RAISE THE CHAN HOIST [ 1 5 ] BETWEEN THE TRAVELLING CRAB [ 1 3 ] AND THE ADDITIONAL - COLUMN [ 7 ] BY OPERATING THE CHAIN HOIST. DO NOT LOCK WHRE RAISING THE TRAVELLING CRAB. + CLOSE THE HINGES WITH SCREWS. — HEIGHT OF NECESSARY FOR COLUMN TUBES TOTAL EXTENSION TAP CHANGERS REQUIRED HEIGHT X TYPE Y S00 BD. M. , M5 0} OO O----- 2047 750 R. T 250 2297 000 E , M- , V 500 2547 2250 D- 2 5 0 + 500 2797 00 C220 , C 3 5 0 , H 1000 3047 27350 S P E C I A L LENGTH 1000 + 250 3297 3000 SPECTAL LENGTH i000 + 500 3547 THE MAX. PERMSSABLE TOTAL HEIGHT OF THE DEVICE IS 3547 MH. REPRESENTATION FOR EXTENSION AT HEIGHT OF 1750 MM. WELD THE FIXING BOLT TO THE TRANSFORMER COVER SEE PAGE 2. MASCHINENFABRIK On-load tap changer type M and MS REINHAUSEN 897 042:1E, sh. 1 Lifting device to be mounted on the tank cover 25 DIVERTER SWITCH UNIT 073507: MATERIAL : XSCrNi189 CHANGER TYPE Rmax WELDING ELECTROIDS FOR EX. X2CrNiMo28155 V 1150 H.,M , MS 1000 7 M-DR 900 £250. D 800 TRANSFORMER COVER D-BR , R , T 700 C350., E 600 MRFerzaa™ MASCHINENFABRIK REINHAUSEN On-load tap changer type M and MS Lifting device to be mounted on the tank cover 897 042:1E, sh. 2 26 12.4 Spare parts list General spare parts, to be used in case of loss or damage only Quantity per unit Item Designation MR-No. MS 1300 | MSI301 M1I500 M1501 | M1802 | MI 1200/1500 Use M lll 350 M1351 MUI600| M 6 0 1 M 11800 12.401 Screw cap 070 071 1 1 1 1 1 1 Bleeder valve Valvet tappet 070 072 1 1 1 1 1 1 of tap changer Circlip 401 034 1 1 1 1 1 1 head cover Washer 455 071 1 1 1 1 1 1 Spring 500 884 1 1 1 1 1 1 O-ring 400 437 1 1 1 1 1 1 12.402 Bleeder screw 020 019 1 1 1 1 1 1 Bleeder screw of Gasket 860 151 1 1 1 1 1 1 elbow of suction Screw cap 047 670 1 1 1 1 1 1 pipe Gasket 860 150 1 1 1 1 1 1 12.403 Hex. hed screw M6 x 30 455 005 6 6 6 6 [:] 6 Attachment of drive Hex. nut M6 455 400 6 6 6 6 6 6 shaft coupling Lock tab 052 092 4 4 4 4 4 4 (=1sel) 12.404 Hex. head scre