LEEA Academy Overhead Travelling Cranes - Step Notes PDF
Document Details
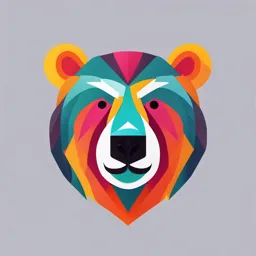
Uploaded by PromisingJadeite8923
null
2017
null
null
Tags
Related
- Overhead Travelling Cranes Step Notes PDF
- LEEA Academy Overhead Travelling Cranes - Step Notes PDF
- LEEA Academy Overhead Travelling Cranes - Step Notes (PDF) Apr 2017
- LEEA Overhead Travelling Cranes - Step Notes PDF, Apr 2017
- LEEA Academy Overhead Travelling Cranes - Step Notes PDF
- LEEA Academy Overhead Traveling Cranes Step Notes PDF
Summary
This document is a set of step-by-step notes on overhead travelling cranes. It covers various topics like rope drums, pulleys, lifting equipment, and different power systems. The document was published in April 2017.
Full Transcript
The written report is to provide a description of the article examined, the date of the examination and a clear statement of its fitness for further use or details of the defects which affect the WLL/SWL and other observations o Where an article is defective, a res...
The written report is to provide a description of the article examined, the date of the examination and a clear statement of its fitness for further use or details of the defects which affect the WLL/SWL and other observations o Where an article is defective, a responsible representative of the user must be informed o If dangerously defective, arrangements must be made for its immediate withdrawal from service o Where Regulations or Acts require statutory notification of defective equipment, steps must be taken to ensure notification to the correct authority, for example LOLER gives requirements for reporting certain matters to the HSE Training It is of paramount importance that lifting equipment inspectors or examiners do not work on live electrical equipment. Lock-out/Tag-out routines should always be considered as part of your risk assessment. 10. Rope Drums and Pulleys 104 Pulleys The shape of the pulley groove is shown below. The finish must always be smooth, with sharp edges removed to reduce the risk of accidental damage to the rope. ©LEEA Academy Overhead Travelling Cranes – Step Notes – Apr 2017 – v1.3 Drums and Pulleys The diameter around which the rope is bent and the depth and shape e.g. pulley and drum grooves that support the rope must be carefully considered o Check the condition of all sheave and drum grooves to ensure that they are capable of accepting the size of the new rope, do not contain any irregularities, such as corrugations, and have sufficient remaining thickness to safely support the rope o For optimal performance, the effective sheave groove diameter should be larger than the nominal rope diameter by about 5 % to 10 %, and ideally, at least 1 % greater than the actual diameter of the new rope For those ropes that are subjected to multi-layer spooling, apply a back-tension to the rope during installation that is equivalent to about 2 ½ % to 5% of the minimum breaking force of the rope. This helps to ensure that the rope on the bottom layer is tightly wound, forming a firm base for succeeding layers Sheave Gauges How to Determine the Amount of Wear Using a Wire Rope Sheave Gauge Use a wire rope sheave gauge to regularly check sheave grooves for wear, which may slow or block a wire rope: 105 1. Place the proper size gauge in the sheave 2. Shine a light behind the gauge 3. Check for light between the gauge and the root of the groove. If you detect light, replace or re-tool the sheave Wire rope will wear the bottom of the sheave groove to a radius smaller than the radius of the sheave. To determine the amount of wear, place the proper size gauge in the sheave and shine a light behind the gauge. Light should not be detected between the gauge and the root of the groove. If wear is evident, the sheave should be re-machined or replaced. LEEA Sheave gauges are available online at www.leeaint.com from the web shop. ©LEEA Academy Overhead Travelling Cranes – Step Notes – Apr 2017 – v1.3 Rope Drum Helix Wear Check manufacturers tolerances which are usually stated for dimensions A and B. Drum Helix Wear 106 ©LEEA Academy Overhead Travelling Cranes – Step Notes – Apr 2017 – v1.3 11. Power Feed Systems Electric Power Operation Electricity is the most common form of power used with lifting appliances. It is used on blocks, winches, trolleys and cranes to provide power for both lifting and travelling or slewing motions. Although examples of DC supply appliances still exist, AC supply is considered to be the norm. Most types 107 of electric power operated lifting appliances are available for three phase operation. Single phase and low voltage hoists and winches are available in the lower capacities and some types of vehicle winches are available for battery operation. Pneumatic Power Operation Pneumatic power operation is used on hoists, trolleys, winches and some cranes. It is less efficient and more difficult to carry to the appliance than electricity. For this reason, it is less common in general use than electricity, but it has many advantages making it more suitable for certain applications. Hydraulic Power Operation Hydraulic power is the least common form of power operation associated with lifting appliances, usually being restricted to special purpose equipment and to some types of winch. Electrical Supply Systems The use of electricity is highly developed throughout industry. It has the advantage over other forms of power of being more readily available and is easily carried from the power source to the appliance by cable or bus-bar conductor systems. As a result, electricity is the most common form of power associated with general purpose lifting appliances. ©LEEA Academy Overhead Travelling Cranes – Step Notes – Apr 2017 – v1.3 The dangers associated with electricity are well known and there is much experience in protection to guard against them and in overcoming them. It is necessary to protect the operative from the dangers of electric shocks, either by insulation or by the use of low voltages. Single phase and low voltage drives are less common in lifting appliances and are restricted to the lower capacity items due to the difficulties associated in providing motors of adequate capacities and ratings. It is therefore more normal to protect the operative by the use of low voltage control circuits as it is in this area that the main danger to the operative exists. The current supply should include a means of isolating the equipment from the power source. In practice, switch fuses and isolators are used to fulfil this requirement. The isolator, which is considered to be part of the supply system, should be positioned at the start of the conductor system so that the system will be isolated from the power source as well as the appliance. Electricity has the disadvantage of requiring special protection in certain environments, e.g. explosive atmospheres, and steps are necessary to contain the danger within the appliance. Such explosion proof 108 appliances and their power feed systems are far more expensive than standard equipment. They tend to be heavy and bulky and armoured cable offers little flexibility making travel difficult. Various types of conductor systems may be used to carry the supply to travelling hoists and cranes. The main factory supply is taken to a point adjacent to the equipment and terminated with a switch fuse/isolator. The power feed to the actual hoist or crane is then taken from this in one of several ways. There are five basic power feed systems that are commonly used for electrically powered hoists: 1. Coiled cable 2. Cable reeling drum 3. Festoon cables 4. Insulated conductors 5. Energy chain cable carriers ©LEEA Academy Overhead Travelling Cranes – Step Notes – Apr 2017 – v1.3 In the past, bare copper conductors were used to provide a power supply for overhead travelling cranes. They are no longer considered suitable in all cases and are not used for new power supply installations. We will consider these systems and the limitations/dangers they present. Bare Copper Conductors Although this system is considered unsuitable for new installations nowadays, it was widely used in the past on all types of installations. Many of these old installations may still be found in service. The general advice is to review the installation; It may be that the bare wires present a possible danger to people working in the area o In this case the advice must be given to change this for a more suitable supply system On the other hand it may be considered that the system is safe by virtue of its position o In this case it may be left in service The owner has a responsibility under section 2 of the Health and Safety at Work Act to provide safe systems of work and it is his responsibility to change this if it is considered necessary. 109 In this system copper wires are stretched parallel to the beam by means of strainer screws with insulators. A collector bracket is fitted to the hoist on which are mounted the collectors. The most common form of collector is the bronze roller, graphite bushed, thus providing good electrical contact and bearing surfaces. Each collection shaft is insulated from the collector bracket. For long runs the wires are supported on porcelain reels, the collectors lifting the wires off the reels as they pass over them. As bare copper wires are not generally recommended they have been superseded by safer and more efficient systems. Coiled Cable In the coiled cable the conductors are contained in a PVC compound insulate which is coiled in a similar manner to a tension spring. The cable is fixed to a swivelling bracket on the side plate of the trolley with the supply end fixed at a convenient point adjacent to the runway. As the hoist is moved along the runway so the cable expands, when the hoist is moved back so the cable contracts. This type of cable is suitable where only short travel distances are required due to the sag in the cable. The normal extension ratio of such a cable is 3 to 1 with a nominal 3 metres extended length. ©LEEA Academy Overhead Travelling Cranes – Step Notes – Apr 2017 – v1.3 Cable Reeling Drum The cable reeling drum provides a means of power on control using a flexible cable wound onto a drum which can be played out and then recovered. At the heavy end of the range reeling drums can be very large and equipped with geared motors actuated by torque sensing for cable recovery. This unit deals only with the more common spring operated type. 110 Construction is very simple, comprising a steel drum mounted on to a fixed shaft and rotating on sealed bearings. The power feed cable is clamped to the drum, the wire ends being connected back to carbon brush gear which rotates with the drum. The power feed to the drum passes through the fixed shaft to the slip rings which are fixed. Slip Rings ©LEEA Academy Overhead Travelling Cranes – Step Notes – Apr 2017 – v1.3 Cable Reeling Drum Since a reeling drum spiral wound spring does not provide a constant torque, spring selection is very important. The cable should not be overloaded by too great a tension or have too much slack, nor should the appliance run back (a possible hazard with coiled cables and reeling drums if used in association with light weight push/pull trolleys). Before a drum can be selected the cable size must be determined taking a number of factors into account: Voltage Drop - Unless it is otherwise stated it is usual to work to IEE Regulations which state that voltage drop shall not exceed 5% of the rated voltage based on the normal operating current Temperature Correction - Generally for ambient temperatures above 30°C the continuous rated current capacities should be eliminated Reeling Configurations - Rated cable capacities should be further de-rated according to the configuration of the reel to be chosen Short Time Rated Motors - In many cases the motors on a lifting appliance may be short time rated thus allowing cable carrying capacities to be increased Note: Although not expected to design electrical power supply systems the Tester and Examiner would be expected to understand the fundamental requirements of a system to enable him for example to identify the reason for a performance deficiency of a hoist under test. 111 Notes: Cable Selection In practice the cable would be selected based on the criteria discussed against technical data provided for a particular product. An example of cable selection will be discussed in the next section (Festoon Cable Systems) since it could apply to both systems. ©LEEA Academy Overhead Travelling Cranes – Step Notes – Apr 2017 – v1.3 Festoon Cables Taut Wire The taut wire system is suitable for light duties over lengths not exceeding 30 metres and is simple and economical to install. The strainer wire is made taut by means of straining screws whilst the cable is carried on trolleys. Festoon Trolleys 112 Festoon Cables Typical taut wire system: ©LEEA Academy Overhead Travelling Cranes – Step Notes – Apr 2017 – v1.3 Tracked Cable Systems The tracked system is a development of the taut wire system. It can support greater loads and is suitable for higher speeds. Most systems incorporate an inverted `U‘ or ‘C’ section track, the cable support trolleys running on the two inner ledges. The manufacturers of these systems offer a range of profile sections for most loading conditions from light to heavy duty. The tracked festoon systems are very safe with perfect insulation hence no loss of energy or voltage drop where current has to pass from conductor to collector. Also on long track installations the size of cables would need to be increased to limit voltage drop hence requiring a heavier track system to support them. In many cases a lifting appliance will have two festoon tracks one to carry power to the hoist the other providing a mobile pendant push button box, e.g. on the bridge of the crane. When a mobile pendant push button box is fitted the festoon cable will terminate in the pendant control box from which is suspended the push button box by means of the pendant cable. 113 ©LEEA Academy Overhead Travelling Cranes – Step Notes – Apr 2017 – v1.3 Typical components of a tracked festoon cable supply: A limiting factor of the festoon system could be loss of travel of the hoist unit due to bunching of the trolleys especially on long track applications. 114 Typical mobile pendant push button box assembly and connection to the pendant connection box on the festoon: ©LEEA Academy Overhead Travelling Cranes – Step Notes – Apr 2017 – v1.3 115 Hoist Control With the majority of electric hoists the contactor panel is mounted on the main frame and therefore travels with the hoist. It is recommended practice that control voltages should not exceed 115 volts which is achieved by transforming down from a single phase of the three phase supply. The low voltage control signals are transmitted via the push button box and multicore pendant cable to the hoist contactor panel. Pendant Cables Pendant cables may have as many as 25 separate cores depending on the number of push buttons/motions required. The modern pendant cable has two independent strainer wires built in to support itself and the weight of the push button box. ©LEEA Academy Overhead Travelling Cranes – Step Notes – Apr 2017 – v1.3 Insulated Conductors Shrouded Conductor Systems Shrouded conductor systems are of various cross sections and the conductor bar is sufficiently shrouded with a PVC cover to ensure finger safety yet provide access for a collector shoe to pick up the current. Typical components of a 4-bar (3 x phase and 1 x Earth conductor) shrouded system: 116 The collection assembly is spring loaded to ensure good contact with the conductor bar and articulated to enable the contact shoe to follow the track without binding. ©LEEA Academy Overhead Travelling Cranes – Step Notes – Apr 2017 – v1.3 Totally Enclosed Conductor Systems A totally enclosed conductor system is used where multiple conductors are required in one housing. It is a rigid and compact system. They are commonly used in overhead crane applications but also for traveling hoists. 117 The illustration below shows how the fully enclosed conductor head collects the power from the enclosed bus-bars and feeds this direct to the hoist. ©LEEA Academy Overhead Travelling Cranes – Step Notes – Apr 2017 – v1.3 The merits of shrouded conductor systems are a much greater protection against accidental contact and a suitability for long runs since intermediate feeders can be added. These systems are available up to 300 amps. They are however unsuitable for flame proof or similar applications. Higher operating temperatures can be achieved by using polycarbonate covers (-40°C to 121°C) or laminated fibre glass (-45°C to 149°C). Expansion With any rigid system particular attention must be paid to expansion and expansion couplings fitted, in accordance with manufacturers recommendations, if problems are to be avoided. Shrouded Conduction Systems With the shrouded conduction system the power feed need not be connected to one end. By connecting in the centre rather than to one end voltage drop is halved and by connecting a power feed to each end the voltage drop is halved again. Energy Chain Systems Most energy chain cable carriers have a rectangular cross section, inside which the cables lie. Cross bars along the length of the carrier can be opened from 118 the outside, so that cables can be easily inserted and plugs connected. Internal separators in the carrier separate the cables. Cables can also be held in place with an integrated strain relief. Mounting brackets fix the ends of the carrier to the machine. Besides only bending in one plane due to the rigid jointed structure, cable carriers also often only permit bending in one direction. In combination with rigid mounting of the ends of the carrier, this can prevent the enclosed cables from flopping in undesired directions and becoming tangled or crushed. Cable carriers are used anywhere on cranes where moving components require power, control and communication power feeds in a flexible media. Energy Chain cable carriers are quiet in operation, lightweight and provide covered cable design and that can be quickly opened. They can be used in extreme conditions such as heat-resistant or clean room environments. ©LEEA Academy Overhead Travelling Cranes – Step Notes – Apr 2017 – v1.3 Compressed Air Supply Systems The production of a clean, dry supply of compressed air suitable for pneumatic power operated lifting appliances is expensive and it is less easily carried from the power source to the appliance than electricity Due to these reasons, its use is more limited than that of electricity Although electric power operated lifting appliances are the usual choice for general purposes, pneumatic power operated appliances have advantages for certain applications as most of the dangers associated with electricity do not exist with compressed air Standard pneumatic equipment is flame proof It can therefore be used in atmospheres where electric equipment would require special insulation and protection to contain the danger With pneumatic equipment, this danger does not exist 119 Pneumatic motors offer variable speeds of operation. Air flow rate to the motor is controlled by the operative via a supply valve. By careful manipulation the operative can control the air delivery rate, the motor speed being governed by the volume of air supplied. At normal working pressure it is impossible to overload a pneumatic motor. Once the load increases beyond the design load of the motor, it will stall and, unlike an electric motor, it will not be harmed by this. Although pneumatic motors are robust in design, capacity for capacity they tend to be smaller and lighter than equivalent electric motors. They will withstand a high degree of heat and moisture. Due to the internal pressure whilst in operation, the motor is self-purging. This makes standard pneumatic equipment suitable for use in steamy atmospheres, such as paper mills and laundries, and in dusty conditions, such as flour mills without any special steps being taken, unlike electrical equipment which requires enclosures to protect the equipment from their effects. ©LEEA Academy Overhead Travelling Cranes – Step Notes – Apr 2017 – v1.3 Compressed air is less efficient than electricity. It contains a high proportion of moisture which has to be removed. Whilst motors will purge and expel this moisture when in operation, condensation will occur when the motor is idle. This will lead to corrosion and contamination of residual lubricants unless steps are taken to prevent this. Pneumatic appliances usually exhaust spent air to atmosphere direct from the motor. Although compressed air is generally considered to be less dangerous than electricity, some dangers do exist. Small leaks are usually harmless, though expensive. However, in dusty environments exhausting air and leaks can cause particles to be propelled through the air and be a hazard to eyes etc. Inspection/Examination Ensure Lock Out-Tag Out Isolation! Following total isolation of the power supply using a lock-out/tag-out routine: Bare Copper Wires Assess if the system is safe, if it is the following checks should be made. Check wires for burns due to arcing, replace if burns exceed 25% of diameter. Check collector shoes for burns and if roller collectors check for burns, loss of metal and wear of graphite bearings. Most burns are caused by vibrations or defective collector mechanisms. Wires must not be greased as this 120 will cause arcing. Coiled Cable Check PVC cover for cracks in the insulation especially at terminations. Replace if cracked or damaged. Check security of terminations, cable glands etc. Cable Reeling Drum Check drum for smooth running. If movement is erratic bearings should be checked. Check slip rings, carbon brushes and pressure springs. Check cable tension with drum fully wound, check cable tension with cable fully extended, i.e. the hoist at the opposite end. Check spare rotation capacity of drum and for a minimum of two remaining turns of cable on the drum. Check cable for cracks and damage. Festoon Systems Check taut wire anchors and runners for free movement. If a track system, inspect each joint section is tight and properly closed up. Inspect cable for cracking, check for loose trolley clamps. Additionally, in the case of festoon control systems, check pendant control box is running freely, festoon and pendant connections are secure. Check pendant secure to push button box. Check operation of buttons including any emergency stop and key switch etc. Shrouded Conductor Systems Check for tightness of joints, signs of burning and that covers are in place. Check shoes for wear and alignment. Check spring tension and general operation. ©LEEA Academy Overhead Travelling Cranes – Step Notes – Apr 2017 – v1.3 General All power feeds must terminate at a fused, lockable isolator. This should have good access from the shop floor and be clearly identified. The isolator is considered to be part of the power feed system and should also be carefully examined for correct operation. When examining a supply system, hoist or crane, the isolator should be locked off with an approved locking mechanism for safety. Safety and Training It is of paramount importance that lifting equipment inspectors or examiners do not work on live equipment. Lock-out/Tag-out routines should always be considered as part of your risk assessment and equipment must be checked by a Competent Person to confirm power supplies are isolated before work commences. Notes: 121 ©LEEA Academy Overhead Travelling Cranes – Step Notes – Apr 2017 – v1.3 12. Motion Limit Switches Mechanical Electrical Electro-Mechanical *Hoists shall be fitted with hoisting and lowering limiters in accordance with EN 12077-2:1998, 5.6.1. (Cranes safety – Requirements for health and safety) Older hoists may only have an upper limit switch If lowering, care needs to be taken because over-lowering will result in the bottom block being lifted but with no hoist limit to prevent block to block impact Electrical limiters need to have a positive opening system *Reference taken from BS EN 14492:2006 +A1 2009 Cranes – Power driven winches and hoists – Part 2 (Hoists) section 5.2.4.1 Note: Lower limit needs to account for minimum engagement of load-rope or chain on the machine at its lowest point of travel. 122 Limit Switch Bar Typical application on a Morris 400 Series EWRH A common with electric wire rope hoists for control of upper and lower hook positions The mechanism comprises a bar, spring loaded into the neutral position. The bar carries two stops which are actuated by the rope guide as it moves along the drum and reaches the upper or lower limits of travel Two micro switches are situated at the end. When the bar is moved by the guide contacting a stop, one micro switch is depressed, stopping the motor and applying the brake ©LEEA Academy Overhead Travelling Cranes – Step Notes – Apr 2017 – v1.3 The mechanism is reset by operating the block in the opposite direction On most hoists the micro switches are easily accessible for maintenance and adjustment Limit Switch Limit Operation 123 ©LEEA Academy Overhead Travelling Cranes – Step Notes – Apr 2017 – v1.3 Weighted Lever In operation, the knock off weight assembly is suspended from lever arm and is raised by the bottom block of the hoist which in turn rotates the shaft and a cam. The rotation of the cam opens a limit switch and the hoist (UP) contactor drops out, the motor is then de‑energised and the hoist brake applied. The mechanism is reset automatically by reversing the direction of the hoist. The mechanism is situated beneath the hoist and is readily accessible for maintenance and adjustment. However, being external it is liable to damage if the hoist is incorrectly used. Hook Operated 124 Hook operated limit switch trips hoisting movement when hook reaches the adjustable lever Hook operated limit switch can be automatic reset or manually reset With automatic reset hoisting movement is possible again after tripping as soon as hook has been lowered from the switching area Hook operated limit switches with automatic resets can be used as a working limit before standard upper limit tripping height ©LEEA Academy Overhead Travelling Cranes – Step Notes – Apr 2017 – v1.3 Rotary Limits Hoisting Limit Switch The rotary hoist limit switch contains sets of contacts for default functions The rotary limit switch unit for hoisting is usually located in 125 the connection box on the hoist gearbox Ultimate Limit To meet European (CE) regulations, a hoist ultimate limit switch prevents damage to the crane by contact between the bottom block and the hoist unit in the event of failure of the over-hoist limit switch by tripping the hoist motor. ©LEEA Academy Overhead Travelling Cranes – Step Notes – Apr 2017 – v1.3 Control and Series Limit Switches Most electric power hoists have the limit switches connected in the control circuit in a parallel arrangement This arrangement means that when one switch is ‘open’ then the other switch is ‘closed’ and motion is still possible in this direction when the push button is depressed. In practice, only one switch can be open at any time Some electric hoists have a second limit switch called the ultimate limit switch This operates when the control limit switch fails. It disconnects the supply to the contactors and should only be reset when the faulty shunt limit has been adjusted or replaced This switch is connected in series and must be reset physically There are two versions of the ultimate limit switch. Control Circuit Type The limit is wired in the main contactor stop circuit and therefore if the normal direction limit fails, the main contactor will break the main supply to the contactors. Series Type The limit has either two or three contacts and is wired directly in the main supply cables to the motor. It must be noted that on older cranes, this is the only type of limit switch fitted. 126 Both types when used as ultimate limits are usually only re-settable manually by maintenance staff who must investigate the reason why the normal limit switch has failed. Series and Parallel Limit Switches ©LEEA Academy Overhead Travelling Cranes – Step Notes – Apr 2017 – v1.3 Notes: 13. Overload Devices 127 Overload Devices for Electric Hoists Circuit and Hoist Overloading Too much electrical current Too much physical load A range of devices are used to avoid circuit overloading, i.e. the circuit being subjected to too great a current, and Mechanical Overloading, e.g. an attempt to raise too great a load, which can result from a fault or from incorrect use. If an attempt is made to use a hoist to raise too great a load the motor will demand an increased current. This raises the motor temperature, leading to insulation burning, shorting and cause the motor to burn out, in addition to the obvious dangers of load bearing components failing. ©LEEA Academy Overhead Travelling Cranes – Step Notes – Apr 2017 – v1.3 Protective devices are used in various ways to limit or prevent such occurrences and each type has its own intended function. Types of Protective Device A fuse or circuit breaker, if properly designed, will prevent circuit overload by isolating the circuit from the power supply before any damage is done o Once they operate, everything on the working side of them is isolated and is inoperative until they have been repaired, replaced or re-set, they are ultimate protection devices Other devices are incorporated into equipment to protect certain parts from damage, e.g. a hoist limit switch, these may then operate to isolate a single component or function but permit other functions to operate. When a hoist limit operates it prevents the block from operating in the hoist mode but still allows the load to be lowered, they are intermediate protection devices Notes: 128 Bi-Metallic Strips Widely used for motor protection and unbalanced currents. The bi‑metal strip consists of two dissimilar metals (e.g. copper and steel) fixed together as a bar. When heated, the strip will bend because one metal will expand at a greater rate than the other. This movement can be used to break contacts in the control circuit to the hoist motor. The illustration below shows a simple arrangement of a thermal relay in a single‑phase circuit: When the load supply exceeds a predetermined value its heating effect causes the deflection of the bi‑ metal strip to open the micro switch and disconnects the supply. ©LEEA Academy Overhead Travelling Cranes – Step Notes – Apr 2017 – v1.3 Thermal Devices Thermistors Negative Temperature Coefficient o With NTC, resistance decreases with temperature to protect against inrush overcurrent conditions. Installed series in a circuit Positive Temperature Coefficient o With PTC, resistance increases with temperature to protect against overvoltage conditions. Installed parallel in a circuit Some hoist motors have thermistors embedded into their stator windings during manufacture. The thermistors are connected via a terminal strip to a relay wired in the control circuit of the contactors. In the event that the temperature of the motor rises to an unacceptable level, the thermistors will trip the relay and render the motor inoperative until it has cooled sufficiently. When the hoist motor has been de‑energised by either an electro magnetic or a thermal device it cannot be restarted until the relay has been reset, normally by a push button. In-Line Thermal Overload Connected in series between the motor contactor and the motor terminals The thermal overload is set at a pre-determined level to trip in the event of temperature increase 129 Fuses A safety device in a circuit that acts as a weak link The fuse breaks the circuit if a fault in an appliance causes too much current flow This protects the wiring and the appliance if something goes wrong The fuse contains a piece of wire that melts easily. If the current going through the fuse is too great, the wire heats up until it melts and breaks the circuit Must be situated in the live conductor, never the neutral conductor Rated in accordance with their current carrying ability, e.g. 13-amp fuse o The rating is the maximum current, which the fuse can carry continuously without deterioration Fuses used with electric hoists should be of the high rupture capacity type (HRC) ©LEEA Academy Overhead Travelling Cranes – Step Notes – Apr 2017 – v1.3 They have good non‑ageing characteristics and they have a high breaking capacity (i.e. will clear short circuits before the equipment is damaged) If equipment is ‘earthed’ to prevent the machine frame becoming live and causing possible electrocution, it is necessary that a fault current 3 times that of the fuse rating can occur in order to blow the fuse quickly. This requires that the earth path resistance must be very low Miniature Circuit Breakers The MCBs disconnect the supply if too large a current flow When the live wire carries the usual operating current, the electromagnet is not strong enough to separate the contacts If something goes wrong with the appliance and a large current flow, the electromagnet will pull hard enough to separate the contacts and break the circuit o The spring then keeps the contacts apart After the fault is repaired, the contacts can be pushed back together by lifting a switch on the outside of the circuit breaker Earth Leakage Circuit Breakers 130 The polarity of the phase winding and neutral winding on the toroid ring is so chosen that, in normal condition of magnetic force, one winding opposes that of another. We assume that in normal operating conditions the current that goes through the phase wire will be returned via neutral wire if there's no leakage in between. As both currents are same, the resultant mmf produced by these two currents is also zero-ideally. The trip coil is connected with another third winding, wound on the toroid ring as secondary. The terminals of this winding are connected to a relay system. In normal operating condition there would not be any current circulating in the third winding as there is no flux in the core due to equal phase and neutral current. When any earth leakage occurs in the equipment, there may be part of the phase current that passes to the earth, through the leakage path instead of returning via metal wire. Hence the magnitude of the neutral current passing through the RCCB is not equal to phase current passing through it. ©LEEA Academy Overhead Travelling Cranes – Step Notes – Apr 2017 – v1.3 Notes: 131 ELCB Operation Normal Condition Load (L) – Neutral Coil (N) = Current (A) As shown in the circuit below, the line input and output are equal therefore the search coil shows no imbalance. ©LEEA Academy Overhead Travelling Cranes – Step Notes – Apr 2017 – v1.3 Earth Fault Load (L) – Neutral Coil (N) = Current (A) Due to earth leakage, the line voltage output current will less than that of the input. The search coil registers an imbalance and generates a current activating the trip coil and opening the circuit. Important Reminder The failure of ultimate devices, such as fuses, call for a thorough investigation by a suitably qualified person before any attempt is made to repair or replace them. It should also be realised that in the case of a serious fault more than one of the protective devices may 132 have operated. Notes: ©LEEA Academy Overhead Travelling Cranes – Step Notes – Apr 2017 – v1.3 Slipping Clutch Slipping clutches, also known as Friction Torque Limiters, are sometimes used in power operated chain hoists and may occasionally be found on overhead travelling cranes. These devices are set to slip when the load increases beyond a predetermined amount, e.g. working load limit plus an allowance which takes into account the effects of dynamic loading. Slipping clutches are ‘direct acting’ rated capacity limiters and act directly in the chain of the drive elements of the hoist. Slipping clutches are also used in some designs of lifting appliances as the upper (hoisting) limit, thereby serving a dual purpose. Slipping Clutch 133 Load Pin Transducer Limit Switch (WLL) Used as an additional form of overload protection on certain wire rope or chain electric hoists The device protects both the hoist and the supporting structure from physical overload ©LEEA Academy Overhead Travelling Cranes – Step Notes – Apr 2017 – v1.3 Lever Operated, Electro-Mechanical Load Limiter A lever-operated overload limiter works in the following manner: 1. The dead-end of the load-rope is fitted to the mechanism. 2. As the load increases, the tension in the load rope increases and pulls the dead end anchor downwards, moving the lever arm. 3. The lever arm is restrained by a combination of cupped washers that are calibrated to offer a resistance to the lever. 134 4. At the end of the lever is a striker: when the arm overcomes the set resistance of the cupped washers, it has moved downwards enough for the striker to contact a micro-switch and disable the 'up' control circuit. 5. When the load is reduced, the lever arm us pushed back into its upper position by the cupped washers: the striker releases the micro-switch and the 'up' circuit is now closed ready for hoisting to commence. The load limiter is set to 110% of WLL to account for dynamic overloading. Rope Operated Load Limiter This device is fitted to one fall of the load rope and the rope is deflected at a shallow angle between the jaw of the strain gauge and the positioning wheels When the rope is under load condition, it tries to pull itself straight. As it does, it pulls the strain gauge anchor with it which is attached to a shaft. Once the shaft reaches a certain pre-set limit, it will open a micro-switch that opens the control power supply to the hoist motor. ©LEEA Academy Overhead Travelling Cranes – Step Notes – Apr 2017 – v1.3 14. Braking Systems Hoist Brakes BS EN 14492-2 states the requirements for brakes that are used for hoisting and lowering movements. Hoists shall be designed in such a way that movements can be decelerated, the load can be held, and that unintended movements are avoided. In addition the rotating masses, the triggering limit of the rated capacity limiter and the maximum speed, e.g. in the event of a phase failure, shall be taken into account. Brakes shall engage automatically in the following cases when: The control device returns to its neutral position; 135 The emergency stop function is activated; The external power supply to the brake is interrupted; The power supply of the corresponding drive (= motor) is interrupted or switched off In addition, in the case of 3 phase motors, brakes must engage when two phases of the power supply to the drive (motor) are interrupted. Failure of Power Supply Electric hoists shall incorporate features so that: The load cannot lower in an uncontrolled manner if a phase should fail The load cannot drop if a phase should fail ©LEEA Academy Overhead Travelling Cranes – Step Notes – Apr 2017 – v1.3 When one phase of a three-phase system is lost, a phase loss occurs. This is also called 'single phasing'. Typically, a phase loss is caused by a blown fuse, thermal overload, broken wire, worn contact or mechanical failure. A phase loss that goes undetected can rapidly result in unsafe conditions, equipment failures, and costly downtime. Phase loss protection devices are relatively inexpensive and simple to install. They provide protection by disconnecting the equipment from the circuit when phase loss is detected. Phase or voltage monitors are the most common solution. Notes: Conical Rotor Motor 136 The sliding rotor principle uses an electric motor specially designed with a conical rotor and stator windings. When power is applied to the motor windings the magnetic field is angular to the centre line of the rotor shaft, operating in effect, two components of force at right angles to each other. The radial component rotates the rotor whilst the horizontal component, pulls the rotor into the windings. ©LEEA Academy Overhead Travelling Cranes – Step Notes – Apr 2017 – v1.3 Notes: 137 Adjustment Brake adjustment must always be carried out in accordance with maker's instructions since incorrect settings will upset motor performance. When the brake lining wears the air gap between the rotor and stator increases and, if not adjusted, will produce erratic motor operation because the magnetic forces will not be powerful enough to move the rotor forward and so will not release the brake. To check if brake adjustment is necessary the rotor should be moved forward manually either by pushing directly onto the shaft or by way of a lever between the brake end cap and the brake wheel. When the rotor is forward as far as it will go, measure the distance between the end of the rotor shaft and the front of the brake end cap. Release the rotor and take a further measurement. ©LEEA Academy Overhead Travelling Cranes – Step Notes – Apr 2017 – v1.3 The difference between the two measurements is the air gap (stroke length) and is usually be between 0.5 and 1.5mm and must never be allowed to exceed 3mm, however LEEA recommends that the appropriate manufacturer's instructions are always followed. If brake adjustment is required, remove the four screws that secure the brake end cap. The brake end cap (which is threaded) can now be turned, and each 90° turn will reduce the air gap (stroke length) by approximately 0.5mm. The securing screws should now be replaced and the air gap checked once more to ensure correct setting. During the first week of operation or after changing the brake lining, the brake should be checked daily, since the lining may wear unequally until bedded in. Ideally it could be argued that the hoist brake should be positioned as near to the hoist drum as possible. For reasons of design accessibility, cooling etc., it is usually on the end of the rotor shaft. The examiner should take the utmost care to satisfy himself that all components are in good working order. Should for example a key shear or the coupling fail, then the load would fall. This drawing shows a cross section of a conical hoist brake. Adjustment is made by removing shims (3) as the lining wears. As shims are removed, the brake end cap 138 and brake lining (1 – shown in red) moves further toward the brake rotor at the end of the rotor shaft and closes the gap. As the brake linings wear down, the path of the rotor displacement increases to a maximum of 3.5mm, after which the braking would become ineffective. It is essential that the movement of the rotor is regularly checked and maintained within the manufacturers limits (approximately 1-1.5mm). Notes: ©LEEA Academy Overhead Travelling Cranes – Step Notes – Apr 2017 – v1.3 Parallel Rotor Principle The brake shown is in the power OFF / brake ON position. The torque springs force the armature plate to the brake rotor and linings preventing the motor drive shaft from moving. The brake shown is in the power ON / brake OFF position with the coil energised and pulling the armature plate against it. This allows the brake rotor to turn as the motor is powered. The air gap is clearly shown between the 139 brake rotor and the coil. The air gap should be checked to ensure that it meets the requirements of the manufacturer to ensure effective use. Brakes (DC Electromagnet) ©LEEA Academy Overhead Travelling Cranes – Step Notes – Apr 2017 – v1.3 The hoist brake is a single disc brake, electro‑magnetic spring applied, DC coil release The coil configuration is of the stator rotor type, direct current is energised to ensure positive action The brake is directly fixed to the main gear case or motor frame and operates on the primary drive shaft Torque is pre-set on factory assembly and should not require further adjustment during its working life The brake is readily accessible for periodic safety checks For additional safety, it is switched independently of the motor supply The fail-safe operation maintains the load in the event of an interruption to the power supply A hand release mechanism is fitted to enable the load to be lowered in the event of power failure The hand release operating handle is detachable and is stored in the brake cover 140 Notes: ©LEEA Academy Overhead Travelling Cranes – Step Notes – Apr 2017 – v1.3 Example of Manufacturer’s Air Gap Settings 141 Travel Brakes Travel brakes may be either the disc or the drum type but in both cases their characteristics need to be a lot different to a hoist brake Braking characteristics have to be finely tuned in order to avoid excessive braking under no load conditions and providing reasonable braking when travelling with a maximum load Disc Travel Brake This is a cross section of a travel brake fitted to a conical rotor motor. A good example of soft travel braking The brake has been greatly reduced on disc and the equivalent of a flywheel has been fitted to the motor shaft This flywheel would have the effect of allowing much smoother acceleration as well as decelerations ©LEEA Academy Overhead Travelling Cranes – Step Notes – Apr 2017 – v1.3 Notes: Thrustor Brake Heavy duty applications Usually electro-hydraulic in operation Centrifugal pump and impeller spinning in oil and developing a pressure head Pressure exerted on a piston directly coupled to the load to be lifted (brake arm) Centrifugal pump driven by AC motor – pressure developed depends on speed of motor Class B insulation, 400v 3Ph 50 Hz motor 142 Main Parts of the Thrustor Brake Base/Arms Rigid wielded construction. Shoes Self-aligning, easily removable high grade cast iron filled with best quality linings fitted with stops. Rods/Grid Rods The tie rod transmits the spring force on shoes by simple lever system. Springs Compression springs are vertically mounted through the grid rods and are held securely between guide plates. One or more springs are used depending on the brake size and thrustor capacity so as to obtain the required braking torque. Operation The braking pressure to the shoes is transmitted from the springs and means of extremely rigid and simple lever/tie rod mechanism. Braking is smooth and positive. Release of the brake shoes is by introduction of a 3 phase mains voltage supply to the thrustor which overcomes the spring force and the shoes are moved clear of the drum by the lever/arm linkage system. ©LEEA Academy Overhead Travelling Cranes – Step Notes – Apr 2017 – v1.3 Checking the Thrustor ALWAYS REFER TO OEM INSTRUCTIONS! Correct operating limits and settings must be gained from the manufacturers data sheets or the crane maintenance manuals. Notes: 143 ©LEEA Academy Overhead Travelling Cranes – Step Notes – Apr 2017 – v1.3 15. Electric Motors and VFDs Electric Motors Electric motors are the most common motive source used with lifting equipment. They therefore form an important part of the study of power operated lifting equipment. Not only are they used to provide the motive force to raise and lower loads, as in hoists and winches, but also to move them, as in travelling hoists and cranes. These different duties call for the motors used for the various functions to have differing characteristics. In this unit we will consider how electric motors work: We will briefly look at how AC motors work We will consider motor duty rating factors AC Motors 3 – phase AC induction motors are used extensively in lifting appliances. There are 3 main parts to the motor: Enclosure (frame) Stator 144 Rotor Electric Motors ©LEEA Academy Overhead Travelling Cranes – Step Notes – Apr 2017 – v1.3 AC Motors Electric Motors When current flows through a conductor, it produces a magnetic field around the conductor. The strength of the magnetic field is proportional to the amount of current. 145 An electrical motor converts electrical energy to mechanical movement. ©LEEA Academy Overhead Travelling Cranes – Step Notes – Apr 2017 – v1.3 Notes: Squirrel Cage AC Motor In squirrel cage motors only the stator has copper coils. The rotor package is a short-circuited aluminium or copper cage that is filled with some conductive material, usually cast aluminium. The rotor bars are slightly angled to increase the efficiency. Cylindrical rotor squirrel cage motors require an auxiliary brake. The brake is mounted on the free end of the motor on the motor shaft. AC Motors In industrial applications most AC motors are three-phase although lighter capacity single phase hoists are 146 available. A three-phase AC electric motor can be wired as shown below. The three poles are arranged at 120 and connected as shown Each pole becomes fully energised at a different time in relation to the others. Hoist motors use 3 phases, the principle works as illustrated below An AC motor creates the revolutions on the rotor Each leg of the 3 phases going to a motor are 120 degrees out of phase with each other, so what happens is the supply, due to the changing of polarity of the supply creates a rotating magnetic field inside the rotor. ©LEEA Academy Overhead Travelling Cranes – Step Notes – Apr 2017 – v1.3 Remember that when we put current into a wire the wire creates a magnetic field around the wire, if you constantly change the polarity of the current being applied to the wire (AC current) and then you have three phases which are 120 degrees out of phase with each other, you get a rotating magnetic field inside the stator, which is what we call the flux. Motor Insulation The stator core and windings are insulated. The type of insulator depends on the operating temperature of the motor. Most motors have type E or F insulation. Class E insulation allows a temperature rise of 70°C whilst Class F permits a rise of 95°C above ambient temperature for totally enclosed motors. Squirrel Cage Motor – Overheating There are no mechanically wearing parts in squirrel cage motors 147 Usually the only thing that burns a motor is overheating A motor burns out when the insulation material around the stator coils heat up too much and melts This causes short circuits, and the motor is no longer functional A burnt motor is either changed or the stator is rewound. The rotor may also be destroyed from overheating Other factors that cause motors to overheat include: o Too many starts (inching) – operator activates high speed first before starting in slow speed o Lifting beyond ED% rating of motor (heavy loads plus lifting time) o Environmental temperature Cooked! ©LEEA Academy Overhead Travelling Cranes – Step Notes – Apr 2017 – v1.3 Notes: 148 Requirements of BS EN 60204 Standard, BS EN 60204-32 Safety of machinery – Electrical equipment of machines states: Clause 7.3 Protection of motors against overheating Protection of motors against overheating shall be provided for each motor rated at more than 2kW This can be achieved by: Overload protection Over temperature protection Current limiting protection Automatic restarting of any motor after the operation of protection against overheating is to be prevented if it can cause a hazardous situation or damage to the machine or work in progress. We will look at hoist overload protection and safety devices later in this course. ©LEEA Academy Overhead Travelling Cranes – Step Notes – Apr 2017 – v1.3 Motor Ingress Protection (IP) Rating IP ratings are used to define levels of sealing effectiveness of electrical enclosures against intrusion from foreign bodies (tools, dirt etc.) and moisture. The table opposite explains the meaning of the IP rating, using the first and second numbers for reference, e.g. IP 40 = 4 – Protected against solid objects over 1mm and 0 = No protection against ingress of liquids. BS EN 60204 requires a minimum of IP23 for all motors. In dusty environments, BS EN 14492-2 requires a minimum IP protection of IP 44, and outdoor motors to have a minimum of IP 54 protection. ED Rating Electrical motors are not only rated according to the power they can generate, but also according to their heat resistance. This is called Efficient Duty. 149 Every motor that is running gets hot due to electrical resistance in the motor The temperature of the motor must not increase above specified values Motors require rest periods to cool down Hoist duty classification specifies the duty factor (ED % = Efficient Duty in percent) and starting frequency (maximum starts per hour) of hoisting motors according to the table below: More starts per hour increases the ED% as well as how much lifting the hoist will do in its work cycles. The ED% is calculated from how much the hoist will lift per each lift and how long each lift will take The ED% is based on a 10-minute period of time An ED rating of 40% means the motor can be operated for an average of 4 minutes in any 10 minute period whilst resting 6 minutes of that period Be aware that after 4 minutes of lifting the motor requires a 6 minute cooling down period ©LEEA Academy Overhead Travelling Cranes – Step Notes – Apr 2017 – v1.3 Another general way of explaining ED% is the maximum number of continuous minutes a motor can be used to lift nominal load in a 10 minute period without overheating the motor. The example hoist data plate below shows that when this particular motor is suppled with a 400v 3 phase 50 hertz supply, the ED rating will be 50%. (Able to run continuously for 5 minutes in every 10). Duty Classification Safe and effective operation of the hoist is dependent on correct classification of the hoist's operating group. Hoists shall be classified in groups of mechanism in accordance with ISO 4301-1 according to the operational requirements and conditions of application. Hoists shall be designed in accordance with FEM 1.001, booklets 1, 2, 3, 4, 5, 8 and 9 and FEM 9.901. We will consider duty classification in the specific hoist modules during this course. 150 Notes: ©LEEA Academy Overhead Travelling Cranes – Step Notes – Apr 2017 – v1.3 Requirements of BS EN 14492 Parts 1 & 2 BS EN 14492 is the current harmonised standard for Cranes – Power driven winches and hoists: Part 1 – Winches Part 2 – Hoists The standard applies to the design, information and use, maintenance and testing of power driven hoists with or without travelling trolleys for which the prime mover is either an electric, hydraulic or pneumatic motor. Annex J of the standard details the requirements for selection of motors in 3 ways: 1. General criteria for the selection of motors and dimensioning of motors according to thermal aspects, usually applying on all sorts of drives in intermittent service 2. Special criteria to dimension motors according to the maximum torque required for lifting motions and according to data on stress occurring during the use of these drives 3. As 2. but details requirements for horizontal drive motors (e.g. travel and traverse motions) Inspection and Examination It is recommended that the following points are checked during the inspection/examination of an electrically powered lifting appliance: Overheating - check cleanliness and correct venting of the motor o Look for signs of burning or paint discolouration on the motor body/housing Vibration 151 o Ensure mountings and fixing bolts are secure o Check that the motor shaft is incorrectly aligned o Check for excessive play in the coupling between motor and transmission equipment o Electrical imbalance, e.g. one phase burnt‑out etc. (Only qualified personnel to check) Running Sound - this will be mainly due to bearings o If they are suspected they should be checked with a listening rod. A perfect bearing gives a whirling sound, whereas a damaged bearing gives a rattle Lubrication - ensure the motor bearings and attachments are adequately and properly lubricated Attachments - check connecting shafts and gears etc. for play and damage which could adversely affect the running of the motor Inverters (Variable Frequency Drives) As we have already studied, the speed of a 3 phase squirrel cage motor can be changed by either changing the number of pairs of poles, or by altering the supply frequency. Many industrial applications require a motor to be operated at a constant speed. Other applications, such as cranes, require the motor to change speed and running direction at a particular point in the operation. Sometimes, speed must remain constant and precise. ©LEEA Academy Overhead Travelling Cranes – Step Notes – Apr 2017 – v1.3 VFD inverters have become very commonplace in the control of overhead travelling crane and other machinery AC squirrel cage motors. Inverter drives can also reduce operating costs while improving productivity. Reduced costs can be realised from: Reliability of drive mechanisms is improved Less downtime Reduction in energy consumption Maintenance costs are reduced Precise and smooth operation reduces wear on mechanical components Inverters can therefore not only provide precise speed control, but also reduce overall operating costs. A VFD (Variable Frequency Drive) inverter operation is sometimes referred to as PWM (Pulse Width Modulation). The inverter changes the 3-phase alternating current (AC) into pulses of positive and negative direct current, (DC). The pulses are combined to simulate the rising and failing sine wave required by the AC motor. 152 PWM is the process of pulsing the DC on and off by quickly switching a number of switches on and off (this can be thousands of times per second), and when this is fed to the motor it has an effect on the current flow. The current actually resembles AC current and so fools the motor into running with an AC power supply, when it is in fact DC. The inverter’s control board signals the power device's control circuits to turn "on" the waveform positive half or negative half of the power device. This alternating of positive and negative switches recreates the 3 phase output. The less time the power device is on, the lower the output voltage and the longer the power device is off, the lower the output frequency. We simply adjust the pulses of DC to the motor in order to adjust its torque and speed. ©LEEA Academy Overhead Travelling Cranes – Step Notes – Apr 2017 – v1.3 Mechanical Brake Control An inverter decelerates a motor to a stop (dynamic braking). The slow down rate is dependent on the set deceleration time when the run command is switched off. The brake simply becomes a ‘parking’ brake as it does not engage until the motor has completely stopped and the inverter switches off the drive command to the motor. This way brake wear is minimized. Only if a failure occurs or the emergency stop button is pushed, the brake closes immediately stopping the motor. It is critically important that the untrained, or inexperienced inspector/examiner does not tamper or interfere with a VFD inverter as this could cause serious health and safety risks and/or physical damage to the crane. Covers should remain intact and safety notices should be strictly adhered to at all times. If in doubt, refer to a Competent Person for advice. Important Reminder It should also be noted that the initial section of the unit is written in a simplistic form that is intended to establish only some basic principles. The aim is to give those with little or no knowledge of the subject a basic understanding and to provide the basis for further study. This module will help examiners/inspectors whom have dealings with electrically powered lifting equipment to understand the principles, recognise the layout and individual items, and be aware of associated dangers. It is in no way intended to provide competence to deal with electrical matters, which must always be 153 dealt with by a suitably qualified person. Safety and Training It is of paramount importance that lifting equipment inspectors or examiners do not work on live electrical equipment. Lock-out/Tag-out routines should always be considered as part of your risk assessment. Under no circumstances should inspectors/examiners whom are not suitably and sufficiently qualified (as required by local legislation) attempt to work on live electrical equipment; this should not be required as part of a thorough examination as the equipment should be isolated following the initial operational/functional checks. ©LEEA Academy Overhead Travelling Cranes – Step Notes – Apr 2017 – v1.3