Colocación Del Hormigón en Condiciones Especiales PDF
Document Details
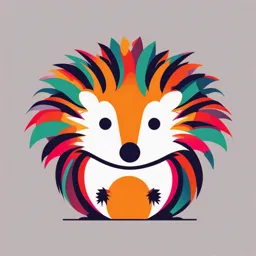
Uploaded by Any
Universidad Central
2015
Tags
Related
- Colocación del Hormigón en Condiciones Especiales PDF
- Colocación Del Hormigón en Condiciones Especiales PDF
- Colocación Del Hormigón En Condiciones Especiales PDF
- Colocación de Hormigones en Condiciones Especiales PDF 2015
- CVE 236: Civil Engineering Materials - Concrete Technology PDF
- Unit 3 Special Concretes PDF
Summary
This document provides information on concrete placement under special conditions, such as underwater or pressurized applications. It covers the techniques and regulations for the proper use of these specialized materials, focusing on concrete design. It is a civil engineering textbook, likely for undergraduate students.
Full Transcript
Colocación Ho del Hormigón en Condiciones Especiales Hormigonados especiales como por ejemplo, bajo el agua o soplado son de gran uso en la construcción civil por lo que se hace imperioso conocer técnicas y normativa para poder hacer uso correcto de este material. Construcciones II...
Colocación Ho del Hormigón en Condiciones Especiales Hormigonados especiales como por ejemplo, bajo el agua o soplado son de gran uso en la construcción civil por lo que se hace imperioso conocer técnicas y normativa para poder hacer uso correcto de este material. Construcciones II [email protected] Universidad Central [email protected] Carrera de Ingeniería Civil 2015 2 [HORMIGONADOS ESPECIALES] 1. Hormigón Autocompactable.- 1.1.- Generalidades.- El concreto autocompactable puede ser colocado en un molde en solo lugar y fluir 30 metros o más sin segregación. Es tan fluido que su consistencia se mide en “flujo de revenimiento”. Cuando un cono estándar de revenimiento se llena y se levanta, se mide el radio de la extensión de la mezcla fluida, más que la distancia a que se derrumba y el flujo de revenimiento puede ser de hasta 85 cm. Este concreto evolucionó a partir de las tecnologí́as usadas en la colocación del concreto bajo el agua en 1988 por el profesor Okamura, en la Universidad de Tokio. En 1989, Master Builders, de Cleveland, desarrolló e introdujo en el mercado concreto de alta resistencia con un flujo de revenimiento de 58 a 66 cm, en una construcción de gran altura. Sin embargo, este concreto aún requería algo de vibración mínima para la compactación. 1.2.- Concepto.-Es un concreto muy fluido, y sin embargo estable, que puede fluir rápidamente al lugar y llenar los encofrados sin experimentar compactación y sin segregación significativa. Se trata de un diseño de mezcla muy controlado, con pocas opciones para su ajuste en sitio. El autocompactable es un concreto “hipersensible”. Pequeños cambios en la mezcla, sobre todo en la cantidad de agua, pueden tener muy grandes repercusiones. Los tres componentes principales del autocompactable incluyen una mezcla de concreto apropiadamente proporcionada, diseñada para la aplicación, un reductor de agua sintético de alto rango o superfluidificador, y a veces un aditivo modificador de la viscosidad. Las cantidades de cada componente pueden variar para el logro de un amplio rango de resultados. Los beneficios de los concretos auto- compactables incluyen, sobre todo, su trabajabilidad en el estado plástico, más que el mejoramiento de las propiedades en el estado endurecido. Por lo tanto, las pruebas más importantes son aquellas que definen su consistencia y fluidez, o sea, la reologí́a de la mezcla. Puesto que no hay pruebas estandarizadas para concreto autocompactable, se han usado un cierto número de métodos. Las pruebas sugeridas para definir las caracte- rí́sticas de una mezcla de autocompactable son: Fluidez.- Más que medir el asentamiento vertical –revenimiento- tal como lo hacemos con el concreto normal, con el concreto autocompactable medimos el flujo del revenimiento horizontal. El auto-compactable puede ser producido de modo que tenga una dimensión de flujo del revenimiento de entre 50 y 76 cm, dependiendo del requisito de la obra. Tasa de flujo.- La prueba T 50 mide cuánto tiempo tarda un concreto auto- compactable en alcanzar un radio del flujo de revenimiento de 50 cm. Fig.# 1 ( Prueba T 50) Capacidad para fluir en un espacio confinado.- Es una de las características definitorias del concreto autocompactable. La prueba de Caja L puede usarse para medir esta propiedad, [email protected] [HORMIGONADOS ESPECIALES] 3 permitiendo que el concreto fluya a través de una caja en forma de L, con varias rejillas de varillas de refuerzo para inhibir el flujo de concreto. Fig.# 2 ( Prueba de la Caja L) Estabilidad.- La capacidad para resistir la segregación –la estabilidad de la mezcla– es una de las cualidades más importantes del concreto autocompactable. La estabilidad típicamente se “mide” usando el índice visual de estabilidad, una clasificación visual desde cero hasta tres en incrementos de 0.5. Fig.# 3 ( Ensayo del índice visual de estabilidad (valor índice=0)) Construcciones II 4 [HORMIGONADOS ESPECIALES] Fig.# 4 ( Ensayo del índice visual de estabilidad (valor índice=1,5)) 1. Hormigón Sumergido.- El hormigonado bajo agua incluye tanto elementos estructurales como elementos no estructurales. También se puede utilizar para añadir peso para hundir las secciones de prefabricado de túneles o en cimentaciones, pozos o lugares inundados donde no es posible agotar el agua por bombeo o gravedad. Las recomendaciones que se dan a continuación son aplicables al hormigonado bajo el agua de grandes volúmenes aunque también son aplicables a pequeños volúmenes. ( Revisar Norma ACI 304R-000). En el caso de hormigonado bajo agua, la colocación adquiere características particulares inherentes al hecho de que no existe visibilidad del hormigón en el sitio, lo cual impide ejercer un control efectivo que permita corregir los efectos que pudieran producirse por lo que es necesario tomar precauciones tanto de diseño de la mezcla como de colocación. Los materiales deben cumplir las especificaciones. Además, deben ser seleccionados por su contribución para mejorar las características del hormigón para fluir. 1.1.- Cemento.- Es importante que le hormigón fluya sin segregación, de ahí́́ que el enfoque al efectuar las dosificaciones sea el de obtener una mezcla con una alta trabajabilidad. Por ello es recomendable mezclas relativamente ricas en cemento (350 Kg/m3. Para hormigonados en el mar incluso 400 a 500 Kg/m3) para compensar el lavado de dicho cemento y para proveer al hormigón de suficiente fluidez y el empleo de aditivos cohesionantes. El empleo de puzolanas [email protected] [HORMIGONADOS ESPECIALES] 5 como adición es favorable debido a que mejoran las características de fluencia. (del 20 al 30 % del peso del cemento o usar cemento puzolánico). 1.2.- Relación Agua/Cemento.- Teniendo en cuenta que la cantidad de agua añadida a la mezcla es uno de los factores que determinan directamente las resistencias tanto iniciales como finales del hormigón, la relación agua/cemento deberá mantenerse lo más baja posible. Se recomiendan mezclas con una máxima relación agua/cemento de 0,45. 1.3.- Áridos.- El tamaño máximo de árido usado en el hormigonado bajo agua es normalmente de 19 mm. Áridos más gruesos (25 mm) pueden ser utilizados dependiendo de la disponibilidad del árido, del espacio entre armaduras, y del mantenimiento de la trabajabilidad del hormigón. Es deseable un contenido de árido fino comprendido entre 45% y 55% del volumen total y un contenido en aire de hasta un 5%. Se usa comúnmente un asentamiento comprendido entre 15 y 22,5 cm siendo adoptado el mayor con armadura abundante o cuando el desplazamiento horizontal es apreciable. En cuanto a su forma, el ideal para los agregados redondeados es la esférica y para los agregados angulosos, es la cúbica. Los que tienen formas laminadas, aplanadas y largas, cilíndricas o formas torcidas, dan mezclas poco trabajables y con tendencia a causar 1.4.-Aire incorporado.- Es esencial en hormigón sumergido en agua de mar ya que permite lograr mayor plasticidad. Por la distribución uniforme del aire en la mezcla, estos esferoides de aire, obran a la vez como un árido fino y como un sistema de “rodamiento de bolas” que facilitan la movilidad y acomodamiento del agregado grueso. Los beneficios que se pueden obtener con el uso del aire incorporado, son: a.- Disminución del contenido de arena en un volumen absoluto igual al del aire incorporado. b.- Disminución del agua de amasado, sin pérdida de asentamiento. c.- Mejoría de la trabajabilidad y disminución de la razón agua cemento. d.- Los glóbulos, se constituyen en una defensa contra la segregación y exudación, lo que facilita el transporte, vaciado y da un mejor acabado superficial. Su porcentaje varía de un 5% a 7%(dependiendo del tamaño máx. del agregado). Actúan también como válvulas de absorción de presiones internas y como freno a la penetración salina. 1.5.- Aditivos.- La elección de aditivos tiene que ser cuidadosa ya que en este tipo de hormigonado hay que tener en cuenta tanto la fluidez (cono 15-20 mm) como la consistencia (que tiene que ser suficientemente cohesiva). La mejor solución es el empleo de un superplastificante/reductor de agua de alta actividad que, al permitir una mayor reducción de agua, proporcionará hormigones más duraderos y resistentes. Aditivos retardantes son beneficiosos en grandes emplazamientos debido a la importancia de mantener el asentamiento. En este tipo de hormigones es muy importante la cohesión para evitar el lavado de la mezcla por lo que también se pueden utilizar aditivos cohesionantes. 1.6.- Consolidación y curado.- los hormigones sumergidos no podrán apisonarse y menos vibrarse, porque con ello se desintegrarían, por lo tanto, lo que más se acepta, es que durante el hormigonado, se golpeen suavemente los encofrados (de existir) con un combo de madera, con el fin de ayudar a la eliminación de las burbujas de aire y así, obtener una mejor compactación. Lo más difundido en el uso de hormigones con características autocompactantes. 1.7.- Puesta en obra.- El hormigonado bajo agua no presenta más problemas que el lavado de la pasta de cemento o de mortero que puede ocasionar el agua en movimiento; si éste problema no existe, se conseguirán buenos hormigones ya que el medio es muy adecuado para una hidratación y curados perfectos además la propia presión del líquido ayuda a su compactación. En ningún caso se tolerará la colocación en obra de masas con indicios de fraguado. a) Técnica Tremié (Tubo-Tolva).- Este proceso o técnica, consiste en colocar el hormigón en obra, por medio de un tubo, cuyo extremo inferior queda siempre embebido en el hormigón fresco, de modo que el lavado y segregación son substancialmente prevenidos, se emplea en diversos propósitos, incluyendo hormigones sumergidos, estructuras submarinas, reparaciones de hormigones sumergidos, construcción y juntas de secciones de túneles submarinos, pilas para fundaciones de estructuras tales como: puentes y plataformas de costa adentro. Este proceso Construcciones II 6 [HORMIGONADOS ESPECIALES] puede ser usado en casos que se quiera lograr una muy alta calidad estructural, y se han logrado exitosas operaciones de hormigonado en profundidades de hasta 50 m, como el hormigonado de machones de puentes. La instalación utilizada, se compone de tubos de 25 a 45 cm., de diámetro, soportados por un puente grúa con cabrestantes móviles, que permiten subir y bajar el tubo, toda la instalación va montada en un andamio con plataforma de servicio. Gracias al cabestrante por una parte y al puente grúa por otra, es posible cubrir con precisión toda la zona a hormigonar. El tubo “tremie” debe permanecer fijo, sin movimientos horizontales, mientras fluye el hormigó n. El movimiento horizontal del “tremie” dana la superficie del hormigó n colocado, crea lechadas adicionales y posiblemente una pé rdida del sellado. La distribució n horizontal del hormigó n se realiza por colocación oscilante, moviendo el tubo, restableciendo el sellado y reanudando la colocación. Fig.# 5 ( Técnica Tremie) Comentarios: En general no se debe verter el hormigó n cuando la velocidad del agua supera los 2 m/s. El tubo “tremie” debe permanecer siempre introducido en la masa del hormigó n de 1 a 1,5 metros para que no se produzca el efecto de caída libre que favorezca el lavado. Además el tubo “tremie” tiene que estar permanentemente lleno para evitar la entrada de agua y se debe contar con la ayuda de buzos especializados para supervisar la buena ejecución del proceso. El tubo termina en su parte superior en una tolva o un embudo para el vertido del hormigón. Se usa tolva cuando se está operando con aportaciones intermitentes de hormigón, Ej. Transporte por cubas. Se usa embudo cuando se está operando con aportación continua, Ej. Hormigón bombeado. La operación de hormigonado comprende tres fases: Cebado del tubo; formación del Bulbo y Vertido. Cebado del tubo: se debe llenar completamente el tubo con hormigón, sin contacto con el agua que contiene. Para esto pueden imaginarse varios artificios (hasta el empleo de aire comprimido), pero el más sencillo parece ser, hacer bajar por el tubo un tapón perdido, que actúe como sello estanco, de modo que la columna de hormigón baje lentamente, sin contacto con el agua y evitar segregación por caída libre; o bien, reemplazar el tapón por una cámara de pelota inflado que se recupera luego de cada cebada. Fig.# 6 ( Método de tapón o bola deslizante para tubería Tremie) [email protected] [HORMIGONADOS ESPECIALES] 7 Fig.# 7 (Método de sellado inferior para tuberías Tremie) Formación del bulbo: bajo el empuje del peso de la columna de hormigón fresco, este, por efecto de la tensión superficial se extiende progresivamente alrededor del tubo, cuyo extremo inferior no debe estar levantado más de 30cm. del fondo, con el fin de evitar la segregación y lavado. Luego, bajo el efecto de la resistencia sobre el fondo, así como por la resistencia en la masa, la superficie toma la forma de una cúpula, en la que, con el tubo hundido a la profundidad deseada, se forma el bulbo en la base. Vertido: en tales condiciones puede realizarse el vertido, desplazando el tubo, mediante el cabestrante y el puente grúa. El tubo debe estar permanentemente lleno, realizándose la carga del hormigón regular y continuamente, con el fin de asegurar que no se descebe, dando lugar a la entrada del agua. El peso del hormigón contenido en el tubo, debe ser en todo momento, superior al efecto de la presión del agua en su base. Siempre, se debe contar con la ayuda de buzos especializados para supervisar la buena ejecución del proceso. Además, esta faena se debe programar de modo que coincida con la alta marea, para tener la seguridad de trabajar con mar tranquilo. Un hormigón tremie bien hecho, puede dar resistencias de 282 Kg/cm2. Su adherencia es buena con el acero, roca, madera y otros hormigones, cuando es puesto bajo el agua. b) Hormigón Ensacado.- Este método se usa para construir muretes o plataformas bajo el agua o para formar la base de una cimentación, ej. Muros de muelles o malecones, siempre la arista más cargada descansa sobre un murete de hormigón en sacos, que transmite los esfuerzos a un fondo de cimentación satisfactorio, descansando el resto, sobre un macizo de escollera. Similar método, se ha usado para sellar juntas, soportar o proteger del oleaje y corriente a elementos prefabricados o tuberías submarinas, en orden de prevenir movimientos dando soporte y protección. Dos métodos son usados para ensacar el hormigón: b.1.-Mezcla de hormigón seco es ensacada.- Se llena hasta la mitad y se cierra, luego es sumergido por medio de pallets y es colocado en obra por un buzo. El cemento se va hidratando, según el agua va penetrando. Este método tiene la ventaja de que el tiempo de manipulación y colocación no es crítico, pero la hidratación es baja y el saco puede ser dislocado por las olas y/o corrientes, antes de que haya fraguado. La adherencia entre sacos adyacentes puede no ser bueno y el cemento puede no ser distribuido uniformemente en la mezcla. Construcciones II 8 [HORMIGONADOS ESPECIALES] Fig.# 8 (Hormigón sumergido en sacos) b.2.-Mezcla de hormigón con un asentamiento de cono bajo, y de estado plástico; los sacos a usar pueden ser de arpillera o yute, deben ser flexibles para que formen un cuerpo entre sí y no deben llenarse completamente (hasta 2/3 de su capacidad), la arpillera deberá estar escardada, y la tela empapada con una lechada muy clara antes de recibir el hormigón. El saco una vez cerrado, puede envolverse en una malla galvanizada de 2 mm y trama 5 cm. Los sacos se sumergen en pallets y envueltos en una funda (manga de polietileno, del doble de diámetro que los sacos y con sus dos extremos abiertos). Luego un buzo sostiene el saco en posición y el otro extrae la funda. Una pareja de buzos puede colocar en obra de 250 a 300 sacos en un día (con un promedio de profundidad de 10 m.). Con este método, se puede lograr una muy buena adherencia con el fin de obtener una obra monolítica, se asegura una total hidratación y la calidad general del hormigón puede ser controlada. Cuando se trata de sellar juntas en que no se requiera adherencia, el hormigón puede ser colocado en bolsas de polietileno de alta densidad, para prevenir cualquier lavado de éste. A veces, para el mejoramiento de fondos, se han sumergido mediante grúas, grandes bolsas que contenían varios metros cúbicos de hormigón. c) Hormigón por Talud que Avanza.- Este procedimiento o técnica, sólo aplicable bajo pequeños espesores de agua (inferiores a 80 cm.). El hormigón se deposita en A, se incorpFigFora por peso a la masa B en fluencia que avanza con un talud C, que es el único en contacto con el agua y sometido al deslavado. Fig.# 9 (Esquema para hormigonado por talud que avanza) [email protected] [HORMIGONADOS ESPECIALES] 9 Es necesario actuar continuamente para evitar los movimientos del agua sobre este talud, en el que efectivamente se forman lechadas (mezcla de cemento y arena muy fina), que no fraguan y que crearían en el macizo planos de deslizamiento y ruptura. Después de cada interrupción, se limpia el talud con escobillas de acero para descarnar la superficie, eliminar los excesos de lechada, que después se bombearán sin agitación. La dosificación a ocupar, es la misma del hormigón tremie estructural, el macizo en avance no puede apisonarse ni vibrarse. La faena se debe programar para hacerla en marea alta, si el mar se agita, hay que interrumpir el trabajo. d) Hormigón en Cubas.- Esta técnica se aplica en profundidades de agua superiores a 80cm. El hormigón atraviesa la capa de agua en una cuba perfectamente estanca, que se hace bajar lentamente, mediante cabestrante o grúa hasta llegar al macizo a hormigonar. La cuba se deposita sobre el macizo y un buzo la abre, elevándose después suavemente para que el hormigón fluya en agua tranquila. Fig.# 10 (Cubas) Este método se debe proscribir, cuando se debe verter en un encofrado de dimensiones reducidas, pues el ascenso y descenso de la cuba, produce un efecto pistón que agita el agua, produciéndose remolinos en el agua que rodea al hormigón fresco, con resultados desastrosos. Es especialmente apropiado, cuando se trata de hormigón en masa, hormigones ciclópeos, en que capas de rocas son alternadas con capa de hormigón, cubrimientos y protección de tuberías submarinas. En aguas poco profundas, en donde las olas y la acción del viento pueden tender a lavar al hormigón tremie, puesto por medio de un tubo; el hormigón en cuba, puede ser más estable y puede ser puesto con un asentamiento de cono bajo, se pueden usar agregados de hasta 20 mm. Las cubas son recipientes perfectamente estancos, con paredes inclinadas para facilitar la salida del hormigón, se abren por el fondo por sistemas hidráulicos y/o neumáticos, además llevan un sistema de pata que le permiten posarse con seguridad, quedando la cuba a cierta altura, de modo que las portezuelas pivotean libremente. La capacidad de las cubas varía de 200 a 1000 L. Durante la operación, las cubas vacían su carga primero en el fondo y luego, sobre las capas anteriormente vertidas aún frescas, por tanto, el hormigón no entra en contacto con el agua, sino Construcciones II 1 0 [HORMIGONADOS ESPECIALES] al extenderse, de modo que se logra una buena trabazón. Cuando el área a hormigonar sea grande, se subdivide en secciones pequeñas, no mayores a 6x6m., ya que el hormigón tiene un radio de extensión de 30 cm. y las cubas no se abrirán a mas de 30 cm., de altura. Una variante del sistema, que se emplea en obras de poco volumen de hormigón, consiste en ocupar bolsas de lona impermeabilizadas, que se bajan boca a bajo, amarradas por el fondo y cerradas en la boca por medio de un nudo de maniobra, que permite abrirlas manualmente. Su capacidad no sobrepasa de los 100 L. La labor de los buzos, se limita a ubicar el capacho sobre el punto a hormigonar y abrirlo, luego enviarlo a la superficie para repetir el ciclo. Fig. #11 (Cuba bajo el agua en un encofrado de dimensiones reducidas) El método de la inmersión en cubas, tiene las ventajas de tener una operatoria sin complicaciones y rapidez de hormigonado, se logran hormigones de buena calidad, con excelente trabazón y no exige más aparatos especiales, que el depósito para sumergir el hormigón. [email protected] 1 [HORMIGONADOS ESPECIALES] 1 2. Hormigón Proyectado.- El hormigón proyectado es actualmente, un elemento indispensable en los procedimientos de sostenimiento y revestimiento estructural de túneles y taludes, sin embargo de aquello se lo utiliza también en: Revestimiento de grandes muros de albañilería. Reparación de Obras de Hormigón. Revestimiento de Paredes Rocosas para evitar derrumbes. Reparación de Obras de Hormigón. Fundición de Placas Arquitectónicas Delgadas. Fig. #12 (Trabajos con Hormigón Proyectado) Es importante aclarar algunas definiciones: Se entiende por gunitar la puesta en obra de un hormigón o mortero proyectado con aire a presión a través de manguera, a gran velocidad sobre un soporte. El hormigón o mortero proyectado “gunita” tiene características de: Baja relación A/C, buena compactación "in situ", alto contenido de cemento, etc. El hormigón proyectado es un hormigón cuyo tamaño máximo de áridos es superior a 8 mm, y que aplicado a máquina, se proyecta a gran velocidad sobre un soporte a través de manguera y boquilla. El empleo de áridos finos o gruesos, o una mezcla de ambos, se hará de acuerdo con el espesor a aplicar en el hormigón proyectado. En general, no se utilizan áridos con tamaños > 15 mm. El mortero proyectado es un mortero cuyo tamaño máximo de áridos no excederá 8 mm, y que aplicado a máquina, se proyecta a gran velocidad sobre una superficie a través de una manguera y boquilla. En la actualidad se usan tres procesos distintos, que son: Mezcla húmeda y Mezcla semi-húmeda. Mezcla seca El proceso de mezcla húmeda conlleva el empleo de más servicios, pero su uso está generalizado para grandes aplicaciones. El sistema de mezcla semi-húmeda, que consiste en la dosificación del agua, aproximadamente 5 metros antes de la boquilla, es un proceso que evita fundamentalmente que la mezcla seca se disperse (especialmente el cemento) a la hora de hacer la proyección. Cuando se confecciona un proyecto en el cual se especifica una Resistencia a Compresión Simple de un hormigón proyectado, se suelen definir las resistencias a 24 horas, 7 días, y 28 días, para cumplir las necesidades de sostenimiento. Estas resistencias dependen de: Áridos, cementos, Construcciones II 1 2 [HORMIGONADOS ESPECIALES] personal especialista, maquinaria, medios auxiliares, aditivos (acelerantes, estabilizadores, superplastificantes, etc.), y adiciones. 2.1.- Sistema de mezcla seca.- El sistema de mezcla seca consta de una serie de fases, y requiere equipos especializados. Fig. #13 (Sistema de Mezcla Seca) Es un procedimiento mediante el cual todos los componentes del hormigón se mezclan previamente, excepto el agua, que se añade en la boquilla antes de la proyección de la mezcla, transportándose la mezcla en seco a través de mangueras de forma neumática hasta la boquilla. 1º El cemento y los áridos se mezclan adecuadamente hasta conseguir una perfecta homogeneidad en proporciones variables. Lo normal es usar cemento Portland, sin embargo, a menudo se emplean cementos especiales, junto con diferentes clases de áridos (artificiales o naturales, de río o machaqueo). 2º La mezcla de cemento/áridos se introduce en un alimentador del equipo (junto con acelerante en polvo si se emplea). 3º La mezcla entra en la manguera mediante una rueda o distribuidor (rotor). 4º La mezcla es transportada mediante aire a presión (flujo diluido) hasta una boquilla o pistola especial. Esta boquilla va equipada con un distribuidor múltiple perforado, a través del cual, se pulveriza agua a presión (junto con acelerante líquido si se emplea), que se mezcla con el conjunto cemento/áridos. 5º La mezcla ya húmeda se proyecta desde la boquilla sobre la superficie soporte que debe gunitarse. El uso de aditivos estabilizadores de fraguado en la proyección de hormigón por vía seca, es necesario cuando la humedad de los áridos es superior al 5%, y el tiempo de transporte superior a 1,5 horas. 2.2.- Sistema de mezcla semi-húmeda.- Este sistema idéntico en sus primeras fases al de la mezcla seca, únicamente difiere de él en que, a una distancia aproximadamente de 5 m de la boquilla, se efectúa la adición de agua, y se puede, y debe, humedecer los áridos, hasta un 10 %, por lo que se mejoran las propiedades de la mezcla al llegar a la boquilla, de la que saldrá el mortero u hormigón proyectado. Otra de las ventajas de este sistema, es que evita el polvo resultante de la proyección, así como la pérdida de cemento en la mezcla al salir de la boquilla. También se puede considerar que el agua añadida se incorpora perfectamente durante esos 5 m a la mezcla, haciéndola más homogénea, y lo que es más importante, que la relación agua/cemento sea adecuada. 2.3.- Sistema de mezcla húmeda.- La gunita posee propiedades específicas que se manifiestan especialmente a través de la naturaleza del método de colocación. La gunita de mezcla húmeda consigue morteros y hormigones de propiedades equivalentes a la mezcla seca con técnicas de dosificación y aditivos, pero se consigue una disminución importante de la dispersión de resultados, causa y preocupación del control de aplicación. Las máquinas de mezcla húmeda producen mortero u hormigón proyectado, por dos procedimientos fundamentales en Flujo diluido y Flujo denso, (Rotor y Bomba), con grandes rendimientos, cubriendo de este modo sobradamente las aplicaciones de las máquinas de mezcla seca. Estas máquinas se limitan a un bombeo a alta velocidad a través de conductos rígidos y [email protected] 1 [HORMIGONADOS ESPECIALES] 3 flexibles hasta una boquilla, provista de un chorro de aire comprimido, con lo que se obtiene un mortero u hormigón de compactación relativa. No obstante, debe añadirse haciendo honor a la verdad, que los recientes progresos, tanto de nuevas máquinas como de aditivos estabilizadores, han conducido esta tecnología a un sistema perfectamente compatible con el fin deseado y con una ventaja importante: La no-formación de polvo y el mantenimiento de la relación Agua/Cemento. Fig. #14(Sistema de Mezcla Húmeda) Para el caso particular de la vía húmeda, la mezcla debe transportarse desde la planta hasta el tajo, permitiendo allí el bombeo de la misma. Por ello, al margen de un detallado estudio de la mezcla de áridos a emplear, se emplearán aditivos superplastificantes capaces de reducir el agua de amasado, y garantizar la consistencia adecuada durante la puesta en obra del hormigón. Atendiendo a la manejabilidad prevista (p.ej. trabajos en túneles por la noche), es habitual el uso de aditivos estabilizadores de fraguado. Con estos aditivos, tras las correspondientes pruebas de campo para determinar la dosificación óptima en cada caso, se consigue mantener una consistencia adecuada para trabajar transcurridas varias horas (hasta 36 horas), sin penalizar las características del hormigón proyectado, ya que el proceso se detiene hasta que se añade el aditivo acelerante en la boquilla del robot. Fig. #15 (Hormigón Bombeable) (Hormigón No Bombeable) Construcciones II 1 4 [HORMIGONADOS ESPECIALES] Fig. #16 (Máquina para “Gunitar” Hormigón) 2.4.- Aplicación.- La calidad de la gunita depende fundamentalmente de los operarios, es esencial que éstos asistan a cursillos, y reciban una formación completa de su especialidad. Fig. #17 (Pistón de la máquina para “gunitar”) El Capataz, Jefe de Equipo, o Encargado debe poseer una gran experiencia, y haber prestado durante un mínimo de cinco años servicio como gunitador. El gunitador, debe por lo menos haber pasado por un aprendizaje de un año de duración, y poseer experiencia en trabajos de naturaleza semejante. La experiencia del gunitador deberá probarse, para ello, se ensayará con un revestimiento de paneles de prueba como parte del programa de ensayos previos a la construcción. Un equipo mínimo consta de: Un gunitador Un maquinista Un operador de la planta de mezclado Un Capataz o Jefe de Equipo Eventualmente, será necesario, que el gunitador tenga un ayudante, así como contar con varios operarios para realizar el transporte, la colocación de andamiajes, etc. Para realizar una buena aplicación del hormigón proyectado es requisito esencial la correcta organización del trabajo. Esta corre a cargo del Capataz o Jefe de Equipo que dispondrá los [email protected] 1 [HORMIGONADOS ESPECIALES] 5 trabajos y observará, que todos los equipos funcionen correctamente, tomando para ello, las precauciones necesarias y adoptando las correspondientes medidas preventivas. Es fundamental que antes de comenzar el trabajo se decidan las instalaciones, ya que éstas servirán de base al funcionamiento posterior y al buen resultado del sistema, y por ello, es muy importante elegir debidamente las zonas de acopio de acelerantes, la situación y distancia de la planta de mezclado (transporte), y la situación de la maquina gunitadora, que debe ocupar el punto más ventajoso para cubrir la zona de trabajo en abanico. 2.4.1.- Aplicación en túneles.- La instalación de la planta de mezclado deberá ser exterior, y por medio del transporte elegido se introducirá la mezcla dentro del túnel hasta la zona de gunitado. En este tipo de trabajo conviene eliminar toda la mano de obra posible, automatizando los sistemas de recepción de mezcla, así como los de proyección. Fig. #18(Aplicación de Hormigón Proyectado en Túneles) 2.4.2.- Aplicación en taludes.- En este caso, conviene que la planta de mezclado se sitúe en la parte superior, si hay acceso, con lo cual se ganará en presión y caída de los materiales por gravedad hasta la situación de la máquina gunitadora. Fig. #19(Aplicación de Hormigón Proyectado en Taludes) 2.5-. Técnicas de Ejecución.- Las técnicas de ejecución que se van a detallar a continuación, son producto de la experiencia de muchos años de trabajo en el campo de la gunita y del hormigón proyectado, lo que significa, que se debe tender hacia su utilización para unificar criterios y ejecuciones. Construcciones II 1 6 [HORMIGONADOS ESPECIALES] En las especificaciones del hormigón proyectado, independientemente de las resistencias a compresión necesarias, tendrá que aparecer, el acabado necesario, dosificación y espesores correspondientes, pudiendo influir tanto en la elección de la máquina y de la dotación del equipo humano, como en el orden del trabajo y la colocación de andamiajes o robot. Por lo general, el gunitador trabajará de abajo arriba, e irá rellenando las armaduras, de tal manera, que queden completamente embebidas en el gunitado evitando la aparición de arenas sueltas detrás de los redondos. También colocará las señales, guías o maestras necesarias para llegar al espesor previsto. El gunitador debe dirigir al maquinista mediante señales con la mano respecto a la producción y velocidad del suministro. Si éste es demasiado fuerte, la presión debe ser disminuida, así como la velocidad del motor, con el fin de producir la mejor proyección. Estos factores contribuyen a la correcta alimentación de la máquina. Es importante facilitar a los operarios las características de la maquinaria a emplear, que suele suministrar el fabricante, así como las recomendaciones que cubren todas las combinaciones en caso de duda. Como resumen podemos definir que el equipo del gunitado debe estar conjuntado y conocer una a una, todas las operaciones, para que sin necesidad de dirigirles, cada uno de ellos solvente las distintas situaciones que se puedan presentar. 2.6.-Preparación de superficies.- Todo tratamiento de hormigón proyectado (gunita) necesita una preparación de superficies, según como sea el soporte. Esta preparación de superficies, será con chorro de aire a presión, chorro de aire y agua a presión, chorro de agua a alta presión chorro de arena, en este último caso, para los soportes de hormigón (Reparación). Como norma, se debe retirar los restos de materiales sueltos o de otros oficios que estén sobre el soporte, evitando la creación de falsas zonas que no adhieran al revestimiento posterior. En líneas generales se deberá hacer siempre la preparación de superficies mediante humectación del soporte para conseguir unas condiciones adecuadas. 2.7.-Proyección.- Una vez elegido el tipo de máquina, así como el diámetro de las mangueras de proyección, el funcionamiento será el siguiente: 1º Comprobación de las mangueras de proyección para ver si están limpias, para ello se conectan a un compresor que disponga de un manómetro, si éste muestra una presión superior a la normal, quiere significar que las mangueras están sucias. En este caso, deben limpiarse doblándolas, torciéndolas o golpeándolas suavemente con un martillo, volviendo a dar aire y expulsando así el material alojado en los conductos. 2º Conectar las mangueras formando el menor número posible de curvas, y a ser posible sin ningún rizo, para ello, las uniones de manguera se asegurarán debidamente. 3º Comprobar la salida del agua o del aditivo, para los casos de vía seca o húmeda respectivamente, así como el funcionamiento de las bombas, en el caso de que se utilicen. Esta comprobación se hará quitando la tobera de la boquilla, y desatrancando si es preciso, los eyectores de agua o aditivo acelerante a la misma. Esta operación se deberá efectuar con la boquilla hacia abajo, para prevenir que la corriente de agua o aditivo vuelva hacia atrás por la manguera. 4º Estando funcionando el agua o aditivo se deberá dar entrada al aire comprimido exclusivamente, con lo cual, se examinará el abanico que forma la pistola, viendo inmediatamente si existe algún fallo de suministro en los eyectores, para lo cual, visto éste, se deberá solucionar limpiando o cambiando la boquilla. Si el abanico es débil quiere decir que no hay suficiente presión de aire, en este caso, se deberá incrementar la misma. Una vez pasada esta operación, el gunitador está preparado para comenzar el trabajo. La primera operación será la de proyectar una mezcla de aire y agua sobre el soporte, a fin de humedecer la superficie. Esta práctica es recomendable para todo tipo de soporte, hormigón, madera, arpillera, roca, tierra o acero. La manguera esta ahora conectada con la boquilla y la gunitadora, y la proyección puede comenzar. El gunitador mantendrá la boquilla (pistola) hacia abajo, en espera del suministro de la mezcla. Cuando la mezcla llegue, regulará rápidamente el suministro y dirigirá el chorro al soporte al revestir. La distancia entre el soporte y la boquilla o pistola estará situada entre 0,6 y 1,5 m, moviendo la boquilla rítmicamente en series de rizos de lado a lado y de arriba abajo, trabajando así de modo uniforme [email protected] 1 [HORMIGONADOS ESPECIALES] 7 En caso de cualquier irregularidad en el suministro de la mezcla, o de escasez de este material, el gunitador debe dirigir la boquilla fuera del trabajo, hasta que la alimentación vuelva a ser adecuada. Si el chorro de mezcla que sale de la boquilla, disminuye de repente, indica una obturación parcial o una avería en la boquilla. En el caso de que el abanico se haga desigual, el trabajo se debe parar y limpiar o cambiar la parte afectada (inyectores). Conseguida una uniformidad de proyección, el desarrollo del trabajo está ahora en manos del gunitador, que debe dirigir constantemente al maquinista, para que regule el abastecimiento aumentando o reduciendo la presión así como la velocidad. La habilidad y conocimientos del gunitador determinarán la calidad del trabajo terminado, así como el rendimiento del mismo. Al terminar el trabajo se deberán limpiar perfectamente las mangueras y máquina, para lo cual, se cortará el suministro de la mezcla, y se dejará el aire comprimido salir libremente por la manguera, doblando ésta antes de la boquilla, disparando de vez en cuando la cantidad de aire para que se limpie totalmente, máquina gunitadora y mangueras en todo su recorrido. Cuando la proyección se hace vertical, es decir, que el punto o soporte del trabajo está por encima de la boquilla, las mangueras deben vaciarse antes de parar el trabajo, sino la mezcla caerá al fondo al quedar sin presión, y no será posible moverla. En este tipo de trabajos es muy conveniente disponer doble juego de mangueras, ya que en caso de una obturación se puede inmediatamente disponer de otra paralela de repuesto. 2.7.1.- Rechazo o rebote.- El rechazo es la pesadilla del gunitador y del gunitado. Un gunitador que haya aprendido a controlar el rebote es muy difícil de encontrar. El rebote está formado por los componentes que no se adhieren a la capa de gunitado o a las armaduras, saliendo rebotados fuera del lugar adecuado. La proporción inicial de rebote es alta cuando el chorro de mezcla se dirige directamente al soporte sobre el que se trabaja, y también cuando se dirige sobre la armadura, pero la formación de una capa amortiguadora sobre el soporte (adherida por la baja relación agua/cemento), reduce dicha cantidad. Por ello, los espesores gruesos tienen una menor proporción de rebote y el espesor delgado tiene los más altos porcentajes. Para el cálculo del rebote existen muchas teorías, tanto prácticas como analíticas, ya que desde un punto de vista económico tiene mucha importancia, incidiendo en el coste del hormigón colocado. En lo que a pérdida de materiales se refiere, el fenómeno de rebote no tiene tanta importancia, pero sí la tiene y mucha, en cuanto al rendimiento del equipo de colocación. El porcentaje de rechazo, en cualquier y situación, depende de: Relación agua/cemento Proporción de la mezcla Gunitador Tipo de áridos (>Arido grueso => más rebote) Eficacia de la hidratación Presión del agua o del aire Diseño y tamaño de la boquilla Velocidad de la proyección Capacidad del compresor Ángulo y distancia del impacto 2.7.2.- Curado.- El curado de la gunita es importante en espesores delgados, para ello, se recomienda que la superficie terminada se mantenga continuamente mojada al menos durante los 7 días siguientes. También se puede proteger mediante arpilleras, manteniendo el agua de fraguado. Se pueden utilizar productos de curado en forma de membrana superficial, pero éstos no deben utilizarse en los casos siguientes: Áreas que se gunitarán de nuevo Zonas donde esté previsto pintar la superficie Cuando su aplicación esté desaconsejada desde el punto de vista estético En líneas generales, se deberán tener en cuenta los detalles normales de curado de hormigón en masa. Construcciones II 1 8 [HORMIGONADOS ESPECIALES] 2.7.3.- Algunas de las técnicas más usuales.- Como técnicas complementarias están las de : 1. Protecciones de superficies próximas, 2. interrupciones del trabajo, 3. y aplicaciones especiales. Las primeras, las zonas próximas al trabajo, que no vayan a ser tratadas se deberán proteger del rebote o rechazo con film de polietileno o papel impermeable adecuados. Así mismo, se protegerán los elementos, máquinas o estructuras que pueden ser dañados por el polvo. En cuanto al segundo, el gunitado se debe suspender cuando la fuerza del viento impida que el gunitador efectúe una correcta colocación de la gunita, cuando haya temperaturas próximas a 0º, o en caso de lluvia que pueda arrastrar el cemento de gunita. En el caso tercero, a veces es necesario un empleo de gunita de características especiales, como pueden ser gunita ligera de gran capacidad aislante o de resistencia al fuego. En estos casos, todo dependerá del tipo de árido que se emplee siendo normalmente áridos ligeros, para ello, habrá que poner un especial cuidado en su granulometría, así como en el proyecto y en la ejecución 3. Hormigonado de Grandes Volúmenes.- Según la ACI 207.1 concreto masivo es “cualquier volumen de hormigón de grandes dimensiones, suficiente para exigir que se adopten medidas para hacer frente al calor de hidratación del cemento y cambiar el volumen empleado para minimizar el agrietamiento”. Un ejemplo claro de hormigonado de grandes volúmenes son las presas, por ejemplo la Presa Hoover, ubicada en el curso del río Colorado en la frontera entre los estados de Arizona y Nevada fue construida como una serie de ménsulas trapezoidales para permitir disipar el enorme calor producido por el concreto. No era suficiente colocar pequeñas cantidades de hormigón en columnas individuales. Para acelerar la refrigeración de hormigón de modo que la siguiente capa pudiera ser vertida, se insertaron tubos de acero de una pulgada. Cuando se vertía el hormigón, el agua de río circulaba por estos tubos. Una vez que el hormigón había recibido una primera refrigeración inicial, enfriaban el agua en una planta de refrigeración sobre la ataguía inferior y la encausaban de nuevo por los tubos para terminar la refrigeración. Fig. #20(Presa Hoover) Colocación de concreto estructural con una dimensión mínima de 1 m, debe considerarse un concreto masivo. La baja conductibilidad térmica del concreto no genera dificultades en el vaciado de concretos no masivos, pues la mayor parte del calor de hidratación [email protected] 1 [HORMIGONADOS ESPECIALES] 9 generado en su masa se disipa rápidamente, por lo que no se generan diferenciales significativos entre la temperatura interior y la exterior, pero en grandes volúmenes el calor generado por el calor de hidratación se disipa muy lentamente lo que genera elevadas temperaturas en la masa de concreto, que producen un significativo diferencial entre la temperatura interior y la del ambiente, lo que a su vez provoca un cambio de volumen diferencial y por lo tanto restricciones internas que resultan en deformaciones y tensiones de tracción en la masa del concreto que pueden causar fisuración del elemento estructural. Para la colocación de concretos masivos se debe desarrollar un plan para asegurar que el concreto en obra no alcance una temperatura interna mayor a los 160º F (71ºC) durante las primeras 36 horas desde su colocación. Existen estudios que indican que temperaturas sobre los 190 º F (87,7 ºC) pueden causar reducción en la resistencia del concreto. Estar alerta sobre el posible diferencial de temperatura máximo entre la porción más caliente del elemento y la superficie minimiza la probabilidad de agrietamiento térmico, generado por la diferencia en contracción entre puntos en la masa que se encuentran a diferentes temperaturas. Esta diferencia causa esfuerzos de tensión que pueden exceder la capacidad de tensión del concreto. Se pueden tomar varias medidas para disminuir la temperatura en una masa de concreto de gran volumen para lo cual se pueden seguir los parámetros expuestos en la normativa ACI 207.1, y lograr cumplir con el requerimiento de temperatura establecido en las especificaciones del concreto puesto en obra 28 ± 2°C. a) Pre enfriamiento de de materiales. Controlar la temperatura del concreto sustituyendo el agua de la mezcla con un porcentaje de hielo en el diseño del concreto utilizado. Pre-enfriamiento de los agregados, utilizando aspersores con agua fría controlando que en ningún momento se exceda la realión agua/cemento. b) Post enfriamiento del concreto Colocar tuberías de diámetro 20 cm empotradas en la masa de concreto por donde se hace circular el agua fría. Fig. #21(Tubería embebida en ele elemento de hormigón) Fuente: Compañía Consuslsismica, Proyecto: Puente sobre el río Daule-Guayas) c) Camadas de bajo espesor con menores frecuencias de colocación d) Trabajar el noche, ya que la temperatura es más baja. Construcciones II 2 0 [HORMIGONADOS ESPECIALES] e) Usar cementos especiales con bajo calor de hidratación. Los siguientes tipos de cemento hidraulico son adecuados para uso en construcción de hormigón masivo: Cemento Portland: tipo I,II, IV y V que cumplan con la norma ASTM C 150. 3.1.- Instrumentación.- El control de temperatura de los componentes del hormigón durante la manipulación del mezclado, el hormigón fresco, antes y después de su descarga en el encofrado pueden ser controlados de forma adecuada con los termómetros ordinarios portátiles con precisión de 1˚F ó 0.5˚C. Los sistemas de post-enfriamientos requieren dispositivos de detección de temperatura (thermocouples-termopares o termómetros de resistencia) embebidos ene el elemento a fin de proporcionar información para el control de tasas de refrigeración. Fig. #22(Termocupla o termómetro de resistencia) Fuente: Compañía Consuslsismica, Proyecto: Puente sobre el río Daule-Guayas) El medio principal para limitar el aumento de la temperatura es controlar el tipo y la cantidad de materiales cementantes. El objetivo de los estudios de dosificación es llegar a un contenido de material cementante no mayor al necesario para llegar a la resistencia de diseño. El factor limitante para llegar a este bajo nivel de cemento es por lo general la necesidad de utilizar una cantidad mínima de cemento con tamaño de partículas necesario para proporcionar trabajabilidad en el hormigón. Sin el uso de adiciones cementicias como puzolana, incorporación de aire, u otros aditivos la mezcla de hormigón masivo en un proyecto puede experimentar una continua lucha para mantener la trabajabilidad, mientras mantiene un bajo contenido de cemento para protegerse del agrietamiento. 4. Hormigón Compactado con Rodillo (HCR ó CCR).- Al CCR lo podemos definir como un concreto seco, con asentamiento “cero”, con bajos contenidos de cemento que pueden ir entre 60 y 240 kg/m3 y que debe ser compactado con un rodillo vibratorio. Esta mezcla debe cumplir con una humedad mínima, que evite que los equipos de colocación se hundan, pero a la vez suficiente para garantizar la uniformidad de la pasta de cemento dentro de la mezcla. [email protected] 2 [HORMIGONADOS ESPECIALES] 1 Por su naturaleza, este material puede ser diseñado considerando la tecnología de suelos y también la tecnología de concretos. Usando la tecnología de suelos, se considera el material como un suelo estabilizado con un material cementante. Se desarrollan curvas densidad- humedad con diferentes grados de compactación y se determina el grado de humedad óptima y la densidad seca máxima. Esta tecnología de compactación del suelo debe estar ligada a los desarrollos de los diseños de concreto, que se basa en la relación A/C. La consistencia de la mezcla se determina usando un Consistómetro VeBe, que es una mesa vibratoria en la que se mide el tiempo requerido de vibración para lograr la consolidación de la misma; este tiempo puede estar alrededor de los 20 segundos. El método para determinar la consistencia de un hormigón fresco por medio del tiempo VeBe no es aplicable cuando el tamaño máximo del árido es mayor de 63 mm. Si el tiempo VeBe es inferior a 5 s o superior a 30 s, el hormigón tiene una consistencia para la cual el ensayo VeBe no es adecuado. Fig. #23(Consitómetro VeBe) Desde aproximadamente el año1975 se ha venido utilizando en forma cada vez más extendida la técnica del hormigón compactado con rodillo vibratorio u hormigón rodillado especialmente en USA donde se lo aplica en la construcción de presas, el hormigonado de grandes superficies (aparcamientos) y firmes de carretera. 4.1.- Aplicación del CCR en la Construcción de Presas.- Las primeras aplicaciones del concreto compactado con rodillo en la construcción de presas se remontan a 1960 en Taiwán; ahí se utilizó para la construcción de la presa de Shihmen. Un década más tarde, al comenzar los años setenta, varios ingenieros propusieron la utilización del CCR en la construcción de presas de gravedad. Pero es quizá hasta los años de 1974 y 1975 en la reconstrucción de la presa de Tarbela, en Pakistán, cuando hace su ingreso el CCR como un material competitivo en la construcción de presas. Desde entonces cada vez son más las obras en que se evalúa y se decide por el CCR como el mejor material para la conformación de presas. Según informes económicos de las presas construidas con CCR en todo el mundo se puede decir que son más económicas (aunque no más fáciles de construir), debido al menor número de obras adicionales necesarias para lograr la impermeabilización ya que las pendientes de las caras de la presa son más altas, lo que trae como consecuencia menores volúmenes de mezcla. Construcciones II 2 2 [HORMIGONADOS ESPECIALES] Fig.# 24 (Fábrica de CCR, represa San Francisco- Minas, entre Azuay y el Oro) http://www.energia.gob.ec/minas-san-francisco/ Dentro de las recomendaciones de colocación del CCR se debe tener en cuenta que la superficie de apoyo para colocar este concreto debe estar nivelada, por lo general se pone una capa de apoyo en concreto convencional compactada con vibrador de inmersión. El transporte de este concreto se puede hacer con volquetas o cualquier equipo de volteo y/o bandas transportadoras. El concreto se coloca por capas (alrededor de 30 cm) que deben ser compactadas con rodillo vibratorio de acuerdo a lo especificado en el diseño; por ejemplo: pueden solicitar una densidad mínima del 98% con respecto a la densidad máxima teórica. Fig.#25 (Presa San Vicente, San Diego- California) http://www.sdcwa.org/es/la-water- authority-hace-historia-en-la-presa-san-vicente [email protected] 2 [HORMIGONADOS ESPECIALES] 3 Fig.#26 (Esquema de capas para construcción de presa con CCR) El principal parámetro a controlar en relación con el CCR es su densidad. Para este objeto, posteriormente a la compactación del hormigón se efectúan determinaciones de la densidad en sitio, generalmente empleando densímetros nucleares. De esta manera, es posible establecer el grado de compactación obtenido y eventualmente, aumentar el número de pasadas del rodillo hasta obtener la densidad mínima prevista. Fig. #24(Colocación de CCR ) Construcciones II 2 4 [HORMIGONADOS ESPECIALES] Fig. #25(Densímetro Nuclear ) 4.1.- Aplicación del CCR en la Construcción de Vías.- Es una técnica para construir pavimentos de concreto a partir de una mezcla seca, de baja relación agua/cemento, que se coloca con pavimentadora de asfalto y se compacta con rodillos vibratorios, por lo general en una sola capa. Sus principales usos son: Vías de baja velocidad (40 km/h), Instalaciones militares, Puertos y muelles, Centros de distribución, Calles, y carreteras, Estacionamientos. Entre los principales beneficios se encuentran: Por ser una mezcla más seca que la del concreto tradicional, su instalación es más rápida. Baja relación agua/cemento Se obtienen mezclas de alta densidad y baja absorción Por su bajo contenido de agua reduce la permeabilidad, al mismo tiempo mejora la durabilidad del pavimento Fácil preparación CCR permiten soportar el tránsito circulando directamente sobre ellos sin protección superficial Soporta tráfico pesado y cargas concentradas Permite apertura rápida al tráfico ligero 24 horas después de su colocación Optimiza el proceso de construcción y reduce costos de mantenimiento Reduce la permeabilidad y aumenta la vida útil del pavimento [email protected] 2 [HORMIGONADOS ESPECIALES] 5 Alta reflectividad solar que reduce la temperatura ambiental y consumos energéticos de la vía Fig. #25( Prueba con Densímetro Nuclear en la construcción de una Vía) 5.- Inyecciones de Cemento.- El tratamiento de inyección consiste en la introducción en el terreno, a presión y caudal relativamente regulado y con magnitudes muy diferentes, de un material que rellena los vacíos o fisuras del terreno, desplaza el terreno existente; o bien generando una mezcla con el terreno original se consigue una mejora de las características geotécnicas de la zona tratada, reduce su deformabilidad y/o disminuye su permeabilidad.Estas inyecciones se realizan mediante perforaciones que permiten alcanzar la zona a tratar y la preparación de la mezcla a inyectar con las características de fluidez y viscosidad adecuadas, además de los equipos de impulsión y control necesarios. 5.1.- Jet Grouting.- El Jet-Grouting es un proceso que consiste en la desagregación del suelo (o roca poco compacta), mezclándolo, y parcialmente sustituyéndolo, por un agente cementante (normalmente cemento). La desagregación se consigue mediante un fluido con alta energía, que puede incluir el propio agente cementante. Esta técnica de alta presión consigue desagregar el suelo o la roca poco compacta, mezclándolo y sustituyéndolo por cemento, así se van llenando huecos y discontinuidades. Básicamente se expulsan chorros de lechada de cemento (grout) a través de unas toberas a velocidades muy altas, logrando así la rotura del terreno y su íntima mezcla con el mismo. La técnica del Jet-Grouting tiene múltiples aplicaciones (mejora del terreno, impermeabilización, túneles, etc.), siendo el fluido de perforación también variable (cemento, bentonita, mezclas químicas, etc.) Construcciones II 2 6 [HORMIGONADOS ESPECIALES] Fig. #26( Jet Grouting ) http://www.collidrill.it 5.2.- Inyección por Impregnación y Fractura.- Esta técnica consiste en el relleno de los poros o fracturas del suelo mediante la inyección de lechada de cemento, sin producir prácticamente cambios de volumen en la estructura del terreno original. Esta técnica se aplica a cualquier tipo de suelo y roca blanda, por ejemplo: suelos granulares gruesos, arcillas de alta plasticidad, roca descompuesta y margas arcillosas. Esta aplicación asegura movimientos no superiores a 2 o 3mm en construcciones o servicios existentes alrededor de la inyección, su finalidad es la de aumentar la carga y/o rellenar los huecos para controlar el flujo de agua. [email protected] 2 [HORMIGONADOS ESPECIALES] 7 Fig. #27 (Inyección por Impregnación y Fractura) Fuente: Hayward Baker 5.3.- Inyección por Consolidación.-La inyección por compactación o desplazamiento introduce en el terreno materiales muy viscosos como lechadas de cemento a altas presiones, de manera que desplazan y comprimen el terreno circundante sin penetrar en él. Esta técnica puede ser aplicada a cualquier tipo de suelo, sin embargo se recomienda para suelos arenosos no cohesivos, donde el proceso de compactación, con un aumento de las tensiones efectivas en la zona afectada, se produce más rápidamente. Se emplea para corregir asentamientos diferenciales de estructuras, sostenimientos de estructuras, refuerzos de excavaciones y en la ejecución de túneles. Fig. #28 (Inyección por Consolidación) Fuente: Hayward Baker Construcciones II 2 8 [HORMIGONADOS ESPECIALES] Fig. #29( Inyección por Consolidación ) http://www.geocron.com/relleno.htm 5.4.- Inyección de Lechada de Cemento – Bentonita y Geles de Silicatos de Sodio.- La bentonita es el principal aditivo para mejorar la estabilidad y penetración de la mezcla de cemento, obteniéndose una alta impermeabilidad del terreno tratado. El silicato de sodio mezclado con agua y un aditivo endurecedor forma un gel de muy baja viscosidad que permite una excelente penetración en el suelo y tiempo de fraguado controlado, logrando una estabilidad temporal de un corte. Debido a su baja viscosidad son efectivas desde suelos gravosos finos hasta suelos de arenas limosas. Este tipo de inyecciones de lechada de cemento se combinan con diferentes tipos de aditivos y/o geles, aplicándose en revestimientos, tranques de relave, estabilización de rocas, etc., para mejorar su impermeabilización. Fig. #30 (Inyección de Lechada de Cemento) Fuente: Hayward Baker [email protected] 2 [HORMIGONADOS ESPECIALES] 9 Fig. #31 (Planta de Inyección) Construcciones II