NAIT Machinist Program - Drill Press 150102dA dB PDF
Document Details
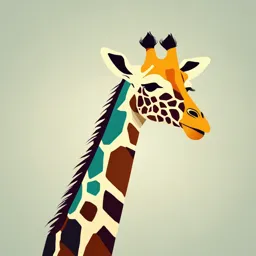
Uploaded by BlamelessIvory
NAIT
NAIT
Tags
Summary
This document provides an overview of drill press operations, including safety procedures, different types of drill presses, and various applications in machining.
Full Transcript
MACHINIST PROGRAM - FIRST PERIOD DRILL PRESS 150102dA and dB SAFETY Safe Operations Dress for safety No Jewelry Eye Safety Hand Safety Chip Removal Work holding Forcing the drill bit too much Lubricants/ coolants / skin conditions Never leave the key in the dri...
MACHINIST PROGRAM - FIRST PERIOD DRILL PRESS 150102dA and dB SAFETY Safe Operations Dress for safety No Jewelry Eye Safety Hand Safety Chip Removal Work holding Forcing the drill bit too much Lubricants/ coolants / skin conditions Never leave the key in the drill chuck Never attempt to stop the spindle with your hand SPEED CHANGE Sensitive Drill Press Speed Change Fig.1 Average Speed 600 – 2800 RPM Note: Belt change is prone to pinch points. RPM Calculation Formula RPM drive x Diameter of Drive Pully = RPM of the driven x Driven Pully Diameter Example: 1800 x 4” diameter = ? RPM x 3” Diameter 1800 x 4 = RPM Driven = 2400 RPM 3 Column Type Fig. 2 Spindle RPM Selector Set when machine is not running only Upright / Column Speed Change Alternate Fig.3 Variable RPM Selector - RPM is set as machine is rotating Note: - Damage will occur if this is not followed Safety Note – Keyed Chucks / Drill Drift Fig.4 Note: Either of these situations can be dangerous if note attended too. DRILL PRESS OPERATIONS The Drill Press Drill Press Operation Drilling holes This is all done by turning a drill bit or other cutting tool and then plunging it downward into a work piece to remove materials Drill Press Application Machine Reaming Hole Sawing Machine Tapping Boring Operations Spot Facing Counter Boring Counter Sinking Drill Drilling; Press Producing a hole Operations by removing material from a solid mass using a cutting tool called a drill. Reaming; producing an accurate sized, smoothly finished hole from a pre- existing hole using a cutting tool having several edges called a reamer. Countersinking; producing a tapered or coned shape at the end of a hole. Counterboring; enlarging the top of a drilled hole to a given depth to provide a square shoulder for the head of a bolt or cap screw. Tapping; Cutting internal threads in a hole with a cutting tool called a tap. Boring; Truing or enlarging an existing hole using a single point cutting tool usually held in a boring bar. Spot-facing; Smoothing and squaring the surface around a hole to provide a seating surface for a cap screw or a bolt. Sawing holes; Producing a hole in a piece of material using a hole saw. DRILL PRESS TYPES AND APPLICATIONS Sensitive Drill Press Capacity: Hole diameters up to 5/8” Work Piece capacity : distance from the column to the center of the drill point Tool holding: Keyed Chuck Stands : Either bench mounted or Floor Mounted Z Table types : solid , rotation on the X axis , round tables rotate around the Z axis Speeds : 300 – 3000 RPM common , manually set by belt and pulley. Sensitive Drill Press The sensitive drill press is used for light duty drilling operations, drilling holes up to ½ inches in diameter. The cutting tool is fed into the work using a hand feed lever which enables the operator to feel the pressure of the tool. The spindle is powered by a V-belt/pulley system that provides the high speeds necessary for light work. Feeds and speeds are manual. Upright Drill Press Tapered Spindle to hold larger tools Power feeds are common Variable Speed selectors are common Commonly have coolant or lubricant reservoirs built in. Capacity: ¼ - 2.00” diameter Upright Drill Press Drill Press The upright drill press has a geared headstock that can power a drill up to 4 inches in diameter. The spindle has a Morse taper to accept taper shank drills. It has power and manual feeds and the table can be raised and lowered with a crank. It may have coolant. Radial Arm Drill Press Radial Arm Drilling Machine. The radial arm drill press is used for drilling holes in large work pieces. The head is powered to permit quick raising and lowering. It has a geared headstock with many speeds and feeds. Spindle has power and manual feeds. Radial Arm Drill Press in Operation Gang Drill Operation Multiple liner based operations performed a single Solid table Each spindle would set up to hold a different tool Not a common tool , replaced by CNC equipment. Multi Spindle Attachment Advantages Drilling a Multiple of Holes in a single process Turret Type Drill Press Magnetic Base Drill https://vimeo.com/84657835 DRILL PRESS SIZING The Sizing of a drill press Page 13 TOOL HOLDING DEVICES Tool holding Devices Drill Chucks ( often called Jacobs Chucks) Sized according to the largest diameter shank they will hold. Have three jaws that move simultaneously to secure the tool. Can hold any number of different cutting tools within its range. Used with straight shank tools only. Lose their accuracy when the jaws become worn and even when new they do not hold tools as securely as other methods. Capacity – up to ½ diameter shank Keyed chuck use Usage Key fits properly Tighten all three locations Stop and tighten if slippage occurs Keyless Drill Chuck Advantage Tool change is quick Not extra tools required to change cutting tools Disadvantages This type of chuck, will not maintain as much gripping force as a keyed type. Drill Chuck Mounting Drill Chucks are mounted to the spindle by two methods 1) Directly onto a spindle shaft that has a Jacobs Taper Machined on to the spindle shaft. 2) Mounted on a Morse Taper Shank with a Jacobs taper machined on to it. Taper Drive Sleeves and Sockets Morse Taper Sleeves Morse Taper Sleeves Allows for the modify and mount cutting and drilling cutting tools to match the machine tool Taper. Morse Taper Shank Removal Drift Quick Release Cutting Tool Holder Each one of the sockets would be used to hold a different tool. The variety of tools provides for multiples of operations without moving the work piece ( ex. Drilling, reaming, tapping) Drill Press Power Tapping Head Tapping Head Quick Auto Reverse Clutch pressure sensitive https://youtu.be/r1rZ_M1Qnys Drill Press Boring Head Boring Head Radial Adjustment by a micro-screw Good Surface finish Virtually any size is a possibility Reamer Holders Two Styles Solid holder does not permit the reamer to self center onto the work piece. Care must be taken to ensure accurate centering has occur or the hole may be out of location, possibly oval in shape. Self Centering reaming heads permit the reamer to locate itself in to the center of the hole and ream to an accurate size and finish. TOOL HOLDING WORK HOLDING Work Piece Holding Standard Drill press vise Work holding is accurate and secure. Device is clamped to the table for extra holding power This vise has the ability to be placed on its side Work Piece Holding – Parallels Work piece holding grooves built into the vise jaws to prevent drilling of the vise and elevating the work piece Angular Drill Vise Permits the drill of angles effectively up to 90 degrees. Limited rigidity when set at angles above 0 degrees Clamping of a Vise to the Table Vises should be clamped to the table with drill bit sizes above 3/8 “ diameter. Under 3/8 “ place a clamp on the left hand side of the table to prevent rotation of the vice. Clamps and Straps Straps and clamps have the ability to secure very heavy and odd shaped work pieces Available in a number of styles and lengths. Strap design Proper Application Parallels Parallels are used to elevate and support the work piece for the pressures exerted will performing the drilling operation. Clamping Technique Proper Operation - Parallels Always ensure parallels are place as close to the drilling operation to prevent work piece bending under the pressure of the drill., V-Blocks Used to hold and locate round objects on the drill press, and milling machine Supporting Devices Often used to support long work pieces onto the drill press table. Angle Plates and Clamps Drilling Jig A drilling jig can be recognized by always having a guide for the cutting tool. CUTTING TOOLS Drill Bit Nomenclature Drill Point Nomenclature Figure 22 Drill point Drill Bit Types Drill bits are produced in two types of holding configurations Taper and straight shank SPECIALTY DRILLS High Helix Jobber drill High helix drill bits Uses Deep ( 3-4 “ ) steel , aluminum materials Not good for Brass, copper, bronze drilling Through Hole Twist Drill This type of drill is often used when material is harder in nature,, and a need to get coolant to the drill point is necessary to prevent point failure. Spade Drilling https://youtu.be/QuWCjqdcPx8 U-Drill Hole Shape Workpiece surface Counter bore / step drill Combination Center drill/ spot drill Centre Drills Drill No. Body Diameter A Pilot Diameter D Pilot Length C 000.125.020.030 00.125.025.030 0.125.031.038 1.125.047.047 2.188.078.078 3.250.109.109 4.313.125.125 5.438.188.188 6.500.219.219 7.625.250.250 8.750.313.313 Combination Spot Drill / Countersink Spot Drill : POINT ANGLE IS MOST OFTEN GROUND TO 90 DEGREE INCLUDED ANGLE. Very rigid Used to locate and spot drill a part, followed by a secondary drilling operation Counter sink Available in 60, 82, 90 degree included angle points. Machine Reamers Shell Reamers are used for holes sized over 1” diameter. Taper Shank Reamers are typically ½ - 1 “ diameter. Straight shank machine reamers are typically 1/8 to ½ “ diameter. Reamer Flute Selection Helical Flute reamers assist the finish of a hole that has an existing slot or hole that may cause the reamer to create an out of round hole. Figure 50 - A helical fluted reamer (A) next to a straight fluted reamer (B). © 2016, Her Majesty the Queen in right of the Province of Alberta Shell Reamers Shell Reamer Reaming Larger Diameter Holes Shell Reamers come in a variety of sizes and must be mounted on an arbor. Advantage One arbor may be used for several sizes of shell reamers. Gun Drills DRILLING A SQUARE HOLE https://youtu.be/rjckF0-VeGI DRILL BIT SIZING Drill Bit Sizes Drill Diameter are available in four series Imperial Fractional - 1/64 – 4 “ (in 1/64 increments) Number size – 1 – 80 (.228” -.013”) Letter Series - A – Z (.238 -.413”) Metric Series -.4 – 100 MM diameters Drill Size Gauges DRILL POINT GRINDING Three Grinding Conditions That Must Be Attended To during the sharpening of a Drill Bit. 1. Cutting Lips the same Length 2. The point Angles must be even 3. The clearance angle behind the cutting Lips Accurate Grinding of the Lip Length Ensuring Cutting Lips Are The Same Angle Grinding Accurate Lip Angle Grinding Correct Lip Clearance Angles Drill Bit Point Angles Point Angle Modifications Grinding a drill point angle for the materials being drilled can significantly increase the tool life and drilling operation. Note: A plate protractor or Vernier Protractor can assist you in achieving these point angles. Point Angle and coolant Selection Chart Drill Point Web Thinning Web thinning is used to restore the drill point back to the thickness from the manufacture after multiple drill sharpening. Thinning is necessary as the drill becomes shorter due to multiple sharpening Drill bit web thickness increases along the drill length. Drill point modification - Cutting Brass Point Angle Modification Modifying Drilling points is done to ensure the drill bit tool point life is extended as far as possible Drill Bit Problems and Solutions Problem Cause Remedy Discolouration Cutting speed too high Reduce cutting speed Not enough coolant Use more coolant Broken or split web Too much feed Decrease feed Not enough clearance Grind more clearance Poor tool life Cutting speed too high Reduce cutting speed Feed too high Decrease feed Feed too low Increase feed Chipped cutting edges Do not overheat drill when Point angle uneven grinding Too much clearance Use drill gauge when grinding Grind less clearance Bell mouth hole Cutting lips uneven length Grind drill, using a drill Point angle uneven gauge Out of round hole Interrupted cut Plug existing hole Excessive drilling Not enough clearance Grind more clearance pressure Chisel edge too wide Make the chisel edge thinner Drill chatter Set-up not rigid enough Use larger machine and Pilot hole too large heavier work holding device Squeals and jams Worn margins Grind drill Excessive heat Use coolant Inadequate chip removal Withdraw drill to clear chips more often Burr Rounded corners on drill Grind drill Blue chips Excessive heat Use coolant Oversize hole Cutting lips uneven length Grind drill, using a drill gauge DRILLING SPEEDS AND FEEDS Speeds and Feeds Appropriate Speeds and Feeds control two very important aspects of machining operations. 1. Tool Life 2. Productivity Two Factors that affect Cutting Speed Selection 1. The type of Material being Cut. 2. The type of the tool that will be used in the operation. The Importance of Cutting Conditions Drilling Speeds and Feeds The speed of the cutting will have the largest affect on the tool life. TOO FAST of rotation will cause premature wear of the tool. TOO SLOW of a rotation will open up an opportunity to over feed the tool with the potential of breakage. Proper calculation will support an efficient drill press operations Speed and Feed For drilling the speed of the cutting tool ( RPM) is calculated by using the cutting tool material ( example high speed steel) and the material being cut by the tool ( Example Mild Steel). The Feed rate ( Feed per Revolution) that the tool enters the work piece is governed by the tool type and the finish required by the designer. Calculating RPM Note: Used to Calculate Speeds for a Note: Used to Calculate Speeds for a CNC Machine tool Manual Machine tool Calculating Metric Sizes to RPM Calculating Drilling Speeds ( Imperial) Cutting Speed x 4 ______________ RPM of The Drill Bit = Diameter Note : See cutting speed chart Cutting Speed Charts - Surface Feet Per Minute Approximate Cutting Speeds for Drilling Type of Material High Speed Steel Carbide Being Cut ft/min m/min ft/min m/min Machine steel 100 30 300 90 Alloy steel 60 18 180 54 Cast iron 80 25 240 72 Aluminum 250 75 750 225 Brass 200 60 600 180 Cutting Speed Calculations Drilling low carbon steel (Mild Steel) 2 inches deep with a 1/2” diameter. 100(SFPM) x 4 RPM = 𝟏/𝟐 RPM = 400 /.5 = 800 RPM RPM Calculations for the Metric System RPM = 1000 x CS RPM for CNC Л Dia RPM = 320 x CS RPM for Manual Machining Diameter Spindle RPM Adjustment To determine the Rpm of the Spindle Formula: RPM x Drive = Rpm x Driven Example: Motor 3600 x 2” dia. Drive Pulley = RPM Driven X Dimeter of pulley Drive 3600 x 2” = RPM x 4.00” Driven Pulley RPM = 7200 / 4 RPM = 1800 Driven Feed Rate for Drilling Feed rate is the velocity at which the cutter is fed or advanced against the workpiece. It is expressed in units of distance per revolution Drilling Feed Rates - See Table 3 Feed rate is dependent on the: Type of tool (a small drill or a large drill, high speed or carbide. Surface finish desired. Power available at the spindle (to prevent stalling of the cutter or workpiece). Rigidity of the machine and tooling setup (ability to withstand vibration or chatter). Strength of the workpiece (high feed rates will collapse thin wall tubing) Characteristics of the material being cut, chip flow depends on material type and feed rate. The ideal chip shape is small and breaks free early, carrying heat away from the tool and work. Initial Drilling Feed Rate Chart Drill Feeds Drill Size Feed per Revolution Inches Millimetres Inches Millimetres 1/ in and smaller 3 mm and smaller 0.001 to 0.002 0.02 to 0.05 8 1/ in to 1/ in 3 mm to 6 mm 0.002 to 0.004 0.05 to 0.10 8 4 1/ in to 1/ in 6 mm to 13 mm 0.004 to 0.007 0.1 to 0.18 4 2 1/ in to 1 in 13 mm to 25 mm 0.007 to 0.015 0.18 to 0.38 2 1 in to 11/2 in 25 mm to 38 mm 0.015 to 0.025 0.38 to 0.63 Feed Rate Machine Setting / Power Feed Formula Feed rate = RPM X Chip Load Per Tooth Example : Drilling a hole in a mild steel work piece, drill diameter is ¾ inch. , Feed rate from chart equals.007 / rev. and the RPM is 525 Feed Rate = 525 x (.007 x 2 teeth) Feed Rate = Approximately 7 ½” per minute DRILL PRESS OPERATIONS Six Approaches to Drilling Operations 1. Drilling Work held in a vice. 2. Drilling to an accurate Layout. 3. Drilling Large Holes 4. Drilling Holes in Mating Parts 5. Drilling Round Work 6. Deep Drilling Holes Hole Drilling Ensuring the Work piece is In the Vise Ensure the work piece is tight on the parallels and or the vise surface prior to drilling Center Punch Marks The center punch should be at least as large as the chisel edge of the drill. Floating to the Center Punched Hole #2 Drilling Holes to an accurate Layout. Process Set drill bit into the center drilled hole and reverse the rotation direction and float the tool into the location. Clamp work piece and verify alignment. Using Permanent Layout as a reference point for accurate hole locations https://youtu.be/ESWzx3YBo3g # 3 Drilling Large Holes When drilling large holes a pilot hole will help the drill stay on center and decrease the pressure needed to feed the drill into the work. Use a pilot hole when the diameter is over ¾”. The pilot hole should be drilled slightly larger than the size of the chisel edge of the Larger drill. Note: Too large a pilot hole will result in out of round holes and excessive chatter. # 4 Drilling Mating Components Process - Align and Clamp mating parts together. - Use a drill bit matching the hole size to dimple the new part, or of smaller than ½ inch diameter, use a transfer punch to center punch the location on the mating part. # 5 Drilling Round Work on the Periphery Process Appropriately support the work piece above the centerline of the part or use a vee-block. Mark the center of the shaft at the location required, align the center punch mark with a rule or vernier caliper ensuring center line location. Float a drill bit into the center punch mark and then clamp # 6 Deep Hole Drilling Deep hole drilling machine, different from the traditional hole processing method, mainly relies on specific drilling technology (such as twin fluted gun drills. It is considered Deep hole drilling with length to diameter ratio greater than 10. High Helix Drill bits with through coolant work the best for these types of hole. Gun Drills are also used for this type of drilling. REAM COUNTERSINK BORING TAPPING HOLE-SAWING SPOT FACING Machine Reaming. Machine Reamers For reamed holes up to ½”diameter, drill 1/64’ smaller than the reamer. For reamed holes over ½” the hole should be drilled 1/32 smaller than the reamer. Set the spindle speed for one half the speed you would use for drilling. Set the feed rate to two or three times greater than you would use for drilling. (half the speed, twice the feed.) Important Use cutting oil or coolant will increase tool life. Never run a reamer in reverse direction , damage to the reamer will result. Countersink Operations Countersinking is the process of cutting a bevel at the top of a hole large enough to accept the head of a flat head screw. Most machine screws have an included angle of 82 deg. Counter Sink Example Cutting Speeds for Countersinking Recommended Countersink Speeds and Feeds Material FEED PER TOOTH (FPT) (SFM) STEEL - HIGH TENSILE (35-45 RC).001-.002 35-60 STEEL - HIGH TENSILE (45-50 RC).001-.002 25-40 STEEL - HIGH TENSILE (50-55 RC).001-.002 15-20 Counter Boring The process of enlarging the top of an existing hole to accept the head of a bolt Counter-bored hole has a flat bottom Pilot guides the counter-bore into the existing hole Some pilots are interchangeable Speed: 1/4 of drilling speed Feed rate as per drilling operation Counter Boring Sample Counter Boring operation Tapping Hand Tapping Ensure the tap is aligned in two planes Use cutting fluid for this operation Turn the tap handle ¾ to 1 turn and reverse the tap handle by one half a revolution to clear chips. Tapping Blind holes: Use a Spiral fluted tap. Clean chips from the bottom of the hole, prior to bottom tapping Machine Taps Spiral Fluted Tap Spiral Pointed Tap Straight Fluted Tap https://www.rntap.com/tap-technical-information/tapping- speed-guide.aspx Specialty Power Taps Displacement Tap- used on soft materials to improve tensile strength around the threads. Tap diameter = Pitch diameter. Hi-helix spiral fluted tap- used for soft materials like copper, Aluminum in an effort to remove the chips away from a blind hole. Power Tapping Head Power TAPPING Use only hand feed , never power feed Rpm, ¼ that of drilling ( See Charts). Use cutting oil ( sulphur based if possible) Ensure appropriate tap is used for the type of work being done. Power Tapping Head https://youtu.be/r1rZ_M1Qnys Drilling Machine - Boring operations Boring Operations Boring head Read Page 34 , Module 150102dB Boring : Speeds and feeds are based upon the same standards as turning tools. Many cutting tools are made from high speed steel , and the Surface Feed per Minute would be 100 for mild steels. Spot-facing Spot-facing is the process of squaring the surface of the work to ensure a tensioning device is not placed under non 90-degree directional stress RPM = ¼ of normal rotational speed. Steady and consistent feed should be applied. https://youtu.be/uTs3RrxWcns Hole Sawing Hole Sawing is the process of cutting a large hole in metal Advantages: Removes a large amount of material in one cut. Limitations Part thickness is limited by the hole saw length https://youtu.be/jTj8JVWDV6Q END