Chapter 13 Quality Management (2024) PDF
Document Details
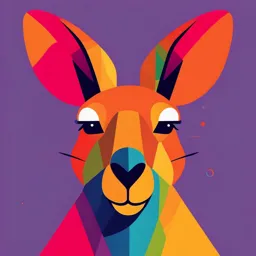
Uploaded by SelfSatisfactionEiffelTower2735
Carnegie Mellon University
Tags
Summary
This document provides an overview of quality management, covering topics such as the definition of quality, quality management tools, quality costs, and the concept of Six Sigma management. It details the history and application of quality management concepts.
Full Transcript
第13章 质量管理 ◼ 质量管理概述 ◼ 质量管理工具 ◼ 质量成本 ◼ 六西格玛管理 1 第一节 质量管理概述 ◼ ISO9000(2000版)对质量的定义是:“一组固 有特性满足要求的程度。” ◼ 质量在一方面指出事物的固有特性,另一方面关 注需求满足的程度。 ❑ 固有特性指满足顾客和其...
第13章 质量管理 ◼ 质量管理概述 ◼ 质量管理工具 ◼ 质量成本 ◼ 六西格玛管理 1 第一节 质量管理概述 ◼ ISO9000(2000版)对质量的定义是:“一组固 有特性满足要求的程度。” ◼ 质量在一方面指出事物的固有特性,另一方面关 注需求满足的程度。 ❑ 固有特性指满足顾客和其他利益相关方要求的特性( 尺寸、重量、安全、速度、耐久性、精度等),并由 其满足要求的程度加以表征。 ❑ 符合性质量(生产者)、适用性质量(顾客)、全面 质量(综合)。 2 质量管理 ◼ 与质量有关的活动都可指为质量管理活动。 ❑ (1)质量策划:制定质量目标并规定必要的运行过程 和相关资源; ❑ (2)质量控制:控制影响质量的因素(人、机、料、 法、环——4M1E),以满足质量要求; ❑ (3)质量保证:向企业最高管理者、顾客、第三方提 供质量信任; ❑ (4)质量改进:不断增强满足质量要求的能力。 3 ◼ 质量管理是技术与管理的结合 ❑ 技术:数学+统计学等科学方法作为质量管理和控 制工具; ❑ 管理:需运用经济学、管理学方法不断改进质量。 ◼ 顾客对品质的要求随时代发展而不断提高,因 此质量管理还与社会发展密切相关。 ❑ 产品质量→服务质量→全面质量 4 现代质量管理发展阶段 (1)质量检验阶段 ❑ 质量检验阶段是传统的质量管理阶段,最早是在20 世纪初,由美国的泰勒提出。 ❑ 在生产出产品之后,进行事后检验。 ◼ 根据质检执行者角色,分为:“操作者的质量管理”、 “工长的质量管理”、 “检验员的质量管理”。 ◼ 事后检验通常是全数检验,花费较高,不适用于破坏性 检验的情况,也无法进行事前预防。 5 现代质量管理发展阶段 (2)统计质量管理阶段 ◼ 1924年,贝尔实验室休哈特的“过程控制研究组”提出 了“事先控制和预防”,建立了生产过程控制图; ◼ 1929年,休哈特的同事道奇和罗米格的“产品控制研究 组”,提出了抽样检验方法。 ◼ 1940年代,美国制定了战时质量控制标准。 ❑ 1920——1940年代进入了统计质量管理阶段:运用 统计推断原理,实现生产过程的事先控制,用抽样 方法弥补了质量检验阶段各种方法的不足。 6 现代质量管理发展阶段 (3)全面质量管理阶段 ❑ 20世纪60年代由通用电气(GE)的阿曼德·费根堡 姆(1922-2014)提出,是目前最主流的方法。 ❑ 全面质量管理将质量控制,从原来的生产系统扩展 到产品寿命周期的全过程,同时强调全体员工、全 体部门参与质量控制。 ❑ 更适应现代多样化生产对质量管理的要求,使质量 管理从局部走向了全面系统的阶段。 7 现代质量管理发展阶段 (4)标准化质量管理阶段 ❑ 由于生产规模及生产模式的多样性,所生产的同一 系列的产品也出现了质量标准的不同,促使许多企 业研究质量管理行业内的统一问题,因此制定了各 种质量管理标准。 ❑ 通过ISO认证是现代企业的普遍做法。 8 质量管理大师:戴明(1900-1993) 戴明环——PDCA循环 ❑ PDCA是一个质量持续改进模型, 包括持续改进与不断学习的四个 循环反复的步骤: 计划(Plan)→执行(Do)→检查(Check)→处理(Action) →Plan→Do→Check→Action→PDCA →…… ❑ 最早由休哈特构思于1930年代,在1950年代,由戴明等人 重新挖掘并提出,成为质量管理的通用工作过程,也被称 为“戴明环”。 9 戴明环——PDCA循环 推动PDCA循环的关键是A(处理)阶段 10 质量管理大师:朱兰(1904-2008) (1)“朱兰”三部曲(Juran’s Trilogy) ❑ 质量计划:确定质量的实现目标和方法预案。 ❑ 质量控制:对过程进行控制,通过对流程质量的控 制,保证产品/服务质量目标的实现。 ❑ 质量改进:发现更好的管理工作方式, 不断改进质量。 11 (2)质量螺旋曲线(朱兰) 销售 适用性 产品 产品开发 市场研究 市场 设计 用户 更高质量水平 销售 生产制造 测试 产品开发 市场研究 设计 检测 生产技术准备 工序控制 初级质量水平 制定制造计划 生产制造 采购 测试仪表装置 供应商 12 质量管理大师:克劳斯比(1926-2001) (1)推行“零缺陷”质量管理 ❑ 质量就是合乎标准; ❑ 质量来自预防,而不是检验; ❑ 工作的唯一标准就是零缺陷; ❑ 以产品不符合标准的代价来衡量质量。 (2)第一次就做对 ❑ 一次就做到符合要求:制定明确的 “要求”,没有明 确的“要求”可循,就根本没有第一次就符合“要求 ”的可能。 ❑ 克劳斯比被称为“零缺陷之父”。 13 质量管理大师:费根堡姆(1922-2014) ◼1958-1968,通用电气(GE)公司质量 控制主管, 92年入选美国工程院院士。 (1)提出全面质量控制——Total Quality Control(TQC) ❑ 使企业全体人员、全体部门参与质量工作,在企业活动全 过程中实行质量控制,以求在最经济水平上,考虑充分满 足用户要求的条件,进行调研、设计、生产和服务,把企 业各部门的研制质量、维持质量和提高质量的全面质量活 动构成一体,形成一个有效体系。 14 ◼ TQC后发展为一种管理理念,称为全面质量管理 (Total Quality Management, TQM) ◼ TQM是指在全面社会的推动下,企业中所有部 门、所有组织、所有人员都以产品质量为核心, 把专业技术,管理技术,数理统计技术集合在一 起,建立起一套科学、严密、高效的质量保证体 系,控制全部业务过程中影响质量的因素,以优 质的工作、最经济的办法提供满足用户所需要的 产品。 15 ◼ 全面质量管理工作流程:PDCA循环工作流程 未解决问题 分析 转入下一循 现状 找出 环 原因 找出 主要 对实施结果 原因 总结分析 A P 制定 措施 C D 实施结果与 实施计划 目标对比 与措施 16 第二节 质量管理工具 一、调查表/检查表 ◼ 调查表又称为检查表、统计分析表,是利用统计 图表进行数据整理和粗略原因分析的一种方法。 ❑ 缺陷位置调查表 ❑ 不良品检查表 ❑ 质量分布调查表 17 缺陷位置检查表 18 不良品检查表 铸件缺陷原始记录表 零件名称:盖子 零件图号: 日期: 单位:××车间××工段 操作者: 填号人: 检查记录 小计 批次Ⅰ 批次Ⅱ 批次Ⅲ 批次Ⅳ 欠铸 正正正 正 正一 29 缩裂 正 一 10 气孔 正正正 正 20 夹渣 一 一 5 折叠 T 一 3 其他 T 2 合计 38 9 8 14 69 19 质量分布调查表 20 二、分层法 ❑ 按照一定的分类标准,将数据分类整理和汇总,将杂乱的 数据归类,使之更能确切反映客观事实。 油底壳生产情况质量统计 产品状况 漏油 不漏油 漏油率(%) 李天一 108 801 11.88 王小二 95 195 32.76 结论:王小二生产的产品漏油率大于李天一? 21 按两种因素(生产者-生产厂)交叉分层 油底壳生产情况质量统计 油底壳 漏油情况 总计 总计漏油率 A厂 B厂 漏油 100 8 108 11.88% 李天一 总产量 900 9 909 漏油率 11.11% 88.89% 漏油 20 75 95 32.76% 王小二 总产量 200 90 290 漏油率 10.00% 83.33% 原因:王小二在条件最差的 B 厂产量最多(造成总体上更吃亏)。 22 三、排列图 ◼ 排列图又称主次因素排列图或帕累托图,是寻 找主要问题或影响质量主要因素所使用的图。 ◼ 由两个纵坐标(频数和百分比)、一个横坐标 、几个按高低顺序依次排列的长方形和一条累 计百分比曲线所组成的图。 23 活塞环槽缺陷排列图 500 100 400 80 百分比 频数 300 60 N=500 229 45.8 200 40 136 100 56 20 42 15 14 8 0 0 精磨 精切 精镗 垂直 斜 凸轮 其它 外圆 环槽 销孔 摆差 油孔 偏差 缺陷 缺陷 缺陷 缺陷 缺陷 缺陷 缺陷 24 四、因果图 ◼ 因果图也称鱼骨图/鱼刺图、特性因素图,用于寻找 质量出问题的原因,常基于头脑风暴法完成。 ◼ 因果图形象地表示了探讨问题的思维过程,通过 有条理地逐层分析,可以清楚地看出“原因-结果 ”、“手段-目标”的关系,使问题的脉络完全显 示出来。 ◼ 因果图往往像一副鱼骨头,因此也称鱼骨图: 25 原因类别 原因类别 主要原因 主要原因 缺 陷 次要原因 次因 主要原因 原因类别 原因类别 原因类别 26 例:分析患近视的原因 材料方面 环境方面 人为方面 主要原因1 字太小 常揉眼睛 灯光太暗 粉尘 遗传因素 印刷不清楚 长时盯屏 近视 灯光太强 意外伤害 主要原因2 桌椅高度 坐车看书 距离过近 看书方法不对 书本质量 走路看书 躺着看书 长时看书不休息 设备方面 方法方面 27 五、直方图 直方图又称频数分布图,是通过对测定或收集 来的数据加以分组整理,描绘直方图来判断和预测 生产过程质量和不合格品率的一种常用工具。 28 示例:产品重量直方图 TL TU T 30 M μ= 26.6(cg) 25 S= 9.0(cg) 20 15 10 5 0 29 各种类型的直方图与可能原因 A. 标准型:正常直方图 B. 陡壁型:尺寸偏离 C. 双峰型:数据多个来源 D. 孤岛型:出现异常 30 E)平顶型:可能刀具变钝 F) 锯齿型:数据分组不当 31 六、散布图 ◼ 散布图又称相关图,是判断两个变量之间是否存 在相关关系的分布状态图形。 ◼ 通过分析研究两种因素的数据关系,来控制影响 产品质量的相关因素。 32 散布图的典型图例 Y Y 强 强 正 负 相 相 关 关 0 X 0 X Y Y 弱 弱 正 负 相 相 关 关 0 X 0 X 33 Y Y 0 X 0 X 不相关 非线性相关 34 七、控制图 ◼ 控制图用来判断生产过程是否处于控制状态(稳 定),区分由异常或特殊原因所引起的波动,以 对影响该过程的某些因素进行识别、调查,保证 生产过程处于受控状态。 ❑ 统计过程控制(stochastic process control,SPC): 运用统计技术对过程中的各个阶段进行监控,从而达 到改进与保证质量的目的,控制图是其主要工具。 35 基本控制图 UCL: 上控制界限, 用虚线表示。 LCL: 下控制界限, 用虚线表示。 CL: 中心线,用细 实线表示。 36 控制图的统计原理 ❑ ±3σ原理:任意抽取一个样本(包含多个产品) ,若生产处于正常控制状态,则样本特性值(如均 值)大概率分布在 μ±3σ 之内(μ为期望值, σ为 方差),在该范围之外是不可能的或小概率事件。 ❑ 如果在实际中发生了小概率事件,则说明过程不正 常或不稳定,需要找到原因并消除之。 ◼ 注意,上下控制线并不一定刚好是±3σ线,也可能只是 接近±3σ 位置的线(不同控制图其控制线不同,绘制方 法也有差异)。 37 控制图分析 (1)判稳准则 判稳准则是指过程处于受控状态且保持稳定所 满足的条件,该条件要求: 第一:控制图上的点“没有”越出控制界限; 第二:控制图上点的排列没有缺陷。 同时满足以上第一条和第二条,则可以判断生 产过程是正常稳定的,称为“判稳”。 38 第一,控制图上的点“没有”越出控制界限,意思 是指同时满足下述三点: ✓ ①连续25个点都在控制限内; ✓ ②连续35个点,至多1个点落在控制限外; ✓ ③连续100个点,至多2个点落在控制限外。 第二,控制图上点的排列没有缺陷,是指点的排列 不出现“判异准则”中抽样点排列型态的小概率事 件。 39 (2)判异准则 ❑ 判异准则用来判断生产过程是否出现异常,主要以 小概率事件为理论依据: ◼ 小概率事件在正常情况下是很难发生的,因此,如 果发生了小概率事件,则可以推测系统或过程存在 异常。 ❑ 判异分为两类: ◼ 点出界被判断为异常(违反第一条判稳准则); ◼ 抽样点的排列型态不随机被判断为异常。 40 ❑ 并不是说只要有某个点出界或某些点排列不随 机就必然是异常的——还要看点出界或排列不随 机是否是小概率事件。 ❑ 理论和实践可知,有八种情况从统计上来说, 都是小概率事件,所以如果控制图呈下述八种 情况之一,即可判断为过程出现异常,称为判 异准则: 41 UCL A B C UCL X C A B B A C LCL X C 准则 一: 不满 足界内 判稳 B 的三种情况,且1个点落在 A LCL A区外(点超出控制界线) ,发生概率P1=0.0027 准则二:连续9个点落在中 心线同一侧,发生概率 P2=0.0038 ⨳表明均值可能产生偏移 42 UCL UCL A A B B C C X X C C B B A A LCL LCL 准则三:连续6点递增或递 准则四:连续14点,相邻两 减,概率P3=0.00278 点上下交替,概率P4=0.004 ⨳可判断过程平均值较小趋 ⨳可能存在两个总体,如两台 势的 变化: 刀具磨 损 , 维 设备或两位操作人员轮流进 修水 平逐渐 降低 , 或操 作 行操作引起的。实际是数据 员技能逐渐提高等。 分层不够的问题。 43 UCL A B C UCL X C A B B C LCL A X C B 准则五:连续3点中有2点落 A LCL 入中心线同一侧的B区以外 ,概率P5=0.003 准则六:连续5点中,有4点 ⨳说明标准差可能已经变大 落在中心线同一侧的C区之 外,概率P6=0.005331 ⨳可能均值发生了变化 44 UCL A B C UCL X C A B B LCL A C X C 准则七:连续 15点全部在中 B 心线两侧C区以内,概率 A LCL P7=0.00326 准则八:连续8点在中心线 ⨳数据分组不当,控制规格太 两侧,却无任何一点在C区 宽和数据不准确所造成。或 内,概率P8=0.000103 应重新计算控制线。 ⨳标准差太大 45 控制图可能会出现两类错误 ◼ α错误(第一类错误):虚发警报(弃真) 这类错误是将正常判为异常:即,生产过程仍处 于统计控制稳定状态,但由于随机噪声的影响,使 得数值点超出控制限,由此虚发警报而误判生产过 程异常。 这类错误称为第Ⅰ类风险,其概率记作α。 46 ◼ β错误(第二类错误):漏发警报(纳伪) 这类错误是将异常判为正常:生产已失稳为非统 计控制状态,但数值点还未超出控制限,由此将已 失稳的生产过程误判为正常。称为第Ⅱ类风险,概率 记作β。 单纯依靠统计方法无法同时减小上述两类风险; 实践表明,控制线在3倍方差附近,可使两类误 差引起的质量成本最小,因此一般取控制线在±3σ 附近。 47 第三节 质量成本 ◼ ISO规定,质量成本分为两方面: ❑ 质量运行成本:企业为保证和提高产品质量而支付的 一切费用,包括:预防成本、鉴定成本。 ❑ 质量故障(损失)成本:指由于低质量造成后果所引 发的费用,包括企业内部故障(损失)成本、外部故 障(损失)成本。 48 质量成本构成 质量预防成本 质量运行成本 质量鉴定成本 质量成本 内部损失成本 质量损失成本 外部损失成本 思考:质量运行成本和质量损失成本之间是什么关系? 49 质量对成本的影响 成本 质量运行成本 总质量成本 质量损失成本 最优质量等级 质量等级 50 第四节 六西格玛管理 ◼ 产品属性(尺寸、重量、服务水平等)存在随机波 动,一般近似服从正态分布,那么其方差σ 越小,表 明属性越稳定,产品质量越高。 ◼ 假 设设 计 规格 限 为 ±T, 如 果 随机 质 量 参 数值 的 ±3σ 在±T 内,不考虑公差中心偏移,那么产品合 格率会达到99.73%。 ◼ 假设±kσ 在±T 内,则 k 越大,精度越高。 51 ◼ 若±6σ 在±T 内,则当公差中心无偏移时,产品 缺陷率为5亿分之1,其合格率接近100%; ◼ 因公差中心偏移,实际合格率一般为百万分之 999996.6(对应缺陷率为百万分之3.4)。 1970年代,美国工业相当于2σ水平; 1980年代,美国工业相当于3σ水平。 日本在1980年代早期就已达到4σ水平; 1980年代中期,日本发展到5σ控制水平。 1980年代后期,摩托罗拉(Motorola)公司进一步提 出了6σ质量目标。 52 ◼ 摩托罗拉公司在1987年开始推广六西格玛质量管 理,很快达到5.6个σ(20个缺陷/百万件),节省 费用达110亿美元。 ◼ 1992年达到 6σ 质量水平(3.4个缺陷/百万件)。 ◼ 摩托罗拉公司取得了质量管理的巨大成功,分别 获得了“波多里奇国家质量奖”和日本制造业的 NIKKEI奖。 53 6σ管理的内涵 ◼ 为什么要达到6σ? ❑ 若单工序质量水平达到±3σ,则单工序的在制品合格 率为99.73%; ❑ 若串联100道工序,实际最终产品的合格率: (99.73%)100=76.31%—— 略超过±1σ水平) ❑ 若单一过程质量提高到6σ水平,则100道工序后成品合 格率会保持在99.96%以上; ❑ 500道工序,成品合格率也在99.83%以上。 54 6σ管理的内涵 ◼ 纯粹依靠控制产品质量本身无法达到6σ水平,需 要依靠流程和工作品质的改进。 ❑ 根据经验,若企业在技术层面全力实施6σ,则每年可 提高一个σ水平,直至4.7σ,资本投入不大,且利润率 提高显著。 ❑ 在 4.8σ 以后,若想再提高,就需要对作业过程重新设 计,重组流程和提升管理水平,才会使产品或服务在 更高平台上获得竞争优势。 55 ◼ 6σ:一套系统的业务流程改进方法体系,旨在对组 织业务过程进行突破性的持续改进,使顾客和其它 相关方满意。 ❑ 6σ管理是一种处世哲学(创造顾客价值); ❑ 是一种文化(实现顾客价值最大化); ❑ 是一种标准(缺陷率小于百万分之三点四); ❑ 是一种追求(追求完美); ❑ 是一种挑战(挑战极限); ❑ 是一个目标(质量零缺陷)。 56 6σ的作业流程改进:DMAIC过程 ◼ 定义(Define):辨别需要改进的产品或过程,确定项目需 要的资源。 ◼ 测量(Measure):定义缺陷,以当前产品或过程的表现作 底线,建立改进目标。 ◼ 分析(Analyze):分析在测量阶段所收集的数据,以确定 一组按重要程度排列的影响质量的变量。 ◼ 改进(Improve):优化解决方案,并确认该方案能够满足 或超过项目质量,改进目标。 ◼ 控制(Control):确保过程改进一旦完成,就能继续保持下 去,而不会返回到先前的状态。 57 ◼ 本章小结 ❑ 质量的基本概念 ❑ 质量管理大师 ❑ 全面质量管理 ❑ 质量管理工具 ◼ 调查表、分层法、排列图、因果图、直方图、散布图、控制 图 ❑ 质量成本 ◼ 质量运行成本 ◼ 质量损失成本 ❑ 6 σ 管理 58