Quality Control and Management PDF
Document Details
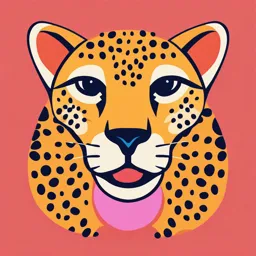
Uploaded by LoyalHeliotrope3514
Louisiana State University
Dr. Nahmens
Tags
Summary
This document provides an overview of quality control and management, including its historical context, modern importance, and key concepts. It discusses the evolution of quality, from the "stone age" to the Industrial Revolution and into modern times. Importantly, the document delves into the Deming Cycle and Juran's Quality Trilogy.
Full Transcript
Quality Control and Management Dr. Nahmens IE 1002 Modern Importance of Quality “The first job we have is to turn out quality merchandise that consumers will buy and keep on buying. If we produce it efficiently and economically, we will earn a profit, in which you will s...
Quality Control and Management Dr. Nahmens IE 1002 Modern Importance of Quality “The first job we have is to turn out quality merchandise that consumers will buy and keep on buying. If we produce it efficiently and economically, we will earn a profit, in which you will share.” - William Cooper Procter (1887) Key Idea Procter’s statement addresses three issues: Productivity- measure of efficiency Cost of operations Quality of goods/services that creates customer satisfaction Building—and maintaining—quality into an organization’s goods and services, and more importantly, into the infrastructure of the organization itself, is not an easy task. Evolution of Quality Quality is not a recent invention- it dates back to the “stone-age”. The Egyptian, the Greek, the Roman, and various other civilizations produced wonders in various fields. Industrial Revolution- Mass production and division of labor (separate quality department). The concept of benchmarking also proliferated during this era. How the evolution in other areas has affected Quality Today? Quality Today! Today’s quality activities involve many activities like product design assurance, procurement quality assurance, product quality audit, etc. Emphasizing the importance of proper design, quality raw materials and an organization’s involvement in producing high quality end product. Another ongoing activity of interest is the development of standards. From Product Quality to TQM } Quality Assurance- product quality (technical) } Through the use of measurements, statistics and problem-solving tools. } Total Quality Management- permanent role } True enablers: listening to customer, developing long- term relationships, developing strategies, measuring performance, rewarding & training employees, & acting as leaders (management). } Integration of quality principles into management systems- TQM Little Q (Product quality) → Big Q (Managing for quality) QUALITY IS……. Defining Quality Perfection Fast delivery Providing a good, usable product Consistency Eliminating waste Doing it right the first time Delighting or pleasing customers Total customer service and satisfaction Compliance with policies and procedures Formal Definitions of Quality } Transcendent definition: excellence } Product-based definition: quantities of product attributes } User-based definition: fitness for intended use } Value-based definition: quality vs. price } Manufacturing-based definition: conformance to specifications Leaders in the Quality Revolution W. Edwards Deming Joseph M. Juran Philip B. Crosby Armand V. Feigenbaum Kaoru Ishikawa Genichi Taguchi Deming Cycle Deming’s System of Profound Knowledge 1. Appreciation for a system 2. Understanding variation 3. Theory of knowledge 4. Psychology 1) Systems Most organizational processes are cross- functional Parts of a system must work together Every system must have a purpose Management must optimize the system as a whole Deming stressed that systems must be focused toward a purpose 2) Variation The variation concept is a law of nature in that no two natural items in any category are the same. Many sources of uncontrollable variation exist in any process Excessive variation results in product failures, unhappy customers, and unnecessary costs Statistical methods can be used to identify and quantify variation to help understand it and lead to improvements Sources of Variation in Production Processes Measurement Operators Methods Materials Instruments INPUTS PROCESS OUTPUTS Tools Human Machines Environment Inspection Performance Common Causes Special Causes 17 Importance of Understanding Variation time PREDICTABLE ? UNPREDECTIBLE 3) Theory of Knowledge Knowledge is not possible without theory Experience alone does not establish a theory, it only describes Theory shows cause-and-effect relationships that can be used for prediction 4) Psychology People are motivated intrinsically and extrinsically; intrinsic motivation is the most powerful Fear is de-motivating Managers should develop pride and joy in work Juran’s Quality Definition } A simple definition of quality: “fitness for use.” } Viewed from both external & internal perspectives; that is, quality is related to: } “(1) product performance that results in customer satisfaction; } (2) freedom from product deficiencies, which avoids customer dissatisfaction.” Juran’s Quality Trilogy Proposed a universal way of thinking about quality: “Quality Trilogy” – Quality planning – Quality control – Quality improvement www.juran.com Phillip B. Crosby Quality is free... “Quality is free. It’s not a gift, but it is free. What costs money are the unquality things -- all the actions that involve not doing jobs right the first time.” Philip B. Crosby Four Absolutes of Quality Management: 1. Definition of quality: Quality means conformance to requirements 2. System for achievement of quality: The rational approach is prevention of defects. 3. Performance standard: The only performance standard is zero defects. 4. Measurement: The performance measurement is the cost of quality. www.philipcrosby.com Statistical Process Control (SPC) A methodology for monitoring a process to identify special causes of variation and signal the need to take corrective action when appropriate. 25 Statistical Process Control (SPC) SPC can be applied to any process. Seven tools: 1. Control Charts 2. Histogram 3. Pareto Diagram 4. Cause-Effect Diagram 5. Check Sheets 6. Process Flow Diagram 7. Scatter Diagram 26 Control Charts Upper Control Limit Quality Characteristic Center Line Lower Control Limit 1 2 3 4 5 6 7 8 9 10 11 12 13 14 Sample (or subgroup) across time 27 Histogram – Histogram- is a graphical display of data such that the characteristic is subdivided into classes or bin. X-axis- represents the quality characteristic. Y-axis- represents the number of observations each class. 28 Pareto Diagram Frequency Frequency 80/20 rule- 80% of customer complaints are caused by 20% of our products or services. 29 Cause-and-Effect People Materials Work Methods Primary Cause Quality Secondary Cause Characteristic Environment Equipment Measurement Causes Effect 30 Check Sheets 31 Process Flow Diagram: Example Ball-Point Pen Assembly 32 Scatter Diagram Scatter Diagram 33