Management of Quality PDF
Document Details
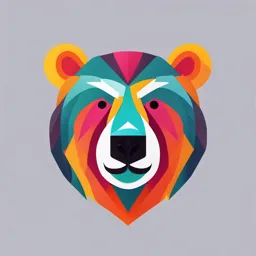
Uploaded by GenialHorseChestnut
Divine Word College of Calapan
Tags
Related
- Introduction to Supply Chain Management in Hospitality PDF
- Introduction to Operations Management & Total Quality Management PDF
- Introduction to Operations Management and Total Quality Management PDF
- Operations Management Reviewer PDF
- Operations Management Exam Notes PDF
- Operations Management: Overview and Principles
Summary
This document provides an overview of quality management. It discusses the evolution of quality management, definitions, dimensions of quality, and various aspects of quality management, such as the factors affecting quality, the roles of individuals in maintaining quality, the impact of poor quality, and ways to improve quality.
Full Transcript
CHAPTER 9 MANAGEMENT OF QUALITY WHAT IS QUALITY? -refers to the ability of a product or service to consistently meet or exceed customer requirements or expectations. THE EVOLUTION OF QUALITY MANAGEMENT INDUSTRIAL REVOLUTION -Prior to the Industrial -A division of lab...
CHAPTER 9 MANAGEMENT OF QUALITY WHAT IS QUALITY? -refers to the ability of a product or service to consistently meet or exceed customer requirements or expectations. THE EVOLUTION OF QUALITY MANAGEMENT INDUSTRIAL REVOLUTION -Prior to the Industrial -A division of labor accompanied the Revolution, skilled craftsmen Industrial Revolution; each worker performed all stages of was then responsible for only a small production. Pride of portion of each product. workmanship and reputation often provided the motivation to see that a job was done right. FREDERICK WINSLOW TAYLOR “Father of Scientific Management” -He gave new emphasis to quality by including product inspection and gauging in his list of fundamental areas of manufacturing management. G. S. RADFORD -He improved Taylor’s methods. -Two of his most significant contributions were the notions of involving quality considerations early in the product design stage and making connections among high quality, increased productivity, and lower costs. BELL TELEPHONE LABORATORIES 1924 -Introduced statistical control charts that could be used to monitor production. H. F. DODGE, H. G. ROMIG AND BELL LABS 1930 -Introduced tables for sampling. -Nevertheless, statistical quality control procedures were not widely used until World War II, when the U.S. government began to require vendors to use them. THE FOUNDATIONS OF MODERN QUALITY MANAGEMENT: THE GURUS A core of quality pioneers shaped current thinking and practice. This section describes some of their key contributions to the field Contributors and Their Key Contributions Walter Shewhart – control charts; variance reduction W. Edwards Deming -14 points; special versus common causes of variation Joseph M. Juran – quality is fitness-for-use; quality trilogy Armand Feigenbaum – quality is a total field; the customer deifines quality Philip B. Crosby – quality is free; zero defects Kaoru Ishikawa – cause-and-effect diagrams; quality circles Genichi Taguchi – taguchi loss function Taiichi Ohno and Shigeo Shirgo – continuous improvement INSIGHTS ON QUALITY MANAGEMENT Successful management of quality requires that managers have insights on various aspects of quality. These include defining quality in operational terms, understanding the costs and benefits of quality, recognizing the consequences of poor quality, and recognizing the need for ethical behavior. We begin with defining quality. SERVICE QUALITY-THE DIMENSIONS OF PRODUCT QUALITY DON’T ADEQUATELY DESCRIBE SERVICE QUALITY. INSTEAD, SERVICE QUALITY IS OFTEN DESCRIBED USING THE FOLLOWING DIMENSIONS DEFINING QUALITY: THE DIMENSIONS OF QUALITY 1.CONVENIENCE – THE AVAILABILITY AND ACCESSIBILITY OF THE SERVICE 2.RELIABILITY– THE ABILITY TO PERFORM A SERVICE DEPENDABLY , Product Quality CONSISTENTLY, AND ACCURATELY 3.RESPONSIVENESS – THE WILLINGNESS OF THE SERVICE PROVIDERS TO HELP 1.Performance – main characteristic of the product CUSTOMERS IN UNUSUAL SITUATIONS AND TO DEAL WITH PROBLEMS 2.Aesthetics – appearance, feel, smell, taste 4.TIME – THE SPEED WITH WHICH SERVICE IS DELIVERED 3.Special features – extra characteristics 5.ASSURANCE –THE KNOWLEDGE EXHIBITED BY PERSONNEL WHO COME IN CONTACT WITH A CUSTOMER AND THEIR ABILITY TO CONVEY TRUST AND 4.Conformance – how well a product corresponds CONFIDENCE to design specifications 6.COURTESY– THE WAY CUSTOMERS ARE TREATED BY EMPLOYEES WHO 5.Reliability – dependable performance COME INTO CONTACT WITH THEM 6.Durability – ability to perform over time 7.TANGIBLES – PHYSICAL APPEARANCE OF FACILITIES, EQUIPMENT, 7.Perceived quality – indirect evaluation of quality PERSONNEL AND COMMUNICATION MATERIALS 8.CONSISTENCY – THE ABILITY TO PROVIDE THE SAME LEVEL OF GOOD (e.g. Reputation) QUALITY REPEATEDLY 8.Serviceability – handling of repairs or complaints 9.EXPECTATIONS – MEET OR EXCEED CUSTOMER EXPECTATIONS 9.Consistency – quality doesn’t vary ASSESSING SERVICE QUALITY -The results of this service quality audit help management identify service strengths and weaknesses. Of particular interest are any gaps or discrepancies in service quality. There may be discrepancies between: Actual customer expectations and management Servqual – an instrument designed to obtain perceptions of those expectations Management perceptions of customer feedback on an organization’s ability to expectations and service-quality specifications provide quality service to customers Service quality and the service actually delivered Its focus are: The service actually delivered and what is communicated about the service to customers Customers’ expectations of the service provider Tangibles and their perceptions of provider delivery Reliability Responsiveness If gaps are found, they can be related to Assurance tangibles or other service quality dimensions to Empathy address the discrepancies. THE DETERMINANTS OF QUALITY Design Quality of design refers to the intention of designers to include or exclude certain features in a product or service. How well the product or service conforms to the design Quality of conformance refers to the degree to which goods and services conform the intent of the designers. Ease of use Service after delivery Quality assurance – responsible for gathering RESPONSIBILITY FOR QUALITY and analyzing data on problems Packaging and shipping - must ensure that goods are not damaged in transit Top management – is ultimately responsible for Marketing and sales - responsible for quality. determining customers’ needs and Design – quality products and services begin with communicating them to appropriate areas of the design. organization. In addition, it must report any Procurement – the procurement department is problems with products or services to the responsible for obtaining goods and services that will company. not detract from the quality of the organization’s Customer service - It is responsible for goods and services. communicating that information to appropriate Production/operations – responsible for ensuring departments, dealing in a reasonable manner that processes yield products and services that with customers, working to resolve problems, and conform to drsign specifications. following up to confirm that the situation has been effectively remedied. BENEFITS OF GOOD QUALITY THE CONSEQUENCES OF POOR QUALITY Enhanced reputation for quality The ability to command premium prices Loss of business Increased in market share Liability Greater customer loyalty Lower liability cost Productivity Fewer production or service problems Costs Fewer complaints from customers Lower production costs Higher profits THE COSTS OF QUALITY CATEGORY DESCRIPTION EXAMPLES Appraisal costs relate to inspection, testing, and other activities intended Costs related to measuring, Inspection equipment, evaluating, and auditing to uncover defective products or services, or to assure materials, testing,labs,inspectors APPRAISAL that there are none. They include the cost of inspectors, COSTS parts, products, and services to and the interruption of assess conformance with quality testing, test equipment, labs, quality audits, and field production to take standards testing. samples Prevention costs Costs related to reducing Quality improvement relate to attempts to prevent defects from occurring. They PREVENTION the programs, training, monitoring, data include costs COSTS potential for quality collection and analysis, such as planning and administration systems, working problems and design costs with vendors, training, quality control procedures, and extra attention in both the design and Costs related to defective Rework costs, problem production phases to decrease the probability of defective INTERNAL solving, material and products FAILURE product losses, scrap, workmanship. or services before they are COSTS and delivered to customers downtime Failure costs are incurred by defective parts or products, or by faulty Costs related to Returned goods, reworking services. Internal failures are those discovered during the EXTERNAL delivering substandard costs,warranty costs, production process, whereas external failures are those FAILURE products or services to loss of goodwill, COSTS customers discovered after delivery to the customer. Internal failures liability claims, and penalties occur for a variety of reasons, including defective material from vendors. ETHICS AND QUALITY MANAGEMENT All members of an organization have an obligation to perform their duties in an ethical manner. Ethical behavior comes into play in many situations that involve quality. QUALITY CERTIFICATION ISO ( International Organization for Standardization) – promotes worldwide standards for the improvement of quality, productivity, and operating efficiency through a series of standards and guidelines ISO 9000- pertains to quality management Concerns what an organization does to ensure its products or services conform to its customers’ requirements ISO 14000 – concerns what an organization does to minimize harmful effects to the environment caused by its operations Bear upon three major areas: 1.Management Systems – systems development and integration of environmental responsibilities into business planning 2.Operations- consumption of natural resources and energy 3.Environmental systems – measuring, assessing, and managing emissions, effluents, and other waste streams ISO 24700 – pertains to the quality and performance of office equipment that contains reused components TOTAL QUALITY MANAGEMENT OBSTACLE TO IMPLEMENTING TQM -the term Total Quality Management refer to as a quest for quality in an Lack of a companywide definition of quality organization. Lack of strategic plan for change We can describe TQM as follows: Lack of customer focus 1. Find out what customers want. This might involve the use of surveys, focus groups, interviews, or some other technique that Poor intraorganizational communication integrates the customer's voice in the decision- making process. Lack of employee empowerment 2. Design a product or service that will meet (or exceed) what customers want. Make it easy to use and easy to produce. View of quality as a "quick-fix" 3. Design processes that facilitate doing the job right the first time. Determine where mistakes are likely to occur and try to Lack of time to devote to quality initiatives prevent them. 4. Keep track of results, and use them to guide improvement in Emphasis on short-term financial results: "Duct-tape" solutions. the system. Never stop trying to improve. 5. Extend these concepts throughout the supply chain. Inordinate presence of internal politics and "turf" issues 6. Top management must be involved and committed. Otherwise, TQM will just be another fad that fails and fades Lack of strong motivation away. Lack of leadership CRITICISMS OF TQM Overzealous advocates may pursue TQM programs blindly, focusing attention on quality even though other priorities may be more important. Programs may not be linked to the strategies of the organization in a meaningful way. Quality-related decisions may not be tied to market performance. Failure to carefully plan a program before embarking on it can lead to false starts, employee confusion, and meaningless results. Organizations sometimes pursue continuous improvement when dramatic improvement is needed. Quality efforts may not be tied to results. PLAN. BEGIN BY STUDYING THE CURRENT PROCESS. DOCUMENT THAT PROBLEM SOLVING AND PROCESS IMPROVEMENT PROCESS, AND THEN COLLECT DATA ON THE PROCESS OR PROBLEM. NEXT, ANALYZE THE DATA AND The Plan-Do-Study-Act Cycle DEVELOP A PLAN FOR IMPROVEMENT. SPECIFY MEASURES FOR EVALUATING THE PLAN. The plan-do-study-act (PDSA) cycle also DO. IMPLEMENT THE PLAN, ON A SMALL SCALE IF POSSIBLE. DOCUMENT ANY referred to as either the Shewhart cycle or the CHANGES MADE DURING Deming wheel, is the conceptual basis for THIS PHASE. COLLECT DATA SYSTEMATICALLY FOR EVALUATION. problem-solving activities. STUDY. EVALUATE THE DATA COLLECTION DURING THE DO PHASE. CHECK HOW CLOSELY THE RESULTS MATCH THE ORIGINAL GOALS OF THE PLAN PHASE. Employing this sequence of steps provides a systematic approach to continuous improvement. ACT. IF THE RESULTS ARE SUCCESSFUL, STANDARDIZE THE NEW METHOD AND COMMUNICATE THE NEW METHOD TO ALL PEOPLE Process improvement is a systematic approach to improving ASSOCIATED WITH THE PROCESS. IMPLEMENT TRAINING FOR THE NEW a process. It involves documentation, measurement, and METHOD. IF THE RESULTS ARE UNSUCCESSFUL, REVISE THE PLAN AND REPEAT analysis for the purpose of improving the functioning of a THE PROCESS OR CEASE THIS PROJECT process. -A business process for SIX SIGMA improving quality, reducing costs, and increasing customer DMAIC is a formalized problem-solving process of Six Sigma. It is composed of five steps that can be applied to any process to satisfaction. improve its effectiveness. 1.Define: Set the context and objectives for Six Sigma is based on these guiding improvement. principles: 2. Measure: Determine the baseline Reduction of variation is an important goal. performance and capability of the process. The methodology is data driven; it requires 3.Analyze: Use data and tools to understand the valid measurements. cause-and-effect relationships of the process. Outputs are determined by inputs; focus on modifying and/or controlling inputs to improve 4. Improve: Develop the modifications that lead outputs. to a validated improvement in the process. Only a critical few inputs have a significant 5.Control: Establish plans and procedures to impact on outputs (the Pareto effect); con- ensure that improvementsare sustained. centrate on those. QUALITY TOOLS -An organization can use a number of tools for problem solving and process improvement. -This section describes eight of these tools, which aid in data collection and interpretation, and provide the basis for decision making. -The first seven tools are often referred to as the seven basic quality tools. METHODS FOR GENERATING IDEAS OPERATIONS STRATEGY Brainstorming-Technique for generating a free flow of ideas All customers are concerned with the in a group of people. quality of goods or services they receive. Quality circles-Groups of For this rea- son alone, business workers who meet to discuss organizations have a vital, strategic ways of improving products or interest in achieving and maintaining high processes quality standards. Moreover, there is a positive link between quality and Benchmarking-Process productivity, giving an additional of measuring performance incentive for achieving high quality and against the best in the same being able to present that image to or another industry. current and potential customers.