CAL-101 Advisory and Quality Basics.pptx
Document Details
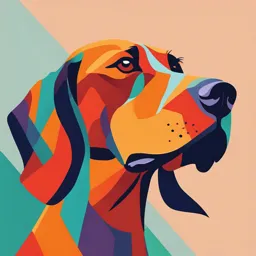
Uploaded by StimulativeLepidolite
2024
Tags
Full Transcript
CAL-Q101 Advisory & Quality Basics A. Zukewich | Training | Canada | August 19, 2024 Version 1.0 This document is the property of ROSEN Swiss AG who will safeguard its rights according to the civil and penal provisions of law. No part of this document may be reproduced or disclosed to any other pa...
CAL-Q101 Advisory & Quality Basics A. Zukewich | Training | Canada | August 19, 2024 Version 1.0 This document is the property of ROSEN Swiss AG who will safeguard its rights according to the civil and penal provisions of law. No part of this document may be reproduced or disclosed to any other party without the prior permission of ROSEN. Agenda CAL-101 Advisory & Quality Basics 01 Objectives 02 Advisory 03 Integrated Management System (IMS) 04 Quality 05 Knowledge Check 06 Questions & Remarks 2 INTERNAL ONLY | ROSEN Internal extended | © ROSEN Group 2024 01 Advisory & Quality Basics Objectives 3 INTERNAL ONLY | ROSEN Internal extended | © ROSEN Group 2024 Advisory & Quality Basics Objectives Gain a basic understanding of the ROSEN Advisory Group, Integrated Management System (IMS) and specifically the Quality elements. After the training, you will be able to: List the Advisory Departments Describe an IMS and its benefits Define what Quality is Define what a process is Identify your internal Suppliers and Clients Find IMS procedures, instructions, and programs Understand the purpose of different IMS document types 4 ROSEN External extended | © ROSEN Group 2024 02 Advisory 5 INTERNAL ONLY | ROSEN Internal extended | © ROSEN Group 2024 Advisory What is Advisory? Best Practice Process Analyze Supports all ROSEN functions in Support process management applying best practices, continual from identification, development, improvement methods and problem- rollout & continuous solving tools improvement Quality Training & Education (TED) Supervisory Supports all functions in the Quality Supports all ROSEN employees to NA in Canada portion of the IMS: standards, gain knowledge and skills through Supports all functions by guidelines, procedures, instructions, root sharing experience and best independent and neutral compliance cause analysis, audits and management practices and ensuring knowledge audits, identifying gaps and reviews. transfer suggesting improvements 6 INTERNAL ONLY | ROSEN Internal extended | © ROSEN Group 2024 Advisory Resources ROSEN Advisory ROHOME Page Quality & Best Practice (QBP) Training & Education (TED) Allison Zukewich Jan Schneider Gina Peak Head of Quality & Best Practice Quality & Best Practice Specialist TED Business Partner 7 INTERNAL ONLY | ROSEN Internal extended | © ROSEN Group 2024 03 Integrated Management System (IMS) 8 INTERNAL ONLY | ROSEN Internal extended | © ROSEN Group 2024 Integrated Management System (IMS) What is an IMS An ISO IMS combines multiple management systems into a unified framework. It integrates processes and standards from various Benefits streamline ISO management systems, such as: operations reduce duplication improve efficiency 9001:2015 14001:2015 45001:2018 27001:2022 maintain Quality Environmental Occupational Health Information compliance with Management Management and Safety Security multiple ISO System (QMS) System (EMS) Management System Management standards (OH&SMS) System (ISMS) 9 INTERNAL ONLY | ROSEN Internal extended | © ROSEN Group 2024 Integrated Management System (IMS) ROSEN Certifications ISO Standards – Global & Canada Other Standards – USA & Europe Achilles & API 10 INTERNAL ONLY | ROSEN Internal extended | © ROSEN Group 2024 Integrated Management System (IMS) IMS ROHOME Page [IMS/] 11 INTERNAL ONLY | ROSEN Internal extended | © ROSEN Group 2024 ROSEN IMS Policy 12 INTERNAL ONLY | ROSEN Internal extended | © ROSEN Group 2024 ROSEN Identity 13 INTERNAL ONLY | ROSEN Internal extended | © ROSEN Group 2024 04 Quality 14 INTERNAL ONLY | ROSEN Internal extended | © ROSEN Group 2024 What is the Definition of Quality? Quality is the degree to which a product, service, or process meets certain standards, requirements, or customer expectations. Fitness for Purpose: The ability of a product or service to fulfill its intended function. Conformance to Requirements: How well a product or service aligns with specified standards, specifications, or regulations. Customer Satisfaction: The extent to which a product or service meets or exceeds customer needs and expectations. 15 INTERNAL ONLY | ROSEN Internal extended | © ROSEN Group 2024 Quality Definition of a Process Inputs Execution Activites Client provides inputs to be Transform Inputs into Outputs transformed Outputs The product or service provided to the Client 16 INTERNAL ONLY | ROSEN Internal extended | © ROSEN Group 2024 Quality Processes & Sub-processes 17 INTERNAL ONLY | ROSEN Internal extended | © ROSEN Group 2024 Quality How to make a peanut butter sandwich Click for video 18 INTERNAL ONLY | ROSEN Internal extended | © ROSEN Group 2024 Quality Locating IMS Documents SharePoint ROSEN Business ROOGLE Search Document Center Software Any ROHOME Source of truth Hyperlinks to the page Document Center DOCS/ Always filter on Doc Center Bookmark it! 19 INTERNAL ONLY | ROSEN Internal extended | © ROSEN Group 2024 Top IMS Documents QHSE Manual QHSE Manual Currently being updated Describes the Integrated Management System 20 INTERNAL ONLY | ROSEN Internal extended | © ROSEN Group 2024 Top IMS Documents IOMS Guideline Shared Processes Responsibilities for (Quality) (HSE) Management Document Management Risk Management Management of Change – MOC Auditing Management Review process Root Cause Analysis Quality HSE Identification & traceability Regulatory Review process Control of measuring and Emergency Response Plan Monitoring devices Incident handling and lessons Quality related incidents and learned findings Behavior Based Safety & Control of Non-Conforming incentives products (HSE) Training and instructions Product recall Local procedures, processes and Customer satisfaction and guidelines Lessons Learned Additional procedures, processes (Quality) Training and instructions. and guidelines 21 INTERNAL ONLY | ROSEN Internal extended | © ROSEN Group 2024 IMS Documents Procedures and Instructions Group Procedures Group Instructions Document Management Document handling document center Root Cause Analysis Handling of Audit Documentation Auditing Handling of Quality Event Management of Change Documentation Management Review Process Control of measuring and monitoring devices Control of nonconforming products Product Recall Incident Handling 22 INTERNAL ONLY | ROSEN Internal extended | © ROSEN Group 2024 IMS Documents Templates Purpose Standardization Ensure consistency across documents, forms and reports Maintain uniformity in the way information is recorded, shared, and reviewed which is crucial for quality management, compliance and efficiency Efficiency Saves time by providing a pre-designed structure that employees can follow. Reduces the need to create documents from scratch, allowing for faster and more streamlines workflows Compliance Help ensure documents meet regulatory, industry, client or organizational requirements Accuracy Reduce the likelihood of errors and omissions Training and Communication Can be used as training tools to explain the required format and content of documentation Continuous Improvement Make it easier to implement changes across the organization by allowing updates to be applied consistently 23 INTERNAL ONLY | ROSEN Internal extended | © ROSEN Group 2024 IMS Documents Purpose Records Evidence of Compliance Provides documented proof that we are complying with processes, industry standards, legal, Client and IMS requirements. Traceability Allows us to trace actions, decisions and changes back to the source which is vital for identifying root causes of problems. Performance Monitoring Allows us to monitor & measure performance overtime, e.g. key performance indicators (KPI). Accountability Establishes accountability by documenting who performed what, when, and under what circumstances. Continuous Improvement Creates historical data that can be used to analyze trends, identify areas for improvement, and implement corrective and preventive actions and drive continual improvement. Risk Management Creates data that is crucial for implementing risk mitigation strategies and preventing future near misses or incidents Knowledge Retention Preserves ROSEN knowledge, ensuring that important information is not lost when employees leave or roles change. Decision Support Accurate and up-to-date records provide the factual basis needed for informed decision- making. 24 INTERNAL ONLY | ROSEN Internal extended | © ROSEN Group 2024 05 Knowledge Check 25 INTERNAL ONLY | ROSEN Internal extended | © ROSEN Group 2024 Knowledge Check Slido 26 INTERNAL ONLY | ROSEN Internal extended | © ROSEN Group 2024 05 Questions & Remarks 27 INTERNAL ONLY | ROSEN Internal extended | © ROSEN Group 2024 28 INTERNAL ONLY | ROSEN Internal extended | © ROSEN Group 2024