Engine-Vehicle Matching PDF
Document Details
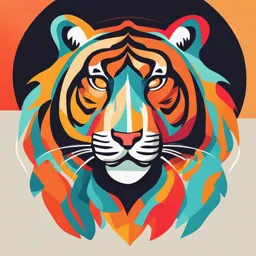
Uploaded by HumourousGreekArt
Politecnico di Torino
Tags
Summary
This document discusses engine-vehicle matching, temperature control, and fuel metering systems for spark-ignition engines. It covers topics such as longitudinal dynamics, coastdown methods, gear ratio selection, and fuel consumption. The document also introduces different mixture formation approaches and fuel supply systems.
Full Transcript
15.5.2 Temperature control................... 226 15.5.3 Boost of heating systems................ 226 15.5.4 Refrigerant circuit with expansion valve........ 227 15.5.5 R744-based refrigeration cycle.............. 228 16 Engine-vehicle matching...
15.5.2 Temperature control................... 226 15.5.3 Boost of heating systems................ 226 15.5.4 Refrigerant circuit with expansion valve........ 227 15.5.5 R744-based refrigeration cycle.............. 228 16 Engine-vehicle matching 229 16.1 Introduction: longitudinal dynamics.............. 229 16.1.1 Lumped parameter model................ 229 16.1.2 Main equations of longitudinal dynamics........ 229 16.1.3 Acceleration and forces due to inertia......... 231 16.1.4 Traction force at the wheels............... 232 16.1.5 Transmission efficiency.................. 233 16.2 Vehicle performance and performance index.......... 234 16.3 Coastdown method........................ 235 16.3.1 Dissipation forces in the transmission......... 235 16.3.2 The coastdown approach................ 235 16.3.3 Various coastdown procedures.............. 236 16.3.4 Vehicle homologation through coastdown method... 239 16.3.5 Coastdown implementation on a test rig........ 240 16.4 Gear ratio selection........................ 241 16.4.1 Gear ratios selection................... 242 16.4.2 Overall gear ratio..................... 243 16.4.3 Selection of the intermediate gears........... 245 16.5 Vehicle fuel consumption..................... 247 16.5.1 Fuel consumption simulation.............. 247 16.5.2 FC simulation: direct approach............. 248 16.5.3 Considerations on FC maps............... 249 16.5.4 Fuel consumption and emissions............ 249 16.6 Matching of transmission to engines.............. 249 16.7 Influence of driving style on fuel consumption......... 249 16.7.1 Rule 1........................... 250 16.7.2 Rule 2........................... 251 16.7.3 Rule 3........................... 251 16.7.4 Rule 5........................... 251 16.7.5 Further considerations on ECO-DRIVE........ 251 16.7.6 FIAT eco:Drive...................... 251 9 Fuel metering system for SI engines Spark-ignition engines operate by burning a premixed mixture of fuel vapor and air. It is, therefore, necessary to prepare the fuel, i.e., transform it into a gaseous phase and mix it with air. The task of the engine induction and fuel systems is to prepare a mixture, from ambient air and fuel in the tank, that once in the cylinder satisfies the requirements of prompt and smooth combustion under all the possible engine operating conditions. In principle, the optimum air-fuel ratio for a spark-ignition engine is that which gives the required power output with the lowest fuel consumption, consistent with smooth and reliable operation. The lowest fuel consumption in a SI engine is obtained for a slightly lean A/F ratio. However, in practice, the constraints of emissions control may dictate a di↵erent A/F ratio, and may also require the recycling of a fraction of the exhaust gases (EGR) into the intake system. 10.1 Mixture requirements The main way in which we express the proportions of air and fuel of the charge in usually not through the air-fuel ratio, but through the relative air- fuel ratio or its reciprocal, the fuel-air equivalence ratio,. The typical value for stoichiometric air-fuel ratio of gasoline is 14.6. In SI engines, the mixture is prepared before combustion and the two processes are separate. In CI, instead, the injection happens just before the combustion and actually initiates it. 10.1.1 Mixture requirements at di↵erent loads The fuel metering system needs to be able to satisfy di↵erent requirements which depend on the operation. We have two main kinds of operation and they can be also divided in sub-requirements. The first one is the steady- state condition, which is divided in: idle operation; part load operation; high load and full load operation. 123 We then have transient conditions, which are divided in: mechanical (acceleration,...); thermal (cold start,...) Certain engine operating condition require mixture adaptation. At idle, we just want a stable combustion. At full load, we have the goal of utilize the inducted air completely, in order to get the maximum power possible. In order to get this, we use a slightly rich mixture. At part load, instead, we try to have a better efficiency and reduced fuel consumption. In this case, we can use the EGR (cooled) in order to improve the efficiency by diluting the charge. This increases the expansion work, the intake pressure increases (pumping work decreases) and the heat losses to the walls also decrease since the temperatures of the burned gas are lower. If there were no regulations on N Ox emissions we would still dilute the charge with air. Since we adopt stoichiometric (around stoichiometric) conditions in order to improve the TWC functioning, we also want to recirculate the exhaust gasses in order to reduce the presence of N Ox even more. The amount of diluent that the engine will tolerate at any given speed and load depends on the details of the engine combustion process. Increasing excess air or the amount of recycled exhaust slows down the combustion process and increases its variability from cycle to cycle. A certain minimum combustion repeatability or stability level is required to maintain smooth engine operation. Deterioration in combustion stability therefore limits the amount of dilution an engine can tolerate. As load decreases, less dilution of the fresh mixture can be tolerated because the internal dilution of the mixture with residual gas (from the previous cycle) increases. At idle conditions, the fresh mixture will not usually tolerate any EGR and may need to be stoichiometric or fuel-rich to obtain adequate combustion stability (the engine should be operated with the air-fuel ratio corresponding to the maximum combustion temperature). If full load torque is to be maximized, and part-load fuel consumption is to be minimized, then could be varied over the load range as shown by solid line (fig. 10.1a). If the engine is endowed with EGR and TWC only, the engine must be operated with a stoichiometric mixture and large percentages of EGR over the low to mid-low range can be tolerated. When EGR is used, the percentage increases from zero at light load to a maximum at mid-load, and then decreases to zero as WOT conditions are approached so air is no longer displaced and maximum bmep can be obtained. If the engine is endowed also endowed with a lean N Ox catalyst (in addition to TWC), lower levels of EGR could be used at mid load to allow the utilization of a lean mixture. What we usually do, is to run the engine at rich conditions only at very low and very high speeds or at very low and very high bmep. 124 (a) Change of with load (b) Zones of operation Figure 10.1: Air-fuel ratio with respect to load Figure 10.2: Methods of mixture formation 10.2 Mixture formation approaches Historically, carburetors were used to control the fuel flow into intake man- ifolds and distribute the fuel across the air stream. Several di↵erent fuel injection concepts have been developed and used, starting from the 1980s. 10.2.1 Fuels for SI engines Before describing the approaches to mixture formation, we need to address quickly the types of fuel used in SI engines, since their characteristics a↵ect how we create the mixture. The predominant fuel for spark-ignition engines is gasoline refined from petroleum. Another liquid fuel in common use is ethanol (ethyl alcohol), either blended with gasoline (e.g., E10, a 10% blend) or as a stand-alone fuel (usually as E85, 85% ethanol and 15% gasoline, by volume). Other fuels in use are LPG, which is a mixture of propane (C3 H8 ) and butane (C4 H10 ), and natural gas, which is predominantly methane (CH4 ). LPG is stored in pressurized tanks as a liquid at ambient temperatures at 125 about 200-800 kPa: it vaporizes in the intake system of spark-ignition en- gines and enters the cylinder as a gas, mixed with air. Also hydrogen can be used as fuel. Flame propagation in premixed hydrogen- air mixtures is extremely rapid (much faster than in equivalent stoichiometry hydrocarbon-air mixtures). Thus hydrogen-fueled SI engines usually oper- ate with well lean of stoichiometric mixtures, and are boosted to obtain acceptable bmep levels and burn rates. 10.2.2 Characteristics of fuels for correct mixture prepara- tion The fuel characteristics impact the engine combustion and emissions forma- tion processes, the onset of any abnormal combustion phenomenon (such as knock), and especially mixture preparation. Successful mixture preparation requires much more than achieving fast stable combustion under warmed-up engine conditions over the full engine load and speed map. A good mixture requires: satisfactory engine starting under cold conditions; good combustion and control during engine transients; minimization of constraints placed by knock risk on engine torque and efficiency; compliance with emission control constraints. 10.2.3 The carburettor approach Back in the days, the carburettor was the main method applied in order to achieve mixture preparation. In a carburetor, the airflow through a converging-diverging nozzle (Venturi) sets up a pressure di↵erence between the carburetor inlet and the throat of the nozzle which depends on the air- flow rate. This pressure di↵erence is used to meter the appropriate fuel flow for the considered airflow. The fuel entered the air stream through the carburetor body, was atomized, and then transported by the air stream past the throttle plate and into the intake manifold. We can use the usual relationship to find the mass flow rate for air and fuel in order to express the air-fuel ratio ma ṁa ⇢a Aa wa ↵= = = mf ṁf ⇢f Af wf Since we cannot consider the density of air as constant, we need to use flow rate formulae for nozzles: q ṁf = Af 2⇢f | p| 126 Figure 10.3: Carburettor working principle v "✓ # u ◆2 ✓ ◆ +1 p1 u p2 p2 ṁa = Aa p t2 RT1 1 p1 p1 We can now say that ↵ is a function of the air flow rate in a nozzle, which is well known (PSAV10 72-30). 10.2.4 Single-point injection system In single-point fuel injection (SPI or central, or throttle-body, fuel injection) a single injector, placed upstream of the throttle plate, meters the fuel ac- cording to the airflow, measured or based on intake manifold pressure, air temperature and engine speed measurements. This approach is the simplest and cheapest of the three injection systems. The problem is that the point of injection is well away from the engine and we have extensive wall wetting of the fuel (fuel impinges on the walls of the manifold and on the valve). This makes precise fuel control very difficult during transients, since the flow of fuel will be delayed. In addition to that, we have no guarantee that the fuel will be evenly distributed among the individual cylinders. The fuel is sprayed towards the throttle plate. The airflow provides e↵ective atomization of the liquid fuel, minimizing liquid fuel deposition on the man- ifold walls. The high air velocity created by the pressure drop across the throttle opening shears and atomizes the liquid sheet on the throttle plate. Vigorous mixing of fuel and air then occurs, especially at part throttle, and provides good mixture uniformity and improves distribution between cylin- ders. Injector fuel delivery is synchronized with the ignition pulses. The 127 injection duration is calculated by the ECU according to air mass to each cylinder and it is corrected considering an exhaust gas oxygen sensor ( sensor) to provide a control to have stoichiometric mixture to the cylin- ders. The injection duration is extended to provide additional fuel during cold start and engine warm-up, and provide enrichment during accelera- tions. The throttle valve potentiometer recognizes changes in throttle valve position. During accelerations, additional fuel beyond the steady-state re- quirement is injected to o↵set delays in fuel reaching each open intake valve to maintain the desired in-cylinder stoichiometry. As WOT is approached, mixture enrichment can be provided to control knock and maximize torque. The injector operates with a fuel supply pressure of about 2 bar (absolute). 10.2.5 Multi-point injection system Multi-point fuel injection (MPI or port fuel injection), has been the dom- inant approach for the past two decades. Such systems require one fuel injector per cylinder, positioned close to the interface between intake mani- fold and intake port, to inject an intermittent fuel spray toward the intake valve. The MPI system provides a short distance between point of injection and intake valve (which reduces the drawback of “wall wetting” phenomenon related to external mixture formation) which allows for more precise con- trol of the fuel metering with the advantages of increased power and torque through improved volumetric efficiency and more precise control of the in- cylinder air-fuel ratio, and more rapid engine response to changes in throttle position. This system is also called PFI (port fuel injection) system. The airflow meter placed upstream of the throttle valve, is based on a sensor plate deflected by the air against a constant return force spring (not any- more adopted). The electrically driven fuel pump delivers the fuel through a filter to the fuel line. A pressure regulator maintains the di↵erential pres- sure between the line to fuel rail and the intake manifold at a fixed value to maintain a constant fuel pressure drop across the injectors (e.g., 270 kPa). Branch lines lead to each electromagnetically actuated fuel injector located in the downstream end of each intake manifold runner at the entrance to the intake port. The injection time required to inject the calculated fuel mass is a function of the opening cross-section of the fuel injector and the pressure di↵erential between the intake manifold and the fuel supply system. When the solenoid injector is not excited, the solenoid armature is forced, with its seal, against the valve seat by the helical spring and closes the fuel nozzle. When the solenoid coil is excited, the armature is attracted and lifts the needle of about 0.15 mm so that fuel can flow through the calibrated annular passage around the valve stem. The front end of the injector needle is shaped as a pintle with a ground top to atomize the injected fuel. In other configurations a high number of orifices is present. The injector is electrically connected to the engine ECU. According to the measured or estimated air 128 Figure 10.4: Schematic of the multi-point injection system mass flow, the ECU (electronic control unit) of the engine controls the mass of fuel injected per injection by varying the duration of the current pulse width (simply called injection time) that excites the solenoid coil of the in- jectors: the fuel spray is injected intermittently toward the intake valves. The control unit also sets mixture enrichment during cold-engine operation, during accelerations and during full-load operations that are detected by the throttle sensor. For cold-start enrichment, one cold-start injector was used to inject additional fuel into the intake manifold plenum. However, it is common practice in modern systems to extend the injection time of the injectors installed in the ports to provide the needed additional fuel. Injection strategies for MPI system The overall objective of the geometric layout of a port-fuel-injection system is to place most of the liquid fuel into the intake port on the back of the intake valve (the hottest surface available) toward the end of the valve closed period (i.e. prior to the start of the intake stroke) to minimize the amount of port wall wetting. Since the intake valve head in a warmed-up engine reaches a temperature in the 150 to 200 C range, it is the surface that will most e↵ectively evaporate liquid fuel. Most of the fuel then vaporizes before entering into the cylinder than would be the case with open (intake) valve injection. Notice that some fuel metering strategies use open valve injection during engine starting as a way to get more of the injected fuel, rapidly, into the cylinder. Engine performance and emissions change as the timing of the start of injection relative to inlet valve opening is varied. Injection toward an open intake valve usually results in higher HC emissions (more liquid fuel droplets pass directly into the cylinder). The mass of fuel injected per cycle usually goes in the range (10 ÷ 40)mg, depending from the load and the injection time is 10ms at maximum. The crank angle used for injection 129 Figure 10.5: Fuel injection pulses is around 1 to 20 degrees CA but it can reach even 300 at very low speed. Obviously, the fuel velocity depends from the pressure di↵erence between the pressure in the supply system and the back pressure in the intake manifold. At steady state, the speed is s 2| p| winj = ⇢f and the mass of fuel is q mf = ṁf tinj = Af 2| p|⇢f · tinj We have three main injection strategies for fuel injection which replaced the old system in which three quarters of the fuel was stored temporarily in front of the intake valve and one quarter entered the cylinder directly. We have: simultaneous injection (or full group): Fuel injection occurs at the same time for all the cylinders every revolution of the crankshaft. Therefore, fuel is injected twice within each four-stroke cycle. The injection pulses are commanded with respect to the crankshaft posi- tion (no need of sensor on camshaft); group injection: The injectors are combined to form two groups. For one revolution of the crankshaft, one injector group injects the total fuel quantity required for its cylinders, and for the next revolution the second group injects; 130 sequential injection: Each injector is singularly controlled and the injection is commanded with respect to the camshaft position. In this way it is possible to set up for each cylinder the injection phase and duration. Some engines used simultaneous or group injection during crank and switched to sequential injection when the engine was running. These strategies allow a shorter engine start time since no synchronisation with the camshaft is necessary before fuel injection begins. These strategies coupled with a large quantity of fuel injected during the first cycles allowed a robust start of the engine. Simultaneous and group injections were abandoned starting from Euro3 regulations, according to which the collection of pollutant emissions starts as soon the engine is switched on (before Euro3 the first 40 s of en- gine emissions at idle in the cycle were neglected). As a matter of fact, the emission levels with simultaneous and group injection are much higher. Liquid injection and fuel film on intake port walls The velocity of the liquid jet is enough to shatter the flowing liquid and its in- teraction with the air further atomizes the fuel. The droplet size distribution varies with the load and the speed. Representative diameters are between 25 and 100 µm. The droplets stay in the manifold for only about 10 ms so only drops of a size smaller than 10 µm will evaporate. The larger droplets move through the air and mostly deposit on the walls of the intake ports and valve heads. We have some vaporization also occurring on the walls. However, the amount of fuel that goes on the walls is significant. Since we have droplets that are too large to be vaporized in the intake manifold, we will have some liquid fuel going into the cylinder, which can deposit on the walls, forming liquid films. Excess fuel will be injected when cold-starting the engine in order to compensate for the amount of fuel that will not be vaporized. In cycles after that, the amount of fuel will be reduced below stoichiometric values (lean) in order to vaporize the excess fuel which had remained in the cylinder after the cold-start. Once the engine has properly warmed up, only a small fraction of fuel enters the cylinder in liquid form. Fuel-film models to compensate for engine transients Any liquid film on the intake port or valve walls (due to the wall wetting phenomenon) is important because it introduces additional fuel transport processes (deposition, liquid transport and evaporation) which have a larger time constant than the air transport process. This means that when we are in transient operation, the changes due to the ”liquid” phenomena will happen faster than the ones due to air flow, unless this discrepancy in time constants is taken into account. The most common approach in order to take these phenomena into account is to consider the fuel in liquid form as 131 one or more ”puddles”. The fuel enters the puddle as part of the injected fuel and leaves it through evaporation and airflow pulling parts of the liquid away. Volume of fuel in the puddle increases with increasing load and speed. Such models have been used primarily to develop fuel metering strategies which compensate for the fuel transport lag. With multi-point port fuel-injection systems, the fuel transport processes can be summarized as follows: the air flow to each cylinder depends on throttle open angle, engine speed, geometric details of the intake manifold and port design, and valve timing and lift. Because the manufacture and operation of individual fuel injectors are not identical, there is some variation in fuel mass injected cylinder-to-cylinder and cycle-to-cycle. Since individual cylinder air flows depend on the design of the manifold, whereas the amount of fuel injected does not, uniform air distribution is especially important with these port injection systems. In order to compensate for these phenomena, we usually increase the amount of fuel that we inject in the port when the load or the speed increase in order to avoid the so-called lean spike, which is due to lack of fuel because of the excessive wall wetting. At low load or speed, we decrease the mass of fuel injected in order to avoid a rich spike that can happen because of less wall wetting with respect to the expected value. 10.2.6 Fuel supply systems We now need to consider di↵erent systems that supply the injectors. Supply with fuel return to tank A characteristic of this fuel system is that the pressure regulator is directly on the fuel rail. The pressure di- aphragm receives the intake mani- fold pressure on one side so that a constant di↵erential pressure arises between the fuel in the fuel rail and the intake manifold. Given a con- stant fuel injector control time, this makes the injected fuel quantity in- dependent of the intake manifold pressure. The main advantages of this fuel supply system are: favorable fuel pressure control dynamics; good hot start behaviour from rising the fuel rail with cool Figure 10.6: Fuel supply with return fuel from the tank; to tank 132 the injected fuel quantity is dependent on the intake man- ifold pressure. A substantial disadvantage is that the fuel is heated in the tank. This increases the fuel evaporation in the tank and the fuel vapors on the carbon canister (system to reduce evaporative emissions from the vehicle). Returnless fuel supply systems In order to reduce evaporation in the tank, returnless fuel supply systems were developed. The returnless fuel systems are characterized by the in- tegration of the fuel pump and pres- sure control valve in the tank or close to the tank. The advantage of this design is that the excess fuel does not have to be first pumped into the engine compartment and then flowed via the pressure regu- lator back into the tank. Due to the location of the pressure regulator, it has no reference to the intake mani- fold pressure and therefore injection times are correspondingly corrected by the engine ECU as a function of the constant fuel pressure of ap- proximately 350 kPa. To avoid large Figure 10.7: Returnless fuel supply pressure fluctuations in the fuel rail that can lead to fluctuations in the injected fuel quantity, pressure pulsation dampers are used in returnless fuel systems. Demand-controlled systems In demand controlled-systems the fuel supply pump delivers only that amount of fuel that is currently used by the engine and that is required to set up the desired pressure. Pressure control is e↵ected by means of a closed control loop in the engine ECU, whereby the current fuel pressure is recorded by a low-pressure sensor. A mechanical pressure regulator is rendered super- fluous. The system is equipped with a pressure relief valve (3) to prevent the buildup of excessive pressure even during overrun fuel cuto↵ or after the engine has been switched o↵. As a result of demand control, no excess fuel is compressed and thus the capacity of the electric fuel pump minimized (this lowers fuel consumption). 133 Figure 10.8: Demand-controlled systems 10.3 Gasoline Direct Injection Gasoline direct injection (GDI) o↵ers two main advantages over injection outside of the cylinder: 1. the fuel goes directly into the cylinder; 2. the fuel distribution within the cylinder can be controlled and stratified by mixing the injected fuel with only part of the in-cylinder air and confining the fuel-air mixture to a specific region of the combustion chamber. The first of these advantages allows more rapid and precise control of mix- ture preparation as engine operating requirements change since the fuel transport delay from the intake port into the cylinder with port fuel in- jection is removed. Better engine transient and cold start operations will result. The second opportunity allows the engine to operate fuel lean overall, like a diesel (at least at part-load) while maintaining an easily combustible close-to-stoichiometric fuel-vapor air mixture in the proximity of the spark plug. These systems can be also referred to as DISI (direct injection spark- ignition). We also have some additional benefits. In fact, fuel vaporization within the air charge in the cylinder cools the charge, allowing higher compression ra- tios (up to a value of about 1-1.5 units) to be used since cooling delays the 134 onset of knock. It also results in the engine inducting more air (increase of volumetric efficiency by up to 10%) thereby increasing WOT torque. We also have tighter control of mixture preparation, and especially stratified overall lean operation, which improve the engine specific fuel consumption (as does the higher compression ratio). Thus, direct fuel injection o↵ers increased output and higher fuel conversion efficiency (about 15-25% reduc- tion of fuel consumption at part load are theoretically possible). Unfortunately, we also have a few drawbacks like the higher fuel system cost due to the necessity of higher injection pressure. We also have an higher tendency to formation of particulate matter (PM) in the cylinder. The first GDI engines were developed and marketed by Mitsubishi in the late ’90s and used to run a lean mixture. Nowadays we focus on stoichio- metric (around stoichiometric) mixtures because of the high e↵ectiveness of the TWC. 10.3.1 DI mixture preparation processes The mixture preparation takes place within the same space (the cylinder) where combustion will occur, and the time available for mixing is shorter. We can have fuel injection during the intake stroke with an homogeneous fuel-air mixture being produced before the initiation of combustion. Another option is to inject the fuel during compression thus producing a stratified fuel-air mixture, with only part of the air being mixed with the fuel vapor. In this way, we create a stoichiometric mixture near the spark plug with excess air surrounding the mixture. The engine operation is overall lean and this results in higher efficiency operation. Combustion only takes place inside of the mixture region. The fuel drops within the injected spray must be dispersed appropriately (throughout the whole combustion chamber with homogeneous operation, whereas only in a specific region of the combustion chamber with strati- fied operation). The drops must vaporize rapidly and should not impinge significantly on the chamber walls. The factors involved in these two DI mixture preparation processes (homogeneous and stratified) are the follow- ing: the desired mixture composition (its stoichiometry), the fuel injector features and injection timing details, the geometry of the combustion sys- tem, i.e., injector location and orientation, nozzle design, intake generated in-cylinder flow (tumble or swirl), cylinder head and piston crown geometry (e.g., bowl-in-piston shape for stratified operation), spark plug gap location. Homogeneous mixture operation With homogeneous mixture combustion where creation of a relatively uni- form fuel-air mixture is the objective, a convenient injector location is below the intake ports. With a wide-angle spray and a tumbling in-cylinder mo- 135 tion, good fuel dispersion, vaporization, and mixing can be achieved. As fuel injection starts during the induction stroke in order to have enough time to inject the desired mass, low injection pressures are sufficient because in- cylinder pressures at this time are small. Stratified mixture operation In the case of stratified operation however, the fuel is injected during the compression stroke. This late injection timing is necessary in order keep the spray cloud compact and to minimize fluctuations of its position and spatial structure at the time of ignition. The more the fuel cloud can be kept compact, the more e↵ective the stratified combustion and the higher the possible reduction of fuel consumption. Large and extremely lean re- gions at the border of the cloud will not burn and will increase fuel con- sumption and emission of unburned hydrocarbons. Because of the increased in-cylinder pressures as well as the very small time interval between injec- tion and ignition, the late injection timing requires significantly increased injection pressures in order to achieve a fast and e↵ective mixture forma- tion. With stratified charge operation, the injector nozzle and spark-plug locations, the fuel injection details, the combustion chamber geometry, and the in-cylinder airflow are all key components of the various combustion approaches used. Flow mixture preparation categories We usually divide the combustion approaches in three air and fuel flow mixture preparation categories: wall-guided, air-guided and spray-guided. In practice, we usually follow two approaches: injector nozzle and spark plug are (relatively) widely spaced and injector nozzle and spark plug (relatively) close spaced. Wide spacing With widely spaced injector nozzle and spark plug, both wall-guiding with a specially shaped piston crown combined with air-guiding (e.g., tumble) are used to create the desired fuel spray behavior, i.e., an approximately stoichiometric fuel-vapor/air mixture cloud that arrives at the spark plug by time of ignition. The central arrangement of the spark plug is advantageous for combustion: it allows a fast and e↵ective burning of the mixture cloud due to the formation of a spherical flame front. The relatively large distance between the injector and the spark plug is also advantageous for mixture formation, because the time interval between injection and ignition is usually longer, compared to a narrow arrangement. Hence, a more homogeneous mixture inside the spray cloud can be achieved, and the risk of soot formation due to excessively rich fuel regions is minimized. However, it is absolutely 136 necessary to keep the cloud compact in order to avoid the formation of very lean mixture regions in the outer spray areas, because this e↵ect reduces the ability of stratification and increases HC emissions and fuel consumption. Since with wall-guided a considerable amount of fuel is injected on the piston surface and cannot completely evaporate until ignition occurs, this technique su↵ers from increased emissions of HC and CO, and the full potential of reducing fuel consumption cannot be reached. In the case of a pure air- guided technique, there is no wall wetting. The in-cylinder airflow is created by a special shape of the inlet ports. Two main in-cylinder air motions are possible, the swirl and the tumble. Special piston geometries are used to enforce the e↵ect of air motion and to make sure that the mixture cloud reaches the spark plug at the time of ignition. The geometries of pistons used for the air-guided technique are all quite complex. Close spacing In the closely spaced configuration, the spark plug electrodes are placed within the developing fuel spray: it is the spray-guiding that brings a com- bustible mixture to the spark plug location at the time of ignition. This prevents the fuel from contacting the piston or combustion chamber walls. This type of combustion places large demands on the preparation of the jet by the fuel injector. The spray-guided technique is the concept that the- oretically allows for the attainment of the highest fuel economy. However, this approach is the most complicated to realize, and for this reason it has only been investigated and tested in research engines. Due to the narrow arrangement, the time between injection and ignition, and thus the time for mixture formation, is extremely small. For this reason, high injection pressures of more than 20 MPa will be necessary to provide enough energy for mixture formation and to avoid the production of soot. The generation of these high injection pressures causes problems regarding system friction and wear, because gasoline has a lower lubricity and viscosity than diesel fuel. Because the time of arrival of the spray at the spark plug is only depen- dent on injection timing and not on complicated air motions, there are no restrictions in ignition timing, and the thermodynamically optimal timing can be realized much easier than in the case of the wall-air-guided concepts. Hence, the spray-guided technique o↵ers the largest possible decrease of fuel consumption at part load. Because the spray does not impact on a wall, and because a strong in-cylinder air motion is not required, heat losses to the engine and pumping losses are the smallest of all three concepts. Be- sides of all these advantages, there are still serious challenges, which have to be overcome in order to realize the spray-guided concept in series produc- tion engines. The most serious problem is the achievement of the required spatial accuracy and reproducibility of the spray shape for all operating points within the stratified mode region in the engine map. Ignition timing 137 is strongly dependent on injection timing, and the accurate timing of both events is crucial in order to avoid misfiring. 10.3.2 GDI engine operations In Figure 10.9, we can see the objectives of the mixture preparation for a correct operation of the engine. Problems with exhaust emissions prevent us from using stratified charging over the whole operating range of the engine. We have at least three states for mixture prepa- ration, depending on the load: homogeneous rich or stoichio- metric at high loads; homogeneous lean or stoichio- metric with EGR at interme- diate loads; Stratified charging with EGR at the lower loads. In the case of full load, a homoge- Figure 10.9: Mixture preparation ob- neous stoichiometric or even fuel- jectives rich mixture inside the complete combustion chamber is necessary in order to include the complete air charge in the combustion process and to achieve maximum torque. No- tice that we need an early injection in order to have enough time to finish the injection process since the fuel quantity is the largest possible. We can- not operate EGR at full load and the engine is controlled in the same way as if we had intake manifold injection. At low and medium loads and speeds, the engine is operated with stratified charging and a high exhaust gas recycling rate reducing throttling opera- tion. This yields lower fuel consumption. The exhaust temperature deter- mines the operating range at low loads in which the engine can be operated unthrottled (or at least less throttled). For the catalytic converter to con- vert the pollutants, the catalytic converter temperature may not fall below 250 C. Completely unthrottled operation is impossible while the engine is idling. Even in a cold start and during warm-up, the engine runs with a homoge- neous, slightly lean mixture to quickly start the catalytic converter. A hot engine can function with throttled stratified charging. If we are at low load and high speed (above 3000 rpm) we cannot achieve proper stratification 138 of the charge since we have too little time to prepare the mixture. When we are in upper partial-load (above 5 bar of bmep) we cannot use stratified charging because of the high emissions of N Ox and because of the risk of soot formation. This is also true for intermediate loads (more than 5 bar of bmep and 3000 rpm) where we run homogeneous charge with close to stoichiometric air-fuel ratio. We could also make the mixture a bit leaner and to use throttling, but the risk of misfiring would increase. 10.3.3 DI engine system components Fuel pressure in DI is much higher than in MPI (up to 200 bar) and a shorter time available for fuel injection. In case of MPI, we have two crankshaft revolution for the injection (about 20 ms at 6000 rpm). In DI, the time is much shorter: at homogeneous operation, we only have half crankshaft revolution. A multi-hole nozzle injector yields a stable spray dispersal angle, good evaporation, and mixture preparation. A problem of GDI is that it yields high (with respect to modern standards) particulate emissions. These are not acceptable and countermeasures are taken in the form of particulate filters. 10.3.4 Fuel delivery in DI Since we have very little time to complete the injection, we need to have a particular fuel delivery system that can supply the injectors fast enough. We need higher pressure and our system is divided in an high-pressure circuit and a low-pressure circuit. The low-pressure system uses components similar to the ones seen in the MPI case. The high-pressure circuit, instead has di↵erent components: high-pressure pump, high-pressure fuel rail, high- pressure sensor and a pressure-control valve. In a continuous-delivery system a high-pressure pump driven by the engine’s crankshaft, forces fuel into the rail, against the system’s pressure. The pump is often a three-barrel radial- piston pump. The quantity of delivered fuel is fixed and the excess fuel not required for the injection is depressurized by the pressure-control valve and returned in the low-pressure circuit. Usually, the fuel is compressed too much with respect to the needed pressure with increased fuel consumption. In fact, this method has been replaced by a demand-controlled system. There, the high-pressure pump (usually a single-barrel radial-piston pump) delivers fuel to the fuel rail in the exact quantity that is required. The pump is driven by the crankshaft. We have a fuel supply control valve that the ECU actuates in order to obtain the desired quantity of fuel in the rail. For safety reasons, the high-pressure circuit features an integrated mechanical pressure-limiting valve; this valve is mounted on the fuel rail in the case of 1st-generation gasoline direct injection, and integrated directly in the high- pressure pump in the case of the 2nd generation (PSAV10 88 for pictures). 139 10.4 Air flow rate measurement In gasoline engines, the load is determined from the measurement of the air mass flow rate. We compute the injected fuel quantity by measuring the load, so on the mass per cycle and per cylinder. The quantity is then cor- rected considering an oxygen sensor in the exhaust gasses. We can compute the airflow with a direct measurement or by using algorithms. 10.4.1 Hot wire and hot film measurements These sensors allow a direct measurement of air mass flow rate. The stream of intake air is conducted past a heated wire (hot-wire). This wire forms part of an electrical Wheatstone bridge circuit. A flow of current passes through the wire to maintain it at a constant temperature above that of the intake air. This principle makes it possible to employ the current requirement as an index of the air mass being drawn into the engine. A resistor converts the heating current into a voltage signal, which is then processed by the ECU along with engine speed as a main input variable. A temperature sensor is mounted in the hot-wire air mass flow meter to ensure that its output signal is not influenced by the temperature of the intake air. The hot-wire air-mass flow meter has no moving parts, and its aerodynamic resistance within the intake tract is negligible. As contamination on the surface of the hot wire could a↵ect the output signal, each time the engine is shut down the wire is electrically heated for one second to burn-o↵ any contamination. The operating principle of the hot-film air mass flow meter is the same as that of the hot-wire sensor, but the sensing element is di↵erent. The main advantages are the fact that this is a direct measurement with a low response time and the resistance to flow within the intake manifold is negligible. We have tough, low performance in case of faults in the surface of the wire and sensitivity to backflow. It has a steep characteristic curve for low air-flow values. It is expensive. 10.4.2 Speed-density method With this method, we consider that the air mass flow rate in the cylinders is equal to n ṁa = ma · i 2 We can then consider the volumetric efficiency starting from the intake man- ifold. The value of the volumetric efficiency ⇤ can be experimentally mea- sured for every operating condition. We can store a table of values of ⇤ as a function of the manifold absolute pressure (MAP) in the ECU memory. We can compute the air mass flow rate as ⇤ n ṁa = ⇢im · iVd · 2 140 This method is easy to calibrate and has a stable algorithm. It is cheap and it has a fast response. It is sensitive to air pressure waves and has to be corrected during high transient operation to compensate filling or emptying of the intake manifold. The volumetric efficiency might change with engine ageing. 10.5 Frequency inputs Frequency inputs are used in the engine management system for measuring the engine speed and to determine the crankshaft position (position of pis- tons). The engine speed is measured through a sensor installed on the crankshaft. The most common configuration is the inductive pick- up sensor, generally called phonic wheel. The sensor is mounted directly opposite a ferromagnetic pulse wheel, from which it is sepa- rated by a narrow air gap. The level of the magnetic flux through the sensor depends on weather the sen- sor is opposite a pulse-wheel tooth or space during the wheel rotation. The number of teeth on the pulse wheel depends on the particular ap- Figure 10.10: Pulse wheel sensor plication. A 60-pitch pulse wheel is normally used, although two teeth are omitted so that the pulse wheel has 60 - 2 = 58 teeth. The space where the missing teeth would be situated is associated to a defined crankshaft position and serves as a reference mark. However, it is not possible to dis- tinguish the two TDCs in a 4-stroke engine. The original sinusoidal signal, which is characterized by strongly varying amplitudes, inside the ECU is converted into a constant-amplitude square wave voltage. 10.5.1 Camshaft position As the engine camshaft rotates at half the crankshaft speed, there is one camshaft rotation for every cycle. It should be therefore possible to use the camshaft rotational position as an indication to distinguish if the TDC of a certain piston corresponds to intake TDC or combustion TDC. The phase sensor on the camshaft provides the ECU with this information. A Hall sensor is generally adopted for this application. Di↵erent configuration exists, e.g. with a single tooth or with more teeth. 141 10.6 Control of the air-fuel ratio It is possible to reduce engine emissions of the three main gaseous pollutants with a TWC in the exhaust system if the engine is operated very close to the stoichiometric air/fuel ratio (with an uncertainty lower than 1%). The engine operating air/fuel ratio is maintained close to stoichiometric through the use of a sensor in the exhaust system, which provides a voltage signal dependent on the oxygen concentration in the exhaust gas stream and therefore on the actual value of. This sensor is called lambda sensor and its signal is the input to a closed-loop control (feedback system) which corrects the fuel injected in the intake, calculated in open loop on the bases of the engine working point (load and speed). 10.6.1 Lambda sensor: HEGO The most common lambda sensor is called HEGO (heated air-fuel ratio exaust gas oxygen analyzer). It compares the residual oxygen content in the exhaust gas with the oxygen content in the atmosphere and indicates whether a rich ( < 1) or lean ( > 1) air-fuel mixture is present in the exhaust gas. Only two values are practically available due to the abrupt change in the residual oxygen content of the exhaust gas side in the range of = 1. The sudden jump in the characteristic curve of these sensors permits air fuel control around = 1 (or really close to 1). 10.6.2 Lambda sensors: UEGO Nowadays, wide-band lambda oxygen sensors are available on the market. They are also called UEGO (Universal air-fuel ratio heated Exhaust Gas Oxygen analyzers) and are used to make a precise measurement of A/F ratio in the exhaust gas in an extensive range. This type of lambda oxygen sensor is therefore also suitable for lambda control with lean-burn concepts on gasoline engines, as well as for diesel engines. The adoption of UEGO sensor provides minor advantages in terms of emissions for SI engines, but is beneficial for fuel consumption reduction at high loads. 10.6.3 Other lambda sensors A lambda sensor is nowadays installed also downstream of the catalytic converter. This sensor is always of the HEGO type. Its purpose is to provide a diagnosis for the catalytic converter (EOBD). The closed-loop control relative to the actual A/F ratio of the engine is performed only with the sensor installed upstream the TWC. The post-cat sensor is less influenced by unstable working conditions due to abnormal combustion, turbulence, poisoning, because it is protected by the filtering e↵ect of the catalyst and by an installation farther from the exhaust manifold. 142 Combustion in compression-ignition engines 11.1 Fundamental features of combustion in CI engines Combustion occurs in a di↵erent way with respect to spark ignition engines. In fact, we have no flame front propagation and the fuel is always injected directly inside of the chamber. The fuel (diesel oil) is injected through several small nozzles that atomize it in small droplets. the fuel then vaporizes (high temperature due to compression of the air) and mixes with air. The air- fuel mixture then ignites spontaneously after an ignition delay, which is a small period of a few crank angle degrees. The unburned portion of the charge is compressed during combustion and this favours the evaporation of the part of the fuel that is still liquid. Injection continues until the desired amount of fuel has entered the cylinder. The air continues to mix with the unburned and burned gasses inside of the cylinder throughout combustion and expansion, until we arrive to the exhaust phase. The fuel burning rate is thus controlled by the rate at which the air mixes with fuel. The flames that result from the combustion are called di↵usion flames, since the fuel and the air must di↵use into each other before they react. Most of the chemical energy of the fuel is released in a thin sheet close to where the fuel vapor and air reach the stoichiometric mixture proportions. An important thing to remember is that the combustion in CI engines depends from local conditions of the charge and not from the speed of the flame and its spread from one point to another. Therefore, the combustion rate is a↵ected by the distribution of the fuel in the chamber. Basically, spontaneous ignition, resulting from the high air temperature and pressure in the cylinder when injection commences, and the fact that fuel-air mixing controls the burning rate, are the distinguishing features of the diesel combustion process. 11.1.1 Features in CI The compression ignition process is extremely complex. We will now discuss about some of its peculiarities. Since injection commences just before combustion starts, mixture formation is heterogeneous and there is no knock limit as in the SI engine result- 143 ing from spontaneous ignition of the premixed fuel and air in the end-gas. Hence, a higher engine compression ratio (15 < rc < 21) can be used in the compression-ignition engine, improving its fuel conversion efficiency relative to the SI engine. Therefore, the limit of compression and boost pressure is not predetermined by “knocking combustion” (as in gasoline engines) but rather by the maximum allowable cylinder pressure, which is why modern diesel car engines operate in ranges of approximately 160-180 bar and com- mercial vehicle engines in ranges of approximately 210-230 bar. The low compression ratio range specified here applies to highly supercharged diesel engines. Since injection timing is used to control combustion timing, the ignition de- lay (ID), i.e. the period between the start of injection (SOI) and start of combustion (SOC) must be kept short (and reproducible). A short delay is also needed to hold the maximum cylinder gas pressure and its derivative value dp/d✓ below the maximum the engine can tolerate. This is done by requiring that diesel fuel has a cetane number (a measure of the ease of ignition of a fuel) above a certain value. Since the combustion process occurs within and around the fuel sprays, en- gine torque can be controlled by varying the amount of fuel injected per cycle, with the engine airflow essentially unchanged. Thus, the engine can be operated unthrottled, so pumping work requirements are low: this im- proves part-load mechanical efficiency relative to the SI engine. As the amount of fuel injected per cycle is increased, problems with air utilization during combustion eventually lead to the formation of excessive amounts of soot which cannot be burned up prior to exhaust. This ex- cessive soot or black smoke in the exhaust constrains the fuel/air ratio at maximum engine power to values some 10-20% lean of stoichiometric. Be- cause the diesel always operates with lean fuel/air ratios ( > 1 , and at part load with very lean fuel/air ratios), the e↵ective value of during the expansion process is higher than in a spark-ignition engine. This gives a higher fuel conversion efficiency than the spark-ignition engine, for a given expansion ratio. 11.1.2 Challenges in the CI combustion chamber design The main issue in the design of the combustion chamber of a CI engine is the need to achieve a proper mixing of air and fuel when the latter is injected. The bores of Diesel engines are between 70 to 900 mm, with the largest measures used in ship propulsion or power generation. We have a constant mean piston speed over this range of measures, at maximum rated power. This means that the speed is mainly proportional to the stroke, being u = 2Sn. The time of combustion for a given crank angle interval, 144 depends on the stroke as well. In fact, ✓ = 6nt, therefore S✓ t= 3u Considering that all other quantities are mainly constant at maximum engine power, we have that the time decreases with the stroke. This limits the speed, since we cannot have too high speed or we would need a too low stroke. This would result in a too low time of combustion which is not ideal. We are limited at a maximum of 5000 rpm. We can compensate for the limit in speed by increasing the bmep through turbocharging, which is easier to achieve in CI engines. 11.2 Fuel injection in CI engines We have two types of injection systems used in CI engines. We have indirect injection, which is not used anymore but was the only one available in the ’80s since the technology was not advanced enough to achieve the system that we now use, which is direct injection. 11.2.1 Indirect injection system In this type of injection, we have a pre-combustion chamber in which the fuel is injected from an injector which has only one hole. The air inside of the chamber is at high pressure. The fuel is at relatively low pressure (450 bar) and the chamber is hot. The combustion actually starts in the pre-combustion chamber and the pressure due to this combustion drives the hot air and fuel into the combustion chamber, where the main combustion happens. The combustion that results is soft and the resulting noise is pretty low. Pre-combustion chambers equipped with a swirl system, manages to give the compressed air in the pre-combustion chamber a swirling motion, which is very good for a good mixture mixing. The configuration with the swirl system has less losses due to the passage of air in the connecting channel since its cross-section is smaller. 11.2.2 Direct injection system In direct injection, the fuel is inserted inside of the combustion chamber di- rectly, without having a pre-combustion chamber. The injector has multiple holes and a much higher fuel pressure (up to 2000 bar). This time we have no losses due to the passage of air in the connecting channel since there is no pre-combustion chamber. As engine size decreases, increasing amounts of air swirl are used because fuel atomization, heating, vaporization and mixing with the air must take place in rapid succession. Air swirl is gen- erated by suitable design of the inlet port (with a helical port design or in 145 (a) Indirect injection (b) Direct injection Figure 11.1: Injection in Diesel engines the configuration of four valve per cylinder, one of the intake runner can be partly closed to further increase swirl). The shape of the combustion cham- ber also contributes to the air flow pattern at the end of the compression stroke (i.e. at the moment of fuel injection). Of the combustion chamber designs used over the history of the diesel engine, the most widely used at present is the ! piston crown recess (bowl-in-piston configuration): the swirl rate is amplified as the piston approaches TDC by forcing the air toward the cylinder axis. Here, the design goal is to hold the amount of liquid fuel which impinges on the piston bowl walls to a minimum. The use of high intake-generated swirl, augmented by the radial inward displacement of the air, and the vigorous squish flow the deep re-entrant bowl-in-piston combus- tion chamber produces, provide fast enough fuel-air mixing and combustion rates to operate up to engine speeds of 4500 to 5000 rpm. 11.2.3 Glow plug In both II and DI, we have an element called glow plug, which is an heated piece of metal placed inside of the pre-combustion chamber (II) or in the combustion chamber (DI). As we start the engine, the glow plug heats the air up in order to have proper temperature during the first cycles. 146 11.3 Heat release rate analysis We need to properly understand the concept of heat release rate in order to better understand diesel combustion. The definition of HRR is the rate at which the chemical energy is released during the combustion. It is usually computed from cylinder pressure versus crank angle data, since the energy is used to increase the pressure. We can define the net heat release rate (or apparent HRR) as dQn dQch dQht 1 dp dV = = V + p d✓ d✓ d✓ 1 d✓ 1 d✓ We can choose a value for that is = (1.3÷1.35). We can see in Figure 11.2 that the heat released by the burn- ing fuel in the combustion is not the net heat. We have a contribution of the heat transferred to the cylinder walls and of the heat inside of the crevices. The fuel vaporization heat is less than 1% of the total heat re- leased. The maximum heat release rate is obtained at the start of com- bustion, while the lowest heat re- lease is obtained in the interval be- tween the start of injection and the start of combustion. After the com- bustion, the net heat release rate starts becoming smaller and smaller in the next interval of crank angle. The injection continues during the Figure 11.2: Contributions to heat re- ignition process and this is why we lease have some peaks in heat release rate after the start of combustion. 11.3.1 Heat release rate in direct injection systems We can identify several phases during the injection-combustion process and relate them to the HRR. Considering fig. 11.3, from a to b, we can see an ignition delay, which is between start of injection and start of combustion. We loose some heat because of the vaporization of the fuel, which requires energy to be completed. In this delay, the fuel properly mixes with air and is ready to be burned. We then have a spike in the HRR (b to c) in which we have the start of combustion. This is called pre-mixed combustion and the mixture already created during the ID burns rapidly, thus releasing a lot of energy in a short time. The longer the ignition delay, the longer the 147 Figure 11.3: HRR during combustion of a single injection DI engine amount of fuel that will burn in this phase. This will generate a larger pressure which might not be good for the cylinder (damage,...). Then (c to d) we have a mixing-controlled or di↵usive combustion phase. Since the chamber temperature and pressure are very high in the chamber, every portion of fuel that is introduced inside of it is instantaneously ignited. The HRR is now dependent from the rate of fuel that is inserted for burning. This means that this phase depends from the load. The HRR decreases as the crank angle progresses. Up to 90% of the fuel chemical energy is released in this phase. Finally, we have a late combustion phase (d to e) in which the HRR decreases as we head into the expansion stroke. 11.4 Fuel injection in DI engines The fuel is injected into the combustion chamber through several holes (8 to 10) with a large pressure across the channel (usually a nozzle) between fuel supply and combustion chamber. The injection pressure can range between 300 bar (at idle) and 2000 bar (up to 3000 bar in the top of the line systems). The diameters of the nozzles can be between 0.1 and 0.3 mm, with length to diameter ratios of 2 to 8. We need a large pressure across the injector in order to have a fuel jet of high velocity (wf > 100 m/s). This is to atomize the fuel into small size droplets to enable rapid evaporation and to make the fuel traverse the combustion chamber in the time available in order to utilize the whole amount of air in the cylinder. We can approximate the mass flow rate of fuel through the nozzle as p ṁf = CD An 2⇢f p and the mass delivered is ✓ mf = ṁf 6n 148 11.4.1 Atomization and spray penetration The droplets that form from the atomized fuel create a spray which is cone- shaped, with a wide angle in order to maximize air usage. The diameter of the droplets is less than 10 µm. The liquid core of the spray (the outer part evaporates first) penetrates into the combustion chamber. It ceases to increase in length at a certain point after injection, but the droplets formed from it keep penetrating because of their momentum. The maximum pen- etration of the liquid core is called liquid length and it depends from the initial conditions of the spray and from condition s in the chamber. As the spray penetrates inside of the chamber, its speed decreases and its width increases since the spray starts diverging. As usual, we need to make a trade-o↵ between penetration (usage of air) and spray spread (bigger sur- face of evaporating fuel). For example, in multi-spray diesel engines, an insufficient penetration results in poor air utilization, since the air in the end of the chamber does not receive any fuel. On the other hand, a too large penetration might result in wall wetting, which increases both hydro- carbons and particulate emissions. As the spray droplets penetrate to the outer regions of the combustion cham- ber, they start interacting with the chamber walls and splitting tangentially along the wall. This makes interact with one another. Most injection sys- tems use swirl to increase fuel-air mixing. The swirl increases the width of the the spray and the mixing with air, but it reduces its penetration. Also the pressure in the chamber influences the spread and the penetration (espe- cially the penetration) of the fuel. The diameter that we use to characterize the droplets is the Sauter mean diameter. The higher the pressure, the lower the Sauter mean diameter. 11.4.2 Spray evaporation and fuel-air mixing The droplets on the edge of the spray evaporate first, creating a fuel-vapor sheet around the liquid core. The evaporation of the droplets is very rapid if compared to the entire combustion process. We have three factors a↵ecting the evaporation of the droplet. The firs one is the deceleration of the droplet due to aerodynamic drag, the second is the heat transfer to the droplet from the air and the third one is the mass transfer of vaporized fuel away from the droplet. In the chamber we can find air and fuel mixed on all values of but only the mixtures in ignition range (in terms of ) will actually burn. Around a droplet we have a value of = (0.3 ÷ 1.5). We need to make sure that we have a lot of zones in the cylinder with this values which means having a lot of small droplets dispersed in a lot of air. Most of the fuel has evaporated at the start of combustion. However, only a small part of the fuel (up to 35%) has mixed with air in flammability limits. The combustion is thus mixing-limited. 149 11.5 Ignition delay The ignition delay in a diesel engine, is defined as the time interval between the start of injection and the start of combustion. Since start of combustion is not easy to determine, we can define the ID as the time between the start of injection and the time at which we have the minimum HRR value after evaporation. Both physical and chemical processes must take place before a noticeable fraction of the chemical energy of the injected liquid fuel can be released. The physical processes (previously described) are: the atomization of the liquid fuel into droplets; the vaporization of some of these droplets; the mixing of fuel vapor with air that has been entrained into the spray. The chemical processes are the pre-major-heat-releasing combustion reactions of the fuel, air, residual gas mixture, that lead to autoignition. These processes are a↵ected by engine design and operating variables, and fuel characteristics. Good atomization requires high fuel-injection pressure, small injector hole diameters, appropriate fuel viscosity, and high cylinder air pressure at the time of injection. The rate of vaporization of the fuel droplets depends on the size of the droplets, their distribution, and their velocity, the pressure and temperature inside the combustion chamber, and the volatility of the fuel. The rate of fuel-air mixing is controlled largely by injector and combustion chamber design. We can compute the ignition delay with an Arrhenius-like equation. 11.5.1 Chemical factors a↵ecting the ID The chemical component of the ignition delay is controlled by the pre- combustion reactions of the fuel. Since the spontaneous ignition characteris- tics of the fuel a↵ect the ignition delay, this property of a fuel is very impor- tant in determining diesel engine operating characteristics such as fuel con- version efficiency, smoothness of operation, misfire, smoke emissions, noise, and ease of starting. The ignition quality of a fuel is defined by its cetane number. Cetane number is determined by comparing the ignition delay of the fuel with that of primary reference fuel mixtures in a standardized en- gine test. The reference fuels are the so-called cetane (n-hexadecane C16 H34 ) with a cetane number of 100 and the iso-cetane (2-2-4-4-6-8-8-heptamethyl- nonane) with a cetane number of 15. CN = % cetane + 0.15 · %HM N Fuel ignition quality Since calculating the cetane number is very expensive and time consuming, we usually go for the cetane index, which is based on the API gravity and mid-boiling point. The minimum required cetane number for European fuels is 51. 150 Figure 11.4: Combustion dependence from ID E↵ect of fuel properties Ignition properties a↵ect the ignition delay. The less branches they are, the better is the auto-ignition tendency. The addition of normal alkanes improves the ignition quality as the chain gets longer. Everything which is an aromatic or a closed-chain element reduces the cetane number. Biodiesel Biodiesel can be an alternative to crude oil diesel. It is derived from vegeta- bles or animal fat and consists in long chain alkyl esters. We usually blend it with regular diesel. We have a lower QLHV but a good cetane number (40 to 60). 11.5.2 Physical factors a↵ecting the ID Injection timing, engine speed, intake air and pressure, injection quantity (load) and other parameters influence the ignition delay. The injection tim- ing influences the delay, since it influences the condition that we have in the chamber. The earlier the injection, the longer the ID. The engine speed, as we have said, decreases the time for combustion, which means decreasing the ID. A larger amount of fuel will result in a shorter ID, since the residual gasses in the chamber will be hotter due to the great quantity of fuel burned in the previous cycle. We also have some e↵ects due to the swirl (not a lot) and to the oxygen concentration. 11.6 Burning rates The temperature during combustion depends from the fuel-air mixing. In fact, if we have a longer ID, we can have more air mixed with fuel and this will mean a larger temperature peak during pre-mixed combustion. Fuel-injection rate and swirl increase the temperature (HRR) in the mixing- controlling phase. 151 Figure 11.5: Factors a↵ecting values in CI Figure 11.6: Conceptual combustion in CI engines 11.7 Conceptual model of DI diesel combustion Over the past 20 or so years, much information has been gained through use of optical laser diagnostics to measure the distributions of various fuel and chemical species that play key roles in the diesel combustion and pollutant formation processes in DI systems. A precise model of the conventional diesel combustion, referred to as conceptual model, was initially developed by Dec in the late 1990s. In the fig. 11.6, is shown a sequence of illustrative drawings of a developing fuel spray and flame in a multi-spray single-injection DI diesel engine without swirl. The needle lift profile for the injector which defines the start and end of fuel injection, and apparent heat-release rate diagram for these drawings, are also plotted in next figure B (PSAV11 72) so they can be keyed to the fuel injection process and fuel chemical energy release. 152 11.8 Multiple injection strategies Modern diesel engine injection equipment permits multiple fuel injection pulses and control of the fuel injection rate during each pulse. So the basic diesel combustion process of a fuel-rich premixed flame within each individ- ual fuel spray, followed by the burning to completion of this rich mixture in a di↵usion flame around each spray, can be modified. The use of multiple injections has several objectives. The di↵erent injection pulses can modify the in-cylinder gas state to reduce the ignition delay of the primary main combustion process (through use of pilot injection), enhance the burning rate of the latter portion of the main injected fuel pulse (split injection), or reduce the in-cylinder particulate loading (post injection). 11.8.1 Pilot injection Pilot injection (injection of a modest fraction of the total amount, injected just prior to the main injection) has the main task of reducing engine noise (one of the primary sources of noise in DI diesel engines). In fact it is used to shorten the ID between SOI and SOC of the main injection. The combustion of the pilot injection fuel with its entrained air raises the temperature of the mixture around the injector, thus reducing the ID of the main-injection fuel. The shorter the delay, the less rapid the initial burning rate of the main fuel pulse, the lower the cylinder pressure gradient. Combustion noise (CN) is in fact related to the maximum cylinder pressure gradient, which usually occurs during the premixed combustion phase and is directly related to the duration of the ID. In diesel combustion, the maximum cylinder pressure gradient is sufficiently high to induce oscillatory shock waves that cause the cylinder block structure to vibrate and emit noise. At higher engine loads and speeds, the in-cylinder gases at time of injection are hotter so the ignition delays are inherently shorter so the impact of pilot injection is significantly reduced. We usually use pilot injection in order to reduce N Ox emissions. In fact, a second e↵ect of pilot injection is that combustion of the pilot fuel adds a diluent (burned gases) to the “air” surrounding the injector. Thus, the flame temperatures in the di↵usion flame surrounding each main-injection fuel spray are reduced, because the oxygen combusted in these di↵usion flames has this additional dilution beyond the nitrogen in the air and the burned gas residual from the previous cycle (PSAV11 77-78 for graphs). Typically, pilot fuel injection amounts are a few percent (5 to 15%) of the total fuel injected, depending on load, and its injection is started some 15 to 35 CA before TDC. Pilot fuel injection results in significant reductions in the ignition delay, by a factor of about two. 153 11.8.2 Post injection Post or after injection (after the main injection) primarily impacts partic- ulate emissions. Post injection with a relatively short delay (some 10 to 15 CA) between end of main injection and start of post injection pulses usefully reduces soot emissions (up to 40%). Particulate emissions are usu- ally increased with post injections closer to the end of main injection, and with significantly later post injections. Use of post injections is primarily a strategy for reducing particulate emissions at lighter loads and lower engine speeds. The late injection pulses are used to enable the performance of ex- haust system after-treatment devices. Fuel injection (and its combustion) part-way through the expansion stroke raises the exhaust gas temperature and is used to initiate the particulate burn-up or regeneration process in particulate traps/filters. 11.9 Advanced concepts of CI In advanced combustion concepts the fuel-air mixing and burning processes di↵er significantly from the normal diesel engine processes. These alterna- tive approaches are being explored for their high efficiency, and low particu- late (PM) and oxides of nitrogen (N Ox ) emissions potential. The term low temperature combustion (LTC) covers a number of advanced combustion strategies, including homogeneous charge compression ignition (HCCI) or premixed charge compression ignition (PCCI). LTC combustion can produce very low emissions of NOx and PM, but often results in increased CO and HC. The performance and emissions of engines using LTC strategies depend on the fuel properties. Advanced combustion strategies have attempted to find an in-cylinder approach to either meet these emission standards fully and thus avoiding the need to use after-treatment or at the very least, to lower the performance demands required from after-treatment systems and thus reducing their cost and complexity. HCCI was one of the early diesel combustion concepts that di↵ered from the conventional diesel combustion (CDC) mode to attract attention. The goal of HCCI work was to achieve a homogeneous mixture of air and fuel before ignition in the same way as in a conventional spark-ignition engine. This can be achieved either by in- jecting fuel into the intake port or directly into the cylinder and allowing sufficient time between injection and ignition to allow complete mixing of air and fuel. The charge then auto-ignites as it is heated by the compressed gases. In general, the approaches to low-temperature combustion are based on high level of premixing of air and fuel (but not to the point where the mixture is homogeneous). Such lean “premixed enough” mixtures feature a lower variation of local conditions of air/fuel ratio with respect to conven- tional diesel combustion (CDC) mode. Much lower soot is formed because the mixture is lean and thermal N Ox formation is largely avoided because 154 combustion temperatures remain relatively low. Nevertheless, LTC com- bustion has some disadvantages such as high CO and HC emissions and a limited load range (max bmap 8 bar). Fuel properties can have a profound impact on the performance and emissions of engines employing LTC. This is especially the case in premixed LTC approaches where ignition occurs well after air and fuel are mixed. The T plot (local equivalence ratio versus local temperature), also known as Kamimoto-Bae diagram, is a convenient way to depict the diesel combustion processes. For conventional combus- tion, the typical path of a fuel element passes through the soot formation zone, the N Ox formation and the soot oxidation zone. The formation and oxidation of soot is clearly visible from the orange flame in the flame lumi- nosity image. When a lean homogeneous mixture is achieved (HCCI), the soot and N Ox formation zones are avoided. When mixing-controlled LTC conditions are achieved with high rates of EGR (such as in PCCI), high temperatures are avoided to keep the combustion process away from the soot and N Ox formation zone (no soot luminosity is observed despite some high local equivalence ratios). 155