ABE Design 424, Design & Management of AB Processing Systems PDF
Document Details
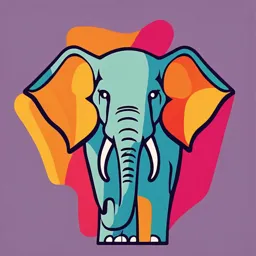
Uploaded by SpeedyPedalSteelGuitar878
Tags
Related
- Kentucky Extension Master Gardener Program Manual PDF
- 2024-2025 Horticultural Nursery Production Course - SOHAG University PDF
- Plant Design Student PPT PDF
- Philippine Agricultural Engineering Standard: Biogas Plant PDF
- Definizioni e concetti fondamentali dell'Impiantistica PDF
- Guía 1 Grado 10° 2025 PDF
Summary
This document discusses the technical aspects of agricultural and food processing plant design. It covers the stages of plant design, including identification, economic evaluation, and commissioning, as well as design specifics. The document also addresses issues like deterioration, seasonal production, and preventing contamination.
Full Transcript
ABE Design 424, Design & Management The basis for selecting and sizing of AB Processing Systems critical pieces of equipment Know about the design and lay-out...
ABE Design 424, Design & Management The basis for selecting and sizing of AB Processing Systems critical pieces of equipment Know about the design and lay-out of food plant Technical Aspects of Apply scientific principles in solving food processing & improving Agricultural and Processing product quality Ways in which the design was Plant Design optimized and the engineering basis for such optimization PLANT DESIGN DIFFERENCES IN THE DESIGN OF Plant design refers to the overall FOOD PROCESSING AND NON-FOOD design of a manufacturing PROCESSING PLANTS enterprise/facility. It moves through several stages before it is completed. The design Food processing generates wastes should consider the technical and with high BOD loads economic factors, various unit The engineering properties of foods operations involved, existing and potential and biological material are less well market conditions. known and more variable than those of pure chemicals and simple STAGES OF PLANT DESIGN mixtures of chemicals 1. Identification and selection of the Vaguely defined sensory attributes product to be manufactured. often have to be preserved, 2. Feasibility analysis and appraisal. generated or modified. 3. Economic evaluation. The storage life of foods is relatively 4. Design report preparation. limited and strongly affected by 5. Procurement of materials including temperature, pH, water activity, plant and machinery construction. maturity, prior history, and initial 6. Installation and commissioning. microbial contamination levels. Very high and verifiable levels of PLANT DESIGN SPECIFIES product safety and sterility have The equipment to be used to be provided. Performance of requirements for Foods are highly susceptible to the equipment microbial attack and insect and Interconnections and raw material rodent infestation. flows in terms of flow charts and Many foods are still living plant layouts organisms or biochemically active long after harvest or slaughter. The placement of equipment, storage spaces, shop facilities, In some cases food (e.g, ripening office spaces, delivery and shipping cheeses) contain active living facilities, access ways, site plans micro-organisms, which induce and elevation drawings chemical transformations for long Required instrumentation and periods of time. controls, and process monitoring Crop-based food raw materials may and control interconnections only be available in usable form on Utility and waste treatment a seasonal basis. Therefore, plant requirements, connections and design may involve the modeling facilities of crop availability. Food raw materials are highly The rationale for site selection variable and that variability is enhanced by the ageing of raw material and uncontrollable production and adequately sizing variations in climatic conditions. plants. Foods are frequently solid. Heat and mass-transfer problems in 2. deterioration solids have to be created in ways that are different than those used To minimize product and for liquid and gas streams. The raw material deterioration, kinetics of microbe and enzyme provisions should be made for: inactivation during thermally refrigerated and controlled induced sterilization and blanching environment storage areas, space and heat-transfer in the solids being and facilities for product inspection sterilized or blanched are strongly and for carrying out quality linked. assurance tests, surge vessels for In the case of foods, prototype processed material between products have to be consumer different operations (particularly tested so as to assure market operations which are subject to acceptability before plants for large breakdown), equipment for pre- scale production are built. cooling material stored in such Mechanical working is sometimes vessels, means of cooling, turning used to induce desired textural over or rapidly discharging the changes. contents of bins and silos when Design Considerations, Food Processing Unit excessive temperature rises, occur, Operations, Prevention of Contamination, and standby refrigeration and utility Sanitation, Deterioration, Seasonal arrangements which are adequate Production to prevent product and raw material deterioration in case of power Food plant designs must provide interruptions or unusual climatic necessary levels of sanitation, means of conditions. preventing product and material contamination and means of preventing or 3. food processing unit operations limiting product, raw material, and intermediate product deterioration due to Food processing involves naturally occurring processes. Great care many conventional unit operations must be exercised to achieve high levels of but it also involves many which product purity and preserve product differ greatly from those usually integrity. encountered in the production of industrial chemicals. These include: freezing and thawing and other 1. Seasonal production temperature-induced phase transitions or phase transition Food plants have to be analogs, freeze drying, freeze sized to accommodate peak concentration, curd and gel seasonal flaws of product without formation, development of excessive delay, and in some structured gels, cleaning and cases, have to be highly flexible so washing (the operation which as to handle different types of fruits occurs with the greatest frequency and vegetables. Modeling of crop in food processing plants), and animal growth processes can leavening, puffing, and foaming, be of great help in scheduling slaughtering, carcass disassembly, component excision, slicing and Plant design situations may arise due dicing, peeling and trimming, to one or more of the following: grading, cell disruption and maceration, pasteurization and design and erection of a sterilization, blanching, baking, completely new plant cooking (for purposes of design and erection of an addition tenderization or textural to the existing plant modification), roasting (for the facility or plant operations and purposes of flavor generation), subsequent expansion restricted radiation sterilization, mechanical by a poor site, thereby expression, structure-based necessitating the setting up of the component separation, filling and plant at a new site packaging, canning and bottling, addition of some new product to coating and encapsulation, the existing range sausage and flexible casing, adoption of some new stuffing, controlled atmosphere process/replacement of some storage, fumigation and smoking, existing equipment churning, artificially induced modernization/ automation of the ripening, fermentation, pureeing, existing facility emulsification and homogenization, expansion of the plant facility biological waste treatment, and relocating the existing plant at a controlled feeding of confined new site animals, poultry and fish. AGRICULTURAL PROCESSING 4. prevention of contamination FACILITY It is important to design Refers to land, buildings, facility with smooth, easily structures, fixtures, and improvements cleanable surfaces to prevent used for processing or producing microbial growth. Separate raw marketable agricultural products, including materials, production area and waste and residues, but not livestock, finished goods to minimize cross- poultry, or wood products. contamination. Examples of Agricultural Processing 5. sanitation Facility: Air flow and human traffic Sugar Mill flow patterns should be maintained Bio-ethanol Plant to eliminate possibilities of Poultry Dressing Plant containment transfer from dirty areas to clean ones. Very high Plant Design Specifies: levels of sanitation must be provided for foodstuffs that provide 1. Flow charts and plant layouts good substrates for the growth of outline interconnections, raw micro-organisms and when material flows, storage, shop, processing temperatures and office, delivery, shipping, and conditions favor such growth. access ways in a plant. 2. Equipment, utilities, and services to be used. 3. Strategic site location, plan, and time involved at each step, and/or elevation. process measurements) When to USE a flow chart? What can you say about the Chemical When you need to define or Process? analyze an existing process. In a chemical process, the When you need to standardize transformation of raw materials into desired or redesign a process. products usually cannot be achieved in When you need to find areas for single step, instead, the overall improvement in a process such transformation is broken down into a as unnecessary steps, gaps, number of steps that provide intermediate barriers, etc. transformations. Use a flow chart to depict and understand the steps in a - Robin Smith, Chemical Process Design process or design a new 1995 process - show connecting processes Flow Chart - identify wasteful steps - uncover sources of variation A flow chart is a representation of - identify areas for sequence of operation in a improvement processing plant or in a process. Document the current process A flow chart is a picture of the when planning and the new separate steps of a process in process after you’ve tested sequential order. improvements A flowchart depicts all of the steps in a process in sequential order CONSTRUCTION OF FLOW from START to FINISH. CHART It is a generic tool that can be adapted for a wide variety of purposes, How flow charts are constructed? and can be used to describe various processes, such as a manufacturing Steps to creating a process map process, an administrative or service process, or a project plan. It’s a Step 1: Identify the problem: Identify common process analysis took and one the goal for creating the creating the of the seven basic quality tools. flowchart and the level of detail required (high or detailed). Elements that may be included in a flowchart: o What is the process that needs to be visualized? Type its title at the Sequence of actions top of the document. Inputs and Outputs (materials or services entering or leaving the Step 2: Brainstorm all the activities that process) will be involved: Decisions that must be made o At this point, sequencing the steps Time & people involved at each isn’t important, but it may help you step (people who become involved, to remember the steps needed for your process. o Assemble the people who know STANDARD FLOWCHART the process best, include people who do the work. Collect SYMBOLS information on the process through experience, observation, Flowcharting uses standardized sets of conversation, interviews, research. symbols. The main symbols used in a flow chart with their description and examples Step 3: Figure out boundaries: are given in the following: o Where or when does the process start? Ovals show the beginning or o How does the process begin? the ending of a process. o What happens first? What happens (terminator symbol) next? Rectangles show an operation o What are the decision points? or activity that needs to be o Where do inputs and outputs come done. (process symbol) into play? o Where or when does the process Arrows represent the direction stop? of flow. Diamond show a point where Step 4: Determine and sequence the a decision must be made. steps: Arrows coming out of a diamond are usually labeled o Begin documenting the process yes or no. Only one arrow steps in sequence. comes out of an activity box. If more than is needed, you Step 5: Draw basic flowchart symbols: should probably use a decision diamond. (decision diamond) o Each element in a process map is Parallelograms show inputs or represented by a specific flowchart outputs (data symbol) symbol, which together represent process mapping symbols. Guidelines for Flowcharting Step 6: Finalize the process flowchart Following guidelines should be followed while drawing a flowchart: o Review the flowchart with other stakeholders (team member, It should be clear, neat, and easy workers, supervisors, suppliers, to follow customers, etc.) to make sure Write each step in the appropriate everyone agrees. shape o Validate your flow chart. Work from The Flow of the flowchart is either step to step asking yourself and from left to right or from top to others if you have correctly bottom represented the sequence of Start with an oval symbol labeled actions and decisions involved in START the process. Draw arrows between shapes to o Identify areas for improvement and indicate the process flow redesign the process. Only one flow line should enter and come out of the process symbol FLOW CHART EXAMPLES A high-level flowchart, outlining 6-10 major steps, give a high-level view of a process. These flowcharts display the major blocks of activity, or the major system components, in a process. These charts are especially useful in the early phases of a project and help to set priorities for improvement work. A detailed flowchart is a close-up view of the process, typically showing dozens of steps. These flowcharts make it easy to identify complexity, excessive steps, etc., in a process and should be used when you want to standardize or make changes in the process.