Easa Supplement PDF
Document Details
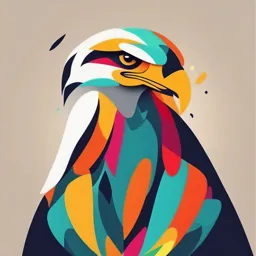
Uploaded by icon_aerospace
2023
Jeff Lambert
Tags
Summary
This document provides details of EASA and FAA regulations for maintenance on aircraft. It describes procedures, forms, and responsibilities for repair stations and maintenance, and lists various sections relating to these procedures. It also includes compliance information.
Full Transcript
EASA SUPPLEMENT ICON AEROSPACE, LLC EASA SUPPLEMENT 600 Radiator Road Indian Trail, NC 28079 EASA SUPPLEMENT REFERENCE NO. 10 TO 14 CFR par 145 REPAIR STATION MANUAL/QUALITY CONTROL MANUAL (RSM/QCM) REFERENCE NO. 11 FAA REPAIR STATION NO. 68IR700B This supplement does not form part of the 14 CFR...
EASA SUPPLEMENT ICON AEROSPACE, LLC EASA SUPPLEMENT 600 Radiator Road Indian Trail, NC 28079 EASA SUPPLEMENT REFERENCE NO. 10 TO 14 CFR par 145 REPAIR STATION MANUAL/QUALITY CONTROL MANUAL (RSM/QCM) REFERENCE NO. 11 FAA REPAIR STATION NO. 68IR700B This supplement does not form part of the 14 CFR part 145 RSM/QCM. Compliance with the FAA accepted supplement together with the 14 CFR part 145 RSM/QCM forms the basis of the European Union Aviation Safety Agency (EASA) Part-145 approval. This supplement forms the part of the applicant’s obligations for EASA Part-145 approval as specified in this guidance. Control Number: 100 Assignment: FAA Inspector Page Revision Number 1 10 Revision Date Original Issue Date May 01, 2023 November 15, 2009 EASA SUPPLEMENT ICON AEROSPACE, LLC TABLE OF CONTENTS Section Cover Table of Contents Highlights of Revisions (1) List of Effective Pages (2) Amendment Procedure (3) Introduction (4) Accountable Manager Commitment Statement (5) Approval Basis and Limitation (6) Access By EASA and FAA (7) Work Orders / Contracts (8) Approved Design and Repair Data (9) Airworthiness Directives (10) Release and Acceptance of Components (11) Certificate of Airworthiness ( C of A ) Validity (12) Release of Aircraft after Maintenance (13) Reporting of Unairworthy Conditions (14) Quality Assurance System (QAS) (15) Provision of Hanger Space for Aircraft Maintenance (16) Contracted Maintenance (17) Human Factors (18) Line Stations (19) Work Away from Fixed Locations Sample Audit Program Sample 8130-3 EASA Sample Audit Form Page Revision Number 2 10 Revision Date Original Issue Date Page 01 02 03 04 05 06 07 08 08 08-09 09-10 10 10-16 16 16 16 17-18 18 18 18-20 20 20 21 22 23-24 May 01, 2023 November 15, 2009 EASA SUPPLEMENT ICON AEROSPACE, LLC REASON FOR REVISION: Update Accountable Manager, Address Change HIGHLIGHTS: RECORD OF REVISION REVISION NUMBER ORIGINAL 1 2 3 4 5 6 7 8 9 10 REVISION DATE April 06, 2013 May 05, 2013 Jan 10, 2014 Feb 08, 2014 Dec 15, 2014 Nov 15, 2015 Jul 09, 2016 Feb 03, 2020 Feb 19, 2021 APR 07,2021 MAY 01, 2023 INSERTION DATE April 06, 2013 May 05, 2013 Jan 10, 2014 Feb 08, 2014 Dec 15, 2014 Nov 15, 2015 Jul 09, 2016 Feb 03, 2020 Feb 19, 2021 APR 07,2021 MAY 01, 2023 PAGES BY ALL ALL ALL ALL 1,2,3,4 ALL ALL ALL ALL 1,2,3,4 ALL AG AG AG AG AG AG AG AG AG AG NH MANUAL DISTRIBUTION MANUAL NUMBER MASTER 100 101 102 103 104 ASSIGNED TO: ACCOUNTABLE MANAGER FAA INSPECTOR DIRECTOR OF OPERATIONS QUALITY ASSURANCE MANAGER SHOP EASA MANUAL Page Revision Number 3 10 TITLE OR ORGANZATION Accountable Manager Aviation Safety Inspector Director Of Operations Quality Assurance Manager Icon Aerospace Icon Aerospace Revision Date Original Issue Date CONTACT INFORMATION 704-821-4266 704-319-7020 704-821-4266 704-821-4266 704-821-4266 704-821-4266 May 01, 2023 November 15, 2009 EASA SUPPLEMENT ICON AEROSPACE, LLC List OF Effective Pages Section Cover Table of Contents Highlights of Revisions (1) List of Effective Pages (2) Amendment Procedure (3) Introduction (4) Accountable Manager Commitment Statement (5) Approval Basis and Limitation (6) Access By EASA and FAA (7) Work Orders / Contracts (8) Approved Design and Repair Data (9) Airworthiness Directives (10) Release and Acceptance of Components (11) Certificate of Airworthiness ( C of A ) Validity (12) Release of Aircraft after Maintenance (13) Reporting of Unairworthy Conditions (14) Quality Assurance System (QAS) (15) Provision of Hanger Space for Aircraft Maintenance (16) Contracted Maintenance (17) Human Factors (18) Line Stations (19) Work Away from Fixed Locations Sample Audit Plan Sample 8130-3 EASA Sample Audit Form Page Revision Number 4 10 Revision Date Original Issue Date Page 01 02 03 04 05 06 07 08 08 08 09 10 10-15 15 15 15 16-17 17 17 18-19 19 19 20 21 22-23 Revision Date MAY 01, 2023 MAY 01, 2023 MAY 01, 2023 MAY 01, 2023 MAY 01, 2023 MAY 01, 2023 MAY 01, 2023 MAY 01, 2023 MAY 01, 2023 MAY 01, 2023 MAY 01, 2023 MAY 01, 2023 MAY 01, 2023 MAY 01, 2023 MAY 01, 2023 MAY 01, 2023 MAY 01, 2023 MAY 01, 2023 MAY 01, 2023 MAY 01, 2023 MAY 01, 2023 MAY 01, 2023 MAY 01, 2023 MAY 01, 2023 MAY 01, 2023 May 01, 2023 November 15, 2009 EASA SUPPLEMENT ICON AEROSPACE, LLC AMENDMENT PROCEDURE This manual will be maintained current at all times. Icon Aerospace, LLC shall assign copies of its manual as required to ensure that all personnel have easy and ready access to it. The appropriate Flight Standards Office (FSO) shall be assigned a copy of this manual. The working practices and procedures are reflected in the 14 CFR part 145 RSM / QCM. A complete list of the assigned copies of the manual can be found in this manual. To prevent access to information that is not maintained current, no employee may make a copy of the manual or pages from the manual, without clearly identifying them as uncontrolled copies. The Quality Assurance Manager (QAM) is responsible for coordinating all revisions to this manual with the local FSDO by forwarding hard a copy of the contemplated changes thirty (30) days prior to the issuance date for comment. Revisions will be recorded on the list of effective pages by the revision date and the revised material or text will be shaded gray until the next revision. If comments are received, they will be directed for proper disposition in accordance with the CFRs. Distribution to the FAA will be by first class mail, hand delivered or electronic mail unless otherwise directed in writing by the local FSDO. Upon review by the FAA or after (30) days, whichever is shorter, the QAM shall update the list of effective pages with the correct revision date and sign the revised list to indicate approval before copying, distribution and insertion. The Master Manual shall be kept and maintained on file by the QAM and contain the signed original documents. The QAM is also responsible for coordinating and distributing the revised versions of this manual. Revisions will be distributed to all those assigned a controlled copy of the manual. The person named on the cover of the manual copy, or an individual delegated that authority will— • • • Revise the manual. Make the appropriate entry in the Record of Revisions Insert the updated List of Effective Pages If the manual has been completely revised, The QAM will ensure that old manuals shall be destroyed. Each Supervisor and Inspector working for Icon Aerospace, LLC will have a current copy of this manual and should thoroughly understand its contents. It will also be available to other repair station personnel. Failure to ensure that the FAA TITLE 14 CFR PART 145 RSM / QCM and this EASA Supplement are kept up to date in respect of regulatory changes (including changes to the MAG) and that the Repair Station staff complies with the procedures therein could invalidate the EASA Approval. Changes to the MAG shall be implemented, as applicable, within 120days after the signature date. Page Revision Number 5 10 Revision Date Original Issue Date May 01, 2023 November 15, 2009 EASA SUPPLEMENT ICON AEROSPACE, LLC INTRODUCTION This Supplement is necessary to perform maintenance on articles installed on aircraft landing in EU member states. EASA Part-145 is a European requirement similar to 14 CFR part 145. Annex 2 agreed to by the FAA and EASA specifies the basic differences between EASA Part-145 and 14 CFR part 145 and identifies these differences as special conditions. A 14 CFR part 145 repair station can be EASA Part-145 approved when the repair station complies with the maintenance special conditions as detailed in this procedure in addition to complying with 14 CFR parts 145 and 43. The supplement should help ensure that the organization is working in accordance with the provisions of its EASA Part-145 Approval Certificate and to ensure that the differences between the EASA and FAA regulations are taken into account. Page Revision Number 6 10 Revision Date Original Issue Date May 01, 2023 November 15, 2009 EASA SUPPLEMENT ICON AEROSPACE, LLC ACCOUNTABLE MANAGER COMMITMENT STATEMENT This Supplement in conjunction with the approved FAA TITLE 14 CFR PART 145 RCM / QCM defines the organization and procedures upon which EASA approval is based. These procedures are approved by the undersigned, and must be adhered to as applicable, when maintenance work/orders are being processed under the conditions of the EASA Part-145 approval. It is accepted that the repair station's procedures do not override the necessity of complying with any additional requirements formally published by EASA and notified to this organization from time to time. It is understood that EASA will issue an Approval Certificate and list Icon Aerospace, LLC in an EASA published list as long as EASA is satisfied that the procedures are being followed and work standards maintained. It is further understood that EASA reserves the right to revoke the Approval Certificate if EASA determines that procedures are not followed or standards not upheld. In the event that the Accountable Manager is replace the new Manager must sign the statement to ensure continuous EASA Part-145 Approval and provide the FAA ASI with the Amendment of the statement. _____________________ ______________ Jeff Lambert Accountable Manager Icon Aerospace, LLC Date Page Revision Number 7 10 Revision Date Original Issue Date May 01, 2023 November 15, 2009 EASA SUPPLEMENT ICON AEROSPACE, LLC APPROVAL BASIS AND LIMITATION EASA approval is based upon compliance with 14 CFR parts 145 and 43 except were varied by the special conditions specified in Annex 2 and associated guidance. However, this approval must not exceed the ratings permitted by Commission Regulation (EU) No 1321/2014. The approval of maintenance work is limited to the scope of work permitted under the current Certificate issued by the FAA to the repair station in accordance with FAA TITLE 14 CFR PART 145 for work carried out within the United States. Deviations have to be agreed to on a case-bycase basis by the JMCB. ACCESS BY EASA AND FAA. In accordance with the Agreement Annex 2, Appendix 1, paragraph 1.2 It is understood that Icon Aerospace, LLC and its staff will allow undenied access to its facilities and records to EASA and the FAA to ascertain compliance with 14 CFR part 145, the EASA special conditions, procedures and standards to investigate specific problems. ICON Aerospace LLC confirms that it will accept investigation and enforcement action that may be taken by EASA in accordance with any relevant EU regulations and EASA procedures and that the organization will cooperate with these actions. WORK ORDERS/CONTRACTS Icon Aerospace, LLC receives a clearly stated work order describing the scope of the work to be accomplished from the customer. Work orders are reviewed at the receiving inspection by the Quality Assurance Manager prior to assigning ICON Aerospace LLC work order to ensure the customers work orders completely specify the inspection, repairs, alterations, overhaul, airworthiness directives and parts replacement that should be carried out. All of this information is listed on to ICON Aerospace LLC work order to accompany the item being serviced. The customers work order is filed with the ICON Aerospace LLC work order. Procedures for completing a Work Order are found in ICON RSM FORMS MANUAL SECTION 3.1.17-I PAGE 47. Icon Aerospace, LLC attaches a copy of work order to each item containing all information including customer request. This work order accompanies the item throughout the repair procedure providing repair and inspection personnel all required information to ensure that compliance with the customer’s request is carried out. At the completion of service for the item during final inspection the inspector verifies that all customer requests have been carried out. In the event that an item requires additional service not called out by the customer, a customer service representative from ICON Aerospace LLC will contact the customer an inform them. This will be done in form of a written teardown report and must be approved by the customer before completion of work The customer remains responsible for correctly informing the repair station by work order of all required maintenance and alterations. Page Revision Number 8 10 Revision Date Original Issue Date May 01, 2023 November 15, 2009 EASA SUPPLEMENT ICON AEROSPACE, LLC APPROVED DESIGN AND REPAIR DATA Changes to the type design: Major Changes, Minor Changes, STCs. The EASA-approved design engineering data is normally data supplied by an EASA Design Organization Approval (DOA) holder, or data approved by the National AA of the Type Certificate Holder (or equivalent), or data supplied by the customer and approved by the EASA. In all cases, the customer is responsible for confirmation of data approval. Details for the acceptance and /or validation of FAA approved changes to the type design by EASA are contained in Annex 1 to the Agreement and in the associated Technical Implementation Procedures for airworthiness and Environmental Certification (TIP). NOTE: EASA defines “design change” as a change to the type design. EASA does not automatically accept alterations that affect type design. Repairs Design Data in Support of Major and Minor Repairs FAA shall approve design data in support of major repairs in accordance with FAA Order 8110.4, Type Certification; FAA Order 8110.37, Designated Engineering Representative Guidance Handbook; FAA Order 8100.15, Organization Designation Authorization Procedures; and FAA Order 8900.1, Flight Standards Information Management System. Minor repairs are made in accordance with “acceptable” data, in accordance with 14 CFR part 43. EASA shall approve design data in support of repairs in accordance with EASA Part 21 Subpart M-Repairs and EASA’s procedure Type Certificate Change and Repair Approval. EASA Acceptance of FAA Repair Design Data 1. EASA shall accept data used in support of major repairs, in accordance with Annex 1 to the agreement and the associated TIP. 2. EASA shall also accept data used in support of minor repairs, in accordance with Annex 1 to the Agreement and the associated TIP. NOTE: An EU company must use EASA Part 21 for the approval of repair data for use on an EU-registered aircraft. Unless the minor repair data has been previously used on an Nregistered aircraft, an EU company cannot determine any data to be acceptable data under 14 CFR Part 43 for use on an EU-registered aircraft. In these circumstances, repair design data are considered to be EASA approved following its approval or acceptance under the FAA’s system, this process does not require application to EASA or compliance findings to the EASA certification basis. Alterations: Details for the acceptance and/or validation of the FAA-approved design data used in support of alterations by EASA are contained in the TIP associated with Annex 1 of the Agreement. Page Revision Number 9 10 Revision Date Original Issue Date May 01, 2023 November 15, 2009 EASA SUPPLEMENT ICON AEROSPACE, LLC AIRWORTHINESS DIRECTIVES This repair station will hold a copy of all Airworthiness Directives the customer requires. It's understood that certain EASA customers may supply non-FAA Airworthiness Directives. The customer is responsible for specifying any Airworthiness Directives compliance required during maintenance through the work order. This Repair Station checks new or previous EASA/FAA Airworthiness Directives (AD Notes) issued against components it maintains. Any applicable AD’s will be filed with the OEM data to ensure compliance prior to return to service. The repair station will advise in writing in form of a teardown report for approval of any applicable AD’s required to be performed on item to the customer. The teardown report has a section to list any applicable AD’s performed on item. In the event that the customer does not approve the applicable AD or for some reason the AD cannot be complied with, the item will be deemed unserviceable, and a teardown report will be provided to the customer. This repair station will not perform any repairs to a non-compliant item and will not release item for return to service. RELEASE AND ACCEPTANCE OF COMPONENTS Approval for release or return to service of components shall be carried out in accordance with FAA TITLE 14 CFR PART 43.9 accept that Section B, Appendix 1, paragraphs 7 to 10 of this supplement must also be taken into account. At the completion of maintenance and FAA Form 8130-3 must be issued as a maintenance release by the repair station NOTE: For more information on using FAA Form 8130-3 on new parts, please refer to the TIP associated with Annex 1 of the Agreement. The FAA Form 8130-3 includes the EASA Part-145 release to service certifying statement with the EASA Part-145 Approval Certificate number in block 12, and specify any overhaul, repairs, alterations, Airworthiness Directives, replacement parts, PMA parts and it should quote the reference and issue/revision of the approved data used. An example completed FAA From 8130-3 dual release must be included by the repair station in the supplement. Instructions must be included in the supplement specifying that blocks 13a through 13e are not to be used by the repair station. The signature of the person returning the component for release or return to service must be in block 14b with the FAA Repair Station Certificate number in block 14C. The status of the component (repaired, inspected, overhauled, etc.) must appear in block 11 with any relevant comments including detailed references to approved data, AD’s etc. in block 12. Example: “Overhauled in accordance with CMM 111, Section X, Rev 2, S/B 23, and in compliance with FAA AD xyz. Full details held on WO 456.” Page Revision Number 10 10 Revision Date Original Issue Date May 01, 2023 November 15, 2009 EASA SUPPLEMENT ICON AEROSPACE, LLC Block 12 must also include the following statement: Certifies that the work specified in block 11/12 was carried out in accordance with EASA Part-145 and in respect to that work the component is considered ready for release to service under EASA Part-145 Approval Number: EASA.145.6295 NOTE: In the case of maintenance carried out by a U.S.-based EASA Part-145 approved organization subject to the Agreement, EASA only recognizes the dual release FAA Form 8130-3 for component, engine, or propeller maintenance. Note that the sub clause “except as otherwise specified” is intended for use with two types of deviations as follows: The case where all required maintenance was not carried out. In this case list the maintenance not carried out in Block 12 and/ or attachments. The case where the particular maintenance requirement was only EASA- approved and not FAA-approved. The repair station must identify in the RSM/QCM roster staff authorized to sign an FAA Form 8130-3 (maintenance release) for approving a maintained or altered article for release or return to service. The supplement should include information regarding the acceptability of components authorized for use during maintenance. that should comply with the following paragraphs and the table on MAG Change 8 page 99. Component means any component part of an aircraft up to and including a complete power plant and any operational or emergency equipment. Only the following new and used serviceable components that meet the requirements listed below may be fitted during maintenance. New Components New components must be traceable to the Production Approval Holder (PAH) and be in a satisfactory condition for installation. An authorized release document, as detailed below, must accompany the new component. 1. For new components from a U.S.-PAH, release must be documented on an FAA Form 8130-3 as a new part. NOTE: New parts that were received into inventory prior to October 1, 2016 must, at a minimum, have a document or statement (containing the same technical information as an FAA Form 8130-3) issued through a design approval holder (DAH), by the PAH or supplier with direct ship authority. These parts in inventory, documented with the required information, will be grandfathered and remain suitable for installation into EU articles, provided the certification/release date of these parts is prior to October 1, 2016. Page Revision Number 11 10 Revision Date Original Issue Date May 01, 2023 November 15, 2009 EASA SUPPLEMENT ICON AEROSPACE, LLC 2. For new components released by an EU-PAH, release must be documented on an EASA Form 1, as a new part. 3. Fabricated parts, produced by an appropriately rated repair station with a quality system, for consumption into a repair or alteration of a product or article in accordance with 14 CFR part 21, section 21.9(a)(6), and part 43, are not subject to the foregoing provision. 4. Standard parts are not subject to the forgoing provisions, provided such parts are traceable to the manufacturer, accompanied by a conformity statement, and are in a satisfactory condition for installation. NOTE: EASA Standard Parts Definition: Per AMC M.A.501C, “Standard Parts are: parts manufactured in complete compliance with an established industry, Agency, competent authority or other Government specification which includes design, manufacturing, test and acceptance criteria, and uniform identification requirements. The specification should include all information necessary to produce and verify conformity of the part. It should be published so that any party may manufacture the part. Examples of specifications are National Aerospace Standards (NAS), Army-Navy Aeronautical Standard (AN), Society of Automotive Engineers (SAE), SAE Sematec, Joint Electron Device Engineering Council, Joint Electron Tube Engineering Council, and American National Standards Institute (ANSI), EN Specifications etc…” 5. PMA parts may only be accepted as detailed in subparagraph 1 above and in the TIP associated with Annex 1 of the Agreement. 6. Engines rebuilt by the production approval holder can be accepted as specified in the TIP associated with Annex 1 of the Agreement. 7. Acceptable components based on provisions of other Bilateral Agreements are not contained in this guidance. Please refer to the individual Agreements or the summary table published on the EASA Web site: https://www.easa.europa.eu/faq/66700 Used Components 1. Used components must be traceable to FAA-and/or EASA-certificated facilities that are approved and authorized to certify the maintenance, preventive maintenance, and/or alterations which they have performed. In the case of life limited parts, the life used must be appropriately documented. The used component must be in a satisfactory condition for installation and be eligible for installation as stated in the PAH parts catalogue or aviation authority (AA) approval document. An authorized release document, as provided below, must accompany the used component. 2. An FAA Form 8130-3 issued as a dual maintenance release must accompany used components from EASA-approved U.S.-based 14 CFR part 145 repair stations. 3. Used components from a 14 CFR part 145 repair station not EASA-approved must not be used even if accompanied by an FAA Form 8130-3. 4. An EASA Form 1 issued as a maintenance release shall accompany used components from EASA Part-145 approved maintenance organizations not located in the U.S. Page Revision Number 12 10 Revision Date Original Issue Date May 01, 2023 November 15, 2009 EASA SUPPLEMENT ICON AEROSPACE, LLC 5. A Canadian Form One issued as a maintenance release must accompany used components from a Canadian EASA-approved maintenance organization. 6. Acceptable components based on provisions of other Bilateral Agreements are not contained in this guidance. Please refer to the individual Agreements or the summary table published on the EASA Website: https://www.easa.europa.eu/faq/66700 7. The following table is a summary of possible cases: (REFER TO TABLE I IN EASA MAG CHANGE 8 EFF DATE 19/MAR/2021 PAGE 99.) Release statements for cases where compliance with both regulatory systems cannot be met (parts installed with single release, AD’s not being complied with). United States One or more products/articles were installed with an EASA Form 1 single release, so the final assembly cannot be released with an FAA Form 8130-3 dual release. The final release should be issued with the following statements in the specified blocks. “The final assembly is eligible to be installed only on an EU-registered aircraft.” In block 14a, check only the box mentioning “Other regulation specified in block 12.” Do not check box that states compliance to § 43.9. In block 12, the following text should be inserted: “Certifies that the work specified in Block 11/12 was carried out in accordance with EASA Part 145 and in respect to that work the component is considered ready for release to service under EASA Part 145 approval no.________. This product/article meets § 43.9 requirements, except for the following items, and therefore is “not” eligible to be installed on U.S.-registered aircraft:” (List the Items) Europe One or more products/articles were installed with an FAA Form 8130-3 single release, so the final assembly cannot be released with an EASA Form 1 dual release. The final release should be issued with the following statements in the specified blocks. “The final assembly is eligible to be installed only on a US-registered aircraft.” In block 14a, check only the box mentioning “Other regulation specified in block 12.” Do not check the box that states compliance to 145.A.50. In block 12, include the following release statement: “The work identified in Block 11 and described herein has been accomplished in accordance with 14 CFR part 43 and in respect to that work, the items are approved for return to service under certificate no._______. “This product/article meets 145.A.50 requirements, except for the following items, and therefore is “not” eligible to be installed on an EU-registered aircraft:” (List the Items) Page Revision Number 13 10 Revision Date Original Issue Date May 01, 2023 November 15, 2009 EASA SUPPLEMENT ICON AEROSPACE, LLC Release Procedure for Components That Are Used Only in an EASA-approved Design (TC/STC). FAA/EASA Policy. The FAA and EASA acknowledge the need for U.S.-based repair stations to perform maintenance, preventive maintenance, and/or alterations on component parts to be installed on non-U.S. type-certificated aircraft. The U.S.-based repair station, under its FAA certificate and ratings, may perform maintenance and/or alteration activities and provide the FAA Form 8130-3 Airworthiness Approval for return to service for the work performed on component parts to be installed on non-U.S. type certificated aircraft. Scope of Maintenance Work Authorized. The authorization/approval to perform maintenance on component parts to be installed on non-U.S. type-certificated aircraft is limited to the scope of the repair station’s FAA ratings and EASA approval based upon compliance with 14 CFR parts 43 and 145, except where it is varied by the Special Conditions specified in the MAG. The EASA approval does not exceed the ratings permitted by Commission Regulation (EU) No 1321/2014. Repair Station Request to Perform Maintenance and/or Alterations. The repair station’s Accountable Manager will submit to the FAA PI assigned, in writing, a request to perform maintenance, preventive maintenance, and/or alterations on component parts to be installed on non-U.S. type-certificated aircraft. The written request must include a revised EASA Supplement listing the component parts, the scope of maintenance that will be performed on the parts, including a self-assessment of the following elements: tooling, equipment, data used, training, facilities, qualified personnel, etc. FAA Review of Repair Station Request. The FAA PI who has oversight responsibility for the repair station shall review the request and verify the repair station ratings and that EASA approval supports the maintenance activities requested (i.e., tooling, equipment, data used, training, qualified personnel, facilities) and review the revised EASA Supplement containing the listed component parts. Once reviewed and found acceptable to the PI, the PI shall forward the Accountable Manager’s request and EASA Supplement page listing the component parts to EASA for acceptance (e-mail to [email protected]). EASA Review of Repair Station Request. Upon receipt, EASA shall review the request and associated EASA Supplement page listing the parts and shall provide, in writing, the acceptance or denial. EASA shall e-mail the repair station’s Accountable Manager of EASA’s decision and shall carbon copy the FAA PI via e-mail. Return to Service. The repair station’s EASA Accountable Manager (or his/her delegate authorized and listed on the return to service roster) must ensure the repair station issues the FAA Form 8130-3 Airworthiness Approval return to service by signing blocks 14b and 14c. The EASA Accountable Manager (or his/her delegate authorized and listed on the return to service roster) must check block 14a, the box stating, “Other regulation specified in Block 12.” The repair station’s EASA Accountable Manager (or his/her delegate authorized and listed on the return to service roster) must notate in block 12, “Certifies that the work performed in block 11/12 was carried out in accordance with EASA Part 145 and, in respect to that work, the component part is considered approved for release or return to service under EASA Part 145 approval no. ____________ for installation on European Union-registered aircraft only. Not for installation on U.S.-registered aircraft or components of such aircraft.” Page Revision Number 14 10 Revision Date Original Issue Date May 01, 2023 November 15, 2009 EASA SUPPLEMENT ICON AEROSPACE, LLC FAA Oversight. The FAA PI who is assigned oversight responsibility for the repair station shall conduct surveillance activities of the non-U.S. type certificated component parts when conducting normal oversight for the EASA. CERTIFICATE OF AIRWORTHINESS (C OF A) VALIDITY Not applicable to Icon Aerospace, LLC RELEASE OF AIRCRAFT AFTER MAINTENANCE Not applicable to Icon Aerospace, LLC REPORTING OF UNAIRWORTHY CONDITIONS When serious defects are found in EU-registered aircraft or components received from an EU customer, the defects must be reported to EASA, the aircraft design organization, the authority of the state of registry and the customer or operator within 72 hours. When reporting to EASA the identity of the customer must be included to allow follow up action. A report will be submitted in a form and manner acceptable to EASA containing the information required by EASA Part-145 in English through the EASA online platform: http://www.aviationreporting.eu/ Submit this form when reportable problems are found on an aircraft, powerplant, propeller, or component thereof that is subject to the regulatory control of EASA. RESPONSABILTY. The Accountable Manager and Quality Assurance Manager are responsible for completing and submitting reports of un-airworthy conditions to EASA NOTE: EASA Part-145 reporting requirements include SUP reporting requirements. Page Revision Number 15 10 Revision Date Original Issue Date May 01, 2023 November 15, 2009 EASA SUPPLEMENT ICON AEROSPACE, LLC QUALITY ASSURANCE SYSTEM (QAS) The primary objective of the QAS system is to enable the organization to satisfy itself that it can deliver a safe product and that it remains in compliance with 14 CFR part 43, 14 CFR part 145 and the EASA Special conditions. N / A (ICON Aerospace LLC does not contract or subcontract any maintenance) ICON Aerospace, LLC. Will develop an audit plan annually that includes assessing a repair station’s compliance with the applicable paragraphs of 14 CFR part 43, 14 CFR part 145, and the EASA special conditions There are two elements to the system: An independent audit system 1. The independent audit system is a process of a sample audit of all aspects of the repair station's ability to carry out all maintenance to the required standards. It represents an overview of the complete maintenance system and does not replace the need for mechanics to ensure that they carry out maintenance to the required standard, nor does it replace any associated inspection / quality control system. Independence will be established by ensuring that audits are not carried out by the personal responsible for the function, procedure or product being audited. 2. The audit system must cover the following. • Procedural audits: The audits will monitor compliance with required aircraft/aircraft components standards and adequacy of the maintenance procedures to ensure that such procedures invoke good maintenance practices and result in airworthy aircraft/aircraft components. • Product audits: The sample check of a product means to witness any relevant testing and visually inspect the product and associated documentation. The sample check should not involve repeat disassembly or testing unless the sample check identifies requiring such action. 3. It is acceptable to use personnel from one section/department to audit the work and products of another section/department in accordance with a procedure under this paragraph which defines the audit program. 4. The process of sample audits will be subdivided over a year period IAW with an audit program. All applicable 14 CFR PART 43 and 145 provisions and the EASA special conditions as detailed in the EASA/FAA MAG should be checked at least once per year against each primary product line. 5. A primary product line is any one avionic or mechanical product line where the systems and procedures are very similar throughout that product line. 6. Not applicable to ICON Aerospace LLC (ICON Aerospace LLC has more than 10 employees and will conduct all audits using in house personnel.) Page Revision Number 16 10 Revision Date Original Issue Date May 01, 2023 November 15, 2009 EASA SUPPLEMENT ICON AEROSPACE, LLC A management/control and follow up system. 1. The management control follow up system which must not be contracted to outside persons, consists of a system to ensure that all findings/discrepancies resulting from the independent audit system are corrected in a timely manner and to enable the accountable manager to remain informed of the state of compliance and any safety issues. The Accountable Manager should hold routine meetings to check the progress on clearing outstanding findings/discrepancies. The accountable manager should meet at least once per year with the senior staff involved to review the overall performance 2. N/A (ICON Aerospace LLC does not have additional locations.) 3. N/A (ICON Aerospace LLC does not have line stations.) 4. Not applicable to ICON Aerospace, LLC (ICON Aerospace LLC does not have additional locations.) 5. One example of the particular product line must be used as the basis of each audit except in the case of stores audits when a random selection of parts should be used for the audit. An example audit program is attached. 6. A report must be prepared for each audit carried out describing what was audited and any resulting findings/discrepancies. The report should be sent to relevant department for rectification action giving target rectification dates. The relevant departments are required to rectify the findings/discrepancies and inform the quality department. 7. A product should be selected in each workshop and the sample audit program conducted at least once per year (twice per year in the case of a repair station with fewer than 10 employees and which chooses to contract the audit to an outside person except that in the case of procedures which are common throughout the repair station, the procedures need only be audited once per year if there are no problems.) PROVISION OF HANGER SPACE FOR AIRCRAFT MAINTENANCE • N/A (ICON Aerospace LLC does not have a hanger.) CONTRACTED MAINTENANCE • N/A (ICON Aerospace LLC does not contract or subcontract any maintenance) Page Revision Number 17 10 Revision Date Original Issue Date May 01, 2023 November 15, 2009 EASA SUPPLEMENT ICON AEROSPACE, LLC 17. HUMAN FACTORS The Accountable Manager along with the Quality Assurance Manager are responsible for training of Human Factors. The duties include maintaining an adequate and knowledgeable staff to plan, perform, supervise, and inspect the work being performed. The Accountable Manager may delegate all duties to qualified persons; however, such delegation does not relieve the Accountable Manager of the overall responsibility. Although company governing policies and procedures are included within the training manual, individual departmental manager shall also be responsible for but not limited to ensuring that all staff is adequately qualified experienced and trained to perform their assigned tasks, which include: General/Introduction to human factors: Safety Culture/Organizational factors: Assuring an organizational atmosphere where safety and health is understood to be, and is accepted as, a high priority. Human Error: The quality of work performed by personnel within their departments. Human performance and limitations: The monitoring of employee performance to ensure not only acceptable performance, but also includes the well-being of the employee from not being over-worked. Environment: The provision and maintenance of an infrastructure required to achieve product conformity. This infrastructure includes workspaces and associated utilities, including temperature, humidity, cleanliness, and lighting. Procedures, information, tools and practices: Ensuring that all staff are familiar with, and have ready access to company and departmental procedures, and that the relevant procedures are effectively implemented. Ensure availability of equipment to include tools, test equipment, process equipment and supporting services such as transport or communication identification of resources to support operation and maintenance of the product. Communication: Initiating, implementing and maintaining work instructions for the departments. Teamwork: Coordinating personnel to work together, creating a healthy competition that motivates individuals and helps the team excel. Professionalism and integrity: Conducting oneself with responsibility, integrity, accountability, and excellence. Communicating effectively and appropriately and always finding a way to be productive. While maintaining moral and integrity. Organization’s Human Factors program: Personnel are trained to ensure and understand all applications of human factors principles. These training sessions are documented and maintained in the individual personnel training records. Recurrent training interval is every 2 years. Various procedures exist that allow for detection and rectification of maintenance errors which may endanger the safe operation of an aircraft. All items serviced at ICON Aerospace LLC are inspected during service and again at final inspection to insure detection of any maintenance error prior to release of unit. In the event that a maintenance error is detected the inspector will ensure the error is corrected and evaluate the situation to determine the root cause. Once determined corrective action is taken to insure the error doesn’t happen again. Page Revision Number 18 10 Revision Date Original Issue Date May 01, 2023 November 15, 2009 EASA SUPPLEMENT ICON AEROSPACE, LLC ICON Aerospace LLC does not have shift changeovers, provides full health insurance, maintains normal hours of operation and does not operate on a weekend (with the exception of an AOG) which is only for required personnel. Personnel are at liberty to take breaks and time for lunch as required including vacation and personal time. An open-door policy is maintained with personnel ensuring freedom of communication with supervisors in the event of illness, stress or fatigue. These cases will be handled by The Accountable Manager which determines the appropriate resolution. In the event that a person requires time away from work because of any given reason this person must then be cleared for return to work by The Accountable Manager. NOTE: The recurrent human factors training must not be a simple repetition of the initial training. Instead, it must be built upon errors/lessons learned and the experiences within the organization (or group of organizations). This should help ensure that the results of internal quality audits and occurrence reports are brought to the attention of all staff. LINE STATIONS Not applicable to Icon Aerospace, LLC WORK AWAY FROM FIXED LOCATIONS Not applicable to Icon Aerospace, LLC Page Revision Number 19 10 Revision Date Original Issue Date May 01, 2023 November 15, 2009 EASA SUPPLEMENT ICON AEROSPACE, LLC SAMPLE AUDIT PLAN CHECK LIST (ONCE A YEAR) Audit Subject Jan Feb Mar Apr May Jun Jul Aug Sep 14 CFR 43.7 Person Auth to Return to Service 14 CFR 43.9 Cont of Maint & Alteration Record 14 CFR 43.12 Falsification of Records 14 CFR 43.13 Standards 14 CFR 43.15 Additional Standards EASA Supp 4 Accountable Manager Statement EASA Supp 7 Customer Work Order EASA Supp 8 Approved Design and Repair Data EASA Supp 9 Airworthiness Directives EASA Supp 10 Release and Acceptance of Components EASA Supp 13 Reporting Unairworthy Conditions EASA Supp 14 Quality Assurance System EASA Supp 17 Human Factors KEY: Page Revision Number 20 10 Revision Date Original Issue Date May 01, 2023 November 15, 2009 Oct Nov Dec EASA SUPPLEMENT Page Revision Number ICON AEROSPACE, LLC 21 10 Revision Date Original Issue Date May 01, 2023 November 15, 2009 EASA SUPPLEMENT ICON AEROSPACE, LLC FAA REPAIR STATION # 68IR700B EASA REFERENCE EASA.145.6295 600 Radiator Rd. Indian Trail NC 28110 TEL: 704-821-4266 Fax 704-821-4286 EASA Sample Audit Form 1) Audit Subject: ______________________ 2) Subject Title: ______________________ YES a) Notes: b) Notes: c) Notes: d) Notes: e) Notes: f) Notes: g) Notes: NO N/A Has an audit been performed I.A.W. Audit Subject? Are there any discrepancies? Is corrective action required? If any discrepancies, has the root cause bee determined? Were samples taken I.A.W. EASA sampling program? Were discrepancies corrected? Is the RS in compliance with Audit Subject? Audit Results: 1. LIST CORRECTIVE ACTION REQ.: _________________________________________ _________________________________________________________________________ 2. US A RE-AUDIT REQ.: ___________________________________________________ _________________________________________________________________________ AUDITOR:____________________________ SIGNATURE: ___________________________ TITLE: _______________________________ DATE: ________________________________ EASA SAMPLE AUDIT FOR # EASA-100 Page Revision Number 22 10 Revision Date Original Issue Date May 01, 2023 November 15, 2009 EASA SUPPLEMENT ICON AEROSPACE, LLC EASA SAMPLE AUDIT FORM INSTRUCTIONS. 1. Insert Audit Subject. (14 CFR 43.xx or EASA Supp. xx) 2. Insert Audit Subject title EXP. (Persons Authorized to Return To Service.) a. Auditor must have a copy of Audit Subject as a reference to perform audit. List any notes in the notes column. b. Check if any discrepancies found. List any notes in the notes column. Use a separate page if required for additional space. c. Check if any corrective action is required. List any notes in the notes column. Use a separate page if required for additional space. d. Check if discrepancies to determine the root cause. List any notes in the notes column. Use a separate page if required for additional space. e. Check if samples were required and taken. List any notes in the notes column. Use a separate page if required for additional space. Attach samples to audit form. f. Check if discrepancies were corrected. List any notes in the notes column. Use a separate page if required for additional space. g. Check if the RS is within compliance. List any notes in the notes column. Use a separate page if required for additional space. Audit Results 1. List Corrective actions. Corrective actions must have final resolution in order for RS to be in compliance. 2. Is a re-audit req. if corrective actions must be initiated a re-audit is required to follow up corrective action. List date for re-audit. List auditors name, signature, title and date Audit was performed. Page Revision Number 23 10 Revision Date Original Issue Date May 01, 2023 November 15, 2009