EASA Module 14 Propulsion PDF
Document Details
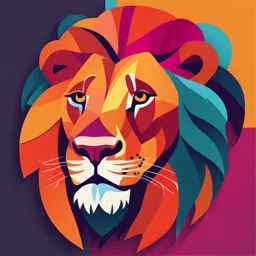
Uploaded by EvocativeJasper9301
2017
Omar Kahn, Roger Petersen
Tags
Related
- FAA Aviation Maintenance Technician Handbook PDF Chapter 15 Ice & Rain Protection
- Easa Part 66 Aviation Maintenance Technician Certification Series PDF
- EASA Module 07A Maintenance Practices PDF
- Aviation Maintenance Technician Handbook PDF
- Aviation Maintenance Assertiveness Training Module 29 PDF
- Aviation Australia: Types of Error in Maintenance Tasks PDF
Summary
This document is a module for aviation maintenance technicians, focusing on aircraft propulsion, specifically turbine engines and associated systems. It explains the construction and operation of different engine types and electronic control systems. The document is part of a certification series and provides information to prepare for EASA certification.
Full Transcript
www.amequestionpaper.in > Visit our website to download all latest EASA / DGCA CAR 66 Module examination Question papers and study material www.amequestionpaper.in > Visit our website to download all latest EASA / DGCA CAR 66 Module examination Question papers and study material ...
www.amequestionpaper.in > Visit our website to download all latest EASA / DGCA CAR 66 Module examination Question papers and study material www.amequestionpaper.in > Visit our website to download all latest EASA / DGCA CAR 66 Module examination Question papers and study material MODULE 14 FOR 82 CERTIFICATION PROPULSION Aviation Maintenance Technician Certification Series 72413 U.S. Hwy 40 Tabernash, CO 80478-0270 USA www.actechbooks.com +1 970 726-5111 AVIATION MAINTENANCE TECHNICIAN CERTIFICATION SERIES Contributors Omar Kahn Roger Petersen Design/Layout Michael Amrine Copyright© 2016- Aircraft Technical Book Company. All Rights Reserved. No part of this publication may be reproduced, stored in a retrieva l system, transmitted in any form or by any means, electron ic, mechanical, photocopying, recording or otherwise, without the prior written permission of the publisher. To order books orfor Customer Service, p lease call +1 970 726-5111. www.actechbooks. com Printed in the United States of America ISBN 978-1941144190 For comments or suggestions about this book, please call or write to: 1.970. 726.5111 I [email protected] 9 781941 144190 WELCOME The publishers of this Aviation Maintenance Technician Certification Series welcome you to the world of aviation maintenance. As you move towards EASA certification, you are required to gain suitable knowledge and experience in your chosen area. Qyalification on basic subjects for each aircraft maintenance license category or subcategory is accomplished in accordance with the following matrix. Where applicable, subjects are indicated by an "X" in the column below the license heading. For other educational tools created to prepare candidates for licensure, contact Aircraft Technical Book Company. We wish you good luck and success in your studies and in your aviation career! REVISION LOG VERSION EFFECTIVE DATE DESCRIPTION 0 FCHANGE -- ---------~ 001 2016 02 Module Creation and Release 002 2017 11 Format Updates -- - - - --- --- --------- -- ---- - -- - - - - -- -- - -- - -- - - - - - - - I - Module 14 - Propulsion iii FORWARD PART- 66 and the Acceptable Means of Compliance (AM C) and Guidance Material (GM) of the European Aviation Safety Agency (EASA) Regulation (EC) No. 1321/2014, Appendix 1 to the Implementing Rules establishes the Basic Knowledge Requirements for those seeking an aircraft maintenance license. The information in this Module of the Aviation Maintenance Technical Certification Series published by the Aircraft Technical Book Company meets or exceeds the breadth and depth of knowledge subject matter referenced in Appendix 1 of the Implementing Rules. However, the order of the material presented is at the discretion of the editor in an effort to convey the required knowledge in the most sequential and comprehensible manner. Knowledge levels required for Category A1, B1, B2, and B3 aircraft maintenance licenses remain unchanged from those listed in Appendix 1 Basic Knowledge Requirements. Tables from Appendix 1 Basic Knowledge Requirements are reproduced at the beginning of each module in the series and again at the beginning of each Sub-Module. How numbers are written in this book: This book uses the International Civil Aviation Organization (ICAO) standard of writing numbers. This method displays large numbers by adding a space between each group of3 digits. This is opposed to the American method which uses commas and the European method which uses periods. For example, the number one million is expressed as so: ICAO Standard 1 000 000 European Standard 1.000.000 American Standard 1,000,000 SI Units: The International System of Units (SI) developed and maintained by the General Conference of Weights and Measures (CGPM) shall be used as the standard system of units of measurement for all aspects of international civil aviation air and ground operations. Prefixes: The prefixes and symbols listed in the table below shall be used to form names and symbols of the decimal multiples and submultiples oflnternational System ofUnits (SI) units. MULTIPLICATION FACTOR PR EFIX SYMBOL I 1 000000000000000000 = 1018 ex a E 1 000 000 000 000 000 = 1015 pet a p 1 000 000 000 000 = 1012 tcra T 1000 0 00 000 = 109 g ig a G 1 000 000 = 10'' mega M 1 000 = 10 3 kilo k 100 = 10 2 hccto h 10 = 10 1 dec a da 0.1 =10-1 dcci d 0.01 = 10-2 ccnti c 0.001 = 10-3 m illi m 001 = 10-6 0.000 mi cro fl 001 = 10-9 0.000 000 nano n 001 = 10-12 0.000 000 000 pi co p 001 = 10-15 0.000 000 000 000 fc mto f 0~000000000000 0 0001 = 10-18 at to a International System of Un its (SI) Prefixes iv ,- --- - EASA LICENSE CATEGORY CHART Module Number and Title ~ A1 Airplane Turbine 81.1 Airplane Turbine 81.2 Airplane Piston 81.3 Helicopter Turbine Mathematics X X X X 2 3 f Physics Electrical Fundamentals X X X X X X X X ! 4 Electronic Fundamentals X X X 5 _Digital Techniques I Electronic Instrument Systems X X X 6 Materials and Hardware X X X 7A Maintenance Practices X X 8 Basic Aerodynamics X X 9A Human Factors X X 10 Aviation Legislation X X 11A Turbine Aeroplane Aerodynamics, Structures and Systems 11 B Piston Aeroplane Aerodynamics, Structures and Systems 12 Helicopter Aerodynamics, Structures and Systems 13 Aircraft Aerodynamics, Structures and Systems 14 Propulsion X 15 Gas Turbine Engine X X 16 Piston Eng ine X 17A l Propeller X X MODULE 14 SYLLABUS AS OUTLINED IN PART-66, APPENDIX 1. LEVELS CERTIFICATION CATEGORY -+ 82 Sub-Module 01- Turbine Engines (a) Constructional arrangement and operation of turbojet, turbofan, turboshaft and 1 turbopropeller engines; (b) Electronic engine control and fuel metering systems (FADEC). 2 Sub-Module 02- Engine Indicating Systems Exhaust gas temperature/interstage turbine temperature systems; 2 Engine speed; Engine thrust indication: engine pressure ratio, engine turbine discharge pressure or jet pipe pressure systems; Oil pressure and temperature: Fuel pressure, temperature and flow; Manifold pressure; Engine torque; Propeller speed. ~ Module 14 - Propulsion A IRCRAFT v f~C H NICI\L BOOK CO MP ANY LEVELS CERTIFICATION CATEGORY ~ 82 Sub-Module 03 - Starting and Ignition Systems Operation of engine start systems and components; 2 Ignition systems and components; Maintenance safety requirements. vi Module 14 - Propulsion CONTENTS PROPULSION Fuel Filters................................................................ 1..23 Welcotne........................................................................ iii Fuel Spray Nozzles And Fuel Manifolds................ 1.24 Revision Log.................................................................. iii Simplex Fuel Nozzle............................................ 1.25 Forward.......................................................................... iv Duplex Fuel Nozzle............................................ 1.25 Contents........................................................................ vii Airblast Nozzles.................................................. 1.25 Flow Divider........................................................ 1.26 SUB-MODULE 01 Fuel Pressurizing And Dump Valves...................... 1.26 Combustion Drain Valves........................................ 1.26 Knowledge Requirements............................................ 1.1 Fuel Qwntity Indicating Units................................ 1.27 Energy............................................................................ 1.2 Q.yestions...................................................................... 1.29 Potential Energy...................................................... 1.2 Answers........................................................................ 1.30 Kinetic Energy.......................................................... 1.2 Newton's Laws Of Motion............................................ 1.3 SUB-MODULE 02 First Law.................................................................. 1.3 Second Law.............................................................. 1.3 Knowledge Requirements............................................ 2.1 "Ihird Law.................................................................. 1.3 Engine Indicating Systems............................................ 2.2 Bernoulli's Principle...................................................... 1.4 Engine Parameters.................................................... 2.2 Boyle's & Charles' Law.................................................. 1.4 Purpose................................................................ 2.2 Force, Work, Power And Torque............................ 1.5 Position.................................................................... 2.3 Force.................................................................... 1.5 Description.............................................................. 2.3 Work.................................................................... 1.5 Operation.................................................................. 2.4 Power.................................................................... 1.6 Operating Parameters.......................................... 2.4 Torque.................................................................. 1.6 Engine 1hrust Indication................................ 2.4 Motion.......................................................................... 1.7 Comparison of EPR and N1.......................... 2.4 Speed And Velocity.................................................. 1.7 EGT (Exhaust Gas Temperature)................ 2.4 Acceleration.............................................................. 1.8 N2.................................................................... 2.5 General Requirements.................................................. 1.8 Flowmeter (FF: Fuel Flow)............................ 2.5 Power And Weight.................................................. 1.9 Monitoring Parameters............................................ 2.5 Fuel Econotny.......................................................... 1.10 Lubrication System.............................................. 2.5 Durability And Reliability...................................... 1.10 Oil Q1antity.................................................. 2.5 Operating Flexibility................................................ 1.10 Oil Pressure.................................................... 2.5 Compactness............................................................ 1.10 Oil Temperature............................................ 2.5 Types And Construction.............................................. 1.11 Low Oil Pressure Alert.................................. 2.6 Turbine Engine Types.............................................. 1.11 Filter Pre-Clogging Alert............................ 2.6 Bypass Ratio.............................................................. 1.11 Engine Vibration Indication................................ 2.6 Turbine Engine Fuel Systems........................................ 1.14 Nacelle Temperature............................................ 2.6 General Requirements.............................................. 1..14 Maintenance............................................................ 2.6 Turbine Fuel Controls.............................................. 1.14 Engine Parameters- Detailed Operation.................... 2.7 Hydromechanical Fuel Controls........................ 1.15 Operation And Controls.......................................... 2.7 Hydromechanical/Electronic Fuel Control........ 1.15 Pressure Data.................................................. 2.7 FADEC Fuel Control Systems................................ 1.17 Temperature Data.......................................... 2.7 FADEC For An Auxiliary Power Unit.............. 1.17 Pressure Data...................................................... 2.7 FADEC Fuel Control Propulsion Engine.......... 1.19 EPR (Engine Pressure Ratio)........................ 2.7 Fuel System Operation............................................ 1.21 Oil Pressure.................................................... 2. 7 Engine Fuel System Components................................ 1.22 Low Oil Pressure Alert.................................. 2.7 Main Fuel Pumps (Engine Driven)........................ 1.22 Fuel Filter Pre-Clogging Alert...................... 2.8 Fuel Heater.............................................................. 1.22 Fuel Pressure.................................................. 2.8 Module 14 - Propulsion vii CONTENTS Temperature Data.................................................... 2.8 Removal, Maintenance And Installation Oflgnition EGT (Exhaust Gas Temperature)...................... 2.8 System Components................................................ 3.15 Oil Temperature.................................................. 2.9 Ignition System Leads.............................................. 3.15 Fuel Temperature................................................ 2.9 Igniter Plugs.............................................................. 3.15 Nacelle Temperature............................................ 2.10 Q.yestions...................................................................... 3.17 Mechanical Movement Data.................................... 2.10 Answers........................................................................ 3.18 N1........................................................................ 2.10 N2........................................................................ 2.10 Acronym Index.............................................................. A. 1 Fuel Flow Rate (FF Or Fuel Flow).................... 2.10 Index.............................................................................. I.l Engine Vibrations................................................ 2.10 Engine Torque...................................................... 2.12 Manifold Pressure................................................ 2.13 Propeller Rotational Speeds................................ 2.14 Interfaces.................................................................. 2.14 Engine Interfaces................................................ 2.14 Aircraft Interfaces................................................ 2.14 Monitoring And Alert............................................ 2.14 Analog Dial Indicators (Gauges)........................ 2.14 Electronic Indicators............................................ 2.15 Maintenance.................................................................. 2.16 Thermocouple Temperature Sensor.......................... 2.16 EPR Thrust Indication............................................ 2.16 Vibration Sensor...................................................... 2.16 N1, N2 Speed Sensors.............................................. 2.16 Q.yestions...................................................................... 2.17 Answers........................................................................ 2.18 SUB-MODULE 03 STARTING AND IGNITION SYSTEMS Knowledge Requirements............................................ 3.1 Starting And Ignition Systems.................................... 3.2 Ignition System Maintenance Safety...................... 3.2 Gas Turbine Engine Starters.................................... 3.2 Electric Starting Systems And Starter Generator Starting Systems.................................................. 3.3 Troubleshooting a Starter Generator Starting System.............................................................. 3.5 Air Turbine Starters............................................ 3.5 Air Turbine Troubleshooting Guide.............. 3.10 Turbine Ignition Systems.......................................... 3.10 Capacitor Discharge Exciter Unit...................... 3.12 Igniter Plugs.............................................................. 3.13 Turbine Ignition System Inspection And Maintenance 3.14 Inspection.................................................................. 3.14 Check System Operation.......................................... 3.15 Repair........................................................................ 3.15 viii Module 14 - Propulsion (f) w z az w w z iD 0:: ::J f- SUB-MODULE PART-66 SYLLABUS LEVELS CERTIFICATION CATEGORY ~ 82 Sub-Module 01 TURBINE ENGINES Knowledge Requirements 14.1 - Turbine Engines (a) Constructional arrangement and operation of turbojet, turbofan, turboshaft and turbopropeller engines; 1 (b) Electronic engine control and fuel metering systems (FADEC). 2 Levell Level2 A familiarization with the principal elements of the subject. A general knowledge of the theoretical and practical aspects of the subject and an abi lity to apply that knowledge. Objectives: (a) The applicant should be familiar with the basic elements of the Objectives: subject. (a) 'Ihe applicant should be able to understand the theoretical (b) The applicant should be able to give a simple description of the fundamentals of the subject. whole subject, using common words and examples. (b) The applicant shou ld be able to give a general description of the (c) The applicant should be able to use typical terms. subject using, as appropriate, typical examples. (c) 'The applicant should be able to use mathematical formula in conjunction with physical laws describing the subject. (d) The applicant should be able to read and understand sketches, drawings and schematics describing the subject. (e) 'TI1e applicant should be able to apply his knowledge in a practical manner using detailed procedures. www.amequestionpaper.in > Visit our website to download all latest EASA / DGCA CAR 66 Module examination Question papers and study material Module 14 - Propulsion 1.1 ENERGY Energy is typically defined as something that gives us and each BTU is capable of 778 ft-lbs of work. So if the capacity to perform work. As individuals, saying that we multiply 778 by 18 900, we find that one pound of we feel full of energy is probably indicating that we can aviation gas is capable of 14 704 200 ft-lbs of work. perform a lot of work. Energy can be classified as one of two types: either potential or kinetic. Imagine the potential energy in the completely serviced fuel tanks of an airplane. POTENTIAL ENERGY Potential energy is defined as being energy at rest, or KINETIC ENERGY energy that is stored. Potential energy may be classified Kinetic energy is defined as being energy in motion. An into three groups: (1) that due to position, (2) that due to airplane rolling down the runway or a rotating flywheel distortion of an elastic body, and (3) that which produces on an engine are both examples of kinetic energy. work through chemical action. Kinetic energy has the same units as potential energy, namely foot pounds or inch pounds. To calculate the Water in an elevated reservoir, and an airplane raised kinetic energy for something in motion, the following off the ground sitting on jacks are examples of the first formula is used: group; a stretched bungee cord on a Piper Tri-Pacer or compressed spring are examples of the second group; Kinetic Energy = 0 Mass x Velocity 2 and energy in aviation gasoline, food, and storage batteries are examples of the third group. To use the formula, we will show the mass as weight + gravity and the velocity of the object will be in feet per To calculate the potential energy of an object due to its second. This is necessary to end up with units in foot position, as in height, the following formula is used: pounds. A calculation based on this formula will produce an Example: A Boeing 777 weighing 600 000 lbs is answer that has units of foot pounds (ft-lbs) or inch moving down the runway on its takeoff roll with pounds (in-lbs), which are the same units that apply a velocity of 200 fps. How many foot pounds to work. Work, which is covered later in this chapter, of kinetic energy does the airplane possess? is described as a force being applied over a measured (J;igure 1-1) distance, with the force being pounds and the distance being feet or inches. It can be seen that potential energy Kinetic E1wgy 0 Mmr x Velority 2 and work have a lot in common. Kinetic Ene1gy 0 X (600 000 + 32.2) X 200' KE 372 670 807ft ib Example: A Boeing 747 weighing 450 000 pounds needs to be raised 4 feet in the air so maintenance can be done on the landing gear. How much potential energy docs the airplane possess because of this raised position? Potml ial E1mgy Weight x Height PE 450 000 fb X 4.fi PE 1 800 OOO.fi-lbr As mentioned previously, aviation gasoline possesses potential energy because of its chemical nature. Gasoline has the potential to release heat energy, based on its British thermal unit (BTU) content. One pound of aviation gas contains 18 900 BTU of heat energy, Figure 1-1. Kinetic energy (Boeing 777 taking off). 1.2 Module 14 - Propulsion NEWTON'S LAWS OF MOTION (/) w The physic laws originated by Sir Isaac Newton are Example: A turbojet engine is moving 150 lbs of z az particularly applicable to the operation of turbine air per second through the engine. The air enters w engines. going 100 fps and leaves going 1 200 fps. How w z much thrust, in pounds, is the engine creating? co a: :::> FIRST LAW f- W(Vf- Vi) Objects at rest tend to Temain at Test and objects in motion F Gt tend to remain in motion at the same speed and in the same 150 (1 200 - 100) diTection, unless acted on by an externalfoTce. F 32.2 (1) When a magician snatches a tablecloth from a table F 5 124 /b ofthrust and leaves a full setting of dishes undisturbed, he is not displaying a mystic art; he is demonstrating the principle THIRD LAW of inertia. Inertia is responsible for the discomfort felt FoT eve1y action thae is an equal and opposite Teaction. when an airplane is brought to a sudden halt in the parking area and the passengers are thrown forward in Newton's third law of motion is often called the law of their seats. Inertia is a property of matter. 1his property action and reaction. This means that if a force is applied of matter is described by Newton's first law of motion. to an object, the object will supply a resistive force exactly equal to and in the opposite direction of the force SECOND LAW applied. It is easy to see how this might apply to objects When afo1'Ce acts upon a body, the momentum ofthat body is at rest. For example, as a man stands on the floor, the changed. 7he mte of change of momentum is proportional to floor exerts a force against his feet exactly equal to his the appliedfoTce. weight. But this law is also applicable when a force is applied to an object in motion. Bodies in motion have the property called momentum. A body that has great momentum has a strong tendency Forces always occur in pairs. The "acting force" means to remain in motion and is therefore hard to stop. For the force one body exerts on a second body, and reacting example, a train moving at even low velocity is difficult force means the force the second body exerts on the first. to stop because of its large mass. Newton's second law applies to this property. When an aircraft propeller pushes a stream of air backward with a force of 500 lbs, the air pushes the Based on Newton's second law, the formula for blades forward with a force of 500 lbs. This forward force calculating thrust is derived, which states that force causes the aircraft to move forward. A turbofan engine equals mass times acceleration: exerts a force on the air entering the inlet duct, causing it to accelerate out the fan duct and the tailpipe. The air (F=MA) accelerating to the rear is the action, and the force inside the engine that makes it happen is the reaction, also Mass equals weight divided by gravity, and acceleration called thrust. equals velocity final minus velocity initial divided by time. Putting all these concepts together, the formula for thrust is: Weight (Velocity Final - Velocity Initial) Force Gm·v ity (Time) W(Vf- Vi) F Gt Module 14 - Propulsion 1.3 BERNOULLI 1S PRINCIPLE Bernoulli's principle explains the action of a liquid Bernoulli's principle is important in understanding how flowing through the varying cross-sectional areas of some of the systems used in aviation work, including tubes. In Figure 1-2 a tube is shown in which the how the wing of an airplane generates lift or why the cross-sectional area gradually decreases to a minimum inlet duct of a turbine engine on a subsonic airplane is diameter in its center section. A tube constructed in this diverging in shape. Key to Bernoulli's principle is that manner is called a "venturi". Where the cross-sectional the total pressure of the airflow remains the same while area is decreasing, the passageway is referred to as a static pressure varies due to negotiation of the curvature converging duct. As the passageway starts to spread out, of a venturi or wing. As the static pressure of the fluid it is referred to as a diverging duct. decreases to move over the curved surface, dynamic pressure increases, expressed as an equation: As a fluid flows through the venturi tube, at A, B, and C are positioned to register the velocity and the static Total Pressure = Static Pressure + Dynamic Presmre pressure of the liquid. The venturi in Figure 1-2 is used to illustrate Bernoulli's principle, which states: The static pressure ofafluid (liquid or gas) decreases at points where the velocity ofthe fluid increases, provided no ene1-gy is added to Velocity Pressure Velocity Pressure nor taken away fi"om the fluid. The velocity of the air is kinetic energy and the static pressure of the air is potential energy. In the wide section of the venturi (points A and C of Figure 1-2), the liquid moves at low velocity, producing a high static pressure, as indicated by the pressure gauge. As the tube narrows in the center, it must contain the same volume of fluid as the two end areas. In this narrow section, the liquid Velocity Pressure moves at a higher velocity, producing a lower pressure Figure 1-2. Bernoulli's principle and a venturi. than that at points A and C, as indicated by the velocity gauge reading high and the pressure gauge reading low. BOVLE 1S & CHARLES LAW Boyle's Law states that when the temperature of a gas Force Pushing Down on Gas is kept constant and the pressure inscreased, its volume is decreased proportionately. In reverse; when a gas is at a constant temperature and presure decreases, volume increases. (Figure 1-3) By itself Boyle's Law is oflittle use because in practice air is not compressed at a constant temperature. Although if we use Boyle's Law in combination with Charles' Law, it becomes more useful. Charles' Law states that if air is heated at a constant pressure, the change in volume will vary with the change in temperature. Therefore, the volume of a mass of gas at constant pressure is Pressure Temperature proportional to the temperature of the gas (ail} So, the Increasing Held Constant product of the pressure and volume of the air through Figure 1-3. Boyle's Law example. 1.4 Module 14 - Propulsion each stage within a turbine engine is proportional to the heat added in the combustion cycle temperature of the air at the stage. ff3 z During compression, as work is done to increase az lU pressure and decrease volume, there is a corresponding lU z rise in temperature. During combustion, the addition of LU Cii a: ;::) a: J fuel to burn with the air increases the pressure and there en en 1- LU expanding gas is a corresponding increase in volume. During exhaust, a: through turbine c.. there is a decrease in the pressure and temperature of the and exhaust gas with an additional increase in volume. (Figure 1-4} I ambient air entering intake FORCE, WORK, POWER AND TORQUE pressure added in compressor \ FORCE VOLUME Before the concept of work, power, or torque can be Figure 1-4. Pressure/volume relationship. discussed, we must understand what force means. According to the dictionary, force is the intensity of an is displaced some distance against a resistive force. To impetus, or the intensity of an input. For example, if calculate work, the following formula is used: we apply a force to an object, the tendency will be for the object to move. Another way to look at it is that for Work= Force (F) x distance (d) work, power, or torque to exist, there has to be a force that initiates the process. In the English system, the force will be identified in pounds and the distance either in feet or inches, so The unit for force in the English system of measurement the units will be foot-pounds or inch-pounds. Notice is pounds, and in the metric system it is newtons. One these are the same units that were used for potential pound of force is equal to 4.448 newtons. When we and kinetic energy. In the metric system, the force is calculate the thrust of a turbine engine, we use the identified in newtons (N) and the distance in meters, formula "Force = Mass x Acceleration," and the thrust with the resultant units being joules. One pound of force of the engine is expressed in pounds. The GE90-115 is equal to 4.448 Nand one meter is equal to 3.28 feet. turbofan engine (powerplant for the Boeing 777-300), One joule is equal to 1.36 ft-lb. for example, has 115 000 pounds of thrust. Example: How much work is accomplished by \NORK jacking a 150 000-lb Airbus A-320 airplane a The study of machines, both simple and complex, is in vertical height of 3 ft? (Figure 1-5) one sense a study of the energy of mechanical work. This is true because all machines transfer input energy, or the work done on the machine, to output energy, or the work done by the machine. Work, in the mechanical sense of the term, is done when a resistance is overcome by a force acting through a measurable distance. Two factors are involved: (1) force and (2) movement through a distance. As an example, suppose a small aircraft is stuck in the snow. Two men push against it for a period of time, but the aircraft does not move. According to the technical definition, no work was done in pushing against the aircraft. By definition, work is accomplished only when an object Figure 1-5. Airbus A-320 being jacked. Module 14 - Propulsion 1.5 Work Force x distance Many years ago there was a desire to compare the power 5 000 lbs x 4ft of the newly evolving steam engine to that of horses. 600 000 ft-lbs People wanted to know how many horses the steam engine was equivalent to. Because of this, the value we Example: How much work is accomplished currently know as one horsepower (hp) was developed, when a tow tractor is hooked up to a tow bar and and it is equal to 550 foot pounds per second (ft-lb/s). a Boeing 737-800 airplane weighing 130 000 It was found that the average horse could lift a weight lbs is pushed 80 ft into the hangar? The force on of 550 lb, one foot off the ground, in one second. the tow bar is 5 000 lbs. The values we use today, in order to convert power to horsepower, are as follows: Work Force x distance 5 000 X 80ft 1 hp 550Jt-lbls 400 000 ft-lbs 1 hp 33 000ji-lhlmin. 1 hp 375 mile pounds per hour (mi lbl/11) In this last example, notice the force does not equal the 1 hp 746 watts (t'/ectricity con·version) weight of the airplane. This is because the airplane is being moved horizontally and not lifted vertically. In To convert power to horsepower, divide the power by the virtually all cases, it takes less work to move something appropriate conversion based on the units being used. horizontally than it does to lift it vertically. Most people can push their car a short distance if it runs out of gas, Example: What power would be needed, and but they cannot get under it and lift it off the ground. also horsepower, to raise the GE-90 turbofan engine into position to install it on a Boeing POWER 777-300 airplane? 1he engine weighs 19 000 lb, The concept of power involves the previously discussed and it must be lifted four ft in two minutes. topic of work, which was a force being applied over a measured distance, but adds one more consideration; Power Force x distance + time time. In other words, how long does it take to accomplish 19 000 lbs x 4ft : 2 minutes the work. If someone asked the average person if he 38 000Jt-lbs I min or she could lift one million pounds five feet off the Horsepower (Hp) 38 OOOft-lbs I min+ ground, the answer most assuredly would be no. This 33 OOO.ft-1/Js I min Hp = 1.15 person would probably assume that he or she is to lift it all at once. What if he or she is given 365 days to lift it, The hoist that will be used to raise this engine into and could lift small amounts of weight at a time? position will need to be powered by an electric motor because the average person will not be able to generate The work involved would be the same, regardless of how 1.15 hp in their arms for the necessary two minutes. long it took to lift the weight, but the power required is different. If the weight is to be lifted in a shorter period TORQUE of time, it will take more power. Torque is a very interesting concept and occurrence, and it is definitely something that needs to be discussed The formula for power is as follows: in conjunction with work and power. Whereas work is described as a force acting through a distance, torque Power = Force x distance+ time is described as a force acting along a distance. Torque is something that creates twisting and tries to make The units for power will be foot pounds per minute, foot something rotate. pounds per second, inch pounds per minute or second, and possibly mile pounds per hour. The units depend on If we push on an object with a force of ten lbs and it how distance and time are measured. moves ten inches in a straight line, we have done 100 in lbs of work. By comparison, if we have a wrench ten inches long that is on a bolt, and we push down on it 1.6 Module 14 - Propulsion with a force of ten lbs, a torque of 100 lb in is applied to are not. The units of work were inch pounds and the the bolt. If the bolt was already tight and did not move units of torque were pound inches, and that is what (/) w as we pushed down on the wrench, the torque of 100 lb differentiates the two. z az in would still exist. The formula for torque is: w Torque is very important when thinking about how w z engines work. Gas turbine engines create torque in iii a: ::J advance of being able to create work or power. The 1- Even though the formula looks the same as the one for turbine blades at the back of the engine extract energy calculating work, recognize that the distance value in from the high velocity exhaust gases. The energy this formula is not the linear distance an object moves, extracted becomes a force in pounds pushing on the but rather the distance along which the force is applied. turbine blades, which happen to be a certain number of inches from the center of the shaft they are trying Notice that with torque nothing had to move, because to make rotate. The number of inches from the turbine the force is being applied along a distance and not blades to the center of the shaft would be like the length through a distance. Notice also that although the of the wrench discussed earlier. units of work and torque appear to be the same, they MOTION The study of the relationship between the motion of Velocity is that quantity in physics which denotes both the bodies or objects and the forces acting on them is often speed of an object and the direction in which the object called the study of"force and motion." In a more specific moves. Velocity can be defined as the rate of motion in a sense, the relationship between velocity, acceleration, particular direction. Velocity is also described as being a and distance is known as kinematics. vector quantity, a vector being a line of specific length, having an arrow on one end or the other. The length Motion may be defined as a continuing change of of the line indicates the number value and the arrow position or place, or as the process in which a body indicates the direction in which that number is acting. undergoes displacement. When an object is at different points in space at different times, that object is said to be Two velocity vectors, such as one representing the in motion, and if the distance the object moves remains velocity of an airplane and one representing the velocity the same for a given period of time, the motion may be of the wind, can be added together in what is called vector described as uniform. Thus, an object in uniform motion analysis. Figure 1-6 demonstrates this, with vectors "N' always has a constant speed. and "B" representing the velocity of the airplane and the wind, and vector "C" being the resultant. With no SPEED AND VELOCITY wind, the speed and direction of the airplane would be In everyday conversation, speed and velocity are often that shown by vector ''A." When accounting for the wind used as if they mean the same thing. In physics they direction and speed, the airplane ends up flying at the have definite and distinct meanings. Speed refers to how speed and direction shown by vector "C." fast an object is moving, or how far the object will travel in a specific time. The speed of an object tells nothing Imagine that an airplane is flying in a circular pattern about the direction an object is moving. For example, if at a constant speed. Because of the circular pattern, the the information is supplied that an airplane leaves New airplane is constantly changing direction, which means York City and travels eight hours at a speed of 150 mph, the airplane is constantly changing velocity. TI1e reason this information tells nothing about the direction in for this is the fact that velocity includes direction. which the airplane is moving. At the end of eight hours, it might be in Kansas City, or if it traveled in a circular To calculate the speed of an object, the distance it route, it could be back in New York City. travels is divided by the elapsed time. If the distance is measured in miles and the time in hours, the units of speed will be miles per hour (mph). If the distance is Module 14 - Propulsion 1.7 Vector B = Wind ACCELERATION Acceleration is defined as the rate of change of velocity. If the velocity of an object is increased from 20 mph to 30 mph, the object has been accelerated. If the increase in velocity is 10 mph in five seconds, the rate of change in velocity is 10 mph in five seconds, or two mph per second. If this were multiplied by 1.467, it could also be expressed as an acceleration of 2.93 feet per second per second (fps/s). By comparison, the acceleration due to gravity is 32.2 fps/s. To calculate acceleration, the following formula is used: Acceleration (A) = _Vl_ e~_ oc_it.L y _F_il_7n_I__,_(~ Vf'-'-}_-_T-_IL_ Io_c_ ity'-l_1_zit_in_I_,_(_V~ i) Time (t) Example: An Air Force F-15 fighter is cruising at 400 mph. TI1c pilot advances the throttles to full afterburner and accelerates to 1 200 mph in 20 seconds. What is the average acceleration in mph/s and fps/s? A=VJ- Vi t A= 1200 - 400 20 A= 40 mp'% or by multiplying by 1.467, 58. 7lP·'!, Figure 1-6. Vector analysis for airplane velocity and wind velocity. In the example above, acceleration was found to be 58.7 fps/s. Since 32.2 fps/s is equal to the acceleration due measured in feet and the time in seconds, the units of to gravity, divide the F -15's acceleration by 32.2 to find speed will be feet per second (fps). To convert mph to out how many G forces the pilot is experiencing. In this fps, multiply by 1.467. Velocity is calculated the same case, it would be 1.82 Gs. way, the only difference being it must be recalculated every time the direction changes. GENERAL REQUIREMENTS Aircraft require thrust to produce enough speed for the heat energy is released at a point in the cycle where the wings to provide lift or enough thrust to overcome the working pressure is high relative to atmospheric pressure. weight of the aircraft for vertical take off. For an aircraft to remain in level flight, thrust must be provided that The propulsive force is obtained by the displacement is equal to and in the opposite direction of the aircraft of a working fluid (again, atmospheric air). 1his air is drag. This thrust, or propulsive force, is provided by a not necessarily the same air used within the engine. By suitable type of aircraft heat engine. All heat engines displacing air in a direction opposite to that in which have in common the ability to convert heat energy the aircraft is propelled, thrust can be developed. This into mechanical energy by the flow of some fluid mass is an application of Newton's third law of motion. It (generally air) through the engine. In all cases, the states that for every action there is an equal and opposite 1.8 Module 14 - Propulsion reaction. So, as air is being displaced to the rear of the so many different types of turbine engines, the term aircraft the aircraft is moved forward by this principle. used to describe most turbine engines is "gas turbine (f) w One misinterpretation of this principle is air is pushing engine." All four of the previously mentioned engines z az against the air behind the aircraft making it move belong to the gas turbine family. w forward. This is not true. w z All aircraft engines must meet certain general requirements iii a: ::J Rockets in space have no air to push against, yet, of efficiency, economy, and reliability. Besides being 1- they can produce thrust by using Newton's third law. economical in fuel consumption, an aircraft engine Atmospheric air is the principal fluid used for propulsion must be economical in the cost of original procurement in every type of aircraft powerplant except the rocket, and the cost of maintenance; and it must meet exacting in which the total combustion gases are accelerated requirements of efficiency and low weight to horsepower and displaced. The rocket must provide all the fuel ratio. It must be capable of sustained high power output and oxygen for combustion and does not depend on with no sacrifice in reliability; it must also have the atmospheric air. A rocket carries its own oxidizer rather durability to operate for long periods of time between than using ambient air for combustion. It discharges the overhauls. It needs to be as compact as possible, yet have gaseous byproducts of combustion through the exhaust easy accessibility for maintenance. It is required to be as nozzle at an extremely high velocity (action) and it is vibration free as possible and be able to cover a wide range propelled in the other direction (reaction). of power output at various speeds and altitudes. The propellers of aircraft powered by reciprocating These requirements dictate engine fuel delivery systems or turboprop engines accelerate a large mass of air at provide metered fuel at the correct proportion of fuel/air a relatively lower velocity by turning a propeller. The ingested by the engine regardless of the attitude, altitude, same amount of thrust can be generated by accelerating or type of weather in which the engine is operated. a small mass of air to a very high velocity. The working The engine needs a type of oil system that delivers oil fluid (air) used for the propulsive force is a different under the proper pressure to lubricate and cool all of the quantity of air than that used within the engine to operating parts of the engine when it is running. Also, produce the mechanical energy to turn the propeller. it must have a system of damping units to damp out the vibrations of the engine when it is operating. Turbojets, ramjets, and pulse jets are examples of engines that accelerate a smaller quantity of air through a large POWER AND WEIGHT velocity change. They use the same working fluid for The useful output of all aircraft powerplants is thrust, propulsive force that is used within the engine. One the force which propels the aircraft. A reciprocating problem with these types of engines is the noise made by engine is rated in brake horsepower (bhp), the gas the high velocity air exiting the engine. The term turbojet turbine engine is rated in thrust horsepower (thp): was used to describe any gas turbine engines, but with thrwt x airrmft speed (mph) the differences in gas turbines used in aircraft, this term 1hp = 375 mile-pounds per hour is used to describe a type of gas turbine that passes all the gases through the core of the engine directly. The value of 375 mile-pounds per hour is derived from the basic horsepower formula as follows: Turbojets, ramjets, and pulse jets have very little to no use in modern aircraft due to noise and fuel consumption. 1 hp 33 000Jt-lbs per minute Small general aviation aircraft use mostly horizontally opposed reciprocating piston engines. While some 33 000 X 60 1 980 000 Jt-lbs per hour aircraft still use radial reciprocating piston engines, 1980000 their use is very limited. Many aircraft use a form of = 3 75 mile-pomzds pa bam· 5 280Jt in a mile the gas turbine engine to produce power for thrust. These engines are normally the turboprop, turboshaft, One horsepower equals 33 000 ft lb per minute or 375 turbofan, and a few turbojet engines. "Turbojet" is the mile pounds per hour. Under static conditions, thrust former term for any turbine engine. Now that there are is figured as equivalent to approximately 2.6 pounds Module 14 - Propulsion 1.9 per hour. If a gas turbine is producing 4 000 pounds of DURABILITY AND RELIABILITY thrust and the aircraft in which the engine is installed is Durability and reliability are usually considered identical traveling at 500 mph, the thp is: factors since it is difficult to mention one without including the other. An aircraft engine is reliable when 4 000 X 500 = 5 333.33 thp it can perform at the specified ratings in widely varying 375 flight attitudes and in extreme weather conditions. It is necessary to calculate the horsepower for each speed Standards of powerplant reliability are agreed upon by of an aircraft, since the horsepower varies with speed. the engine manufacturer, and the airframe manufacturer. Therefore, it is not practical to try to rate or compare the The engine manufacturer ensures the reliability of the output of a turbine engine on a horsepower basis. TI1e product by design, research, and testing. Close control of aircraft engine operates at a relatively high percentage manufacturing and assembly procedures are maintained, of its maximum power output throughout its service and each engine is tested before it leaves the factory. life. The aircraft engine is at full power output whenever a take off is made. It may hold this power for a period Durability is the amount of engine life obtained while of time up to the limits set by the manufacturer. The maintaining the desired reliability. The fact that an engine is seldom held at a maximum power for more engine has successfully completed its type or proof test than two minutes, and usually not that long. Within a indicates that it can be operated in a normal manner few seconds after liftoff, the power is reduced to a power over a long period before requiring overhaul. However, that is used for climbing and that can be maintained for no definite time interval between overhauls is specified longer periods of time. After the aircraft has climbed to or implied in the engine rating. The time between cruising altitude, the power of the engine(s) is further overhauls (TBO) varies with the operating conditions, reduced to a cruise power which can be maintained for such as engine temperatures, amount of time the engine the duration of the flight. is operated at high-power settings, and the maintenance received. Recommended TBOs are specified by the FUEL ECONOMY engine manufacturer. The basic parameter for describing the fuel economy of aircraft engines is usually specific fuel consumption. Reliability and durability are built into the engine by Specific fuel consumption for gas turbines is the fuel the manufacturer, but the continued reliability of the flow measured in (lbs/hr) divided by thrust (lbs). This engine is determined by the maintenance, overhaul, and is called thrust-specific fuel consumption. Equivalent operating personnel. Careful maintenance and overhaul specific fuel consumption is used for the turboprop methods, thorough periodical and preflight inspections, engine and is the fuel flow in pounds per hour divided by and strict observance of the operating limits established a turboprop's equivalent shaft horsepower. Comparisons by the engine manufacturer make engine failure a can be made between the various engines on a specific rare occurrence. fuel consumption basis. OPERATING FLEXIBILITY At low speed, reciprocating and turboprop engines Operating flexibility is the ability of an engine to have better economy than the pure turbojet or turbofan run smoothly and give desired performance at all engines. However, at high speed, because of losses in speeds from idling to full power output. The aircraft propeller efficiency, a reciprocating or turboprop engine's engine must also function efficiently through all the efficiency becomes limited above 400 mph less than that variations in atmospheric conditions encountered in of the turbofan. Equivalent specific fuel consumption widespread operations. is used for the turboprop engine and is the fuel flow in pounds per hour divided by a turboprop's equivalent COMPACTNESS shaft horsepower. Comparisons can be made between To affect proper streamlining and balancing of an the various engines on a specific fuel consumption basis. aircraft, the shape and size of the engine must be as compact as possible. In single engine aircraft, the shape and size of the engine also affect the view of the pilot, making a smaller engine better from this standpoint, in 1.10 Module 14 - Propulsion addition to reducing the drag created by a large frontal spread out an engine is, the more difficult it becomes area. Weight limitations, naturally, are closely related to to keep the specific weight within the allowable limits. (/) w the compactness requirement. 1be more elongated and z az w TYPES AND CONSTRUCTION w z co0:: ::J In a reciprocating engine, the functions of intake, evolved, these other engine types were developed to 1- compression, combustion, and exhaust all take place take the place of the pure turbojet engine. The turbojet in the same combustion chamber. Consequently, each engine has problems with noise and fuel consumption in must have exclusive occupancy of the chamber during the speed range that airliners fly (.8 Mach). Due to these its respective part of the combustion cycle. A significant problems, use of pure turbojet engines is very limited. So, feature of the gas turbine engine is that separate sections almost all airliner type aircraft use a turbofan engine. are devoted to each function, and all functions are performed simultaneously without interruption. A Turbofan engines were developed to turn a large fan or typical gas turbine engine consists of: set of fans at the front of the engine and produces about 1. An air inlet, 80 percent of the thrust from the engine. 1his engine is 2. Compressor section, quieter and has better fuel consumption in the high sub- 3. Combustion section, Mach speed range. Turbofan engines have more than 4. Turbine section, one shaft in the engine; many are two shaft engines. 'This 5. Exhaust section, means that there are compressors and turbines that drive 6. Accessory section, and it. 1bese two shafted engines use two spools (a spool 7. 1he systems necessary for starting, lubrication, is a compressor and a shaft and turbines that driven fuel supply, and auxiliary purposes, such as anti- that compressor). In a two spool engine, there is a high icing, cooling, and pressurization. pressure spool and a low pressure spool. The low pressure spool generally contains the fan(s) and the turbine stages Another common nomenclature describing the various it takes to drive them. The high pressure spool is the sections of a turbine engine are known as the "cold high pressure compressor, shaft, and turbines. This spool section" and the "hot section". Cold section refers to makes up the core of the engine, and this is where the the parts of the engine from the inlets up through the combustion section is located. The high pressure spool is compressors and/or diffusers. Hot section refers to also referred to as the gas generator because it contains the areas past the compressors from the combustion the combustion section. chambers through the exhaust. BYPASS RATIO The major components of all gas turbine engines Turbofan engines can be low bypass or high bypass. 1be are basically the same; however, the nomenclature amount of air that is bypassed around the core of the of the component parts of various engines currently engine determines the bypass ratio. As can be seen in in use varies slightly due to the difference in each Figure 1-8, the air generally driven by the fan does not manufacturer's terminology. T'hese differences are pass through the internal working core of the engine. reflected in the applicable maintenance manuals. The amount of air flow in lbs/sec from the fan bypass compared to the amount of air that flows through the TURBINE ENGINE TYPES core of the engine is the bypass ratio. One of the greatest single factors influencing the construction features of any gas turbine engine is the ,c;: I type of compressor or compressors for which the engine is designed. Four types of gas turbine engines are used Turbofan engines are generally categorized as high to propel and power aircraft. They are the turbofan, bypass or low bypass in accordance with their bypass turboprop, turboshaft, and turbojet. (Figure 1-7) The ratios. Most transport category aircraft use high bypass term "turbojet" was used to describe any gas turbine engines. Some low bypass turbofan engines are used in engine used in aircraft. As gas turbine technology speed ranges above.8 Mach (military aircraft). These Module 14 - Propulsion 1.11 www.amequestionpaper.in high pressure turbo fan fan low low pressure pressure compressor turbine turbo prop turbo jet intake compression combustion exhaust turbo shaft turbine exhaust compressor compressor I power shaft Figure 1-7. The four primary types of gas turbine engines. 1.12 Module 14 - Propulsion (f) LlJ z az LlJ LlJ z iii a: :J 1- Figure 1-8. Fan airflow and core airflow of a turbofan engine. engines use augmenters or afterburners to increase thrust. By adding more fuel nozzles and a flame holder in the exhaust system extra fuel can be sprayed and burned which can give large increases in thrust for short amounts of time. The turbofan gas turbine engine is, in principle, the same as a turboprop, except that the propeller is replaced by a duct enclosed axial flow fan. (Figure 1-9) The fan can be a part of the first stage compressor blades or can be mounted as a separate set of fan blades. The blades can be mounted forward of the compressor. Figure 1-9. A turbofan engine. The general principle of the fan engine is to convert more of the fuel energy into pressure. With more of Two different exhaust nozzle designs are used with the energy converted to pressure, a greater product of turbofan engines. The air leaving the fan can be ducted pressure times area can be achieved. One of the major overboard by a separate fan nozzle (Figure 1-7), or it advantages is turbofan production of this additional can be ducted along the outer case of the basic engine thrust without increasing fuel flow. The end result is fuel to be discharged through the mixed nozzle (core and economy with the consequent increase in range. Because fan exhaust together). The fan air is either mixed with more of the fuel energy is turned into pressure in the the exhaust gases before it is discharged (mixed or turbofan engine, additional stages must be added in the common nozzle), or it passes directly to the atmosphere turbine section to provide the power to drive the fan. without prior mixing (separate nozzle). Turbofans are This means there is less energy left over and less thrust the most widely used gas turbine engine for air transport from the core exhaust gases. aircraft. The turbofan is a compromise between the good operating efficiency and high thrust capability of Also, in a mixed-exhaust nozzle (where fan air and core a turboprop and the high speed, high altitude capability air mix in a common nozzle before entering ambient of a turbojet. conditions) the exhaust nozzle must be larger in area. The result is that the fan develops most of the thrust. The turboprop engine is a gas turbine engine that turns a The thrust produced by the fan more than makes up for propeller through a speed reduction gear box. This type the decrease in thrust of the core (gas generator) of the of engine is most efficient in the 300 to 400 mph speed engine. Depending on the fan design and bypass ratio, it range and can use shorter runways that other aircraft. produces 80 percent of the turbofan engine's total thrust. Approximately 80 to 85 percent of the energy developed by the gas turbine engine is used to drive the propeller. The rest of the available energy exits the exhaust as thrust. Module 14 - Propulsion 1.13 The turboshaft engine used in aviation is a gas turbine units (APU's). APU's are used on large aircraft to engine made to transfer horsepower to a shaft to provide electrical power and bleed air on the ground and operate something other than a propeller. They are emergency backup power in flight. used primarily to power helicopters and auxiliary power TURBINE ENGINE FUEL SYSTEMS GENERAL REQUIREMENTS turbine in excess of that necessary to maintain a constant The fuel system is one of the more complex aspects of rpm. However, if the fuel flow increases too rapidly, an the gas turbine engine. It must be possible to increase or over rich mixture can be produced, with the possibility decrease the power at will to obtain the thrust required of a rich blowout or compressor stall. for any operating condition. In turbine-powered aircraft, this control is provided by varying the flow Turbofan, turbojet, turboshaft, and turboprop engines of fuel to the combustion chambers. However, some are equipped with a fuel control unit which automatically turboprop aircraft also use variable pitch propellers; satisfies the requirements of the engine. Although the thus, the selection of thrust is shared by two controllable basic requirements apply generally to all gas turbine variables, fuel flow and propeller blade angle. engines, the way in which individual fuel controls meet these needs cannot be conveniently generalized. The quantity of fuel supplied must be adjusted automatically to correct for changes in ambient TURBINE FUEL CONTROLS temperature or pressure. If the quantity of fuel becomes Gas turbine engine fuel controls can be divided into excessive in relation to mass airflow through the engine, three basic groups: the limiting temperature of the turbine blades can 1. Hydromechanical be exceeded, or it will produce compressor stall and 2. Hydromechanical/Electronic a condition referred to as rich blowout. Rich blowout 3. Full Authority Digital Engine (or Electronics) occurs when the amount of oxygen in the air supply Control (FADEC) is insufficient to support combustion and when the mixture is cooled below the combustion temperature The hydromechanicallelectronic fuel control is a hybrid by the excess fuel. The other extreme, lean flame-out, of the two types of fuel control, but can function solely occurs if the fuel quantity is reduced proportionally as a hydromechanical control. In the dual mode, inputs below the air quantity. The engine must operate through and outputs are electronic, and fuel flow is set by servo acceleration and deceleration without any fuel-control- motors. The third type, FADEC, uses electronic sensors related problems. for its inputs and controls fuel flow with electronic outputs. The FADEC type control gives the electronic The fuel system must deliver fuel to the combustion controller (computer) complete control. The computing chambers not only in the right quantity, but also in the section of the FADEC system depends completely on right condition for satisfactory combustion. The fuel sensor inputs to the electronic engine control (EEC) to nozzles form part of the fuel system and atomize or meter the fuel flow. The fuel metering device meters the vaporize the fuel so that it ignites and burns efficiently. fuel using only outputs from the EEC. Most turbine The fuel system must also supply fuel so that the engine fuel controls are quickly going to the FADEC type of can be easily started on the ground and in the air. This control. This electronically controlled fuel control is means that the fuel must be injected into the combustion very accurate in scheduling fuel by sensing many of the chambers in a combustible condition during engine engine parameters. starting, and that combustion must be sustained while the engine is accelerating to its normal idling speed. Regardless of the type, all fuel controls accomplish the same function. That function is to schedule the fuel flow Another critical condition to which the fuel system must to match the power required by the pilot. Some sense respond occurs during a rapid acceleration. When the more engine variables than others. The fuel control engine is accelerated, energy must be furnished to the can sense many different inputs, such as power lever 1.14 Module 14 - Propulsion position, engine rpm for each spool, compressor inlet delivers the fuel to the engine fuel system. Actual pressure and temperature, burner pressure, compressor operating procedures for a hydromechanical fuel control (/) lJ.J discharge pressure, and many more parameters as is very complicated and still the fuel metering is not z az needed by the specific engine. These variables affect the as accurate as with an electronic type of interface or lJ.J lJ.J amount of thrust that an engine produces for a given fuel control. Electronic controls can receive more inputs with z flow. By sensing these parameters, the fuel control has a greater accuracy than hydromechanical controls. Early iii a: :::> clear picture of what is happening in the engine and can electronic controls used a hydromechanical control with f- adjust fuel flow as needed. Each type of turbine engine an electronic system added on the system to fine tune has its own specific needs for fuel delivery and control. the metering of the fuel. This arrangement also used the hydromechanical system as a backup if the electronic HYDROMECHANICAL FUEL CONTROLS system failed. {Figure 1-10) Hydromechanical fuel controls w