Maintenance Manual for BG Coaches of ICF Design PDF
Document Details
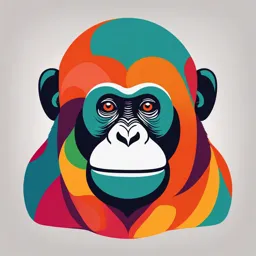
Uploaded by ImaginativePeachTree
STC/JHS
Tags
Related
- Maintenance Manual for BG Coaches of ICF Design (PDF)
- Maintenance Manual for BG Coaches of ICF Design - Air Brake System PDF
- Bogie Mounted Air Brake System PDF
- Maintenance Manual for BG Coaches of ICF Design PDF
- Maintenance Manual for BG Coaches of ICF Design PDF
- Maintenance Manual for BG Coaches of ICF Design PDF
Summary
This document is a maintenance manual for BG coaches of ICF design, focusing on air-conditioned coaches. It provides detailed instructions and procedures for various maintenance tasks. It covers major equipment, maintenance schedules, and other relevant information.
Full Transcript
Maintenance Manual for BG coaches of ICF design Air Conditioned Coaches CHAPTER 8 AIR CONDITIONED COACHES 801 INTRODUCTION Types of AC coaches on Railways can be c...
Maintenance Manual for BG coaches of ICF design Air Conditioned Coaches CHAPTER 8 AIR CONDITIONED COACHES 801 INTRODUCTION Types of AC coaches on Railways can be classified broadly as under : AC COACHES End –On –Generation Self – Generating coaches coaches Under Slung Roof Mounted Under Slung Roof Mounted Package Unit Package Unit 801a Power Supply System: As far as power 801b MAJOR EQUIPMENTS USED IN AC supply system is concerned, the coaches UNIT ARE : are of the following two types : 1. Compressor (open type for under (i) End-On-Generation (EOG) : In this slung, sealed type for Roof Mounted system two types of Power cars are used Package Unit (RMPU) 2. Condenser including liquid receiver a. Coaches mounted with 50 KVA, 750 V/415V, 3 φ and dehydrator. transformer. 3. Expansion Valve b. Coaches with out stepdown 4. Evaporator with heater element. transformer suitable only for old low capacity power cars. 5. Motors for compressor, condenser, (ii) Self Generating (SG) : Based on evaporator. AC equipment, there are two types 6. Other protective devices and control of Self Generating coaches. panels. a. 110 V DC with under slung type AC equipment working 7. Thermostat, Filters etc. from 110 V DC. 802 MAINTENANCE SCHEDULES FOR b. 110 V DC with Roof SELF GENERATING AIR Mounted AC Package Units CONDITIONED COACHES FITTED working from 415 V, 3 φ, WITH UNDER SLUNG EQUIPMENT: obtained with the help of 25 (Ref: RDSO’s maintenance KVA inverters mounted on schedule No EL/TL- underslung as well as AC/Maint.Sched./Rev.1) onboard. Chapter 8 – Page 1 of 28 Maintenance Manual for BG coaches of ICF design Air Conditioned Coaches 802a TRIP SCHEDULE (PRIMARY AND iii. Alternators SECONDARY MAINTENANCE) n Check the condition of i Axle Pulley outgoing cables and its cleating arrangement. n Examine the indicating Replace the grommet, if white mark on the pulley necessary. Ensure that axle and ensure that the flexible pipe carrying the pulley has not shifted. If cables is connected properly pulley has shifted , pulley to to the grommet to prevent be removed and re- damage to insulation. tightened after replacing n Check the suspension pin, rubber pads. Indicating bush and securing nuts and white marks to be provided. bolts. Also check distance between wheel axle and axle pulley n Check the pulley fixing, with gauge. concentrating on lock nut and locking collar pin. If n Tap wit h hammer and lock nut is damaged, replace judge the tightness by it. sound. n Carry out visual inspection of terminal box for signs of n Check the lock nuts and overheating and presence of split pins for availability fumes. Blow off dust if and tightness. required. n Check the terminal box for n Check profile of ‘V’ presence of water and drain groove for worn out out if necessary. pulleys, replace pulley if worn out. n Check the connections for looseness or cracks, if ii Belts required re-crimping/ tightening should be done. n Check condition of belt for n Check main suspension lugs fraying of edges and replace of alternators for signs of it on condition basis. crack. n Clean the regulator box n Check the belts for overturn externally and remove all the and correct it, if necessary. dust particularly from heat sinks. n Check the number of belts. n Check safety chains and The belts should be 12 (6 on chain fixing nuts, bolts and either side) for each split pins. alternator in primary depot n Check tension rod fixing pin and 10 (5 on either side) in of alternator with washer secondary depot. and split pin. n Tension should be felt by n Check the log book for hand by striking it slightly. abnormal /unequal load Belt in correct tension will sharing. Corrective action respond `alive'. Pull the belt should be taken to ensure and check the spring action. that the difference is within the range of 30 %. Chapter 8 – Page 2 of 28 Maintenance Manual for BG coaches of ICF design Air Conditioned Coaches iv. Battery & Battery Box n Ensure that spare batteries, particularly VRLA cells are n Check the level of properly kept at places not electrolyte in all the cells exposed to direct sunlight, and top up with distilled rain, dust etc. The batteries water, if necessary. should be stored indoor preferably between 20 to n Check the specific gravity 35°C in clean and dry and voltage of 4 pilot cells. location. n Check inter-cell connection for looseness. Check for n VRLA Batteries : SMI crack in containers leading no.RDSO/PE/TI/SMI/0001- to leakage. If needed replace 98 (Rev.0) dt. 01.06.98 to be the defective cell with followed. healthy cell of similar capacity and lug date. v. Compressor and Condenser Motor n Check for heating signs on the positive and negative n In case of compressor motor, terminals and discolouring examine the tyre coupling of the cells container/top lid. for any indication of n If required, individual cells looseness or slip and rectify in the battery bank or defects. complete battery bank may be subject to charging so that n Open insp ection cover and the Specific Gravity (SPG) examine the condition of may rises to min. 1240. commutator. Clean with sand paper or pumice stone, n Check the top of cells and if necessary. Do not remove keep it clean and dry. Plugs the dark tan film should be tight. unnecessarily. Clean all n In case of Valve Regulated carbon dust with dry Lead Acid (VRLA) compressed air. batteries, check for abnormal bulging of cell lids, cracks n Check condition of carbon on positive and negative brushes. If worn out, replace terminals. Replace defective with carbon brushes of cells.. approved grade. n In case of sulphation of n Check condition of pigtails. terminals remove the connectors, clean, put back If necessary, replace as per and apply petroleum jelly. the manufacturer's recommendation. n Check suspension/cradle of battery box for availability n Check the starting resistance of all suspension bolts, signs connectors for tightness. of any crack, corrosion, rusting and take corrective n Check suspension of action, if necessary. compressor motor unit for n Check for proper fitment of any signs of crack, corrosion battery cells in battery box and rusting. Take remedial or module fitment in case of action if required. VRLA batteries, if required proper packing may be n Carry out visual inspection provided. for signs of overheating and presence of fumes. Blow off dust if required. Chapter 8 – Page 3 of 28 Maintenance Manual for BG coaches of ICF design Air Conditioned Coaches n Examine flexible type n Check the direction of coupling and replace, if rotation for correctness if the found defective. same has been attended. n Clean the compressor n Check the fan blades for externally with compressed tightness in case of air. condenser motor. n Check for signs of leakage vi. Evaporator Motor at joints & shaft seal and take remedial measure n Open the inspection cover wherever necessary. and examine the condition of commutator. Clean with 0-0 n Examine the fixing sand paper or pumice stone, arrangement, check the if necessary. Do not remove condition of the anti the dark tan film vibration mountings for unnecessarily. Clean all tightness of the fixing bolt. carbon dust with dry compressed air. viii. Condenser n Check condition of carbon n Check and ensure that the brushes and pigtails. Replace protection plates and grills if necessary as per the are provided on the three manufacturer's sides of the frame. recommendation. n Examine the fins for external n Check the bearing for noise. damage due to flying ballast and take corrective action if n Check the blower fixing for necessary. tightness. n Check suspension of the n Carry out visual inspection condenser for signs of for signs of overheating and cracks, corrosion or rusting presence of fumes. Blow off and take remedial action. dust if required. Tighten bolts, etc., if necessary. vii. Compressor ix. Dehydrator And Liquid Receiver n Check the proper lubrication of compressor n Check the sight glass for level of oil when operating leakage, rectify if necessary. should be upto half of the bull eye glass. n After 10 minutes of starting the compressor, check the n Lubricate the compressor as level of liquid refrigerant per RDSO SMI No. should be at the bottom of RDSO/AC/SMI/6 the lower glass of the liquid receiver. n Examine the reading of HP, LP and OP gauges recorded n After 15 minutes of starting during the journey for the plant, feel the outlet and abnormality and take inlet to dehydrator by hand necessary action. for temperature difference. The outlet should not be colder than inlet. Chapter 8 – Page 4 of 28 Maintenance Manual for BG coaches of ICF design Air Conditioned Coaches xiii. Lights And Fan Wiring x Filters n Check for earth leakage in n Remove fresh air and return the wiring with a double test air filters and replace it by lamp. Rectify if any defect spare clean units. noticed. n Check and ensure that fresh n Check for any loose air dampers are in proper connection & tighten if order. necessary. xi Thermostats xiv. Lights And Fans n If the report of the attendant n Check all the lights and fans indicates that thermostate for proper working. Rectify do not work, examine the or replace if necessary. thermostats for break in mercury, break in stem, etc. n Clean the fan and light Replace the thermostats, if fitting externally. necessary. Follow RDSO SMI No RDSO/SMI/AC/15. n Check all switches, fan regulators, call bells and n Clean thermostat bulb with push buttons for proper cotton. working. Replace if necessary. n Ensure working of plants in auto mode for all xv. Pre-Cooling Unit temperature setting. n Clean rectifier unit xii. Panel Board externally with dry compressed air. n Clean the panel and remove dust. n Check the presence of water in terminal box, drain out if n Check the working of necessary. indication lamps, replace it if necessary. n Load the pre-cooling unit to its maximum capacity and n Check the availability of check for any overheating. spare fuses in the place provided for the same and n Check suspension of battery provide if necessary. charger for sign of any crack, corrosion or rusting n Check the availability of arc and take action if required. chute and provide if necessary. n Check the pre-cooling socket n Check and clean the contacts pins and its fixing of contactors 12, 13 and arrangements. 13A. xvi. General n Check the operation of cooling pilot relay (by short n Check log- sheet of last trip circuiting terminals C.T.). and attend all the faults Remove short after the recorded in the log sheet. completion of check. Chapter 8 – Page 5 of 28 Maintenance Manual for BG coaches of ICF design Air Conditioned Coaches n Run the plant for half an iii. Rectifier Cum Regulator Box hour. Check system operation, specially the n Clean all dust with dry following: compressed air externally. 1. Suction pressure gauge n Open the cover and check reading should be 2-3 sealing rubber gasket for signs Kg/cm2. of fraying. Drain out water if 2. Delivery pressure gauge any. reading should be 10 – 14 Kg/cm2. n Clean all dust with dry 3. Oil pressure should be compressed air. preferably a minimum 3kg/cm2 above hand blower from inside to suction pressure. remove all dust particularly 4. Suction should be cold from heat sink of electronic and sweaty. Delivery components and terminal should be very hot and board. liquid line should be warm. n Check that the voltage and 5. Feel the expansion valve current setting. Ensure that by hand. It should be they have not been disturbed cold. and are in locked position. n Note the battery voltage on n Check the field fuses and LOAD and NO LOAD. phase fuse and ensure that only specific HRC fuses have been 802b MONTHLY SCHEDULE used. In addition to the trip schedule n Check all the electrical items, following are also to be attended. connections for tightness. i. Axle Pulley iv. Alternators n Ensure that the gap between n Lubricate the threads of the the two halves of the pulley is tension rod and adjusting nut. 3 mm. Check tightness of the axle pulley bolts by 30 kg-m n Check the profile of ‘V’ torque wrench. grooves and replace worn-out pulleys. n Check distance between wheel hub and axle pulley with v. Battery Chargers gauge plate. n Ensure that the coarse ii. Belts and fine control switch is in position No.1. n Check tension of belts. For the n Check and clean all exact measurement of static connections and contacts. tension, apply force `P' with a Spring balance at the Centre of vi. Battery span in direction perpendicular to the span until Conventional Lead Acid the belt is deflected from the Batteries normal to the extent of 16 mm per metre of span. The force n Check specific gravity `P' should be between 31.4 to and voltage of all cells. 47.0 kg. If the belts are loose. replace them. Chapter 8 – Page 6 of 28 Maintenance Manual for BG coaches of ICF design Air Conditioned Coaches n Remove inter-cell viii. Condenser & Condenser Motor connection, take out the cells, clean thoroughly n Clean the condenser fins the cells, intercell and end thoroughly with high cell connectors and fit pressure water jet so that air back in the coach. Use passes through the fins petroleum jelly. uniformly. n Examine condition of n Clean fins with liquid battery boxes. Paint if solution and high force necessary. water jet. n Check vent plugs. Tighten n Ensure minimum air flow of if necessary. Replace if 4 meters per second through missing. condenser. n Check the condition of n Check the incoming leads cells by cell tester. for proper connection and Replace defective cells. tightness. Ensure that the grommet is in position and VRLA Batteries the flexible hose- pipe is connected properly at both SMI no.RDSO /PE/ TL /SMI /0001-98 ends. (Rev.0) dt. 01.06.98 and n Check the spring tension as RDSO/PE/TL/SMI/0002-98 (Rev.0) recommended by the dt. 09.12.98 to be followed. manufacturers. vii. Compressor Motor n Check the carbon brushes; replace with approved grade n Check tightness of the of carbon brushes if coupling and mounting bolts necessary. by 30 kg-m torque wrench and tighten, if necessary. ix. Evaporator Motor n Check the terminal n Check the blower drum connections in the terminal for looseness. box and tighten, if necessary. n Check the spring tension n Examine the incoming leads as recommended by the manufacturers. for proper connections and tightness. Check the flexible n Flush the drip tray. Check conduit for proper anchoring drain pipe of drip tray for at both ends. clogging by passing n Measure the spring tension water through the drip of brush holder. If less than tray and clean, if found clogged. the value recommended by manufacturer, replace the spring. x. Compressor n Check the carbon brushes; if necessary, replace with n Check tightness of bolts approved grade of carbon of anti-vibration mounting brushes. with 30 kg- m torque and tighten if necessary. n Check the alignment of the compressor and motor. Chapter 8 – Page 7 of 28 Maintenance Manual for BG coaches of ICF design Air Conditioned Coaches n Do not remove dark tan film n Check the tightness of unnecessarily. If necessary, nuts and bolts of replace the carbon brushes compressor head and its with carbon brushes of cover. approved grade. n Check oil and liquid n Remove the cover of tube levels and note any signs light, night light and clean the of leakage which will be bulb, tube and cover from indicated by presence of inside. the oil at the point of leakage. 802c QUARTERLY SCHEDULE n Clean the oil strainer with petrol or CTC (Carbon In addition to Trip and Monthly Schedule Tetrachloride). items, following are also to be attended. xi. Evaporator & Drip Water Drain i. Axle Pulley n Clean evaporator coil. n Check grooves for wear and n Replace return and fresh take necessary action. air filters. ii. Alternator n Pour water on evaporator coil and ensure the water n Disconnect the regulator and drains out easily.. measure the insulation by 500 V megger; if less than 2 xii. Panel Board Meg ohm, remove winding of alternator and heat in the n Clean contactor tips of all oven at 80 degrees C for 1 contactors; replace where hour. necessary. n Check all the electrical iii. Compressor, Condensor And connections for tightness Evaporator Motors and tighten if necessary. n Check the relays and n Disconnect the motors, contactors for their proper measure the insulation by functioning. 500 V megger; if less than 2 Meg ohms, remove and n Check the PCB in the heat in air oven at 80° C thermostat circuits. for 1 hour. n Check the diodes provided n Check for the positive on the panel board. locking of rockers. n Check the rotary switch for n Lubricate the bearings of fluorescent lights. The all motors with polarity change connections recommended grease. should be in order. iv. Condenser xiii. Light and Fan n Clean the compressor fins and copper tubes as per n Open the inspection-cover of RDSO SMI No. each coach fan and examine RDSO/SMI/AC/16 the condition of commutator. Clean with 0-0 sand paper. if n Check the condition of necessary. body frame and replace the condenser, if necessary. Chapter 8 – Page 8 of 28 Maintenance Manual for BG coaches of ICF design Air Conditioned Coaches with pre-cleaned/new-filter v. Dehydrator and Liquid and close access doors Receiver properly. n Clean the strainer in the v. Check the log sheet maintained dehydrator-cum-filter for each AC coach and attend unit. the defects noticed during run as reported by escorting staff. vi. Evaporator And Expansion Valve vi. Check for working of Roof Mounted Package Unit n Clean the strainer used (RMPU) and Control panel as before expansion valve. following:. n Clean the assembly of n Switch `ON’ RSW-I and evaporator coil and check that all the three surroundings with pilot indication lamps vacuum cleaner. (Red, yellow and blue) for R.Y.B. phases and power n Clean the drip tray and `ON’ indication LED drain-pipe thoroughly and (Green) are glowing. check for water leakages. n Put RSW-2 in ``ON’ vii. General position and keep RSW-3 in `VENT’ position and n Adjust the air distribution check that: by measuring the temperature of each q Indication LED (green compartment. colour) for Blower `ON’ is glowing and 803 MAINTENANCE SCHEDULE q Blower fan is working FOR ROOF MOUNTED AC PACKAGE UNITS AND ITS CONTROL PANEL n Check for satisfactory operation of vane relay by 803a TRIP SCHEDULE (PRIMARY moving the flap by hand AND SECONDARY gently. MAINTENANCE) n Check for satisfactory i. Clean all dust from panel by operation of the package dry compressor air from the unit by moving RSW-3, in panel. AUTO, MANUAL HEATING & MANUAL ii. Check that all the safety and COOLING modes. This protection devices are in can also be verified from working condition and not in indication LEDs (green the by passed condition. colour). iii. Replace defective/by passed n Check that cooling system components including is working even if only indication LEDs and lamps, if one condenser fan out of any. the two is working. This iv. Remove fresh air and return air can be done by simply filters by opening the access switching off MCB 2 or doors provided under the MCB 3/taking out fuses of bottom of unit. Clean these condenser motor 1 or filters with pressurised air and condenser motor 2. jet of water and place them in their place or replace them Chapter 8 – Page 9 of 28 Maintenance Manual for BG coaches of ICF design Air Conditioned Coaches n Check that cooling and heating 803b MONTHLY SCHEDULE thermostats works properly, i.e. A/C system “cut-off” and “cut-in’ In addition to trip schedule following in auto-mode. items should also to be attended to:- n Check that compressor by pass i. Run the plant for half an hour and switch RSW-5 works satisfactorily check the current drawn by various n HP1 & HP2 Cut-outs equipment with the help of clamp tester. Switch ‘ON’ the compressor with condenser fan ‘OFF’. Take out Normal currents for various equipment fuses /switch-off MCB-1 and and mode of operation shall be as MCB-3 of the condenser fan under:- motors and keep the package in manual cooling mode. n Package in cooling mode Compressor should trip within 10 : 20-23 Amp. minutes. HP cut outs should be n Package in heating mode reset after each tripping. : 11-13 Amp. n LP-1 & LP-2 Cut outs n Compressor motors : 7-10 Amp. Switch `ON’ the compressor with n Condenser motors condenser. Take out fuses/switch- : 1.5-2 Amp. off MCB-1 provided in the power circuit of blower motor and short n Blower Motor terminals of vane relay. Keep the : 1.5-2.5 Amp. package in manual cooling mode. n Check working of both Roof Compressor should trip with 10 Mounted Package Unit (RMPUs) minutes. with either of the inverter on the Self Generating (SG) AC coaches n OHP1 and OHP2 provided with two package units. Switch ‘ON’ the heaters with ii. Check and tighten all terminals in the blower off, take out blower motor control panel. fuses or put off MCB-I and short the terminals of contactors AC-I iii. Check and clean contacts of contactors or vane Relay. In old control and replace pitted contacts if required. panels where AC-I is not iv. Check visually condenser fan blades provided, keep the package in and ensure there is no crack on the manual heating mode. The blades or the hubs. heaters should trip with 10 v. Check and tighten mountings of minutes. blower and condenser motors and ensure that these are in good n CONTROL PCB conditions. Keep the AC package unit in vi. Check that all legend plates inside the Auto Mode. Run the blower short control are intact. terminals of cooling thermostat vii. Check all connections on switch gears, on PCB. The compressor LED terminal blocks are tight. indication should come ‘ON’. viii. Check that glass cover over indication Open the terminals of heating PCB is intact. thermostat on PCB Heater LED should come `ON’. ix. Check for proper tightening of cover provided over evaporators compartments. Chapter 8 – Page 10 of 28 Maintenance Manual for BG coaches of ICF design Air Conditioned Coaches x. Create single phasing in compressor n Terminal Connections/Fixing : circuits by taking out one fuse/removing one phase wire from n Electrical - Normally loose incoming terminals of MCB-4/MCB-5. connections leading to wire Compressors should trip and CP1/CP2 burning/sparking are observed at over load trip indication should come connection terminals. ``ON’. n Usage of spring washer mostly xi. Check for proper operation of time avoids this problem. delay relays provided in compressor circuit. As soon as power supply is n Gently shake the wire (especially switched `ON’ first compressor should power cables) near the joints and come in circuit immediately and the on observation of loose joints, second one after 2.5 minutes. tighten the same and also observe cable insulation for any xii. Inverter deformation/brittleness. If so Caution: Inverter must be switched off replace them with same size of preferably at power panel itself before the cable only. attempting to do any maintenance n Mechanical - Inverter should be operation. fixed at the bottom as well as top, tighten the bolts and nuts used for § Cleaning of cubuicle : Dust deposit fixing the inverter and ensure that inside the converter should be it does not vibrate in run. Also carefully removed at regular basis. tighten the sub-assemblies if Unit should be cleaned with brush found loosened. In case of under- and vacuum cleaner or with dry slung inverter these shall also be compressor (Max. 1bar) – regularly checked and tightened. inaccessible parts. n Protection circuit/ Induction § Cleaning of PCBs : Using a soft circuit : brush, remove the dust collected on PCBs gentle. n Check the indication/ protection circuits ensure 803c QUARTERLY SCHEDULE that all the protection and indication are working In addition to trip and monthly schedules properly. following items should also be attended. n Uses of fuse of power i. Inverter rating in the inverter, don,t use wire fuses. Caution: inverter must be switched n Remove both inverter and off preferably at power panel itself battery fuses in power before attempting to do any panel before attempting maintenance operation. some fitting or wiring in the inverter. n Cleaning of cubicle : Dust deposit inside the converter n Capacitor - On observing should be carefully removed at leakage of any capacitor regular basis. Unit should be inside the inverter remove cleaned with brush and vacuum the respective capacitor cleaner or with dry compressor and replace with new one (Max. 1 bar) – inaccessible parts. of the same value and make. n Cleaning of PCBs : Using a soft brush, remove the dust collected on PCBs gently. Chapter 8 – Page 11 of 28 Maintenance Manual for BG coaches of ICF design Air Conditioned Coaches n Cooling Fan – Check the cooling n Check anti-vibration mountings of fan for operation. If damaged/burnt compressor, condenser and blower replace with new one of the same motors and replace if necessary. rating. Life of fan is about 3 years, n Charge refrigerant (R-22) if less replace, if due. cooling is noticed.(refer RDSO SMI No. RDSO/AC/SMI/7 n Instrument cooling fans- Check if the instrument fan provided n Check that locking arrangement of between inverter and chopper control panel works properly. modules is working when the inverter is “ON”. If not working n Check insulation resistance of all the motor by 1000 V megger. replace the fan, by taking out Attend motors with poor insulated chopper and inverter modules. (in on-board type inverter). less than 2 Mega-ohm. iv. NOTE : n PCB Terminal – Gently tap the wires at PCB terminals and check n SKF/FAG (imported) make for any loose connection. Tighten bearings for alternator procured the screw or solder the terminals if directly from manufacturers as found blackened, informed the specified in the RDSO specification inverter supplier. shall be used. Use of other makes of bearing is not permitted. n Colour change in PCBs – Check for any colour change in PCBs. n Shock pulse meter shall be Replace the PCB, if found procured by Railways and blackened and inform the inverter workshops to monitor condition of supplier. the bearing regularly during maintenance service and after n MCCB – When MCCB is switched replacement of defective bearings. “ON” MCCB is tripping and fuse is blowing instantaneously, it is due n Induction heater/oil bath shall be to IGBT problems. They have to be used for heating the bearing to the checked and replaced, if they are required recommended found defective. temperature. ii. Drip Tray n The pulley condition such as wear on V group, pulley key way, shaft key way, groove angle etc. shall be n Check the normal flow of water in monitored during POH. Proper drip tray by running the AC plant gauges shall be used for checking continuously for 2 to 3 hours. “V” groove of the pulley. n Pour water into drip tray and 804 SIX MONTHLY SCHEDULE ensure that the poured water is drained through the outlet pipe. 804a V-belts: n Some sort of cleaning agent should The existing “V” belts shall be replaced be used for cleaning the sludge with the new “V” belt (6+6) nos., having inside the pipe walls. same grade/make. The old “V” belts removed from service to be destroyed. iii. Others 805 POH SCHEDULES OF UNDER SLUNG Self Generating (SG) TYPE n Check all the motors for abnormal AIR CONDITIONED COACHES sound use shock pulse meter and (Ref : RDSO doc. No. EL/AC/POH replace the bearing of condenser Schedule/002, Nov.,93) and blower motor, if necessary. Chapter 8 – Page 12 of 28 Maintenance Manual for BG coaches of ICF design Air Conditioned Coaches 805a. SEQUENCE OF WORK TO BE DONE iii. Dusting DURING POH With the help of compressed air On arrival into shop place the coach on pit remove the dust of air ducts. line and inspect electrical and A/C equipment. Note down the defects and iv. Cleaning and overhauling deficiencies. Disengage the `V' belt tensioning gear on both the bogies. Before overhauling, measure the Disconnect the alternator connection, and insulation resistance of all the remove the belt-tensioning device. electrical equipment such as alternator, motor and wiring to know i. Lifting the condition of equipment. Check and clean all the under frame Remove the alternator cables and suspension arrangements, lugs and carry out visual inspection on conduit terminals. After POH, test the wiring and refrigeration pipes. Remove the for insulation and fit the pre-cooling alternators from bogies. Replace plugs. alternator, regulator and tensioning gears with over hauled alternator, v. Simulation testing regulator and tensioning gear. During this activity carry out repairs, if Check the alternator output on required, to equipment suspension different load conditions. Check arrangement on under carriage. Send both the alternators for load sharing the alternators and regulators to shop with the help of variable speed for overhauling. motors. ii. Stripping vi. Equipping During this activity, the following air- In this activity fit all the conditioning and electrical equipment refrigeration and electrical will be removed: equipment to their respective n Fresh air and return air filter positions. Connect all the wiring and flanges in the refrigeration system n Compressors and their motors wherever necessary. Charge the gas n Condenser including liquid into the system. receiver cum dehydrator and condenser motors vii. Static testing n Evaporator unit and its motor Run the plant through pre-cooling n Water raising apparatus terminal and check for proper n Battery and battery box for functioning of electrical and AC repairs. equipment. n Battery charger-cum-pre-cooling transformer viii. Alternator Connection and Tensioning n Thermostats n Control p anel Join the connections of alternators n Expansion valve and fit the belt-tensioning device. Provide the new 6+6 `V' belts for n Gauges and cutouts alternators. n Carriage fans n Berth light fittings n Ammeters and voltmeters of power panel Chapter 8 – Page 13 of 28 Maintenance Manual for BG coaches of ICF design Air Conditioned Coaches 805b OVERHAULING ACTIVITIES OF n In case of carrier 5F 30 MAJOR AC EQUIPMENTS DURING compressor match the colour POH to ensure proper matching between tapered shaft and i. Compressors corresponding flexible n The given activities are only for coupling. under slung type AC system n In case of ACCEL installed with open type compressor check the end compressors. Remove driving play of crank shaft and flange and provide `V' groove replace the thrust plate, if pulley. Test the compressor to necessary. ascertain its condition. Record n Check the anti vibration the oil pressure during run. For mounting and replace, if Carrier and ACCEL necessary on condition basis. compressors, oil pressure developed should be 3.2 to 3.9 n Use suitable grade of oil for Kg/Sq. cm and 4.2 to 4.9 Lubricating the compressor Kg/Sq.cm respectively. as per RDSO SMI No.RDSO/AC/SMI/6. n Dismantle the compressor completely. ii. Tests on Overhauled Compressor n Inspect and check the dimensions of the wearing Following tests should be components. Replace the worn conducted on overhauled out components. compressor n Replace following components n Temperature rise test 100% irrespective of their condition. n Volumetric efficiency test n Piston rings n Leak back test n Scrapper ring n Vacuum test n Suction and discharge valve n Sub merge test n Shaft seal assembly/O Temperature rise test rings n Gasket packing This test shall be conducted with n Half section bearing compressor running in free air with both suction and discharge valve n Self locking nuts open. Run the compressor till the n Lubricating oil of correct temperature gets stabilized. The grade. temperature will be recorded on the casing cover. Maximum n Replace other components temperature rise at shaft seal shall on condition basis. The not be more than 45° C. sealed control valve shall be replaced after ascertaining Volumetric efficiency test its performance. n Assemble the compressor The compressor shall be run with with replaced components air at nominal speed of 1500 and charge it with rev/min and time taken to attain a lubricating oil. Change the pressure of 7 Kg./Sq.cm shall be lube oil and refrigerant recorded when the discharge line is suction strainers. connected to a reservoir of 100 litters capacity. Chapter 8 – Page 14 of 28 Maintenance Manual for BG coaches of ICF design Air Conditioned Coaches The time taken to attain a pressure of 7 n Immerse the heat exchanger in Kg./sq cm in the reservoir should not be water tank for 24 hours. Wash more than 53 seconds for ACCEL the coils and fins thoroughly compressor and 73 seconds for Carrier, with compressed water jet at KPC, Elgi and Alfa Laval compressors. 12 Kg/sq.cm pressure. Remove Time to attain above specified pressures all the suspended material from in the reservoir shall vary according to the fins. Clean the water- working speed of the compressor and spraying pipe and open the atmospheric pressure also. holes. n The cleaning process shall be Leak back test supplemented by scrubbing with brush and use of This test is in continuation of volumetric compressed water jet. efficiency test. In this test immediately after attaining pressure of 7 Kg/sq.cm. in n After cleaning the cooling coil the reservoir, the compressor shall be pressurize with air at 300 psi stopped and pressure drop due to leakage (21kg./sq.cm.) and immerse in shall be noted. Pressure shall be recorded water tank duly connecting a at the end of 5 minutes and the drop in pressure gauge for 24 hours to pressure shall not exceed 1.25 Kg/sq.cm. detect any leakage by air bubble method. Also see if the Vacuum test pressure drops. Leaks in pipe shall be detected and brazed. The compressor shall be run with suction n After cleaning check the air valve closed and delivery valve open to atmosphere till a vacuum of 100 mm of flow of unit with anemometer. Hg. below atmospheric pressure is n Deflange the liquid receiver by created. The drop in vacuum level shall be removing the outer cover and recorded, after switching off the gasket packing. Clean compressor. thoroughly the inner walls of receiver to remove any Sub-merge test oil/impurity. Clean the sight glass. Assemble the cleaned The compressor shall be charged with dry liquid receiver parts by air at 21 Kg/sq.cm pressure and providing suitable gasket and submerged in water. Then check shall be flanging the outer cover. conducted for any leakage; the same shall be attended and test repeated. No leakage n Pressurize the liquid receiver through casing shall be permitted. at 300 psi (21 kg./sq.cm) and test it for leakage by iii. Condenser Unit (Including liquid immersing in water tank and receiver cum dehydrator) notice for any air bubble in case of leakage. n Dismantle the MS Frame, n Replace the filter and drier condenser coil, liquid receiver- after leak testing of the liquid cum-dehydrator. Cover the inlet receiver. Clean the condenser and outlet flanges of cooling coil housing thoroughly and paint it with a strip of cover plate and before assembly of other gasket so that water may not enter equipment. in to cooling coil. Clean thoroughly n Change the dehydrator-cum- the condenser coil, MS frame by filter element. Also clean the dry air to remove the loose conical filter thoroughly. suspended particles in and around cooling fins. Chapter 8 – Page 15 of 28 Maintenance Manual for BG coaches of ICF design Air Conditioned Coaches iv. Evaporator Unit v. Motors for Condenser, Compressor & Evaporator n Dis-mantle the housing assembly and take out the cooling coil. n Dismantle the motor. Attend the heating element in n Test the insulation resistance position by conducting continuity of armature with 500 V test. Also check the insulation megger. It should be more value between the positive than 1 mega ohm. terminal and negative terminals shorted and the earth. If the value n Check armature winding by a is less than 2 meg ohms, replace voltage drop test method for the complete unit. IR value shall open circuit & short circuit be measured with 500 V megger. fault. n Clean the cooling coil by blowing n If the armature is burnt, over compressed air. Cover the inlet heated or short circuited, and outlet flanges of cooling coil rewind it as per with strip of cover plate and manufacturer's instructions. gasket so that water may not n If armature is in good enter into cooling coil. Immerse in water tank for 24 hours and condition apply a coat of air drying varnish on the wash with compressed water jet winding. at 12kg./cm. sq. pressure. Remove all suspended material n Check the commutator on fins and clean the cooling coil. surface. If the surface is found (as per RDSO SMI No. improper, skim the RDSO/AC/SMI/8 commutator surface. n The cleaning process shall be n Check the under cut between supplemented by scrubbing with segments. If it is found brush and use of compressed shallow under cut the mica to water jet. the required depth. Chamfer the edges of the segments. n After cleaning the cooling coil pressurize with compressed air at n Check the bearing with the 300 psi (21kg./sq.cm) and help of shock pulse meter. In immerse in water tank duly case of compressor and connecting a pressure gauge to condenser motors, replace by detect any leakage by air bubble new ones on condition basis, method. Also see if the pressure otherwise after cleaning and drops. Leaks in pipe shall be greasing re-use it. In case of detected and brazed. evaporator motor 100%, bearings shall be changed. n Clean the Evaporator housing and paint it. Assemble the cleaned n Check the field winding by unit. resistance measurement method for open circuit and n Take out main and auxiliary drip trays from the bottom of the short circuit. evaporator unit, disconnecting the n Check the insulation of field drain pipe connection. Check for coil with the help of 500 Volt free flow of water through drip megger. It shall be more than drainpipe by admitting water on 1 mega ohm. Replace the the drip tray. Replace the hose field coil, if defective. If field pipes and hose clips by new ones. winding is in good condition apply a coat of air drying varnish on the windings. Chapter 8 – Page 16 of 28 Maintenance Manual for BG coaches of ICF design Air Conditioned Coaches n Check the brush boxes and vi. Control Panel studs for rigidity, clean the n Completely isolate the panel rocker assembly. from the power supply and n Replace the carbon brushes its loads, Contacts of the and clean the brushes using contactors (12, 13, 13A, 29 sand paper of size 400 grade and 17) shall be removed and or by using brush seating cleaned by means of clean rag stone until the faces of socked in petrol. Any brushes make perfect contact contacts, which are burnt, on commutator surface. Blow should be replaced, after out the carbon dust using dry which they should be lightly air jet. covered with vaseline. n After assembly conduct the n Similarly, dismantle the load test and insulation test. contacts of the relays and Current taken by motor clean them by means of clean should not be more than the rag socked in petrol. Any rated current. Conduct contacts which are burnt insulation test with 500v should be replaced. megger. It should be more than 1 meg ohm. n Check the flexible braided connections. If found n After the compressor/ damaged, replace the same. condenser motor is n The pin holding the pull off completely assembled spring on the armature frame- connect a milli-voltmeter work of the contactor should across brushes of opposite polarity. Connect the shunt be pulled out of its slot and the armature hinge pin field to 110V mains through a removed. This should be switch. Switch on the mains and note the kick in the examined for wear and if necessary, replaced by a new voltmeter. Rock the brush pin lightly covered with gear to the left or right and vaseline. repeat the test as before. Clamp the rocker arm in a n Measure the insulation particular position at which resistance of each relay and the kick is zero or minimum. contactor. If the insulation Before this test, care should value is less then 2 mega be taken to make sure that the ohms, replace the coil of the brushes are bedded properly. respective unit. If brushes are at neutral axis, n Check whether all the speed in both the connections are tight. If found directions of rotation will be loose, tighten the same. same. n Replace all the fuse links. n After the evaporator is completely assembled the vii. Gauge and Cut outs neutral axis can be selected by running the motor in both n Clean the contacts with the directions on no load at CTC/Petrol and test for approximately 25% of the correct operation of settings. rated voltage and measure the Calibrate with the standard speed in both the directions. gauge. If brushes are at neutral axis, n Check the performance of the the speed in both the gauges. Calibrate with the directions of rotation will be standard gauge. Replace same. defective gauges. Chapter 8 – Page 17 of 28 Maintenance Manual for BG coaches of ICF design Air Conditioned Coaches viii. Refrigerator Piping n Check IR value of the transformer with 500V n Whenever the AC equipment megger. It shall be minimum are removed from the one mega ohms. refrigeration system for the n Check the gasket for sealing purpose of overhauling the the front cover provided for pipe outlets should be closed proofing. immediately to prevent entry of any foreign material into n Check the diodes and the piping system. adhesion with heat sink. Clean the base and heat sink n After reconnecting all the AC and tightened diode as per equipment, pressure test and manufacturers guide line. vacuum test shall be performed before charging x. Fans the refrigerant. n Dismantle the lower guard, ix. Pre-Cooling Transformer & upper guard, blade and fan Rectifier Unit motor. n Check the guard assembly, n Open the cover and clean repair/replace if necessary. externally with compressed air. n Check the blade angle with a measuring gauge. Correct the n Dismantle the unit as per same, if necessary. manufacturer's instructions. n Check the insulation resistance of the fan motor. n Remove and clean the The IR value should not be contacts by means of a clean less than 2 mega ohms as rag soaked in petrol. specified in IS: 6680-1992. Contacts, which are burnt shall be replaced and covered n Check the fan leads and change it if necessary. with petroleum jelly. n Check the armature winding n Clean the transformer, and field coil, repair/replace, rectifier and rotary switch if necessary. (RSW). Check for operation n Check the commutator for and, if defective, change it. grooving, pitting marks, Checking shall be done as per ovulity, blackness etc. Skim following activities: or polish the commutator as n Check proper functioning required. of indication lamp. n Check the carbon brush and n Check all protective brush spring. Replace by circuit and fuses etc. correct grade of carbon brush n Ensure that earthing of as recommended by RDSO. housing is intact at two The fan spring should meet points. the requirements given in IS:6680. Replace the same if n Check for any crack/aging necessary. in PVC cable. Replace if required. n Apply air drying insulating varnish if IR value of the n Check the voltage armature and field coils is generation at RSW low, give impregnation position 1-1 and 4-4. treatment in an air circulating oven. Chapter 8 – Page 18 of 28 Maintenance Manual for BG coaches of ICF design Air Conditioned Coaches n Clean the ball bearing, check q Surface of copper sockets for noise, replace if necessary and bus bars shall be or grease it with cleaned to remove the oxide recommended grade. film from the jointing surface before making a n Testing bolted joint and shall be coated with corrosion q Check the load current resistant conducting grease at rated voltage. The of approved make to wattage of the fan prevent reformation of should not exceed the oxide film. value specified in IS- n Fire retardant PVC grommets to 6680. BS-1767 or grade 6 of IS-5831 shall be provided at all cable entry q Check the air delivery points in metallic members. of one or two fans from a batch to ascertain the n The under frame wiring if running correctness of the blade loose shall be provided in rigid angle. The value of the steel conduit. air delivery shall not be n All inspection covers shall be less than that specified opened to check the distribution in IS- 6680. boards and condition of wiring. xi. Wiring xii. Air Filter n Light fittings n For cleaning the ferrule type fresh The light fittings, reflectors, clear air and return air filters remove acrylic sheet cover, glass globe, them from frames and after holders, etc., shall be checked brushing or shaking off all loose and cleaned. Any defective part dirt immerse them in a solution of shall be replaced. Anti- theft hot water and soda (sodium arrangement for fluorescent light carbonate) approximately 6 grams fittings shall be checked as per to one litre of water. When ICF Drg. No. ICF/STD 7-6-001. thoroughly cleaned, the filter units should be rinsed in clean hot water n Coach insulation and allowed to dry. When properly dry, they should be completely Insulation resistance of the coach kept immersed in the oil shall be measured with 500 V (compressor lubricating oil) until megger. IR value will be air bubbles cease to rise. Then minimum 2 mega ohms but it remove and allow to drain for at should not be less than 1 mega least 8 hrs. before being placed in ohm under highly humid/wet service again. weather. n Replace the filter with new one in case of synthetic type filters. n Cable termination joint xiii. Cooling Tests q All cable joints shall be checked. Loose joints and n Cooling capacity test should be cables having damaged carried out by providing electrical insulation shall be compensating loads for worst replaced/repaired. All cable ambient conditions and full ends shall be properly occupancy of the coach. The screwed with crimping type duration for pre cooling of the copper sockets. coach should be between 3 to 4 hrs. Chapter 8 – Page 19 of 28 Maintenance Manual for BG coaches of ICF design Air Conditioned Coaches After the stabilization of the n Check earth leakage by two temperature of each berth (20 mm lamp method. from window and back rest and n Check refrigration system 100 mm above the berth) should be for any leakage before recorded. The variation in charging the gas. temperature on different berths n Conduct vacuum test. (For should not exceed 1 deg. C. 12 hrs.) n Conduct pressure test ( by n The cycling duty of the plant shall charging Freon 12 or CO2 be determined by recording ON gas ) and OFF time of the compressor. It n Vacuum test for 15 minutes should be between 10 to 15 cycles for dehydration of per hour. refrigeration system. n Check control panel and xiv. Additional Items for End-On- ensure that proper fuses are Generation (EOG) Coaches provided. n Check contactors, relay and n Overhaul the DG set as per switches for correct the manufacturer's sequential operation. instructions. n Ensure that time delay in operation of contactor No. n Inter-vehicle coupler, 12, 13, 13A is 2.5 sec. ratchet assembly, junction n Check heaters for correct box and connections: operation. inspect, clean and check for n Check hooter for proper over heating, solder run out, operation. replace if defective. Tighten n Start the plant and check connections as needed. condenser motor, n Measure insulation compressor motor, blower resistance value of the motor for any abnormality. circuit with 500 V megger. It n Check leakage air from should not be less than 2 doors. mega ohms. n Check oil level in compressor, the level when n Check the proper operating should be 1/2 functioning of WRA. bull's eye. n Check the proper working of xv. Final Testing of AC Coach, after capacity control solenoid POH valve. n Run the plant for four hours. n Visual inspection of each An equivalent heat load equipment for their proper (convector heater) should be fitment. kept for performance test of n Ensure that refrigerant pipes plant. are properly clamped. n If new expansion valve is provided during POH, it n Ensure all the modifications should be set properly. are complied with. n Ensure that batteries are in n Check safety chain and fully charged condition. tension rod of alternator for n Run the plants with proper fitness. dynodrive motors for 8 hrs. n Under frame cables leading at different speeds. n Ensure that both the to alternator should be alternators are sharing load properly cleaned. equally during run. If