Ensamblado de piezas PDF
Document Details
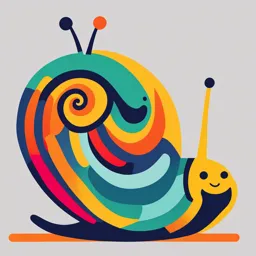
Uploaded by BestSellingSonnet
CEDE
Tags
Summary
Este documento describe diferentes tipos de uniones de piezas, enfocándose en las uniones atornilladas y remachadas. Explica conceptos previos como roscas, tipos de perfiles, número de hilos y el lugar de realización. También analiza elementos y dimensiones fundamentales de las roscas, proporcionando fórmulas y tablas para su cálculo.
Full Transcript
Ensamblado de piezas Introducción Si hablásemos de las uniones de piezas podríamos hacer dos grandes divisiones: uniones fijas y uniones desmontables. Entendemos como uniones fijas aquellas que no permiten su desmontaje sin destruir alguno de sus elementos. Por lo tanto, los ensambles soldados, rema...
Ensamblado de piezas Introducción Si hablásemos de las uniones de piezas podríamos hacer dos grandes divisiones: uniones fijas y uniones desmontables. Entendemos como uniones fijas aquellas que no permiten su desmontaje sin destruir alguno de sus elementos. Por lo tanto, los ensambles soldados, remachados, etc. están dentro de este tipo de uniones. Las uniones desmontables permiten el desmontaje y posterior montaje de las piezas que conforman el conjunto sin destruir ningún elemento. Como ejemplos podemos englobar dentro de este tipo las realizadas con tornillos, pasadores, chavetas, etc. En este tema nos centraremos en las uniones atornilladas y remachadas. Seguidamente estudiaremos las soldadas. Uniones atornilladas Antes de estudiar este tipo de ensamble debemos tener unos conocimientos previos. Conceptos previos Podemos entender una rosca como un alambre, con un perfil determinado, arrollado en forma de hélice sobre un cilindro. En realidad lo que se hace es una ranura que genera la rosca. Al material que forma la rosca se le llama filete o hilo, y la ranura que queda entre los filetes recibe el nombre de entrada. Para poder clasificar las roscas tendremos en cuenta la forma de la rosca, el número de hilos, el lugar donde está realizada y el sentido de la hélice. Forma de la rosca: según el perfil del filete podremos encontrarlos: a) Triangulares → Empleados básicamente para fijación, debido a su mayor rozamiento entre los filetes del tornillo y tuerca. b) Cuadradas o trapeciales → Las roscas trapeciales poseen un perfil de trapecio isósceles. Tanto éstas como las cuadradas se emplean para transmitir esfuerzos. Se suelen encontrar en mesas de maquinaria, sargentos de sujeción, gatos de elevación, prensas mecánicas, etc., de manera que transformen movimientos circulares en lineales. Estas formas facilitan la reversibilidad, transmitiendo la fuerza en ambos sentidos sin necesidad de aplicar un gran par de giro. c) Redondas → Se aplican cuando deben estar sometidas a grandes desgastes y en uniones rápidas para tuberías. Además de las mencionadas anteriormente, existen otras formas de filetes diseñadas para fines concretos. Número de hilos: dependiendo del número de hilos que estén realizados encontramos: 1º Roscas de una entrada (fig.1) → Son las que están compuestas de un solo filete. Se emplean en casi todos los tornillos y husillos que requieren un avance normal. 2º Roscas de varias entradas (fig.2) → Están formadas por dos o más hilos. Se utilizan cuando se requiere un avance grande. En la vida cotidiana las podemos observar en las tapas de los botes de conservas, tapones roscados de las botellas, etc. 243 Fig. 1 Rosca de una entrada. Fig. 2 Rosca de dos entradas. Lugar de realización de la rosca: Evidentemente podemos encontrar la rosca ejecutada exteriormente o interiormente, obteniendo un tornillo o tuerca respectivamente. Sentido de la hélice: Diferenciamos entre rosca a derecha o a izquierda, dependiendo de la forma en que esté generada la hélice. Tendremos una rosca a derecha cuando el tornillo avanza o aprieta al girarlo en el sentido de las agujas del reloj. Será una rosca izquierda si al girar el tornillo de la misma forma, éste retrocede o se afloja. Fig. 3 Aquí podemos observar una rosca a derecha y una rosca a izquierda. El sentido de la rosca se puede apreciar a simple vista. Si cogemos el tornillo verticalmente por su cabeza y nos fijamos en la inclinación del filete de izquierda a derecha podemos observar que esta pendiente es ascendente o descendente, así tendremos un tornillo rosca derecha o rosca izquierda respectivamente (fig.3). Elementos y dimensiones fundamentales de las roscas Como podemos observar en las figuras 4 y 5, tanto en el tornillo como en la tuerca hay valores comunes y el conocimiento de los mismos es de suma importancia. Las dimensiones fundamentales que debemos conocer son las que se muestran a continuación. Filete: se puede definir como la porción de hélice que hay en una vuelta completa. Fig.5 Dimensiones fundamentales de las roscas. D D2 D1 Vano: es el espacio vacío que se encuentra entre dos filetes consecutivos. Flancos: son las caras laterales de los filetes. H1 P Cresta: es la unión de los flancos por la parte exterior. Fondo: unión de los flancos por la parte interior. Ángulo de la rosca: corresponde al ángulo que generan dos flancos de la rosca medidos en un plano axial a la misma. Diámetro nominal: D = d Es el más importante para identificar las roscas. d d2 d1 Fig. 4 Elementos de las roscas. Flanco Izquierdo P Cresta h1 Ángulo de la rosca Flanco Derecho Vano Filete Fondo 244 Diámetro medio: D2 = d2 Se emplea básicamente para verificar los tornillos. Corresponde al diámetro tomado en la altura media del triángulo generador. Diámetro del núcleo del tornillo y de la tuerca: d1 Entendemos como núcleo el volumen ideal sobre el que se coloca la rosca. Diámetro del núcleo de la tuerca: D1 = d1 Paso: P Es la distancia existente entre dos puntos iguales de filetes consecutivos. Junto con el diámetro nominal forman las dos dimensiones fundamentales para la designación de las roscas. Avance: a Lo definimos como la distancia que recorre en sentido del eje un punto del tornillo o tuerca al dar una vuelta completa. En las roscas de un filete el avance es igual al paso: a = P En las roscas de varios filetes el avance será igual al paso multiplicado por el número de entradas a = P. z Sistemas de roscas Podemos definirlos como las clasificaciones que pueden hacerse de cada tipo de rosca normalizada. A continuación veremos los sistemas más empleados, con sus especificaciones, designaciones y medidas. Rosca Métrica ISO Antiguamente la rosca métrica poseía la cresta aplanada y la raíz redondeada, pero la norma UNE 17701:2002 define el perfil como se representa en la fig.8. Su forma es de triángulo equilátero, por lo que tiene un ángulo de 60º. Para calcular sus medidas se deben tomar como base los dos parámetros principales de la rosca, que son, como ya hemos visto, el paso “P” y el diámetro nominal de rosca “d”. Fig.7 Representación de un tornillo y tuerca de M 24. Cuando se representan unidos, el tornillo es el que se impone sobre la tuerca, es decir, los grosores de las líneas serían las correspondientes a las del tornillo. Fig. 8 TUERCA TORNILLO 245 Las fórmulas que se emplean son las siguientes: Altura del triángulo generador: H 3 P 0 ,866 P 2 Diámetro interior de la tuerca: D1 d 1 d 1,082 P Altura de contacto: H 1 5 H 0 ,541 P 8 Diámetro medio: D2 d 2 d 0 ,649 P La norma UNE 17702 establece la serie general de diámetros y pasos de roscas métricas ISO (tabla 9). Al emplear la tabla 9, que se presenta a continuación, siempre que sea posible se elegirán los diámetros correspondientes a la 1ª serie, si fuese necesario recurriríamos a la 2ª serie, y finalmente utilizaríamos los de la serie 3ª. Las roscas métricas pueden tener un paso normal, comúnmente llamado grueso, o por el contrario poseer un paso fino. Este paso fino incrementa la resistencia del tornillo en el apriete y suele ser utilizado cuando la longitud de la unión que se atornilla es pequeña. Tabla 9 Diámetros nominales Pasos 1ª Serie 2ª Serie 3ª Serie Gruesos 1 1,1 1,2 1,4 1,6 1,8 Finos 0,25 0,2 0,25 0,2 0,25 0,2 0,3 0,2 0,35 0,2 0,35 2 0,2 0,4 2,2 0,25 0,45 2,5 3 3,5 0,25 0,45 0,35 0,5 0,35 0,6 4 4,5 5 0,35 0,7 0,5 0,75 0,5 0,8 0,5 5,5 6 0,5 1 7 8 0,75 1 0,75 1,25 9 10 11 12 14 1 0,75 1,25 1 0,75 1,5 1,25 1 0,75 1,5 1 0,75 1,75 1,5 1,25 1 2 1,5 1,25 1 15 16 2 17 18 20 22 24 1 1,5 1 1,5 1 2,5 2 1,5 1 2,5 2 1,5 1 2,5 2 1,5 1 3 2 1,5 1 25 2 1,5 1 26 1,5 27 3 2 1,5 1 2 1,5 1 (3) 2 1,5 1 28 30 3,5 32 33 2 1,5 3,5 (3) 2 1,5 35 36 1,5 1,5 4 3 2 1,5 246 Tabla 10b Rosca Whitworth En la figura 10a observamos un tornillo del sistema Whitworth. Como se puede apreciar, posee un perfil triangular isósceles. El ángulo entre las caras es de 55º y los vértices interiores y exteriores están redondeados. A diferencia de la métrica, no existen huecos entre el ajuste del tornillo y la tuerca, lo que facilita la estanqueidad del conjunto. Fig. 10a TUERCA TORNILLO El cálculo de las distintas dimensiones se realiza empleando las siguientes fórmulas: Altura del triángulo generador: H 0 ,960 P Diámetros nominales in mm 1/16 '' 1,588 3/32'' 2,381 1/8'' 3,175 5/32'' 3,969 3/16'' 4,763 Pasos (Nº de hilos por pulgada) Gruesos Finos 60 48 40 32 24 32 7/32'' 5,556 24 28 1/4'' 6,350 20 26 9/32'' 7,144 - 26 5/16'' 7,938 18 22 3/8'' 9,525 16 20 7/16'' 11,113 14 18 1/2'' 12,701 12 16 9/16'' 14,288 12 16 5/8'' 11/16' ' 3/4'' 13/16' ' 7/8'' 15,876 11 14 17,463 - 14 19,051 10 12 20,638 - 12 22,226 9 11 1'' 25,401 8 10 1''1/8'' 28,576 7 9 1''1/4'' 31,751 7 9 1''3/8'' 34,926 6 8 1''1/2'' 38,101 6 8 1''5/8'' 41,277 5 8 1''3/4'' 44,452 5 7 1''7/8'' 47,627 4 - 2'' 50,802 4 7 2''1/4'' 57,152 4 6 2''1/2'' 63,502 4 6 2''3/4'' 69,853 3 6 3'' 76,203 3 5 Altura de contacto: H 1 0 ,640 P Altura del filete del tornillo y de la tuerca: h3 H 1 0 ,640 P Diámetro medio: D2 d 2 d 0 ,640 P Diámetro interior del tornillo y de la tuerca: d 3 D1 d 1,280 P Diámetro exterior de la tuerca: D d Al igual que la rosca métrica, la Whitworth puede tener paso normal o paso fino (tabla 10b). En esta tabla observamos los mismos, percatándonos de que los diámetros exteriores vienen expresados en pulgadas, y el paso en hilos por pulgada, es decir, el número de filetes que se encuentran, en 25,4mm. Rosca Whitworth Gas Es un sistema derivado del Whitworth; emplea el mismo perfil, pero con una profundidad de filete menor. Se utiliza para el roscado de tubos, ya que la menor relación entre el diámetro y la profundidad de roscado evita que éste se debilite, ofreciendo una gran estanqueidad. En la tabla 11 se indican algunas medidas de utilidad para la determinación de roscas pertenecientes a este sistema. 247 Tabla 11 Otras roscas Hasta el momento hemos visto los sistemas de roscas más empleados, y que nos podemos encontrar con mayor frecuencia. Sin embargo, existen otros muchos que pueden localizarse en elementos de máquinas y que debemos conocer: Rosca Trapecial (fig.12) Son muy empleadas en husillos de maquinaria, y siempre que sea necesario transmitir grandes esfuerzos en ambos sentidos o transformar movimientos angulares en lineales. Están normalizadas en el sistema ISO y ACME. En sustitución de este tipo de rosca nos podemos encontrar con la cuadrada. Rosca en diente de sierra (fig.13) Se utilizan para transmitir y transformar movimientos, principalmente cuando las presiones están aplicadas en un solo sentido. Esto es debido a la forma de los filetes, con flacos asimétricos. Estas roscas en diente de sierra tienen una gran aplicación en los tornillos que van a ser empleados en fijaciones sobre plásticos. Rosca Redonda (fig.14) Este tipo de perfil ofrece muy buenas propiedades mecánicas; sin embargo, es poco utilizado por la complejidad de su fabricación, lo que implica un elevado coste. Se pueden encontrar en partes de maquinaria sometidas a impactos. Rosca Edison Se utilizan en los casquillos de las bombillas y en los portalámparas. Como se observa en la figura 15, posee un perfil redondo, especialmente diseñado para ser fácilmente laminado en las chapas que posteriormente conformarán la unión roscada. Fig. 12 TUERCA TORNILLO Fig. 13 Fig. 14 Diámetro exterior de la rosca (mm) Paso (hilos por pulgada) 1/8” 9,728 28 1/4" 13,157 19 3/8” 16,662 19 1/2" 20,995 14 5/8” 22,911 14 3/4" 26,441 14 7/8” 30,201 14 1" 33,249 11 1"1/8” 37,897 11 1"1/4” 41,91 11 1"3/8” 44,323 11 1"1/2” 47,803 11 1"3/4” 53,746 11 2" 59,614 11 2"1/4” 65,71 11 2"1/2” 75,184 11 2"3/4” 81,538 11 3" 87,884 11 3"1/4” 93,98 11 3"1/2” 100,33 11 3"3/4” 106,68 11 4" 113,03 11 Diámetro nominal Fig. 15 TUERCA TUERCA TUERCA TORNILLO TORNILLO TORNILLO Designación de las roscas Evidentemente, las roscas se designan según unas normas preestablecidas. La forma de realizar esta designación en los sistemas de roscas más empleados es la siguiente: 1. La designación de las roscas comienza con una letra representativa, que indica el sistema al que pertenece (tabla 16). 2. A continuación, se indica el diámetro exterior, en milímetros para la rosca métrica y en pulgadas para la rosca Whitworth y la Unificada (se ha de tener en cuenta que el diámetro a indicar en la rosca Whitworth Gas es el del interior del tubo). 3. Seguidamente se reseña el paso de la rosca, en milímetros para la métrica y en hilos por pulgada para la Whitworth y la Unificada. Si el paso de la rosca es normal, no es necesario indicarlo; sin embargo, cuando el paso es fino obligatoriamente ha de quedar representado. 4. También se deberá marcar el sentido de giro. Cuando éste sea a izquierda, en la designación se indicará la abreviatura "LH". No se pondrá nada si el sentido de rosca es a derecha. Si posee más de una entrada se indicará con la siguiente designación: "2 ent", "3 ent", etc. Cuando en una rosca no se designe ningún parámetro de este cuarto punto, se entenderá que se trata de una rosca de avance derecho y una entrada. 248 Ejemplos: Métrica: M (diámetro exterior de la rosca en milímetros). La designación M 8 indica una rosca de diámetro exterior 8 mm y paso 1,25mm. Métrica fina: M (diámetro exterior de la rosca en milímetros) x (paso en mm). La designación M 8x1 indica una rosca de diámetro exterior 8 mm y paso 1mm. Como podemos observar, se trata de una rosca métrica de paso fino. Whitworth: W (diámetro exterior de la rosca en pulgadas). La designación W 1/2" indica una rosca de diámetro exterior 1/2" = 12,7mm y paso de 12 hilos por pulgada = 2,116mm. Whitworth fina: W (diámetro exterior de la rosca en pulgadas) x (paso en pulgadas). La designación W 1/2"x16h” indica una rosca de diámetro exterior 1/2" = 12,7mm y paso de 16 hilos por pulgada = 1,587mm. Rosca trapezoidal: Tr (diámetro exterior de la rosca) x (paso en mm). Tabla 16 Sistema de rosca Símbolo habitual Otras simbologías válidas Rosca Métrica paso normal Rosca Métrica paso fino M M SI SIF Rosca Whitworth de paso normal W BSW Rosca Whitworth de paso fino W BSF Rosca Whitworth gas (cilíndrica para tubos) G BSP Rosca Trapezoidal Métrica ISO Tr Rosca trapezoidal americana para usos generales ACME Rosca de filetes redondos Rd Rosca Edison E Rosca para tubos de conducción eléctrica Pg Rosca para bicicletas C Rosca Whitworth cónica exterior para tubos estanca R BSPT Rosca Whitworth cónica interior para tubos estanca Rc BSPT Rosca Diente de Sierra S Rosca para tubos blindados Rosca Americana Unificada p. normal Rosca Americana Unificada p. fino PG UNC UNF Pr NC, USS NF, SAE Rosca Americana Unificada p. extrafino UNEF NEF Rosca Americana Cilíndrica para tubos NPS Rosca Americana Cónica para tubos NPT ASTP Rosca Americana paso especial UNS NS Determinación del paso de una rosca Simplemente bastará con ir probando sobre la rosca distintas galgas o peines (fig. 17), hasta localizar la que coincida perfectamente con el perfil. En la figura 18 se observa la forma de comprobar el paso de una rosca. Cuando se trate de husillos, esta operación se realizará utilizando un pie de rey y midiendo la distancia entre dos puntos iguales de filetes consecutivos. Por ejemplo, de cresta a cresta (fig.19). Se comprobará el valor obtenido midiendo la distancia entre varios filetes, por ejemplo 10, y contrastando el valor obtenido. Fig. 17 Los peines son galgas para la medida de roscas que constan de hojas mecanizadas de forma precisa que cubren la gama de perfiles de rosca métrica, Whitworth o el sistema que se necesite, para una identificación rápida y segura de los pasos de rosca internos y externos. Todas las hojas están identificadas. Fig. 19 Fig. 18 Comprobación del paso de una rosca mediante un peine 249 Uniones atornilladas Estas uniones se realizan mediante elementos roscados que permiten montar y desensamblar el conjunto sin destruir ninguno de sus componentes. Nos podemos encontrar con los siguientes casos: - Tornillo pasante: Las piezas se unen entre sí por compresión mediante un tornillo pasante y una tuerca. Si observamos el detalle de la figura 20, vemos como para llevar a cabo este ensamble el tornillo debe atravesar las piezas holgadamente, sin roscar en ninguna de ellas, por lo que el agujero deberá tener un diámetro mayor que el exterior del tornillo. Finalmente se introduce la tuerca, que es ajustada convenientemente. Se acostumbra a colocar una arandela entre la tuerca y la pieza para protegerla a la hora del apriete. En definitiva, la secuencia a seguir para realizar esta unión es la siguiente: 1º Se verifica que el diámetro de las piezas es superior al del tornillo; 2º Se coloca el tornillo; 3º Por el otro extremo introducimos la arandela y la tuerca para fijar la unión. Cuando este sistema no es factible por no poder realizar el agujero pasante en las piezas, se ha de recurrir al siguiente método. Fig. 20 Tornillo pasante - Fig. 21 Tornillo de unión Tornillo de unión: Las piezas se unen entre sí por compresión mediante un tornillo de unión, el cual hace presión contra la pieza. En este caso no se emplea tuerca. En la figura 21 vemos cómo una de las piezas va provista de un agujero pasante, de diámetro superior al nominal del tornillo, mientras que la otra posee un agujero ciego roscado, que hace las veces de tuerca. Solamente la última pieza puede ir roscada, ya que si ésta se ejecutase en todas y se introdujese el tornillo, las piezas no quedarían unidas, sino que habría una pequeña separación propia de las imperfecciones que se crean al pasar de roscar una pieza a la siguiente. Por lo tanto, la unión no sería por compresión. - Espárrago o varilla roscada: Otro sistema bastante empleado y derivado del que acabamos de estudiar es el empleo de varillas roscadas o espárragos. La concepción de este método es la misma, ya que solamente irá roscada la última pieza a unir, mientras que las demás tendrán un agujero pasante de diámetro superior al de la espiga (fig.22). Una parte del espárrago va roscado en la pieza y en el otro extremo introducimos una tuerca, con lo que conseguimos la unión. Mediante este sistema se pretende proteger la zona roscada de la pieza, ya que permite desmontar el conjunto sin necesidad de sacar el espárrago, evitando por lo tanto el deterioro de la parte roscada y la rotura de los hilos, sobre todo si se trata de fundiciones, materiales quebradizos o hay poca longitud de rosca. Tanto en los espárragos como en los tornillos, para evitar este último inconveniente se aconseja que la longitud de rosca ejecutada en la pieza no sea inferior a 1,25 veces el diámetro del espárrago siempre que la pieza sea de acero, bronce o metal ligero bonificado. Para materiales ligeros o suaves se aconseja una longitud de rosca no inferior a 2,5 veces el diámetro del espárrago. 250 Fig. 22 Espárrago aprisionando dos piezas. TUERCA HEXAGONAL ARANDELA PLANA BISELADA PIEZA 1 PIEZA 2 ESPARRAGO PIEZA 3 - Tornillo prisionero Tiene como finalidad presionar el tornillo contra una pieza para producir su inmovilización (fig.23). También se emplean introduciéndolos entre dos piezas distintas para asegurar el posicionamiento de ambas y que se muevan solidariamente (fig.24). En definitiva, se trata de una varilla roscada provista de una cabeza para su apriete y una punta, que puede tener varias formas, la cual se introduce en la pieza a inmovilizar. En gran cantidad de componentes de maquinaria, después de su montaje se asegura su posición mediante estos tornillos prisioneros. También se emplean asiduamente en el ajuste y regulación de piezas, tales como guías, regletas, etc. (fig.25). Fig. 23 Fig. 24 Para montar el conjunto que vemos en esta figura se introduce el anillo en el agujero de la polea. A continuación se hacen coincidir las semi-roscas de la polea con las del casquillo y una vez situadas se introducen los tornillos prisioneros, de manera que todo el conjunto gire solidario una vez ajustado en el eje correspondiente. - Fig. 25 En este ensamble podemos apreciar dos tornillos de unión situados en los extremos. También vemos dos tornillos prisioneros que aprietan sobre una regleta que ajusta la cremallera. Tornillo guía: Tornillo guía Los tornillos guía aseguran una posición determinada permitiendo movimientos en otros sentidos. Estos tornillos no ejercen presión sobre las piezas, sino que simplemente limitan los movimientos. Normalmente impiden los desplazamientos axiales, permitiendo los giros (figs. 26 y 27), aunque se pueden encontrar diversidad de casos de guiado. Fig. 26 Detalle del ajuste de un tornillo guía. Fig. 27 Aplicación del sistema. El husillo gira y se desplaza, mientras que la pieza unida por el tornilloguía solamente se desplazará en uno u otro sentido, sin realizar ningún tipo de giro. Forma de realizar en las uniones el agujero pasante y el agujero roscado En muchas ocasiones nos encontraremos con la necesidad de realizar agujeros pasantes que serán atravesados por tornillos. Para ejecutarlos, emplearemos normalmente una broca de metal duro o de acero rápido. Como hemos visto, los agujeros deberán ser mayores que los tornillos para que éstos pasen holgadamente. La calidad de ejecución puede ser media, fina o basta y las dimensiones aconsejables para estos agujeros pasantes son los que se indican en las tablas 28 y 29. En otras ocasiones necesitaremos realizar agujeros roscados; el diámetro inicial del agujero que debe hacerse para roscar no es el diámetro del núcleo del tornillo, (obtenido en tablas o mediante cálculos teóricos), sino que será ligeramente mayor para facilitar la operación de roscado y que al introducir los machos arranquen el material con facilidad, sobre todo en materiales duros o roscas largas. Además, los materiales se dilatan y deforman, por lo que un ajuste demasiado exacto podría provocar el gripado del conjunto. Normalmente, la altura del filete suele ser de un 75% del teórico. En esta página se exponen unas tablas con los diámetros que emplearemos para realizar el roscado de los sistemas más comunes (tablas 30, 31 y 32). Seguidamente estudiaremos en profundidad las operaciones del roscado a mano, ya que es una operación básica dentro del campo del mecanizado. 251 Fig. 33 El roscado a mano (fig. 33) Esta operación consiste en la realización de una rosca en un elemento de revolución generalmente cilíndrico (tornillo) o en la periferia de un agujero (tuerca). Para explicarlo detalladamente separaremos estos dos procesos; así tendremos: Roscado de un agujero: esta operación se lleva a cabo por medio de una especie de “tornillos” llamados machos de roscar que suelen estar fabricados en acero templado de calidad (HSS) o incluso metal duro integral. Estos machos tienen a lo largo de la longitud de su cuerpo tres o cuatro ranuras (fig. 34) que son las que forman las aristas de corte y a su vez facilitan el desprendimiento y la salida del material sobrante al exterior del agujero (fig. 35). Las aristas de corte están configuradas de tal forma que tienen un pequeño destalonamiento que facilita la entrada del macho en dicho agujero. En la figura 36 podemos observar las distintas partes de las que se compone un macho. Fig. 36 Fig. 35 Fig. 34 Estos machos suelen presentarse en juegos, empleándose tres machos en el roscado de pequeños agujeros y dos cuando se incrementa su diámetro (figs. 37 y 38). Además, se deben aplicar siguiendo un orden determinado. Si nos fijamos en los machos de un mismo juego, observaremos que se diferencian en su altura de roscado, siendo este parámetro el que indique el orden de empleo para el roscado. No obstante, suelen presentar unas marcas para distinguir con facilidad la secuencia de aplicación (fig. 37). El primero es el de prerroscado, le sigue el de roscado medio, para finalizar con el de acabado. Existen juegos de cada diámetro nominal y paso (fig. 39), cuyas partes principales son las siguientes: Fig. 38 Fig. 37 Fig. 39 252 Tabla 30 Diámetro de la broca para realizar el agujero que posteriormente se roscará Diámetro nominal de la rosca en pulgadas y en milímetros Tabla 28 Tabla 29 Whitworth normal Whitworth Gas Diámetro Diámetro del agujero pasante nominal del tornillo Whitworth Acabado Acabad Acabado Fino o Medio Basto 1/16” 1,588 1,2 __ ½” 14 15 16 3/32” 2,381 1.8 — 5/8” 17 18 19 1/8” 3,175 2,6 8,9 3/4” 20 22 24 5/32” 3,969 3,1 — 7/8” 23 25 26 3/16” 4,763 3,6 — 1” 26 28 30 7/32” 5,556 4,4 — 1 1/8” 30 32 34 1 1/4” 33 35 37 1/4” 6,350 5/16” 7,938 5,1 11,9 3/8” 9,525 7,9 15,4 1/2” 12,701 10,5 19 5/8” 15,876 13,5 — 3/4” 19,051 16,5 24,7 7/8” 22,226 19,3 28,4 1” 25,401 22 30,8 1 1/8” 28,576 24,8 35,5 1 1/4” 31,751 27,8 39,4 1 3/8” 34,926 30,5 42 1 1/2” 38,101 33,5 45,4 6,5 — 1 3/8” 36 1 1/2” 38 40 1 5/8” 42 43 45 Diámetro nominal de la rosca de paso norma Diámetro de la broca para realizar el agujero que se roscará M3 45 48 1 3/4” 46 48 50 Diámetro del agujero pasante Acabado Fino Acabado Medio Acabado Basto 1 1,1 1,2 1,3 1,2 1,3 1,4 1,5 1,4 1,5 1,6 1,8 1,6 1,7 1,8 2 1,7 1,8 1,9 2,2 2 2,2 2,4 2,6 2,3 2,5 2,7 2,9 2,5 2,7 2,9 3,1 2,6 2,8 3 3,2 3 3,2 3,4 3,6 3,5 3,7 3,9 4,1 2” 52 54 58 4 4,3 4,5 4,8 2 1/4” 58 62 66 5 5,3 5,5 5,8 2 1/2” 66 70 74 6 6,4 6,6 7 78 7 7,4 7,6 8 8 8,4 9 10 10 10,5 11 12 12 13 14 15 14 15 16 17 16 17 18 19 18 19 20 21 20 21 22 24 22 23 24 26 24 25 26 28 2 3/4” 70 74 Tabla 32 Tabla 31 40 Diámetro nominal del tornillo Métrico Diámetro nominal de la rosca de paso fino Diámetro de la broca para realizar el agujero que se roscará M 3 x 0,35 2,65 27 28 30 32 2,5 M 4 x 0,5 3,5 30 31 33 35 M4 3,3 M 5 x 0,5 4,5 M5 4,2 M 6 x 0,75 5,2 33 34 36 38 M6 5 M8x1 7 36 37 39 42 M8 6,8 M10 x 1,25 8,8 39 40 42 45 M10 8,5 M12 x 1,25 10,8 42 43 45 48 M12 10,2 46 48 52 14 15,4 45 M16 M16 x 1,5 M20 17,5 M20 x 1,5 18,5 48 50 52 56 M24 x 2 22 M30 x 2 28 M36 x 3 33 M24 21 M30 26,5 M36 32 M42 37,5 M48 43 o Cuadrado de arrastre o cabeza: es la zona en la que se sujeta el bandeador (fig. 40). o Mango: es la parte cilíndrica donde aparecen grabadas las características del macho y el orden en el que se utiliza (fig. 37). o Cono de incidencia: es la parte cónica de la punta del macho; está roscada y su función es la de facilitar su penetración en el agujero. Dentro de un juego de machos, presentará mayor o menor longitud, siendo el más largo el utilizado en el prerroscado (fig. 40). o Cuerpo cilíndrico roscado: es la parte totalmente cilíndrica del macho y tienen la función de guiar la herramienta por el interior del agujero. o Acanaladuras: cada macho tiene tres o cuatro ranuras que guían la viruta sobrante hacia el exterior del agujero (fig. 34). 253 Fig.41 Bandeador Fig.40 Fig.42 Al girar una de las varillas de sujeción se ajusta progresivamente la mordaza del bandeador. Fig.43 Detalle de macho colocado en el bandeador. Los machos de roscar se sujetarán sobre los bandeadores adecuados. Un bandeador es un soporte que consta de dos varillas, una fija y otra con posibilidad de giro, que se disponen una a cada lado del cuerpo de sujeción (fig. 41). En este cuerpo se introduce la cabeza del macho, y, al girar la varilla móvil, se desplaza lateralmente una pieza que afianza el macho impidiendo que se mueva (figs. 42 y 43). Existen bandeadores de diferentes medidas dependiendo del tamaño del macho de roscar. Estas dimensiones podrán estar indicadas en el sistema métrico o en el anglosajón. Antes de comenzar la realización de un agujero roscado tendremos en cuenta una serie de consideraciones de vital importancia: 1. Determinación del diámetro del agujero: hay que tener presente que el diámetro del agujero será menor que el diámetro nominal de la tuerca, para que, al introducir los machos, estos arranquen material y se pueda generar la rosca. Por eso, lo primero que tendremos en cuenta es el tipo de rosca que se pretende ejecutar. Para determinar el diámetro del agujero a realizar se consultarán las tablas 30, 31 ó 32, pero también lo podremos calcular siguiendo el criterio que se muestra a continuación: o Si la rosca es métrica, el diámetro del agujero será: diámetro broca = Diámetro nominal tornillo – Paso o Si la rosca es whitworth: d = D – (1,28 · P); siendo “d” el diámetro de la broca, “D” el diámetro nominal o exterior del tornillo y “P” el paso. 2. Una vez determinado el valor del diámetro a taladrar, se realizará el debido agujero teniendo en cuenta si es pasante o ciego. Por último, se realizará un avellanado a 120º para evitar las rebabas y facilitar la entrada de los machos (figs. 44 y 45). 254 Fig.44 Proceso de taladrado. Fig.45 Secuencia del avellanado. Existen diferentes tipos de machos dependiendo del material a roscar, el tipo de roscado, si se realiza a mano o a máquina y el empleo que se le va a dar, es decir, si se trata de realizar una rosca nueva, o por el contrario se va a repasar una hecha con anterioridad. Por tanto, antes de comenzar, se elegirá el juego de machos más apropiado al trabajo que se va a desarrollar. El método más habitual de roscado es el manual, pero, cuando se deben realizar muchas roscas, es conveniente emplear una máquina roscadora, la cual sólo emplea un único macho para ejecutar la rosca, logrando una gran velocidad de trabajo (figs.46, 47 y 48). Estas máquinas suelen estar constituidas por una bancada provista de una mesa de trabajo. Sobre esta superficie podrá actuar un brazo articulado, con un extremo libre que incorporará un cabezal portamachos. Este cabezal siempre asegurará que el macho se encuentre totalmente perpendicular a la superficie de trabajo, independientemente de la posición relativa que ocupe el brazo articulado. Fig.46 Roscadora Fig.47 Proceso de roscado a máquina. Fig.48 Macho de roscado a máquina. Pasos a seguir para el roscado de una tuerca Para ejecutar un roscado de forma correcta, se seguirán una serie de pasos que se detallan a continuación: 1. Se prepararán todos los materiales necesarios y se sujetará firmemente la pieza donde se va a practicar el roscado; por norma general en el tornillo de banco (fig. 49). 2. En primer lugar, utilizaremos el macho que solo tiene una marca, también denominado macho de “prerroscado”. Se colocará en el bandeador adecuado y nos aseguraremos que, en todo momento, el macho entra perpendicular a la pieza a roscar (fig. 50). En un primer momento se hará presión sobre el macho a la vez que se gira, al menos dos vueltas, en el sentido del avance; con ello lograremos iniciar el corte de material. Esta primera operación es crucial para un buen roscado posterior. Seguidamente es necesario que el movimiento de giro, al progresar con el roscado, sea alternativo. Es decir, al ir arrancando viruta ésta se acumulará en el filo de corte, por lo que periódicamente giraremos el macho en sentido contrario al avance con la finalidad de romper la viruta que se va generando (fig. 51). De esta forma nos aseguraremos de que la ejecución de la rosca es correcta y evitaremos posibles desperfectos en el macho. 255 Fig.50 La posición del macho siempre ha de ser perpendicular al agujero a roscar. Fig.49 Elementos empleados en el roscado. Fig.51 Movimientos a realizar 3. Una vez concluida la operación anterior se mecanizará el agujero con el macho de roscar que tiene dos marcas, siguiendo el mismo procedimiento de trabajo. 4. En último lugar se empleará el tercer macho, que no presenta marcas de identificación. Éste último es el que finalizará la rosca, dejándola a las medidas apropiadas y concluyendo el roscado. 5. Durante todo el proceso se usará un lubricante para el roscado (fig. 52), (que en muchos casos será aceite de corte), con el fin de facilitar el arranque de viruta por parte de la herramienta. Esto también sirve para que el acabado de la rosca sea el adecuado. El orden de los machos también se puede saber por el truncamiento que presentan sus filetes. El de mayor espesor y menor altura es el primero a emplear, y el de mayor altura y menor espesor, el último (fig. 53). Fig.53 Observamos los distintos truncamientos que presentan los machos de un mismo juego. Fig.52 Detalle de macho colocado en el bandeador. Roscado de un tornillo: esta operación se basa fundamentalmente en la realización de una ranura en forma de hélice a lo largo de la longitud de un cilindro. Para ello, se empleará una herramienta llamada terraja o cojinete, que tiene forma de tuerca (fig. 54) y que se ajusta en un soporte o bandeador (figs. 55 y 56) que posibilita su manejo. Las terrajas suelen poseer cuatro o más ranuras a lo largo de su longitud, dependiendo del tamaño de la terraja (fig. 54), que, al igual que sucedía con los machos, forman las aristas de corte a la vez que facilitan el desahogo del material arrancado. Existen diferentes tipos de terrajas, dependiendo del material a roscar, del tipo de roscado y del uso para el que se vaya a ser destinado. 256 Fig.54 Terrajas de distintas dimensiones. Fig.55 Bandeadores para terrajas. Fig. 56 Forma que presentan los bandeadores. Antes de comenzar la realización de un tornillo, partiendo de una varilla, tendremos en cuenta una serie de consideraciones de vital importancia: 1. Para facilitar la correcta entrada de la terraja, se le realizará un chaflán a la varilla (fig.57). 2. Es conveniente que el diámetro de la varilla sea ligeramente más pequeño que el diámetro nominal de la rosca (tabla 58), ya que el arranque y deformación del material puede hacer recrecer el diámetro, sobre todo si se trata de aceros dulces. Fig.57 Forma que presenta la varilla con chaflán. Tabla 58 d´= diámetro de la varilla Material Tornillo Formulas para preparar la pieza en el roscado a mano Acero d´= d – 0.1 x p Blando d´= d – 0.2 x p Pasos a seguir para el roscado de una varilla: para la ejecución de un roscado de forma correcta se seguirán una serie de pasos que se explican a continuación: 1. Sujetar firmemente la pieza de manera que no se mueva. 2. Colocar la terraja en el bandeador adecuado y de forma correcta, de manera que el lado de cierre del bandeador empuje al cojinete hacia la varilla y no al revés (fig. 59a). 3. Se comienza el roscado colocando la terraja totalmente perpendicular a la varilla (fig. 59b) y se gira de tal forma que por cada media vuelta de avance se retroceda ¼ de vuelta, con el fin de facilitar el corte y el desprendimiento de la viruta hacia el exterior. 4. Ya que el rozamiento producido entre la terraja y la varilla es muy elevado, es aconsejable el uso de abundante lubricante, ya sea aceite de corte o taladrina. Fig. 59 a Terraja montada en el bandeador, apoyando por su parte posterior en el lado de cierre o tope. Fig.59 b Terraja entrando perpendicular a la varilla. 257 Fig.60 Tornillos Entendemos por tornillo una varilla roscada provista de cabeza. Sus partes principales son la cabeza, el vástago y la punta (fig.60). Pueden presentar formas muy diversas, tanto en su cabeza como en su punta; la longitud de su vástago se elige según las necesidades. Cabeza de los tornillos La cabeza de los tornillos tiene la función de adaptarse a la herramienta que va a ejercer el par de apriete necesario. No se aplica la misma fuerza con un destornillador que con una llave fija, por lo que esta cabeza será elegida en concordancia con el esfuerzo que deba soportar el tornillo. Así, las formas más habituales que podemos encontrar son las siguientes: - Tornillos con cabeza avellanada: Esta cabeza, además de tener forma avellanada, puede ser plana o abombada. La cavidad donde ajusta la herramienta recibe el nombre de huella, la cual puede ser ranurada, de estrella, pozidriv, cuadrada, allen, torx, etc. (fig.61). Estos tornillos suelen emplearse cuando se quiere que la unión quede rasante. Cuando los tornillos son avellanados con cabeza abombada se conocen por el nombre de “gota de sebo”. Fig.61 Aquí podemos ver diversos tipos de cabeza avellanada plana o abombada. Siguiendo el orden de las imágenes tenemos los avellanados de cabeza plana y abombada ranurada. En tercer y cuarto lugar vemos el de estrella y el de huella pozidriv. Finalmente tenemos el tornillo de cabeza avellanada abombada con huella torx. - Tornillos con cabeza cilíndrica o de boquilla (fig. 62): aunque los podemos encontrar en otras disposiciones, habitualmente se emplean de forma que la cabeza queda oculta, empotrada en la pieza. Fig.62 Diversos tipos de cabezas cilíndricas. - Tornillos con cabeza redondeada o abombada (fig. 63): apoyan directamente sobre la superficie, quedando el resalte de la cabeza del tornillo. Fig.63 Tornillos con cabezas redondeadas Fig.64 Tornillo con cabeza cuadrada 258 - Tornillos con cabeza cuadrada (fig.64): son poco utilizados. Los podemos encontrar en utillajes y en fijaciones de herramientas de maquinaria. Suelen utilizarse con el fin de que, al apretar la tuerca, la cabeza del tornillo se ponga en contacto con algún resalte que impida su giro. Así evitamos la posibilidad de que al girar la tuerca el tornillo también gire y se dificulte el apriete. - Tornillos de cabeza hexagonal: son los más empleados en cuestiones de fijación, bien sean como tornillos pasantes o de unión. Debido a la forma de su cabeza, permiten pares de apriete grandes, por lo que generan fijaciones seguras. Dependiendo de su forma tendremos tornillos de cabeza hexagonal (fig.65) o tornillos de cabeza hexagonal con brida (fig.66), que además hacen la función de arandela. Fig.65 - Fig.66 Tornillos con cabezas especiales: junto con las anteriores, podemos encontrar un sinfín de formas y tipos que se adaptan a distintas funciones. A continuación, se exponen algunas de estas terminaciones (fig. 67): Fig.67 Por orden vemos: un tornillo estriado o moleteado, un tornillo de ala o mariposa, ambos para apriete manual. A continuación, observamos un perno de cabeza de seta y caña cuadrada, de forma que una vez ajustado su forma cuadrada impide su giro. Finalmente tenemos dos pernos o cáncamos usados habitualmente para el amarre o sujeción de diversos tipos de cargas. - Tornillos de ajuste: Además de las formas exteriores de la cabeza, podemos encontrar tornillos sin cabeza, es decir, con cavidades dentro de la espiga roscada (fig.68). Se emplean sobre todo como tornillos prisioneros o de ajuste. Punta de los tornillos: Igual que existen diversas configuraciones de la cabeza, la forma de la punta de los tornillos también puede adquirir varias formas según las necesidades. Las más usuales son las que aparecen en la figura 69. 259 Fig.69 Fig.70 TORNILLO CABEZA HEXAGONAL (Rosca parcial) Norma: UNE EN 4014 Designación de los tornillos Las dimensiones fundamentales de los tornillos de cabeza hexagonal son las que se muestran en la figura 70. d M-2 M-2,5 M-3 M-4 M-5 M-6 M-8 M-10 M-12 M-14 M-16 M-18 k 1,4 1,7 2 2,8 3,5 4 5,3 6,4 7,5 8,8 10 11,5 12,5 e 4,32 5,45 6,01 7,66 8,79 11,05 14,38 18,9 21,1 24,49 26,75 30,14 33,53 s l 4 5 5,5 7 8 10 13 17 19 22 24 27 30 5 X X X 6 X X X X X 8 X X X X X X 10 X X X X X X X 12 X X X X X X X 14 X X X X X X X 16 X X X X X X X X X X X X X 18 20 X X M-20 X X X X X X X X X X X 22 X X X X X 25 X X X X X X X X 30 X X X X X X X X X X 35 X X X X X X X X X X 40 X X X X X X X X X X 45 X X X X X X X X X X 50 X X X X X X X X X X X X X X X X X X X X X X X X X X X X X X X X X X X X X X X X X X X X X X X X X X X X X X X X X 90 X X X X X X X X 100 X X X X X X X X 55 60 X X 65 70 X 75 80 X La designación de los tornillos tiene dos partes fundamentales: 1ª parte → Consta de la denominación del objeto. Los tornillos se suelen caracterizar por el tipo de cabeza que presentan, por lo que éste será su calificativo principal. 2ª parte → Está compuesta de los siguientes apartados: sistema de rosca que tiene, longitud de su vástago, norma específica, tipo de ejecución y características mecánicas o resistencia. 260 Seguidamente, se expone un ejemplo que clarifica la forma de realizar las designaciones: Ejemplo: Tornillo cabeza hexagonal M 10 x 1,5 x 70 UNE-EN 4017 g 5.8 La primera parte define el tipo de tornillo; Tornillo cabeza hexagonal = Denominación o nombre. Después se designa la rosca, la longitud del vástago, la norma que los define, el tipo de ejecución y finalmente la resistencia o características mecánicas: - M10 x 1,5 = Designación de la rosca; 70 = Longitud del vástago; UNE-EN-ISO 4017 = La norma que especifica el tornillo; g = Ejecución gruesa; 5.8 = Clase de resistencia o características mecánicas. Cuando la rosca sea a izquierda, deberemos indicarlo en su designación mediante las letras “LH”. En ocasiones nos encontraremos con la necesidad de emplear tornillos que no sean de acero. En este caso, en su designación aparecerán las iniciales del material con el que están realizados, informándonos de la resistencia del mismo. Algunas otras normas relativas a tornillos son: UNE-EN-ISO 4762:1998. Tornillo de cabeza redonda y hexágono interior. UNE-EN-ISO 2009:1995. Tornillo de cabeza avellanada. UNE-EN-ISO 1207:1995. Tornillo con ranura y cabeza cilíndrica. Resistencia del material de los tornillos Acabamos de ver cómo se designan los tornillos y hemos tenido en cuenta como último parámetro la resistencia de los mismos. Si nos fijamos con más detalle, observamos que consta de dos números separados por un punto. En el caso anterior “5.8”. La norma ISO 898 establece unas calidades de acero para los tornillos, así diremos que, si sometemos a tracción el tornillo hasta su fractura, obtenemos una tensión última o máxima del tornillo, empleando la nomenclatura de la norma diremos: f ub N mm 2. Si ese valor lo dividimos entre cien, resulta el primer dígito de esa designación. Por lo tanto, ese número lo podríamos definir como la centésima parte de la tensión de tracción capaz de romper el tornillo, expresada en N/mm2. f ub F S0 Si estudiamos la relación entre la tensión donde el material empieza a fluir y la necesaria para obtener la rotura del material por tracción Valor nominal del límite elástico f yb , obtenemos un valor que, al multiplicarlo por diez, Resistencia última a tracción f ub nos da la segunda cifra de la designación. En definitiva, este valor nos indicará la “plasticidad” que presenta el material y además, con él podremos obtener el límite elástico del tornillo f yb multiplicar la resistencia a la rotura 6 y 9. Ejemplo: f ub N mm 2 , ya que se obtendrá de por la décima parte de ese segundo número. Este valor suele oscilar entre Un tornillo que tenga en su designación los valores de 5.8, nos indicaría lo siguiente; f ub N , de donde f ub 5 100 500 de tensión nominal de rotura por tracción. 100 mm 2 → Segunda cifra: calculándolo analíticamente diremos que f yb f ub 0 ,1 8 500 0.8 400 N 2 mm → Primera cifra: 5 En muchos tornillos, estos valores vienen troquelados en su cabeza (fig. 71), aunque en algunas ocasiones encontraremos unas marcas (fig. 72) que nos indicarán su resistencia. También se da el caso que en algunos elementos roscados no aparezca esta indicación. 261 Fig.71 Vemos varias cabezas de tornillos, entre ellos uno de cabeza hexagonal, con dureza 8.8, de rosca métrica ISO. Comparándolo con un tornillo de iguales dimensiones pero realizado en acero dulce, vemos que posee una mayor resistencia a la tracción (mínima de 80kgf/mm2), que permite emplear menor número de fijaciones o de menor diámetro y, cuando se aprieta correctamente, la capacidad de soportar mayores impactos, golpes y vibraciones. Símbolos Fig.72 Resistencias que implican 8.8 9.8 10.9 12.9 En los tornillos con rosca a izquierda de dimensiones superiores a 5mm, aparecerá grabada la letra “L”, que nos informará sobre su sentido de roscado. Las tuercas también pueden venir marcadas indicando su resistencia. Cuando así sea, sobre ellas aparecerá indicado el primer número que veíamos en la resistencia de los tornillos (fig. 73 a), es decir, el que corresponde a la décima parte de la resistencia mínima a la tracción. También podemos encontrar en vez del número, una serie de marcas (fig. 73 b) que nos informarán de su resistencia. Fig.73 a Fig.73 b Marcas Resistencias que implican 8 10 12 14 Tuercas En muchos casos, para completar las uniones son necesarias las tuercas. Sus formas exteriores pueden ser variadas y en su centro hay un agujero roscado, por el cual se introduce el tornillo. Para que el ensamble pueda ser efectivo, tanto el tornillo como la tuerca deben de pertenecer al mismo sistema de roscas y poseer el mismo paso. A continuación, vemos los tipos de tuercas más usuales. Las tuercas más empleadas en sistemas de fijación, al igual que los tornillos, son las hexagonales. Básicamente se diferencian entre las normales y las rebajadas (fig.74). Estas últimas se utilizan normalmente como contratuercas. De igual manera podemos encontrar tuercas hexagonales con bridas (fig.75). Todas ellas suelen tener los vértices achaflanados y un avellanado en la rosca para facilitar el acoplamiento. Fig.74 Fig.75 262 Podemos también hablar de las tuercas hexagonales ciegas, con remate en forma de cúpula o normal (fig.76). Se utilizan cuando han de ser vistas y las terminaciones de la unión deben presentar un buen acabado. Fig.76 Fig.77 Fig.78 Si se requiere una unión de seguridad, se puede emplear una tuerca hexagonal almenada (fig.77), que, unida a un pasador, asegura el acoplamiento, impidiendo que se pueda aflojar por vibraciones u otros motivos. En ciertos mecanismos y sobre todo en carpintería son muy utilizadas las tuercas cuadradas (fig. 78), cuya forma, una vez ajustadas e introducidas en su alojamiento, impide el giro de las mismas. En muchas máquinas también encontraremos tuercas redondeadas (fig. 79). Se aprietan con llaves de gancho, de pitones o especiales y sirven para asegurar husillos mediante tuerca y contratuerca, para regular ejes o ajustar rodamientos. Fig.79 En esta figura se observa: tuerca con agujeros, ranurada y con agujeros frontales. Fig.80 A continuación vemos una tuerca de cáncamo, una redonda moleteada y una tuerca de mariposa o de ala. Finalmente estudiamos las tuercas de ajuste manual (fig. 80). Evidentemente están diseñadas para ofrecer una buena manipulación y la presión de apriete que se desarrolla es menor que con las anteriores. Designación de las tuercas La designación de las tuercas es similar a la de los tornillos. Comenzaremos por definir el tipo de tuerca, a continuación, indicaremos el paso, seguido de la norma que la define, el tipo de ejecución y finalmente la resistencia, anotando la primera cifra de ésta. Ejemplo: Tuerca hexagonal M 10 x 1,5 UNE-EN 4032 g 5 Las dimensiones fundamentales de las tuercas de cabeza hexagonal son las que se muestran en la figura y en la tabla 81. Fig.81 TUERCA HEXAGONAL Norma: UNE EN 4032 Algunas otras normas relativas a las tuercas son: UNE-EN-ISO 4032:2001. Tuercas hexagonales, tipo 1. UNE-EN-ISO 4033:2001. Tuercas hexagonales, tipo 2. DIN 935. Tuercas almenadas. 263 Tabla 81 s e M-1,6 d 3,2 3,48 1,3 m M-2 4 4,38 1,6 M-2,5 5 5,45 2 M-3 5,5 6,01 2,4 M-3,5 6 6,58 2,8 M-4 7 7,66 3,2 M-5 8 8,79 4 M-6 10 11,05 5 M-7 11 12,12 5,5 M-8 13 14,38 6,5 M-10 17 18,9 8 M-12 19 21,1 10 M-14 22 24,49 11 M-16 24 26,75 13 M-18 27 29,56 15 M-20 30 32,95 16 M-22 32 35,03 18 M-24 36 39,55 19 M-27 41 45,2 22 M-30 46 50,85 24 M-33 50 55,37 26 M-36 55 60,79 29 M-39 60 66,44 31 M-42 65 72,09 34 M-45 70 76,95 36 M-48 75 82,6 38 M-52 80 88,25 42 Arandelas Las arandelas son discos de pequeño espesor con un orificio practicado generalmente en su centro. Se emplean para: proteger las superficies de apriete, sobre todo cuando los montajes y desmontajes son muy repetitivos; soportar la fuerza que se genera en el ajuste; asegurar el cierre hermético de una junta o como elementos de seguridad para impedir que se afloje el tornillo o la tuerca. Las arandelas normalmente se fabrican de metal, aunque se pueden encontrar de plástico u otros materiales. Dependiendo de la fuerza de apriete se utilizarán unas u otras. Si quisiéramos hacer una clasificación de las arandelas podríamos dividirlas en: 1- Arandelas de protección. Suelen presentar forma cilíndrica recta o biselada 2- Arandelas de seguridad. Al interponerlas entre el elemento roscado y la pieza, se genera una presión constante en el tornillo o la tuerca, por lo que se asegura la fuerza de apriete del conjunto, evitando aflojamientos involuntarios, aunque el conjunto esté sometido a vibraciones que pudiesen aflojar la unión. También existen las que generan el bloqueo de la unión doblando una pestaña de la arandela contra la pieza y la tuerca. Los tipos de arandelas más utilizadas son las que se exponen a continuación: Arandelas Planas. Presentan una forma cilíndrica. También podemos encontrar arandelas planas con reborde ancho (fig. 82). Fig.82 A la izquierda observamos una arandela convencional y a la derecha una de reborde ancho. Arandelas Grower. Como podemos ver en la figura 83, se trata de un anillo abierto y deformado en forma de espiral. Dispone de una sección cuadrada y hay una diferencia axial o paso, entre el inicio y el fin de la arandela, igual al espesor de la misma. Se utiliza habitualmente en maquinaria, automoción, etc. Arandelas dentadas. Pueden encontrarse con dentado externo (fig. 84) y con dentado interno (fig.85). Este tipo de arandelas también se puede definir como elásticas o de seguridad, ya que al emplearlas la unión es resistente a las vibraciones. Consiste en una serie de dientes interiores, exteriores o en forma cónica (fig.85a). Al apretar el tornillo o la tuerca, los vértices del dentado se deforman e incrustan en los cuerpos adyacentes a ella, evitando el giro y asegurando la unión. Figs. 84 y 85 Arandela con dentado externo y con dentado interno. Fig.83 Arandela Grower y aplicación. Arandela Grower Fig. 85a Formas habituales de arandelas dentadas d1 d2 Forma "A" d2 d2 d1 d1 Forma "J" 264 Forma "V" Arandela ondulada (fig. 86). Ofrece una gran resistencia cuando se encuentra bajo compresión. Al igual que las de dentado, son resistentes a las vibraciones, pero tienen la ventaja de no dañar ni marcar las superficies de las piezas entre las que se interpone. Cuando se emplean en acero inoxidable son adecuadas para la mayoría de las aplicaciones de alimentación, médicas, químicas, electrónicas y de la construcción. Arandela antivibraciones (fig. 87). Este tipo de arandelas de seguridad se han diseñado para impedir que se aflojen los conjuntos de tornillos debido a la vibración. Cuando se emplean por parejas, las excéntricas anguladas situadas sobre las superficies acopladas hacen que las arandelas se expandan más que el paso de la rosca, con el resultado de una mayor carga previa en el fijador y su bloqueo en la junta. Trabajan a cualquier frecuencia/amplitud (golpes o carga constante) El bloqueo no se ve afectado por la temper atura o los lubricantes. Son reutilizables. Fig.86 Arandela Ondulada. Arandelas de solapa (fig. 88). En su constitución, la podríamos comparar con una arandela convencional, pero cabe destacar una solapa que presentan con el fin de doblarse sobre una arista de la pieza una vez apretados el tornillo y la tuerca. De esta forma logramos un bloqueo firme y seguro. También podemos encontrarlas con dos solapas o con pestaña. s Fig.87 Arandela Antivibraciones y forma de aplicación. Fig.88 En estas imágenes vemos, sucesivamente una arandela con pestaña; en el centro, con dos pestañas y finalmente una arandela con solapa. s d2 d1 d2 d1 b s l1 b l1 l2 d2 d1 Arandela de cierre o de retención (fig. 89). Debemos conocer este tipo de arandelas ya que son muy empleadas en aquellos mecanismos que emplean tuercas ranuradas. Habitualmente las veremos en los rodamientos. Su forma de trabajar es sencilla; una vez ajustada la tuerca contra la arandela, se doblará la pestaña coincidente con la ranura de la tuerca. De esta forma logramos establecer una unión segura evitando que se afloje. Fig.89 Arandela de cierre y su aplicación en la fijación de un rodamiento. Arandela de retención Tuerca ranurada 265 Como hemos visto, casi todas las arandelas que proporcionan seguridad a la unión se basan en la fuerza generada por una deformación elástica. Las tuercas o tornillos se aflojan cuando no están sometidos a presión, ya que el rozamiento entre los filetes disminuye y esto facilita el desajuste. Para impedirlo podemos emplear estas arandelas que aseguran los tornillos mediante la aplicación de una presión constante o por la deformación plástica de alguna de sus superficies. Arandela plana 5 UNE-EN 7089 Designación de las arandelas d1 d2 h 1,7 4 0,3 2 2,2 5 0,3 2,5 2,7 6,5 0,5 3 3,2 7 0,5 3,5 3,7 8 0,5 4 4,3 9 0,8 5 5,3 10 1 6 6,4 12 1,6 7 7,4 14 1,6 8 8,4 16 1,6 10 10,5 20 2 12 13 24 2,5 Sistemas de seguridad en los tornillos 14 15 28 2,5 16 17 30 3 Como hemos visto, muchos elementos de unión deben asegurar la posición que ocupan una vez apretados, impidiendo su aflojamiento aun cuando estén sometidos a vibraciones o golpes. La seguridad se consigue por medio de alguno de los siguientes métodos: 18 19 34 3 20 21 37 3 22 23 39 3 24 25 44 4 27 28 50 4 30 31 56 4 33 34 60 5 36 37 66 5 39 40 72 6 42 43 78 7 45 46 85 7 48 50 92 8 50 52 92 8 52 54 98 8 h M 1,6 d2 Como establecen las normas, la designación se realiza indicando el tipo de arandela, seguido del diámetro nominal del tornillo o tuerca donde se van a ajustar. Lógicamente, el diámetro interior de la arandela es ligeramente superior al nominal del tornillo para que pueda introducirse en el mismo fácilmente. Por ejemplo, una arandela plana para un tornillo de métrica 5, poseerá un diámetro interior de 5,3 mm. Finalmente, la designación se completa con la norma que la define. d1 Ejemplo: Una arandela de tipo plano que se va a emplear en un tornillo de métrica 5, se designará de la siguiente forma: 1. Mediante una doble tuerca, también denominado tuerca – contratuerca Se utiliza en numerosas aplicaciones. Para ello se emplean dos tuercas, normalmente una más estrecha que la otra, que hace la función de contratuerca. Al presionarse entre ellas, se generan unas fuerzas como se representa en la figura 90. Se establece así un rozamiento entre los flancos superiores de la tuerca y los contrarios de la contratuerca, de manera que se genera una presión continua, que asegura la unión y evita que se afloje el tornillo. Para desmontarlo, primero debemos eliminar la fuerza ejercida entre tuerca y contratuerca, por lo que procederemos a aflojar la contratuerca superior para después liberar la tuerca y el tornillo. Fig. 90 Sistema tuerca – contratuerca. CONTRATUERCA TUERCA ARANDELA PIEZA 266 Fig.91 2. Mediante tuercas autoblocantes (fig. 91) Su fijación se consigue gracias a un anillo de nylon relleno de vidrio. Una vez ajustados no se aflojan o sueltan por causa de las vibraciones, por lo que se elimina el empleo de tuercas adicionales. Este tipo de tuercas es reutilizable y su anillo no daña las roscas de los tornillos donde son colocadas. Son resistentes al agua, al aceite, etc., por lo que pueden emplearse en un gran número de aplicaciones. De igual manera, suelen usarse en un amplio margen de temperaturas, desde -70°C a +200°C. 3. Mediante arandelas de seguridad Existen diversos tipos de arandelas que pueden definirse como arandelas de seguridad, ya que su fin es asegurar el correcto apriete de los tornillos o tuercas. 4. Mediante bloqueo mecánico En este apartado veremos dos tipos de fijación. Uno muy habitual consiste en emplear una tuerca almenada que, mediante la acción de un pasador introducido en las ranuras de la tuerca, logra un bloqueo seguro (figs. 92). Otra fijación de seguridad se puede lograr mediante la colocación de un tornillo entre los elementos roscados, es decir, la tuerca y el tornillo de fijación (fig. 93). Este sistema es muy empleado, no solo entre tuercas y tornillos, sino entre elementos que deban estar unidos asegurando un giro o impidiendo el movimiento relativo entre ambos. Figs. 92 Fig.93 TUERCA ALMENADA Tornillo de fijación Tornillo que asegura la unión Tuerca de fijación PASADOR DE ALETA Montaje y desmontaje de tornillos, tuercas y arandelas Evidentemente, en su montaje y desmontaje se deberán tener ciertas consideraciones. Las roscas estarán en perfecto estado, ya que cualquier golpe o rebaba dificultaría enormemente la unión. La arandela suele intercalarse entre el elemento que se girará y la pieza fija para ajustar el conjunto. Normalmente será la tuerca, pero cuando se trate de tornillos de unión, se habrá de colocar entre éste y la pieza a sujetar. La utilización de aceite o lubricante facilita considerablemente estas labores de montaje y desmontaje. Cuando realicemos una unión mediante tornillos y tuercas, normalmente van a aparecer las fuerzas que se indican en la figura 94. Si no apretásemos el conjunto, el tornillo se comportaría como un pasador o un remache, y todo el esfuerzo sería de cortadura en la sección del tornillo correspondiente a la unión de las dos piezas. Si por el contrario se afianza el conjunto, el Fig.94 tornillo comienza a trabajar a tracción con una fuerza de pretensado. Debido a este apriete, también aparecerá en el tornillo un esfuerzo de torsión, por lo que, en ocasiones, una vez apretada la tuerca, se gira ligeramente en sentido contrario (aproximadamente 10º), con el fin de liberar estos esfuerzos perjudiciales. Una vez concluida esta operación se dice que el tornillo está pretensado y, por lo tanto, el sistema puede empezar a trabajar. 267 Fig.95 Es muy importante aplicar el momento de apriete adecuado, tanto para los tornillos como las tuercas. Se prestará especial atención a la fuerza ejercida en el apriete, ya que si es excesiva podemos producir el cizallamiento del tornillo. En la tabla 96 se muestran las tensiones de apriete aproximadas. Marca de referencia Si es necesario un apriete predeterminado, la forma de realizarlo será mediante una llave dinamométrica y deberá efectuarse de forma continua, sin interrupción, hasta llegar al valor del momento. Para realizar una comprobación del momento de apriete se realizarán los siguientes pasos: en primer lugar, se marcará una señal que una el tornillo o tuerca con su base de apoyo. Esta marca nos servirá como referencia o guía. A continuación, procederemos a aflojar el conjunto para posteriormente volver a ajustarlo suavemente mediante una llave dinamométrica, hasta que coincidan las señales. En ese punto se verificará el valor del momento de apriete (fig. 95). Tabla 96 Valores orientativos de fuerzas y pares de apriete. Calidad - 4.6 TIPO DE LLAVE Cabeza hexagonal exterior M Calidad - 5.6 Allen F [N] M [Nm] F [N] M [Nm] 1.5 Calidad - 6.9 F [N] M [Nm] Calidad - 8.8 Calidad - 10.9 F [N] M [Nm] F [N] M [Nm] 2 4 284 0.12 378 0.16 731 0.31 863 0.37 1216 0.52 M 2.3 4.5 407 0.20 544 0.27 1049 0.51 1245 0.60 1755 0.84 M 2.6 5 525 0.28 701 0.37 1353 0.73 1598 0.86 2246 1.21 3 5.5 726 0.44 966 0.59 1863 1.13 2206 1.34 3109 1.88 3.5 6 971 0.68 1294 0.90 2501 1.74 2962 2.06 4168 2.89 M 4 7 3 1255 1.00 1677 1.34 3226 2.60 3825 3.04 5374 4.32 M 5 7, 8, 9 4 2059 1.96 2736 2.65 5286 5.10 6257 6.03 8806 8.48 M 6 8, 10 5 2903 3.43 3864 4.51 7543 8.73 8836 10.30 12405 14.71 M 7 11 6 4236 5.59 5649 7.45 10885 14.22 12945 17.16 18191 24.52 M 8 10, 13 6 5315 8.24 7090 10.79 13680 21.58 16230 25.50 22751 35.30 M 10 13, 15, 17 8 8473 16.67 11278 21.58 21771 42.17 25791 50.01 36284 70.61 M 12 15, 18, 19, 21 10 12356 28.44 16475 38.25 31773 73.55 37657 87.28 52956 122.60 M 14 22, 23, 24 12 12965 45.11 22653 60.80 43639 116.70 51681 138.30 72667 194.20 M 16 21, 24, 26 14 23340 69.63 31087 93.16 60016 178.50 71196 210.80 100027 299.10 M 18 27 14 28341 95.12 37853 127.50 72961 245.50 86494 289.30 121602 411.90 M 20 27, 30, 34 17 36481 135.3 48641 180.45 93849 384.10 111305 411.90 156415 578.60 M 22 32, 34, 36, 41 17 45601 182.4 60801 245.16 117189 470.70 139254 559.00 195642 784.50 M 24 36, 41 19 52563 230.5 70019 308.91 135331 598.20 160338 711.00 225552 1000.00 M 27 41, 46 19 69235 343.2 92280 460.90 177990 887.50 210842 1049.00 296159 1481.00 M 30 46, 50 22 84043 465.8 112286 622.72 215745 1206.00 255952 1422.00 359902 2010.00 M 33 50, 55 24 104931 632.5 139744 848.30 269682 1628.00 319695 1932.00 449142 2716.00 M 36 55, 60 27 123073 814.00 164261 1089.00 316753 2099.00 374612 2481.00 527595 3491.00 M M 2.5 Uniones remachadas Conceptos previos Entendemos por roblonado o remachado la unión fija de dos elementos utilizando un roblón o remache. Antiguamente este procedimiento estaba muy extendido, sin embargo, su uso ha disminuido, aunque se sigue empleando en ciertas aplicaciones que veremos a lo largo del tema. Forma y materiales de los roblones o remaches Siguiendo un criterio general de estudio, podemos decir que los remaches ordinarios están formados por un vástago cilíndrico en cuyo extremo presenta una cabeza de forma semiesférica. En el otro extremo del vástago, durante su montaje, se realizará la conformación de otra cabeza (figs. 97 y 98). 268 Fig. 97 Fig. 98 Fig. 99 Si nos fijamos en la forma de la cabeza, podremos diferenciar cuatro tipos (fig. 99): remache de cabeza esférica; remache de cabeza esférica para construcciones estancas; remache de cabeza avellanada; remache de cabeza avellanada abombada. El material comúnmente empleado es el acero dulce, es decir, con poco contenido de carbono. Esta característica favorece el conformado, ya que el material se deforma y adapta fácilmente al aplicarle los golpes. Podríamos decir que este tipo de material es fácilmente maleable. Cuando se trata de remaches de pequeño tamaño, es decir, inferior a 12 mm de diámetro, las operaciones de unión se hacen en frío. Cuando el diámetro es superior, estas operaciones se realizan con el roblón previamente calentado. A esta operación se le llama caldeo. Independientemente de lo comentado, en ciertas aplicaciones también podemos encontrar remaches de aluminio, cobre, etc. Formas de remachado El remachado puede realizarse manualmente o con máquinas que aplican la fuerza necesaria para el conformado del remache. Aunque esta operación se realice de forma manual o automática, debemos conocer las disposiciones de los elementos que unen y el fin que se persigue con la unión. Si tenemos en cuenta la forma de colocación de las piezas a unir tendremos las siguientes posiciones: 1. 2. 3. Por recubrimiento (fig. 100) Por simple cubrejunta (fig. 101) Por doble cubrejunta (fig. 102) En todos estos ensambles la colocación de los remaches puede hacerse en una o varias filas, según las cargas que deban de soportar. Fig. 100 Fig. 101 Fig. 102 Si estudiamos la finalidad de la unión, nos podemos encontrar con los siguientes casos: 1. Los roblones deben soportar un esfuerzo dado, por lo que servirán como elementos de fuerza. Un ejemplo lo vemos en muchas construcciones antiguas de estructuras metálicas, como los puentes del ferrocarril. Incluso la Torre Eiffel está construida con estos elementos de unión. 2. La unión, además de soportar un pequeño esfuerzo, debe asegurar una estanqueidad. Como ejemplo tenemos los cofres de baterías, cuya tapa se roblona asegurando un cierre perfecto. 269 3. En ciertas instalaciones encontraremos elementos remachados que, además de asegurar la estanqueidad, deben soportar un esfuerzo considerable. Esto lo vemos en calderas o depósitos a presión. Para realizar el remachado de forma manual, además del martillo debemos disponer de tres herramientas esenciales: la sufridera, el asentador y la buterola. La manera de proceder es la siguiente (fig. 103): Una vez que tenemos preparados los elementos a unir, con sus correspondientes orificios, se introducen los roblones, caldeándolos previamente si fuese necesario. A continuación, se coloca la sufridera y se realiza el asiento de todas las piezas. Para ello se emplea el asentador. Una vez hecho esto, se aplican golpes de martillo para darle forma a la cabeza. Cuando el remache no es muy grande suele emplearse la bola del martillo. Para concluir la unión se utiliza la buterola que al aplicarle golpes hace que el material se sigua deformando para adoptar la forma que ésta posee. Si la unión tuviese que asegurar la estanqueidad se realizaría la última operación que recibe el nombre de calafateado. Fig. 103 Se puede dar el caso de unir una chapa fina mediante un remache. Para ello se suele practicar un avellanado en la pieza inferior, de forma que la propia chapa se deforme al introducir el remache y su cabeza no sobresalga (fig. 104). A este sistema se le suele llamar remache embutido. Fig. 104 Evidentemente, antes de realizar estas operaciones debemos conocer ciertas dimensiones, como pueden ser las de los agujeros que se realizarán en las piezas y la de los remaches que se emplearán. El diámetro del agujero donde se introducirá el remache siempre ha de ser superior al de éste. Esto implicará una fácil colocación y que exista cierta holgura entre el remache y los elementos a unir. Al proceder al remachado, la presión que se le aplica al roblón hace que se deforme por compresión y empiece a adquirir forma de tonel, para progresivamente ir rellenando todas las holguras y formalizar, de esta forma, la unión. También deberá existir un sobrante de material por el extremo opuesto a la cabeza, de manera que pueda generarse la otra cabeza aplicando golpes en ese extremo. (fig. 105) Para saber, de forma aproximada, las dimensiones del remache y del agujero se aplicarán las siguientes fórmulas: Fig. 105 Dimensiones Diámetro del remache “d” en función del espesor de las chapas a unir: d 1,5 e 4 Diámetro donde se aloja el remache “D” es: D 1,05 d 270 Habitualmente se realiza el agujero entre uno y dos milímetros mayor que el diámetro del remache. El material sobrante para remachar “S” será aproximadamente: Para remaches redondeados: Para remaches embutidos: S 1,5 d S 0 ,6 d Remaches especiales Además de los remaches convencionales que acabamos de estudiar, existen otros tipos más evolucionados y utilizados frecuentemente en un sinfín de aplicaciones. Los más habituales son los que se detallan a continuación: Remache hueco: Este tipo de remaches consta de dos partes bien diferenciadas: el cuerpo y el vástago. Su cuerpo suele ser de aluminio y el vástago de acero, aunque también existen íntegramente de acero, de acero inoxidable o incluso de cobre. Su funcionamiento se basa en la deformación que provoca en el cuerpo un vástago que es traccionado por la remachadora (fig. 106). Fig. 106 Aunque en esencia todos los remaches de estas características son semejantes, podemos diferenciar varios tipos: - Remaches estándar (fig. 107): tienen numerosas aplicaciones en mantenimiento y producción. Son capaces de remachar metal o cualquier tipo de material laminado. Se suministran varios tamaños, dependiendo de su diámetro y de la longitud de su cuerpo. - Remaches de ala ancha (fig. 108): se emplean principalmente para unir piezas de materiales blandos debido a la mayor superficie de apoyo que presentan, la cual distribuye las presiones y permite afianzar materiales como, por ejemplo, el plástico, la tela, etc. - Remaches estancos; principalmente empleados en procesos de montaje que deben contener líquidos o gases. Su constitución evita las filtraciones o fugas una vez remachados. - Remaches avellanados (fig. 109): presentan en su cuerpo un resalte avellanado, mediante el que se obtiene una superficie plana una vez terminado el ensamble. - Remaches de flor: al ir aplicando progresivamente la presión se abren cuatro pétalos en el cuerpo del remache, deformándose ampliamente y obteniendo una mayor superficie de apoyo posterior. - Remaches inoxidables: este material los hace óptimos para ser aplicados en la industria de la alimentación o de la medicina. 271 Fig. 107 Fig. 108 Fig. 109 Para aplicar todos estos remaches es necesaria una remachadora, existiendo diversos modelos, ya que podrán ser desde manuales (fig. 110), hasta neumáticas, que consiguen una gran rapidez de trabajo. Fig. 110 Tuercas remachables (fig. 111): Fig.111 Son muy prácticas y de rápida aplicación. Proporcionan un medio simple pero efectivo para fijar casquillos roscados a materiales de pequeño espesor. Ofrecen elevadas resistencias y suelen aplicarse donde el espesor reducido no permite un roscado directo. También son muy útiles para emplearlas en piezas tubulares. Las tuercas para remache son adecuadas para su fijación a acero dulce, acero inoxidable, aluminio en láminas, etc., con un margen de espesor del material de 0,5 a 3,25mm Se suelen encontrar en radiadores, electrodomésticos, etc. Su aplicación se realizará de la siguiente manera (fig. 112 a y b): En primer lugar, introduciremos la tuerca en el orificio ejecutado a tal efecto. A continuación, roscaremos el mandril coincidente con la rosca de la tuerca. Éste irá fijado por su parte posterior a la remachadora. Después se realizará el remachado de la tuerca, obteniendo una deformación de la misma y un aprisionamiento. Finalmente retiraremos la remachadora y el mandril. Fig. 112 a Fig. 112 b Juego de tuercas remachables y remachadora. 272