Basic Pneumatics PDF - 9/4/2024
Document Details
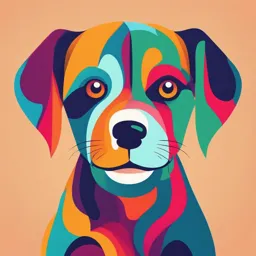
Uploaded by AmplePlot
2024
Sanjay Humania
Tags
Summary
This presentation covers fundamental concepts of pneumatics, including definitions, components, and applications. The presentation, titled Basic Pneumatics, was created on 9/4/2024 by Sanjay Humania, an M.Tech in Mechatronics, and provides a general overview of pneumatics for an engineering audience.
Full Transcript
Basic Pneumatics Sanjay Humania [M.Tech - Mechatronics] 9/4/2024 1 Introduction to pneumatics During the few decades various automation techniques has been introduced in the field of manufacturing in order to enhance the overall industrial productivity. ...
Basic Pneumatics Sanjay Humania [M.Tech - Mechatronics] 9/4/2024 1 Introduction to pneumatics During the few decades various automation techniques has been introduced in the field of manufacturing in order to enhance the overall industrial productivity. Among the various technologies that are playing important role in rapid growth of industries, fluid power is unique. During past decade number of applications have been developed based on Pneumatics. Sanjay Humania [M.Tech - Mechatronics] 9/4/2024 2 Pneumatics - Definition The study of pneumatics deals with system operation with air or gaseous medium to impart power or to control power. The term pneumatics is derived from the Greek word pneuma, meaning wind or breath. Pneumatic power is the power that is transmitted by pressurized/compressed air. Compressed Normal Air Compressor Control valve Actuator Air Sanjay Humania [M.Tech - Mechatronics] 9/4/2024 3 A simple pneumatic system Composition of Atmospheric air Dry air at sea level comprises 78.03% nitrogen, 20.99% oxygen, 0.98% argon by volume. It also contains traces of carbon dioxide, hydrogen, neon, helium, krypton and xenon. Apart from gases, atmospheric air holds many harmful impurities like dust, etc. Air has a mass & exert pressure on the surface of the earth. Atmospheric pressure at normal sea level is 1.013bar. Sanjay Humania [M.Tech - Mechatronics] 9/4/2024 4 Air pressure F Force [F] is applied to the air enclosed in a chamber through a piston of area [A]. The enclosed air is compressed and its pressure [P] raised in directly proportional to the applied force and inverse proportional to the area of the piston. P=F/A Sanjay Humania [M.Tech - Mechatronics] 9/4/2024 5 Unit of pressure In SI system unit of pressure is Pascal (Pa), & 1 Pa is constant pressure acting on surface area of 1 square meter with a perpendicular force of 1 Newton. 1Pa = 1N/m^2 For industrial pneumatic purpose, Pascal is to small unit for use in measurement & hence a more practical unit, called ‘bar’ is used. 100,000 Pa = 1 bar 14.5 psi (Pound per inch) = 1 bar Sanjay Humania [M.Tech - Mechatronics] 9/4/2024 6 Pneumatic applications Some industrial applications General applications: employing pneumatics are listed below: – Packaging – Filling General methods of material handling: – Metering – Clamping – Locking – Shifting – Driving of axes – Positioning – Door control – Orienting – Transfer of materials – Branching of material flow – Turning and inverting of parts – Sorting of parts – Stacking of components – Stamping and embossing of components Sanjay Humania [M.Tech - Mechatronics] 9/4/2024 7 Pneumatic applications Points switch for two conveyor belts Pneumatic cutter Sanjay Humania [M.Tech - Mechatronics] 9/4/2024 8 Standardization For a uniform definition & standardization of pneumatic components were initiated by German organization like VDI & VDMA. This led to DIN & CETOP & later to DIN ISO standards & recommendations for a uniform consistent terminology in pneumatics. System engineer must draw pneumatic circuit that installation engineer & maintenance person can read & understand easily. Therefore standardization was required. Sanjay Humania [M.Tech - Mechatronics] 9/4/2024 9 Standardization CETOP : Comité Européen des Transmissions Oléohydrauliques et Pneumatiques is a federation of European manufacturing, which is involved, since 1962. DIN : Deutsches Institute fur Normung E.V. VDI : Verin Deutscher Ingenieure (Association of German Engineers) VDMA : Verband Deutscher Maschinen und Anlagenbau (Association of Mechanical Engineers) Sanjay Humania [M.Tech - Mechatronics] 9/4/2024 10 Some pneumatic standards ISO 1219-1 2006 : fluid power system & component – Graphic symbols & circuit diagram. ISO 5599 : Port marking of pneumatic direction control valve. ISO 6432, 6431 : Mounting dimension of pneumatic cylinders. CETOP RP41 : Hydraulic & Pneumatic system circuit diagram. And many more… Sanjay Humania [M.Tech - Mechatronics] 9/4/2024 11 Compressed Air Generation & Contamination Control Sanjay Humania [M.Tech - Mechatronics] 9/4/2024 12 A typical pneumatic system Sanjay Humania [M.Tech - Mechatronics] 9/4/2024 13 Air generation and distribution The generation of compressed air starts Inlet filter with compression. Air compressor The compressed air flows through an entire Air reservoir series of components Air dryer before reaching the Air filter with water consuming device. separator The equipment to be Pressure regulator considered in the generation and Air lubricator as preparation of air required include : Drainage points Sanjay Humania [M.Tech - Mechatronics] 9/4/2024 14 Intake filter It is used to clean & filter the air used for systems. Before the surrounding air enters the compressor, it must pass through a filter to remove most of the dirt & other solid contaminants. These filters can be of dry or wet type depending on the compressor manufacturer & the application. Sanjay Humania [M.Tech - Mechatronics] 9/4/2024 15 Air compressors A compressor is the most common industrial energy supply unit that convert mechanical energy into fluid energy. It is design to take in air at atmospheric pressure and deliver the received air to a closed system with a certain volumetric flow rate, at a higher pressure. Sanjay Humania [M.Tech - Mechatronics] 9/4/2024 16 Reciprocating piston compressors A piston compresses the air drawn in via an inlet valve. The air is passed on via an outlet valve. Reciprocating compressors are very common and provide a wide range of pressures and delivery rates. For higher pressures multistage compression is used with inter-cooling between each stage of compression. Sanjay Humania [M.Tech - Mechatronics] 9/4/2024 17 Reciprocating piston compressors A reciprocating compressor consist of the crankshaft by a connecting rod. Crankshaft is externally rotate by a electric motor. Crankshaft & connecting rod convert rotary motion into reciprocating motion. Sanjay Humania [M.Tech - Mechatronics] 9/4/2024 18 Flow compressor These are particularly suitable for large delivery quantities. Flow compressors are made in axial or radial form. The air is made to flow by means of one or several turbine wheels. The kinetic energy is converted into pressure energy. In the case of an axial compressor, the air is accelerated in the axial direction of flow by means of blades. Sanjay Humania [M.Tech - Mechatronics] 9/4/2024 19 Reservoirs A reservoir is configured downstream of a compressor to stabilise compressed air. A reservoir compensates the pressure fluctuations when the compressed air is taken from the system. If the pressure in the reservoir drops below a certain value, the compressor will compensate until the set higher value is reached again. This has the advantage that the compressor does not need to operate continuously. Sanjay Humania [M.Tech - Mechatronics] 9/4/2024 20 Reservoirs Sanjay Humania [M.Tech - Mechatronics] 9/4/2024 21 Air dryers The most common type of dryer today is the refrigeration dryer. With refrigerated drying, the compressed air is passed through a heat exchanger system through which a refrigerant flows. The aim is to reduce the temperature of the air to a dew point which ensures that the water in the air condenses and drops out in the quantity required. Sanjay Humania [M.Tech - Mechatronics] 9/4/2024 22 Sanjay Humania [M.Tech - Mechatronics] 9/4/2024 23 Compressed air filter The selection of the correct filter plays an important role in determining the quality and performance of the working system which is to be supplied with compressed air. One characteristic of compressed-air filters is the pore size. The pore size of the filter element indicates the minimum particle size which can be filtered out of the compressed air. Sanjay Humania [M.Tech - Mechatronics] 9/4/2024 24 Compressed air filter Sanjay Humania [M.Tech - Mechatronics] 9/4/2024 25 Lubricator As a rule the compressed air which is generated should be dry, i.e. free of oil. For some components lubricated air is damaging, for others, it is undesirable, but for power components it may in certain cases be necessary. Lubrication of the compressed air should therefore always be limited to the plant sections which require lubrication. For this purpose, lubricators are fitted to feed the compressed air with specially selected oils. Oils which are introduced into the air from the compressor are suitable for the lubrication of control system components. Sanjay Humania [M.Tech - Mechatronics] 9/4/2024 26 Sanjay Humania [M.Tech - Mechatronics] 9/4/2024 27 Service unit The individual functions of compressed air preparation, i.e. filtering, lubricating and regulating , can be fulfilled by individual components. These functions have often been combined into one unit, i.e. the service unit or FLR. Service units are connected upstream of all pneumatic systems. Sanjay Humania [M.Tech - Mechatronics] 9/4/2024 28 Service unit Pressure gauge Air filter Pressure control valve Sanjay Humania [M.Tech - Mechatronics] 9/4/2024 29 Service unit Sanjay Humania [M.Tech - Mechatronics] 9/4/2024 30 Sanjay Humania [M.Tech - Mechatronics] 9/4/2024 31 Actuators Sanjay Humania [M.Tech - Mechatronics] 9/4/2024 32 Actuators and output devices An actuator is an output device for the conversion of supply energy into useful work. The output signal is controlled by the control system, and the actuator responds to the control signals via the control element. Other types of output devices are used to indicate the status of the control system or actuators, e.g. a pneumatically actuated visual display. Sanjay Humania [M.Tech - Mechatronics] 9/4/2024 33 Actuators and output devices The pneumatic actuator can be described under two groups, linear and rotary : Linear motion Single-acting cylinders Double-acting cylinders Rotary motion Air motor Semi-Rotary actuator Sanjay Humania [M.Tech - Mechatronics] 9/4/2024 34 Single-acting cylinders With single-acting cylinders compressed air is applied on only one side of the piston face. The other side is open to atmosphere. The cylinder can produce work in only one direction. The return movement of the piston is effected by a built-in spring or by the application of an external force. The spring force of the built-in spring is designed to return the piston to its start position with a reasonably high speed under no load conditions. Sanjay Humania [M.Tech - Mechatronics] 9/4/2024 35 Single-acting cylinders Spring to push Spring to pull Sanjay Humania [M.Tech - Mechatronics] 9/4/2024 36 Plunger type single acting cylinder In the case of plunger cylinders, the piston and rod form a single component. Due to the design of the cylinder, the return stroke can only be effected by external forces. The cylinders can therefore generally be installed only vertically. Sanjay Humania [M.Tech - Mechatronics] 9/4/2024 37 Double-acting cylinders The construction principle of a double-acting cylinder is similar to that of the single-acting cylinder. But no return spring, and the two ports are used alternatively as supply and exhaust ports. The double-acting cylinder has the advantage that the cylinder is able to carry out work in both directions of motion. The force transferred by the piston rod is somewhat greater for the forward stroke than for the return stroke as the effective piston surface is reduced on the piston rod side by the cross-sectional area of the piston rod. Sanjay Humania [M.Tech - Mechatronics] 9/4/2024 38 Double-acting cylinders Sanjay Humania [M.Tech - Mechatronics] 9/4/2024 39 Double-acting cylinder with cushioning If large masses are moved by a cylinder, cushioning is used in the end positions to prevent sudden damaging impacts. Before reaching the end position, a cushioning piston interrupts the direct flow path of the air to the outside. Instead a very small and often adjustable exhaust aperture is open. For the last part of the stroke the cylinder speed is progressively reduced. If the passage adjustment is too small, the cylinder may not reach the end position due to the blockage of air. Sanjay Humania [M.Tech - Mechatronics] 9/4/2024 40 Double-acting cylinder with cushioning Sanjay Humania [M.Tech - Mechatronics] 9/4/2024 41 Tandem double-acting cylinder The tandem cylinder incorporates the features of two double-acting cylinders which have been joined to form a single unit. By this arrangement and with the simultaneous loading of both pistons, the force on the piston rod is almost doubled. This design is suitable for such applications where a large force is required but the cylinder diameter is restricted. Sanjay Humania [M.Tech - Mechatronics] 9/4/2024 42 Tandem double-acting cylinder Sanjay Humania [M.Tech - Mechatronics] 9/4/2024 43 Cylinders with through piston rod This cylinder has a piston rod on both sides, which is a through piston rod. The guide of the piston rod is better, as there are two bearing points. The force is identical in both directions of movement. The through piston rod can be hollow, in which case it can be used to conduct various media, such as compressed air. A vacuum connection is also possible. Sanjay Humania [M.Tech - Mechatronics] 9/4/2024 44 Cylinders with through piston rod Sanjay Humania [M.Tech - Mechatronics] 9/4/2024 45 Multi-position cylinders The multi-position cylinder consists of two or several double-acting cylinders, which are interconnected. The individual cylinders advance when pressure is applied. In the case of two cylinders with different stroke lengths, four positions are obtained. Sanjay Humania [M.Tech - Mechatronics] 9/4/2024 46 Multi-position cylinders Sanjay Humania [M.Tech - Mechatronics] 9/4/2024 47 Multi-position cylinders Sanjay Humania [M.Tech - Mechatronics] 9/4/2024 48 Rotary cylinders With this design of double-acting cylinder, the piston rod has a geartooth profile. The piston rod drives a gear wheel, and a rotary movement results from a linear movement. The range of rotation varies from 45o, 90o, 180o, 270oto 360o. The torque is dependent on pressure, piston surface and gear ratio; values of roughly up to 150 Nm are possible. Sanjay Humania [M.Tech - Mechatronics] 9/4/2024 49 Rotary cylinders Sanjay Humania [M.Tech - Mechatronics] 9/4/2024 50 Diaphragm cylinder This is the simplest form of single acting cylinder. In diaphragm cylinder , piston is replaced by a diaphragm is replaced by a diaphragm of hard rubber, plastic or metal clamped between the two halves of a metal casing expanded to form a wide, flat enclosure. The operating stem which takes place of the piston rod in diaphragm cylinder can also be designed as a surface element so as to act directly as a clamping surface for example. Only short operating strokes can be executed by a diaphragm cylinder, up to a maximum of 50 mm. This makes the diaphragm type of cylinder particularly adaptable to clamping operations. Return stroke is accomplished by a spring built into the assembly or by the tension of diaphragm itself in the case of very short stroke. Diaphragm cylinders are used for short stoke application like clamping, riveting, lifting, embossing and riveting Sanjay Humania [M.Tech - Mechatronics] 9/4/2024 51 Diaphragm cylinder Sanjay Humania [M.Tech - Mechatronics] 9/4/2024 52 Cylinder construction The cylinder consists of a cylinder barrel, bearing and end cap, piston with seal (double-cup packing), piston rod, bearing bush, scraper ring, connecting parts and seals. The cylinder barrel (1) The end cap (2) The bearing cap (3) The piston rod (4) Sealing ring (5) Bearing bush (6) In front of this bearing bush is a scraper ring (7). Sanjay Humania [M.Tech - Mechatronics] 9/4/2024 53 Air Motors Devices which transform pneumatic energy into mechanical rotary movement with the possibility of continuous motion are known as pneumatic motors. The pneumatic motor with unlimited angle of rotation has become one of the most widely used working elements operating on compressed air. Pneumatic motors are categorised according to design: Piston motors Sliding-vane motors Gear motors Turbines (high flow) Sanjay Humania [M.Tech - Mechatronics] 9/4/2024 54 Air Motors Sanjay Humania [M.Tech - Mechatronics] 9/4/2024 55 Semi rotary actuator The limited angle rotary actuator is applied when the shaft has to rotate over a limited angle. The animation shows how this simple actuator works: in this case the shaft can rotate over an angle of about 270 degrees. This type of actuator is, among others, used as a rotator actuator on (small) cranes and excavators Sanjay Humania [M.Tech - Mechatronics] 9/4/2024 56 Semi rotary actuator Sanjay Humania [M.Tech - Mechatronics] 9/4/2024 57 Pneumatic grippers Handling equipment must have grippers for picking up, moving and releasing the workpiece. Grippers establish either a force-locking or a positive-locking connection with the part. All gripper types have a double-acting piston drive and are self-centring. Contactless position sensing is possible with proximity sensors. External gripper fingers make the grippers suitable for a wide variety of applications. Sanjay Humania [M.Tech - Mechatronics] 9/4/2024 58 Pneumatic grippers Pneumatic grippers a) Radial grippers b) Parallel grippers c) 3-point grippers d) Angle grippers Sanjay Humania [M.Tech - Mechatronics] 9/4/2024 59 Vacuum generators Handling with suction cups is generally a simple, low- cost and reliable solution. Suction cups allow the handling of different workpieces with weights ranging from a few grams right up to several hundred kilograms. They come in a wide variety of different shapes, such as universal, flat or bellows suction cups, for example. Sanjay Humania [M.Tech - Mechatronics] 9/4/2024 60 Vacuum generators & Sucker Sanjay Humania [M.Tech - Mechatronics] 9/4/2024 61 Sanjay Humania [M.Tech - Mechatronics] 9/4/2024 62 Sanjay Humania [M.Tech - Mechatronics] 9/4/2024 63 Pneumatic Valves Sanjay Humania [M.Tech - Mechatronics] 9/4/2024 64 Pneumatic Valves Valve is a device which is used to control out put of the circuit. The main purpose of a valve in pneumatics or hydraulic circuit is to control Final output. Valves are divided into number of groups according to what they control. Sanjay Humania [M.Tech - Mechatronics] 9/4/2024 65 Classification of Valves Function Example: DCV, FCV, PCV. Design Example: Spool valve, poppet valve. Method of actuation Manual, mechanical, pneumatic, electric. Mounting angle Manifold, in line, sub plate. Application Speed control, signal processing, proportional valve. Sanjay Humania [M.Tech - Mechatronics] 9/4/2024 66 Functional Classification of Valves Most commonly used valves are. Direction control valve (DCV). Non return valves. Pressure control valve (PCV). Flow control valve (FCV). Sanjay Humania [M.Tech - Mechatronics] 9/4/2024 67 Direction control valves Control valve symbols – The basic symbol for control valve is a square. Two or more squares are used. Each square representing the switching position provided by the valve. Two position valve. Three position valve. Sanjay Humania [M.Tech - Mechatronics] 9/4/2024 68 Graphical representation Lines in the boxes are used to show flow path with arrow indicating direction of flow. FLOW The shut off position is indicated by the line drawn at right angle to the horizontal line inside the rectangle. SHUT OFF / NO FLOW Sanjay Humania [M.Tech - Mechatronics] 9/4/2024 69 Graphical representation PIPE CONNECTIONS The pipe connections i.e. inlet and outlet ports to the valve are indicated by lines drawn on outside of the box and right angle to the horizontal line. The first position from left indicates the rest, initial or neutral position when the valve is not actuated. The second position or square from left indicates actuated position. Sanjay Humania [M.Tech - Mechatronics] 9/4/2024 70 Graphical representation PIPE CONNECTIONS Single position (initial) Two position valve Three position valve Sanjay Humania [M.Tech - Mechatronics] 9/4/2024 71 Graphical representation PORT & POSITIONS TABLE: The ports of the valve are show on the outside of the box. These are labeled by a number or letter according to its functions. For this purpose some standard letters or numbers with symbols are used which are shown in the following table. Sanjay Humania [M.Tech - Mechatronics] 9/4/2024 72 Graphical representation PORT & POSITIONS TABLE: Port Alphabetic system No. sys. Comment Pressure port P 1 Supply port Working port A 2 3/2 DC valve Working ports A, B 4, 2 4/2 or 5/2 DC valve Exhaust port R 3 3/2 DC valve Exhaust ports R, E,S 3, 5 3/2 DC valve Pilot port Z or Y 12 Pilot line (1 2) Pilot port Z 14 Pilot line (1 4) Pilot port Z or Y 10 Pilot line (flow closed) Internal pilot port Pz, Py 81, 91 Auxiliary pilot air Sanjay Humania [M.Tech - Mechatronics] 9/4/2024 73 COMMONLY USED DIRECTION CONTROL VALVE. D.C. valve is used to control or to change the direction or to start or stop the fluid flow only on the receipt of any signal which may be mechanical, electrical or a fluid pressure pilot signal. D.C. valves are described by number of ports and number of positions n / n way valve ( n = 1, 2, 3,……) Sanjay Humania [M.Tech - Mechatronics] 9/4/2024 74 COMMONLY USED DIRECTION CONTROL VALVE. Way Valve Ports Positions 2/2 2 (1 input , 1 output) 2 3/2 3 (1 input, 1 output, 1 exhaust) 2 4/2 4 (1 input, 2 output, 1 exhaust) 2 5/2 5 (1 input, 2 output, 2 exhaust) 2 Sanjay Humania [M.Tech - Mechatronics] 9/4/2024 75 Ports and positions (ways) Sanjay Humania [M.Tech - Mechatronics] 9/4/2024 76 2/2 way valve 2 (A) 1 (P) 2/2 way Normally closed valve Initially no flow from1 to 2, switched to flow from 1 to 2. figure indicates 2/2 way valve normally closed and that when activated connects pressure port (1) to the output port (2) and therefore it is used for ON/OFF switch. Sanjay Humania [M.Tech - Mechatronics] 9/4/2024 77 2 (A) 2/2 way valve 1 (P) 2/2 way Normally opened valves Initially flow from 1 to 2. Switched to no flow from 1to2. figure shows 2/2 way valve normally opened with the pressure port (1) connected to the output port (2) when activated it close both the ports and it is also used for ON/OFF switch. Sanjay Humania [M.Tech - Mechatronics] 9/4/2024 78 3/2 way valve 2 3/2 way normally closed valve 1 3 Initially no flow from 1to 2 but flow from 2 to 3 switched to flow from 1 to 2 and 3 closed. Figure shows 3/2 way valve normally closed in which pressure port 1 is off and output port (2) exhausting via exhaust port (3). when it is activated the pressure is applied to the output port directly and the exhaust port will be closed. Sanjay Humania [M.Tech - Mechatronics] 9/4/2024 79 2 3/2 way valve 1 3 3/2 way normally opened valve– Initially flow from 1 to 2 and 3 closed, switched to flow from 2 to 3 and no flow from 1. figure indicates 3/2 way valve normally opened in which pressure is connected to the output port and exhaust port is closed. When activated pressure port (1) is off and output port (2) exhaust via exhaust port (3). Sanjay Humania [M.Tech - Mechatronics] 9/4/2024 80 4 2 4/2 way valve 1 3 4/2 way valve Initially flow from 1 to 2 and 4 to 3.switched to flow or from 1 to 4 and from 2 to 3. A 4/2 way valve is shown in figure in which pressure is applied to the output port while the output port exhaust through the exhaust port. When activated the pressure port (1) is connected to the output port (4) while output port (2) exhaust through the exhaust port (3). Sanjay Humania [M.Tech - Mechatronics] 9/4/2024 81 4 2 5/2 way valve 5 3 5/2 way valve 1 Initially flow from 1 to 2 and flow 4 to 5, 3 closed. Switched to flow from 1 to 4 and from 2 to 3, 5 closed. Figure indicates 5/2 way valve in which pressure is applied to the output port while output port exhaust through the exhaust port. When activated pressure (1) is connected to the output port (4) exhaust through exhaust port (5) 3 will be closed. Sanjay Humania [M.Tech - Mechatronics] 9/4/2024 82 Methods of actuation Sanjay Humania [M.Tech - Mechatronics] 9/4/2024 83 Methods of actuation Sanjay Humania [M.Tech - Mechatronics] 9/4/2024 84 Methods of actuation Sanjay Humania [M.Tech - Mechatronics] 9/4/2024 85 3/2 way valve 2 2 1 3 1 3 Push button operated spring returned Push button operated spring returned 3/2 way normally closed valve 3/2 way normally open valve Sanjay Humania [M.Tech - Mechatronics] 9/4/2024 86 3/2 way valve Internal construction of a 3/2 way normally closed valve Sanjay Humania [M.Tech - Mechatronics] 9/4/2024 87 Striking switch 2 1 3 striking switch 3/2 way normally closed valve 9/4/2024 Sanjay Humania [M.Tech - Mechatronics] 88 3/2 way valve Internal construction of a 3/2 way normally open valve Sanjay Humania [M.Tech - Mechatronics] 9/4/2024 89 3/2 way valve 2 2 1 3 1 3 Roller operated spring returned Roller operated spring returned 3/2 way normally closed valve 3/2 way normally open valve Sanjay Humania [M.Tech - Mechatronics] 9/4/2024 90 3/2 way roller operated valve Internal construction of a roller operated 3/2 way NC valve Sanjay Humania [M.Tech - Mechatronics] 9/4/2024 91 3/2 way Idle return roller operated spring returned 2 1 3 Idle return roller operated spring returned 3/2 way normally Closed valve Sanjay Humania [M.Tech - Mechatronics] 9/4/2024 92 Pneumatically operated spring returned 2 2 12 12 1 3 1 3 Pneumatically operated Pneumatically operated spring returned spring returned 3/2 way normally closed valve 3/2 way normally open valve (3/2[M.Tech Sanjay Humania way- Mechatronics] single pilot) (3/2 way single93 pilot) 9/4/2024 Pneumatically operated spring returned Internal construction of a 3/2 way single pilot valve NC Sanjay Humania [M.Tech - Mechatronics] 9/4/2024 94 4/2 BOTH SIDE PILOT OPERATED VALVE MEMORY VALVE 14 12 Pneumatically operated Spring returned 5/2 way valve (5/2 way single pilot) Sanjay Humania [M.Tech - Mechatronics] 9/4/2024 95 4/2 SINGLE SIDE PILOT OPERETED SPRING TO RETURN 14 Pneumatically operated Spring returned 4/2 way valve (4/2 way single pilot) Sanjay Humania [M.Tech - Mechatronics] 9/4/2024 96 Pneumatically operated Spring returned 4 2 14 5 3 1 Pneumatically operated Spring returned 5/2 way valve Sanjay Humania [M.Tech - Mechatronics] 9/4/2024 97 (5/2 way single pilot) Push button operated Spring returned 4 2 5 3 1 striking switch 5/2 way valve Sanjay Humania [M.Tech - Mechatronics] 9/4/2024 98 Both pneumatically operated valve 5/2 way valve 4 2 14 12 5 3 1 Pneumatically operated pneumatically return 5/2 way valve (5/2 way double pilot valve / memory valve) Sanjay Humania [M.Tech - Mechatronics] 9/4/2024 99 5/2 way double pilot valve 5/2 way double pilot valve with longitudinal slide Sanjay Humania [M.Tech - Mechatronics] 9/4/2024 100 Shutoff valves Sanjay Humania [M.Tech - Mechatronics] 9/4/2024 101 Non return valve Sanjay Humania [M.Tech - Mechatronics] 9/4/2024 102 Pilot operated check valve Sanjay Humania [M.Tech - Mechatronics] 9/4/2024 103 Two pressure valve Sanjay Humania [M.Tech - Mechatronics] 9/4/2024 104 Shuttle valve Sanjay Humania [M.Tech - Mechatronics] 9/4/2024 105 Flow control valves Sanjay Humania [M.Tech - Mechatronics] 9/4/2024 106 Throttle valve Sanjay Humania [M.Tech - Mechatronics] 9/4/2024 107 One way flow control valve Sanjay Humania [M.Tech - Mechatronics] 9/4/2024 108