EET227W24 - Lecture on Pneumatic Control Devices PDF
Document Details
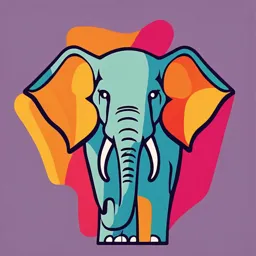
Uploaded by SkillfulStarlitSky9380
Centennial College
Tags
Summary
This lecture covers ISO and ANSI symbols used for pneumatic control devices, including schematic directional valves, valve actions, valve actuators, and their various combinations, like 2/2, 3/2 valves, and more. The document also explains different types of actuators, such as spring, solenoid, manual, and pilot actuators, and details about the logic operations in pneumatic systems, including parallel and series connections. The lecture notes also cover topics such as automatic return stroke and oscillating movement.
Full Transcript
EET-227 Instrumentation 2 School of Engineering Technology & Applied Science (SETAS) LECTURE: 3 ISO and ANSI symbols used for pneumatic control devices. 1 Objectives Review Symbo...
EET-227 Instrumentation 2 School of Engineering Technology & Applied Science (SETAS) LECTURE: 3 ISO and ANSI symbols used for pneumatic control devices. 1 Objectives Review Symbols for : ï‚§ Schematic Directional Valves ï‚§ Valve Actions ï‚§ Valve Actuators 2 A family of graphic symbols has been developed to represent fluid power components and systems on schematic drawings. In the United States, the American National Standards Institute (ANSI) is responsible for symbol information. The Institute controls the make-up of symbols and makes changes or additions as required. The International Standards Organization (ISO) has the same control over symbols used internationally. Both systems have almost the same format 3 Schematic Symbols for Directional Valves The development of pneumatic systems is assisted by a uniform approach to the representation of the elements and the circuits. The symbols used for the individual elements must display the following characteristics: ï‚§ Actuation and return methods ï‚§ Number of connections ï‚§ Number of switching positions. ï‚§ General operating principle. ï‚§ Simplified representation of the flow path. 4 The ANSI symbol for directional valves are the most complicated of all the fluid power symbols, but some of the most important. A typical directional valve symbol is made up of three parts: LEFT VALVE RIGHT ACTUADOR ACTION ACTUATOR The actuators are the devices or methods that cause the valve to shift from one position to another. 5 The valve action refers to the combinations of positions and flow paths which the valve offers. Position Boxes Every valve provides two or more usable positions, each position providing one or more flow paths. For example, the single solenoid spring return valve provides two usable positions: ï‚§ One position occurring when the solenoid is in command of the valve, ï‚§ The other position occurring when the spring is in command of the valve. 6 The ANSI symbol for a directional valve is built around a series of boxes or rectangles, one box for each usable position of the valve. A 2-Position valve is shown by two boxes A 3-Position valve is shown by three boxes Most air moves are either 2-position or 3-position valves, but it would be possible to have an unusual valve with four or five or even six positions. In any case, there would be a box to represent each position of the valve. 7 Valve Ports Every valve port, which appears on the outside of the valve, is supposed to be shown on the symbol. But the ports are shown on only one of the boxes, the box that represents the flow paths that exist at the start of the machine cycle. A 2-position A 2-position A 3-position 2-port valve 3-port valve 4-port valve 8 Flow Paths Each box contains a group of lines that represent the flow paths the valve provides when it is in that position. If a port is blocked, we show that by the symbol If two ports are connected and air can flow, this is shown by an arrow drawn between the two ports. In the example, the left box shows the conditions that exist at the start of the cycle. 9 Example #1 ï‚§ At the start of the cycle, the flow path from port 1 to port 2 is blocked. ï‚§ When the valve shifts, flow is from port 1 to port 2. 10 Example #2 ï‚§ At the start of the cycle, the flow path from port 1 to port 2 is blocked. ï‚§ When the valve shifts, port 1 is opened to port 2, ï‚§ But during some part of the cycle air flows from port 1 to port 2, and during another part of the cycle air flows from port 2 to port 1. 11 Typical Symbols for Valve Actions 2/2, Blocked at 2/2, Open at start of cycle start of cycle 3/2, Blocked at 3/2, Open at start of cycle start of cycle 12 4/2 Single Inlet Single Exhaust 5/2 Single Inlet Dual Exhausts 13 Symbols for Valve Actuators The symbols for the valve actuators are drawn next to the end of the valve boxes. The rule is that each actuator is drawn next to the box that exists when that actuator is in command. In the drawing above, when the spring has control of the valve, the flow paths in the lefthand box. When the solenoid (the righthand actuator) is in command, the flow paths in the righthand box exist. 14 There are a series of standard symbols for actuators. These symbols may be drawn on either end of the valve without altering their meaning. Spring Solenoid Manual Air Pilot Push Button Air Pilot - Alternate Detent Lever Mechanical 15 Combined Actuation Methods If two actuator symbols are drawn side by side, this means that either one may cause the valve to actuate Either the air pilot OR the spring can cause the valve to move. Typical Actuator Combinations 2-Position Double 3-Position Double pilot, detent pilot, spring centered 16 Miscellaneous Valve Symbols Check Valve Allows flow in one direction but blocks flow in the other direction. In this example flow can go from 1 to 2, but flow 2 to 1 is blocked. Fixed Restriction or orifice Restricts flow in both directions. Adjustable Restriction Adjustable flow restriction flow in both directions. 17 Flow Control Valve (also called speed control valve) allows free flow in one direction but restricts flow in the other direction. In the above example: Free flow is from right to left, restricted flow from left to right. In this example: None restricted flow is from left to right. Restricted flow is from right to left. 18 Shuttle Valve A three-port valve with two inlets and one outlet. Ports 1 and 2 are inlets, port 3 is the outlet. If pressure is applied to port 1, it will appear at port 3 without back-flowing into port 2. If pressure is applied to port 2, it will appear at port 3 without back-flowing into port 1. 19 Summary Explanation of Valve Terminology TWO Way Valve Normally Closed: Flow is from inlet to outlet when the valve is actuated. Fluid in outlet line is trapped when the valve is deactivated. THREE Way Valve Normally Closed: Flow is from inlet to outlet when the valve is actuated. On deactivation of valve, outlet line is vented to atmosphere. Normally Open: Flow is from inlet to outlet in the deactivated valve condition. Actuation of the valve stops flow from inlet to outlet, the outlet is then exhausted. 20 FOUR Way Valve From inlet, flow is diverted to one of the outlets. Outlet port that is not active is vented to atmosphere. Valve can be either spring return or two-position type. FLOW Control Valve Allows free flow in one direction and controlled adjustable flow rate in the other direction. SHUTTLE Valve Allows flow from either input to the output. PULSE Valve A unitized valve that converts a continuous supply of air into an outlet pulse of air and then remains closed until the supply pressure is exhausted. 21 Electrical Control in Pneumatic Applications electro-pneumatics When the entire signal processing needs of an electro- pneumatic control system can be implemented with: ï‚§ Control Relays ï‚§ Programmable Logic Controllers(PLCs) are commonly used for signal processing instead of relay control systems. 22 Direct Control of Single Acting Cylinder The piston rod of the single-acting cylinder extends when pushbutton PB1 is pressed and retracts when the pushbutton is released. 23 Indirect Control of Single Acting Cylinder When pushbutton PB1 is pressed, current flows through CR1 relay coil. Contact CR1 of the relay closes, SOL1 is energized and the directional control valve switches. The piston rod is then extended. 24 Logic Operations ï‚§ Combine signals from several control elements through logic operations. Parallel Connection (OR Circuit) ï‚§ The intent is to extend a cylinder with multiple input elements activated together or individually. ï‚§ The contacts of the two pushbuttons PB1 and PB2 are connected in parallel in the circuit. 25 Series Connection (AND Circuit) ï‚§ The intend is to extend a cylinder with two different input elements activated simultaneously. ï‚§ In this case the piston rod of a cylinder is to be advanced only when both pushbuttons, PB1 and PB2, are pressed together. ï‚§ The contacts of the two pushbuttons are connected in series in the circuit. 26 Automatic Return Stroke Application 1: Create the following electro-pneumatic application: ï‚§ The piston rod of a double-acting cylinder is to be extended when pushbutton PB1 is actuated. ï‚§ When the forward end position is reached, the piston rod is to retract automatically. ï‚§ The prerequisite for the return movement is that pushbutton PB1 must had been released. 27 Application 1 - Solution: 28 Oscillating Movement Application 2: ï‚§ The piston rod of a cylinder is to reciprocate (extends and retracts automatically) when the control switch is actuated. ï‚§ When the control switch is reset, the piston rod is to occupy the retracted end position. 29 Application 2 - Solution 30