Pneumatics and Hydraulics-Engr_CeeJhay PDF
Document Details
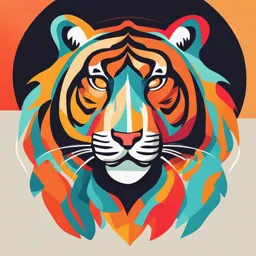
Uploaded by HealthfulBromeliad9890
TUP Manila College of Engineering
Tags
Summary
This document discusses pneumatics and hydraulics, covering definitions, key components, applications, and advantages/disadvantages. It's suitable for undergraduate-level engineering students.
Full Transcript
TUP MANILA COLLEGE OF ENGINEERING ELECTRICAL DEPARTMENT INSTRUMENTATION AND CONTROL Pnuematic and Hydraulic Systems LEARNING OBJECTIVES After completing this lesson, you will be able to: ❑ Define the pneumatics and hydraulics ❑ Identify the different compon...
TUP MANILA COLLEGE OF ENGINEERING ELECTRICAL DEPARTMENT INSTRUMENTATION AND CONTROL Pnuematic and Hydraulic Systems LEARNING OBJECTIVES After completing this lesson, you will be able to: ❑ Define the pneumatics and hydraulics ❑ Identify the different components used and functions in hydraulic and pneumatic systems. ❑ Understand the working principle of various components used in hydraulic and pneumatic systems. ❑ Understand the industrial applications of hydraulic and pneumatic systems. ❑ Explaining the operating principles of hydraulic and pneumatic systems. ❑ Provide knowledge on the working principles of fluid power systems. Pneumatic System What does PNEUMATIC means? ❑ Pneumatics comes from the Greek word pneuma, which means “breath or wind”. It is basically the use of under pressure gas that helps in performing a certain work in science and technology. Definition of PNEUMATICS ❑ Pneumatics is the transmission and control of forces and movements by means of compressed air. (The use of compressed air as a medium to do work). What is the fluid power? ❑ Fluid power is the energy transmitted and controlled by means of a pressurized fluid, either liquid or gas. The term fluid power applies to both hydraulics and pneumatics. Hydraulics (oil or water) use liquids under pressure while pneumatics use compressed air or other neutral gases. Pneumatics technology has for some considerable time been used in carrying out the simplest mechanical tasks, but nowadays has played a vital and important role in automation and development of sophisticated technologies. Application of Pneumatics 1.1 Industrial Applications Pneumatic systems are used in many industrial applications such as: ▪ Material handling ▪ Clamping ▪ Shifting ▪ Positioning ▪ Branching of material flow ▪ Packaging ▪ Filling ▪ Transfer of materials ▪ Sorting of parts ▪ Stamping and embossing of components 44 | P a g e TUP MANILA COLLEGE OF ENGINEERING ELECTRICAL DEPARTMENT INSTRUMENTATION AND CONTROL 1.2 Industrial Processes Pneumatic systems are used in carrying out machining and some industrial processes such as: ▪ Drilling ▪ Turning ▪ Milling ▪ Sawing ▪ Finishing ▪ Forming 1.3 Some of the pneumatic applications in our life ▪ A pneumatic machine is used to dismantle an automobile tire. ▪ A pneumatic machine is used in an automobile painting. ▪ A heavy-duty pneumatic jackhammer. ▪ A pneumatic filling machines. ▪ A dental drill is one of the uses of the pneumatic technology. ▪ A pneumatic device is used to fill the tire with compressed air to adjust the tire pressure. Advantages and Disadvantages of Pneumatics Advantages: 1. Availability: Air is available everywhere in unlimited quantities. 2. Transport: Air can be easily transported in pipelines, even over large distances. 3. Storage: Compressed air can be stored in a reservoir/tank and removed as required. 4. Temperature: Compressed air is relatively insensitive to temperature fluctuations. 5. Cleanliness: Unlubricated exhaust air is clean. 6. Cost: The running cost is relatively inexpensive 7. Speed: Compressed air is a very fast working medium. This enables high working speeds to be attained. 8. Overload safe: Pneumatic tools and operating components can be loaded to the point of stopping and are therefore overload safe. Disadvantages: 1. Preparation: Compressed air requires good preparation. Dirt and condensates should be removed. 2. Speed: As air is compressible; it is difficult to achieve uniform and constant piston speed. 3. Force requirement: Compressed air is economical only up to a certain force requirement. Under the normal working pressure of 600 to 700 kPa (6 to 7 bar). 4. Noise level: The exhaust air is loud (noise). This problem has now, however been largely solved due to the development of sound absorption material and silencers. Structure and Signal of Pneumatic System Pneumatic systems consist of an interconnection of different groups of elements. This group of elements forms a control path for signal flow, starting from the signal section (input) through to the actuating section (output). Control elements control the actuating elements in accordance with the signals received from the processing elements. 45 | P a g e TUP MANILA COLLEGE OF ENGINEERING ELECTRICAL DEPARTMENT INSTRUMENTATION AND CONTROL PRIMARY LEVELS OF THE PNEUMATIC SYSTEM: Pneumatic signal flow and corresponding control elements Example of pneumatic control elements shown in a practical circuit Air Generation and Distribution The main function of the air generation and distribution is to provide the system with compressed air, which is dry, clean, and at the required pressure. The compressed air supply for a pneumatic system should be adequately calculated and made available in the appropriate quality. Air is compressed by the air compressor and delivered to an air distribution system in the factory. To ensure that the quality of the air is acceptable, air service unit is utilized to prepare the air before being supplied to the control system. Malfunctions can be considerably reduced in the system if the compressed air is correctly prepared. A number of aspects must be considered. 46 | P a g e TUP MANILA COLLEGE OF ENGINEERING ELECTRICAL DEPARTMENT INSTRUMENTATION AND CONTROL PREPARATION OF THE COMPRESSED AIR: The following points should be considered in preparing compressed air plants: 1. Quantity of air required to meet the demand of the system. 2. Type of compressor to be used to produce the quantity required. 3. Pressure requirements. 4. Storage requirements. 5. Requirements for air cleanliness. 6. Acceptable humidity levels to reduce corrosion and sticky operation. 7. Lubrication requirements, if necessary. 8. Temperature of the air and effects on the system. 9. Line sizes and valve sizes to meet demand. 10. Material selection to meet environmental and system requirements. 11. Drainage points and exhaust outlets in the distribution system. 12. Layout of the distribution system to meet demand. MAIN PARTS IN THE COMPRESSED AIR PREPERATION 1. Air Compressor Air compressor is used to produce the compressed air for the system by the required volume and pressure. As a rule, pneumatic components are designed for a maximum operating pressure of 800-1000 kPa (8 - 10 bar) but in practice it is recommended to operate at between 500-600 kPa (5 and 6 bar) for economic and safe use. Due to the pressure losses in the distribution system, the compressor should provide pressure between 650-700 kPa (6.5 and 7) bar. (a) (b) (c) Fig. (a) and (b) are examples of some practical air compressors. Fig. (c) ISO symbol of air compressor 2. Air Tank (Reservoir) An air reservoir should be fitted to: Store and stabilize the compressed air. Compensate the pressure fluctuation. Cool the air. (a) (b) Fig. (a) is example of an air reservoir. Fig. (b) ISO symbol of an air reservoir. 47 | P a g e TUP MANILA COLLEGE OF ENGINEERING ELECTRICAL DEPARTMENT INSTRUMENTATION AND CONTROL 3. Compressed air filter Compressed air filter has the job of removing all contaminants from the compressed air flowing through it as well as water which has already condensed. The compressed air enters the filter bowl through guide slots. Liquid particles and larger particles of dirt are separated centrifugally collecting in the lower part of the filter bowl. The collected condensate must be drained before the level exceeds the maximum condensate mark, as it will otherwise be re-entrained in the air stream. (a) (b) Fig. (a) is example of an air filter. Fig. (b) ISO symbol of an air filter. 4. Cooling and drying unit As the air comes out from the compressor very hot and humid; The cooling and drying unit is used to: Condensate the water vapor (humidity) from the compressed air. Reduce the compressed air temperature (cooling). The accumulation of condensate depends largely on the relative air humidity. The relative air humidity is dependent on the air temperature and the weather situation. To remove the humidity, we use many types of air dryers, the very common and practical one is by using a cooling unit which cool the air and at the same time remove the water vapor. (a) (b) (c) Fig. (a)and (b) are some examples of real air dryer. Fig. (c) ISO symbol of air dyer. 5. Shut off valve It is used to open and close the compressed air supply manually. (a) (b) Fig. (a) is picture of shut off valve. Fig. (b) ISO symbol of shut off valve. 6. Piping The pipe diameter of the air distribution system should be selected in such a way that the pressure loss from the pressurized reservoir to the consuming device ideally does not exceed approx. 10 kPa (0.1 bar). Selection factors of the pipe diameter: 1. Flow rate 2. Line length 3. Permissible pressure loss 4. Operating pressure 5. Number of flow control points in the line 48 | P a g e TUP MANILA COLLEGE OF ENGINEERING ELECTRICAL DEPARTMENT INSTRUMENTATION AND CONTROL Piping Layout Ring circuits are most frequently used as main lines as shown in the figure. This method of installing pressure lines also achieves a constant supply in the case of high air consumption. Ring (loop) pneumatic distribution system In pipe-run layout, the pipelines must be installed in the direction of flow with a gradient of 1 to 2%. This is particularly important in the case of branch lines. Condensate can be removed from the lines at the lowest point. Pipe-run pneumatic distribution system Any branching of air consumption points where lines run horizontally should always be installed on the upper side of the main line. Shut-off valves can be used to block sections of compressed air lines if these are not required or need to be closed down for repair or maintenance purposes. 7. Air Service unit The air service unit a is a combination of the following: Compressed air filter (with water separator) Compressed air regulator Compressed air lubricator (a) (b) (c) Fig. (a) Show some real air service unit. Fig. (b) shows the detailed ISO symbol of the service unit. Fig. (c) shows the Simplified ISO symbol of the service unit. The main function of the service unit is to provide the pneumatic system with a well cleaned, lubricated and regulated compressed air. (Condition the compressed air). 49 | P a g e TUP MANILA COLLEGE OF ENGINEERING ELECTRICAL DEPARTMENT INSTRUMENTATION AND CONTROL 8. Pressure regulator Reduce/regulate the pressure. The purpose of the regulator is to keep the operating pressure of the system (secondary pressure) virtually constant regardless of fluctuations in the line pressure (primary pressure) and the air consumption. (a) (b) Fig. (a) pressure regulator. Fig. (b) ISO symbol of the pressure regulator. 9. Air lubricator Lubricate the moving parts. Most moving parts require some type of lubrication. The efficiency of cylinders, valves and air motors can be greatly improved if they are supplied with adequate lubrication. Pneumatic components can be lubricated by using an air line lubricator, a device for adding lubricating oil in aerosol form into a compressed air line. The air passing through the lubricator transports the lubricant to air tools, cylinders or other air operated equipment. (a) (b) Fig. (a) Air lubricator. Fig. (b)ISO symbol of the air lubricator. 10. Manifolds (distributor) It is used to provide multi equal pressure outlets. Each output port has check valve (Non return valve). (a) (b) (c) Fig. (a) shows a pneumatic manifold (distributor). Fig. (b) represents the ISO symbol of the pneumatic pressure source. Fig. (c) represents the ISO symbol of T junction. 11. Tubes and fittings Figure (a) shows some types of tubes that are used in connecting pneumatic circuits. Figure (b) shows some important fittings such as T connections and cross connections. Fittings are parts used to connect sections of pipe, tube, and hose in pneumatic (pressurized gas) systems. (a) (b) 50 | P a g e TUP MANILA COLLEGE OF ENGINEERING ELECTRICAL DEPARTMENT INSTRUMENTATION AND CONTROL 11. Tubes and fittings It used to display the actual amount of the pressure in two main units PSI and bar. (1 bar= 14.7 PSI) (a) (b) (c) Fig. (a)and (b) shows a real pressure gauge. Fig. (b) represents the ISO symbol of the pressure gauge. Hydraulic System The hydraulic system works on the principle of Pascal’s law which says that the pressure in an enclosed fluid is uniform in all the directions. Definition of HYDRAULICS ❑ Hydraulics is a branch of fluid mechanics that deals with the forces that acts on or within water. It also deals with the forces that acts on objects due to the movement of or presence of water. What is Fluid Mechanics? ❑ Fluid mechanics is a branch of Engineering Mechanics that deals with the forces acting on or within body of fluids, which was known to exist either in the form of gas and liquid. The force given by fluid is given by the multiplication of pressure and area of cross section. As the pressure is same in all the direction, the smaller piston feels a smaller force and a large piston feels a large force. Therefore, a large force can be generated with smaller force input by using hydraulic systems. The hydraulic systems consist of a number of parts for its proper functioning. These include storage tank, filter, hydraulic pump, pressure regulator, control valve, hydraulic cylinder, piston and leak proof fluid flow pipelines. The schematic of a simple hydraulic system is consisting of: ❑ A movable piston connected to the output shaft in an enclosed cylinder ❑ Storage tank ❑ Filter ❑ Electric or hydraulic pump ❑ Pressure regulator ❑ Control valve ❑ Leak proof closed loop piping Schematic of hydraulic system 51 | P a g e TUP MANILA COLLEGE OF ENGINEERING ELECTRICAL DEPARTMENT INSTRUMENTATION AND CONTROL The output shaft transfers the motion or force however all other parts help to control the system. The storage/fluid tank is a reservoir for the liquid used as a transmission media. The liquid used is generally high-density incompressible oil. It is filtered to remove dust or any other unwanted particles and then pumped by the hydraulic pump. The capacity of pump depends on the hydraulic system design. These pumps generally deliver constant volume in each revolution of the pump shaft. Therefore, the fluid pressure can increase indefinitely at the dead end of the piston until the system fails. The pressure regulator is used to avoid such circumstances which redirect the excess fluid back to the storage tank. The movement of piston is controlled by changing liquid flow from port A and port B. The cylinder movement is controlled by using control valve which directs the fluid flow. The fluid pressure line is connected to the port B to raise the piston and it is connected to port A to lower down the piston. The valve can also stop the fluid flow in any of the port. The leak proof piping is also important due to safety, environmental hazards and economical aspects. Some accessories such as flow control system, travel limit control, electric motor starter and overload protection may also be used in the hydraulic systems which are not shown in figure above. Applications of hydraulic systems The hydraulic systems are mainly used for precise control of larger forces. The main applications of hydraulic system can be classified in five categories: ❑ Industrial: Plastic processing machineries, steel making and primary metal extraction applications, automated production lines, machine tool industries, paper industries, loaders, crushes, textile machineries, research and development (R&D) equipment and robotic systems etc. ❑ Mobile hydraulics: Tractors, irrigation system, earthmoving equipment, material handling equipment, commercial vehicles, tunnel boring equipment, rail equipment, building and construction machineries and drilling rigs etc. ❑ Automobiles: It is used in the systems like breaks, shock absorbers, steering system, wind shield, lift and cleaning etc. ❑ Marine applications: It mostly covers ocean going vessels, fishing boats and navel equipment. ❑ Aerospace equipment: There are equipment and systems used for rudder control, landing gear, breaks, flight control and transmission etc. which are used in airplanes, rockets and spaceships. Hydraulic Pump The combined pumping and driving motor unit is known as hydraulic pump. The hydraulic pump takes hydraulic fluid (mostly some oil) from the storage tank and delivers it to the rest of the hydraulic circuit. In general, the speed of pump is constant and the pump delivers an equal volume of oil in each revolution. The amount and direction of fluid flow is controlled by some external mechanisms. In some cases, the hydraulic pump itself is operated by a servo-controlled motor but it makes the system complex. The hydraulic pumps are characterized by its flow rate capacity, power consumption, drive speed, pressure delivered at the outlet and efficiency of the pump. The hydraulic pumps can be of two types: ❑ Centrifugal pump ❑ Reciprocating pump 1. Centrifugal pump Centrifugal pump uses rotational kinetic energy to deliver the fluid. The rotational energy typically comes from an engine or electric motor. The fluid enters the pump impeller along or near to the rotating axis, accelerates in the propeller and flung out to the periphery by centrifugal force. In centrifugal pump the delivery is not constant and varies according to the outlet pressure. These pumps are not suitable for high pressure applications and are generally used for low-pressure and high-volume flow applications. The maximum pressure capacity is limited to 20-30 bars. Most of the centrifugal pumps are not self priming and the pump casing needs to be filled with liquid before the pump is started. 52 | P a g e TUP MANILA COLLEGE OF ENGINEERING ELECTRICAL DEPARTMENT INSTRUMENTATION AND CONTROL 2. Reciprocating pump Reciprocating pump is a positive plunger pump. It is also known as positive displacement pump or piston pump. It is often used where relatively small quantity is to be handled and the delivery pressure is quite large. The construction of these pumps is similar to the four stroke engine. The crank is driven by some external rotating motor. The piston of pump reciprocates due to crank rotation. The piston moves down in one half of crank rotation, the inlet valve opens and fluid enters into the cylinder. In second half crank rotation the piston moves up, the outlet valve opens and the fluid moves out from the outlet. At a time, only one valve is opened and another is closed so there is no fluid leakage. Depending on the area of cylinder the pump delivers constant volume of fluid in each cycle independent to the pressure at the output port. Pump Lift In general, the pump is placed over the fluid storage tank. The pump lift creates a negative pressure at the inlet which causes fluid to be pushed up in the inlet pipe by atmospheric pressure. It results in the fluid lift in the pump suction. The maximum pump lift can be determined by atmospheric pressure and is given by pressure head as: Pressure Head, P = ρgh, where: ρ = density of the gas or fluid (kg/m3); g = acceleration of the object due to gravity (9.80 m/s2); h = height of the column of gas or fluid (m). Theoretically, a pump lift of 8 m is possible but it is always lesser due to undesirable effects such as cavitation. The cavitation is the formation of vapor cavities in a liquid. The cavities can be small liquid-free zones ("bubbles" or "voids") formed due to partial vaporization of fluid (liquid). These are usually generated when a liquid is subjected to rapid changes of pressure and the pressure is relatively low. At higher pressure, the voids implode and can generate an intense shockwave. Therefore, the cavitation should always be avoided. The cavitation can be reduced by maintaining lower flow velocity at the inlet and therefore the inlet pipes have larger diameter than the outlet pipes in a pump. The pump lift should be as small as possible to decrease the cavitation and to increase the efficiency of the pump. Pressure Regulation This is the process of reduction of high source pressure to a lower working pressure suitable for the application. It is an attempt to maintain the outlet pressure within acceptable limits. The pressure regulation is performed by using pressure regulator. The primary function of a pressure regulator is to match the fluid flow with demand. At the same time, the regulator must maintain the outlet pressure within certain acceptable limits. The schematic of pressure regulator and various valves placement is shown in figure. When the valve V1 is closed and V2 is opened then the load moves down and fluid returns to the tank but the pump is dead ended and it leads to a continuous increase in pressure at pump delivery. Finally, it may lead to permanent failure of the pump. Therefore, some method is needed to keep the delivery pressure P1 within the safe level. It can be achieved by placing pressure regulating valve V3 as shown in figure. This valve is closed in normal conditions and when the pressure exceeds a certain limit, it opens and fluid from pump outlet returns to the tank via pressure regulating valve V3. As the pressure falls in a limiting range, the valve V3 closes again. When valve V1 is closed, the whole fluid is dumped back to the tank through the pressure regulating valve. This leads to the substantial loss of power because the fluid is circulating from tank to pump and then pump to tank without performing any useful work. This may lead to increase in fluid temperature because the energy input into fluid leads to the increase in fluid temperature. This may need to the installation of heat exchanger in to the storage tank to extract the excess heat. Interestingly, the motor power consumption is more in such condition because the outlet pressure is higher than the working pressure. 53 | P a g e TUP MANILA COLLEGE OF ENGINEERING ELECTRICAL DEPARTMENT INSTRUMENTATION AND CONTROL Advantages and Disadvantages of Hydraulic system Advantages ❑ The hydraulic system uses incompressible fluid which results in higher efficiency. ❑ It delivers consistent power output which is difficult in pneumatic or mechanical drive systems. ❑ Hydraulic systems employ high density incompressible fluid. Possibility of leakage is less in hydraulic system as compared to that in pneumatic system. The maintenance cost is less. ❑ These systems perform well in hot environment conditions. Disadvantages ❑ The material of storage tank, piping, cylinder and piston can be corroded with the hydraulic fluid. Therefore one must be careful while selecting materials and hydraulic fluid. ❑ The structural weight and size of the system is more which makes it unsuitable for the smaller instruments. ❑ The small impurities in the hydraulic fluid can permanently damage the complete system, therefore one should be careful and suitable filter must be installed. ❑ The leakage of hydraulic fluid is also a critical issue and suitable prevention method and seals must be adopted. ❑ The hydraulic fluids, if not disposed properly, can be harmful to the environment. Classification of Hydraulic Pumps These are mainly classified into two categories: 1. Non-positive displacement pumps 2. Positive displacement pumps. 1. Non-Positive Displacement Pumps These pumps are also known as hydro-dynamic pumps. In these pumps the fluid is pressurized by the rotation of the propeller and the fluid pressure is proportional to the rotor speed. These pumps can not withstanding high pressures and generally used for low-pressure and high-volume flow applications. The fluid pressure and flow generated due to inertia effect of the fluid. The fluid motion is generated due to rotating propeller. These pumps provide a smooth and continuous flow but the flow output decreases with increase in system resistance (load). The flow output decreases because some of the fluid slip back at higher resistance. The fluid flow is completely stopped at very large system resistance and thus the volumetric efficiency will become zero. Therefore, the flow rate not only depends on the rotational speed but also on the resistance provided by the system. The important advantages of non-positive displacement pumps are lower initial cost, less operating maintenance because of less moving parts, simplicity of operation, higher reliability and suitability with wide range of fluid etc. These pumps are primarily used for transporting fluids and find little use in the hydraulic or fluid power industries. Centrifugal pump is the common example of non-positive displacement pumps. 2. Positive Displacement Pumps These pumps deliver a constant volume of fluid in a cycle. The discharge quantity per revolution is fixed in these pumps and they produce fluid flow proportional to their displacement and rotor speed. These pumps are used in most of the industrial fluid power applications. The output fluid flow is constant and is independent of the system pressure (load). The important advantage associated with these pumps is that the high-pressure and low-pressure areas (means input and output region) are separated and hence the fluid cannot leak back due to higher pressure at the outlets. These features make the positive displacement pump most suited and universally accepted for hydraulic systems. The important advantages of positive displacement pumps over non-positive displacement pumps include capability to generate high pressures, high volumetric efficiency, high power to weight ratio, change in efficiency throughout the pressure range is small and wider operating range pressure and speed. The fluid flow rate of these pumps ranges from 0.1 and 15,000 gpm, the pressure head ranges between 10 and 100,000 psi and specific speed is less than 500. It is important to note that the positive displacement pumps do not produce pressure but they only produce fluid flow. The resistance to output fluid flow generates the pressure. It means that if the discharge port (output) of a positive displacement pump is opened to the atmosphere, then fluid flow will not generate any output pressure above atmospheric pressure. But, if the discharge port is partially blocked, then the pressure will rise due to the increase in fluid flow resistance. If the discharge port of the pump is completely blocked, then an infinite resistance will be generated. This will result in the breakage of the weakest component in the circuit. Therefore, the safety valves are provided in the hydraulic circuits along with positive displacement pumps. Important positive displacement pumps are gear pumps, vane pumps and piston pumps. 54 | P a g e TUP MANILA COLLEGE OF ENGINEERING ELECTRICAL DEPARTMENT INSTRUMENTATION AND CONTROL Gear Pumps Gear pump is a robust and simple positive displacement pump. It has two meshed gears revolving about their respective axes. These gears are the only moving parts in the pump. They are compact, relatively inexpensive and have few moving parts. The rigid design of the gears and houses allow for very high pressures and the ability to pump highly viscous fluids. They are suitable for a wide range of fluids and offer self-priming performance. Sometimes gear pumps are designed to function as either a motor or a pump. These pumps include helical and herringbone gear sets (instead of spur gears), lobe shaped rotors similar to Roots blowers (commonly used as superchargers), and mechanical designs that allow the stacking of pumps. Based upon the design, the gear pumps are classified as: ❑ External gear pumps ❑ Lobe pumps ❑ Internal gear pumps ❑ Gerotor pumps Generally, gear pumps are used to pump: ❑ Petrochemicals: Pure or filled bitumen, pitch, diesel oil, crude oil, lube oil etc. ❑ Chemicals: Sodium silicate, acids, plastics, mixed chemicals, isocyanates etc. ❑ Paint and ink ❑ Resins and adhesives ❑ Pulp and paper: acid, soap, lye, black liquor, kaolin, lime, latex, sludge etc. ❑ Food: Chocolate, cacao butter, fillers, sugar, vegetable fats and oils, molasses, animal food etc External gear pumps The external gear pump consists of externally meshed two gears housed in a pump case. One of the gears is coupled with a prime mover and is called as driving gear and another is called as driven gear. The rotating gear carries the fluid from the tank to the outlet pipe. The suction side is towards the portion whereas the gear teeth come out of the mesh. Lobe pumps Lobe contact is prevented by external timing gears located in the gearbox. Similar to the external gear pump, the lobes rotate to create expanding volume at the inlet. Lobe pumps are frequently used in food applications because they handle solids without damaging the product. Internal gear pumps Internal gear pumps are exceptionally versatile. They are often used for low or medium viscosity fluids such as solvents and fuel oil and wide range of temperature. This is non-pulsing, self-priming and can run dry for short periods. It is a variation of the basic gear pump. Some common internal gear pump applications are: ❑ All varieties of fuel oil and lube oil ❑ Food products such as corn syrup, chocolate, and peanut butter ❑ Resins and Polymers ❑ Paint, inks, and pigments ❑ Alcohols and solvents ❑ Soaps and surfactants ❑ Asphalt, Bitumen, and Tar ❑ Glycol ❑ Polyurethane foam (Isocyanate and polyol) Gerotor pumps The name Gerotor is derived from "Generated Rotor". At the most basic level, a Gerotor is essentially one that is moved via fluid power. Originally this fluid was water, today the wider use is in hydraulic devices. These pumps are primarily suitable for low pressure applications such as lubrication systems or hot oil filtration systems, but can also be found in low to moderate pressure hydraulic applications. Gerotors are widely used in industries and are produced in variety of shapes and sizes by a number of different methods. These pumps are primarily suitable for low pressure applications such as lubrication systems or hot oil filtration systems, but can also be found in low to moderate pressure hydraulic applications. However common applications are as follows: ❑ Light fuel oils ❑ Cooking oils ❑ Lube oil ❑ Hydraulic fluid 55 | P a g e TUP MANILA COLLEGE OF ENGINEERING ELECTRICAL DEPARTMENT INSTRUMENTATION AND CONTROL Vane Pumps Vane pumps are available in a number of vane configurations including sliding vane, flexible vane, swinging vane, rolling vane, and external vane etc. External vane pumps can handle large solids. Flexible vane pumps can handle only the small solids but create good vacuum. Sliding vane pumps can run dry for short periods of time and can handle small amounts of vapor. The vane pumps are known for their dry priming, ease of maintenance, and good suction characteristics. These pumps have various applications for the pumping of following fluids: ❑ Aerosol and Propellants ❑ Alcohols ❑ Aviation Service - Fuel Transfer, Deicing ❑ Refrigeration - Freons, Ammonia ❑ Auto Industry - Fuels, Lubes, Refrigeration Coolants ❑ Solvents ❑ Bulk Transfer of LPG and NH3 ❑ Aqueous solutions ❑ LPG Cylinder Filling Unbalanced vane pump The rotor is offset within the housing, and the vanes are constrained by a cam ring as they cross inlet and outlet ports. The pressure difference between outlet and inlet ports creates a large amount of load on the vanes and a significant amount of side load on the rotor shaft which can lead to bearing failure. This type of pump is called as unbalanced vane pump. Balance vane pump This pump has an elliptical cam ring with two inlet and two outlet ports. Pressure loading still occurs in the vanes but the two identical pump halves create equal but opposite forces on the rotor. It leads to the zero net force on the shaft and bearings. Thus, lives of pump and bearing increase significantly. Also the sounds and vibrations decrease in the running mode of the pump. Adjustable vane pump In general, the adjusted vane pumps are pressure compensated. It means that the discharge is controlled by pre-adjusted value and when the discharge pressure reaches a certain (adjusted) value; the pumping action ceases. These pumps are used as energy savings devices and have been used in many applications, including automotive transmissions. Piston Pumps Piston pumps are meant for the high-pressure applications. These pumps have high-efficiency and simple design and needs lower maintenance. These pumps convert the rotary motion of the input shaft to the reciprocating motion of the piston. These pumps work similar to the four stroke engines. They work on the principle that a reciprocating piston draws fluid inside the cylinder when the piston retracts in a cylinder bore and discharge the fluid when it extends. Axial piston pumps are positive displacement pumps which converts rotary motion of the input shaft into an axial reciprocating motion of the pistons. These pumps have a number of pistons (usually an odd number) in a circular array within a housing which is commonly referred to as a cylinder block, rotor or barrel. These pumps have sub-types as: Bent axis piston pump In these pumps, the reciprocating action of the pistons is obtained by bending the axis of the cylinder block. The cylinder block rotates at an angle which is inclined to the drive shaft. The cylinder block is turned by the drive shaft through a universal link. The cylinder block is set at an offset angle with the drive shaft. The cylinder block contains a number of pistons along its periphery. These piston rods are connected with the drive shaft flange by ball-and socket joints. These pistons are forced in and out of their bores as the distance between the drive shaft flange and the cylinder block changes. Swash plate axial piston pump A swash plate is a device that translates the rotary motion of a shaft into the reciprocating motion. It consists of a disk attached to a shaft. If the disk is aligned perpendicular to the shaft; the disk will turn along with the rotating shaft without any reciprocating effect. Similarly, the edge of the inclined shaft will appear to oscillate along the shaft's length. 45 | P a g e TUP MANILA COLLEGE OF ENGINEERING ELECTRICAL DEPARTMENT INSTRUMENTATION AND CONTROL The typical construction of radial piston pump. The piston pump has pistons aligned radially in a cylindrical block. It consists of a pintle, a cylinder barrel with pistons and a rotor containing a reaction ring. The pintle directs the fluid in and out of the cylinder. Pistons are placed in radial bores around the rotor. The piston shoes ride on an eccentric ring which causes them to reciprocate as they rotate. The eccentricity determines the stroke of the pumping piston. Each piston is connected to inlet port when it starts extending while it is connected to the outlet port when start retracting. In general, the applications of Hydraulic Pumps can be summarized as: ❑ Hydraulic pumps are used to transfer power via hydraulic liquid. These pumps have a number of applications in automobiles, material handling systems, automatic transmissions, controllers, compressors and household items. ❑ The hand operated hydraulic pump is used in a hydraulic jack where many strokes of the pump apply hydraulic pressure to lift the ram. ❑ A backhoe uses an engine driven hydraulic pump to drive the articulating parts of the mechanical hoe. ❑ The hydraulic pumps are commonly used in the automotive vehicles especially in power steering systems. ❑ The lift system of tractor is operated by the hydraulic pumps. These are used in automatic transmissions and material handling systems in industries. ❑ Many precise controllers are developed by using hydraulic pumps. The commonly used compressor is operated by reciprocating pumps. ❑ The hydraulic pumps are also used in routine household systems like power lift and air-conditions. Therefore, it can be said that the hydraulic pumps have significant applications in industries as well as ones routine life. Control Valves There are basically three types of valves employed in hydraulic systems: 1. Directional control valves 2. Flow control valves 3. Pressure control valves Directional Control Valves Directional control valves are used to control the distribution of energy in a fluid power system. They provide the direction to the fluid and allow the flow in a particular direction. These valves are used to control the start, stop and change in direction of the fluid flow. These valves regulate the flow direction in the hydraulic circuit. These control valves contain ports that are external openings for the fluid to enter and leave. Directional control valves can be classified in the following manner: 1. Type of construction: ❑ Poppet valves ❑ Spool valves 2. Number of ports: ❑ Two-way valves ❑ Three-way valves ❑ Four-way valves. 3. Number of switching position: ❑ Two-position ❑ Three-position 4. Actuating mechanism: ❑ Manual actuation ❑ Mechanical actuation ❑ Solenoid actuation ❑ Hydraulic actuation ❑ Pneumatic actuation ❑ Indirect actuation 45 | P a g e TUP MANILA COLLEGE OF ENGINEERING ELECTRICAL DEPARTMENT INSTRUMENTATION AND CONTROL 1. Type of construction These are unidirectional valves and permit the free flow in one direction only. These valves have two ports: one for the entry of fluid and the other for the discharge. They are consists of a housing bore in which ball or poppet is held by a small spring force. The valve having ball as a closing member is known as ball check valve. Check valves These are unidirectional valves and permit the free flow in one direction only. These valves have two ports: one for the entry of fluid and the other for the discharge. These consists of a housing bore in which ball or poppet is held by a small spring force. The valve having ball as a closing member is known as ball check valve. These valves are generally small sized, simple in construction and inexpensive. Generally, the check valves are automatically operated. Human intervention or any external control system is not required. These valves can wear out or can generate the cracks after prolonged usage and therefore they are mostly made of plastics for easy repair and replacements. required. These valves can wear out or can generate the cracks after prolonged usage and therefore they are mostly made of plastics for easy repair and replacements. Inline check valve The simplest check valve is an inline check valve. The ball is held against the valve seat by a spring force. It can be observed from the figure that the fluid flow is not possible from the spring side but the fluid from opposite side can pass by lifting the ball against. However, there is some pressure drop across the valve due to restriction by the spring force. Therefore, these valves are not suitable for the application of high flow rate. When the operating pressure increases the valve becomes more tightly seated in this design. The advantages of the poppet valves include no leakage, long life and suitability with high pressure applications. These valves are commonly used in liquid or gel mini-pump dispenser spigots, spray devices, some rubber bulbs for pumping air, manual air pumps, and refillable dispensing syringes. Right angel check valve The right angle check valve is used for the high flow rate applications. The pressure drop is comparatively less in right angle check valve. Restriction check valve When the closing member is not a ball but a poppet energized by a spring is known as poppet valve. The typical poppet valve is shown in the figure. Some valves are meant for an application where free flow is required in one direction and restricted flow required in another direction. These types of valves are called as restriction check valve. These valves are used when a direction sensitive flow rate is required. For example, the different actuator speeds are required in both the directions. The flow adjustment screw can be used to set the discharge (flow rate) in the restricted direction. Pilot operated check valve Another important type of check valve known as pilot operated check valve. The function of the pilot operated check valve is similar to a normal check valve unless it gets an extra pressure signal through a pilot line. Pilot allows free flow in one direction and prevents the flow in another direction until the pilot pressure is applied. But when pilot pressure acts, the poppet opens and the flow is blocked from both the sides. These valves are used to stop the fluid suddenly. Spool valves The spool valves derive their name from their appearance. It consists of a shaft sliding in a bore which has large groove around the circumference. This type of construction makes it look like a spool. The spool is sealed along the clearance between moving spool and housing (valve body). The quality of seal or the amount of leakage depends on the amount of clearance, viscosity of fluid and the level of the pressure. The grooves guide the fluid flow by interconnecting or blocking the holes (ports). The spool valves are categorized according to the number of operating positions and the way hydraulic lines interconnections. One of the simplest two way spool valve is shown in the figure below. The standard terms are referred as Port ‘P’ is pressure port, Port ‘T’ is tank port and Port ‘A’ and Port ‘B’ are the actuator (or working) ports. The actuators can move in forward or backward direction depending on the connectivity of the pressure and tank port with the actuators port. 46 | P a g e TUP MANILA COLLEGE OF ENGINEERING ELECTRICAL DEPARTMENT INSTRUMENTATION AND CONTROL 2. Number of Ports Two way valves Two way valves have only two ports as shown in the figures above. These valves are also known as on-off valves because they allow the fluid flow only in direction. Normally, the valve is closed. These valves are available as normally open and normally closed function. These are the simplest type of spool valves. When actuating force is not applied to the right, the port P is not connected with port A as shown in the first figure. Therefore, the actuation does not take place. Similarly, the second figure shows the two-way spool valve in the open condition. Here, the pressure port P is connected with the actuator port A. Three way valves When a valve has one pressure port, one tank port and one actuating port as shown in the figures below, it is known as three way valve. In this valve, the pressure port pressurizes one port and exhausts another one. As shown in figures, only one actuator port is opened at a time. In some cases, a neutral position is also available when both the ports are blocked. Generally, these valves are used to operate single acting cylinders. Four way valves The figure below shows a four-way valve. It is generally used to operate the cylinders and fluid motors in both the directions. The four ways are: pump port P, tank port T, and two working ports A and B connected to the actuator. The primary function of a four way valve is to pressurize and exhaust two working ports A and B alternatively. 3. Number/Ways of Switching Position Three position four way (3/4) valves Three position four way (3/4) valves are used in double-acting cylinders to perform advance, hold and return operation to the piston. The figure below shows three position four way valves. These types of valves have three switching positions. They have a variety of possible flow path configurations but have identical flow path configuration. When the centered path is actuated, port A and B are connected with both the ports P and T respectively. In this case, valve is not active because all the ports are open to each other. The fluid flows to the tank at atmospheric pressure. In this position work cannot be done by any part of the system. This configuration helps to prevent heat buildup. When left end (port B) is actuated, the port P is connected with ports B and T is connected with port A as shown in the first figure below. Similarly, when the right end is actuated the port P is connected to A and working port B is connected to port T as shown in second figure. The three position valves are used when the actuator is needed to stop or hold at some intermediate position. It can also be used when the multiple circuits or functions are accomplished from one hydraulic power source. 47 | P a g e TUP MANILA COLLEGE OF ENGINEERING ELECTRICAL DEPARTMENT INSTRUMENTATION AND CONTROL Three position four way valve: P to B and A to T Three position four way valve: P to A and B to T The figure below shows a three position four way valve in the closed center position. The working of the valve is similar to open center directional control valves (DCV). In closed center DCV all user ports (port A and port B) are closed. Therefore, these ports are hydraulically locked and the actuator cannot be moved by the external load. The pumped fluid flows through the relief valve. The pump works under the high pressure condition which not only wastes the pump power but also causes wear of the pump parts. The fluid temperature also rises due to heat generation by the pump energy transformation. The increase in fluid temperature may lead to the oxidation and viscosity drop of the fluid. The oxidation and viscosity drop reduces the pump life and leakage in the system. Three position four way valve: closed center The figure below shows a tandem center three position four way direction control valve. In this configuration, the working ports A and B are blocked and the pump port P is connected to the tank port T. Tandem center results in the locked actuator. However, pump to tank flow takes place at the atmospheric temperature. This kind of configuration can be used when the load is needed to hold. Disadvantages of high pressure pumping in case of closed center can be removed by using this configuration. The regenerative center is another important type of common center configuration used in hydraulic circuits. Tandem centered valve Regenerative means the flow is generated from the system itself. Regenerative center is used when the actuator movement in one direction requires two different speeds. For example, the half-length of the stroke requires fast movement during no-load condition and remaining half-length requires slow motion during load conditions. The regenerative center saves the pump power. The figure below shows the regenerative configuration for the three position four way (3/4) DCV in its mid position. This configuration increases the piston speed. In the mid position pump Port P is connected to A and B, and tank port T is blocked. Regenerative Center The figure below shows the floating center 3/4 DCV in its mid position. In this configuration, the pump port is blocked and both the working ports A and B are connected to the tank port T. Therefore, the working ports A and B can be moved freely which is reason they are called as floating center. The pumped fluid passes through the relief valve. Therefore, pump works in the high pressure condition. This configuration is used only in some special cases. 48 | P a g e TUP MANILA COLLEGE OF ENGINEERING ELECTRICAL DEPARTMENT INSTRUMENTATION AND CONTROL Floating Center Two position four way (2/4) valves The two position four way valves have only two switching positions and do not have any mid position. Therefore, they are also known as impulse valves. The typical connections of 2/4 valves is shown in the figures below. These valves can be used to operate double acting cylinders. These are also used to reciprocate or hold an actuator. The operation is faster because the distance between ports of these valves is smaller. Hence, these valves are used on machines where fast reciprocation cycles are needed such as punching and stamping etc. Two position four way DCV: P to B and A to T Two position four way DCV: P to A and B to T 4. Actuating Mechanism Manual actuation In this type, the spool is operated manually. Manual actuators are hand lever, push button and pedals etc. Mechanical actuation The DCV spool can be operated by using mechanical elements such as roller and cam, roller and plunger and rack and pinion etc. In these arrangements, the spool end is of roller or a pinion gear type. The plunger or cam or rack gear is attached to the actuator. Thus, the mechanical elements gain some motion relative to the actuator (cylinder piston) which can be used for the actuation. Solenoid actuation The solenoid actuation is also known as electrical actuation. The schematic of solenoid actuation is shown in the figure below. The energized solenoid coil creates a magnetic force which pulls the armature into the coil. This movement of armature controls the spool position. The main advantage of solenoid actuation is its less switching time. Working of solenoid to shift spool of valve Hydraulic actuation This type actuation is usually known as pilot-actuated valve and a schematic is shown in the figure below. In this type of actuation, the hydraulic pressure is directly applied on the spool. The pilot port is located on one end of the valve. Fluid entering from pilot port operates against the piston and forces the spool to move forward. The needle valve is used to control the speed of the actuation. Pilot actuated DCV 49 | P a g e TUP MANILA COLLEGE OF ENGINEERING ELECTRICAL DEPARTMENT INSTRUMENTATION AND CONTROL Pneumatic actuation DCV can also be operated by applying compressed air against a piston at either end of the valve spool. The construction of the system is similar to the hydraulic actuation. The only difference would be the actuation medium. The actuation medium is the compressed air in pneumatic actuation system. Indirect actuation of directional control valve The direction control valve can be operated by manual, mechanical, solenoidal (electrical), hydraulic (pilot) and pneumatic actuations. The mode of actuation does not have any influence on the basic operation of the hydraulic circuits. Mostly, the direct actuation is restricted to use with smaller valves only because usually lot of force is not available. The availability of limited force is the greatest disadvantage of the direct actuation systems. In practice, the force required to shift the spool is quiet higher. Therefore, the larger valves are often indirectly actuated in sequence. First, the smaller valve is actuated directly and the flow from the smaller valve is directed to either side of the larger valve. The control fluid can be supplied by the same circuit or by a separate circuit. The pilot valve pressure is usually supplied internally. These two valves are often incorporated as a single unit. These valves are also called as Electro-hydraulic operated DCV. Flow Control Valves In practice, the speed of actuator is very important in terms of the desired output and needs to be controlled. The speed of actuator can be controlled by regulating the fluid flow. A flow control valve can regulate the flow or pressure of the fluid. The fluid flow is controlled by varying area of the valve opening through which fluid passes. The fluid flow can be decreased by reducing the area of the valve opening and it can be increased by increasing the area of the valve opening. A very common example to the fluid flow control valve is the household tap. The figure shows the schematic diagram of a flow control valve. The pressure adjustment screw varies the fluid flow area in the pipe to control the discharge rate. The pressure drop across the valve may keep on fluctuating. In general, the hydraulic systems have a pressure compensating pump. The inlet pressure remains almost constant but the outlet pressure keeps on fluctuating depending on the external load. It creates fluctuating pressure drop. Thus, the ordinary flow control valve will not be able to maintain a constant fluid flow. A pressure compensated flow control valve maintains the constant flow throughout the movement of a spool, which shifts its position depending on the pressure. Flow control valves can also be affected by temperature changes. It is because the viscosity of the fluid changes with temperature. Therefore, the advanced flow control valves often have the temperature compensation. The temperature compensation is achieved by the thermal expansion of a rod, which compensates for the increased coefficient of discharge due to decreasing viscosity with temperature. Types of Flow Control Valve The flow control valves work on applying a variable restriction in the flow path. Based on the construction; there are mainly four types viz. plug valve, butterfly valve, ball valve and balanced valve. Plug or Glove valve The plug valve is quite commonly used valve. It is also termed as glove valve. This valve has a plug which can be adjusted in vertical direction by setting flow adjustment screw. The adjustment of plug alters the orifice size between plug and valve seat. Thus, the adjustment of plug controls the fluid flow in the pipeline. The characteristics of these valves can be accurately predetermined by machining the taper of the plug. The typical example of plug valve is stopcock that is used in laboratory glassware. The valve body is made of glass or teflon. The plug can be made of plastic or glass. Special glass stopcocks are made for vacuum applications. Stopcock grease is used in high vacuum applications to make the stopcock air tight. 50 | P a g e TUP MANILA COLLEGE OF ENGINEERING ELECTRICAL DEPARTMENT INSTRUMENTATION AND CONTROL Butterfly valve It consists of a disc which can rotate inside the pipe. The angle of disc determines the restriction. Butterfly valve can be made to any size and is widely used to control the flow of gas. These valves have many types which have for different pressure ranges and applications. The resilient butterfly valve uses the flexibility of rubber and has the lowest pressure rating. The high performance butterfly valves have a slight offset in the way the disc is positioned. It increases its sealing ability and decreases the wear. For high-pressure systems, the triple offset butterfly valve is suitable which makes use of a metal seat and is therefore able to withstand high pressure. It has higher risk of leakage on the shut-off position and suffer from the dynamic torque effect. Butterfly valves are favored because of their lower cost and lighter weight. The disc is always present in the flow therefore a pressure drop is induced regardless of the valve position. Ball valve This type of flow control valve uses a ball rotated inside a machined seat. The ball has a through hole. It has very less leakage in its shut-off condition. These valves are durable and usually work perfectly for many years. They are excellent choice for shutoff applications. They do not offer fine control which may be necessary in throttling applications. These valves are widely used in industries because of their versatility, high supporting pressures (up to 1000 bar) and temperatures (up to 250°C). They are easy to repair and operate. Balanced valve Schematic of a balanced valve is shown in the figure. It comprises of two plugs and two seats. The opposite flow gives little dynamic reaction onto the actuator shaft. It results in the negligible dynamic torque effect. However, the leakage is more in these kind of valves because the manufacturing tolerance can cause one plug to seat before the other. The pressure-balanced valves are used in the houses. They provide water at nearly constant temperature to a shower or bathtub despite of pressure fluctuations in either the hot or cold supply lines. Pressure Relief Valves The pressure relief valves are used to protect the hydraulic components from excessive pressure. This is one of the most important components of a hydraulic system and is essentially required for safe operation of the system. Its primary function is to limit the system pressure within a specified range. It is normally a closed type and it opens when the pressure exceeds a specified maximum value by diverting pump flow back to the tank. The simplest type valve contains a poppet held in a seat against the spring force. The fluid enters from the opposite side of the poppet. When the system pressure exceeds the preset value, the poppet lifts and the fluid is escaped through the orifice to the storage tank directly. It reduces the system pressure and as the pressure reduces to the set limit again the valve closes. This valve does not provide a flat cut-off pressure limit with flow rate because the spring must be deflected more when the flow rate is higher. 51 | P a g e TUP MANILA COLLEGE OF ENGINEERING ELECTRICAL DEPARTMENT INSTRUMENTATION AND CONTROL 1. Direct Types of Relief Valve This type of valves has two ports; one of which is connected to the pump and another is connected to the tank. It consists of a spring chamber where poppet is placed with a spring force. Generally, the spring is adjustable to set the maximum pressure limit of the system. The poppet is held in position by combined effect of spring force and dead weight of spool. As the pressure exceeds this combined force, the poppet raises and excess fluid bypassed to the reservoir (tank). The poppet again reseats as the pressure drops below the pre-set value. A drain is also provided in the control chamber. It sends the fluid collected due to small leakage to the tank and thereby prevents the failure of the valve. 2. Unloading Valve This valve consists of a control chamber with an adjustable spring which pushes the spool down. The valve has two ports: one is connected to the tank and another is connected to the pump. The valve is operated by movement of the spool. Normally, the valve is closed and the tank port is also closed. These valves are used to permit a pump to operate at the minimum load. The drain is provided to remove the leaked oil collected in the control chamber to prevent the valve failure. The unloading valve reduces the heat buildup due to fluid discharge at a preset pressure value. 3. Sequence Valve The primary function of this type of valve is to divert flow in a predetermined sequence. It is used to operate the cycle of a machine automatically. A sequence valve may be of direct-pilot or remote- pilot operated type. It consists of the two ports; one main port connecting the main pressure line and another port (secondary port) is connected to the secondary circuit. The secondary port is usually closed by the spool. The pressure on the spool works against the spring force. When the pressure exceeds the preset value of the spring; the spool lifts and the fluid flows from the primary port to the secondary port. For remote operation; the passage used for the direct operation is closed and a separate pressure source for the spool operation is provided in the remote operation mode. 4. Counterbalance Valve It is used to maintain the back pressure and to prevent a load from failing. The counterbalance valves can be used as breaking valves for decelerating heavy loads. These valves are used in vertical presses, lift trucks, loaders and other machine tools where position or hold suspended loads are important. Counterbalance valves work on the principle that the fluid is trapped under pressure until pilot pressure overcomes the pre-set value of spring force. Fluid is then allowed to escape, letting the load to descend under control. This valve is normally closed until it is acted upon by a remote pilot pressure source. Therefore, a lower spring force is sufficient. It leads to the valve operation at the lower pilot pressure and hence the power consumption reduces, pump life increases and the fluid temperature decreases. 5. Pressure Reducing Valve Sometimes a part of the system may need a lower pressure. This can be made possible by using pressure reducing valve. These valves are used to limit the outlet pressure. Generally, they are used for the operation of branch circuits where the pressure may vary from the main hydraulic pressure lines. These are open type valve and have a spring chamber with an adjustable spring, a movable spool. A drain is provided to return the leaked fluid in the spring (control) chamber. A free flow passage is provided from inlet port to the outlet port until a signal from the outlet port tends to throttle the passage through the valve. The pilot pressure opposes the spring force and when both are balanced, the downstream is controlled at the pressure setting. When the pressure in the reduced pressure line exceeds the valve setting, the spool moves to reduce the flow passage area by compressing the spring. It can be seen from the figure that if the spring force is more, the valve opens wider and if the controlled pressure has greater force, the valves moves towards the spring and throttles the flow. 52 | P a g e TUP MANILA COLLEGE OF ENGINEERING ELECTRICAL DEPARTMENT INSTRUMENTATION AND CONTROL Graphical representation of Hydraulic and Pneumatic Elements The hydraulic and pneumatic elements such as cylinders and valves are connected through pipelines to form a hydraulic or a pneumatic circuit. It is difficult to represent the complex functioning of these elements using sketches. Therefore, graphical symbols are used to indicate these elements. The symbols only specify the function of the element without indicating the design of the element. Symbols also indicate the actuation method, direction of flow of air and designation of the ports. Symbols are described in various documents like DIN24300, BS2917, ISO1219 and the new ISO5599, CETOP RP3 and the original American JIC and ANSI symbols. The symbol used to represent an individual element display the following characteristics: ❑ Function ❑ Actuation and return actuation methods ❑ Number of connections ❑ Number of switching positions ❑ General operating principle ❑ Simplified representation of the flow path The symbol does not represent the following characteristics: ❑ Size or dimensions of the component ❑ Particular manufacturer, methods of construction or costs ❑ Operation of the ports ❑ Any physical details of the elements ❑ Any unions or connections other than junctions Earlier the ports were designated with letter system. Now as per ISO5599 the ports are designated based on number system. The port designations are shown in table below. The graphical representation, designation and explanation of various components and equipments used in hydraulic and pneumatic system are given in table below. Readers are suggested to study these representations carefully. 53 | P a g e TUP MANILA COLLEGE OF ENGINEERING ELECTRICAL DEPARTMENT INSTRUMENTATION AND CONTROL 54 | P a g e TUP MANILA COLLEGE OF ENGINEERING ELECTRICAL DEPARTMENT INSTRUMENTATION AND CONTROL Design of Hydraulic Circuit Problem Definition: Package Lifting Device Schematic of a Package lifting system for LED TVs For a dispatch station of a LED TV production house, design a package lifting device to lift packages containing 21” to 51” LED TVs from the inspection conveyor to the dispatch conveyor. Draw the hydraulic circuit diagram. List the components. Readers are requested to assume suitable data. Problem Definition: Package Lifting Device By applying the principle of hydraulics and after studying the various sensors, pumps, valves and hydraulic actuators, the proposed hydraulic circuit. Components required are listed in table. Proposed hydraulic circuit and its operation 55 | P a g e TUP MANILA COLLEGE OF ENGINEERING ELECTRICAL DEPARTMENT INSTRUMENTATION AND CONTROL The proposed hydraulic circuit shows the design for package lifting device. The two direction hydraulic motor is run by using a hydraulic power pack. Required valves and pressure sensors are also included for desired control action. Readers are requested to carefully read the circuit and comprehend the circuit. Once the hydraulic circuit has been assembled and checked, valve 1V1 and pressure relief valve 1V2 can be operated in sequence to obtain the rotary motion of hydraulic motor in required direction (clockwise/counter clockwise). This rotary motion can further be converted into linear motion by using suitable motion converter mechanism viz. Rack and pinion mechanism. Linear motion is used to lift the packages. It is required to develop a PID based controller to control the operation of the valves. The pressure gauge and flow sensor are used to monitor the operation continuously. REFERENCES https://www.quia.com/files/quia/users/sfah6922/BasicPneumatics2011.2012/ATM1132_Basic_Pneu matics_module_2.pdf https://www.studocu.com/ph/document/university-of-the-east-philippines/hydraulics- lecture/hydraulics-lecture-introduction/27858745 NPTEL – Mechanical – Mechatronics and Manufacturing Automation 56 | P a g e