Chapter One PDF - Mechanisms and Kinematics
Document Details
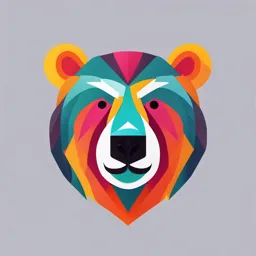
Uploaded by IdealEpic
Vongchavalitkul University
Tags
Summary
This document describes mechanisms and kinematics, including examples such as a can crusher and shear press. It explores actuator types and concepts like degrees of freedom using kinematic diagrams.
Full Transcript
10 CHAPTER ONE and M = 3(n - 1) - 2jp - j h = 3(4 - 1) - 2(4) - 0 = 1 With one degree of freedom, the clamp mechanism is constrained. Moving only one link, the handle, precisely...
10 CHAPTER ONE and M = 3(n - 1) - 2jp - j h = 3(4 - 1) - 2(4) - 0 = 1 With one degree of freedom, the clamp mechanism is constrained. Moving only one link, the handle, precisely positions all other links in the clamp. EXAMPLE PROBLEM 1.4 Figure 1.16 shows a beverage can crusher used to reduce the size of cans for easier storage prior to recycling. Draw a kinematic diagram, using the end of the handle as a point of interest. Also compute the degrees of freedom for the device. FIGURE 1.16 Can crusher for Example Problem 1.4. SOLUTION: 1. Identify the Frame The back portion of the device serves as a base and can be attached to a wall. This component is designated as the frame. The motion of all other links is determined relative to this frame. The frame is numbered as link 1. 2. Identify All Other Links Careful observation shows a planar mechanism with three other moving parts: Link 2: Handle Link 3: Block that serves as the crushing surface Link 4: Bar that connects the crushing block and handle 3. Identify the Joints Three pin joints are used to connect these different parts. One pin connects the handle to the base. This joint is labeled as A. A second pin is used to connect link 4 to the handle. This joint is labeled B. The third pin connects the crushing block and link 4. This joint is labeled C. The crushing block slides vertically during operation; therefore, a sliding joint connects the crushing block to the base. This joint is labeled D. 4. Identify Any Points of Interest The motion of the handle end is desired. This is designated as point of interest X. 5. Draw the Kinematic Diagram The kinematic diagram is given in Figure 1.17. X 3 C 4 B D 2 1 A FIGURE 1.17 Kinematic diagram for Example Problem 1.4. Introduction to Mechanisms and Kinematics 11 6. Calculate Mobility It was determined that there are four links in this mechanism. There are also three pin joints and one slider joint. Therefore, n = 4, jp = (3 pins + 1 slider) = 4, j h = 0 and M = 3(n - 1) - 2jp - j h = 3(4 - 1) - 2(4) - 0 = 1 With one degree of freedom, the can crusher mechanism is constrained. Moving only one link, the handle, precisely positions all other links and crushes a beverage can placed under the crushing block. EXAMPLE PROBLEM 1.5 Figure 1.18 shows another device that can be used to shear material. Draw a kinematic diagram, using the end of the handle and the cutting edge as points of interest. Also, compute the degrees of freedom for the shear press. FIGURE 1.18 Shear press for Example Problem 1.5. SOLUTION: 1. Identify the Frame The base is bolted to a working surface and can be designated as the frame. The motion of all other links is de- termined relative to this frame. The frame is numbered as link 1. 2. Identify All Other Links Careful observation reveals two other moving parts: Link 2: Gear/handle Link 3: Cutting lever 3. Identify the Joints Two pin joints are used to connect these different parts. One pin connects the cutting lever to the frame. This joint is labeled as A. A second pin is used to connect the gear/handle to the cutting lever. This joint is labeled B. The gear/handle is also connected to the frame with a gear joint. This higher-order joint is labeled C. 4. Identify Any Points of Interest The motion of the handle end is desired and is designated as point of interest X. The motion of the cutting surface is also desired and is designated as point of interest Y. 5. Draw the Kinematic Diagram The kinematic diagram is given in Figure 1.19. 12 CHAPTER ONE X 2 B C 1 3 A Y FIGURE 1.19 Kinematic diagram for Example Problem 1.5. 6. Calculate Mobility To calculate the mobility, it was determined that there are three links in this mechanism. There are also two pin joints and one gear joint. Therefore, n = 3 jp = (2 pins) = 2 jh = (1 gear connection) = 1 and M = 3(n - 1) - 2jp - j h = 3(3 - 1) - 2(2) - 1 = 1 With one degree of freedom, the shear press mechanism is constrained. Moving only one link, the handle, precisely positions all other links and brings the cutting edge onto the work piece. 1.7.2 Actuators and Drivers Engines also generate continuous rotary motion. The speed of an engine can be throttled within a range In order to operate a mechanism, an actuator, or driver of approximately 1000 to 8000 rpm. They are a device, is required to provide the input motion and energy. popular and highly portable driver for high-power To precisely operate a mechanism, one driver is required for applications. Because they rely on the combustion each degree of freedom exhibited. Many different actuators of fuel, engines are used to drive machines that are used in industrial and commercial machines and mecha- operate outdoors. nisms. Some of the more common ones are given below: Servomotors are motors that are coupled with a con- Electric motors (AC) provide the least expensive way troller to produce a programmed motion or hold a to generate continuous rotary motion. However, fixed position. The controller requires sensors on the they are limited to a few standard speeds that are a link being moved to provide feedback information on function of the electric line frequency. In North its position, velocity, and acceleration. These motors America the line frequency is 60 Hz, which corre- have lower power capacity than nonservomotors and sponds to achievable speeds of 3600, 1800, 900, 720, are significantly more expensive, but they can be used and 600 rpm. Single-phase motors are used in resi- for machines demanding precisely guided motion, dential applications and are available from 1/50 to such as robots. 2 hp. Three-phase motors are more efficient, but Air or hydraulic motors also produce continuous mostly limited to industrial applications because rotary motion and are similar to electric motors, but they require three-phase power service. They are have more limited applications. This is due to the available from 1/4 to 500 hp. need for compressed air or a hydraulic source. These Electric motors (DC) also produce continuous rotary drive devices are mostly used within machines, such motion. The speed and direction of the motion can as construction equipment and aircraft, where high- be readily altered, but they require power from a gen- pressure hydraulic fluid is available. erator or a battery. DC motors can achieve extremely Hydraulic or pneumatic cylinders are common com- high speeds––up to 30,000 rpm. These motors are ponents used to drive a mechanism with a limited most often used in vehicles, cordless devices, or in linear stroke. Figure 1.20a illustrates a hydraulic applications where multiple speeds and directional cylinder. Figure 1.20b shows the common kinematic control are required, such as a sewing machine. representation for the cylinder unit. Introduction to Mechanisms and Kinematics 13 Piston Rod Pin joint Cylinder Link B Link A Sliding (piston/rod) Pin joint (cylinder) joint (a) (b) FIGURE 1.20 Hydraulic cylinder. The cylinder unit contains a rod and piston assembly more expensive than cylinders if air or hydraulic that slides relative to a cylinder. For kinematic pur- sources are available. Similar to cylinders, screw actu- poses, these are two links (piston/rod and cylinder), ators also have provisions for pin joints at the two connected with a sliding joint. In addition, the ends. Therefore, the kinematic diagram is identical to cylinder and rod end usually have provisions for pin Figure 1.20b. joints. Manual, or hand-operated, mechanisms comprise a large Screw actuators also produce a limited linear stroke. number of machines, or hand tools. The motions These actuators consist of a motor, rotating a screw. A expected from human “actuators” can be quite com- mating nut provides the linear motion. Screw actua- plex. However, if the expected motions are repetitive, tors can be accurately controlled and can directly caution should be taken against possible fatigue and replace cylinders. However, they are considerably stain injuries. EXAMPLE PROBLEM 1.6 Figure 1.21 shows an outrigger foot to stabilize a utility truck. Draw a kinematic diagram, using the bottom of the sta- bilizing foot as a point of interest. Also compute the degrees of freedom. FIGURE 1.21 Outrigger for Example Problem 1.6. SOLUTION: 1. Identify the Frame During operation of the outriggers, the utility truck is stationary. Therefore, the truck is designated as the frame. The motion of all other links is determined relative to the truck. The frame is numbered as link 1. 2. Identify All Other Links Careful observation reveals three other moving parts: Link 2: Outrigger leg Link 3: Cylinder Link 4: Piston/rod 3. Identify the Joints Three pin joints are used to connect these different parts. One connects the outrigger leg with the truck frame. This is labeled as joint A. Another connects the outrigger leg with the cylinder rod and is labeled as joint B. The last pin joint connects the cylinder to the truck frame and is labeled as joint C. One sliding joint is present in the cylinder unit. This connects the piston/rod with the cylinder. It is labeled as joint D. 14 CHAPTER ONE 4. Identify Any Points of Interest The stabilizer foot is part of link 2, and a point of interest located on the bottom of the foot is labeled as point of interest X. 5. Draw the Kinematic Diagram The resulting kinematic diagram is given in Figure 1.22. C 3 1 D B A 4 2 X FIGURE 1.22 Kinematic diagram for Example Problem 1.6. 6. Calculate Mobility To calculate the mobility, it was determined that there are four links in this mechanism, as well as three pin joints and one slider joint. Therefore, n = 4, jp = (3 pins + 1 slider) = 4, j h = 0 and M = 3(n - 1) - 2jp - j h = 3(4 - 1) - 2(4) - 0 = 1 With one degree of freedom, the outrigger mechanism is constrained. Moving only one link, the piston, precisely positions all other links in the outrigger, placing the stabilizing foot on the ground. 1.8 COMMONLY USED LINKS model of the eccentric crank. The advantage of the eccen- tric crank is the large surface area of the moving pin, which AND JOINTS reduces wear. 1.8.1 Eccentric Crank On many mechanisms, the required length of a crank is so 1.8.2 Pin-in-a-Slot Joint short that it is not feasible to fit suitably sized bearings at the A common connection between links is a pin-in-a-slot two pin joints. A common solution is to design the link as an joint, as shown in Figure 1.24a. This is a higher-order joint eccentric crankshaft, as shown in Figure 1.23a. This is the because it permits the two links to rotate and slide relative design used in most engines and compressors. to each other. To simplify the kinematic analysis, primary The pin, on the moving end of the link, is enlarged joints can be used to model this higher-order joint. The such that it contains the entire link. The outside circumfer- pin-in-a-slot joint becomes a combination of a pin joint ence of the circular lobe on the crankshaft becomes the and a sliding joint, as in Figure 1.24b. Note that this moving pin joint, as shown in Figure 1.23b. The location of involves adding an extra link to the mechanism. In both the fixed bearing, or bearings, is offset from the eccentric cases, the relative motion between the links is the same. lobe. This eccentricity of the crankshaft, e, is the effective However, using a kinematic model with primary joints length of the crank. Figure 1.23c illustrates a kinematic facilitates the analysis. e e e (a) Eccentric crankshaft (b) Eccentric crank (c) Eccentric crank model FIGURE 1.23 Eccentric crank. Introduction to Mechanisms and Kinematics 15 1.8.3 Screw Joint A screw joint, as shown in Figure 1.25a, is another common connection between links. Screw mechanisms are discussed in detail in Chapter 12. To start with, a screw joint permits two relative, but dependent, motions between the links being joined. A specific rotation of one link will cause an associ- ated relative translation between the two links. For example, (a) Actual pin-in-a-slot joint (b) Pin-in-a-slot model turning the screw one revolution may move the nut along FIGURE 1.24 Pin-in-a-slot joint. the screw threads a distance of 0.1 in. Thus, only one inde- pendent motion is introduced. (a) Actual screw joint (b) Screw modeled as a slider FIGURE 1.25 Screw joint. A screw joint is typically modeled with a sliding joint, as An actuator, such as a hand crank, typically produces shown in Figure 1.25b. It must be understood that out-of- the out-of-plane rotation. A certain amount of rotation will plane rotation occurs. However, only the relative translation cause a corresponding relative translation between the links between the screw and nut is considered in planar kinematic being joined by the screw joint. This relative translation is analysis. used as the “driver” in subsequent kinematic analyses. EXAMPLE PROBLEM 1.7 Figure 1.26 presents a lift table used to adjust the working height of different objects. Draw a kinematic diagram and compute the degrees of freedom. FIGURE 1.26 Lift table for Example Problem 1.7. SOLUTION: 1. Identify the Frame The bottom base plate rests on a fixed surface. Thus, the base plate will be designated as the frame. The bearing at the bottom right of Figure 1.26 is bolted to the base plate. Likewise, the two bearings that support the screw on the left are bolted to the base plate. From the discussion in the previous section, the out-of-plane rotation of the screw will not be considered. Only the relative translation of the nut will be included in the kinematic model. Therefore, the screw will also be considered as part of the frame. The motion of all other links will be determined relative to this bottom base plate, which will be numbered as link 1. 16 CHAPTER ONE 2. Identify All Other Links Careful observation reveals five other moving parts: Link 2: Nut Link 3: Support arm that ties the nut to the table Link 4: Support arm that ties the fixed bearing to the slot in the table Link 5: Table Link 6: Extra link used to model the pin in slot joint with separate pin and slider joints 3. Identify the Joints A sliding joint is used to model the motion between the screw and the nut. A pin joint, designated as point A, connects the nut to the support arm identified as link 3. A pin joint, designated as point B, connects the two sup- port arms––link 3 and link 4. Another pin joint, designated as point C, connects link 3 to link 6. A sliding joint joins link 6 to the table, link 5. A pin, designated as point D, connects the table to the support arm, link 3. Lastly, a pin joint, designated as point E, is used to connect the base to the support arm, link 4. 4. Draw the Kinematic Diagram The kinematic diagram is given in Figure 1.27. C D 5 6 B 3 4 A E 2 1 FIGURE 1.27 Kinematic diagram for Example Problem 1.7. 5. Calculate Mobility To calculate the mobility, it was determined that there are six links in this mechanism. There are also five pin joints and two slider joints. Therefore n = 6 jp = (5 pins + 2 sliders) = 7 j h = 0 and M = 3(n - 1) - 2j p - j h = 3(6 - 1) - 2(7) - 0 = 15 - 14 = 1 With one degree of freedom, the lift table has constrained motion. Moving one link, the handle that rotates the screw, will precisely position all other links in the device, raising or lowering the table. 1.9 SPECIAL CASES OF THE MOBILITY EQUATION Mobility is an extremely important property of a mecha- nism. Among other facets, it gives insight into the number of actuators required to operate a mechanism. However, to obtain correct results, special care must be taken in using the Gruebler’s equation. Some special conditions are presented (a) Three rotating links (b) Two rotating and one sliding link next. FIGURE 1.28 Three links connected at a common pin joint. 1.9.1 Coincident Joints one pin may be used to connect all three links. However, by Some mechanisms have three links that are all connected at a definition, a pin joint connects two links. common pin joint, as shown in Figure 1.28. This situation For kinematic analysis, this configuration must be mathe- brings some confusion to kinematic modeling. Physically, matically modeled as two separate joints. One joint will Introduction to Mechanisms and Kinematics 17 connect the first and second links. The second joint will then come together at a common pin, the joint must be modeled as connect the second and third links. Therefore, when three links two pins. This scenario is illustrated in Example Problem 1.8. EXAMPLE PROBLEM 1.8 Figure 1.29 shows a mechanical press used to exert large forces to insert a small part into a larger one. Draw a kinematic diagram, using the end of the handle as a point of interest. Also compute the degrees of freedom. FIGURE 1.29 Mechanical press for Example Problem 1.8. SOLUTION: 1. Identify the Frame The bottom base for the mechanical press sits on a workbench and remains stationary during operation. Therefore, this bottom base is designated as the frame. The motion of all other links is determined relative to the bottom base. The frame is numbered as link 1. 2. Identify All Other Links Careful observation reveals five other moving parts: Link 2: Handle Link 3: Arm that connects the handle to the other arms Link 4: Arm that connects the base to the other arms Link 5: Press head Link 6: Arm that connects the head to the other arms 3. Identify the Joints Pin joints are used to connect the several different parts. One connects the handle to the base and is labeled as joint A. Another connects link 3 to the handle and is labeled as joint B. Another connects link 4 to the base and is labeled as C. Another connects link 6 to the press head and is labeled as D. It appears that a pin is used to connect the three arms—links 3, 4, and 6—together. Because three separate links are joined at a common point, this must be modeled as two separate joints. They are labeled as E and F. A sliding joint connects the press head with the base. This joint is labeled as G. 4. Identify Any Points of Interest Motion of the end of the handle is desired and is labeled as point of interest X. 5. Draw the Kinematic Diagram The kinematic diagram is given in Figure 1.30. 6. Calculate Mobility To calculate the mobility, it was determined that there are six links in this mechanism, as well as six pin joints and one slider joint. Therefore, n = 6, j p = (6 pins + 1 slider) = 7, j h = 0