Mechatronics Module 2 PDF
Document Details
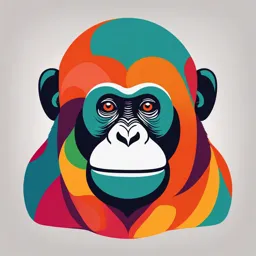
Uploaded by UnrivaledSugilite5134
M.DIT Polytechnic College
Tags
Summary
This document covers core themes in mechatronics including types of mechanical actuators, a review of kinematics chains, the Geneva mechanism, motor selection, and hydraulic and pneumatic systems. It provides detailed explanations of how different aspects of mechatronics work, and the document includes diagrams.
Full Transcript
MECHATRONICS MODULE 2 MECHANICAL ACTUATORS The mechanical actuator is a device that uses a power source to attain physical movement. These actuators are important & available nearly on each automated machine. The power sources used in these actuators are; electric current, pneumatic & hydraulic...
MECHATRONICS MODULE 2 MECHANICAL ACTUATORS The mechanical actuator is a device that uses a power source to attain physical movement. These actuators are important & available nearly on each automated machine. The power sources used in these actuators are; electric current, pneumatic & hydraulic which are operated manually or turned ON/OFF through an automated system. The mechanical actuator’s function is to change the motion from rotary to linear with the help of gearing at a different speed WORKING PRINCIPLE OF MECHANICAL ACTUATORS The working principle of a mechanical actuator is to perform the movement by changing rotary motion into linear motion. So the mechanical actuator operation mainly depends on structural component combinations like rails & gears, or chains & pulleys. MECHANICAL ACTUATOR TYPES There are mainly three types of mechanical actuators available in the market 1) Pneumatic Actuators 2) Hydraulic Actuator 3) Electric Actuator PNEUMATIC ACTUATORS A pneumatic actuator uses pressurized gas or compressed air to form a controlled movement. These actuators are versatile &can be modified to use in any project. The main advantage of this actuator is very simple to utilize and is a secure alternative to both hydraulic & electric actuators as they do not need electricity or ignition to operate. The main drawback of this actuator is that a compressor should run continuously to maintain working pressure whether the device is used or not. HYDRAULIC ACTUATOR Hydraulic mechanical actuator uses liquid pressure to make a mechanical movement. So these actuators are mainly used whenever a significant amount of power is required for a system or machine to function. These are commonly available in heavy machinery where hydraulic power is simply controlled through the amount of liquid within a cylinder. When the fluid is increased then pressure is created and pressure is decreased through decreasing fluid. ELECTRIC ACTUATOR An electric actuator is used to change the energy from electrical to mechanical from an electrical power source. An electric actuator is used for valve operation, food & beverage manufacturing, material handling & cutting equipment. Generally, these are very easy to maintain as compared to hydraulic actuator & provides a high range of precision. KINEMATICS CHAINS ▪ Definitions: Each part of a mechanism which has motion relative to some other part is termed a link A link should be capable of transmitting the required force with negligible deformation Fig 8.4 shows examples of links with two or more nodes “points of attachment to other links” A joint is a connection between two or more links at their Links: (a) with two nodes, (b) with three nodes and which nodes, (c) with four nodes allows some motion between the connected links KINEMATICS CHAINS Examples of links: levers, cranks, connecting rods & pistons sliders, pulleys, belts and shafts. A sequence of joints and links is known as kinematics chain. Consider motor car engine where the reciprocating motion of a piston is transformed into rotational motion of a crankshaft on bearings mounted in a fixed frame. Link 1 crankshaft, Link 2 the connecting rod, Link 3 the fixed frame, Link4 the slider i.e. the piston which move relative to the fixed Figure 8.5 Simple engine mechanism frame KINEMATICS CHAINS The design of many mechanisms are based on two basic forms of kinematic chains: the four bar chain and the slider –crank chain KINEMATICS CHAINS It consists of four links connected to give four joints about which turning can occur. The No of forms of the four – bar chain is produced by altering the relative lengths of the links. Grashof condition: If (length of shortest + longest) is less than or equal to the sum of the two other links, then at least one link will be capable of making a full revolution w.r.t the fixed link Double lever mechanism lever crank mechanism double crank mechanism KINEMATICS CHAINS Slider–crank mechanism It consists of crank, connecting rod and a slider which show simple engine mechanism. Link 3: is fixed i.e no relative movement between the centre of rotation of the Crank and the housing in which the piston slides Link1: the crank that rotates Link2: connecting rod Link4: the slider which moveS relative to the fixed link. So when the piston moves backwards and forwards, the crank (link1) is forced to rotate, hence the mechanism transforms an input of backwards and forwards motion into rotational motion GENEVA MECHANISM The Geneva drive is a gear mechanism that translates a continuous rotation movement into intermittent rotary motion. There are three basic types of Geneva motion mechanisms namely external, internal and spherical. External Geneva Mechanism The rotating drive wheel is usually equipped with a pin that reaches into a slot located in the other wheel (driven wheel) that advances it by one step at a time. The drive wheel also has an elevated circular blocking disc that "locks" the rotating driven wheel in position between steps. GENEVA MECHANISM Internal Geneva Mechanism An internal Geneva drive is a variant on the design. The axis of the drive wheel of the internal drive can have a bearing only on one side. The angle by which the drive wheel has to rotate to effect one step rotation of the driven wheel is always smaller than 180° in an external Geneva drive and always greater than 180° in an internal one, where the switch time is therefore greater than the time the driven wheel stands still. GENEVA MECHANISM Spherical Geneva Mechanism In a spherical Geneva drive, the driven wheel is spherical and is connected to the rotating drive wheel externally. The driving and driven wheels are on perpendicular shafts. SELECTION OF A MOTOR The selection of a driving motor depends primarily on the conditions under which it has to operate and the type of load it has to handle. Main guiding factors for such a selection are as follows: (a) Electrical characteristics (b) Mechanical considerations (c) Size and rating of motors d) Cost SELECTION OF A MOTOR a) Electrical characteristics 1. Starting characteristics 2. Running characteristics 3. Speed control 4. Braking (b) Mechanical considerations 1. Type of enclosure 2. Type of bearings 3. Method of power transmission 4. Type of cooling 5. Noise level SELECTION OF A MOTOR Bearings These are used for supporting the rotating parts of the machines and are of two types: 1. Ball or roller bearings 2. Sleeve or bush bearings (a) Ball Bearings Up to about 75kW motors, ball bearings are preferred to other bearings because of their following advantages: 1. They have low friction loss 2. They occupy less space 3. They require less maintenance 4. Their use allows much smaller air-gap between the stator and rotor of an induction motor 5. Their life is long. Their main disadvantages are with regard to cost and noise particularly at high motor speeds. (b) Sleeve Bearings These are in the form of self-aligning porous bronze bushes for fractional kW motors and in the form of journal bearings for larger motors. Since they run very silently, they are fitted on super-silent motors used for driving fans and lifts in offices or other applications where noise must be reduced to the absolute minimum. SELECTION OF A MOTOR c) Size and rating of motors 1. Requirement for continuous, intermittent or variable load cycle 2. Overload capacity (d) Cost 1. Capital cost 2. Running cost HYDRAULIC AND PNEUMATIC SYSTEMS ▪ Hydraulic and pneumatic systems are two types of fluid power systems used in various industrial applications to transmit power. Both systems utilize the principles of fluid mechanics to generate, control, and transmit power. Here's an overview of each system: HYDRAULIC SYSTEM A hydraulic system circulates the same fluid repeatedly from a fixed reservoir that is part Of the prime mover. The fluid is an almost non-compressible liquid, so the actuators it drives can be controlled to very accurate positions, speeds, or forces. Most hydraulic systems use mineral oil for the operating media but other fluids such as water, ethylene glycol, or synthetic types are not uncommon. Hydraulic oil is used because it can handle high pressure and has good lubricating properties. Working Principle: Pascal's law is fundamental to hydraulic systems. It states that any change in pressure applied at any point in a confined fluid is transmitted undiminished throughout the fluid. HYDRAULIC SYSTEM Components: Hydraulic pump: Converts mechanical energy into hydraulic energy. Hydraulic cylinder: Converts hydraulic energy into mechanical energy. Control valves: Regulate the flow and direction of hydraulic fluid. Hydraulic reservoir: Stores hydraulic fluid. Hydraulic hoses and pipes: Transmit fluid between components. HYDRAULIC SYSTEM Functions of the components shown in Fig. 1.1 are as follows: 1. The hydraulic actuator is a device used to convert the fluid power into mechanical power to do useful work. The actuator may be Of the linear type (e.g., hydraulic cylinder) or rotary type(e.g., hydraulic motor) to provide linear or rotary motion, respectively. 2. The hydraulic pump is used to force the fluid from the reservoir to rest of the hydraulic circuit by converting mechanical energy into hydraulic energy. 3. Valves are used to control the direction, pressure and flow rate of a fluid flowing through the circuit. 4. External power supply (motor) is required to drive the pump. 5. Reservoir is used to hold the hydraulic liquid, usually hydraulic Oil. 6. Piping system carries the hydraulic oil from one place to another. 7. Filters are used to remove any foreign particles So as keep the fluid System clean and efficient, as well as avoid damage to the actuator and valves. 8. pressure regulator regulates (i.e., maintains) the required level Of pressure in the hydraulic fluid. HYDRAULIC SYSTEM Working of Hydraulic System The piping shown in Fig. 1.1 is of closed-loop type with fluid transferred from the storage tank to one side Of the piston and returned back from the other side Of the piston to the tank. Fluid is drawn from the tank by a pump that produces fluid flow at the required level of pressure. If the fluid pressure exceeds the required level, then the excess fluid returns back to the reservoir and remains there until the pressure acquires the required level. ▪ Cylinder movement is controlled by a three-position change over a control valve. ▪ When the piston Of the valve is changed to upper position, the pipe pressure line is connected to port A and thus the load is raised. ▪ When the position of the valve is changed to lower position, the pipe pressure line is connected to port B and thus the load is lowered. ▪ When the valve is at centre position, it locks the fluid into the cylinder (thereby holding it in position) and dead-ends the fluid line (causing all the pump output fluid to return to tank via the pressure relief) HYDRAULIC SYSTEM Advantages: High power density. Precise control of movement and force. Well-suited for heavy-duty applications. Applications: Heavy machinery (construction equipment, excavators). Hydraulic presses. Aircraft control systems. PNEUMATIC SYSTEM Most pneumatic circuits run at IOW power usually around 2 to 3 horsepower. Two main advantages of air-operated circuits are their low initial cost and design simplicity. Uses compressible air or other gases. Working Principle: Boyle's law and Charles's law are fundamental to pneumatic systems. Boyle's law states that the pressure of a gas is inversely proportional to its volume. Charles's law states that the volume of a gas is directly proportional to its absolute temperature. PNEUMATIC SYSTEM Components: ▪ Compressor: Compresses air to the required pressure. ▪ Pneumatic cylinder: Converts compressed air into mechanical energy. ▪ Control valves: Direct the flow of compressed air. ▪ Air reservoir: Stores compressed air. ▪ Air hoses and pipes: Transmit compressed air between components. PNEUMATIC SYSTEM Functions of the components shown in Figure are as follows; 1. The pneumatic actuator converts the fluid power into mechanical power to perform useful work. 2.The compressor is used to compress the fresh air drawn from the atmosphere. 3.The storage reservoir is used to Store a given volume Of compressed air. 4.The valves are used to control the direction, flow rate and pressure of compressed air. 5.External power supply (motor) is used to drive the compressor. 6.The piping system carries the pressurized air from one location to another. PNEUMATIC SYSTEM Working of Pneumatic System Air is drawn from the atmosphere through an air filter and raised to required pressure by an air compressor. As the pressure rises, the temperature also rises; hence, an air cooler is provided to cool the air with some preliminary treatment to remove the moisture. The treated pressurized air then needs to get stored to maintain the pressure. With the storage reservoir, a pressure switch is fitted to start and stop the electric motor when pressure falls and reaches the required level, respectively. The three-position change over the valve delivering air to the cylinder operates in a way similar to its hydraulic circuit PNEUMATIC SYSTEM Advantages: Lightweight and easy to install. Cost-effective. Safe for use in certain environments (non-explosive). Applications: Manufacturing automation (conveyors, robotic arms). Automotive systems (brake systems, suspension). Packaging machinery. COMPARISON BETWEEN A HYDRAULIC AND A PNEUMATIC SYSTEM LINEAR ACTUATORS Single acting hydraulic and pneumatic cylinder (actuator) The simplest Of linear actuator is the single acting hydraulic (or Pneumatic) cylinder. In this device. the pressurized fluid is admitted through only one side. So this cylinder will produce work in only one direction. The return Stroke is actuated by a string or gravity Fig. LINEAR ACTUATORS It consists or a piston inside a cylinder body called a barrel. The piston rod is attached to the one end Of the piston. The piston rod extends Out during extension and inside cylinder during retraction. Inlet is provided at the other end of the cylinder. Single acting cylinders' pistons do not retract but it is by using gravity force (or) using compression spring as shown in the following Fig. 2.2 LINEAR ACTUATORS Double acting Hydraulic and Pneumatic cylinder (actuator) In this double acting cylinders, (Fig. 2.3) the pressurized liquid is admitted in both sides of the piston alternately. Work is performed during forward motion as well as backward motion of the piston. To prevent leakage, seals are provided in five locations. Extend ROTARY ACTUATORS -HYDRAULIC PUMPS Pumps are used to supply the high pressure that the mechatronic system requires. Three types are most commonly used: (a) the gear pump (b) the vane pump (c) the piston pump HYDRAULIC PUMPS Gear Pump Gear pumps are used in hydraulic systems. For a clockwise rotation of the upper gear as shown in Figure 10.2, fluid is carried between the gear teeth in the same direction from the inlet to the high-pressure discharge side of the pump. The meshing teeth seal the fluid and prevent it from returning to the low-pressure side. This type of pump is cheap but becomes troublesome at high operating speeds and pressures. HYDRAULIC PUMPS Vane Pump ▪ Vane pumps are used in hydraulic systems. When the rotor rotates in a counter clockwise direction a large amount of fluid is carried from the inlet to the outlet. ▪ This results from the eccentricity of the center of the rotor with respect to that of the housing. ▪ The net flow of fluid is a function of the eccentricity and when it is varied, the vane pump can then be used as a variable-delivery pump. HYDRAULIC PUMPS Piston Pump The pistons are parallel to and located in the rotor, which is axially driven by the shaft. HYDRAULIC VALVES Fluid power is controlled primarily through the use of control devices called valves. Hydraulic and pneumatic systems require control valves to direct and regulate the flow of fluid from pump (or compressor) to hydraulic cylinders (or) hydraulic motors. The selection of these control devices depends on the type, size, actuating technique and remote - control capability. There are three basic types of control valves. 1. Direction Control Valve 2. Pressure Control Valve 3. Process or Flow Control Valve DIRECTION CONTROL VALVE ▪ Pneumatic and hydraulic systems use directional control valves to direct the flow of fluid through a system. ▪ They are not intended to vary the rate of flow of fluid but are either completely open or completely closed, i.e. on/off devices. Such on/off valves are widely used to develop sequenced control systems. They might be activated to switch the fluid flow direction by means of mechanical, electrical or fluid pressure signals. DIRECTION CONTROL VALVE Direction Actuator Direction Control Valve for Hydraulic System Direction Control Valve for Pneumatic System Operating principle of Direction Control Valves (DCV) The load is connected to the ports A and B and the supply from the pump to the port P. The fluid is returned the tank from the port T. TO extend the ram, port P and B are connected to deliver fluid and ports A and T are connected to return fluid to the tank. To retract the ram, the ports P and A are Connected to deliver fluid and ports B and T to return the fluid to the tank. Most Of the DCV use a sliding spool to change the path of flow through valve. For a given position Of the Spool, a unique flow path configuration exists within the valve. Direction control valves operate with either two position of the spool (or) three position of the spool. Directional control valves can be classified in a number of ways: ▪ According to type Of construction: 1. Poppet valves 2. Spool valves ▪ According to Function 1. Check valve 2. 2/2 valve 3. 3/2valve 4. 4/2 valve 5. 4/3 valve 6. 5/3 valve According to Method Of Actuation. Manual actuation 1. Palm Operated 2. Push Button Operated 3. Hand Lever Operated 4. Foot Pedal Operated 5. Cam Operated Pilot Operated 1. Single Pilot Valve 2. Double Pilot Valve Solenoid (Electrical) Operated 1. Single Solenoid Valve 2. Double Solenoid Valve Poppet valves ▪ A poppet valve is a type of directional control valve commonly used in hydraulic and pneumatic systems. ▪ It consists of a cylindrical plug, called a poppet, which moves up and down or back and forth within a seating area to control the flow of fluid. ▪ Poppet valves are known for their simplicity and reliability, making them suitable for various applications. ▪ The poppet valve consists of a movable element (the poppet) and a stationary seat. ▪ The poppet is usually a cylindrical or tapered plug that fits into a corresponding seat. Operation: ▪ The poppet moves within the valve body to either block or allow fluid flow through the valve. ▪ The movement of the poppet is controlled by external forces such as springs, solenoids, or pilot pressure. Applications: Poppet valves are used in a variety of applications, including hydraulic and pneumatic systems, as well as in internal combustion engines for controlling the intake and exhaust of gases. Spool valves ▪ A common type of directional control valve is the spool valve. A Spool moves horizontally within the valve body to control the flow. Figure shows a particular form of spool valve. In (a) the air supply is connected to port P and it is closed by the spool. The port A is connected to port T which is the exhaust. When the spool is moved to the left, the air supply flows from port P to port A and port T is closed. Thus the movement of the spool has allowed the air to flow out of the system and then be reversed to flow into the system. Rotary spool valves have a rotating spool which, when it rotates, opens and closes ports in a similar way. TWO WAY SPOOL VALVES WITH TWO POSITIONS, (2/2 VALVE) ▪ The simplest type of directional control valve valve which is a two-way valve because it contains two ports. ▪ Two way valves have only two ports as shown in Figure. ▪ These valves are also known as on-off valves because they allow the fluid flow only in direction. ▪ Normally, the valve is closed. These valves are available as normally open and normally closed function. These are the simplest type of spool valve THREE-WAY VALVE ▪ When a valve has one pressure port, one tank port and one actuating port as shown in Figure, it is known as three way valve. ▪ In this valve, the pressure port pressurizes one port and exhausts another one. As shown in figures, only one actuator port is opened at a time. ▪ In some cases a neutral position is also available when both the ports are blocked. ▪ Generally, these valves are used to operate single acting cylinders FOUR WAY VALVES WITH THREE POSITIONS (4/3 VALVE) ▪ Fig shows three position four way (4/3) valve with closed center position. It is used in double-acting cylinders to perform advance, hold and return operation to the piston. ▪ These types of valves have three switching positions. The center position is closed one. In this position both working ports A and B are closed. Thus cylinder becomes in hold condition. Check Valve ▪ A check valve, also known as a non-return valve or one-way valve, is a mechanical device designed to allow fluid or gas to flow through it in one direction only. ▪ It prevents reverse flow or backflow of the medium, ensuring that it moves in the intended direction. PILOT OPERATED CHECK VALVE ▪ Another type of check valve is the pilot operated check valve. ▪ The pilot operated check valve always permits free now in one direction but permits now in the normally blocked opposite direction only if pilot pressure pushes the pilot piston downward. ▪ In this construction, the pilot piston is attached (or) integral part of the valve poppet. ▪ The spring holds the poppet seated in a no flow condition by pushing against the piston Two way valve The flow can go through the valve in two unique ways depending on the spool position. Spool Position 1 Flow can go from P to B The ports A and T are blocked. Spool position 2 Flow can also go from P to A. The ports B and T are blocked. FOUR WAY VALVE The flow can go through the valve in four unique ways depending On the spool position. Spool position 1: Flow can go from P to A and B to T. Spool position 2: Flow can go from A to T and P to B. ACTUATION OF VALVES Direction control valves may be actuated by a variety of methods. Actuation is the method of moving the valve element from one position to another. There are four basic methods of actuation: Manual, mechanical, solenoid-operated and pilot-operated. Several combinations of actuation are possible using these four basic methods. ▪ Manually operated In manually operated DCVs, the spool is shifted manually by moving a handle pushing a button or stepping on a foot pedal. When the handle is not operated, the spool returns to its original position by means of a spring. ▪ Mechanically operated The spool is shifted by mechanical linkages such as cam and rollers. Solenoid operated When an electric coil or a solenoid is energized, it creates a magnetic force that pulls the armature into the coil. This causes the armature to push the spool of the valve. Pilot operated A DCV can also be shifted by applying a pilot signal (either hydraulic or pneumatic) against a piston at either end of the valve spool. When pilot pressure is introduced, it pushes the piston to shift the spool. SYMBOLS FOR ACTUATION PRESSURE CONTROL VALVE ▪ A pressure control valve is a device used in various industries and systems to regulate or control the pressure of a fluid, such as a gas or liquid, within a system. ▪ These valves are crucial for maintaining a stable and safe operating pressure in different processes. Here are some key points about pressure control valves: ▪ Function: The primary function of a pressure control valve is to maintain a specific pressure level within a system. It achieves this by either opening or closing in response to changes in pressure. APPLICATIONS: ▪ Water and Wastewater Systems: Used to control water pressure in municipal water supply systems. ▪ Industrial Processes: Employed in manufacturing and processing industries to control pressure in various fluid systems. ▪ Oil and Gas Industry: Utilized in pipelines and wellheads to regulate pressure. CLASSIFICATION OF PRESSURE CONTROL VALVE The pressure control valves diverting the fluid are I. Pressure Relief valve 2.Compound Relief valve 3.Pressure Reducing valve 4.Unloading valve 5.Sequence valve 6.Counter balance valves 1) PRESSURE RELIEF VALVE ▪ The pressure control valves are used in hydraulic circuits to maintain desired pressure in various parts of the circuits. ▪ The most widely used type of pressure control valve is the pressure relief valve. It is normally a closed valve. ▪ Its main function is to limit the pressure to a specified maximum value by diverting pump flow back to the tank. WORKING It is also employed as a backup device when the main pressure control device fail. A poppet is held seated inside the valve by a heavy spring. When the system pressure reaches enough high pressure, the poppet is forced off its seat. This allows the flow through the outlet to tank as long as the high pressure level is maintained. The adjusting screw cap is used to vary the spring force and thus to vary the Cracking pressure at which the valve begins to open. A partial hydraulic circuit consisting of pump and pressure relief valve is shown symbolically. 2) SEQUENCE VALVE ▪ A sequence valve is used to perform two operations in sequence one after the other. ▪ For example cylinder 1 extend first and then cylinder two will extend and vise versa Construction ▪ It has an adjusting screw , a spring and a conical poppet, which are mounted inside the valve body as shown in figure. ▪ The valve has one inlet port and two outlet ports, outlet port “1” and outlet port “2”. Working When the fluid under pressure is supplied to inlet port of sequence valve, It flows directly to outlet port 1. Hence cylinder 1 extend first. By the end of extension of cylinder 1 ,pressure in the line increase and sequence valve opens to allow fluid to flow to port 2 , cylinder 2 extends CIRCUIT DIAGRAM 3) PRESSURE REDUCING VALVE Pressure reducing valve is used to limit its outlet pressure. Reducing valves are used for the operation Of branch circuits, where pressure may vary from the main system pressures. The pressure reducing valve is normally an open type valve. Figure 4.32 shows the pressure reducing valve. Working ▪ The valve consists Of a spring chamber (control chamber) with an adjustable spring to set the pressure as required by the system. ▪ A small opening is provided in the control chamber to drain the Oil that may be collected due to leakage, thereby preventing the failure of valve. ▪ A free flow passage is provided through the valve from inlet to secondary outlet until a signal from the Outlet side tends to throttle the passage through the valve. ▪ The valve operates on principle that pilot pressure from the controlled pressure side opposes an adjustable bias spring normally holding the valve open. ▪ When the two forces are equal, the pressure downstream is controlled at the pressure setting. ▪ Thus, it can be visualized that if the spring has greater force, the valves open wider and if the controlled pressure has greater force, the valves moves towards the spring and throttles the flow. FLOW CONTROL VALVE ▪ Process control valves are used to control various parameters of fluid flow like flow rate, speed etc. (Hence it is also called Flow control valves.) ▪ Flow control valves are used to control the speed of the hydraulic actuators by adjusting the flow rate to these actuators. ▪ Control of fluids is very much necessary since the speed of the machine elements depends on the rate of flow of the pressurized hydraulic fluid. ▪ These valves may be fixed orifice valve, adjustable needle valve, globe valve, gate valve, non-compensated valve (or) compensated valves. DIAPHRAGM ACTUATOR PROCESS CONTROL VALVE ▪ A common form of pneumatic actuator used with process control valves is the diaphragm actuator. ▪ Essentially it consists of a diaphragm with the input pressure signal from the controller on one side and atmospheric pressure on the other, this difference in pressure being termed the gauge pressure. ▪ The diaphragm is made of rubber which is sandwiched in its center between two circular steel discs. The effect of changes in the input pressure is thus to move the central part of the diaphragm, as illustrated in Figure. ▪ This movement is communicated to the final control element by a shaft which is attached to the diaphragm NEEDLE VALVES ▪ Needle valves are used to provide finer control of flow in small diameter piping. ▪ As the name implies, the needle valves have sharp pointed conical disc and matching seat. ▪ Needle valves are normally made up of steel bar. ▪ The needle valves are also used as a stop valve in hydraulic circuit to shut off the flow of fluid from one part of a circuit to another part. ▪ These valves can be adjusted to control the rate of fluid flow. GLOBE VALVE ▪ Globe valves have a round disk to control (or) stop the fluid flow. The globe valve is shown in figure ▪ The flow area of the globe valve is more than that of the needle valve. Hence, globe valve will have a larger flow capacity at a lower pressure drop than a needle valve of the same size. ▪ Needle valves are suitable for throtling ie, the flow area is slowly reduced as the valve is closed, gradually reducing the quantity of fluid passing through the valve. But, the globe valves are not so suitable for throttling function. GATE VALVE ▪ Gate valves are not normally used as flow control valves. Most of the gate valves are used as 'stops' to shut off fluid flow (or) to open the line to full flow. ▪ The gate valve provides a opening with minimum pressure drop. ▪ The simple valves discussed above all are non compensated type i.e. They are not compensated for changes in fluid pressure (or) temperature. ▪ Without compensation, the flow through these simple valves will vary according to the pressure (or) temperature changes of the fluid. CONTROL OF A SINGLE ACTING CYLINDER CONTROL OF A DOUBLE ACTING CYLINDER OPERATION OF A LIFT SYSTEM USING TWO DCVS ▪ Fig shows a lift system operated by two push button operated DCVs. ▪ The cylinder is a single acting cylinder which retracts down due to its self weight. ▪ When the push button of UP DCV is pressed, the pressurized fluid supply flows to cylinder which push the piston outwards. ▪ When the down dcv is pressed fluid in the cylinder is escaped through the vent in the DCV which retracts the cylinder ELECTRICAL ACTUATION SYSTEMS The electrical actuation devices are 1.Switching devices such as mechanical switches, e.g. relays, key boards 2.solid-state switches, e.g. diodes, thyristors, and transistors, where the control signal switches on or off some electrical device, perhaps a heater or a motor. 3.Solenoid type devices where a current through a solenoid is used to actuate a soft iron core, as, for example, the solenoid operated hydraulic/pneumatic valve where a control current through a solenoid is used to actuate a hydraulic/pneumatic how. 4.Drive systems, such as d.c. and a.c. motors, where a current through a motor is used to produce rotation. RELAYS ▪ Relays are electrically operated switches in which changing a current in one electrical circuit switches a current on or off in another circuit. ▪ For the relay shown in Figure , when there is a current through the solenoid of the relay, a magnetic field is produced which attracts the iron armature, moves the push rod, and so closes the normally open (NO) switch contacts and opens the normally closed (NC) switch contacts. ▪ Relays are often used in control systems; the output from the controller is a relatively small current and a much larger current is needed to switch on or off the final correction element, ▪ e.g. the current required by an electric heater in a temperature control system or a motor. ▪ In such a situation they are likely to be used in conjunction with transistors. and Figure (b) shows the type of circuit that might be used. Because relays are inductances, they can generate a back voltage when the energizing current is switched off or when their input switches from a high to low signal. ▪ As a result damage can occur in the connecting circuit. To overcome this problem, a diode is connected across the relay. When the back e.m.f. occurs, the diode conducts and shorts it out. SOLID STATE SWITCHES There are a number of solid-state devices which can be used electronically switch circuits. These include: i. Diodes. ii. Thyristors and triacs. iii. Bipolar transistors. iv. Power MOSFETs. DIODES ▪ The diode has the characteristic shown in Figure and so allows a significant current in one direction only. ▪ A diode can thus be regarded as a ‘directional element’, only passing a current when forward biased, i.e. with the anode being positive with respect to the cathode. ▪ If the diode is sufficiently reverse biased, i.e. a very high voltage, it will break down. If an alternating voltage is applied across a diode, it can be regarded as only switching on when the direction of the voltage is such as to forward bias it and being off in the reverse biased direction ▪ The result is that the current through the diode is half-rectified to become just the current due to the positive halves of the input voltage THYRISTORS The thyristor, or silicon-controlled rectifier (SCR). can be regarded as a diode which has a gate controlling the conditions under which the diode can be Switched on. Figure shows the thyristor characteristic. With the gate current zero, the thyristor passes negligible current when reverse biased (unless sufficiently reverse biased, hundreds of volts, when it breaks down). When forward biased the current is also negligible until the forward breakdown voltage is exceeded. When this occurs the voltage across the diode falls to a low level, about 1 to 2 V, and the current is then only limited by the external resistance in a circuit Once switched on the thyristor remains ON until the forward current is reduced to below a level of a few milliamps. The voltage at which forward breakdown occurs is determined by the current entering the gate, the higher the current the lower the breakdown voltage. The power-handling capability of a thyristor is high and thus it is widely used for switching high power applications. TRIACS The triac is similar to the thyristor and is equivalent to a pair of thyristors connected in reverse parallel on the same chip. The triac can be turned on in either the forward or reverse direction. Figure shows the characteristic. Triacs are simple, relatively inexpensive method of controlling a.c. power Figure shows the type of effect that occurs when a sinusoidal alternating voltage is applied across (a) a thyristor and (b) a triac. Forward breakdown occurs when the voltage reaches the breakdown value and then the voltage across the device remains low. BIPOLAR TRANSISTORS Bipolar transistors come in two forms. the npn and the pnp. Figure shows the symbol for each. For the npn transistor, the main current flows in at the collector and out at the emitter, a controlling signal being applied to the base. The pnp transistor, has the main current flowing in at the emitter and out at the collector, a controlling signal being applied to the base. For a npn transistor connected as shown in Figure (a), the so termed common-emitter circuit, the relationship between the collector current Ic and the potential difference between the collector and emitter Vce is described by the series of graphs shown in Figure (b). When the base current In is zero the transistor is cut off; in this state both the base- emitter and the base-oollector junctions are reverse biased. When the base current is increased, the collector current increases and Vcs decreases as a result of more of the voltage being dropped ELECTRIC MOTORS Electric motors are frequently used as the final control element in positional or speed-control systems. Motors can be classified into two main categories: d.c. motors and a.c. motors, most motors used in modem control systems being d.c. motors. The basic principles involved in the action of a motor are: 1. A force is exened on a conductor in a magnetic field when a current passes through it. For a conductor of length L, carrying a current I in a magnetic field of flux density 8 at right angles to the conductor, the force F equals BIL. 2. When a conductor moves in a magnetic field then an e.m.f. is induced across it. The induced e.m.f.‘e’ is equal to the rate at which the magnetic flux ϕ swept through by the conductor changes (Faraday‘s law), i.e. e = -d ϕ /dt. The minus sign is because the e.m.f. is in such a direction as to oppose the change producing it. (Lenz’s law) DC MOTOR ▪ Figure shows the basic principle of the d.c. motor, a loop of wire which is free to rotate in the field of a permanent magnet. ▪ When a current is passed through the coil, the resulting forces acting on its sides at right angles to the field cause forces to act on those sides to give rotation. However, for the rotation to continue, when the coil passes through the vertical position the current direction through the coil has to be reversed. In the conventional d.c. motor, coils of wire are mounted in slots on a cylinder of magnetic material called the armature. ▪ The armature is mounted on bearings and is free to rotate. It is mounted in the magnetic field produced by field poles. These may be, for small motors, permanent magnets or electromagnets with their magnetism produced by a current through the held coils. ▪ Figure shows the basic principle of a four-pole d.c. motor with the magnetic field produced by current carrying coils. ▪ The ends of each armature coil are connected to adjacent segments of a segmented ring called the commutator with electrical contacts made to the segments through carbon contacts called brushes. ▪ As the armature rotates. the commutator reverses the current in each coil as it moves between the field poles. ▪ This is necessary if the forces acting on the coil are to remain acting in the same direction and so the rotation continue. The direction of rotation of the d.c. motor can be reversed by reversing either the armature current or the field current 1) SERIES WOUND MOTOR ▪ With the series wound motor the armature and fields coils are in series Such a motor exerts the highest starting torque and has the greatest no- load Speed. ▪ With light loads there is a danger that a series wound motor might run at too high a speed. ▪ Reversing the polarity of the supply to the coils has no effect on the direction of rotation of the motor; it will continue rotating in the same direction since both the field and armature currents have been reversed. 2) SHUNT WOUND MOTOR ▪ With the shunt wound motor the armature and held coils are in parallel. ▪ It provides the lowest starting torque, a much lower no-load speed and’ has good speed regulation. ▪ Because of this almost constant Speed regardless of load, shunt wound motors are very widely used. ▪ To reverse the direction of rotation, either the armature or field supplied must be reversed. ▪ For this reason, the separately excited windings are preferable for such a situation. 3) COMPOUND MOTOR ▪ The compound motor has two field windings, one in series With the field and one in parallel. ▪ Compound wound motors aim to get the best features of the series and shunt wound motors, namely a high starting torque and good speed regulation. 4) SEPARATELY EXCITED MOTOR The separately excited motor has separate control of armature and field currents and can be considered to be a special case of the shunt wound motor. A. C. MOTORS Alternating current motors can be classified into two groups, single phase and three phase with each group being further subdivided into induction and synchronous motors. Single-phase motors tend to be used for low power requirements while three phase motors are used for higher powers. Induction motors tend to be cheaper than synchronous motors and are thus very widely used. SINGLE-PHASE SQUIRREL-CAGE INDUCTION MOTOR ▪ The single-phase squirrel-cage induction motor consists of a squirreI-cage rotor, this being copper or aluminium bars that fit into slots in end rings to form complete electrical circuits. ▪ There are no external electrical connections to the rotor. The basic motor consists of this rotor with a stator having a set of windings. ▪ When an alternating current passes through the stator windings an alternating magnetic field is produced. ▪ As a result of electromagnetic induction, e.m.fs are induced in the conductors of the rotor and currents flow in the rotor THREE PHASE INDUCTION MOTOR ▪ The three-phase induction motor is similar to the single-phase induction motor but has a stator with three windings located 120° apart, each winding being connected to one of the three lines of the supply. ▪ Because the three phases reach their maximum currents at different times, the magnetic field can be considered to rotate round the stator poles, completing one rotation in one full cycle of the current. ▪ The rotation of the field is much smoother than with the single-phase motor. The three-phase motor has a great advantage over the single-phase motor of being self-starting. ▪ The direction of rotation is reversed by interchanging any two of the line connections, this changing the direction of rotation of the magnetic field. SYNCHRONOUS MOTORS Synchronous motors have stators similar to those described above for induction motors but a rotor which is a permanent magnet. The magnetic field produced by the stator rotates and so the magnet rotates with it. With one pair of poles per phase of the supply, the magnetic field rotates through 360° in one cycle of the supply and so the frequency of rotation with this arrangement 'is the same as the frequency of the supply. Synchronous motors are used when a precise speed is required. They are not self-starting and some system has to be employed to Stan them. AC. motors have the great advantage over dc motors of being cheaper, more rugged, reliable and maintenance free. However speed control is generally more complex than with d.c. motors. Speed control of ac. motors is based around the provision of a variable frequency supply, since the speed of such motors is determined by the frequency of the supply. STEPPER MOTORS ▪ The stepper motor is a device that produces rotation through equal angles, the so-called steps, for each digital pulse supplied to its input. ▪ Thus, for example, if with such a motor 1 pulse produces a rotation of 6° then 60 pulses will produce a rotation through 360°. There are a number of forms of stepper motor: VARIABLE RELUCTANCE STEPPER Figure shows the basic form of the variable reluctance stepper motor. With this form the rotor is made of soft steel and is cylindrical with four poles, i.e. fewer poles than on the stator. When an opposite pair of windings has current switched to them, a magnetic field is produced with lines of force which pass from the stator poles through the nearest set of poles on the rotor. Since lines of force can be considered to be rather like elastic thread and always trying to shorten themselves, the rotor will move until the rotor and stator poles line up. This is termed the position of minimum reluctance. This form of stepper generally gives step angles of 7.5° or 15°. PERMANENT MAGNET STEPPER ▪ Figure shows the basic form of the permanent magnet motor. The motor shown has a stator with four poles. ▪ Each pole is wound with a field winding, the coils on opposite pairs of poles being in series. Current is supplied from a dc source to the windings through switches. ▪ The rotor is a permanent magnet and thus when a pair of stator poles has a current switched to it, the rotor will move to line up with it. Thus for the currents giving the situation shown in the figure the rotor moves to the 45° position. ▪ If the current is then switched so that the polarities are reversed, the rotor will move a further 45° in order to line up again. ▪ Thus by switching the currents through the coils the rotor rotates in 45° steps. With this type of motor, step angles are commonly l.8°, 7.5°, 15°, 30°, 45° or 90°. HYBRID STEPPER ▪ Hybrid stepper motors combine the features of both the variable reluctance and permanent magnet motors, having a permanent magnet encased in iron caps which are cut to have teeth (Fig. 7.42). ▪ The rotor sets itself in the minimum reluctance position in response to a pair of stator coils being energizsed. ▪ Typical step angles are 0.9° and l.8°. Such stepper motors are extensively used in high accuracy positioning applications, e.g. in computer hard disc drives.