WS 02 - Operations Analysis PDF
Document Details
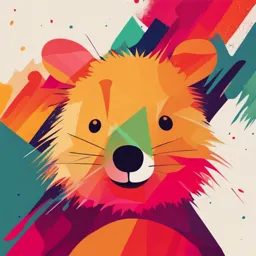
Uploaded by CompliantHeliotrope192
Tags
Summary
This document is a methods engineering and operations analysis study guide. It covers various concepts like methods engineering and operations analysis, their objectives, names, and how to approach methods engineering. It includes steps to define and analyze problems, formulate alternatives, evaluate, and implement solutions. The document is aimed at understanding and improving workplace efficiency and possibly used as a study guide for learners within a higher education environment.
Full Transcript
METHODS ENGINEERING AND OPERATIONS ANALYSIS Methods engineering is the analysis and design of work methods and systems, including the tooling, equipment, technologies, workplace layout, plant layout, and work environment Other names for methods engineering: Work study Work...
METHODS ENGINEERING AND OPERATIONS ANALYSIS Methods engineering is the analysis and design of work methods and systems, including the tooling, equipment, technologies, workplace layout, plant layout, and work environment Other names for methods engineering: Work study Work simplification Methods study Process re-engineering Business process re-engineering Objectives in Methods Engineering Increase productivity and efficiency Reduce cycle time Reduce product cost Reduce labor content Other Objectives Improve customer satisfaction Improve product and/or service quality Reduce lead times and improve work flow Increase flexibility of work system Improve worker safety Apply more ergonomic work methods Enhance the environment (both inside and outside the facility) Operations Analysis Study of an operation or group of related operations for the purpose of analyzing their efficiency and effectiveness so that improvements can be developed relative to specified objectives. Objectives in operations analysis Increase productivity Reduce time and cost Improve safety and quality Methods engineering and operations analysis are very similar, except that methods engineering places more emphasis on design. Methods Engineering Can be divided into two areas: Methods analysis and Methods design. Methods analysis is concerned with the study of an existing method or process. Objectives: Eliminate unnecessary and non-value-adding work elements Combine elements and operations Rearrange elements into more logical sequence Simplify remaining elements and operations Methods design is concerned with either of the following situations: 1. Design of a new method or process Required for new product or service and there is no existing standard Method must be designed from scratch, using best existing practice for similar operations 2. Redesign of an existing method or process based on a previous methods analysis. HOW TO APPLY METHODS ENGINEERING Systematic Approach in Methods Engineering has its basis in the scientific method used in science, research and development, engineering design, and other problem areas. The systematic approach in methods engineering consists of the steps described below. Step 1: Define the Problem and Objectives. The problem in methods engineering study may be low productivity, high cost, inefficient methods, or the need for a new method or a new operation. The objective is the desired improvement or new methods design. Possible objectives are to increase productivity, reduce labor content and cost, improve safety, or develop a new method or new operation. Step 2: Analyze the Problem. Data collection and analysis activities for the type of problem being studied. Activities often used in this step include the following: Identify the basic function of the operation. Gather background information. Observe the existing process or observe similar processes if the problem involves a new work design. Collect data on the existing operation and document the details in a format that provides itself to examination. Conduct experiments on the process. Develop a mathematical model of the process or utilize an existing mathematical model Perform a computer simulation of the process. Use charting techniques. Step 3: Formulate Alternatives. There are always multiple ways to perform a task or accomplish a process, some of which are more efficient and effective than others. The purpose of this step in the problem-solving approach that is not to identify the best alternative but to formulate all of the alternatives that are feasible. Step 4: Evaluate Alternatives and Select the Best. This step consists of a systematic assessment of the alternatives and the selection of the best solution among them, based on the original definition of the problem and objectives. Step 5: Implement the Best Method. Implementation means installing the selected solution: introducing the changes proposed in the existing method or operation, or installing the new method or process. This may involve pilot studies or trials of the new or revised Implementation also includes complete documentation of the new or revised method and replacement of the previous documentation Step 6: Audit the Study. Perform an audit or follow-up on the methods engineering project. How successful was the project in terms of the original problem definition and objectives? What were the implementation issues? What should be done differently in the next methods engineering study? For an organization committed to continuous improvement, answers to these kinds of questions help to fine-tune its problem-solving and decision-making skills. Select the job to be studied Record by collecting data or by direct observation by Challenging purpose, place, sequence, and Examine method of work new methods drawing on contributions of those Develop Method Study concerned To Simplify the job Evaluate results of different alternative solutions and develop more economical methods of doing it Define new method and present it new method and train persons in applying it Install and establish control procedures Maintain Select – Where to Look Poor use of resources Select Bad layout Record Bottlenecks - which are holding up other Examine production operations, or lengthy operations that consume a great deal of Develop time Evaluate Inconsistent quality Define High fatiguing work Install Excessive overtime Maintain Employee’s complaints Select – Economic Considerations Will it pay to begin, or continue, a method Select study of this job? Record Key profit- generating operations Examine Key costly operations Develop Repetitive work - using a great deal of Evaluate labor Define and ones that are likely to run for a long Install time. Long travels Maintain Excessive overtime Select – Technical Considerations Desire to acquire more advanced technology Select Record Extensive paperwork Examine Repetitive work (automation) Develop Hazardous work Evaluate Define Inconsistent quality Install Maintain Select – Human Considerations Workers satisfaction/resentment Select Record Satisfaction level Examine Develop Start with non-controversial Evaluate jobs Define HSE Install Maintain Select – Limiting the Scope Setting boundaries and determining Select content Record One operation or a sequence Examine Develop The whole operation or part Evaluate Which aspect: worker, materials, Define equipment, … etc. Install Maintain Select – Possible Results Increased production rate Reduced cost Select Less labor, materials, or Record Examine equipment Develop Improved quality Evaluate Improved safety Define Reduced scrap Install Maintain Improved standards of cleanliness Basic Data Collection & Analysis Tools 1. Histograms 2. Pareto charts 3. Pie charts 4. Check sheets 5. Defect concentration diagrams 6. Scatter diagrams 7. Cause and effect diagrams Histogram A histogram is a statistical graph consisting of bars representing different values or ranges of values, in which the length of each bar is proportional to the frequency or relative frequency of the value. A useful tool because the analyst can quickly visualize the features of the data, such as: (1)the shape of the distribution, (2)any central trend exhibited by the distribution, (3)approximations of the mean and mode of the distribution, (4)the amount of scatter or spread in the data. Histogram for Data Display Pareto Chart Special form of histogram in which attribute data are arranged according to some criterion such as cost or value Based on Pareto’s Law: “the very important few and the unimportant many” Often identified as the 80%-20% rule 80% of a nation’s wealth is owned by 20% of the population 80% of sales are accounted for by 20% of the Stock Keeping Units 80% of a factory’s production output is concentrated in only 20% of its product models. Select – Pareto Analysis Select Record Examine Develop Evaluate Define Install Maintain To illustrate the point we will consider the following example. Let us assume that a certain enterprise produces 20 different products. Each of these products generates a certain profit. By listing the annual production and profit contribution one obtains the results shown in table 6. The next step consists of rearranging these items in descending order of importance according to profit. The result would then appear like the one shown in table 7. From table 7 it can be seen that three products only, listed as “A items”, account for 60 per cent of the profit. To illustrate the point we will consider the following example. These are the most profitable and any improvement in methods of producing these particular products would reflect highly on profits. They would be a priority for study. Products listed under “B”, which are seven in number, contribute 25 per cent of the profit. They could then assume a second importance, while products “C” would command the last priority since their contribution to profit is minimal. The same type of analysis can be conducted to determine “the most costly products or processes” or “the products or processes that yield the highest waste”. Those would then become a priority for study by the work study specialist. Pie Charts Example: Annual sales revenues and customer distributions for two years Cause and Effect Diagram A graphical-tabular chart used to list and analyze the potential causes of a given problem Can be used to identify which causes are most significant and how to take corrective action against them Also known as a “fishbone diagram” In application, cause and effect diagrams are often developed by worker teams who study operational problems. The diagram provides a graphical means for discussing and analyzing a problem and listing its possible causes in an organized and understandable way. As a starting point in identifying the causes of the problem, six general categories of causes are often used because they are the factors that affect performance of most production and service processes. They are called the 5Ms and 1P Machines. This refers to the equipment and tooling used in the process. Materials. These are the starting materials in the process. Methods. This refers to the procedures, sequence of activities, motions, and other aspects of the method used in the process. Mother Nature. This is for environmental factors such as temperature and humidity that might affect the process. Measurement. This relates to the validity and accuracy of the data collection procedures. People. This is the human factor. Does the worker bring the necessary skills to the process? Cause and Effect Diagram Record- Symbols Operation (Make ready, Do, Put away) Select Inspection Record Examine Transport Develop Evaluate Delay Define Install Maintain Storage Record- Symbols Operation (Make ready, Do, Put away) Select Record Examine Develop Evaluate Define Install Maintain Record- Symbols Select Record Examine Develop Evaluate Define Install Maintain Record- Symbols Select Record Examine Develop Evaluate Define Install Maintain Record- Symbols Select Record Examine Develop Evaluate Define Install Maintain Record- Symbols Select Record Examine Develop Evaluate Define Install Maintain Record- Charts and Diagrams Outline Process Chart Flow Process Chart (Worker, Material, Equipment) Select Two-Handed Process Chart Record Procedure Chart Examine Simultaneous motion Cycle Chart Develop Multiple Activity Chart Evaluate Flow Diagram Define String Diagram Install Cyclegraph Maintain Chronocyclegraph Travel Chart Operation Process Chart Chronological sequence of all operations, inspections, time allowances, materials Depicts entrance and exit of all components and sub-assemblies and products Provides information on the number of employees required time for jobs and inspections Record- Example Outline Chart Turn shank Face both sides Face, turn, cut Remove chip Drill hole Face opposite end Dimensions Final check Dimension and finish Degreasing Straddle mill four flats Cadmium plating Remove burr Final inspection of machining Final check Select Degreasing Record Cadmium plating Final check Examine Develop Assemble and drill Evaluate Fit stop pin Define Install Final check Switch Rotor Maintain Record- Example Select Record Examine Develop Evaluate Define Install Maintain Record- Example Outline Chart Select Record Examine Develop Evaluate Define Install Maintain Operation Process Chart Plywood Pipe 5’ 4 Cutting 5’ 1 Cutting Circular Saw Circular Saw Polishing 6’ 5 3’ 2 Forming Grinding Press Painting 15’ 6 2’ 3 Make Screw Sprayer Drilling 3’ 7 Make Screw I-1 Drilling I-2 Assembly & 10’ 18 Inspection Mannual 42 Record- Example Flow Chart Select Record Examine Develop Evaluate Define Install Maintain Record- Example Flow Chart Select Record Examine Develop Evaluate Define Install Maintain Record- Example Flow Chart Select Record Examine Develop Evaluate Define Install Maintain Record- Example Flow Chart Select Record Examine Develop Evaluate Define Install Maintain Record- Example Flow Chart Select Record Examine Develop Evaluate Define Install Maintain Flow Process Chart More detailed, fit for closer observation of smaller components or assemblies Shows all moves (distances) and storage delays (times) for product movement in plant Aids in the reduction of hidden costs, “Muda.” Can be beneficial for plant layout suggestions Flow Process Chart Similar to OPC, except that more detail that is shown by including transportation and delay The objective is to list every detail and to examine each detail closely necessary or can be improved ? can be combined with another? should the sequence be changed? is the proper person to be doing this activity ? 49 Flow Process Chart- Present Method Process : Prepare Spaghetty Man or Material x Noodles Begins : In Storage Ends : ready to Serve Charter : Ind. Engineering Date : 9/16 Step Symbol Notes 1. Noodle in Shelf 2. Carried to cooker 3. Cook 4. Placed in Bowl Washed in Cooker ? 5. Carried to Sink Very Heavy 6. Washed 7. Bowl Carried to Work Area Very Heavy 8. Placed in Serving Pans Six Pans-Full 9. Meat and Sauce Added to Pans Repeated Six Times 10. Pans Carried to Heater Repeated Six Times 11. Warned 12. Carried to Serving Line Repeated Six Times 50 Flow Process Chart-Proposed Method Process : Prepare Spaghetty Man or Material x Noodles Begins : In Storage Ends : ready to Serve Charter : Ind. Engineering Date : 9/16 Step Symbol Notes 1. Noodle in Shelf 2. Carried to cooker 3. Cooked 4. Washed in Cooker Add a Tap Adjacent to Cooker 5. Meat and Sauce Added to Pans 6. Warmed 7. Placed in Serving Pans Repeated Six Times 12. Carried to Serving Line Repeated Six Times 51 FLOW PROCESS CHART ANALYST PAGE Job Requisition of petty cash D. Kolb 1 of 2 Details of Method Requisition made by department head Put in “pick-up” basket To accounting department Account and signature verified Amount approved by treasurer Amount counted by cashier Amount recorded by bookkeeper Petty cash sealed in envelope Petty cash carried to department Petty cash checked against requisition Receipt signed Petty cash stored in safety box Worker and Machine Process Charts Used to study, analyze, and improve one workstation Shows the time relationship between working cycle of the person and the operating cycle of the machine Reveals idle time for both machines and workers Establishes “TAKT” time Worker-Machine Chart Graphical model of the simultaneous activities of a worker and the equipment he/she operates. Helps identify idle time and costs of both workers and machines. For analyzing alternative worker-machine combinations to determine the most efficient arrangement. Job Photo-Id Cards Date 10/14 Time Time (min) Operator (min) Photo Machine –1 Key in customer data 2.6 Idle on card –2 Feed data card in 0.4 Accept card –3 Position customer for photo 1.0 Idle –4 Take picture 0.6 Begin photo process Worker- –5 Machine Chart –6 Idle 3.4 Photo/card processed –7 –8 Inspect card & trim edges 1.2 Idle –9 Flow Diagram Pictorial representation of the layout of the plant Good supplement to the Flow Process Chart Flow Diagram Gang Process Chart Record- Example Multiple activity Chart Select Record Examine Develop Evaluate Define Install Maintain Record- Example String Diagram Select Record Examine Develop Evaluate Define Install Maintain Record- Example String Diagram Select Record Examine Develop Evaluate Define Install Maintain Record- Example Travel Chart Select Record Examine Develop Evaluate Define Install Maintain Record- Example Two-handed process Chart Select Record Examine Develop Evaluate Define Install Maintain Examine- The Questions Purpose: What is actually done? Why is it necessary? Place: Where? Why? Select Sequence: When? Why? Record Person: Who? Why? Examine Means: How? Why? Develop Evaluate With a view to: Define Eliminate Install Combine or Rearrange Maintain Simplify Examine- Secondary Questions Purpose: What is done? Why is it done? Select What else might be done? Record What should be done? Examine Develop With a view to: Evaluate Eliminate Define Simplify Install Maintain Examine- Secondary Questions Place: Where is it done? Why is it done there? Select where else might it be done? Record Where should it be done? Examine Develop With a view to: Evaluate Combine or Rearrange Define Install Maintain Examine- Secondary Questions Sequence: When is it done? Why is it done then? Select when might it be done? Record When should it be done? Examine Develop With a view to: Evaluate Combine or Rearrange Define Install Maintain Examine- Secondary Questions Person: Who does it? Select Why does that person do it? Record Who else might do it? Examine Who should do it? Develop Evaluate With a view to: Define Combine or Rearrange Install Maintain Examine- Secondary Questions Means: How is it done? Select Why is it done that way? Record How else might it be done? Examine How should it be done? Develop Evaluate With a view to: Define Simplify Install Maintain Develop New Designs Select Multidisciplinary Teams Record Worker Involvement Examine Develop Quality Circles Evaluate Simple Ideas (Spring Loaded Table) Define Install Maintain Evaluate Multiple Improvement Ideas Select Consider costs, benefits, and drawbacks Record Report (ABC, Accurate, Brief, and Clear) Examine Develop Example Evaluate Define Install Maintain Define The written standard practice Prepare a written standard practice, also known as an "operative instruction sheet". This serves several Select purposes Record 1. It records the improved method for future reference. Examine 2. It can be used to explain the new method to management, supervisors and operatives. It also Develop advises all concerned, including the works engineers, Evaluate of any new equipment required or of changes needed Define in the layout of machines or workplaces. Install 3. It is an aid to training or retraining operatives. Maintain 4. It forms the basis on which time studies. Define The written standard practice outlines in simple terms the methods to be used by the operative. Three sorts of information will normally be required: Select (1) The tools and equipment to be used and the general Record operating conditions. Examine (2) A description of the method. The amount of detail Develop required will depend on the nature of the job and the Evaluate probable volume of production. For a job which will occupy several operatives for several months, the Define written standard practice may have to be very detailed, Install going into finger movements. Maintain (3) A diagram of the workplace layout and, possibly, sketches of special tools, jigs or fixtures. Define Select Record Examine Develop Evaluate Define Install Maintain Install Installation can be divided into five stages, namely: (1) Gaining acceptance of the change by management. Select (2) Gaining acceptance of the change by the Record departmental supervision. Examine There is no point in trying to go any further if this Develop approval and acceptance have not been obtained. Evaluate (3) Gaining acceptance of the change by the workers Define and their representatives. Install (4) Preparing to make the changes. Maintain (5) Controlling the changeover. Install Training: May use films to demonstrate the old and the new methods. Films are particularly valuable when retraining. Select Develop the habit of doing the job in the correct way. Record Train to follow a numbered sequence illustrated on a chart. Examine Learning curves Develop In the first stages of learning, rests between periods of Evaluate practice should be longer than the periods of practice Define themselves. Install When the operative has begun to grasp the new method and Maintain to pick up speed, rest periods can be very much shorter. Nursing the new method. Install Select Record Examine Develop Evaluate Define Install Maintain Maintain Workers should not be permitted to slip Select back into old methods, or introduce Record elements not allowed for, unless there is very good reason for doing so. Examine Develop To be maintained, a method must first be Evaluate very clearly defined and specified. Define Assign a specialists permanently. Install Maintain Formal review. Method Study in the Office Offices use resources, must be used efficiently. Percentage of workers in offices continues to increase. Administrative costs (overheads) must be controlled. Introduction of advanced technology (machinery). In most offices, most of the work is routine. Look for areas or activities that: Account for a significant proportion of office labor costs. Are producing large numbers of errors or serious errors. Are creating high levels of dissatisfaction. Need to change in response to some external change. Quality circle. Method Study in the Office Most office work can be placed on a hierarchy which includes systems, procedures, activities and methods. Method Study in the Office Use the columnar chart form in which each column represents one department or section of the organization (figure 60). Method Study in the Office Design of forms Naturally, a document or form should be examined together with the procedure in which it is used. Changing a system or procedure may have automatic implications for forms used. Forms themselves should be examined when the procedure itself has been examined and improved or validated. Examination of a form follows the basic critical examination process, asking: Why is the form necessary? What information does it convey? Who uses it? When do they use it? Where is it used? How is it used? (Is the form produced by a computer, are entries typed on to the form, is it filled in manually, etc.?) Then examining and evaluating alternatives. Method Study in the Office Design of forms When designing forms we are trying to make the form: compatible with its intended use easy to complete easy to use Consideration must be given to: paper size; paper weight; shape; color; maintaining any house style or corporate identity; and balancing these with the cost involved. Method Study in the Office Details that affect design are: the filing/retrieval process; the routing of the form throughout the organization the degree to which additional entries are made on the form at subsequent stages); the nature of data entered on the form and the degree to which they can be grouped. Method Study in the Office Control of forms The most important part of controlling forms is to undertake regular audits to discover if each form is still necessary to serve a particular business function (MAINTAIN). Where the purpose of the form is still valid, questions must be asked about the environment in which the form operates and whether changes here, for example, in technology or filing methods require changes to be made to the form. Method Study in the Office Control of forms Other items to be considered are: The production method: How is the form produced and are there now better or cheaper ways? How much stock of each form is held, and where is it held? Is this appropriate to the use of the form? How are supplies to users reordered? How is stock issued to users? How is issued stock tracked? Method Study in the Office Control of forms What is the useful life of information on the form? Are there any legal constraints on disposal? How do we ensure that forms are disposed of, after their useful life is ended (to release valuable space)? Are there security restrictions on disposal (should forms be shredded or burnt)? Office Layout Office layout study should consist of the following steps: Record details of the major systems in use in the office. Record details of the clerical procedures that support those systems. Examine the working methods of those procedures and carry out a basic method study of each one. Carry out a capacity assessment of each part of the procedure Analyze volumes of output and question the senior managers to discover likely future trends. Identify communication and contact paths and frequencies. Design individual workstations ( ergonomics) From volume and capacity data, calculate total workstation requirements. Office Layout Office layout study should consist of the following steps: Decide on basic type of layout. Identify any "external" constraints. Draw up a schematic layout Investigate available hardware solutions Discuss the provisional layout with both the users Modify the layout in accordance with the results of discussions and prepare the proposed layout. Motion Study and Work Design Concerned with basic motions of a human worker while performing a given task Examples of basic motion elements: Reach Grasp Move Release Guidelines for work design include “principles of motion economy” that is guidelines for work design in three categories: (1) use of the human body in developing the standard method, (2) workplace layout, and (3) design of the tooling and equipment used in the task. Facility Layout Planning What is Facility Layout? Refers to the size and shape of a facility, the arrangement of the different functions and/or departments in it, and the way the equipment is positioned. Plays a significant role in determining the overall efficiency of the operations accomplished in the facility. Objectives are to maximize Customer satisfaction Utilization of space, equipment, & people Efficient flow of information, material, & people Employee morale & safety Problem area includes: Design of a new facility Installing new equipment, retiring old equipment Expanding (or contracting) an existing facility How do you conduct a plant layout project? 1. Define or redefine the goals of the facility. 2. Specify the activities to be performed in accomplishing the goals 3. Determine the interrelationships among all activities 4. Determine the space requirements for all activities 5. Generate alternative facility layouts 6. Evaluate alternative facility layouts 7. Select a facility layout 8. Implement facility layouts 9. Maintain and adapt the facility layout Work Measurement Techniques Four basic work measurement techniques: 1. Direct time study 2. Predetermined motion time systems (PMTS) 3. Standard data systems 4. Work sampling PMTS and work sampling can be often used in methods engineering to make improvements in the work methods Predetermined motion time system (PMTS) is a database of basic motion elements and their associated normal time values, and it includes procedures for applying the database to analyze manual tasks and establish standard times for the tasks. The principal application of a PMTS is to determine standard times. Work sampling is a statistical technique for determining the proportions of time spent by workers or machines in various categories of activity. It can be applied to determine machine utilization, worker utilization, and the average time spent performing various types of activities. As such it can be a useful tool in methods engineering for identifying areas that need attention. For example, if a work sampling study finds that workers in a facility spend large amounts of their time waiting for work, then this is a management problem that should be addressed. Methods Engineering and Automation USA Principle Ten Strategies for Automation Automation Migration Strategy. The USA principle is a common sense approach to automation projects. USA stands for three steps in the analysis and design procedure: Understand the existing process. Simplify the process. Automate the process. Understand the Existing Process What are the inputs? What are the outputs? What exactly happens to the work unit between input and output? What is the function of the process? How does it add value to the product? Simplify the Process What is the purpose of this operation or this transport? Can this step be eliminated? Is the most appropriate technology being used? How can this step be simplified? Can steps be combined? Can steps be performed simultaneously? Can steps be integrated into a manually operated production line? Automate the Process The USA Principle is a good first step in any automation evaluation project. If automation seems a feasible solution to improve productivity, quality, or another measure of performance, then the following ten strategies provide a road map to search for these improvements. The ten strategies constitute a checklist of the possibilities for improving the work system though automation or simplification. For many situations, multiple strategies can be implemented in one improvement project. Ten Strategies for Automation 1. Specialization of operations 2. Combined operations 3. Simultaneous operations 4. Integration of operations 5. Increased flexibility 6. Improved material handling and storage 7. On-line inspection 8. Process control and optimization 9. Plant operations control 10. Computer integrated manufacturing (CIM)