Unit-4 EBS Merged PDF
Document Details
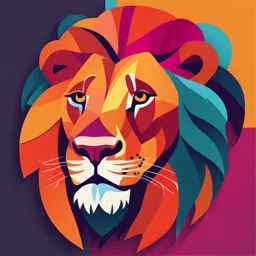
Uploaded by WelcomeFreedom1926
PES
Raghu B. A.
Tags
Related
- Understanding Procurement and Contract Management PDF
- Week 4 ERP - Inventory Management (PDF)
- Supply Chain Logistics Management PDF
- Allgemeine Betriebs-wirtschaftslehre Modul 4: Materialwirtschaft und Beschaffung PDF
- Materialbeschaffung & -verwaltung PDF
- ES Fundamentals for Business Short Course Manual PDF
Summary
This document covers procurement and inventory management within enterprise business systems. It details the procurement process, types of procurement, and how enterprise resource planning (ERP) systems support these processes. The content is suitable for students studying business and computer science.
Full Transcript
ENTERPRISE BUSINESS SYSTEMS Procurement and Inventory Management (PIM) Raghu B. A. Department of Computer Science and Engineering [email protected] ENTERPRISE BUSINESS SYSTEMS (EBS) Procurement and Inventory Management (PIM) Procurement Management: 1.Overview Topic Agenda – Chap...
ENTERPRISE BUSINESS SYSTEMS Procurement and Inventory Management (PIM) Raghu B. A. Department of Computer Science and Engineering [email protected] ENTERPRISE BUSINESS SYSTEMS (EBS) Procurement and Inventory Management (PIM) Procurement Management: 1.Overview Topic Agenda – Chapter 22 2.Procurement Management Process Types of Procurement Maturity Model Master Data KPIs for ERP Procurement ERP Solutions 3.Inventory Management 2 ENTERPRISE BUSINESS SYSTEMS (EBS) Procurement and Inventory Management (PIM) Inventory Management: Topic Agenda 1.Overview 2.Procurement 3.Inventory Management IM Processes Concept of IM Pyramid IM Processes in ERP Models of IM KPIs for ERP IM Solutions for ERP IM 3 ENTERPRISE BUSINESS SYSTEMS (EBS) Procurement and Inventory Management (PIM) Procurement Management: What is it? 4 ENTERPRISE BUSINESS SYSTEMS (EBS) Procurement and Inventory Management (PIM) Procurement Management: Procurement Process Definition: “Procurement is the process of sourcing materials from vendor, inspecting it and finally paying the vendor for the accepted materials.” Procurement is a requirement for almost every organization Hence considered a fundamental module of any ERP system It is a transaction intensive process Widely used module Other definitions: From www.purchasecontrol.com “Procurement management is a strategic approach to optimizing organizational spend. It involves sourcing, requisitioning, ordering, inspection, and reconciliation. It means acquiring your goods and services from preferred vendors, within your determined budget, either on or before the deadline.” May 2019 5 ENTERPRISE BUSINESS SYSTEMS (EBS) Production Planning and Execution Procurement Management: Procurement Process 1) Determining what to buy and how much – Procurement Planning 2) Determination of the source of supply 3) Selecting the vendor 4) Purchase Order (PO) creation 5) Goods Receipt (GR) 6) Invoice verification 7) Processing vendor payment 6 ENTERPRISE BUSINESS SYSTEMS (EBS) Procurement and Inventory Management (PIM) Procurement Management: Procurement Process 7 ENTERPRISE BUSINESS SYSTEMS (EBS) Production Planning and Execution Procurement Cycle: Source Determination / Vendor Selection Procurement Planning Procurement Purchase Order Creation Cycle Vendor Payment Goods Receipt 8 ENTERPRISE BUSINESS SYSTEMS (EBS) Production Planning and Execution Procurement Cycle: ERP Support: ✔ Purchase Info record ✔ Scheduling Agreement ERP Support: Source Determination / ✔ Contract ✔ Auto creation of PR by MRP run ✔ Auto Request for Quotation creation ✔ Easy entry of PR data in case of manual PR Vendor Selection ✔ Comparison of vendor quotes ✔ Different Planning and lot sizing tools Procureme How ERP make this process nt more efficient Planning Purchase Procurement Order Creation Cycle ERP Support: ✔ Auto creation of P.O. from PR, RFQ ✔ Minimum data entry ✔ Can automatically calculate price based on conditions ✔ Electronic P.O. communication to Vendor vendor Payment Goods Receipt ERP Support: ERP Support: ✔ Auto matching on invoices ✔ Goods receipt in different scenarios with GR qty and P.O. price ✔ Auto updation of stock and inventory ✔ Blocking of invoices valuation 9 ✔ Reporting of aging invoices ENTERPRISE BUSINESS SYSTEMS (EBS) Procurement and Inventory Management (PIM) Procurement Management: How ERPs Support Procurement Process 1) Determining what to buy and how much – Procurement Planning ✔Auto generation of PR by MRP run 2) Determination of the source of supply ✔Purchase information record 3) Selecting the Vendor (or Supplier) ✔Scheduling agreement & contracts ✔Comparison of vendor quotes 4) Purchase order (PO) creation ✔Auto creation of PO from PR, RFQ & e-communication to vendor 5) Goods receipt 6) Invoice verification 7) Processing vendor payment 10 ENTERPRISE BUSINESS SYSTEMS (EBS) Procurement and Inventory Management (PIM) Procurement Management: How ERPs Support Procurement Process 1) Determining what to buy and how much – Procurement Planning 2) Determination of the source of supply 3) Selecting the vendor 4) Purchase order (PO) creation 5) Goods receipt (GR) a) Quality inspection and shelf life expiration check b) Under/Over delivery check & report c) Auto updation of stock and inventory valuation 6) Invoice verification 7) Processing vendor payment 11 ENTERPRISE BUSINESS SYSTEMS (EBS) Procurement and Inventory Management (PIM) Procurement Management: How ERPs Support Procurement Process 1) Determining what to buy and how much – Procurement Planning 2) Determination of the source of supply 3) Selecting the vendor 4) Purchase order (PO) creation 5) Goods receipt (GR) 6) Invoice verification a) Invoice entry 7) Processing vendor payment a) Auto or 3-way Matching of Invoice with GR, and PO b) Blocking of invoices – quality inspection, amount variances, manual blocking/releasing, parking c) Credit/Debit Memos d) Invoice Ageing and their reporting 12 ENTERPRISE BUSINESS SYSTEMS (EBS) Procurement and Inventory Management (PIM) Procurement Management: 1.Overview Topic Agenda 2.Procurement Management Process 🡺 Procurement Cycle – activities and steps involved 🡺 3-way matching 🡺 ERP Support Types of Procurement – Variants, Challenges Maturity Model Master Data KPIs for ERP Procurement ERP Solutions 3.Inventory Management 13 ENTERPRISE BUSINESS SYSTEMS (EBS) Procurement and Inventory Management (PIM) Procurement Management: How ERPs Support Procurement Process Some Important Functionalities of ERP for Procurement Process Purchase Requisition (PR) Contracts – types: Quantity contract, Value contract Central contract, Plant specific contract Quota arrangement Required for multiple sources Delivery Schedule – for better planning by the supplier Forecast, Detailed or Firm schedules Source list Allowed/Preferred/Blocked suppliers list - material wise RFQ (Request for Quotation) Manual entry or PR based Quotation processing Data entries, comparison, selection and rejection PO (Purchase Order) > Cont’d in next slide 14 ENTERPRISE BUSINESS SYSTEMS (EBS) Procurement and Inventory Management (PIM) Procurement Management: How ERPs Support Procurement Process Some Important Functionalities of ERP for Procurement Process Cont’d PO (Purchase Order) Definition = a formal request/document to a vendor to supply certain goods or services under conditions stated in the order. Converting PR to PO (or from previous PO) PO creation: reduces data entry and errors; use of default values of terms, addresses, etc. Blanket PO Consumables Longer period validity 15 ENTERPRISE BUSINESS SYSTEMS (EBS) Procurement and Inventory Management (PIM) Procurement Management: Procurement Process Variants for Different Types of Procurement A)Procurement of Materials and Services B)Procurement of Direct and Indirect Items C)Commodity Procurement D)Govt. / PSU Procurement Typical Challenges 1)Service cannot be inventorized 2)Difficult to specify service specifications 3)Price comparison is complex 4)Goods receipt is replaced by service entry and acceptance for service procurement [PSU = Public Sector Unit] 16 ENTERPRISE BUSINESS SYSTEMS (EBS) Procurement and Inventory Management (PIM) Procurement Management: Differences between Material And Service Procurements Material Procurement Service Procurement Materials can be inventorized Services can not be inventorized Specifications are clearly defined Some times it is difficult to define a during material procurement service specification during procurement For a given specification price For a given specification service comparison is simple price comparison is difficult – price may differ by time of purchase, ambience, etc. 17 ENTERPRISE BUSINESS SYSTEMS (EBS) Procurement and Inventory Management (PIM) Procurement Management: Difference between Direct And Indirect Procurements Direct Items Indirect Items ▪ Demand driven by Market demand of End items ▪ Demand not driven by end item demand and mostly driven by past consumption trend ▪ Involvement for procurement department is much ▪ Involvement for procurement department is higher here as they need to collaborate with supplier much lower here as mostly off the shelf items to design the component or product. are procured. ▪ Generally contribute a significant portion by value of ▪ Generally contribute a small portion by value total monthly procurement spend of total monthly procurement spend as these are typically low value items. ▪ Planning is done generally through planning runs of ▪ Planning is consumption based. In some cases MRP or Advanced planning systems. purchase requisitions are created manually. ▪ Procurement is always done by procurement team. ▪ Procurement can be done by procurement team and also by end user / employee through E Procurement or Portal. ▪ Back end integration needed with ERP solutions is ▪ Back end integration needed with ERP much higher here for reasons like delivery schedules solutions is lower here. 18 release ENTERPRISE BUSINESS SYSTEMS (EBS) Procurement and Inventory Management (PIM) Procurement Management: ERP’s Functionality For Commodity Procurement ✔ Commodities are the items which are not branded and can see wide price variations depending on demand, supply and seasonal variations in price. ✔ Commodity procurement is a specialized procurement process ✔ ERPs provide special procurement tools for managing commodity procurement. These are: E-procurement = Auction, Hedging 19 ENTERPRISE BUSINESS SYSTEMS (EBS) Production Planning and Execution Procurement Management: Procurement Strategy for Different Item Groups MRO refers to Maintenance, Repair and Operation High supplies. Production Critical Items Items Strategic Impact (e.g. Spares) (e.g. components) (Driver: Should never (Driver: Need closer be out of stock) collaboration with vendor) MRO (indirect goods/ services) Commodities (e.g. raw material) (Driver: Purchase (Driver: Price is right) Low admin cost should be low) 20 Low Financial Impact High ENTERPRISE BUSINESS SYSTEMS (EBS) Procurement and Inventory Management (PIM) Procurement Management: Level 1: Basic Processes Basic Procurement planning Manual PRs & POs Procurement Maturity Model and Vendor payment Goods Receipt Item based Procurement Strategy Quality Inspection Level 2: Matured Processes Optimum Procurement planning E-procurement Collaboration with suppliers for Forecasting, Inventory Level 3: Innovative Processes Sourcing optimization SRM Auctions and reverse auctions Advanced collaboration with suppliers Advanced Supplier Analytics Exception management 21 ENTERPRISE BUSINESS SYSTEMS (EBS) Production Planning and Execution Procurement Management: Procurement Maturity Model Sourcing Optimization Supplier Relationship Management Auctions and Reverse Auctions Level 3 Advanced supplier collaboration Innovative For Product development Processes Advanced supplier analytics Exception management Optimum Procurement Planning Level 2 (using MRP or APS) Matured E Procurement ERS for vendor payment Processes Basic supplier collaboration for Forecast, Inventory Basic Procurement planning / Level 1 Mostly Manual PRs Purchase order processes Basic Processes Vendor payment Goods receipt Quality inspection 22 ENTERPRISE BUSINESS SYSTEMS (EBS) Production Planning and Execution Procurement Management: Master Data For ERP Procurement Material Master Vendor Master ERP Procurement Master Data Terms and Conditions Service Master / Master Service Catalog 23 ENTERPRISE BUSINESS SYSTEMS (EBS) Procurement and Inventory Management (PIM) Procurement Management: Master Data for ERP Procurement 1)Material Master 2)Vendor Master 3)Terms & Conditions Master 4)Service Master Record & Service Catalog 24 ENTERPRISE BUSINESS SYSTEMS (EBS) Procurement and Inventory Management (PIM) Procurement Management: KPIs for Procurement # Measure Definition 1 Cost Savings Departments contribution to the financial success of the organization. 2 Supplier Performance of suppliers on price, delivery, quality, Performance service, etc. 3 Procurement Average time taken between requisition submission and Cycle Time PO placement 4 Procurement Ratio of savings made by operating costs. ROI Measures dept's cost efficiency. 5 Contract No. of exceptions in contract – quantity, price, etc. Compliance 6 Purchasing Analysis Order value analysis – net order value, ABC analysis, 25 frequency analysis, etc. ENTERPRISE BUSINESS SYSTEMS (EBS) Procurement and Inventory Management (PIM) Procurement Management: ERP Solutions for Procurement ⚫SAP Offerings Leading Vendor Offerings 1) Consumption based planning 2) Reorder point planning Oracle Offerings: 3) Forecast based planning 1) Internet Procurement 4) MRP based planning 2) Purchasing Intelligence 3) Online Supplier Portal Procurement Scenarios: 4) Purchasing 1) Purchase requisition 5) Oracle Sourcing 2) Purchase of materials to production 6) Procurement Contracts 3) Purchase to stock 7) Daily Business Intelligence 4) Purchase by KANBAN 8) Quality 5) Purchase to sales order 6) Purchase to projects 7) Procurement for direct consumption 8) Internal procurement between plants 9) Procurement via sub-contracting 26 ENTERPRISE BUSINESS SYSTEMS (EBS) Procurement and Inventory Management (PIM) Procurement Management: Topic Agenda 1.Overview 2.Procurement 3.Inventory Management IM Processes Concept of IM Pyramid IM Processes in ERP Models of IM KPIs for ERP IM Solutions for ERP IM 27 ENTERPRISE BUSINESS SYSTEMS (EBS) Procurement and Inventory Management (PIM) Inventory Management: IM Processes in ERP Concept of IM Pyramid A) Inventory Transaction Processes B) Inventory Control Processes C) Inventory Planning Processes D) Strategic IM Processes 28 ENTERPRISE BUSINESS SYSTEMS (EBS) Procurement and Inventory Management (PIM) Inventory Management: IM Processes in ERP : Concept of IM Pyramid A)Transaction Processes 1) Goods Receipt (GR) 2) Goods Issue 3) Reservations 4) Stock Transfer A)Inventory Control Processes 1) Quality Control a) Physical Inventory b) Cycle Counting c) Stock Overview 2) Value Control / Stock Valuation a) ABC Classification of Materials A)Inventory Planning Processes 1) Design better process for replenishment 2) Supporting processing/handling of exceptions 3) Scientific approach to reordering – when & what quantity A)Strategic IM Processes 29 ENTERPRISE BUSINESS SYSTEMS (EBS) Procurement and Inventory Management (PIM) Inventory Management: IM Processes in ERP : Concept of IM Pyramid A)Transaction Processes 1) Goods Receipt (GR) 2) Goods Issue 3) Reservations 4) Stock Transfer A)Inventory Control Processes 1) Quality Control a) Physical Inventory b) Cycle Counting c) Stock Overview 2) Value Control / Stock Valuation a) ABC Classification of Materials A)Inventory Planning Processes 1) Design better process for replenishment 2) Supporting processing/handling of exceptions 3) Scientific approach to reordering – when & what quantity A)Strategic IM Processes 30 ENTERPRISE BUSINESS SYSTEMS (EBS) Procurement and Inventory Management (PIM) Inventory Management: IM Processes in ERP Concept of IM Pyramid A)Transaction Processes 1) Goods Receipt (GR) 1) ASN = Advanced Shipping Notice (from supplier) 2) Receiving goods (PO / Delivery Schedule) 3) Damage identification 4) Unloading & unpacking 5) Capture Lot # details 6) Reconcile PO – Delivery Schedule – GR 7) Returns – quality not acceptable 8) Bar codes, RFID – simpler, faster process 2) Goods Issue 1) Create ASN (to customer) 2) Packing and loading 3) Issue goods and post in ERP - I 4) Receive POD (proof of delivery) from customer 3) Reservations 1) By customer for a later date. Ensure availability. 4) Stock Transfer 1) Plant to Plant, to Company, to Stores, to Warehouse, to Dealer 31 ENTERPRISE BUSINESS SYSTEMS (EBS) Procurement and Inventory Management (PIM) Inventory Management: IM Processes in ERP Concept of IM Pyramid A)Transaction Processes B)Inventory Control Processes 1)Quality Control a) Physical Inventory a) To match System Inv is a challenge b)Cycle Counting a) A method of physical inventory counting in periodic intervals b)Policy based on ABC class of items c) Pareto analysis c) Stock Overview a) Stocks at different levels – ERP enabled 1)Value control / Stock Valuation A)ABC Classification of materials B)Valuation methods available A)Moving average price B)Std price (in Matl Master) 32 ENTERPRISE BUSINESS SYSTEMS (EBS) Procurement and Inventory Management (PIM) Inventory Management: IM Processes in ERP Example of ABC classification of materials The A items account for 60.5% of the value and 13.3% of the items The B items account for 25% of the value and 26.7% of the items The C items make up last 14.5% of the value and 60% of items 33 ENTERPRISE BUSINESS SYSTEMS (EBS) Procurement and Inventory Management (PIM) Inventory Management: IM Processes in ERP Example of ABC classification of materials ABC classification helps in classifying inventory and allocating control efforts as per importance A – Very Important, B – Moderate Important, C – Least Important 34 ENTERPRISE BUSINESS SYSTEMS (EBS) Procurement and Inventory Management (PIM) Inventory Management: 35 ENTERPRISE BUSINESS SYSTEMS (EBS) Procurement and Inventory Management (PIM) Inventory Management: IM Processes in ERP : Concept of IM Pyramid C) Inventory Planning Processes Two basic drivers for better inventory planning i) Never have a stock out for finished goods Customer dissatisfaction Lost sales for raw materials Production loss i. Never carry excess inventory Increases cost of operation Chance of obsolescence Heavy markdown Solutions to overcome / prevent : 1) Design better process for replenishment 2) Support processing / handling of exceptions 3) Scientific approach to reordering – when & how much (quantity) Q model, P model, Min-Max model, 2-bins model 36 ENTERPRISE BUSINESS SYSTEMS (EBS) Procurement and Inventory Management (PIM) Inventory Management: IM Processes in ERP : Concept of IM Pyramid C) Inventory Planning Processes (cont’d) Inventory Models supported by ERPs 1)Q model EOQ model – reorder point ordering, qty is constant 2)P model Periodic review Opposite of Q model – qty differs, freq is constant 3)Min-max model Pre-define min and max stock level Order when stock on hand is at/near min level 4)Two bin model Use 2 bins Order when first bin is empty 37 ENTERPRISE BUSINESS SYSTEMS (EBS) Procurement and Inventory Management (PIM) Inventory Management: IM Processes in ERP : Concept of IM Pyramid A)Transaction Processes A)Inventory Control Processes A)Inventory Planning Processes B)Strategic IM Processes 1)Process of Inventory Collaboration 2)Deciding Inventory based on Service Levels 3)Best practice processes of IM like Cross Docking 4)Lean Inventory Management 38 ENTERPRISE BUSINESS SYSTEMS (EBS) Procurement and Inventory Management (PIM) Inventory Management: IM Processes in ERP : Concept of IM Pyramid Process of Inventory Collaboration VMI – vendor managed inventory D) Strategic Inventory Management Processes Wal-Mart and P&G collaboration Deciding Inventory based on service levels Critical items, high service levels => high inventory Low service levels => low inventory Best practice processes Cross docking Effective coordination of inbound & outbound shipments Example: Wal-Mart SAP, Oracle, Manhattan Associates Lean Inventory Management Lean principles Reduce waste from supply chain Kanban or JIT 39 ENTERPRISE BUSINESS SYSTEMS (EBS) Production Planning and Execution Inventory Management: ERP can support all levels of Inventory Management Pyramid ▪ Adopting Inventory Mgmt Best Practices like Lean, Cross Docking Gai Strategic ▪ Deciding inventory based on service levels n Inventory ▪ Inventory collaborative approaches like - VMI, CPFR Mgmt ▪ Scientific determination of Safety stock, Cycle stock etc. Maintai ▪ Determining when to order how much – Inventory model n ▪ Inventory replenishment planning (ERP tool like DRP) Lose ▪ ERP systems supporting basic inventory transactions like Goods Issue, Receipt, Stock transfer etc. ▪ ERP systems support basic inventory control techniques like cycle counting for inventory accuracy, Inventory Valuation etc. ▪ ERP systems help in locating where how much inventory is lying of what value 40 ENTERPRISE BUSINESS SYSTEMS (EBS) Procurement and Inventory Management (PIM) Inventory Management: KPIs for Inventory Management ⚫Measures ⚫Definition Stock outs #incidents of stock not available when required Inventory Turn Annual sales / Average inventory level Inventory Carrying Cost Ʃ all costs of finished goods SKU turnover # SKU cycles/turns Inventory Ageing Total Gross Inv% for specific periods Inventory Cycle Sum of var. b/w physical Inv. and perpetual inv. OR Counting Accuracy #accurate part part cycles count / total #cycle counts performed Shrinkage Costs of breakage, pilferage, deterioration of inv. Storage space utilization Volume of storage / total storage capacity in % Inv Obsolescence as a Obsolete & scrap inv. / Gross inv. value %age of Total Inventory 41 ENTERPRISE BUSINESS SYSTEMS (EBS) Procurement and Inventory Management (PIM) Inventory Management: Vendor Solutions for 1)Oracle Offerings Inventory Management Oracle Inventory Management Inbound, Outbound and Reverse Logistics’ Transactional Support Tracking raw materials, WIP components, finished goods Active alerts, intelligent messages for proactive management Global inventory visibility and many more 2)SAP Offerings SAP Materials Management (MM) module GR, GI, Goods Return Stock Transfers Physical Inv. and Cycle Counting Inventory Valuation and many more 3)IBM offerings Dynamic Inventory Optimization (DIOS) 42 ⚫ERP vs Best of breed ENTERPRISE BUSINESS SYSTEMS (EBS) Procurement and Inventory Management (PIM) Topic Summary ⚫P&IM is an important area management of product ⚫Procurement definition ⚫Procurement cycle ⚫Scenarios: Material vs.Service procurements; P. types ⚫Procurement maturity model ⚫Master Data ⚫Inventory management pyramid ⚫Inventory models ⚫KPIs for procurement and inventory processes ⚫ERP vendor offerings for procurement and inventory processes 43 43 THANK YOU Raghu B. A. Department of Computer Science and Engineering [email protected] ENTERPRISE BUSINESS SYSTEMS ERP Product Selection Raghu B. A. Department of Computer Science and Engineering [email protected] ENTERPRISE BUSINESS SYSTEMS ERP Product Selection Raghu B. A. Department of Computer Science and Engineering ENTERPRISE BUSINESS SYSTEMS (EBS) ERP Product Selection ERP Product Selection: Topic Agenda 1.Introduction 2.Criteria for Initial Package Selection 3.Initial Package Shortlisting 4.Final Package Selection 5.RFP Process for Package Selection 6.Finalizing the Contract with ERP Package Vendor 7.ERP Package Market 56 ENTERPRISE BUSINESS SYSTEMS (EBS) ERP Product Selection ERP Product Selection: ⚫ Selecting Right ERP Package A) Selecting the right ERP package that meet a company’s business needs is one of the most crucial factor for ERP project success. B) ERP packages comes from different origin, different features and at various price points. For example: ✓ Some of them can be very strong in particular processes like Peoplesoft in Human Resource, BAAN in Manufacturing etc. ✓ Some of them can be strong in particular industry like Mincom in Mining, Retek for Retail industry, Ramco for Utilities etc ✓ Some of them can support particular database (like JD Edwards supports DB2, Oracle supports Oracle database etc) and some of them support all leading databases (like SAP) ✓ Some of them support particular operating system (like few ERPs only run on Windows operating system) and some of them support all leading OS. ENTERPRISE BUSINESS SYSTEMS (EBS) ERP Product Selection ERP Product Selection: Selecting the right ERP solution can be a make or break for success of the ERP project. Several factors need to be considered for this selection. No package will meet 100% of the company’s needs. Objective is to find a package that is a good-fit (75-80% match) to business requirements and supports long term goals. Package that fits well would result in the following: ⚫ Lower resistance from the users ⚫ Reduced training needs ⚫ Less organizational adaptation issues Gap analysis is done for figuring out the gap between the process, data and user interface requirements and ERP offerings. ENTERPRISE BUSINESS SYSTEMS (EBS) ERP Product Selection ERP Product Selection: Package Selection Process Intro 1)Who will do the selection? l Selection committee with CIO / CFO 2)How to deal with ERP Vendors? l Requirements l Vendor Demo l Critical scenarios in new ERP Package l References l Product comparison 3)ERP Selection – a two step process l Initial Shortlisting = screening l Final Selection – comparison – detailed evaluation with ⚫ weighted scoring > product selection ENTERPRISE BUSINESS SYSTEMS (EBS) ERP Product Selection ERP Product Selection: ⚫ Who Does Package Selection ✓ Typically a small team from the company comprising of different department heads and company’s top management (CIO or CFO) is part of the selection committee. ✓ Sometimes selection committee also has few consultants who know the leading packages well. ✓ This selection committee define the selection process, the selection criteria, attend all vendor’s presentations, put relevant questions to them, do comparative analysis of different ERP vendors and finally do ERP selection. ENTERPRISE BUSINESS SYSTEMS (EBS) ERP Product Selection ERP Product Selection: ⚫ Tips For Dealing With ERP Vendors ✓ Have your list of requirements ready and ask vendor question on how some of these tricky requirements can be met during the presentation ✓ Ask the vendor to give a demo and to run some of your critical business scenarios in their ERP system. ✓ Ask for reference sites where the selection committee can visit and hear from the users. ✓ Ask the vendor how they differentiate from other ERP vendors ENTERPRISE BUSINESS SYSTEMS (EBS) ERP Product Selection ERP Product Selection Process: Have ERP selection team in place Decide Selection criteria and weights for each criteria Screening of Initial list of vendors and shortlist a few Detailed final evaluation of short listed vendors Finalize the ERP vendor and enter into contract with the vendor ENTERPRISE BUSINESS SYSTEMS (EBS) ERP Product Selection ERP Product Selection: ⚫ Process for ERP Selection ✓ Most of the companies follow a two step approach for package selection. ✓ Evaluation process can start with large number of packages and based on a set of criteria, few of them (say two to maximum three) are short listed. This process is called screening. ✓ Now these two or three packages are compared against the list of requirements (100s) of the company. ✓ After the detailed evaluation of these short listed packages, one is selected and the company enters into contract with selected vendor. ENTERPRISE BUSINESS SYSTEMS (EBS) ERP Product Selection ERP Product Selection: Things to be considered for Package Selection ENTERPRISE BUSINESS SYSTEMS (EBS) ERP Product Selection ERP Product Selection: Selection of ERP Package 1)Criteria for Initial Package Screening 2)Initial Package Shortlisting 3)Final Package Selection 4)Deviations in Package Selection Process 5)RFP Process for ERP Package Selection 6)Finalizing the Contract with ERP Package Vendor 7)ERP Package Market ENTERPRISE BUSINESS SYSTEMS (EBS) ERP Product Selection ERP Product Selection: Selection Criteria for ERP Package Customer Technology Service / Consulting Maturity Support Partnerships Local Package Presence Cost Industry Integration rd with Experience 3 Party apps Functionality Financial Fit Viability Product Strategy Vision, Innovation ENTERPRISE BUSINESS SYSTEMS (EBS) ERP Product Selection ERP Product Selection: Things to be considered for Package Selection 1)Criteria for Initial Package Screening A)Product Strategy, Vision & Investment in Innovation by Vendor B)Financial Viability of the Application Vendor ⚫ JD Edwards, Peoplesoft, Siebel, Retek > Oracle ⚫ Manugistics > JD Edwards ⚫ BAAN, Commerce One C)Installed Base and Local Presence ⚫ Geography/Country specific ⚫ Industry Domain specific ⚫ MNC ENTERPRISE BUSINESS SYSTEMS (EBS) ERP Product Selection ERP Product Selection: Things to be considered for Package Selection 1)Criteria for Initial Package Screening (Cont’d) A) Product Strategy, Vision & Investment in Innovation by Vendor B) Financial Viability of the Application Vendor C) Installed Base and Local Presence D) Partnerships Implementation partnerships with Consulting Companies Application partnership with other third party application E) Technology Maturity – OS, platform (server, middleware) F) Vendor's Customer Service – support strength, upgrades G) Cost of the Software – initial capital, AMC, scaling #users, TCO = Total Cost of Ownership! 2)Initial Package Shortlisting ENTERPRISE BUSINESS SYSTEMS ERP Product Selection Raghu B. A. Department of Computer Science and Engineering ENTERPRISE BUSINESS SYSTEMS (EBS) ERP Product Selection ERP Product Selection: Things to be considered for Package Selection 1)Criteria for Initial Package Screening (Cont’d) 2)Initial Package Shortlisting ✓Based on above criteria packages given weighted scores – highest scoring shortlisted 3)Final Package Selection a)Comparison chart or matrix b)Functional requirements match i. Full or direct match ii. Partial match iii.No match c)Category of requirements: Vital, Essential and Desirable d)Evaluation or scoring is done based on above parameters and detailed functional requirements and the vendors ERP offering. ENTERPRISE BUSINESS SYSTEMS (EBS) ERP Product Selection ERP Product Selection: Possible Evaluation Parameters ENTERPRISE BUSINESS SYSTEMS (EBS) ERP Product Selection ERP Product Selection: Possible Evaluation Parameters ENTERPRISE BUSINESS SYSTEMS (EBS) ERP Product Selection ERP Product Selection: Possible Parameters Functionality Cost Reliability No customization Implementation time Platform independence No process modification Running cost Maintenance Software cost Consultancy cost Infrastructure cost Hardware cost Availability of trained manpower Training required Total cost Payment terms Flexibility Total time ENTERPRISE BUSINESS SYSTEMS (EBS) ERP Product Selection ERP Product Selection: ⚫ Exceptions in The Package Selection Process ▪ Lot of companies do not follow the traditional process for ERP package selection for reasons like: ✓ Pressure from major customers to go for particular ERP so that it can be on the same platform as of their customer. ✓ Same ERP for all the companies in the same group to solve problems of integration / business consolidation etc. ✓ Price becomes the most dominant factor for ERP selection (especially for SMB). ✓ Industry specific functionality. ENTERPRISE BUSINESS SYSTEMS (EBS) ERP Product Selection ERP Product Selection: ⚫ RFP Process For Package Selection ▪ Some of the large organizations follow RFP (Request For Proposal) process for selecting ERP package. It is common for large ERP projects. RFP process is must for Public Sector Organizations. ▪ An typical RFP document can contain details like ✓ High Level Scope and Project Duration ✓ Overview of Company’s business and operations ✓ Business benefits the company is expecting from the project ✓ Proposal submission details – when and how the offer to be submitted ✓ Payment schedule, Bonus, Penalty etc ENTERPRISE BUSINESS SYSTEMS (EBS) ERP Product Selection ⚫ Contracting with Package Vendor ▪ Salient points of such contract can be: ⚫ Payment terms ⚫ Intellectual property or copyright clauses ⚫ List of deliverables along with software ⚫ How training in the software will be handled ⚫ How the software maintenance will be handled ⚫ How future upgrades in the software will be provided and at what cost ⚫ Software installation help to be provided ⚫ Prerequisite to install the software – the hardware specification, operating system needed, database needed etc ⚫ Any audit or review by the package vendor during package implementation (like Final blueprint audit, Audit before go live etc) ⚫ License cancellation costs ✓ERP package procurement is not a one time transaction with ERP vendor. ✓Help of ERP vendor is needed through out the package life cycle for supporting the application, for upgrading, for training, etc. ENTERPRISE BUSINESS SYSTEMS (EBS) ERP Product Selection ERP Product Selection: GAP Analysis (Discussion) Assess the gap between the offering and the requirements. The gap analysis will involve the vendor as well the selection team. There are two ways to perform the gap analysis: 1)Vendor makes a presentation of their ERP system. 2)The vendor makes a prototype available to experiment with. The selection team asks questions and based on the answers of the vendor, gap is established. Vendor may be provided with a detailed requirements document and the vendor submits a response to all the requirements. ENTERPRISE BUSINESS SYSTEMS (EBS) ERP Product Selection ERP Product Selection: ERP Packages (Vendors) Market 1)SAP ⚫ All-in-One (for medium size Cos) ⚫ Business One (for small Cos) 2)Oracle ⚫ PeopleSoft, JD Edwards , Siebel 3)Infor 4)IFS 5)Epicor 6)Microsoft 7)Ramco 8)other ERPs 9)For SMBs: Preconfigured templates – reduces time and cost of implementation ENTERPRISE BUSINESS SYSTEMS (EBS) ERP Product Selection ERP Product Selection: ERP Market – Leading Players Tier 1 1 SAP, Oracle Microsoft Dynamics, JD Edwards, Peoplesoft, Tier 2 Infor, IFS, Epicor, Lawson Tier 3 Small players, local players... ENTERPRISE BUSINESS SYSTEMS (EBS) ERP Product Selection ERP Product Selection: Topic Summary Selection right ERP package is critical Variety – technology platforms, features, $$$$$s Selection committee 2-step process – initial & final Influences RFP process Vendor contract Package vendors ERP market 83 THANK YOU Raghu B. A. Department of Computer Science and Engineering [email protected] ENTERPRISE BUSINESS SYSTEMS ERP Consulting Partner Selection Raghu B. A. Department of Computer Science and Engineering [email protected] ENTERPRISE BUSINESS SYSTEMS ERP Consulting Partner Selection Raghu B. A. Department of Computer Science and Engineering ENTERPRISE BUSINESS SYSTEMS (EBS) ERP Consulting Partner Selection Selecting an ERP Consulting Partner: Topic Agenda 1.Overview 2.Things to be considered for selection 3.Request for Proposal method 4.In-house implementation team vs. External consultants 5.Offshore Implementation 6.ERP Consulting Companies 87 ENTERPRISE BUSINESS SYSTEMS (EBS) ERP Consulting Partner Selection Selecting an ERP Consulting Partner: ▪ Selecting the right consulting partner is crucial for ERP project success. ▪ There can be different consulting partners for different phases of the project like; – One for package selection – Second one for doing package implementation – A third one for doing all technical works from a low cost country ▪ Large global implementations these days are mostly broken between multiple partners. ▪ When multiple partners are involved in an implementation, coordination between different players become extremely important. ENTERPRISE BUSINESS SYSTEMS (EBS) ERP Consulting Partner Selection Selecting an ERP Consulting Partner: Size of the Selection team: 4–10 people, could be 60 for large organizations Time: Two to six months, up to one year is not unusual Reports from consultancy firms Follow Selection Process ENTERPRISE BUSINESS SYSTEMS (EBS) ERP Consulting Partner Selection Selecting an ERP Consulting Partner: Ways of Selecting a Vendor Competitive bidding: The vendors bid and the most competitive one is awarded the contract provided he fulfills the requirements. Two-phase acquisition: The selected bidders are asked to do some additional work on which they are evaluated and awarded the contract. ERP vendors are generally selected through competitive bidding only. ENTERPRISE BUSINESS SYSTEMS (EBS) ERP Consulting Partner Selection Selecting an ERP Consulting Partner: Things to be considered for Partner Selection ENTERPRISE BUSINESS SYSTEMS (EBS) ERP Consulting Partner Selection Selection Criteria for an ERP Consulting Partner: Process Industry Client Consulting Experience Satisfaction Experience Price and Client Value References for Money End-to-End Reputation Service Quality of Global Project Presence Mgmt Quality of Tools & Methodology ENTERPRISE BUSINESS SYSTEMS (EBS) ERP Consulting Partner Selection Selecting an ERP Consulting Partner: Things to be considered for Partner Selection 1)Vendor's Industry Experience 2)Process Consulting Experience 3)Client Reference and Client Satisfaction Level 4)Ability to Provide End-to-End Service 5)Quality of Project Management 6)Quality of Tools and Methodologies 7)Presence in Different Geographies 8)Global Delivery Capability 9)Reputation and Branding 10)Price and Value for Money 11)Selection matrix for partner comparative evaluation and selection ENTERPRISE BUSINESS SYSTEMS (EBS) ERP Consulting Partner Selection RFP Process for Consulting Partner Selection: Some of the large organizations follow RFP (Request For Proposal) process for selecting consulting partner for ERP implementation. RFP process is must for Public Sector Organizations. Sometimes an RFI (Request For Information) is issued prior to RFP. Based on RFI response a few vendors can be short listed among many. An RFP can contain details like 1)High level Scope and Project Duration 2)Overview of Company’s business and operations 3)Business benefits the company is expecting from the project 4)Proposal submission details – when and how the offer to be submitted 5)Payment schedule, Bonus, Penalty, etc. ENTERPRISE BUSINESS SYSTEMS ERP Consulting Partner Selection Raghu B. A. Department of Computer Science and Engineering ENTERPRISE BUSINESS SYSTEMS (EBS) ERP Consulting Partner Selection Selecting an ERP Consulting Partner: Request for Proposal (RFP) Method for Selection of Consulting Partner ⚫What is an RFP? ⚫RFP process (details next slide) ⚫Sections of a typical RFP l... l Scope of project l Duration of project l Payment terms with schedule l Performance bonus/penalty clause l... ⚫Bids ⚫Evaluation l Technical l Financial ENTERPRISE BUSINESS SYSTEMS (EBS) ERP Consulting Partner Selection Selecting an ERP Consulting Partner: ⚫RFP Process Steps Request for Proposal (RFP) Method 1)RFI Process Outputs (optional) for Selection of Consulting Partner 2)RFP Preparation 3)RFP Release – selected vendors a)Conference Call b)Common Meeting c) Media Advertisement 4)RFP Response Collection 5)RFP Evaluation 6)Partner Selection 7)Contract Negotiations 8)Partner Finalization 9)Contract Signing 10)Project Implementation Start/Kick off ENTERPRISE BUSINESS SYSTEMS (EBS) ERP Consulting Partner Selection Selecting an ERP Consulting Partner: In house Implementation Team – In house Implementation – Advantages: vs. External Consultants ✔Need not pay external consultants ✔Team may have better process knowledge In house Implementation – Disadvantages: ✔ External consulting team will have better package knowledge ✔ In house team do not have access to methods and tools which a consulting company brings as part of their implementation methodology ✔ Implementation is not their core competency ✔ May lack on ERP project management skills ✔ Overall may not work out to be cost effective if all internal costs are factored In house Implementation – Where it may work: ✔ Better suited for roll outs ✔ Some help from external consultants on specific areas ENTERPRISE BUSINESS SYSTEMS (EBS) ERP Consulting Partner Selection Selecting an ERP Consulting Partner: Pros and Cons of In-house Implementation Cons Pros Better process knowledge Product Expertise Better industry knowledge ERP Project Mgmt Skill Lack of methods and tools No money goes outside No implementation experience High chances of failure In house implementation may work in case of Rollout projects where implementation in the first site had been done by consulting team and subsequent rollout by in-house team. ENTERPRISE BUSINESS SYSTEMS (EBS) ERP Consulting Partner Selection Selecting an ERP Consulting Partner: Doing Part of ERP Projects from Offshore ✔ Project Phases In an ERP Implementation 1)Project Preparation 2)Business Blueprint 3)Realisation 4)Final Preparation and Go Live 5)Support ENTERPRISE BUSINESS SYSTEMS (EBS) ERP Consulting Partner Selection Selecting an ERP Consulting Partner: Project phase wise What activity can be offshored Project Phase ▪ % of ▪ % of Type of activity from Offshore activity activity ▪ from from On-site Offshore Project Preparation 100% 0% Business Blueprint 90% 10% ▪ Building Proof of concept / Demo scenarios, Blueprint documentation (Partial) Realization 30% 70% ▪ Configuration, Testing, Development Final Preparation 50% 50% ▪ Data Migration, End user training, and Go Live Content preparation Support 20% 80% ▪ Resolving Issues, Running routine utility jobs, System development, Managing change requests ENTERPRISE BUSINESS SYSTEMS (EBS) ERP Consulting Partner Selection Selecting an ERP Consulting Partner: Doing Part of ERP Projects ✔ Activities that commonly get offshored from Offshore l Development l Unit testing, Volume testing l Training content preparation ✔ Support Activities that can be offshored to limited extent l Configuration l Data migration ✔ Activities that are difficult to offshore [hence done on-site] l Business blueprinting l Integration testing l UAT l End User Training l Change management activities ENTERPRISE BUSINESS SYSTEMS (EBS) ERP Consulting Partner Selection Selecting an ERP Consulting Partner: ERP Consulting Companies 1)IBM 2)Accenture 3)SAP 4)Cap gemini Etc. (see next slide) Many others ENTERPRISE BUSINESS SYSTEMS (EBS) ERP Consulting Partner Selection Selecting an ERP Consulting Partner: ERP Consulting Companies – Global Tier 1 1 IBM, Accenture, SAP Tier 2 Capgemini, Deloitte, HP, CSC, TCS, Infosys, Wipro Tier 3 HCL-Axon, Siemens, Cognizant, L&T Infotech, Atos, smaller cos., local players like Ramco... ENTERPRISE BUSINESS SYSTEMS (EBS) ERP Consulting Partner Selection Selecting an ERP Consulting Partner: Topic Summary ⚫Criteria for selection of Consulting Partner ⚫RFP method and process ⚫In-house vs. External consultants ⚫3 tiers of consulting companies ⚫Offshoring – GDC/ODC ODC = Offshore Development Center GDC = Global Delivery Center 105 THANK YOU Raghu B. A. Department of Computer Science and Engineering [email protected] ENTERPRISE BUSINESS SYSTEMS ERP2: Customer Relationship Management Raghu B. A. Department of Computer Science and Engineering [email protected] ENTERPRISE BUSINESS SYSTEMS ERP2: Customer Relationship Management (CRM) Raghu B. A. Department of Computer Science and Engineering ENTERPRISE BUSINESS SYSTEMS (EBS) ERP2: Customer Relationship Management Topic Agenda 1.Overview 2.CRM Benefits 3.CRM Application Areas 4.CRM Analytics 5.Leading CRM Products or Vendors ENTERPRISE BUSINESS SYSTEMS (EBS) ERP2: Customer Relationship Management CRM Introduction ✔ Customer Relationship Management (CRM) is a strategy for managing a company’s interactions with it’s customers and sales prospects. ✔ Often CRM is equated with automating business processes related to sales, marketing and customer service – CRM is not just about technology. ✔ It involves strategy and redesign of business processes with the overall goal to find, attract, and win new customers, retaining those customers and finally getting feedback from them to better design company’s product and customer facing processes. ENTERPRISE BUSINESS SYSTEMS (EBS) ERP2: Customer Relationship Management CRM Introduction ✔ CRM uses people, processes, and technology to gain insight into the behavior of customers ✔ CRM can bring together information from all data sources within an organization (and from outside the organization if needed like social media) to give one holistic view of customer in real time. ✔ CRM allows customer facing employees from sales, customer support, and marketing to make informed decisions on everything from cross selling and upselling opportunities to target marketing strategies to competitive positioning tactics. ✔ CRM can also reduce the costs of marketing, sales and customer service. ENTERPRISE BUSINESS SYSTEMS (EBS) ERP2: Customer Relationship Management CRM Benefits Higher Productivity Increased Customer Better Cross Retention / Sell / Up Sell Loyalty Better Improved profitability / Customer revenue per CRM Benefits Service / customer Satisfaction Reduced Sales Better and Marketing Opportunity Expenses Close Focused Marketing ENTERPRISE BUSINESS SYSTEMS (EBS) ERP2: Customer Relationship Management CRM Application Areas Sales Force Automation Field Service Revenue and Pricing e-Commerce Product Configuration CRM Call Centre Order Management Applications Partner Relationship Mgmt CRM Analytics Marketing ENTERPRISE BUSINESS SYSTEMS (EBS) ERP2: Customer Relationship Management CRM Application Areas 1)Sales Force Automations (SFA) 2)Field Service Applications 3)E-Commerce Applications 4)Call Center Applications 5)Partner Relationship Management 6)Marketing Management 7)Revenue and Pricing Management 8)Product Configuration Management ENTERPRISE BUSINESS SYSTEMS (EBS) ERP2: Customer Relationship Management Sales Force Automation (SFA) SFA applications help sales force in their daily jobs and aimed at increasing their productivity. With these applications sales force need not remember or store contact information of thousands of company’s existing customers and new prospects. SFA applications help them to manage new leads and sales opportunities. These applications helps sales force in managing sales in their territory and tracking sales performance, based on which they are provided incentive / compensation. Typical areas of sales force automation applications are: ✔ Contact management ✔ Lead management / Opportunity management ✔ Sales forecasting and pipeline ✔ Sales performance management ✔ Territory management ✔ Quote generation Web 2.0 is getting popularity among SFA vendors. ENTERPRISE BUSINESS SYSTEMS (EBS) ERP2: Customer Relationship Management E Commerce Application These applications help companies to buy, sell, and do other transactions over the Web. Today companies use these applications for variety of purposes like product search / browse, buying through shopping cart, product promotion, personalization, cross-sell and up-sell, product configurations, registries, multichannel ordering, customer self service etc. Today e-Commerce is becoming even more powerful with Web 2.0. Typical capabilities of E Commerce applications are: ✔ eMarketing ✔ Campaigns ✔ Cross sell / Up sell ✔ Personalization ✔ Online ordering ✔ Online product configuration ✔ Online auctions ✔ Online exchange and return ✔ Online Billing and Payment ENTERPRISE BUSINESS SYSTEMS (EBS) ERP2: Customer Relationship Management Call Centre / Contact Centre Application These solutions provide customer support by answering different types of customer queries / calls and routing the calls to the most competent person who can handle it. Call centre uses a variety of technologies like: local area networks (LAN), automatic call distributors (ACD), computer technology integration (CTI), web integration, interactive voice response (IVR), voice logging and messaging, IVR/speech portals etc. Call centers today are capable of supporting complex customer interactions, such as scheduling service requests, providing technical support, and handling financial transactions. Typical capabilities of call centre applications are: ✔ Predefined escalation route ✔ Previous records of the caller ✔ Support in different time zones in different languages ✔ Managing call assignments ✔ Knowledge base ✔ Self service capabilities ✔ Workflow ✔ Field service management ENTERPRISE BUSINESS SYSTEMS (EBS) ERP2: Customer Relationship Management Marketing Mgmt Application These applications are used by companies to manage their end-to-end process from gathering and analyzing customer data across web sites and other channels, to planning, budgeting, to executing customer communications and measuring results / effectiveness. It helps the enterprise identify and target its best customers and generate qualified leads for the sales team. Marketing automation also encompasses capabilities for managing customer loyalty, lists, collateral, and internal marketing resources. These tools support an integrated approach to marketing strategy, development, delivery, and measurement across the marketing mix. Typical capabilities of Marketing Management applications are: ✔ Campaign management ✔ Customer interaction management ✔ Marketing planning ✔ Marketing resource and asset management ✔ Opportunity / Lead management ✔ Loyalty marketing ENTERPRISE BUSINESS SYSTEMS (EBS) ERP2: Customer Relationship Management CRM Analytics There can be different types of CRM analytics like: ✔ Sales analytics: This allow companies monitor and understand customer actions and preferences, through dashboards that graphically display KPIs. ✔ Marketing analytics Marketing applications generally come with predictive analytics to improve customer segmentation and targeting, and tools to measure the effectiveness (ROI) of a marketing / sales promotion campaign. ✔ Customer service analytics are increasing in popularity as companies demand greater visibility into the performance of call centers and other support channels, in order to correct problems before they affect customer satisfaction levels. ▪ CRM applications support different types of customer analytics and reports through Dashboards, Built in reports, Custom reports, Trend analysis, Historical comparison, Graphics, Drilldown etc. ENTERPRISE BUSINESS SYSTEMS (EBS) ERP2: Customer Relationship Management Leading CRM Products ✔ Salesforce ✔ SAP ✔ Oracle ✔ Adobe ✔ Microsoft ✔ Zoho ENTERPRISE BUSINESS SYSTEMS (EBS) ERP2: Customer Relationship Management Leading CRM Products ✔ 2018 ENTERPRISE BUSINESS SYSTEMS (EBS) ERP2: Customer Relationship Management Topic Terminology 1) Sales Funnel 2) Leads conversion 3) > Prospects 4) > Opportunities [deals] 5) > Customer [Sales Order] 1) > Account [and Cases] 2) Repeat Sales / Customer 126 ENTERPRISE BUSINESS SYSTEMS (EBS) ERP2: Customer Relationship Management Topic Terminology 1) “Close the deal, In less time” 2) Cold calls 3) Contact 4) Customer satisfaction 5) Engagement 6) Follow up/through 7) Improve business, boost profits 8) Leads – catch ‘em all, hot leads 9) Loyal customers 10)Opportunity 11)Pipelines 12)Prospects 13)Relationships 14)Retention, Acquisition 15)Sales funnel 16)Strategy 127 ENTERPRISE BUSINESS SYSTEMS (EBS) ERP2: Customer Relationship Management Topic Agenda 1.Overview 2.CRM Benefits 3.CRM Application Areas 4.CRM Analytics 5.Leading CRM Products or Vendors 128 THANK YOU Raghu B. A. Department of Computer Science and Engineering [email protected] ENTERPRISE BUSINESS SYSTEMS ERP2: Supply Chain Management Raghu B. A. Department of Computer Science and Engineering [email protected] ENTERPRISE BUSINESS SYSTEMS ERP2: Supply Chain Management (SCM) Raghu B. A. Department of Computer Science and Engineering ENTERPRISE BUSINESS SYSTEMS (EBS) Supply Chain Management Topic Agenda ⚫Supply Chain Planning Overview and history of evolution of SCP Software ◦ Understanding the difference between Strategic, Tactical and Operational Planning ◦ Difference between Supply Chain Planning (SCP) and Execution (SCE) ◦ Comparison with ERP ⚫SCP Solutions - modules ⚫Collaborative Planning ◦ VMI ◦ CPFR ⚫SCM Application Vendors and Products ENTERPRISE BUSINESS SYSTEMS (EBS) Supply Chain Management Supply Chain Management (SCM) ⚫SCM is the oversight of materials, information, and finances as they move in a process from supplier to manufacturer to wholesaler to retailer to consumer. ⚫Supply chain management involves coordinating and integrating these flows both within and among companies/Users. ⚫Goal of effective supply chain management system is to reduce cost of inventory and efficient movement of materials (supply). ENTERPRISE BUSINESS SYSTEMS (EBS) Supply Chain Management SCM – Contd. ⚫SCM has become crucial ◦ Manufacturing at multiple sites, many vendors, distributors. ◦ Ex. – Consider the situation of Big Bazaar ordering for supply of plastic chairs to a manufacturer with many facilities across the country ⚫A method to optimize overall demand and supply flow ⚫Also known as IRP – Intelligent Resource Planning 134 ENTERPRISE BUSINESS SYSTEMS (EBS) Supply Chain Management SCM – Contd. ⚫Typically includes Inventory management ◦ Track costs and needs and optimize inventory levels ⚫Includes Warehouse management ◦ Space utilizations ◦ Interfaces to material moving equipment ◦ Integrate with material identification technology ⚫Transportation management ◦ Carrier selection, loading, routing, scheduling… ⚫Current day SCMs support “open data models”; allowing for sharing of data even outside the enterprise ◦ Suppliers would know status of inventory ◦ Customers would know status of orders, lead times... 135 ENTERPRISE BUSINESS SYSTEMS (EBS) Supply Chain Management SCM – Contd. ⚫Tracks flow of ◦ 1) Material movement movement of goods from a supplier to a customer, ◦ 2) Information / Documentation flow Mandatory forms, import/export, license-permit,... The information flow involves transmitting orders and updating the status of delivery. ◦ 3) Financial tracking Payment schedules, COD – Cash on Delivery handling, … 136 ENTERPRISE BUSINESS SYSTEMS (EBS) Supply Chain Management Importance of SCM/SCP ⚫Consider the cost of Mineral water bottle ◦ How much it costs you at the corner shop? ◦ How much would be the raw material cost? ◦ Is there a difference? Is it significant? Why? ⚫Related terms / concepts ◦ Work in Progress (WIP) ◦ Advanced Shipping Notice (ASN), ◦ GRN – Goods Received Note (GRN), ◦ Airway Bill Number (AWB) / Bill of Lading ◦ Vendor Managed Inventory (VMI) ◦ 3PL – Third Party Logistics ENTERPRISE BUSINESS SYSTEMS (EBS) Supply Chain Management Supply Chain Management ⚫Deals with movement of materials Supplier Manufacturer / Integrator Distributor Customer Retailer 138 ENTERPRISE BUSINESS SYSTEMS (EBS) Supply Chain Management SCOR standard for Supply Chain processes ⮚SCOR = Supply Chain Operational Reference ⮚What are the 5 basic components of a supply chain management system? ⮚ Plan, ⮚ Source, ⮚ Make, ⮚ Deliver, ⮚ Return. ENTERPRISE BUSINESS SYSTEMS (EBS) Supply Chain Management The seven “rights” are, Supply Chain Management Definitions 1) to deliver the right product, 2) in the right quantity and 3) the right condition, 4) to the right place 5) at the right time 6) for the right customer 7) at the right price. These seven rights highlighted the importance of moving and storing materials in an efficient, timely, and reliable manner. In commerce, supply chain management, the management of the flow of goods and services, involves the movement and storage of raw materials, of work-in-process (WIP) inventory, and of finished goods as well as end to end order fulfilment from point of origin to point of consumption. Wikipedia What is supply chain management (SCM) in simple words? Supply chain management is the management of the flow of goods and services and includes all processes that transform raw materials into final products. It involves the active streamlining of a business's supply-side activities to maximize customer value and gain a competitive advantage in the marketplace. Jul 1, 2020 ENTERPRISE BUSINESS SYSTEMS (EBS) Supply Chain Management Supply Chain Planning Solutions - Evolution ⚫Term SCM became popular post 1995 Value Perception ✔ Advanced Demand Planning ✔ Supply Chain Planning and Optimization ✔ Production scheduling, Optimization ✔ Transportation Planning, ✔ Route Optimization ✔ Global Available to Promise ✔ MRP 2 ✔ Advanced Collaboration ✔ Material Requirement ✔ Demand Planning Calculation Like VMI, CPFR etc. ✔ Integration with SCM execution ✔ Calculation of M/c / Labor systems (Transport, Warehouse, Resource Materials Management, ✔ Sales & Ops Plan (SOP) Production Execution) ✔ Master Schedule (MPS) ✔ Order Promising (ATP) ✔ Distribution Plan (DRP) ✔ Capacity Planning MRP 2 ERP SCM Planning & Collaboration ENTERPRISE BUSINESS SYSTEMS Supply Chain Management Raghu B. A. Department of Computer Science and Engineering ENTERPRISE BUSINESS SYSTEMS (EBS) Supply Chain Management Strategic, Tactical & Operational Planning ▪Supply chain planning helps decisions at 3 levels: ⚫1) Strategic decisions: Long term decisions. l Critical decision for the company having long term implications – #years. (Even beyond annual business plan) ◦ Factory geography, warehouse locations, sources for procurement – local / global, etc. ◦ Decisions are difficult to reverse without substantial cost for the change. ◦ These decisions influence company’s long term profit and sales goal. ⚫2) Tactical decisions: Medium term decisions. ◦ Applicable for months to quarters. ◦ Sales and Operations planning, MPS, MRP fall in this category. ⚫3) Operational decisions: Short term decisions. ◦ Reviewed week/daily. ◦ Vendor schedules, distribution plan, transportation and route plan, etc. fall in this category. ENTERPRISE BUSINESS SYSTEMS (EBS) Supply Chain Management Different planning horizon needs separate SCP Strategic What is my long term capacity management strategy? Years (Yearly / Quarterly) What is my most optimized network design? {Planning Tools: Network Design, Long Term Planning(LTP)} Tactical How do I meet my monthly customer requirements? (Monthly / Weekly) {Planning Tools: Sales and Operations Planning (SOP), Master Production Scheduling (MPS), Material Requirement Planning (MRP)} Operational How do I schedule my orders, my transport routes? (Daily / Hourly) {Planning Tools: Detailed scheduling, Transportation Planning, Minutes Route scheduling} ENTERPRISE BUSINESS SYSTEMS (EBS) Supply Chain Management ROI Impac t Strategic Tactical Operational Years Quarters Month Days Hours Planning Horizon Strategic supply chain decisions have maximum impact on business ENTERPRISE BUSINESS SYSTEMS (EBS) Supply Chain Management What is SCM, SCP and SCE? ⚫Supply Chain Management (SCM) is the management of a network of interconnected activities towards the provision of product and/or service packages required by the end customers. Since customers may have customers (B2B) in turn, this forms a business chain or supply chain. ⚫Supply chain management spans all movement and storage of raw materials, work- in-process inventory, and finished goods from point of origin to point of consumption. ⚫SCM is sometimes broken down into the stages of planning, execution and shipping. l Supply Chain Planning (SCP) and l Supply Chain Execution (SCE) l are the two main categories of SCM. ⚫Supply Chain Planning (SCP) is the component of supply chain management (SCM) involved with predicting future requirements to balance supply and demand. ENTERPRISE BUSINESS SYSTEMS (EBS) Supply Chain Management ERP vs. Supply Chain Planning ERP Supply Chain Planning Focus Transaction and Basic Planning Advanced Planning and Optimization Planning Order Sequential planning of material and Simultaneous planning of material and capacity capacity Prioritization Can not handle any prioritization rule Can handle any prioritization rules (Customer, Product etc) Handling Simulation Limited simulation capability Have extensive simulation capability Constraints Can not do any constraints based planning Can do constraint based planning planning Capacity Mgmt Plan based on infinite capacity Can plan based on finite capacity i.e. available capacity Forecasting Have basic forecasting capability Have advanced forecasting capability (Statistical forecasts/ Causal models etc) Replanning Replanning takes long time Replanning can be very quick ATP – Available to Limited order promising capability Advanced order promising capability in terms of alternate promise location or alternate product ENTERPRISE BUSINESS SYSTEMS Supply Chain Management Raghu B. A. Department of Computer Science and Engineering ENTERPRISE BUSINESS SYSTEMS (EBS) Supply Chain Management Supply Chain Planning Solution – Modules Typical modules of supply chain planning are: ✔ Network design ✔ Demand planning ✔ Supply Network planning ✔ Production planning ✔ Detailed scheduling ✔ Transportation planning ✔Vehicle Scheduling ✔Route Planning ENTERPRISE BUSINESS SYSTEMS (EBS) Supply Chain Management Supply Chain Planning Solutions ENTERPRISE BUSINESS SYSTEMS (EBS) Supply Chain Management SAP APO Supply Chain Product Suite APO APO Supply Chain Cockpit Demand Planning PP / DS Supply Global Network ATP Planning Deployment Transportation Planning ENTERPRISE BUSINESS SYSTEMS Supply Chain Management Raghu B. A. Department of Computer Science and Engineering ENTERPRISE BUSINESS SYSTEMS (EBS) Supply Chain Management Supply Chain Planning Solutions – Vendors ✔ i2 / JDA { Strong in Retail } ✔ SAP (SAP Advanced Planner and Optimizer solution - APO) ✔ Oracle (Oracle Advanced Planning and Scheduling solutions / Oracle Value Chain planning – APS) ✔ Manugistics / JDA ✔ Adexa ✔ Demantra ✔ Logility ✔ Aspentech { Strong in Process Industry } ✔ IFS ✔ IBM’s ILOG SCO https://www.supplychain247.com/article/2019_top_20_supply_chain_software_suppliers/technology ENTERPRISE BUSINESS SYSTEMS (EBS) Supply Chain Management SCP & SCE Solution Providers ENTERPRISE BUSINESS SYSTEMS (EBS) Supply Chain Management Topic Summary ⚫SCP is a specialized application to ensure balanced management of orders and supply ⚫Goal is optimization of many of the elements involved in the supply chain ⚫SCP helps planning chain – strategic, tactical and operational THANK YOU Raghu B. A. Department of Computer Science and Engineering [email protected] ENTERPRISE BUSINESS SYSTEMS ERP2: Product Lifecycle Management Raghu B. A. Department of Computer Science and Engineering [email protected] ENTERPRISE BUSINESS SYSTEMS ERP2: Product Lifecycle Management (PLM) Raghu B. A. Department of Computer Science and Engineering ENTERPRISE BUSINESS SYSTEMS (EBS) ERP2: Product Lifecycle Management Topic Agenda 1.Overview 2.Why PLM – Business Drivers & Value Proposition 3.Phases of Product Life Cycle 4.The BCG Matrix 5.PLM differences with ERP 6.PLM Functionalities 7.PLM Product Vendors ENTERPRISE BUSINESS SYSTEMS (EBS) ERP2: Product Lifecycle Management Product Life cycle Management Product lifecycle management (PLM) is a new set of enterprise application that manages all data and information about a product from its initial conception to retirement. Product lifecycle includes conceptualization of the product, design, manufacturing, ensuring quality of the product through out its life cycle, ensuring product safety during its manufacturing – distribution and usage and finally service from concept to development till the product retires from service. Products may have short (market) life cycle / lifespan or a prolonged one. A winter fashion Or a ship engine ENTERPRISE BUSINESS SYSTEMS (EBS) ERP2: Product Lifecycle Management Product Lifecycle Management( PLM) ⚫PLM is designed to manage creation, storage, change, version, and configuration of all the data, information, and relationships required to build, maintain, and support the product throughout its lifecycle. Supporting collaboration and process automation ⚫PLM processes are cross functional – involves multiple functions ◦ R&D, Engineering, Marketing, Production, Quality, Sales and Service ◦ May also involve business partners who are involved in one or more phases of the product Say, a car dealer ENTERPRISE BUSINESS SYSTEMS (EBS) ERP2: Product Lifecycle Management Product Life cycle ENTERPRISE BUSINESS SYSTEMS (EBS) ERP2: Product Lifecycle Management Product Life cycle ENTERPRISE BUSINESS SYSTEMS (EBS) ERP2: Product Lifecycle Management Seamless Integration ⚫Tight linkage between operational planning and execution is very important ⚫Also critical is “Engineering Change Management” ◦ A well defined product / service is the essence of the organization. ◦ Changes to product design, production planning, quality control, packaging and other product line dependencies are to be highly controlled. *** PDM – Product Data Management Keep track of all product related data – organization, management, analysis Accessible across company by relevant functions to add notes about releases and revisions. ENTERPRISE BUSINESS SYSTEMS (EBS) ERP2: Product Lifecycle Management Business Drivers for PLM Today’s business is facing challenges – becoming very important to maintain product information for following reasons: Regulatory Compliance Pressure Intellectual Asset Mgmt Reduced Engg Resource Promotion Shorter Product Life Cycle Cost Reduction Pressure Objectives More products Increased Focus on Innovation Product Development had become global ENTERPRISE BUSINESS SYSTEMS (EBS) ERP2: Product Lifecycle Management PLM – Business Drivers ⚫Product Variants and growing product lines ◦ Company has to cater to different segments of users ◦ Maximize infrastructure and other resources ◦ “Hedge” against single product risks ◦ Acquisitions ⚫Shorter product development cycles ◦ Window of opportunity is getting smaller ◦ To be the first in marketplace for both credibility and profitability ⚫Cost reduction pressure ◦ Facilitate design reuse, quicker access to fact sheets & design info. ⚫Reduced engineering resources ◦ Support design outsourcing ENTERPRISE BUSINESS SYSTEMS (EBS) ERP2: Product Lifecycle Management PLM – Business Drivers ❖ Collaboration needs with local and global partners ❖ ❖Unified environment to deal with distributed teams ❖Collaboration features ❖Connectivity with other design software – CAD / other ERP ❖ Regulatory compliance ❖Increasing demands – Ex. Environmental standards ❖Auditing - Traceability of design / manufacturing process ❖Special process requirements – FDA ❖Quality standards – process compliances – ISO 9001, CAM ❖ Process and data integration needs between R&D, Production, Supply ❖ Innovation focus – business model, processes, product ❖ Intellectual asset management ❖Control of information access; ❖Guarding against infringement ❖ Documentation control ❖Structured storage of all relevant info, - Otherwise poorly maintained information ENTERPRISE BUSINESS SYSTEMS (EBS) ERP2: Product Lifecycle Management Value Drivers Of PLM Accelerate new product Environmental introduction Compliance Drive, facilitate and Higher Engg Productivity capture innovation Manage complete product Reuse of Parts life cycle ENTERPRISE BUSINESS SYSTEMS (EBS) ERP2: Product Lifecycle Management Topics ?Current ?All Standards Bodies and Structures 163 Standards 581 Standards Chassis 241 Standards 581 Standards Automotive Design Engineering and Styling 33 Standards 76 Standards Industry Electrical, Electronics and Avionics 338 Standards 869 Standards Standards Environment 72 Standards 187 Standards Fuels and Energy Sources 241 Standards 645 Standards Human Factors and Ergonomics 101 Standards 252 Standards Interiors, Cabins and Cockpits 179 Standards 407 Standards Maintenance and Aftermarket 138 Standards 351 Standards Management and Product 90 Standards 283 Standards Development ENTERPRISE BUSINESS SYSTEMS (EBS) ERP2: Product Lifecycle Management PLM – Benefits ❖Addresses the requirement of business drivers adequately. ❖Eliminates manual processes and integrates automated parts. ❖Tight integration between manufacturing BOM, engineering change management (ECM) and product design data; ❖Reduces ‘lead time’ for manufacture and ensures correct operation. ❖Integrates with SCP ENTERPRISE BUSINESS SYSTEMS (EBS) ERP2: Product Lifecycle Management PLM - Data elements across product lifecycle Product Lifecycle Management Portfolio Concept Production Maintenance Retirement planning development Design and support and disposal Product Data / Information Product Plans Product Design / Engg Manufacturing Maintenance Performance requirements Bill of Materials Bill of instructions specifications CAD files (EBOM) Materials Spare parts Engineering (MBOM) Release Part and Schedules material changes Packaging specifications Part instructions Process specification specifications ENTERPRISE BUSINESS SYSTEMS (EBS) ERP2: Product Lifecycle Management PLM – Phase wise needs - Summary ❖PortfolioPlanning ❖ Consistent management of information across long periods of time 18 – 36 months during design and development ❖Connect multiple projects ❖Concept Development ❖Collaboration support, ❖Adhoc import/export from variety of sources ❖Design ❖Parallel design, multiple versions, review changes, ❖Integration with CAD software ❖IP – Intellectual Property handling ENTERPRISE BUSINESS SYSTEMS (EBS) ERP2: Product Lifecycle Management PLM – Phase wise needs - Summary ❖Production ❖Integrate with ERP for production; pass on quality specifications ❖MBOM – Manufacturing BOM ❖Export special info related to production & packing ❖Maintenance & Support ❖Handle product design change situations ❖Support product performance data collection and analytics ❖Retirement = Product withdrawal = Sunset = End-of-life ❖Link with next generation product appropriately ❖Upgrade paths ENTERPRISE BUSINESS SYSTEMS (EBS) ERP2: Product Lifecycle Management Topic Agenda 1.Overview 2.PLM Business Drivers & Value Proposition 3.Phases of PLM 4.The BCG Matrix 5.PLM differences with ERP 6.PLM – Functionalities 7.Product Safety and Environmental Compliance ENTERPRISE BUSINESS SYSTEMS (EBS) ERP2: Product Lifecycle Management Product Lifecycle: The BCG Matrix The growth–share matrix (aka the product portfolio matrix, Boston Box, BCG-matrix, Boston matrix, Boston Consulting Group analysis, portfolio diagram) is a chart that was created by Bruce D. Henderson for the Boston Consulting Group in 1970 to help corporations to analyze their business units, that is, their product lines. This helps the company allocate resources and is used as an analytical tool in brand marketing, product management, strategic management, and portfolio analysis. -- https://en.wikipedia.org/wiki/Growth-share_matrix ENTERPRISE BUSINESS SYSTEMS (EBS) ERP2: Product Lifecycle Management Topic ENTERPRISE BUSINESS SYSTEMS (EBS) ERP2: Product Lifecycle Management ERP and PLM system - Differences ERP System PLM System ▪ Typically supports the processes in Sales, Finance, HR, ▪ Typically supports the processes in R&D and Procurement and Production department of a company Engineering department of a company ▪ Supports transaction oriented processes ▪ Supports innovation processes ▪ Starts from the point the product and its components ▪ Helps in defining the Bill of material and has a defined Bill of material and specification specification for the product ▪ ERP systems do not capabilities to store documents of ▪ PLM systems have specific document different format (especially design and drawing management solutions to store data in documents). different formats. ▪ ERP systems with only one Bill of material for items ▪ PLM systems can work with several Bill of (Manufacturing BOM) material (Engineering BOMs) and configuration options to come up with optimum BOM design ▪ ERP systems do not have 2D or 3D visualization ▪ PLM systems offer strong visualization capabilities of product structure. capability. ▪ ERP solutions do not offer out of box integration with ▪ PLM solutions offer out of box integration with CAD software. CAD software. ▪ ERP systems do not support system engineering. ▪ PLM systems support system engineering. ENTERPRISE BUSINESS SYSTEMS (EBS) ERP2: Product Lifecycle Management PLM Integration 1) Leading PLM software need to integrate with CAD tools. 2) ERP Integration When thinking of the relationship between PLM and ERP systems, it is helpful to think of PLM managing the product innovation process and then ERP managing the execution process. PLM builds the product definition, while ERP builds the physical part. For any business to run successfully, PLM systems need to be integrated with ERP systems for sourcing the components for new product, for costing the product and finally manufacturing it. ENTERPRISE BUSINESS SYSTEMS (EBS) ERP2: Product Lifecycle Management Product Lifecycle Management (PLM) Functionalities Product Safety Handling hazardous / dangerous goods Environmental compliance System Engg Integration Requirement Mgmt ▪ CAD ▪ ERP Portfolio / Product Data Mgmt (PDM) Project Storing Product data in different formats Portfolio Mgmt Managing BOM / Configuration / Structure Program Mgmt Visualization Project Mgmt Collaboration Idea Mgmt Workflow Change Mgmt ENTERPRISE BUSINESS SYSTEMS (EBS) ERP2: Product Lifecycle Management PLM Functionality – BOM Management Bill Of Material Management ✔ BOM Management capability includes building BOM structures, adding or removing parts, comparing BOMs, and managing BOM changes and transformation through their lifecycle. ✔ PLM systems help in transformation of a CADBOM to EBOM (Engineering BOM) to MBOM (Manufacturing BOM). ✔ PLM systems can manage complex BOMs through their lifecycle and configuration changes. ✔ PLM systems also have the ability to manage configurable options within a BOM. ✔ PLM systems also support BOM Cost Management through different BOM comparison. ⚫EBOM = Engineering Bill of Materials Organized according to CAD/EDA tool and engineers’ preferences and processes Represents only the physical product being “engineered,” not the packaging or manufacturing consumables Often includes items for a single engineering discipline only, summarizing or excluding items from other disciplines ⚫MBOM = Manufacturing Bill of Materials ◦ Organized into sub-assemblies that reflect the manufacturing process ◦ Represents the physical product, packaging and included documentation ◦ Contains all components required to build the product — MTS, OTS, mechanical, electrical, software & firmware ENTERPRISE BUSINESS SYSTEMS (EBS) ERP2: Product Lifecycle Management PLM Functionality – New Product Development (NPD & NPI) ⚫New Product Development: An organisation’s new product development (NPD) or new product introduction (NPI) process can be managed through the programme/project management function. Typical phases of a new product development cycle are: market research, idea generation, concept feasibility, concept development and project planning, design and development, ramp up, launch and production start up, production and phase out/retirement. ENTERPRISE BUSINESS SYSTEMS (EBS) ERP2: Product Lifecycle Management PLM Vendors Some of the leading vendors in PLM space are listed below: ✔ CAD (Computer Aided Design) / ✔ CAM (Computer Aided Manufacturing) / ✔ CAE (Computer Aided Engineering) / ✔ Document Management System vendors moving into PLM space PTC Dassault Systémes Siemens Leading ERP vendors building PLM solution: SAP Oracle IFS ENTERPRISE BUSINESS SYSTEMS (EBS) ERP2: Product Lifecycle Management 222 ENTERPRISE BUSINESS SYSTEMS (EBS) ERP2: Product Lifecycle Management Leading PLM Products ✔ 2018 ✔ Dassault - Enovia ✔ PTC - Windchill ✔ Siemens PLM ✔ Autodesk Vault, Fusion ✔ SAP PLM ✔ Oracle Agile PLM ✔ IFS ✔ Infor Opitva https://www.ptc.com/en/resources/plm/report/quadrant-knowledge-solutions-repor https://www.predictiveanalyticstoday.com/top-product-lifecycle-management-plm-software/ ENTERPRISE BUSINESS SYSTEMS (EBS) ERP2: Product Lifecycle Management Future of PLM Market ENTERPRISE BUSINESS SYSTEMS (EBS) ERP2: Product Lifecycle Management Topic Summary ⚫PLM is an important area for industries with design a