UNIT 1 MMD - RV College of Engineering PDF
Document Details
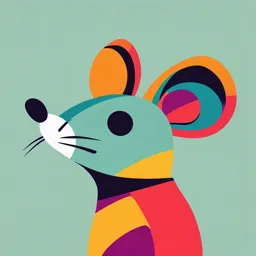
Uploaded by WellReceivedSerpentine5267
R.V. College of Engineering
Keshavamurthy YC
Tags
Summary
This document is UNIT 1 of the Metrology and Machine Drawing course at RV College of Engineering. It covers concepts of measurements, methods, and the evolution of standards. Keywords include measurement, metrology, standards, and engineering.
Full Transcript
Go, change the world RV College of Engineering Course Title: Metrology and Machine Drawing Course Code: 21ME35 UNIT 1 By: Keshavamurthy YC RV College of Go,...
Go, change the world RV College of Engineering Course Title: Metrology and Machine Drawing Course Code: 21ME35 UNIT 1 By: Keshavamurthy YC RV College of Go, change the world UNIT -I Engineering Concepts of Measurements: Methods of measurements, errors in measurements, accuracy and precision, repeatability, standards and their roles, wavelength standard, modern metre, Hierarchical classification of standards, Line and End measurements, calibration of end bars. Fundamentals of measurement systems, generalized measurement system Transducers-Characteristics transfer efficiency, primary and secondary transducers, mechanical transducers. KYC 11-Jan-23 2 RV College of Go, change the world EXPLORATION Engineering During the ancient times, an Egyptian carpenter never misplaced his ruler because it was attached to his body. A span is the distance measured by a human hand, from the tip of the thumb to the tip of the little finger of an outstretched hand. In ancient times, a span was considered to be half a cubit. 11-Jan-23 KYC 3 RV College of Go, change the world EXPLORATION Engineering A cubit is the distance from the tip of the middle finger of the outstretched hand to the front of the elbow. 11-Jan-23 KYC 4 RV College of Go, change the world Engineering MEASURING INSTRUMENTS 11-Jan-23 KYC 5 RV College of Go, change the world Engineering EVOLUTION OF STANDARDS A brief look at history reveals the following interesting facts. The Egyptian cubit was the earliest recorded length standard—the length of the Pharaoh’s forearm plus the width of his palm. The royal cubit was the first master standard made out of black granite, which was used in Egyptian pyramid construction. The actual foot length of the Greek monarch was defined as a foot. King Henry I decreed the length from the tip of nose to the end of the middle finger, when the arm is fully stretched as one yard. The metric system, which was accepted by France in 1795, coexisted with medieval units until 1840, when it was declared as the exclusive system of weights and measures. In 1798, Eli Whitney introduced the concept of manufacturing interchangeable components for assembling guns. This led to the development of standardization of manufacturing activities to achieve 11-Jan-23 interchangeability KYC 6 RV College of Go, change the world EVOLUTION OF STANDARDS Engineering In 1855, the imperial standard yard was developed in England, which was quite accurate. In 1872, the first international prototype metre was developed in France. The International Metric Convention, which was held in France in 1875, universally accepted the metric system, and provisions were also made to set up the International Bureau of Weights and Measures (BIPM – Bureau International des Poids et Mesures) in Paris, which was signed by 17 countries. In 1866, the USA passed an act of Congress to employ the metric system of weights and measures in all contracts, dealings, and court proceedings. In the USA, since 1893, the internationally accepted metric standards have served as the basic measurement standards. Around 35 countries, including continental Europe and most of South America, officially adopted the metric system in 1900. 11-Jan-23 KYC 7 RV College of Go, change the world EVOLUTION OF STANDARDS Engineering Establishment of international organizations for standardization such as the International Electrotechnical Commission (IEC) in 1906 and the International Organization for Standardization (ISO) in 1947. In October 1960, at the 11th General Conference on Weights and Measures held in Paris, the original metric standards were redefined in accordance with the 20th-century standards of measurement and a new revised and simplified international system of units, namely the SI units was devised. SI stands for systeme international d’unites (international system of units). In 1999, a mutual recognition arrangement (MRA) was signed by the Committee of Weights and Measures to cater to the growing need for an open, transparent, and comprehensive method to provide users with reliable quantitative information on the comparability of national metrology services. 11-Jan-23 KYC 8 RV College of Go, change the world Introduction to Measurements Engineering Definition : Measurement is defined as the process of obtaining a quantitative comparison between a predefined standard and an unknown magnitude. OR Measurement is a process of comparing quantitatively an unknown magnitude with a predefined standard. Requirements Standards must be accurately known Procedure & apparatus –commonly accepted & provable Significance of measurement system Fundamental basis for R&D Measurement is fundamental element of any process control Measurement is required for proper performance Forms basis of commerce. 11-Jan-23 KYC 9 RV College of Go, change the world GENERAL MEASUREMENT CONCEPTS Engineering The primary objective of measurement in industrial inspection is to determine the quality of the component manufactured. Different quality requirements, such as permissible tolerance limits, form, surface finish, size, and flatness, must be considered to check the conformity of the component to the quality specifications. Quantitative information of a physical object or process has to be acquired by comparison with a reference. 11-Jan-23 KYC 10 RV College of Go, change the world Engineering Fundamentals of measurement systems The three basic elements of measurements Measurand, a physical quantity such as length, weight, and angle to be measured. Comparator, to compare the measurand (physical quantity) with a known standard (reference) for evaluation. Reference, the physical quantity or property to which quantitative comparisons are to be made, which is internationally accepted. All these three elements would be considered to explain the direct measurement using a calibrated fixed reference. In order to determine the length (a physical quantity called measurand) of the component, measurement is carried out by comparing it with a steel scale (a known standard). 11-Jan-23 KYC 11 RV College of Go, change the world Fundamentals of measurement systems Engineering 11-Jan-23 KYC 12 RV College of Go, change the world Engineering Methods of Measurement Measurements are performed to determine the magnitude of the value and the unit of the quantity under consideration. For instance, the length of a rod is 3m, where the number, 3, indicates the magnitude and the unit of measurement is meter. The choice of the method of measurement depends on the required accuracy and the amount of permissible error. Irrespective of the method used, the primary objective is to minimize the uncertainty associated with measurement. The common methods employed for making measurements are as follows: Direct method, Indirect method, Fundamental or absolute method, Comparative method, Transposition method, Coincidence method, Deflection method, Complementary method, Null measurement method, substitution method, Contact method, Contactless method, Composite method 11-Jan-23 KYC 13 RV College of Go, change the world Methods of Measurement Engineering Direct method: The quantity to be measured is directly compared with the primary or secondary standard. Scales, vernier callipers, micrometers, bevel protractors, etc., are used in the direct method. This method is widely employed in the production field. In the direct method, a very slight difference exists between the actual and the measured values of the quantity. This difference occurs because of the limitation of the human being performing the measurement. Indirect method: In this method, the value of a quantity is obtained by measuring other quantities that are functionally related to the required value. Measurement of the quantity is carried out directly and then the value is determined by using a mathematical relationship. Some examples of indirect measurement are angle measurement using sine bar, measurement of strain induced in a bar due to the applied force, determination of effective 11-Jan-23 diameter of a screw thread, etc. KYC 14 RV College of Go, change the world Methods of Measurement Engineering Fundamental or absolute method: In this case, the measurement is based on the measurements of base quantities used to define the quantity. Fundamental measures are estimated directly from observation (such as height and weight), rather than derived indirectly by means of other measures (such as density and electrical resistance). Comparative method: In this method, the quantity to be measured is compared with the known value of the same quantity or any other quantity practically related to it. The quantity is compared with the master gauge and only the deviations from the master gauge are recorded after comparison. The most common examples are comparators, dial indicators, etc. Transposition method: This method involves making the measurement by direct comparison, wherein the quantity to be measured (V) is initially balanced by a known value (X) of the same quantity; next, X is replaced by the quantity to be measured and balanced again by another known value (Y). If the quantity to be measured is equal to both X and Y, then it is equal to V = XY An example of this method is the determination of mass by balancing methods and known weights. 11-Jan-23 KYC 15 RV College of Go, change the world Engineering Methods of Measurement Coincidence method: This is a differential method of measurement wherein a very minute difference between the quantity to be measured and the reference is determined by careful observation of the coincidence of certain lines and signals. Measurements on Vernier caliper and micrometer are examples of this method. Deflection method: This method involves the indication of the value of the quantity to be measured directly by deflection of a pointer on a calibrated scale. Pressure measurement is an example of this method. Complementary method: The value of the quantity to be measured is combined with a known value of the same quantity. The combination is so adjusted that the sum of these two values is equal to the predetermined comparison value. An example of this method is determination of the volume of a solid by liquid displacement. Null measurement method: In this method, the difference between the value of the quantity to be measured and the known value of the same quantity with which comparison is to be made is brought to zero. 11-Jan-23 KYC 16 RV College of Go, change the world Engineering Methods of Measurement Substitution method: It is a direct comparison method. This method involves the replacement of the value of the quantity to be measured with a known value of the same quantity, so selected that the effects produced in the indicating device by these two values are the same. The Borda’s method of determining mass is an example of this method. Contact method: In this method, the surface to be measured is touched by the sensor or measuring tip of the instrument. Care needs to be taken to provide constant contact pressure in order to avoid errors due to excess constant pressure. Examples of this method include measurements using micrometer, vernier caliper, and dial indicator. Contactless method: As the name indicates, there is no direct contact with the surface to be measured. Examples of this method include the use of optical instruments, tool maker’s microscope, and profile projector. 11-Jan-23 KYC 17 RV College of Go, change the world Methods of Measurement Engineering Composite method The actual contour of a component to be checked is compared with its maximum and minimum tolerance limits. Cumulative errors of the interconnected elements of the component, which are controlled through a combined tolerance, can be checked by this method. This method is very reliable to ensure interchangeability and is usually effected through the use of composite GO gauges. The use of a GO screw plug gauge to check the thread of a nut is an example of this method. 11-Jan-23 KYC 18 RV College of Go, change the world Methods of Measurement Engineering Null Deflection Contact KYC Contactless 11-Jan-23 19 RV College of Go, change the world Engineering Generalized System of Measurement Physical quantities such as length and mass can be directly measured using measuring instruments. However, the direct measurement of physical quantities such as temperature, force, and pressure is not possible. In such situations, measurements can be performed using a transducer, wherein one form of energy/signal that is not directly measurable is transformed into another easily measurable form. Calibration of the input and output values needs to be carried out to determine the output for all vales of input. A generalized measurement system essentially consists of three stages. Each of these stages performs certain steps so that the value of the physical variable to be measured is displayed as an output for our reference. 11-Jan-23 KYC 20 RV College of Go, change the world Engineering Generalized System of Measurement The three stages of a measurement system are as follows Stage I : A Detector –transducing or sensor stage Stage II: An Intermediate stage modifying stage, or signal conditioning stage Stage III: A Terminating or read-out stage 11-Jan-23 KYC 21 RV College of Go, change the world Engineering Generalized System of Measurement BLOCK DIAGRAM OF THE GENERALIZED MEASURING SYSTEM 11-Jan-23 KYC 22 RV College of Go, change the world Generalized System of Measurement Engineering BLOCK DIAGRAM OF THE GENERALIZED MEASURING SYSTEM 11-Jan-23 KYC 23 RV College of Go, change the world Engineering Generalized System of Measurement STAGE I: DETECTOR–TRANSDUCER STAGE The main function of the primary detector–transducer stage is to sense the input signal and transform it into its analogous signal, which can be easily measured. The input signal is a physical quantity such as pressure, temperature, velocity, heat, or intensity of light. The device used for detecting the input signal is known as a transducer or sensor. The transducer converts the sensed input signal into a detectable signal, which may be electrical, mechanical, optical, thermal, etc. The generated signal is further modified in the second stage. The transducer should have the ability to detect only the input quantity to be measured and exclude all other signals. 11-Jan-23 KYC 24 RV College of Go, change the world Engineering Generalized System of Measurement STAGE II: INTERMEDIATE MODIFYING STAGE In the intermediate modifying stage of a measurement system, the transduced signal is modified and amplified appropriately with the help of conditioning and processing devices before passing it on to the output stage for display. Signal conditioning (by noise reduction and filtering) is performed to enhance the condition of the signal obtained in the first stage, in order to increase the signal-to-noise ratio. If required, the obtained signal is further processed by means of integration, differentiation, addition, subtraction, digitization, modulation, etc. It is important to remember here that in order to obtain an output that is analogous to the input, the characteristics of the input signals should be transformed with true fidelity. 11-Jan-23 KYC 25 RV College of Go, change the world Generalized System of Measurement Engineering STAGE II: OUTPUT OR TERMINATING STAGE The output or terminating stage of a measurement system presents the value of the output that is analogous to the input value. The output value is provided by either indicating or recording for subsequent evaluations by human beings or a controller, or a combination of both. The indication may be provided by a scale and pointer, digital display. Thus, measurement of physical quantities such as pressure, force, and temperature, which cannot be measured directly, can be performed by an indirect method of measurement. This can be achieved using a transduced signal to move the pointer on a scale or by obtaining a digital output. 11-Jan-23 KYC 26 RV College of Go, change the world Engineering Example of Generalized Measurement System Figure: Tyre gauge for measuring pressure in automobiles 11-Jan-23 Figure: Block diagram KYC of tyre gauge functions 27 RV College of Go, change the world Example of Generalized Measurement System Engineering To illustrate a very simple measuring system, let us consider the familiar tyre gauge used for checking automobile tyre pressure. It consists of a cylinder and piston, a spring resisting the piston movement, a stem with scale divisions. As the air pressure bears against the piston, the resulting force compresses the spring until the spring and air forces balance. The calibrated stem, which remains in place after the spring returns the piston, indicates the applied pressure. The piston-cylinder combination constitutes a force-summing apparatus, sensing and transducing pressure to force. As a secondary transducer, the spring converts the force to a displacement. Finally, the transduced input is transferred without signal conditioning to the scale and index for read out. 11-Jan-23 KYC 28 RV College of Go, change the world Example of Generalized Measurement System Engineering 11-Jan-23 Block diagram of measuring KYC system of acceleration 29 RV College of Go, change the world Example of Generalized Measurement System Engineering Illustration of more complex system (measurement of velocity). The first stage device, the accelerometer, provides voltage analogous to acceleration. In addition to voltage amplifier, the second stage may also include a filter that selectively attenuates unwanted high frequency noise components. It may also integrate the analogue signal with respect to time, thereby providing velocity-time relation, rather than an acceleration time signal. Finally, the signal voltage will probably need to be increased to the level necessary to be sensed by the third or recording and read out stage, which may consist of data acquisition computer and printer. The final record will then be in the form of computer generated graph. 11-Jan-23 KYC 30 RV College of Go, change the world SI: fundamental Units Engineering Physical Quantity Unit Name Symbol length meter m mass kilogram kg time second s electric current ampere A temperature Kelvin K amount of substance mole mol luminous intensity candela cd 11-Jan-23 KYC 31 RV College of Go, change the world Engineering SI: Derived Units Physical Quantity Unit Name Symbol area square meter m2 volume cubic meter m3 speed meter per second m/s acceleration meter per second square m/s2 weight, force newton N pressure pascal Pa energy, work joule J 11-Jan-23 KYC 32 RV College of Go, change the world Supplementary units Engineering Physical Quantity Unit Name Symbol Plane angle Radian rad Solid angle Steradian sr 11-Jan-23 KYC 33 RV College of Go, change the world STANDARDS OF MEASUREMENT Engineering During the medieval period, the measurement process underwent an evolution and people accepted the process in specific trades, but no common standards were set. In order to make measurements a meaningful exercise, comparison with a known quantity is very essential. It is necessary to define a unit value of any physical quantity under consideration such that it will be accepted internationally. Standard is defined as the fundamental value of any known physical quantity, as established by national and international organizations of authority, which can be reproduced. Fundamental units of physical quantities such as length, mass, time, and temperature form the basis for establishing a measurement system. Standards play a vital role for manufacturers across the world in achieving consistency, accuracy, precision, and repeatability in measurements and in supporting the system that enables the manufacturers to make such measurements. 11-Jan-23 KYC 34 RV College of Go, change the world MEASUREMENTS STANDARDS LABORATORY Engineering International International Organization of Legal Metrology, Paris International Bureau of Weights and Measures at Sevres, France India National Physical Laboratory Dr. K.S. Krishnan Marg New Delhi – 110012 India Phone: 91-11-45609212 Fax: 91-11-45609310 Email: [email protected] or [email protected] KYC 11-Jan-23 35 RV College of Go, change the world Engineering MATERIAL STANDARD Two standard systems for linear measurement that have been accepted and adopted worldwide are yard and metric systems. Most countries have realized the importance and advantages of the metric system and accepted meter as the fundamental unit of linear measurement. The problem with material standards is that the materials used for defining the standards could change their size with temperature and other conditions. In order to keep the fundamental unit unchanged, great care and attention had to be exercised to maintain the same conditions. The natural and invariable unit for length was finalized as the primary standard when they found that wavelength of monochromatic light was not affected by environmental conditions. Yard or meter is defined as the distance between two scribed lines on a bar of metal 11-Jan-23 maintained under certain conditions of temperature KYC and support. 36 RV College of Go, change the world Standards of Measurement Engineering First- Imperial standard Yard-England. Second- International Prototype Meter- France. Wavelength standard. 11-Jan-23 KYC 37 RV College of Go, change the world Imperial Standard Yard Engineering The imperial standard yard is a bronze bar 1 sq. inch in cross-section and 38 inches in length, having a composition of 82% Cu, 13% tin, and 5% Zn. The bar contains holes of ½-inch diameter × ½-inch depth. It has two round recesses, each located one inch away from either end and extends up to the central plane of the bar. A highly polished gold plug having a diameter of 1/10 of an inch comprises three transversely engraved lines and two longitudinal lines that are inserted into each of these holes such that the lines lie in the neutral plane. The top surface of the plug lies on the neutral axis. Yard is then defined as the distance between the two central transverse lines of the plug maintained at a temperature of 62 °F. Yard, which was legalized in 1853, remained a legal standard until it was replaced by the wavelength standard in 1960. 11-Jan-23 KYC 38 RV College of Go, change the world Engineering Imperial Standard Yard One of the advantages of maintaining the gold plug lines at neutral axis is that this axis remains unaffected due to bending of the beam. Another advantage is that the gold plug is protected from getting accidentally damaged. It is important to note that an error occurs in the neutral axis because of the support provided at the ends. This error can be minimized by placing the supports in such a way that the slope at the ends is zero and the flat end faces of the bar are mutually parallel to each other. Airy points can be defined as the points at which a horizontal rod is optionally supported to prevent it from bending. These points are used to support a length standard in such a way as to minimize the error due to bending. 11-Jan-23 KYC 39 RV College of Go, change the world Engineering Imperial Standard Yard Sir George Biddell Airy (1801–92) showed that the distance d between the supports can be determined by the formula 1 ×L n2 − 1 Where n is the number of supports and L is the length of the bar. When it is supported by two points, n=2. Substituting for n, the distance between the supports is obtained as 0.577L. This means that the supports should be at an equal distance from each end to a position where they are 0.577L apart. Normally, airy points are marked for length bars greater than 150 mm. 11-Jan-23 KYC 40 RV College of Go, change the world Engineering Imperial Standard Yard 11-Jan-23 KYC 41 RV College of Go, change the world Engineering Imperial Standard Yard 11-Jan-23 KYC 42 RV College of Go, change the world Engineering Imperial Standard Yard 11-Jan-23 KYC 43 RV College of Go, change the world Imperial Standard Yard Engineering 38" 36" at 62 deg F Neutral axis 1" 1" Gold plug Bronze bar 82% Cu, 13% Tin, 5% Zinc 1" Enlarged view of gold plug showing engraving 11-Jan-23 KYC 44 RV College of Go, change the world Engineering Airy points Deflection in bars- errors in length caused by end faces not being parallel 11-Jan-23 KYC 45 RV College of Go, change the world Engineering Significance of Airy-Points in Imperial Standard Yard 11-Jan-23 KYC 46 RV College of Go, change the world Engineering Airy points - contd… 1 = Distance between supports ×L n −1 2 n: no. of supports L: length of bar 1 For simply supported beam = × L = 0.577 L 3 L − 0.577 L Distance of each support from end of bar = 2 Bessel points : At points of min deflection ends sag so as to lift the centre & minimize central deflection. Occurs when points of support are 0.554L. 11-Jan-23 KYC 47 RV College of Go, change the world Difference between Airy points & Bessel points Engineering Airy points (end faces parallel) Bessel points (minimum deflection points) Sag permitted to pull ends of bar up with Ends allowed to sag to lift centre to prevent measuring plane. deflection. No deflection at ends. Ends deflected downwards. Distance between supports =0.577L Distance between supports =0.554L Distance between supports & sagging at Distance between supports & sagging at center is center is more. less. Suitable for length standards. Suitable for line standards. Indicated on length bars above 150 mm. Not indicated on straight edges & reference planes. 11-Jan-23 KYC 48 RV College of Go, change the world Engineering International Prototype Meter International prototype meter was established in 1875 by International Bureau of Weights and Measures. It is defined as the distance between the centre positions of the two lines engraved on the highly polished surface of a 102 cm bar of pure platinum–iridium alloy (90% platinum and 10% iridium) maintained at 0°C under normal atmospheric pressure and having the cross- section of a web. The top surface of the web contains graduations coinciding with the neutral axis of the section. The web-shaped section offers two major advantages. Since the section is uniform and has graduations on the neutral axis, it allows the whole surface to be graduated. This type of cross-section provides greater rigidity for the amount of metal involved and is economical even though an expensive metal is used for its construction. The bar is inoxidizable and can have a good polish, which is required for obtaining good- quality lines. 11-Jan-23 KYC 49 RV College of Go, change the world International Prototype Meter Engineering It is supported by two rollers having at least 1 cm diameter, which are symmetrically located in the same horizontal plane at a distance of 751 mm from each other such that there is minimum deflection. Web section – max rigidity, economy of costly material. 11-Jan-23 KYC 50 RV College of Go, change the world Engineering International Prototype Meter 11-Jan-23 KYC 51 RV College of Go, change the world Disadvantages of Material Standards Engineering Material standards are affected by changes in environmental conditions such as temperature, pressure, humidity, and ageing, resulting in variations in length. Preservation of these standards is difficult because they must have appropriate security to prevent their damage or destruction. Replicas of material standards are not available for use at other places. They cannot be easily reproduced. Comparison and verification of the sizes of gauges pose considerable difficulty. While changing to the metric system, a conversion factor is necessary. 11-Jan-23 KYC 52 RV College of Go, change the world WAVELENGTH STANDARD Engineering By using wavelengths of a monochromatic light as a natural and invariable unit of length, the dependency of the working standard on the physical standard can be eliminated. The definition of a standard of length relative to the meter can easily be expressed in terms of the wavelengths of light. The use of the interference phenomenon of light waves to provide a working standard may thus be accepted as ultimate for all practical purposes. However, there were some objections to the use of the light wavelength standard because of the impossibility of producing pure monochromatic light, as wavelength depends upon the amount of isotope impurity in the elements. However, with rapid advancements in the field of atomic energy, pure isotopes of natural elements have been produced. Cadmium 114, krypton 86, and mercury 198 are possible sources of radiation of wavelengths suitable for the natural standard of length. 11-Jan-23 KYC 53 RV College of Go, change the world WAVELENGTH STANDARD Engineering There is no need to preserve the wavelength standard as it is not a physical one. This standard of length is reproducible, and the error of reproduction can be of the order of 1 part in 100 million. Finally, in 1960, at the 11th General Conference of Weights and Measures held in Paris, it was recommended and decided that krypton 86 is the most suitable element if used in a hot-cathode discharge lamp maintained at a temperature of 68 K. According to this standard, meter is defined as 1,650,763.73 wavelengths of the red–orange radiation of a krypton 86 atom in vacuum. Yard is defined as 1,509,458.35 wavelengths of red-orange radiation in vacuum of krypton-86 isotope. (Yard=0.9144meter) This standard can be reproduced with an accuracy of about 1 part in 109 and can be accessible to any laboratory. Krypton 86 chosen as it produces sharply defined interference lines. 11-Jan-23 KYC 54 RV College of Go, change the world Engineering Wavelength standard/Optical length standard 11-Jan-23 KYC 55 RV College of Go, change the world Advantages of Wavelength Standards Engineering Length does not change (not influenced by effects of variation in surrounding conditions). Need not be stored / preserved. Easily reproducible. Used for comparative measurements of very high accuracy. Not subjected to destruction by wear and tear. 11-Jan-23 KYC 56 RV College of Go, change the world Metre as of today (Modern Meter) Engineering Metre is defined as the length of the path travelled by light in vacuum in 1/299 792 458 second. The modern meter was defined in the 17th General Conference of Weights and Measures held on 20 October 1983. According to this, the meter is the length of the path travelled by light in vacuum during a time interval of 1/299,792,458 of a second. This standard is technologically more accurate and feasible when compared to the red– orange radiation of a krypton 86 atom and can be realized in practice through the use of an iodine-stabilized helium–neon laser. The reproducibility of the modern meter is found to be 3 parts in 1011, which could be compared to measuring the earth’s mean circumference to an accuracy of about 1 mm. 1 yard = length of path travelled in 3*10-9 seconds. 11-Jan-23 KYC 57 RV College of Go, change the world Engineering Subdivisions of standards Primary standards Secondary standards Tertiary standards Working standards 11-Jan-23 KYC 58 RV College of Go, change the world Engineering Subdivision of standards Primary standards: It is essential that there should be one and only one material standard (in paris). No direct application to a measuring problem encountered in engineering Used after 10-20 years for comparison with secondary stds. Secondary standards: These are close copies of primary standards with respect to design, material and length. Kept in the custody of every country in laboratory. Used for comparison with tertiary stds. Safeguard against loss or destruction of primary stds. 11-Jan-23 KYC 59 RV College of Go, change the world Subdivision of standards contd… Engineering Tertiary standards: Tertiary standards are reference standards employed by National Physical Laboratory (NPL) and are the first standards to be used for reference in laboratories and workshop True copies of secondary stds. Reference for comparison with working stds. Working standards: These standards are similar in design to primary, secondary and tertiary standards, but being less in cost and are made of low-grade materials. Used on the shop floor. General application in metrology laboratories. 11-Jan-23 KYC 60 RV College of Go, change the world Classification of standards based on purpose Engineering Standard Purpose Reference Reference Calibration of inspection and working Calibration standards Inspection Used by inspectors Working standards Used by operators 11-Jan-23 KYC 61 RV College of Go, change the world Hierarchical Classification of standards Engineering 11-Jan-23 KYC 62 Go, change the world Hierarchical Classification of standards RV College of Engineering Accuracy is one of the most important factors to be maintained and should always be traceable to a single source, usually the national standards of the country, that are in close contact with the BIPM. Hence, there is an assurance that items manufactured to identical dimensions in different countries will be compatible with each other, which helps in maintaining a healthy trade. Comparisons with national standards are seldom performed, as frequent comparisons may degrade their accuracy. For frequent comparisons of the lower-order standards, national reference standards are generally used. For calibration purposes, normally working standards are employed. These working standards stand third in the hierarchical classification and are sometimes called national working standards. Interlaboratory standards and reference standards for laboratories, which 11-Jan-23 are of good quality, are derived from working KYC standards. 63 RV College of Go, change the world Line standards Engineering Line standards: When length being measured is expressed as the distance between two lines. Line standards do not provide high accuracy as that of end standards. Example: Measuring scale, Imperial standard yard, International prototype meter, meter rule with divisions. Scales can be engraved Quick & easy to use Scale markings are subjected to wear No built-in datum Scales are subjected to parallax error Magnifying lens/ microscope required. 11-Jan-23 KYC 64 RV College of Go, change the world Engineering End Standards End standards: When the length being measured is expressed as the distance between two parallel end faces. End standards can be made to a very high degree of accuracy. Example: Slip gauges, gap gauges, vernier calipers, micrometer etc. Highly accurate , precise. Time consuming & measures only one dimension Subjected to wear and no parallax error Disadvantages: Forming two parallel surfaces at ends Heat treat ends for stability. 11-Jan-23 KYC 65 RV College of Go, change the world Engineering Comparison between Line standards and End standards Characteristics Line standards End Standards Principle of Length -distance between as distance b/w two flat parallel measurement distance b/w two lines faces Accuracy Limited accuracy +/- 0.5 mm High accuracy +/-0.001 mm Ease & time of Measurements made using scale Requires skill & time measurement are quick & easy consuming No wear, may occur on leading Wear on their measuring Effect of wear ends surfaces. Cannot align with axis of Can align with axis of Alignment measurement measurement Manufacture & Simple and low cost Complex & high cost cost Parallax effect Subjected to parallax error No parallax error Slip gauges, end bars, Examples Scale micrometer 11-Jan-23 KYC 66 RV College of Go, change the world Engineering TRANSFER FROM LINE STANDARD TO END STANDARD Primary standards are basically line standards and that end standards are practical workshop standards. Line standards are highly inconvenient for general measurement purposes and are usually used to calibrate end standards, provided that the length of primary line standard is accurately known. There is a probability of the existence of a very small error in the primary standard. It is important to accurately determine the error in the primary standard so that the lengths of the other line standards can be precisely evaluated when they are compared with it. Measurements are made using end standards, the distance is measured between the working faces of the measuring instrument, which are flat and mutually parallel. A composite line standard is used to transfer a line standard to an end standard. 11-Jan-23 KYC 67 RV College of Go, change the world TRANSFER FROM LINE STANDARD TO END STANDARD Engineering It has already been clarified that the line standard of length is a highly inconvenient form for general measurement applications. In order to determine the position of the defining lines in the standard, a special microscope has to be employed. Since the line standard was defined first, and end standards being of real importance and more utility ; the end standards had to be produced of the highest accuracy in relation to the line standard. In end standards, the distance is defined between the working faces which are flat and mutually parallel. In order to transfer the line standard correctly to the ends of a bar, the use of an instrument called Line-standard comparator is made. It consists of two microscopes mounted about a yard apart over a table. A gauge, about 35½ inches in length is produced with end faces flat and mutually parallel. Two ½ inch blocks are taken and wrung at the ends of this gauge. The two ½ inch blocks are engraved with a fine line on one surface approximately in the centre of the two end faces. Thus the distance between the centre lines is approximately 36 inches after wringing these inch blocks to the main 35 ~ inches gauge. 11-Jan-23 KYC 68 RV College of Go, change the world TRANSFER FROM LINE STANDARD TO END STANDARD Engineering The standard and the above blocks are mounted on the table. The microscopes have accurate micrometer screw controlled eyepieces. In eyepiece, there are cross wires to focus on the lines of the standard. The table is capable of being traversed across so that either block may be brought under the microscope. The apparatus compares the positions of lines on the standard with lines on the gauge, and with micrometer eyepieces any small longitudinal variations between them can be determined. Let the actual length 35 inches gauge be. The distance between two lines on line standard is 36″. The two blocks at end are arranged in four ways. (Fig. shows one position and other three positions are self-explanatory) and difference of readings between lines on standard and the line on gauges are noted every time. Let the difference be d1 d2, d3 and d4 respectively. Then for the successive positions of the | inch blocks, we have 11-Jan-23 KYC 69 RV College of Go, change the world Engineering TRANSFER FROM LINE STANDARD TO END STANDARD (NPL method of deriving End standard from line standard) Line Standard Comparator x1 Measured difference d1= x1- x2 x2 36 inch line standard 1 / 2 inch block /2 inch block 1 35 1/2 inch end standard a b l c d 11-Jan-23 KYC 70 RV College of Go, change the world TRANSFER FROM LINE STANDARD TO END STANDARD Engineering A line standard comparator is used to transfer the line standard correctly to the ends of a bar. It consists of two microscopes mounted about a yard apart over a table. An end standard about 35½ inch in length is produced with flat & parallel faces. Two ½inch blocks with centrally engraved lines are ‘wrung’ to the ends of this end standard, such that the distance between the center lines is approximately 36 inches. The difference of readings between the lines on the line standard & the lines on the end standard are noted every time, by arranging the end blocks in different ways to eliminate errors in wringing & of marking of center lines. If the actual length of the end standard is l, then for the four different ways of wringing the end blocks, we can write; l + b + c = 36 + d1 l + b + d = 36 + d 2 l + a + c = 36 + d3 l + a + d = 36 + d 4 11-Jan-23 KYC 71 RV College of Go, change the world Engineering TRANSFER FROM LINE STANDARD TO END STANDARD Where d1, d2, d3 & d4 are the differences noted for the successive positions of the ½ inch blocks respectively. 1 ∑d Taking mean, l + (a + b + c + d ) = 36 + 1 2 4 Next the 35½ inch end standard wrung with one of the ½ inch blocks is compared with 36inch end bar (to be calibrated) on a Brooke’s level comparator & the deviation D1 may be noted. Then the other ½inch block is wrung with it & again is compared with the end bar (to be calibrated) & the deviation D2 is noted. If L is the actual length of the 36inch end bar, then l + a + b = L + D1 l + c + d = L + D2 1 l + (a + b + c + d ) = L + ∑ D 2 2 2 Combining the above equation 1 & 2 L =36 + ∑d − ∑D 4 2 11-Jan-23 KYC 72 RV College of Go, change the world TRANSFER FROM LINE STANDARD TO END STANDARD Engineering /2 inch block 1 D1 b a 35 1/2 inch end standard L 36 inch end bar being calibrated 11-Jan-23 KYC 73 RV College of Go, change the world BROOKES LEVEL COMPARATOR Engineering 11-Jan-23 KYC 74 RV College of Go, change the world Calibration of End bars Engineering The actual lengths of end bars can be found by wringing them together and comparing them with a calibrated standard using a level comparator and also individually comparing among themselves. This helps to set up a system of linear equations which can be solved to find the actual lengths of individual bars. The procedure is clearly explained in the forthcoming numerical problems. 11-Jan-23 KYC 75 RV College of Go, change the world Calibration of End Bars Engineering A one meter (1000mm) calibrated bar is wrung to a surface plate and two 500mm bars (A and B) are wrung together to form a basic length of one meter, which is then wrung to a surface plate adjacent to a meter bar as shown in the Figure. The difference in height X1, is noted. 11-Jan-23 KYC 76 RV College of Go, change the world Engineering Calibration of End Bars Then comparison is made between the two 500mm length bars A and B to determine the difference in length. LA= the length of 500mm length bar A LB=the length of 500mm length bar B X1=difference between one meter length bar and the combined length of bars A and B X2=difference in length between bar A and bar B L=Actual length of one meter bar. L ± X 1 = LA + LB From fig.(a) L= B LA ± X 2 From fig.(b) L ± X 1 = LA + ( LA ± X 2 ) =2 LA ± X 2 2 LA =L ± X 1 ± X 2 L ± X1 ± X 2 LA = 2 11-Jan-23 KYC 77 RV College of Go, change the world NUMERICALS Engineering 1. A calibrated meter end bar has an actual length of 1000.0003mm. It is to be used in the calibration of two bars A and B, each having a basic length of 500mm. When compared with the meter bar LA+LB was found to be shorter by 0.0002mm. In comparing A with B it was found that A was 0.0004mm longer than B. Find the actual length of A and B. 11-Jan-23 KYC 78 RV College of Go, change the world Engineering NUMERICALS 1. A calibrated meter end bar has an actual length of 1000.0003mm. It is to be used in the calibration of two bars A and B, each having a basic length of 500mm. When compared with the meter bar LA+LB was found to be shorter by 0.0002mm. In comparing A with B it was found that A was 0.0004mm longer than B. Find the actual length of A and B. L − X 1 = LA + LB L= A LB + X 2 L − X 1 = ( LB + X 2 ) + LB L − X 1 = 2 LB + X 2 2 LB =L − X 1 − X 2 L − X 1 − X 2 1000.0003 − 0.0002 − 0.0004 =LB = 2 2 LB = 499.99985mm LA = LB + X 2 = 499.99985 + 0.0004 LA = 500.00025mm KYC 11-Jan-23 79 RV College of Go, change the world Engineering NUMERICALS 2. Three 100mm end bars are measured on a level comparator by first wringing them together and comparing with a 300mm bar. The 300mm bar has a known error of +40µm and the three bars together measure 64µm less than the 300mm bar. Bar A is 18µm longer than bar B and 23µm longer than bar C. Find the actual length of each bar. 11-Jan-23 KYC 80 RV College of Go, change the world NUMERICALS Engineering 3. Four length bars A, B, C, D of approximately 250mm each are to be calibrated with standard calibrated meter bar which is actually 0.0008mm less than a meter. It is also found that, bar B is 0.0002mm longer than bar A, bar C is 0.0004mm longer than bar A and bar D is 0.0001mm shorter than bar A. The length of all four bars put together is 0.0003mm longer than the calibrated standard meter. Determine the actual dimensions of each bar. 11-Jan-23 KYC 81 RV College of Go, change the world Engineering NUMERICALS 2. Answer : LA=100.006mm LB=99.988mm LC=99.983mm 3. Answer: LA=249.99975mm LB=249.99995mm LC=250.00015mm LD=249.99965mm 11-Jan-23 KYC 82 RV College of Go, change the world Engineering NUMERICALS It is required to obtain a meter standard from a calibrated line standard using a composite line standard. The actual length of the calibrated line standard is 1000.015 mm. The composite line standard comprises a length bar having a basic length of 950 mm and two end blocks, (a+b) and (c+d), each having a basic length of 50 mm. Each end block contains an engraved line at the centre. Four different measurements were obtained when comparisons were made between the calibrated line standard and the composite bar using all combinations of end blocks:L1=1000.0035 mm, L2=1000.0030 mm, L3=1000.0020 mm, and L4=1000.0015 mm. Determine the actual length of the meter bar. Block (a + b) was found to be 0.001 mm greater than block (c + d) when two end blocks were compared with each other. 11-Jan-23 KYC 83 RV College of Go, change the world ACCURACY Engineering Accuracy is the closeness with which an instrument reading approaches the true value of the quantity being measured. Accuracy is the degree of agreement of the measured dimension with its true magnitude. Accuracy can also be defined as the maximum amount by which the result differs from the true value or as the nearness of the measured value to its true value, often expressed as a percentage. True value may be defined as the mean of the infinite number of measured values when the average deviation due to the various contributing factors tends to zero. In practice, realization of the true value is not possible due to uncertainties of the measuring process and hence cannot be determined experimentally. Positive and negative deviations from the true value are not equal and will not cancel each other. 11-Jan-23 KYC 84 RV College of Go, change the world Engineering ACCURACY Requirements of accurate measuring instruments Error should be eliminated Sources of inaccuracy eliminated Instrument should be calibrated Should possess constant accuracy Factors affecting accuracy of measuring system Factors affecting calibration standards Factors affecting work piece Factors affecting inherent characteristics of instrument Factors affecting person Factors affecting environment 11-Jan-23 KYC 85 RV College of Go, change the world ACCURACY Engineering Factors affecting calibration standards Coefficient of thermal expansion Internal calibration Elastic properties Stability with time Factors affecting work piece Cleanliness of workpiece Surface finish Defects on workpiece Factors affecting inherent characteristics of instrument Adequate sensitivity Adequate consistency Good accuracy precision 11-Jan-23 KYC 86 RV College of Go, change the world ACCURACY Engineering Factors affecting person Skill and training methodology Selection of instruments and standards of measurements Altitude towards personal accuracy achievements Factors affecting environment Temperature , humidity Clean surrounding Adequate illumination 11-Jan-23 KYC 87 RV College of Go, change the world PRECISION Engineering Precision is the degree of repetitiveness of the measuring process. It is the degree of agreement of the repeated measurements of a quantity made by using the same method, under similar conditions. The ability of the measuring instrument to repeat the same results during the act of measurements for the same quantity is known as repeatability. Repeatability is random in nature and, by itself, does not assure accuracy, though it is a desirable characteristic. Precision refers to the consistent reproducibility of a measurement. Reproducibility is normally specified in terms of a scale reading over a given period of time. If an instrument is not precise, it would give different results for the same dimension for repeated readings. In most measurements, precision assumes more significance than accuracy. 11-Jan-23 KYC 88 RV College of Go, change the world The person hit the bull's-eye? Engineering Three targets with three arrows each to shoot. Both Precise but Neither accurate not accurate and precise accurate nor precise 11-Jan-23 KYC 89 RV College of Go, change the world Precision v/s Accuracy Engineering Precision Accuracy Degree to which measured value agrees Repeatability of process with true value of measured quantity Never designates accuracy May designate precision Close relationship of observed reading Relationship between value of with average value observed Standard deviation is index of precision Difference between measured and true less value of standard deviation more value is error of measurements. Less precise the instrument error more accuracy 11-Jan-23 KYC 90 RV College of Go, change the world REPEATABILITY & REPRODUCIBILITY Engineering Five factors may contribute to the variability found in repeated measurements: (1) observer, (2) instrument used (eg, model, serial number), (3) instrument calibration, (4) environment (temperature, humidity, etc), and (5) time interval between measurements. Precision consists of both repeatability and reproducibility. Repeatability refers to the variability in repeated measurements in which the above factors are considered constant. Reproducibility, on the other hand, refers to variability when 1 or more of the 5 factors vary. 11-Jan-23 KYC 91 RV College of Go, change the world REPEATABILITY & REPRODUCIBILITY Engineering Repeatability pertains to the closeness of output readings when the same input is applied repetitively over a short period of time with the same measurement conditions, same instrument and observer, same location and same conditions of use maintained throughout. Reproducibility relates to the closeness of output readings for the same input when there are changes in the method of measurement, observer, measuring instrument, location, conditions of use and time of measurement. 11-Jan-23 KYC 92 RV College of Go, change the world Engineering Calibration Calibration is a comparison of instrument performance to standards of known accuracy. Calibrations directly link customers measurement equipment to national and international standards. Calibration : the procedure laid down for making adjusting or checking a scale so that readings of an instrument or measurement system conform to an accepted standard. Graphical representation of calibration record is called calibration curve. Curve relates standard values of input or measurand to actual values of output throughout operating range of instrument. Advantages of calibration Accuracy in performing manufacturing operations, Reduced inspection and ensured quality products by reducing errors in measurement. 11-Jan-23 KYC 93 RV College of Go, change the world SENSITIVITY Engineering Sensitivity refers to the ability of a measuring device to detect small differences in a quantity being measured. Sensitivity is the rate of displacement of the indicating device of an instrument with respect to the measured quantity. Sensitivity is the ratio of the changes in the output of an instrument to a change in the value of the quantity to be measured. Ratio of scale spacing to scale division value It is also called amplification factor/ gearing ratio Sensitivity has wide range of units Operation of resistance thermometers depends on change in resistance to change in temperature. Units: ohms/deg c i/p to o/p of electrical/ electronic equipment –gain Increase in displacement with optical and mechanical instruments – amplification 11-Jan-23 KYC 94 RV College of Go, change the world Engineering SENSITIVITY Thus, if the sensitivity of a thermocouple is denoted as 10µV/°C, it indicates the sensitivity in the linear range of the thermocouple voltage vs. temperature characteristics. Similarly, sensitivity of a spring balance can be expressed as 25 mm/kg, indicating additional load of 1 kg will cause additional displacement of the spring by 25mm. Sensitivity of an instrument may also vary with temperature or other external factors. This is known as sensitivity drift. Suppose the sensitivity of the spring balance mentioned above is 25 mm/kg at 20°C and 27mm/kg at 30°C. Then the sensitivity drift/°C is 0.2 (mm/kg)/°C. In order to avoid such sensitivity drift, sophisticated instruments are either kept at controlled temperature, or suitable in-built temperature compensation schemes are provided inside the instrument. 11-Jan-23 KYC 95 RV College of Go, change the world Engineering Sensitivity If the calibration curve is linear, as shown, the sensitivity of the instrument is the slope of the calibration curve. If the calibration curve is not linear as shown, then the sensitivity varies with the input. 11-Jan-23 KYC 96 RV College of Go, change the world Engineering LINEARITY Linearity is defined as the ability to reproduce the input characteristics symmetrically and linearly. Linearity is actually a measure of nonlinearity of the instrument. When we talk about sensitivity, we assume that the input/output characteristic of the instrument to be approximately linear. But in practice, it is normally nonlinear, as shown in Fig. The linearity is defined as the maximum deviation from the linear characteristics as a percentage of the full scale output. ∆O Linearity = Omax − Omin 11-Jan-23 KYC 97 RV College of Go, change the world Readability Engineering Readability is defined as the closeness with which the scale of the analog instrument can be read. Readability is defined as the ease with which readings may be taken with an instrument. Readability difficulties may often occur due to parallax errors when an observer is noting the position of a pointer on a calibrated scale Fine and widely spaced graduation lines ordinarily improve the readability. If the graduation lines are very finely spaced, the scale will be more readable by using the microscope, however, with the naked eye the readability will be poor. 11-Jan-23 KYC 98 RV College of Go, change the world Engineering HYSTERESIS Hysteresis is phenomenon which depicts different output effects when loading and unloading, whether it is a mechanical / electrical or any system. Hysteresis exists not only in magnetic circuits, but in instruments also. For example, the deflection of a diaphragm type pressure gage may be different for the same pressure, but one for increasing and other for decreasing, as shown in Fig. H = Hysteresis ×100 Omax − Omin 11-Jan-23 KYC 99 RV College of Go, change the world HYSTERESIS Engineering Causes: All energy put to stressed parts when loading is not reversible upon unloading Different values of output for same input under increasing and decreasing conditions. Due to mechanical friction, slack motion in bearings, elastic deformation, magnetic & thermal effects. 11-Jan-23 KYC 100 RV College of Go, change the world Drift Engineering Drift causes the measurement result to vary for a given input quantity. It occurs due to wear and tear of parts, hysteresis effect in metals, changes in metals caused by contamination, environmental factors, magnetic fields, changes in temperature and mechanical vibrations, high mechanical stress in parts. Thus drift is an undesirable quantity and it occurs very slowly. Drift cant be easily compensated for but can be carefully guarded against by care, prevention, inspection and maintenance. It is drift which causes change in calibration of instrument. Drift can be classified into three categories (i) Zero drift: It sets in when the calibration gradually shifts due to slippage, permanent set. It can be taken care of by zero setting. (ii) Span drift: Proportional change in the indication all along the upward scale in called span drift. (iii) Zonal drift: It occurs only in a zone (portion) of span. 11-Jan-23 KYC 101 RV College of Go, change the world Engineering Drift Span drift Zero drift 11-Jan-23 KYC 102 RV College of Go, change the world Definitions and Concepts Engineering Range (or span) : It defines the maximum and minimum values of the inputs or the outputs for which the instrument is recommended to use. For example, for a temperature measuring instrument the input range may be 100-500°C and the output range may be 4-20 mA. Threshold : If instrument input is increased very gradually from zero , there will be some minimum value below which no output can be detected. This minimum value defines threshold of instrument. Threshold of a measuring instrument is the minimum value of input signal that is required to make a change or start from zero Resolution: If the input is slowly increased from some arbitrary input value, it will again be found that output does not change at all until a certain increment is exceeded. This increment is called resolution. Thus, resolution refers to the smallest change of input for which there 11-Jan-23 will be a change output. KYC 103 RV College of Go, change the world Engineering STATIC & DYNAMIC CHARACTERISTICS OF MEASUREMENT SYSTEM Static characteristics: The set of criteria defined for the instruments, which are used to measure the quantities which are slowly varying with time or mostly constant, i.e., do not vary with time. Static characteristics refer to the characteristics of the system when the input is either held constant or varying very slowly. Classification of static characteristics are mainly: Accuracy, Precision, Range, Sensitivity, Linearity, Hysteresis, Resolution, Drift, Static error, Dead zone. Dynamic characteristics: The performance of the instrument when the input variable is changing rapidly with time. The dynamic performance of an instrument is normally expressed by a differential equation relating the input and output quantities. It is always convenient to express the input-output dynamic characteristics in form KYC of a linear differential equation. 11-Jan-23 104 RV College of Go, change the world Dynamic characteristics Engineering Speed of response: The rapidity with which a measurement system responds to changes in the measured quantity. Measuring lag: The retardation or delay in the response of a measurement system to changes in the measured quantity. Retardation lag : Response begins immediately after the change in measured quantity Time delay lag : Response begins after a dead time after the application of the input (shifted along the time scale). Fidelity: Fidelity of a system is defined as the ability of the system to reproduce the output in the same form as the input. It is the degree to which a measurement system indicates changes in the measured quantity without any dynamic error. Ideally a system should have 100% fidelity and there is no distortion produced by the system. Dynamic error: It is the difference between the true value of the quantity changing with time & the value indicated by the measurement system if no static error is assumed. It is also called measurement error. 11-Jan-23 KYC 105 RV College of Go, change the world Dynamic characteristics Engineering 11-Jan-23 KYC 106 RV College of Go, change the world Response of Measuring Systems Engineering The evaluation of the ability of a system to transmit and present all the pertinent information included in the input signal and to exclude everything else, is called response If the output information truly represents the input. If the input information is in the form of a sine wave, a square wave, or a sawtooth wave, does the output appear as a sine wave, a square wave, or a sawtooth wave. Is each of the harmonic components in a complex wave treated equally, or are some attenuated, completely ignored, or perhaps shifted timewise relative to the others? These questions are answered by the response characteristics of the particular system—that is, (1) amplitude response, (2) frequency response, (3) phase response, and (4) slew rate. 11-Jan-23 KYC 107 RV College of Go, change the world Engineering Response of Measuring Systems Amplitude response is governed by the system’s ability to treat all input amplitudes uniformly. If an input of 5 units is fed into a system and an output of 25 indicator divisions is obtained, we can generally expect that an input of 10 units will result in an output of 50 divisions. Although this is the most common case, other special nonlinear responses are also occasionally required. Whatever the arrangement, whether it be linear, exponential, or some other amplitude function, discrepancy between design expectations in this respect and actual performance results in poor amplitude response. Of course no system exists that is capable of responding faithfully over an unlimited range of amplitudes. 11-Jan-23 KYC 108 RV College of